
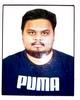
- Open Access
- Authors : Mayank Chaturvedi, Prof. Dinesh Jaiswal, Dr R.P Tiwari, Dr D.K Jain
- Paper ID : IJERTV14IS020059
- Volume & Issue : Volume 14, Issue 2 (February 2025)
- Published (First Online): 24-02-2025
- ISSN (Online) : 2278-0181
- Publisher Name : IJERT
- License:
This work is licensed under a Creative Commons Attribution 4.0 International License
Laboratory Investigation on the Bituminous Mix Design Modified with the Use of Plastic Waste Rubber
Mayank Chaturvedi
Research Scholar, Dept of Civil Engineering,
Prof. Dinesh Jaiswal
Assistant Prof.& Guide Department of Civil Engineering
Dr R.P Tiwari
H.O.D Department of Civil Engineering
Dr D.K Jain
Professor Department of Civil Engineering Rewa Engineering College, Rewa (M.P)
Abstract: – Using waste accoutrements like plastics and rubber in road construction is being decreasingly encouraged to reduce environmental impact. Plastics and rubbers are one of them. The plastic waste volume in external solid waste is increasing due to increased population and life changes. also, most tires, especially those fitted to motor vehicles, are manufactured from synthetic rubber. Disposal of both is a serious problem. At the same time, a nonstop increase in the number of vehicles emphasizes on need for roads with better quality and engineering design. This waste plastic and rubber can be used to incompletely replace the conventional bitumen material to ameliorate asked mechanical characteristics for particular road mixes. In the present study, a comparison is carried out between the use of waste plastic like PET bottles and scruple rubber (and 25) by weight of bitumen) in bitumen concrete mixes to dissect which has a better capability to modify bitumen to use it for road construction.
Keywords: PET rubber, Bitumen, summations Marshall Stability test.
-
INTRODUCTION
Bituminous concrete mix is a combination of aggregates and binders. The aggregates act as the pavement's structural skeleton and bitumen acts as the glue of the mix. The properties of the aggregates have a direct and significant effect on the performance of the pavement Patel et al. (2016) and Sun et al. (2018). Using commercial by-products and recycled materials in construction as secondary and alternative materials has gained widespread acceptance and is becoming more important. The demands for industrial by-products and recycled materials are increasing per annum Joni et al. (2019). Using industrial byproducts in pavement engineering not only provides construction materials with possible savings over new materials, but it also reduces demands on natural construction materials. It also protects the environment and saves money by reducing the amount of waste materials requiring disposal. An asphalt pavement, which is designed and constructed properly will eventually undergo various types of failures due to various reasons such as several years of pavement served, type of paving materials used, and due to other environmental factors, etc Tran et al. (2015) Irfan et al. (2018) and Wang et al. (2019). Among various types of pavement failures rutting or grooving on the top layer is the major type of failure that reduces the life of the flexible pavements. This may be due to the insufficient compaction of the base/sub-base layer or bituminous layers during construction. The type of mix used in pavement construction plays an important role for minimizing the rut depth. Stone Mastic Asphalt or Stone Matrix Asphalt (SMA), is one such mix that provides tough and durable asphalt mix. It is highly used as a rut-resistant mix for wearing and intermediate courses.
SMA is a gap-graded asphalt mix that has a stone-on-stone contact to provide strength and a rich mortar binder to provide durability. Generally, SMA is more expensive than conventional bituminous mixes because SMA requires high asphalt content and more durable aggregates and fibres as a stabilizer. The cost of stone matrix asphalt is found to be 20-25 % higher than the typical dense-graded mixes. Thus, there is a need for the study of alternate materials that can reduce the cost of SMA mix.
Reclaimed Asphalt Pavement (RAP) is the scarified pavement material containing aggregates and asphalt. Large quantities of RAP materials are generated during the construction and maintenance of the highway Hanumanth Rao et al. (2019) and Joni et al. (2019). The use of reclaimed asphalt pavement materials can substitute the high consumption of coarse aggregates and asphalt for SMA mix. On the other hand, recycling RAP also reduces the use of depleting natural aggregates and solves the disposal issues of reclaimed asphalt material generated from pavement rehabilitation.
Problem statement and aim of the study: Virgin Bitumen (VG 30) is commonly used in most of India, and Indian roads are subjected to higher traffic loading and hot weather conditions. The weather conditions in India lead to variations of temperature of about 60°Cat surface to 30°Cat subgrade during summer. The main objective of this study was to evaluate the effect of crumb rubber-modified bitumen in the binder course of stone mastic mix. Which involves the study of volumetric properties and mechanical properties of SMA mix in the binder course.
-
MATERIALS AND METHOD
The experimental program in this research study aims to evaluate the effect of CRMB for binder courses by evaluating the mechanical properties of crumb rubber-modified stone mastic asphalt mixes.
-
Materials: asphalt binder with penetration grade 40/60 and an average softening point of 56°C was utilized. Tables 3 and 4 illustrate the physical and chemical properties of crumb rubber-modified bitumen respectively. In the present studies crumb rubber with grade 55 is selected based on the climate condition in the southern part of India I S 15462 (2004) and the density of CRMB was found to be 1.11 (gm/cm3). CRMB 55 was procured from Mangalore Refineries and Petrochemicals Limited, Mangalore, Karnataka, India.
The composite aggregate consists of course, medium, and fine aggregate with a maximum 19 mm thickness. Fine aggregate consists of the manufactured sand resulting from crushing operations going through a sieve of 2,36 mm and held on a sieve of 0,075 mm. Aggregates for this study are collected from KMS crusher, Bhagalpur, Tamilnadan. The properties of aggregates are summarised in table 1.
Table 1: Physical Properties of Aggregates
Property
Test
Natural
RAP aggregates
IRC-SP: 79
Aggregates
Specifications
Particle shape
Combined EI & FI
10.51%
22.68%
Max 30%
Strength
Aggregate crushing
23%
19.56%
Max 30%
Toughness
Aggregate Impact value
17.51%
9.73%
Max 18%
Water absorption
Water absorption
0.4%
0.55%
Max 2%
Specific gravity
Specific gravity
2.734
2.66
2.5-2.8
The gradation for 19mm SMA is carried out as per Indian Road Congress SP: 79: 2008 as illustrated in Table 2.
Table 2: Aggregate gradation adopted for SMA (Binder course) as per MORT&H
IS
Percentage passing
Desired Gradation
Obtained
Sieve
gradation
Size
20mm
12mm
6.3mm
Baghouse
dust
upper
Lower
(mm)
down
Down
down
dust
limit
Limit
26.5
100
100
100
100
100
100
100
100
19
89.4
100
100
100
100
100
90
95.44
13.2
11.7
100
100
100
100
70
45
62.0
9.5
0
69.5
100
100
100
60
25
51.20
4.75
0
0
30
100
99.6
28
20
23.96
2.36
0
0
6
100
81.2
24
16
17.32
1.18
0
0
0
100
67.8
21
13
14.78
0.6
0
0
0
100
60.4
18
12
14.04
0.3
0
0
0
100
53
20
10
13.3
0.075
0
0
0
96
42.6
12
8
11.94
Table 3: Physical Properties of Plastic waste-55
Bitumen test
Bitumen grade
Standard test
Plastic waste
Penetration @ 25 °C
57
ASTM D5
Softening point @ °C
56
ASTM D36
Flash Point @ °C
280
ASTM D92
Elastic Recovery @15 °C
35
ASTM D6084
Separation @ 3°C
2.9
ASTM D7173
Viscosity @ 135°C (m/Pas)
301.5
ASTM D4402
Ductility @ 25°C
>100
ASTM D113
Specific Gravity
1.03
ASTM D972
Table 4: Chemical Properties of Plastic-5% Mahrez (1999)
Chemical Components
Test result
Acetone extract (%)
23.1
Rubber hydrocarbon (%)
46.6
Carbon black content (%)
25.08
Ash Content (%)
5.2
Natural rubber content (%)
43.85
Particle size
425
-
Sample Preparations and Test Method: In the design of bituminous mixes, the Marshall method of mix design is generally practiced in India. It is a former design method developed by Bruce Marshall. In this method, the plastic deformation resistance of the cylindrical sample of the bituminous mix is measured when the mix is loaded at 5 cm/minute on its lateral surface. Marshall Stability is defined as the load-carrying capacity of the specimen in kg or kN at the standard temperature of 60 °C. In the Present studies CRMB is added to SMA mix at different percentages of 5.3%, 5.7%, 6%, 6.3%, and 6.6.% by the weight of the total mix, and filler of 10% is added to preparing SMA mixes, approximately
The aggregate gradation matching to Grade 2 of Bituminous Concrete as per MORT&H requirements as shown in Table
3.4 was used for the preparation of Marshall samples. The integrated gradation of the coarse aggregates, fine aggregates, and mineral fillers shall be within limits. The aggregate's gradation is shown in Figure 2.2
Aggregate Gradation is the first step to preparing the Marshall Samples and the gradation is done as per the specifications laid in the MORT&H Standards. To get good stability, use strong, rough, dense-graded, cubical aggregate with just enough binder to coat the aggregate particles. Excess asphalt cement lubricates the aggregate particles and lets them slide past each other more easily (which reduces stability).
The sieves are arranged from the smallest at the bottom to the biggest at the top. Measure a minimum of 1200 g of aggregate sample put in the sieves and shake the aggregate. The aggregate retained in each sieve is then passed through a thickness gauge as shown in Figure 3.9. The gauge collects, weighs, and records all particles that pass through it. For all of the remaining sieves, the same technique is followed, and the flakiness index is computed using the aforementioned equation. It is pertinent to mention that aggregates passing through the sieves are considered for arriving the flakiness. For the elongation index, the particles retained through the gauge are noted and the elongation index is calculated using the above equation.
Washed coarse aggregate is kept on a 4.75mm screen and dried in an oven having a temperature of 105°C in an oven. Then, the dry aggregate is sieved at 80mm, 63mm, 40mm, 20mm, 10mm, and 4.75mm. The aggregate sample is put in a wire mesh basket and soaked in a sodium sulphate solution for at least 16 hours or until it is covered by 15 mm of sodium sulphate. The sample should then be removed and allowed to drain for 15 minutes before being placed in the oven until it reaches a consistent mass, after which it should be taken off and kept for drying at room temperature. Again, immerse in sodium sulphate solution as above and dry it in the oven this process is repeated 10 times and then the aggregate is washed thoroughly. Then put the sample in the oven and dry it thoroughly and the weight of the aggregate is then noted. The average loss of weight should not be more than 12%
1200gm of aggregates are weighed and heated to a temperature of 175°C to 190°C and a quantity of bitumen is heated to a temperature of 120°C to 165 °C. Heated bitumen is added to the heated aggregates and mixed thoroughly at the specified mixing temperature by hand mixing or using a mechanical mixer. The prepared mix is placed in a pre-heated Mold of 95°C to 165°C and compacted using a hammer by applying 50 blows on either side. Compacted Molds are kept for one day without disturbance, then samples are extracted from Molds, and the dimensions and weight of samples are noted down. After that samples are kept in a water bath maintained at 60°C for half an hour. Then the specimens are tested in a Marshall testing machine and stability, and flow are noted. Then the specimen properties are calculated and illustrated.
-
-
RESULTS AND DISCUSSIONS
-
Marshall test results
-
Marshall stability. The results obtained for different percentages of plastic 55 are tabulated in Table 6 and illustrated in Figures 2, 3, 4, and 5. Pavement may be subjected to several repeated stresses, deformation, and also fatigue cracks due to the movement of heavy traffic loads on the pavement so, the mix design used for the pavement construction must be done properly to withstand stresses coming from the vehicles. Mix design should possess resistance to low-temperature cracking, moisture damage, and also permanent deformation. In the design of SMA mix, several properties are considered such as percentage of air voids, voids in mineral aggregates binder content, and voids in aggregates are should be within the permissible limit [23].
Table 5 SMA mix requirements as per IRC: SP: 79-2008
Mix Design Parameters (%)
Requirements
Air void content
4
Bitumen content
5.8 min
Cellulous fibres
0.3% minimum by weight of total mix
Voids In mineral Aggregates (VMA)
17 min
Tensile Strength Ratio (TSR)
85 min
C Plastic waste 5%
Table 6 Marshall stability test results for different content of CRMB
Bitumen
Air voids
Voids in the mineral
Flow value (mm)
Stability (kN)
Content
AV (%)
aggregates
VMA (%)
5.7
5.79
17.97
2.07
8.85
6
4.95
17.80
2.50
9.88
6.3
4.12
17.64
3.18
11.10
6.6
3.88
17.98
4.23
9.33
6.9
3.64
18.33
5.06
8.38
12.00
11.00
10.00
9.00
8.00
7.00
5.4
5.9
6.4
6.9
7.4
Figure 2 Stability values versus CRMB Content
6
5
4
3
2
1
5.4
5.7
6
6.3
6.6
6.9
7.2
Plastic waste10%
Figure 3 Flow results versus Plastic Content
18.40
18.30
18.20
18.10
18.00
17.90
17.80
17.70
17.60
5
5.5
6
6.5
7
Plastic waste 10%
Figure5 VMS results versus Plastic Content
7.00
6.00
5.00
4.00
3.00
2.00
1.00
0.00
5.4
5.6
5.8
6
6.2
6.4
6.6
6.8
7
Plastic waste15(%)
Figure4 Air void results versus Plastic Content
Table 5, explains the mix design parameters for a typical SMA mix [23]. The Marshall stability test results satisfy all the volumetric properties such as stability, flow, VMA, and air voids which are tabulated in the table and illustrated in figure 2, 3, 4, and 5. Among all the percentages of Plastic waste, the stability value obtained for 6.3% of Plastic waste was higher compared to other percentages of plastic waste, and with further increase in Plastic waste content, the stability value started decreasing.
In the case of Marshall flow value and Plastic waste content, 6.3% of Plastic waste achieved the desired flow value further increase in binder content leads to an increase in flow value which in turn leads to an increase in voids. Concerning voids filled in mineral aggregates (VMA) and Air voids (Av) i.e. VMA should be min 17% and AV should be 4% respectively, both the mix design parameter was satisfied by 6.3% of CRMB 55. Further SMA mix samples with 6.3% CRMB 55 are prepared using the Marshall mix design method which was designed and developed by Bruce Marshall and Indirect tensile strength, fatigue, and rutting test is carried out.
-
-
-
CONCLUSIONS
Based on the laboratory studies carried out, the following conclusions can be drawn.
-
The stability / Strength of the stone mastic asphalt mix is increased by adding 6.3% of CRMB 55.
-
The volumetric properties of CRMB 55 in SMA mix for the binder course, satisfy the standard requirements.
-
The addition of 6.3% of CRMB55 increases the fatigue life of the SMA mix at various temperatures and stress levels, the mixture was found to achieve higher fatigue life for 6.3% CRMB55 compared to another percentage of CRMB 55.
-
The addition of 6.3% of CRMB55 to the SMA mix plays an important role in improving the rutting resistance.
-
Use of different modified binders, aggregate gradation, and recycled materials are recommended for future studies.
-
-
REFERENCES
-
Al-bared M A M and A. Marto (2019), Evaluating the compaction behavior of soft marine clay stabilized with two sizes of recycled crushed tiles, In: Pradhan B. (eds) GCEC 2017. GCEC 2017. Lecture Notes in Civil Engineering, vol 9. Springer, Singapore. Springer Singapore.
-
Ariapita R H, S. P. Hairdryer, and R. J. Subrata (2017), Contributions crumb rubber in hot mix asphalt to the resilient modulus, AIP Conf. Proc., vol. 1855, Doi: 10.1063/1.4985475.
-
ASTM D1559-89 (1992), Standard test method for resistance to plastic flow of bituminous mixtures using Marshall Apparatus.
-
Hanumanth Rao C, T. Anil Pradhyumna, K. Durga Prasad, N. Naveenkumar, G. Shantha Kumar Reddy, and M. Hemanth Vardhan (2019), Crumb rubber modified bitumen and quarry dust in flexible pavements, Int. J. Recent Technol. Eng., vol. 8, no. 1, pp. 28682873.
-
Huang B, G. Li, D. X. Shu, and B. K. Egan (2005), Laboratory Investigation of Mixing Hot-Mix Asphalt with Reclaimed Asphalt Pavement,
Transp. Res. Rec. J. Transp. Res. Board, vol. 1929, no. 1, pp. 3745, doe:
10.1177/0361198105192900105.
-
I S 15462 (2004), Polymer and Rubber Modified Bitumen, Bureau of Indian Standards, 2004.
-
I S 15462, Polymer and Rubber Modified Bitumen, Bureau of Indian Standards.
-
IRC: SP:79-2008 (2008), Tentative Specifications for Stone Matrix Asphalt, Indian Road Congress.
-
Irfan M, Y. Ali, S. Ahmed, and I. Hafeez (2018), Performance Evaluation of Crumb Rubber-Modified Asphalt Mixtures Based on Laboratory and Field Investigations, Arab. J. Sci. Eng., vol. 43, no. 4, pp. 17951806, Doi: 10.1007/s13369-017-2729-2.
-
Joni H H, R. H. A. Al-Rubie, and M. A. (2019), Rejuvenation of aged asphalt binder extracted from reclaimed asphalt pavement using waste vegetable and engine oils, Case Stud. Constr. Mater., vol. 11, p. e00279, Doi: 10.1016219.e00279.
-
Kök B V and H. Çolak (2011), Laboratory comparison of the crumb-rubber and SBS modified bitumen and hot mix asphalt, Constr. Build. Mater., vol. 25, no. 8, pp. 32043212, 2011, Doi: 10.1016/j..
-
Mahrez A (1999), Properties of rubberized bitumen binder and its effect on the bituminous mix [M.S. thesis], Faculty of Engineering, University of Malaya, Kuala Lumpur, Malaysia.
-
Mazzoni G, E. Bocci, and F. Canestrari (2018), Influence of rejuvenators on bitumen aging in hot recycled asphalt mixtures, J. Traffic Transp. Eng. (English Ed., vol. 5, no. 3, pp. 157168, Doi: 10.1016/j.jtte.2018.01.001.
-
Patel A ka, S. Gupte, and N. B. Parmar (2016), Stone Matrix Asphalt (SMA) Mix Design Using Different Filler, vol. 3, no. 3, pp. 179182.
-
Shen J, S. Amirkhanian, and J. Aune Miller (2007), Effects of rejuvenating agents on Superpave mixtures containing reclaimed asphalt pavement,
J. Mater. Civ. Eng., vol. 19, no. 5, pp. 376384, 2007, doe: 10.1061/(ASCE)0899-1561(2007)19:5(376).
-
Sun Y, C. Fang, D. Fan, J. Wang, and X. Yuan (2018), A Research on Fatigue Damage Constitutive Equation of Asphalt Mixture, Math. Probe. Eng., vol. 2018, Doi: 10.1155/2018/3489082.
-
Talati Anand V. Talati (2014), Study of Stone Matrix Asphalt for The Flexible Pavement, Int. J. Eng. Dev. Res., vol. 2, no. 1, pp. 789792, [Online]. Available: www.ijedr.org.
-
Tran N, A. Taylor, P. Turner, C. Holmes, and L. Porto (2016), Effect of rejuvenator on performance characteristics of high RAP mixture, Asp. Paving Technol. Assoc. Asp. Paving Technol. Tech. Sess., vol. 85, pp. 283313, Doi:
10.1080/14680629.2015.1266757.
-
Wang H, X. Liu, M. van de Ven, G. Lu, S. Erkens, and A. Scarpas (2020), Fatigue performance of long-term aged crumb rubber modified bitumen containing warm-mix additives, Constr. Build. Mater., vol. 239, p. 117824, Doi:
10.1016/j.conbuildmat.2019.117824.
-
Wang H, Z. Dang, L. Li, and Z. You (2013), Analysis on fatigue crack growth laws for crumb rubber modified (CRM) asphalt mixture, Constr. Build. Mater., vol. 47, pp. 13421349, Doi: 10.1016/j.conbuildmat.2013.06.014.
-
Xiao F and S. N. Amirkhanian (2008), Resilient modulus behaviours of rubberized asphalt concrete mixtures containing reclaimed asphalt pavement, Road Mater. Pavement Des., vol. 9, no. 4, pp. 633649, Doi: 10.3166/rmpd.9.633-649.
-
Xiao F, S. Amirkhanian, and C. H. Juang (2007), Rutting resistance of rubberized asphalt concrete pavements containing reclaimed asphalt pavement mixtures, J. Mater. Civ. Eng., vol. 19, no. 6, pp. 475483, Doi: 10.1061/(ASCE)0899-1561(2007)19:6(475).
-
Xiao F, S. N. Amirkhanian, J. Shen, and B. Putman (2009), Influences of crumb rubber size and type on reclaimed asphalt pavement (RAP) mixtures, Constr. Build. Mater., vol. 23, no. 2, pp. 10281034, doi:
10.1016/j.conbuildmat.2008.05.002.
-
Zamanis M, R. B. Mallick, L. Policanos, and R. Frank (2015), Influence of six rejuvenators on the performance properties of Reclaimed Asphalt Pavement (RAP) binder and 100% recycled asphalt mixtures, Compu. Chem. Eng., vol. 71, pp. 538550, 2014, Doi: 10.1016/j.conbuildmat.2014.08.073.
-
Zamanis M, R. Mallick, and R. Frank (2013), Evaluation of rejuvenators effectiveness with conventional mix testing for 100% reclaimed Asphalt pavement mixtures, Transp. Res. Rec., no. 2370, pp. 1725, doi: 10.3141/2370-03.