
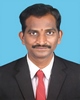
- Open Access
- Authors : S. M. Vadivel , A. H. Sequeira
- Paper ID : IJERTV11IS070175
- Volume & Issue : Volume 11, Issue 07 (July 2022)
- Published (First Online): 26-07-2022
- ISSN (Online) : 2278-0181
- Publisher Name : IJERT
- License:
This work is licensed under a Creative Commons Attribution 4.0 International License
Lean Service Tools for the Positive Sustainable Growth – A Critical Literature Review
-
M. Vadivel 1, A. H. Sequeira 2
1 Assistant Professor, Vellore Institute of Technology Chennai, Business School, Chennai 600127, India.
2 Professor, National Institute of Technology Karnataka, School of Management, Surathkal 575025, India.
Abstract:- The research paper aims to study the Systematic Literature Review (SLR) on how lean systems implemented in service industries and extended to the sustainability model. This study explores SLR considering 137 papers published from 2002 to 2019 into account and focusing on the significance of sustainable development of a conceptual model to explore the research further. This literature review triggered the sustainability development in service sectors such as healthcare, education, public sector, banking, and financial services, IT/ITES, telecom services, hotel, and product services. The limitation of this work excluded lean related studies applied in manufacturing sectors and books during the period of study. Specific features discussed on implications of lean applied in service industries and its importance of sustainability, which is scant in the literature. Hence, both academicians and practitioners can be beneficiary from the SLR point of view.
Keywords:- Lean service, Service industries, Sustainable growth, Systematic literature review
-
INTRODUCTION
Today across the globe, all the organizations facing the intricate problems of environmental and social sustainability (McCarty et al., 2011). Service operations are often well known around the globe. Suppliers, service organizations, and customers link it through service, information sometimes capital flows. Companies all over the world are trying to figure out how to manage their environmental and social performance better. Hence, enhancing sustainability performance and decreasing environmental problems will ensure business in an imperative form. Service organizations responsible for the environmental and sustainability of their customers. For instance, hospitals generate a lot of healthcare waste, and there are issues with storage, transportation, and disposal of that waste. (Unger, Campion, Bilec, & Landis, 2016). Mazzocato et al. (2010) implemented lean in the healthcare sector. The results showed that staff empowerment and continuous improvement in operations prominent to sustainable outcomes. Hence, lean is sustainable in the long term, which is more effective than other approaches in the healthcare department.
In India, the postal department utilizes abundant labour availability for their postal services. Postal service industries make environmental pollution by emitting gas through their vehicle transportation. In the sealing section, employees knowingly or unknowingly inhale the smoke during the dispatched delivery article sealing bags (Ramachandiran.K, 2011). It is a hazard that can cause cancer after a particular period. The postal department has to give prime importance to address this problem and improve the social protection of human well-being through their sustainability. By observing lean performers, Niepce and Molleman (1998) discovered correlations between lean and socio-technical architecture. Venkat and Wakeland (2006) investigated the lean supply chains using CO2 gas emissions as a key performance indicator to measure environmental performance. Leite et al. (2015) suggested that when a lean system implemented correctly in service industries, a lot of benefits can get it from the organization in terms of operational and financial performance. The word sustainable development has attained significant importance in current periods, which will impact our life and society. Hence, organizations have recognized sustainability as a competitive advantage.
Higher education institutes can improve sustainability and reduce environmental problems through assignment submission and academic files, and it must be in digital form. The motto of the education institutes goes by save the environment; save trees concepts. Comm & Mathaisel, 2005 criticized that there is no school has awarded as a sustainable practice. Hence the articles, as mentioned earlier, were explained lean applied in service industries and the importance of sustainability issues. Research Questions (RQs) formulated to address these issues,
-
Under which conditions lean service articles classified?
-
What is the significance of the sustainability model in service industries?
-
What are the research gaps and future scope of this review paper?
The paper arranged as follows. Section 2 deals with methodology; Section 3 explains a descriptive analysis of SLR; Section 4 describes the importance of sustainable development and model for this research; the section 5 concludes with limitations and future research directions.
-
Basic terminology
The book "The computer that changed the world" by Womack and Jones (1990) popularised the lean idea. First and foremost, manufacturing companies all over the world have gradually introduced Lean Manufacturing (LM). The advantage of LM produces more outputs with less input, such as space, material, human effort, and time. It requires fewer inventories on hand to provide the quality of variety products (Womack, J.P, Jones D.T. 1990). In several industries, especially automotive manufacturers and their suppliers, LM techniques aided in the production volume. In the lean definitions, eight forms of wastes
known as TIMWOODS (transport, inventory, motion, waiting, over-processing, overproduction, defects, and underutilization of resources).
These wastes were something that customers do not wish to pay known as non-value added activities. Hunter (2002) showed that by introducing the LM, not only does it require less human effort, but it also increases productivity while reducing inventory. According to lvarez et al. (2008), value stream mapping can easily define waste and areas in need of improvement, and the card system (Kanban) can help reduce inefficiencies. In the United States, Zhou (2012) performed an empirical analysis on SMEs. According to the findings, the majority of businesses are aware of the lean model and its values. The majority of businesses save money by implementing quality enhancement, reducing waste, and improving the overall plant/facility layout. Slowly, LM concepts moved to service industries and implemented successfully in service operations. Progressively, lean concepts implemented in healthcare, education, public services, hotel, financial and IT industries, etc. and stimulating developments started from 2005. The rise of environmental and sustainability, the USAs Environmental Protection Agency (EPA, 2003) defined lean as Produce high-quality goods at a low cost, with the shortest lead time possible, and with constant waste reduction while putting people and the environment first.
Meanwhile, Robin Roy et al. (2000) highlights the significance of lean sustainable product-service systems. The sustainable development started in 1972 at the UN Conference on Human Environment held in Stockholm (Rogers et al., 2008). In service sectors, sustainability aims to improve the service operations in higher customer satisfaction (example: patient safety in hospitals) and profits with minimization environmental impacts, use the resources and energy optimally. The three scopes of sustainability, as described by Dyllick and Hockerts (2002), are business case (economic), natural case (environmental), and societal case (social). The primay outline of this paper is how sustainability helps in service industries while considering the goals of all three dimensions in service operations.
-
-
RESEARCH METHODOLOGY
The research aims to analyse the suitable articles for the scope of sustainable development in service industries, which is scant in literature. A literature review is a logical method to formulate model in any developing field (Easterby-Smith et al., 2002). The top journal articles considered from the period of 2002 to 2019. The reason for selecting 2002 is lean manufacturing concepts widely adopted in service industries, and the argument started on sustainability during this period. We have used keywords such as lean service, lean applied in service industries, lean implemented in service, sustainability, sustainable service, lean sustainable service. Refer Figure 1 SLR process of literature review flowchart.
Research objectives
-
To classify the issues examined in the recent lean system applied in service industries.
-
To provide suggestion for future research in lean sustainability for service industries.
Definition of literature boundaries
-
Broad observation of lean service for various contents (For example. Healthcare, IT/ITES, Finance, Public Sectors, Hotel etc.)
-
Inclusion of Case, Review, Theory, Model, Survey of LS articles.
Setting of inclusion criteria:
-
Cover period: January 2002 Dec. 2019 (17 years)
-
Search term: Keyword << lean service >> in << Article title, Abstract, Keywords >>
-
Search boundaries: Top 137 academic journals applied lean in-service industries, Lean service practitioners journals.
Applying the exclusion criteria:
-
No grey literature (Books, Book chapters, Dissertations, Abstract and Working papers).
-
Articles not covering with lean manufacturing or lean tool applied in manufacturing industries.
Figure 1. A summary of SLR process
The Boolean operators (AND and OR) has been used to find the relevant titles. All 137 selected papers analysed concisely to ensure that articles were significant to our review. An Excel database was created to classify the articles according to their inter- relationships.
-
-
DESCRIPTIVE ANALYSIS
-
Selection of articles and time zone
137 papers considered from 2002 to April 2019 as shown in Figure 2 in a year wise distribution. Figure 3 shows papers becoming greater in size published over the period of time. More than 52% of the papers were published in JCLP, IJLSS, and POM journals. The JCLP literature review papers played a major role as it contributes 6.56%. Interestingly, from 2013 to 2016 greener management related articles were published in reputed journals such as JCLP (9), IJLSS (3), PP&C (4).
Table 1. Distribution of publications as per journals names
S.No.
Journals name
Publication
1
Anesthesiology Clinics
1
2
Annals of Emergency Medicine
2
3
ASQ
2
4
Benchmarking: An International Journal
3
5
Cardiovascular Revascularization Medicine
1
6
CIRP Journal of Manufacturing Science and Technology
1
7
Clinical Governance: An International Journal
1
8
Computers in Industry
1
9
Computers & Industrial Engineering
1
10
Empirical Software Engineering
1
11
European Journal of Marketing
1
12
European Journal of Operational Research
3
13
IBM Center for The Business of Goverment
1
13
ICMA Public Management Magazine
1
14
IFAC-Papers on Line
2
15
IFAC Proceedings
1
16
Industrial Management & Data Systems
1
17
International Conference on Technology and Business Management
1
18
International Journal of Basic & Applied Sciences
1
19
International journal of Business Excellence
1
20
International journal of Business information systems
1
21
International Journal of Business and Social Science
1
22
International Journal of Computational Intelligence Systems
2
International Journal of Health Care Quality Assurance
2
24
International Journal of Information Management
1
25
International Journal of Lean Six Sigma
4
26
International Journal of Operations & Production Management
4
27
International Journal of Productivity and Performance Management
6
28
International Journal of Production Economics
1
29
International Journal of Production Research
1
30
International Journal of Quality & Reliability Management
4
31
International Journal of Quality and Service Sciences
1
32
International Journal of Scientific and Research Publications
1
33
International Journal Services Technology and Management
1
34
International Journal of Six Sigma and Competitive Advantage
4
35
International journal of Supply Chain Management
1
36
IOP Conference Series: Materials Science and Engineering
1
37
Journal of Cleaner Production
9
38
Journal of the merican College of Radiology
1
39
journal of Engineering manufacture
1
40
Journal of Health Organization and Management
2
41
Journal of Information and Knowledge Systems
1
42
Journal of Manufacturing Systems
1
43
Journal of Manufacturing Technology Management
3
44
Journal of Organizational Excellence
1
45
Journal of Operations Management
3
46
Journal of Pediatric Surgery
1
47
Journal of Psychosomatic Research
1
48
Journal of Transport Geography
1
49
Leadership in Health Services
1
50
Marine Policy
1
51
Neural Computation & Applications
1
52
Perioperative Care and Operating Room Management
1
53
Production
1
54
Production Planning & Control
4
55
Production Planning & Control the Management of Operations
2
56
Procedia Engineering
1
57
Procedia Computer Science
1
58
Procedia CIRP
5
59
Procedia Manufacturing
2
60
Procedia – Social and Behavioral Sciences
3
61
Public Management Review
1
62
Quality Assurance in Education
2
63
Sage
1
64
SAIIE25 Proceedings
1
65
Supply Chain Management: An International Journal
2
66
The Journal of Behavioral Health Services & Research
1
67
The British Accounting Review
1
68
The Online Journal of McKinsey & Co
1
69
The International Journal of Human Resource Management
2
70
Total Quality Management & Business Excellence
3
71
Tourism Management
1
72
Tropical Medicine and Health
1
73
Transformations in business & economics
1
74
The Surgeon
1
75
TQM
1
76
The TQM journal
3
77
TQM and Business excellence
1
78
International Journal of Business and Commerce
1
79
International journal of System Assurance and Engineering Management
1
35
30
25
20
15
10
5
0
2002 2004 2005 2006 2007 2008 2009 2010 2011 2012 2013 2014 2015 2016 2017 2018 2019
Year of Publication
Number of Articles
Figure 2. Across the time period distribution of publications
-
Articles classifications
The articles arranged into five categories, namely theoretical or conceptual, case study, surveys, modelling, and literature review. Further, for clear understanding to readers, Fifty four papers presented in empirical research. Twelve articles were theoretical or conceptual. Some journals do not come under case papers, and theoretical papers such as survey accounts for 13 journals and literature review has 24 papers. Finally, the conceptual models' articles are 34, which is the intermediate link between the theoretical and case papers has considered. Figure 3 shows the research methodology applied in this SLR. The Venn diagram describes the distribution of papers among these five research methodologies.
Table 2. Summary of research methodogies applied
Research methodology
No.of papers
Case study (C)
54
Model (M)
34
Review (R)
24
Survey (S)
13
Theory (T)
12
8 41
1
22 R
T 2 C
1 10 1
1 M 4 S 9
18
Figure 3. Distribution papers according to the rearch methodologies employed
-
Geographical contributions
Table 3 shows the details about the geographical regions selected for lean service and sustainability development articles. Developed countries made valuable contributions to their research in lean service and sustainability, almost 70% of contribution leading countries such as the USA, UK, Sweden, Spain, and Australia. Developing countries contributed 30% emerging countries such as India, Malaysia, Turkey, and Srilanka are in a nascent stage. Underdeveloped countries like Ethiopia (0.08%). Developed countries have to encourage the importance of incorporating lean service and sustainability principles to underdeveloped countries. Developing countries has to improve their social-economic feature through implementing sustainability principles.
Developing countries
Publications
India
13
Malaysia
5
Turkey
6
Mexico
2
Republic of Serbia
1
Brazil
3
Morocco
1
Srilanka
4
Omen
1
Libya
1
Indonesia
3
South africa
1
Poland
1
China
1
Under developed countries
Publications
Ethiopia
1
Table 3. Distribution of countries publications (Developed,Developing and Under developed countries
Developed countries
Publications
USA
26
UK
22
Sweden
9
Netherlands
3
Italy
3
Norway
2
Canada
2
Australia
4
France
1
Singapore
1
Ireland
2
Spain
5
Portugal
1
Soothe Arabia
1
New Zealand
1
UAE
1
Germany
1
Taiwan
5
Finland
1
Greece
1
Japan
1
SLR spread
Journals Demography Research methodology Type of Industries
Publication
Year of Publications
Country wise
distribution
Developed Countries
Theory
Case
Healthcare
Education
Developing Countries
Survey
Financial
Under-Developed Countries
Model
IT/ITES
Review
Public sector
Hotel
Telecommunication
Transport
Shipping
Figure 4. Lean service – literature classification
-
SLR spread
From the Figure 5 show that the most of the articles were related to healthcare, followed by IT/ITES and other service sectors. The dominance of the health sector initially implemented the lean concepts in the year 2009 in the UK and later combined with sustainability to identify and remove the hospital wastes. Then, IT and ITES sectors looking for an improved process, eliminate wastes, reducing the documentation work (paperwork) to measure with CMMI level, and SCROM compliance certificates. From the SLR, more force has been given to hospital to develop sustainability in their operations in terms of patient safety and care.
50
45
40
35
30
25
20
15
10
5
0
Figure 5. Distribution of research by industrial sector
-
Development of sustainable development
The articles have five categories of sustainable development. The five types are (1) economy (2) social (3) environmental (4) sustainable (5) others. Most of the articles (82) were dealing with economic issues. The economy category has the majority of the publications, whereas remaining groups need more attention to the lean service practitioners and academicians the sustainability based on three pillars (Economic, Environmental, and Social). If one's support is fragile, then the whole system is not stable. Rightly Gladwin et al. (1995) mentioned that, if any organization wants to achieve sustainability these three dimensions must be satisfied.
90
80
70
60
50
82
40
30
20
10
0
34
economy social sustainable environmental others
9
8
4
Figure 6. Distribution of articles based on sustainability
-
-
RESEARCH GAPS IN EXISTING LITERATURE
After carefully analysing the SLR, we have portrait the research gaps in present lean system conceptual and empirical world in the existing state of knowledge.
Operational definition
Measurement variable
Manufacturing Industries
Lean Manufacturing System (LMS)
Empirical world
Conceptual world
Empirical world
Conceptual world
Service Industries
Lean Service System (LSS)
Operational definition
Measurement variable
Sustainability development
Strong linkages in existing literature
Weak (emerging) linkages in existing literature
Figure 7 Research scope for future sustainable model from the existing literature
-
Towards a sustainable development model
Both sustainability and lean service background the review conducted. Then, we try to conceptualize the model in three parts as follows:
-
Triggers for lean sustainability in service industries
-
Lean sustainability barriers and performance for adoption
-
Lean sustainable service
-
4.1.1 Triggers for lean sustainability in service industries
The triggers for the field and related activities were identified by the careful analysis articles and it was highlighted in Figure 8. The first point is to apply lean concepts or techniques in the service sector based on their expectations. Then, organisation has to evaluate their barriers or critical success factors through survey or suitable methods. Third point any organisation needs to integrate the sustainability principle along with lean system. A Service industry has to perform their sustainability activities through standard guidelines given by environmental (ISO 14001) and social standards (SA 8000).
Guidelines for deployment
Service organizations
Lean Practices
Economy Environment
Society
Service evaluation for barriers and critical success factors
Need to integrate sustainability with lean service
Figure 8. Motivations for lean sustainability in service industries
4.1. 2 Lean service barriers and performance
-
Generalizing model
-
Eco efficiency service (i.e.) lean green service, lean sustainable service
-
Performance metrics of lean service
-
Employees
Commitment
-
Learning environments
-
Standard models
-
Integrate with
appropriate tools
-
Need clear guidelines
-
Workers and managers commitment
-
Learning environments
Three aspects mentioned as barriers for implementing sustainability in service sectors such as higher costs, the complexity of the service, and lack of coordination. Before incorporating sustainability, the lean system has to be appropriately aligned with standard models, integrate with appropriate tools, need clear guidelines, worker and managers commitment, learning environments in the service organizations.
Barriers and Success factors
Lean Practices
Service industries
Figure 9. Lean sustainability barriers and success factors in service industries
4.1.3 Lean Service for sustainability
Sustainability is the term improved economic, social, and environmental standards. This paper has an extensive configuration of the triple ottom line of the framework with sustainability principles. The primary goal of this paper is to create a long-term framework model for service industries while also highlighting the market's competitive strategy.
Impacts and requirements as per the future demand
Lean Practices
Service industries
Sustainable Service
-
Increase relationship starting
from suppliers to customers
-
Open culture
-
Sustainable development (lean and green)
Customer
Figure 10. Lean sustainability for service industries
-
-
CONCLUSION
-
This paper highlights the SLR of lean applied in different service industries starting from January 2002 and ending to April 2019 in 137 top academic journals. First, this research provides recent patterns in LS literature – classifying research context, country wise. Second, we included conceptual, case study, theory, review, survey articles, to analyse different features and activities in lean service field. Third, we have depicted a clear and rigors lean sustainability model for service industries. Fourth, we have shown the importance of lean sustainability barriers and critical success factors while implementing in service industries. The limitation of this work we have excluded lean related studies and books and consideration of period study. The implication of this paper has a complete alignment with the triple bottom line framework of sustainability principles. In future scope, academicians and practitioners may apply this model to test empirically to check robustness & sustainability in different service industries.
REFERENCES PAPERS CONTAINED IN THE LITERATURE REVIEW
[1] Adebanjo, D., Laosirihongthong, T., & Samaranayake, P. (2016). Prioritizing lean supply chain management initiatives in healthcare service operations: a fuzzy AHP approach. Production Planning & Control The Management of Operations, 7287(April). https://doi.org/10.1080/09537287.2016.1164909. [2] Agarwal, S., Gallo, J. J., Parashar, A., Agarwal, K. K., Ellis, S. G., Khot, U. N., Samir, R. (2015). Impact of Lean Six Sigma Process Improvement Methodology on Cardiac Catheterization Laboratory Efficiency. Cardiovascular Revascularization Medicine. https://doi.org/10.1016/j.carrev.2015.12.011. [3] Al-Baik, O., & Miller, J. (2014). Waste identification and elimination in information technology organizations. Empirical Software Engineering, 19(6), 20192061. https://doi.org/10.1007/s10664-014-9302-3. [4] Al-Balushi, S., Sohal, A. S., Singh, P. J., Al Hajri, A., Al Farsi, Y. M., & Al Abri, R. (2014). Readiness factors for lean implementation in healthcare settings–a literature review. Journal of Health Organization and Management, 28(2), 135153. https://doi.org/10.1108/JHOM-04-2013-0083 [5] Alnajem, M., Garza-Reyes, J. A., & Antony, J. (2019). Lean readiness within emergency departments: a conceptual framework. Benchmarking. https://doi.org/10.1108/BIJ-10-2018-0337. [6] Alvarez, S., & Rubicon, A. (2015). Carbon footprint in Green Public Procurement: A case study in the services sector. Journal of Cleaner Production, 93, 159166. https://doi.org/10.1016/j.jclepro.2015.01.048. [7] Amaratunga, T., & Dobranowski, J. (2016). Systematic Review of the Application of Lean and Six Sigma Quality Improvement Methodologies in Radiology. Journal of the American College of Radiology, 13(9), 1088-1095.e7. https://doi.org/10.1016/j.jacr.2016.02.033. [8] Anand Gurumurthy;Rambabu Kodali. (2011). Design of lean manufacturing systems using value stream mapping with simulation. Journal of Manufacturing Technology Management, 5(3), 325344. https://doi.org/10.1108/17410381111126409. [9] Andrea L. Lorden, Yichen zhang, Szu-husuan lin, M. J. cote. (2014). Measures of Success: The Role of Human Factors in Lean Implementation in Healthcare. ASQ, 21(3). [10] Andres-Lopez, E., Gonzalez-Requena, I., & Sanz-Lobera, A. (2015). Lean Service: Reassessment of Lean Manufacturing for Service Activities.Procedia Engineering, 132, 2330. https://doi.org/10.1016/j.proeng.2015.12.463.
[11] Angel DÃaz, J. P. and L. S. (2012). Improving healthcare services: lean lessons from Aravind. Int. J. Business Excellence, 5(4). [12] Arfmann, D., & Barbe, G. T. (2014). The Value of Lean in the Service Sector: A Critique of Theory & Practice. International Journal of Business and Social Science, 5(2), 1825. [13] Aronsson, H., Abrahamsson, M., & Spens, K. (2011). Developing lean and agile health care supply chains. Supply Chain Management: An International Journal, 16(3), 176183. https://doi.org/10.1108/13598541111127164. [14] Arslankaya, S., & Atay, H. (2015). Maintenance management and lean manufacturing practices in a firm which produces dairy products. Procedia – Social and Behavioral Sciences, 207, 214224. https://doi.org/10.1016/j.sbspro.2015.10.090. [15] Asnan, R., Nordin, N., & Othman, S. N. (2015). Managing Change on Lean Implementation in Service Sector. Procedia – Social and Behavioral Sciences, 211, 313319. https://doi.org/10.1016/j.sbspro.2015.11.040. [16] Atkinson, P., & Mukaetova-ladinska, E. B. (2012). Nurse-led liaison mental health service for older adults: Service development using lean thinking methodology. Journal of Psychosomatic Research, 72(4), 328331. https://doi.org/10.1016/j.jpsychores.2011.11.018. [17] Atkinson, P., & Mukaetova-Ladinska, E. B. (2012). Nurse-led liaison mental health service for older adults: Service development using lean thinking methodology. Journal of Psychosomatic Research, 72(4), 328331. https://doi.org/10.1016/j.jpsychores.2011.11.018. [18] Babur, F., Cevikcan, E., & Bulent Durmusoglu, M. (2016). Axiomatic Design for Lean-Oriented Occupational Health and Safety Systems: An Application in Shipbuilding Industry. Computers & Industrial Engineering, 100, 88109. https://doi.org/10.1016/j.cie.2016.08.007. [19] Baril, C., Gascon, V., Miller, J., & Côté, N. (2016). Use of a discrete-event simulation in a Kaizen event: A case study in healthcare. European Journal of Operational Research, 249(1), 327339. https://doi.org/10.1016/j.ejor.2015.08.036. [20] Bateman, N., Hines, P., & Davidson, P. (2014). Wider applications for Lean: An examination of the fundamental principles within public sector organisations. International Journal of Productivity and Performance Management, 63(5), 550568. https://doi.org/10.1108/IJPPM-04-2013-0067. [21] Bertoni, A., Bertoni, M., Panarotto, M., Johansson, C., Larsson, T., Boucher, X., & Brissaud, D. (2015). Expanding Value Driven Design to meet Lean Product Service Development. Procedia CIRP, 30, 197202. https://doi.org/10.1016/j.procir.2015.02.153. [22] Bhatia, N., & Drew, J. (2007). Applying Lean production to the public sector. The Online Journal of McKinsey & Co, 15. Retrieved from http://executivesondemand.net/managementsourcing/images/stories/artigos_pdf/produtividade/Applying_lean_production_to_the_public_sector.pdf. [23] Bonome, L., Costa, M., & Filho, M. G. (2017). Lean healthcare: review , classification and analysis of literature. Production Planning & Control, 7287(March), 114. https://doi.org/10.1080/09537287.2016.1143131. [24] Brailsford, S., & Vissers, J. (2011). OR in healthcare: A European perspective. European Journal of Operational Research, 212(2), 223234. https://doi.org/10.1016/j.ejor.2010.10.026 [25] Caldera, H. T. S., Desha, C., & Dawes, L. (2017). Exploring the role of lean thinking in sustainable business practice: A systematic literature review.Journal of Cleaner Production, 167, 15461565. https://doi.org/10.1016/j.jclepro.2017.05.126.
[26] Carvalho, C.P. , Carvalho, D.S. and Silva, M. B. (2019). Value stream mapping as a lean manufacturing tool: A new account approach for cost saving in a textile company. International Journal of Production Management and Egineering, 6, 112. [27] Castaldi, M., Sugano, D., Kreps, K., Cassidy, A., & Kaban, J. (2016). Lean Philosophy and the Public Hospital Full. Perioperative Care and Operating Room Management. https://doi.org/10.1016/j.pcorm.2016.05.006. [28] Cavdur, F., Yagmahan, B., Oguzcan, E., & Arslan, N. (2018). Lean service system design: a simulation-based VSM case study. Business Process Management Journal, 14637154. https://doi.org/10.1108/BPMJ-02-2018-0057. [29] Chadha, R., Singh, A., & Kalra, J. (2012). Lean and queuing integration for the transformation of health care processes: A lean health care model.Clinical Governance: An International Journal, 17(3), 191199. https://doi.org/10.1108/14777271211251309.
[30] Chan, F. T. S., Chan, H. K., Lau, H. C. W., & Ip, R. W. L. (2006). An AHP approach in benchmarking logistics performance of the postal industry.Benchmarking: An International Journal, 13(6), 636661. https://doi.org/10.1108/14635770610709031.
[31] Chandrakumar, C., Gowrynathan, J., & Kulatunga, A. K. (2016). Incorporate LEAN and Green Concepts to Enhance the Productivity of Transshipment Terminal Operations. Procedia CIRP, 40, 301306. https://doi.org/10.1016/j.procir.2016.01.042. [32] Cherrafi, A., Elfezazi, S., Chiarini, A., Mokhlis, A., & Benhida, K. (2016). The integration of lean manufacturing, Six Sigma and sustainability: A literature review and future research directions for developing a specific model. Journal of Cleaner Production, 139, 828846. https://doi.org/10.1016/j.jclepro.2016.08.101. [33] Chowdhury, M. M. H., & Quaddus, M. A. (2016). A multi-phased QFD based optimization approach to sustainable service design. International Journal of Production Economics, 171, 165178. https://doi.org/10.1016/j.ijpe.2015.09.023. [34] Cirp, P., Authors, T., This, E. B. V, By-nc-nd, C. C., Systems, P., & Cycle, L. (2016). Lean and Green SC for PSS: The literature review and a Conceptual Framework. Procedia CIRP, 47, 162167. https://doi.org/10.1016/j.procir.2016.03.057. [35] Comm, C. L., & Mathaisel, D. F. X. (2005). An exploratory study of best lean sustainability practices in higher education. Quality Assurance in Education, 13(3), 227240. https://doi.org/10.1108/09684880510607963. [36] Costa, N., PatrÃcio, L., Morelli, N., & Magee, C. L. (2018). Bringing Service Design to manufacturing companies: Integrating PSS and Service Design approaches. Design Studies, 55, 112145. https://doi.org/10.1016/j.destud.2017.09.002. [37] Dannapfel, P., Poksinska, B., Thomas, K., & Dannapfel, P. (2014). Dissemination strategy for Lean thinking in health care. International Journal of Health Care Quality Assurance, 27(5), 391404. https://doi.org/10.1108/IJHCQA-01-2013-0001. [38] Dellve, L., Williamsson, A., Strömgren, M., Holden, R. J., & Eriksson, A. (2015). Lean implementation at different levels in Swedish hospitals: the importance for working conditions and stress. International Journal of Human Factors and Ergonomics, 3. https://doi.org/10.1504/IJHFE.2015.073001. [39] Desta, A., Asgedom, H. B., Gebresas, A., & Asheber, M. (2014). Analysis of Kaizen Implementation in Northern Ethiopia s Manufacturing Industries. International Journal of Business and Commerce, 3(8), 3957. [40] Dickson, E. W., Anguelov, Z., Vetterick, D., Eller, A., & Singh, S. (2009). Use of Lean in the Emergency Department: A Case Series of 4 Hospitals.Annals of Emergency Medicine, 54(4), 504510. https://doi.org/10.1016/j.annemergmed.2009.03.024.
[41] Dobrzykowski, D. D., McFadden, K. L., & Vonderembse, M. A. (2016). Examining pathways to safety and financial performance in hospitals: A study of lean in professional service operations. Journal of Operations Management, 4243, 3951. https://doi.org/10.1016/j.jom.2016.03.001 [42] Dominic, P. D. D., & Kamil, A. (2011). Lean principles in IT services: a case study on implementation and best practices Suresh Malladi. Int. J. Business Information Systems, 8(3), 247268. [43] Dos, H., Leite, R., & Vieira, G. E. (2015). Lean philosophy and its applications in the service industry: a review of the current knowledge.Production, (x), 529541. https://doi.org/10.1590/0103-6513.079012.
[44] Duarte, S., & Cruz-Machado, V. (2009). Modelling Lean and Green: a review from Business models. International Journal of Lean Six Sigma, 4(3), 123. https://doi.org/10.1108/IJLSS-05-2013-0030. [45] Dües, C. M., Tan, K. H., & Lim, M. (2013). Green as the new Lean: How to use Lean practices as a catalyst to greening your supply chain. Journal of Cleaner Production, 40, 93100. https://doi.org/10.1016/j.jclepro.2011.12.023. [46] E.V., G., Antony, J., & M, and V. S. (2019). Application of Lean Six Sigma in IT support services a case study services. The TQM Journal, 1754 2731. https://doi.org/10.1108/TQM-11-2018-0168. [47] Ebel, T., George, K., Larsen, E., Neal, E., Shah, K., Shi, D., Huijsman, R. (2011). Supply chain management in health services: an overview.Supply Chain Management: An International Journal, 16(3), 159165. https://doi.org/10.1038/31527.
[48] Efe, B., & Efe, Ö. F. (2016). An Application of Value Analysis for Lean Healthcare Management in an Emergency Department. International Journal of Computational Intelligence Systems, 9(4), 689697. https://doi.org/10.1080/18756891.2016.1204117. [49] Emiliani, M. L. (2004). Improving business school courses by applying lean principles and practices. Quality Assurance in Education, 12(4), 175 187. https://doi.org/10.1108/09684880410561596. [50] ERFAN, O. M. (2015). Management Beyond Manufacturing, A Holistic Approach. International Journal of Engineering & Technology, 3(1), 291. https://doi.org/10.1007/978-3-319-17410-5. [51] Fercoq, A., Lamouri, S., Carbone, V., Leli??vre, A., & Lemieux, A. A. (2013). Combining lean and green in manufacturing: A model of waste management. IFAC Proceedings Volumes (IFAC-PapersOnline). https://doi.org/10.3182/20130619-3-RU-3018.00164. [52] Gallear, W. H. A. M. D. (2016). Is lean service promising? A socio-technical perspective. International Journal of Operations & Production Management, 36(6). https://doi.org/10.1108/01443571111165839. [53] Garza-reyes, J. A., Villarreal, B., Kumar, V., & Molina, P. (2016). The Management of Operations Lean and green in the transport and logistics sector a case study of simultaneous deployment. Production Planning & Control The Management of Operations, 7287(June). https://doi.org/10.1080/09537287.2016.1197436. [54] Gopalakrishnan Narayanamurthy, Gurumurthy Anand, R. C. (2017). Applying lean thinking in an educational institute an action research.International Journal of Productivity and Performance Management. https://doi.org/10.1108/IJPPM-07-2016-0144.
[55] Hadid, W. (2014). The relationship between lean service , activity-based costing and business strategy and their impact on performance. The British Accounting Review, (April), 1244. https://doi.org/10.1016/j.bar.2017.03.001. [56] Hadid, W., & Afshin Mansouri, S. (2014). The lean-performance relationship in services: a theoretical model. International Journal of Operations & Production Management, 34(6). https://doi.org/10.1108/IJOPM-02-2013-0080. [57] Haque, B., Moore, M. J., & Lai, U. K. (2015). Measures of performance for lean product introduction in the aerospace industry. Journal of Engineering Manufacture, 218, 13871398. [58] Hartono, Y., Diar, R., & Jin, T. (2015). Enabler to successful implementation of lean supply chain in a book publisher. Procedia Manufacturing, 4(Iess), 192199. https://doi.org/10.1016/j.promfg.2015.11.031. [59] Hesse, M., & Rodrigue, J. P. (2004). The transport geography of logistics and freight distribution. Journal of Transport Geography, 12(3), 171184. https://doi.org/10.1016/j.jtrangeo.2003.12.004 [60] Heuvel, J. Van Den, Does, R. J. M M., & Koning, H. De. (2006a). Lean Six Sigma in a hospital. International Journal of Six Sigma and Competitive Advantage, 2(4), 377. https://doi.org/10.1504/IJSSCA.2006.011566. [61] Heuvel, J. Van Den, Does, R. J. M. M., & Koning, H. De. (2006b). Lean Six Sigma in a hospital. International Journal of Six Sigma and Competitive Advantage, 2(4), 377. https://doi.org/10.1504/IJSSCA.2006.011566. [62] Hicks, B. J. (2007). Lean information management: Understanding and eliminating waste. International Journal of Information Management, 27(4), 233249. https://doi.org/10.1016/j.ijinfomgt.2006.12.001. [63] Hofer, C., Eroglu, C., & Rossiter Hofer, A. (2012). The effect of lean production on financial performance: The mediating role of inventory leanness.International Journal of Production Economics, 138(2), 242253. https://doi.org/10.1016/j.ijpe.2012.03.025.
[64] Holden, R. J. (2011). Lean thinking in emergency departments: A critical review. Annals of Emergency Medicine, 57(3), 265278. https://doi.org/10.1016/j.annemergmed.2010.08.001. [65] Iberahim, H., Mazlinda, H., Marhainie, M. D., & Hidayah, A. N. (2016). Determinants of Sustainable Continuous Improvement Practices in Mail Processing Service Operations. Procedia – Social and Behavioral Sciences, 219, 330337. https://doi.org/10.1016/j.sbspro.2016.04.040. [66] Ingelsson, P., & MÃ¥rtensson, A. (2014). Measuring the importance and practices of Lean values. The TQM Journal, 26(5), 463474. https://doi.org/10.1108/TQM-07-2012-0047. [67] Jeyaraman, K., & Kee Teo, L. (2010). A conceptual framework for critical success factors of lean Six Sigma. International Journal of Lean Six Sigma, 1(3), 191215. https://doi.org/10.1108/20401461011075008. [68] Jnanesh, S. B. E. V. G. N. A. (2016). Productivity and performance improvement in the medical records department of a hospital An application of Lean Six Sigma Shreeranga. International Journal of Productivity and Performance Management. [69] Kanamori, S., Shibanuma, A., & Jimba, M. (2016). Applicability of the 5S management method for quality improvement in health-care facilities: a review. Tropical Medicine and Health, 44, 21. https://doi.org/10.1186/s41182-016-0022-9. [70] Khodambashi, S. (2014). Lean Analysis of an Intra-operating Management Process-identifying Opportunities for Improvement in Health Information Systems. Procedia Computer Science, 37(1877), 309316. https://doi.org/10.1016/j.procs.2014.08.046. [71] Kollberg, B., Dahlgaard, J. J., & Brehmer, P.-O. (2007). Measuring lean initiatives in health care services: issues and findings. International Journal of Productivity and Performance Management, 56(1), 724. https://doi.org/10.1108/17410400710717064. [72] Kostic-Nikoli, S., & Nikolic, I. (2013). Lean Six Sigma in Food Industry. International Journal of Basic & Applied Sciences, 13(06), 2130. [73] Krings, D., Levine, D., & Wall, T. (2006). The Use of Lean in Local Government. ICMA Public Management Magazine, Vol. 88, pp. 19. https://doi.org/10.1111/j.1467-9302.2006.00528. [74] Kumar, B. V. J. A. G.-R. V. (2016). A lean thinking and simulation-based approach for the improvement of routing operations. Industrial Management & Data Systems. [75] Kundu, G. K., & Manohar, M. (2016). Prioritizing lean practices for implementation in IT support services. Journal of Information and Knowledge Systems, 46(1), 104122. https://doi.org/10.1108/VJIKMS-12-2014-0064. [76] Kuo-chung, L. M. M. A. (2013). Using data mining technique to perform the performance assessment of lean service. Neural Comput & Applic, 14331445. https://doi.org/10.1007/s00521-012-0848. [77] Kupiainen, E., Mäntylä, M. V, & Itkonen, J. (2015). Using metrics in Agile and Lean Software Development A systematic literature review of industrial studies. Information and Software Technology, 62, 143163. https://doi.org/10.1016/j.infsof.2015.02.005. [78] Laganga, L. R. (2011). Lean service operations: Reflections and new directions for capacity expansion in outpatient clinics. Journal of Operations Management, 29(5), 422433. https://doi.org/10.1016/j.jom.2010.12.005. [79] Lameijer, B. A., Veen, D. T. J., Does, R. J. M. M., & Mast, J. D. E. (2016). Perceptions of Lean Six Sigma: A Multiple Case Study in the Financial Services Industry. ASQ, (2007). [80] Lawton, L. (2005). Lean Strategy Deployment Delivers Customer Satisfaction at GE Healthcare. Journal of Organizational Excellence, 24(4), 97102. https://doi.org/10.1002/joe.
[81] Lindsay, C., Commander, J., Findlay, P., Bennie, M., & Dunlop, E. (2014). Lean , new technologies and employment in public health services: employees experiences in the National Health Service. The International Journal of Human Resource Management, 25(21), 29412956. [82] M, V. S. (2016). Lean Six Sigma in Higher Education Institutions. International Journal of Quality and Service Sciences, 8(2). [83] Maleyeff, J. (2007). Improving Service Delivery in Government with Lean Six Sigma. IBM Center for The Business of Goverment, 48. [84] Malmbrandt, M., & Ã…hlström, P. (2013a). An instrument for assessing lean service adoption. International Journal of Operations & Production Management, 33(9), 11311165. https://doi.org/10.1108/IJOPM-05-2011-0175. [85] Malmbrandt, M., & Ã…hlström, P. (2013b). An instrument for assessing lean service adoption. International Journal of Operations & Production Management, 33(9), 11311165. https://doi.org/10.1108/IJOPM-05-2011-0175. [86] Manohar, G. K. K. M. (2016). Prioritizing lean practices for implementation in IT support services. VINE Journal of Information and Knowledge Management Systems. https://doi.org/10.1108/VJIKMS-12-2014-0064. [87] MartÃnez-Jurado, P. J., & Moyano-Fuentes, J. (2014). Lean management, supply chain management and sustainability: A literature review. Journal of Cleaner Production, 85, 134150. https://doi.org/10.1016/j.jclepro.2013.09.042. [88] Mason, S. E., Nicolay, C. R., & Darzi, A. (2014). The use of Lean and Six Sigma methodologies in surgery: A systematic review. The Surgeon, 13(2), 91100. https://doi.org/10.1016/j.surge.2014.08.002. [89] Matloub Hussain Mohsin Malik. (2016). Prioritizing Lean Management Practices in Public and Private Hospitals. Journal of Health Organization and Management. [90] Meade, D. J., Kumar, S., & Houshyar, A. (2006). Financial analysis of a theoretical lean manufacturing implementation using hybrid simulation modeling. Journal of Manufacturing Systems, 25(2), 137152. https://doi.org/10.1016/S0278-6125(06)80039-7. [91] MG.Kanakana. (2013). Lean in Service Industry. SAIIE25 Proceedings, (July), 5741. [92] Mo, J. P. T. (2009). The role of lean in the application of information technology to manufacturing. Computers in Industry, 60(4), 266276. https://doi.org/10.1016/j.compind.2009.01.002. [93] Modi, A., & Doyle, L. (2012). Applicability of lean-sigma in IT service delivery system. In IFAC Proceedings (Vol. 45). https://doi.org/10.3182/20120611-3-IE-4029.00030. [94] Moultrie, J., Sutcliffe, L., & Maier, A. (2016). A maturity grid assessment tool for environmentally conscious design in the medical device industry.Journal of Cleaner Production, 122, 252265. https://doi.org/10.1016/j.jclepro.2015.10.108.
[95] Narang, R. (2010). Measuring perceived quality of health care services in India. International Journal of Health Care Quality Assurance. https://doi.org/10.1108/09526861011017094. [96] Narayanamurthy, G., & Gurumurthy, A. (2016). Systemic leanness: An index for facilitating continuous improvement of lean implementation.Journal of Manufacturing Technology Management, 27(8), 10141053. https://doi.org/http://dx.doi.org/10.1108/JMTM-04-2016-0047.
[97] Niall Piercy Nick Rich. (2015). The relationship between lean operations and sustainable operations. International Journal of Operaions & Production Management, 35(2), 282315. [98] OLoughlin, C., & Coenders, G. (2010). Application of the European Customer Satisfaction Index to Postal Services. Structural Equation Models versus Partial Least Squares. TQM and Business Excellence, 15(910), 12311255. https://doi.org/10.1080/1478336042000255604. [99] Paixão, A. C., & Marlow, P. B. (2002). Strengths and weaknesses of short sea shipping. Marine Policy, 26(3), 167178. https://doi.org/10.1016/S0308-597X(01)00047-1. [100] Pär Ã…hlström. (2004). Lean service operations: translating lean production principles to service operations. Int. J. Services Technology and Management, 5(1994). [101] Perera, H. S. C. (2013). Developing a Performance Measurement System for Apparel Sector Lean Manufacturing Organizations in Sri Lanka. Sage. https://doi.org/10.1177/0972262913505371. [102] Pettersen, J. (2009). Defining lean production: some conceptual and practical issues. The TQM Journal, 21(2), 127142. https://doi.org/10.1108/17542730910938137. [103] Piercy, N., & Rich, N. (2008). Lean transformation in the pure service environment: the case of the call service centre. International Journal of Operations & Production Management. https://doi.org/10.1108/01443570910925361. [104] Piercy, N., & Rich, N. (2009a). High quality and low cost: the lean service centre. European Journal of Marketing, 43(11), 14771497. https://doi.org/10.1108/03090560910989993. [105] Piercy, N., & Rich, N. (2009b). High quality and low cost: the lean service centre. European Journal of Marketing, 43(11/12), 14771497. https://doi.org/10.1108/03090560910989993. [106] Procter, S., & Radnor, Z. (2014). Teamworking under Lean in UK public services: lean teams and team targets in Her Majesty s Revenue & Customs ( HMRC ). The International Journal of Human Resource Management, 25(21), 29782995. [107] Rad, A. M. M. (2005). A survey of total quality management in Iran: Barriers to successful implementation in health care organizations. Leadership in Health Services, 18(3), 1234. https://doi.org/10.1108/13660750510611189. [108] Radnor, Z., & Osborne, S. P. (2013). Lean: A failed theory for public services? Public Management Review, 15(April 2013), 265287. https://doi.org/10.1080/14719037.2012.748820 [109] Raju, V. R. S. R. (2016). A systematic literature review of Lean Six Sigma in different industries. International Journal of Lean Six Sigma. [110] Rane, J. R. J. S. S. M. S. B. (2014). Exploring barriers in lean implementation. International Journal of Lean Six Sigma, 5(2), 122148. https://doi.org/http://dx.doi.org/10.1108/MRR-09-2015-0216. [111] Rauch, E., Damian, A., Holzner, P., & Matt, D. T. (2016). Lean Hospitality – Application of Lean Management Methods in the Hotel Sector.Procedia CIRP, 41, 614619. https://doi.org/10.1016/j.procir.2016.01.019.
[112] Resta, B., Powell, D., Gaiardelli, P., & Dotti, S. (2015). Towards a framework for lean operations in product-oriented product service systems. CIRP Journal of Manufacturing Science and Technology, 9, 1222. https://doi.org/10.1016/j.cirpj.2015.01.008. [113] Robinson, S., Radnor, Z. J., Burgess, N., & Worthington, C. (2012). SimLean: Utilising simulation in the implementation of lean in healthcare.European Journal of Operational Research, 219(1), 188197. https://doi.org/10.1016/j.ejor.2011.12.029.
[114] Robinson, S. T. (2015). Lean Strategies in the Operating Room. Anesthesiology Clinics, 33(4), 713730. https://doi.org/10.1016/j.anclin.2015.07.010. [115] Robinson, S. T., & Kirsch, J. R. (2015). Lean Strategies in the Operating Room. Anesthesiology Clinics, 33(4), 713730. https://doi.org/10.1016/j.anclin.2015.07.010. [116] Ryan-Fogarty, Y., ORegan, B., & Moles, R. (2015). Greening healthcare: Systematic implementation of environmental programmes in a university teaching hospital. Journal of Cleaner Production, 126, 248259. https://doi.org/10.1016/j.jclepro.2016.03.079. [117] Saja Ahmed Albliwi Jiju Antony Norin Arshed Abhijeet Ghadge. (2017). Implementation of Lean Six Sigma in Saudi Arabian Organisations: Findings from a Survey. International Journal of Quality & Reliability Management, 34(4). https://doi.org/http://dx.doi.org/10.1108/MRR-09-2015- 0216. [118] Sassanelli, C., Pezzotta, G., Rossi, M., Terzi, S., & Cavalieri, S. (2015). Towards a lean Product Service Systems (PSS) design: State of the art, opportunities and challenges. Procedia CIRP, 30, 191196. https://doi.org/10.1016/j.procir.2015.02.123. [119] Shazali, N. A., Habidin, N. F., Ali, N., Khaidir, N. A., & Jamaludin, N. H. (2013). Lean Healthcare Practice and Healthcare Performance in Malaysian Healthcare Industry. International Journal of Scientific and Research Publications, 3(1), 15. [120] Shradha Gupta, M. S. & V. S. M. (2016). Lean Services: a Systematic Literature Review. International Journal of Productivity and Performance Management, 65(8), 10251056. [121] Staats, B. R., James, D., & Upton, D. M. (2011). Lean principles , learning , and knowledge work: Evidence from a software services provider.Journal of Operations Management, 29(5), 376390. https://doi.org/10.1016/j.jom.2010.11.005.
[122] Steinfeld, B., Scott, J., Vilander, G., Marx, L., Quirk, M., Lindberg, J., & Koerner, K. (2015). The Role of Lean Process Improvement in Implementation of Evidence-Based Practices in Behavioral Health Care. The Journal of Behavioral Health Services & Research, 42(4), 504519. https://doi.org/10.1007/s11414-013-9386-3. [123] Sua, M. F. (2012). Lean Service: A literature analysis and classification. TQM, 23(4), 359380. [124] Tagge, E. P., Lenart, J., Thirumoorthi, A. S., Garberoglio, C., & Mitchell, K. W. (2017). Improving Operating Room Efficiency in Academic Childrens Hospital Using Lean Six Sigma Methodology. Journal of Pediatric Surgery. https://doi.org/10.1016/j.jpedsurg.2017.03.035. [125] Tay, H. L. (2016). Lean Improvement Practices: Lessons from Healthcare Service Delivery Chains. IFAC-PapersOnLine, 49(12), 11581163. https://doi.org/10.1016/j.ifacol.2016.07.660. [126] Taylor, P., Roberto, J., Alves, X., & Alves, J. M. (2015). Production management model integrating the principles of lean manufacturing and sustainability supported by the cultural transformation of a company. International Journal of Production Research, (May), 3741. https://doi.org/10.1080/00207543.2015.1033032. [127] Thomas, A., Antony, J., Haven-tang, C., Francis, M., Fisher, R., Thomas, A., Sigma, S. (2017). Implementing Lean Six Sigma in to Curriculum Design and Delivery A Case Study in Higher Education. International Journal of Productivity and Performance Management. https://doi.org/10.1108/IJPPM-08-2016-0176. [128] Unger, S. R., Campion, N., Bilec, M. M., & Landis, A. E. (2016). Evaluating quantifiable metrics for hospital green checklists. Journal of Cleaner Production, 127, 134142. https://doi.org/10.1016/j.jclepro.2016.03.167. [129] Unutulmaz .O, O. D. . (2014). Total Quality Management & Business Excellence Lean production in healthcare: a simulation-based value stream mapping in the physical therapy and rehabilitation department of a public hospital. Total Quality Management & Business Excellence, (December), 3741. https://doi.org/10.1080/14783363.2014.945312. [130] Vadivel S.M., Sequeria A. H., Sunil Kumar Jauhar, Vimal Kumar (2019) Sustainable postal service design: Integrating quality function deployment from the customers perspective International Journal of System Assurance Engineering and Management, Springer publishers. [131] V, V., Suresh, M., & Aramvalarthan, S. (2016). Lean in service industries: A literature review. IOP Conference Series: Materials Science and Engineering, 149(1), 12008. https://doi.org/10.1088/1757-899X/149/1/012008. [132] Vlachos, I., & Bogdanovic, A. (2013). Lean thinking in the Europea hotel industry. Tourism Management, 36, 354363. https://doi.org/10.1016/j.tourman.2012.10.007. [133] Wang, F.-K., & Chen, K.-S. (2010). Applying Lean Six Sigma and TRIZ methodology in banking services. Total Quality Management & Business Excellence, 21(3), 301315. https://doi.org/10.1080/14783360903553248. [134] Wijewardana, R. L., & Rupasinghe, T. (2013). Applicability of Lean healthcare in Sri Lankan Healthcare Supply Chains. Int. J Sup. Chain. Mgt, 2(4), 4249. [135] Wnuk-pel, T. (2016). Management accounting systems and lean management: a service company perspective. Transformations in Business & Economics, 15(1), 5577. [136] Wong, W. P., Ignatius, J., & Soh, K. L. (2012). What is the leanness level of your organisation in lean transformation implementation? An integrated lean index using ANP approach. Production Planning & Control, 25(4), 273287. https://doi.org/10.1080/09537287.2012.674308. [137] Wood, L. C., Wang, C., Abdul-Rahman, H., & Jamal Abdul-Nasir, N. S. (2016). Green hospital design: Integrating quality function deployment and end-user demands. Journal of Cleaner Production, 112, 903913. https://doi.org/10.1016/j.jclepro.2015.08.101.FURTHER REFERENCES
[1] Alvarez R, Calvo R, Pena, Domingo R, (2008). Redesigning an assembly line through lean manufacturing tools. The International Journal of Advanced Manufacturing Technology, 43(9-10), pp.949958. [2] Bankole, O. O., Roy, R., Shehab, E., Cheruvu, K., & Johns, T. (2012). Productservice system affordability in defence and aerospace industries: state- of-the-art and current industrial practice. International Journal of Computer Integrated Manufacturing, 25(4-5), 398-416. [3] Dyllick, T., & Hockerts, K. (2002). Beyond the business case for corporate sustainability. Business strategy and the environment, 11(2), 130-141. [4] Gladwin, T. N., Krause, T. S., & Kennelly, J. J. (1995). Beyond ecoefficiency: Towards socially sustainable business. Sustainable Development, 3(1), 35-43. [5] Hunter, S.L., (2002). Ergonomic Evaluation of Manufacturing. , 20, pp.429444. [6] Kumar, V., & Wayne, W. (2006). Is Lean Necessarily Green?. In Proceedings of the 50th Annual Meeting of the ISSS-2006, Sonoma, CA, USA. [7] Lervik, J. E., Fahy, K. M., & Easterby-Smith, M. (2010). Temporal dynamics of situated learning in organizations. Management Learning, 41(3), 285- 301. [8] Mazzocato, P., Savage, C., Brommels, M., Aronsson, H., & Thor, J. (2010). Lean thinking in healthcare: a realist review of the literature. BMJ Quality& Safety, 19(5), 376-382.
[9] McCarty, T., Jordan, M., & Probst, D. (2011). Six Sigma for sustainability (Vol. 1). McGraw-Hill Professional. [10] Niepce, W., & Molleman, E. (1998). Work design issues in lean production from a sociotechnical systems perspective: Neo-Taylorism or the next step in sociotechnical design?. Human relations, 51(3), 259-287. [11] Ramachandiran.K, (2011), Indian postal history focus on Tamilnadu, Imayaa publication, India. [12] Stacey, P. K., & Tether, B. S. (2015). Designing emotion-centred product service systems: the case of a cancer care facility. Design Studies, 40, 85-118. [13] Sim, K. L., & Rogers, J. W. (2008). Implementing lean production systems: barriers to change. Management research news, 32(1), 37-49. [14] Unger, S. R., Campion, N., Bilec, M. M., & Landis, A. E. (2016). Evaluating quantifiable metrics for hospital green checklists. Journal of cleaner production, 127, 134-142. [15] Womack, J.P, Jones D.T, and Ross,D, The machine that changed the world:The story of lean production, Rawson Association,USA,(1990). [16] Zhou, B., (2012). Lean principles, practices, and impacts: a study on small and medium-sized enterprises (SMEs). Annals of Operations Research, 1-18.