
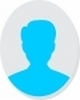
- Open Access
- Authors : Alexander Osayimwense Osadolor, Afeez Olamide Showole, Gideon Akwasi Asamoah, Tochukwu Judethaddeus Eze
- Paper ID : IJERTV13IS080020
- Volume & Issue : Volume 13, Issue 08 (August 2024)
- Published (First Online): 15-08-2024
- ISSN (Online) : 2278-0181
- Publisher Name : IJERT
- License:
This work is licensed under a Creative Commons Attribution 4.0 International License
Life Cycle Assessment of Polylactic Acid (PLA) in 3D Printing Applications: Evaluating Environmental Impacts and Energy Consumption
Alexander Osayimwense Osadolor, Afeez Olamide Showole, Gideon Akwasi Asamoah, Tochukwu Judethaddeus Eze
Students, School of Computing, Engineering & Digital Technologies, Sustainable Engineering System, Teesside University, Middlesbrough, Uk
Abstract
PLA is a biodegradable polymer derived from renewable resources, presents a sustainable alternative to conventional fossil-fuel-based plastics in various applications, including 3D printing. This study conducts a comprehensive LCA to evaluate the carbon footprint associated with the production, transportation, usage, and disposal of PLA lattice structures in 3D printing. Key stages analysed include computer-aided design, additive manufacturing using FDM technology, UV aging tests, and compression tests. Results indicate that accelerated UV test (333.87kg CO2e) significantly contributes to emissions due to its prolonged operational time. The study highlights the importance of waste management and recycling practices to minimize PLA's environmental footprint. The findings underscore the potential of PLA in reducing GHG emission and support the adoption of circular economy principles to enhance sustainability in manufacturing. Further research is recommended to explore lifecycle impacts and optimize disposal methods for bio plastics.
Graphical Abstract
Keywords: Polylactic Acid (PLA), Carbon Footprint, Life Cycle Assessment (LCA), 3D Printing, Biodegradable Plastics, Circular Economy
INTRODUCTION
Lactic acid is created through the fermentation of renewable materials like corn or sugarcane, and it can be converted into PLA, a biodegradable and renewable polymer. Due to PLA's environmental friendliness and ability to lessen the plastic industries negative environmental effects, it has drawn attention as a viable substitute for conventional polymers derived from fossil fuels [1]. When compared to plastics made from fossil fuels, the production of PLA can result in significant energy and greenhouse gas reductions. It is seen as a sustainable alternative to typical petroleum-based plastics because of its biodegradability and decreased greenhouse gas emissions [2]. Environmentally friendly bio plastics, such as PLA, offer a sustainable alternative to traditional
non-degradable plastics, aiming to reduce emissions of CO2. PLA is an eco-friendly bioplastic and commercially available with diverse applications, including packaging, biomedical, tissue engineering, and drug delivery. The research by Chow and Ng, 2022 [3] focus on the application of PLA for packaging, emphasizing its eco- friendliness and alignment with sustainable development goals. By implementing bioplastics like PLA in packaging, there is potential to manage resources efficiently through concepts like the circular economy, reducing energy consumption, and promoting the use of renewable resources.
When compared to conventional plastics, PLA has various advantages for the environment. It comes from sustainable and bio-based sources, like agriculture and marine items, which can aid in the industrial process's absorption of CO2 [1]. This means that PLA can contribute to reducing greenhouse gas emissions. Additionally, due to PLA's ability to decompose naturally, there are a variety of end-of-life solutions available, including industrial composting, chemical and mechanical recycling, landfilling, and recycling. Several LCA research have been conducted to assess the environmental footprint of PLA production. These studies consider various factors, including the production of feedstock, manufacturing processes, and end-of-life options. For example, a study conducted in Thailand provided cradle-to-gate information on the environmental impacts of PLA produced from sugarcane, highlighting the potential for further reducing environmental impacts through improvements in feedstock production and manufacturing processes [4].
PLA's ability to be processed using conventional plastic production processes like as injection moulding, extrusion, and 3D printing adds to its attractiveness to both producers and consumers [5]. In a different investigation, the environmental impact of single-use drinking cups composed of PET, PP, and PLA was observed and compared. According to the study, PLA cups performed better environmentally than PET cups but not PP cups [6].
The sustainability of PLA materials also requires consideration of their end-of-life options. PLA is biodegradable, decomposing into water and CO2 in a regulated composting setting in less than 90 days [7]. The challenges emerge with the disposal of PLA, because its total decomposition needs precise composting conditions, and inappropriate disposal may lead to gradual degradation and significant damage to ecosystems [8]. To address these concerns, a LCA was performed to analyse several disposal techniques for post-consumer PLA waste, including hydrolysis, alcoholises and incineration. Landfilling PLA can have a huge environmental impact. These materials contribute to the formation of leachate and gases, including methane and CO2, which are powerful GHG. However, landfills globally contribute to 20% of anthropogenic methane emissions [9].
This information gap impedes attempts to improve processes, decrease emissions and promote a circular economy. As a result, there is an urgent concern for comprehensive LCA to measure and analyse PLA carbon footprint, identify important sources to emissions and recommend methods for minimising its environmental effect. The purpose of this study is to conduct a Life Cycle Assessment of the carbon footprint of PLA Lattice Structure in 3D printing applications. This will entail assessing the environmental effect of PLA from manufacture to usage to end-of-life disposal. However, it is important to determine the energy consumption involved with 3D printing PLA lattice structures, including the power consumption of computers, printers, and test equipment.
LITERATURE REVIEW
The soaring worry about pollution of the environment have led to the search for more sustainable materials. Derived from renewable resources, PLA which a biodegradable material, has been identified as a more sustainable alternative to fossil-based plastics [10]. PLA has emerged as a promising bioplastic due to its biodegradability, renewability, and potential to reduce carbon emissions compared to conventional petroleum-based plastics. Evaluating the environmental impact of PLA throughout its life cycle is crucial for understanding its sustainability and identifying opportunities for improvement.
Morão and de Bie, 2019 [4] emphasized the potential of PLA for the mitigation of adverse impacts on the environments from the disposal of single-use polyethylene, further underlining its role in sustainable material choices. They supply information on the carbon footprint for the cradle to the gate of PLA manufactured commercially in Thailand, encompassing the water use, direct land use change, and the plausibility for the reduction of the impacts on the environment via enhancements of the feedstock production and the PLA manufacturing process. Their study highlighted how the different production stages contributed to the total GWP of PLA, including CO2 uptake in the time of sugarcane growth and PLA pellets production, and their assessment offers insights into the environmental implications of PLA production, particularly in terms of greenhouse gas emissions and energy use.
Choi, Yoo and Park, 2018 [11] examined the carbon footprint of packaging films, with a specific focus on multiple waste scenarios based on the South Korean database. Their research evaluates the global warming potential of packaging films that were manufactured from LDPE, PLA, and PLA/PBAT blends, emphasizing the scenarios from the waste treatment and employing a cradle to grave approach. Their research sheds light on the impact these packaging materials have on the environment in South Korea, indicating that the carbon footprint of films for packaging produced from LDPE, PLA and PLA/PBAT blends varies significantly based on the scenarios of their waste treatment. Their analysis of LDPE, PLA, and PLA/PBAT blends reveal varying results in terms of emissions
from greenhouse gases and values of global warming potential, highlighting the potential environmental advantages of bioplastics over traditional petroleum-based plastics.
Zhao et. al., 2022 [12] investigated the environmental implications of PLA plastic packaging products using LCA, focusing on Tianjin, China, as a case study. They identified stages such as raw material acquisition, product production, and end-of-life scenarios as significant contributors to environmental impacts, particularly in terms of GWP and ADP. Their findings underscored the need for optimizing energy consumption and improving material conversion rates during PLA production to effectively mitigate environmental burdens. Additionally, Zhao et al. highlighted the importance of sustainable sourcing practices and efficient waste management strategies to enhance the overall environmental performance of PLA packaging materials [12].
Benavides, Lee and Zarè-Mehrjerdi, 2020 [13] shed light on the potential roles of sustainable material choices and waste management strategies, as the environmental impact of plastic production and disposal has become a significant concern in the context of sustainability. They delve into the comparative LCA of the GHG emissions and energy use associated with PLA, bio-derived polyethylene, and fossil-derived polyethylene, and their study reveals that bio-derived polyethylene, synthesized from bio-based feedstock, presents a promising environmental profile, with reduced greenhouse gas emissions compared to fossil-derived polyethylene. Furthermore, they emphasize the significance of waste management strategies, such as composting for biodegradable plastics like PLA, to fully realize their environmental benefits.
Rezvani Ghomi et al., 2021 [14] explored PLA's potential as a low-carbon material through a detailed LCA approach. Their study assessed the entire life cycle of PLA, from raw material sourcing to end-of-life scenarios, aiming to quantify its environmental footprint comprehensively. The researchers emphasized PLA's benefits in reducing carbon emissions compared to traditional plastics but cautioned that effective waste management and recycling infrastructure are crucial for maximizing its environmental benefits. They advocated for continuous improvements in PLA production technologies and recycling systems to support its sustainable use in various applications, including packaging, textiles, and biomedical fields [14].
Schwarz et al., 2023 [15] conducted a comprehensive LCA of advanced grade PLA products, focusing on innovative end-of-life treatments through depolymerisation. Their study highlighted the importance of advanced recycling methods in minimizing environmental impacts, particularly by reducing greenhouse gas emissions associated with traditional disposal methods like incineration or landfilling [15]. The researchers emphasized the significance of closed-loop recycling systems that can effectively recover high-value components from PLA products at the end of their life, thus contributing to a circular economy model.
METHODOLOGY
Figure 1: Process from the PLA acquisition to testing of the lattice structure
The carbon footprint of the design and impact of ultraviolet aging on PLA Lattice Structures carried out by [16] was determined with every device and stage of the process in the laboratory setup accounted for alongside the acquisition of the PLA as shown in figure1. The total operating times and total energy consumptions were determined at every stage using equation1, and the emission factors were used to calculate the associated CO2 emissions using equation2 and equation3.
The total energy consumption:
() = () × () (1)
1000
The carbon footprint for electricity usage:
(kg CO2e) = (kWh) × Emission factor(kg CO2e per kWh) (2) The carbon footprint for materials:
(kg CO2e) = (tonnes) × Emission factor(kg CO2e per tonne) (3)
Data collection and analysis of the materials and devices Computer Aided Design
The computer aided design of the lattice structure as shown in figure2 using Siemens NX on a HP EliteOne 800 G6 24 All-in-One PC, with the time accounting for the powering of the computer and launching the software.
-
Power consumption: 280 W
-
Operating time: 1 hour
-
The total energy consumption (kWh) = 0.28 kWh
Figure 2: Designed 3D Lattice structure ready for printing (Osadolor et. al., 2024)
3D Printing
The additive manufacturing of the 12 PLA lattice structures as shown in figure3 with the use of Fused Deposition Modeling (FDM) Technology of the Stratasys F170 3D Printer to print 12 specimens of
39.93grams each, which is a total of 479.16grams.
-
Power rating: 1.61 kW
-
Time to print 1 specimen = 2 hours 31 minutes = 2.5167 hours
-
Energy consumption per lattice structure: 4.052 kWh
-
Time to print 12 specimens = 30.2004 hours
-
Total energy consumption for 12 lattice structures: 48.62 kWh
Figure 3: A 3D printed lattice structure (Osadolor et. al., 2024)
The manually removed infills from the 12 printed specimens as shown in figure4, which were disposed for landfill.
-
Infill PLA mass of 1 specimen = 13.72 grams
-
Total infill PLA mass from 12 lattice structures = 164.64 grams
Figure 4: Infill from the printed lattice structure (Osadolor et. al., 2024)
Aging test
The simulation of real-world conditions in a short time via the exposure to UV radiation using the Biuged BGD 852 Bench UV light Accelerated Aging weathering tester. The total run time was for a total of 8 weeks; 1344 hours, with the first set removed after 4 weeks and the second set removed after 6 weeks.
-
Power rating of the UV aging tester: 1.2 kW
-
Operating time: 8 weeks = 1344 hours
-
Total Energy Consumption: 1612.80 kWh
Compression tests
Table1 shows the time in seconds for the compression tests on all the specimens using a 3367 dual column tabletop testing system.
Table 1: Compression time for the specimens
Compression time (seconds)
Specimen
control
4 weeks
6 weeks
8 weeks
1
17
22
21
20
2
20
23
17
19
3
22
22
23
20
-
Power rating of the compression machine: 0.6 kW
-
Operating time: 246 seconds = 0.06833 hours
-
Total Operating Time: 0.06833 hours
-
Total Energy Consumption: 0.04100 kWh
RESULT AND DISCUSSION
Environmental impact of manuacturing of PLA
The carbon footprint of PLA produced from renewable resources, such as sugarcane or corn, is generally lower than that of conventional plastics. Studies indicate that the GWP of PLA produced from sugarcane in Thailand can be around 500 grams of CO2 per kilogram of PLA [4], [17], [18], [19]. The total mass of PLA used for this work was 479.16 grams, which indicates that the carbon footprint for its production was about 0.2396 kg of CO2.
Environmental impact of transporting the PLA
The transportation of goods is a crucial aspect of global trade and commerce, facilitating the movement of products from manufacturers to consumers. Air transportation is the fastest but also the most carbon-intensive mode of transporting goods, and is typically used for high-value, time-sensitive goods that need to be delivered quickly. Road transportation, particularly by bus, is a widely used method for moving goods over short to medium distances. It offers flexibility in terms of routes and schedules, making it a popular choice for businesses within a locality. Rail transportation is often considered a more environmentally friendly alternative to road transportation. It is particularly effective for moving large quantities of goods over long distances, and the efficiency of rail transport stems from its ability to move a substantial amount of freight with relatively lower energy consumption per ton-kilometer, thereby having a lower carbon footprint than vans or buses. The difference in their carbon footprints highlights the potential environmental benefits of shifting more freight transportation to these modes. By doing so, businesses and policymakers can reduce the overall carbon footprint associated with the logistics sector. Shipping the PLA from the Netherlands to Middlesbrough in the UK will entail the mixed use of a freight train and a van. An average freight train with capacity of 16800 tonnes for a distance of about 960 km, having an emission factor: 0.02779 kg CO2e per tonne.km [20]. For a distance of about 0.6437km, an average van with a capacity of 3.5 tonnes has an emission factor of 0.61643 kg CO2e per tonne.km [20]. From equation2, the freight train's carbon footprint is 0.012796kg CO2e, and the van's carbon footprint is 0.00019048kg CO2e, which gives a total Carbon Footprint 0.01299 kg CO2e for its transportation.
Environmental impact of testing the PLA lattice structures
The HP EliteOne 800 G6 24 All-in-One PC, the Stratasys F170 3D Printer, the Biuged BGD 852 Bench UV light Accelerated Aging weathering tester and the 3367 dual column tabletop testing system were all powered by electricity in the United Kingdom (UK). The electricity emission factor in the United Kingdom is 0.20705 kg CO2 per kWh [20], and figure5 shows the downward trend of greenhouse gas emissions from electricity generation in the UK over the years. The infills from the printed lattice structures were disposed for landfill, and the waste emission factor for plastics for landfill is 8.88386 kg CO2e per tonne [20].
Figure 5: UK greenhouse gas emissions from electricity generation over the years (Circular Ecology, 2023)
The carbon footprint of the items of equipment were calculated using euation2 and the carbon footprint for the infills as waste was calculated using euation3.
The carbon footprint for each stage:
-
The HP EliteOne 800 G6 24 All-in-One PC had a carbon footprint of 0.058kg CO2e
-
The FDM 3D Printer had a carbon footprint of 10.07kg CO2
-
The disposed PLA material for landfill had a carbon footprint of 0.001462kg CO2
-
The Biuged BGD 852 Bench UV light Accelerated Aging weathering tester had a carbon footprint of
333.87kg CO2
Item
Emission
Manufacture of the PLA
0.2396kg CO2e
Transportation of the PLA
0.01299kg CO2e
HP EliteOne 800 G6 24 All-in-One PC
0.058kg CO2e
Stratasys F170 3D Printer
10.07kg CO2e
Biuged BGD 852 Bench UV light Accelerated Aging weathering tester
333.87kg CO2e
3367 Dual Column Tabletop Testing System
0.00849kg CO2e
PLA infill disposal
0.001462kg CO2e
Total emission
344.260542kg CO2e
-
The 3367 Dual Column Tabletop Testing System had a carbon footprint of 0.00849kg CO2 Table 2: Environmental impact of testing 3D printed PLA lattice structures
Figure 6: Picture of the environmental impacts of the different stages
Emission Breakdown
The total emissions for testing 479.16 grams of PLA amount to 344.26 kg CO2e as shown in table112, which represents the cumulative environmental impact of the manufacturing, transportation, testing and disposal processes associated with these items. As shown in figure6, the Biuged BGD 852 Bench UV Light Accelerated Aging Weathering Tester has the highest emissions at 333.87 kg CO2e, accounting for approximately 97% of the total emissions. This piece of equipment has a significant environmental footprint, due to its energy consumption, because it was left to run for 8 weeks uninterrupted. The Stratasys F170 3D Printer, with emissions of 10.07 kg CO2e, also contributes a notable amount to the total. Its emissions is attributed to its operational time of 30.2004 hours. Manufacturing PLA: Emitting 0.2396 kg CO2e, the carbon footprint for the manufacturing process is relatively low in comparison to the total emission. The HP EliteOne 800 G6 24 All-in-One PC has emissions of
0.058 kg CO2e, which is quite low, suggesting efficient energy use. At 0.01299 kg CO2e, transportation of the PLA is one of the lowest emissions contributions, indicating that the mode of transportation has a minimal impact relative to the manufacturing. With emissions of 0.00849 kg CO2e for the 3367 Dual Column Tabletop Testing System, and 0.001462 kg CO2e for the PLA Infill Disposal, they contributed the least impacts to the environment with negligible emissions.
End-of-Life Considerations
The resulting carbon footprint was approximately 0.00146 kg CO2e. This relatively low figure reflects the small quantity of PLA waste, yet it underscores the importance of considering end-of-life disposal impacts in sustainability assessments. When comparing PLA to other bioplastics and traditional plastics, it is essential to consider the entire life cycle. Some studies suggest that while PLA has a lower carbon footprint, the overall environmental impact can vary based on specific production methods and waste management practices, such as the PLA manufactured from corn having a carbon footprint of 1.8Kg of CO2 per Kg of PLA [21]. As the environmental impact of PLA also depends on how it is disposed of, composting and recycling can mitigate its carbon footprint, while landfill disposal may lead to higher emissions due to anaerobic degradation [22].
Developing facilities specifically designed to handle PLA is crucial, as these facilities can ensure that PLA is processed correctly, as it requires different conditions compared to traditional plastics. The UK government is working on introducing consistent recycling collections for all households and businesses, as this would help ensure that PLA products are collected separately from general waste, making it easier to process them appropriately [23]. Investing in research to develop new technologies for recycling PLA can enhance the efficiency and effectiveness of the recycling process. This includes exploring chemical recycling methods that can break down PLA into its monomers for reuse [24]. Implementing regulations that specifically address the recycling of biodegradable plastics like PLA can help create a structured appoach to managing these materials, reduce their carbon footprint and achieve a circular economy [25].
Future Research
Further research is needed to explore the lifecycle impacts of PLA in various applications. Comparative studies with other biodegradable and non-biodegradable materials can provide insights into the most sustainable options for 3D printing. Additionally, investigating the effects of different environmental conditions on PLA degradation can inform better material design and application strategies.
CONCLUSION
This study highlights the potential of PLA as a sustainable material for 3D printing, emphasizing the importance of considering both production and disposal impacts. By optimizing design, printing, and disposal processes, and continuing to innovate in material science, we can move towards more sustainable manufacturing practices. The carbon footprint results for various technologies serve as a critical reminder of the environmental impacts associated with production and consumption. By adopting circular economy principles, businesses can not only reduce their carbon emissions but also contribute to a more sustainable and resilient economic model. This shift is essential for addressing the pressing challenges of climate change and resource depletion, ultimately leading to a healthier planet and society. The analysis of the carbon footprints associated with the HP EliteOne 800 G6, FDM 3D Printer, UV Aging Tester, 3367 Dual Column Tabletop Testing System, and PLA material disposal reveals a diverse range of emissions that reflect the varying energy requirements and efficiencies of each technology. While some devices demonstrate minimal carbon footprints, others, particularly those requiring significant energy for operation, pose challenges to sustainability efforts. Organizations should utilize this information to make informed decisions about technology acquisition, energy sourcing, and operational practices. By prioritizing energy efficiency and exploring renewable energy options, businesses can effectively contribute to reducing their carbon footprint and promoting a more sustainable future.
Abbreviation
Polylactic Acid |
PLA |
Life Cycle Assessment |
LCA |
polyethylene terephthalate |
PET |
polypropylene |
PP |
Greenhouse gases |
GHG |
Global warming potential |
GWP |
Low-Density Polyethylene |
LDPE |
Polybutylene Adipate Terephthalate |
PBAT |
Global warming potential |
GWP |
Abiotic depletion potential |
ADP |
REFERENCE
-
Rezvani Ghomi, E., Khosravi, F., Saedi Ardahaei, A., Dai, Y., Neisiany, R.E., Foroughi, F., Wu, M., Das, O. and Ramakrishna, S., 2021. The life cycle assessment for polylactic acid (PLA) to make it a low-carbon material. Polymers, 13(11), p.1854.
-
TWI. What is PLA? (Everything You Need To Know). www.twi-global.com. 2023. Available from: https://www.twi-global.com/technical- knowledge/faqs/what-is-pla.
-
Chow, W.S. and Ng, W.K. (2022) 'Poly(lactic acid) for Sustainable Packaging Applications,' in Elsevier eBooks, pp. 330338. https://doi.org/10.1016/b978-0-12-820352-1.00243-1.
-
Morão, A. and De Bie, F., 2019. Life cycle impact assessment of polylactic acid (PLA) produced from sugarcane in Thailand. Journal of Polymers and the Environment, 27(11), pp.2523-2539.
-
Mohammad Raquibul Hasan, Davies IJ, Alokesh Pramanik, John M, Biswas WK. Potential of Recycled PLA in 3D Printing: A Review. Sustainable manufacturing and service economics. 2024 Mar 1;100020:1000200.
-
Moretti, C., Hamelin, L., Jakobsen, L.G., Junginger, M.H., Steingrimsdottir, M.M., Høibye, L. and Shen, L., 2021. Cradle-to-grave life cycle assessment of single-use cups made from PLA, PP and PET. Resources, Conservation and Recycling, 169, p.105508.
-
Toor, R., 2019-. How Sustainable is PLA 3D Printer Filament? https://www.filamentive.com/how-sustainable-is-pla/.
-
Singhvi, M. and Gokhale, D. (2013) 'Biomass to biodegradable polymer (PLA),' RSC Advances, 3(33), p. 13558. https://doi.org/10.1039/c3ra41592a.
-
Kumar, N.C. (2020) 'Landfill emissions and their impact on the environment,' International Journal of Engineering Research And, V9(08). https://doi.org/10.17577/ijertv9is080187.
-
Fonseca, A., Ramalho, E., Gouveia, A., Figueiredo, F. and Nunes, J. (2023). Life Cycle Assessment of PLA Products: A Systematic Literature Review. Sustainability, [online] 15(16), p.12470. doi:https://doi.org/10.3390/su151612470.
-
Choi, B., Yoo, S. and Park, S. (2018). Carbon Footprint of Packaging Films Made from LDPE, PLA, and PLA/PBAT Blends in South Korea. Sustainability, 10(7), p.2369. doi:https://doi.org/10.3390/su10072369.
-
Zhao, M., Yang, Z., Zhao, J., Wang, Y., Ma, X., Guo, J. (2022). Life Cycle Assessment of Biodegradable Polylactic Acid (PLA) Plastic Packaging ProductsTaking Tianjin, China as a Case Study. Journal of Resources and Ecology, 13(3), 428-441. doi: 10.5814/j.issn.1674- 764x.2022.03.008.
-
Benavides, P.T., Lee, U. and Zarè-Mehrjerdi, O. (2020). Life cycle greenhouse gas emissions and energy use of polylactic acid, bio-derived polyethylene, and fossil-derived polyethylene. Journal of Cleaner Production, 277(124010), p.124010. doi:https://doi.org/10.1016/j.jclepro.2020.124010.
-
Rezvani Ghomi, E.R., Khosravi, F., Saedi Ardahaei, A.S., Dai, Y., Neisiany, R.E., Foroughi, F., Wu, M., Das, O. and Ramakrishna, S. (2021). The Life Cycle Assessment for Polylactic Acid (PLA) to Make It a Low-Carbon Material. Polymers, [online] 13(11), p.1854. doi:https://doi.org/10.3390/polym13111854.
-
Schwarz, A., [et al.]. (2023). Life Cycle Assessment of Advanced Grade PLA Product with Novel End-of-Life Treatment through Depolymerization. Science of the Total Environment, 905, 167020. doi: 10.1016/j.scitotenv.2023.167020
-
Osadolor, A.O., Showole, A.O., Eze, T.J., Ajayi, V. and Owulo, R.O. (2024). Design and Analysis of the Impact of Ultraviolet Aging on the Mechanical Properties and Durability of PLA Lattice Structures. Journal of Materials Science Research and Reviews, [online] 7(2), pp.287301. Available at: https://journaljmsrr.com/index.php/JMSRR/article/view/332 [Accessed 27 Jul. 2024].
-
Packaging Europe (2019). Low carbon footprint of PLA confirmed by peer reviewed Life Cycle Assessment. [online] Packaging Europe. Available at: https://packagingeurope.com/low-carbon-footprint-of-pla-confirmed-by-peer-reviewed-life-cycle-assessment/4207.article.
-
TotalEnergies Corbion (2019). TotalEnergies Corbion. [online] www.totalenergies-corbion.com. Available at: https://www.totalenergies- corbion.com/news/low-carbon-footprint-of-pla-confirmed-by-peer-reviewed-life-cycle-assessment/.
-
Menglei, Z., Zeng, Y., Jingnan, Z., Wang, Y., Xiaolei, M. and Jian, G. (2022). Life Cycle Assessment of Biodegradable Polylactic Acid (PLA) Plastic Packaging Products-Taking Tianjin, China as a Case Study. Journal of Resources and Ecology, 13(3). doi:https://doi.org/10.5814/j.issn.1674-764x.2022.03.008.
-
GOV.UK (2024). Greenhouse gas reporting: conversion factors 2024. [online] Department for Energy Security and Net Zero. Available at: https://www.gov.uk/gvernment/publications/greenhouse-gas-reporting-conversion-factors-2024.
-
Benavides, P., Zare`-Mehrjerdi, O. and Lee, U. (2019). LIFE CYCLE INVENTORY FOR POLYLACTIC ACID PRODUCTION in GREET ® 2019.
-
BioSpherePlastic (2012). Polylactic Acid: BioPlastic Creates more Co2 Equivalent than Landfills. [online] BioSphere Plastic. Available at: https://biosphereplastic.com/information/polylactic-acid-bioplastic-creates-more-co2-equivalent-than-landfills.
-
gov.uk (2021). Landmark reforms to boost recycling and fight plastic pollution. gov.uk. [online] 24 Mar. Available at: https://www.gov.uk/government/news/landmark-reforms-to-boost-recycling-and-fight-plastic-pollution.
-
British Plastics Federation (2018). Plastic Recycling. [online] Bpf.co.uk. Available at: https://www.bpf.co.uk/sustainability/Plastics_Recycling.aspx.
-
Circular Ecology (2023). Defra 2023 Emissions Factors Released. [online] Circular Ecology. Available at: https://circularecology.com/news/defra-2023-emissions-factors-released.