
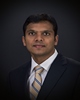
- Open Access
- Authors : Aravind Potturu
- Paper ID : IJERTV9IS110144
- Volume & Issue : Volume 09, Issue 11 (November 2020)
- Published (First Online): 25-11-2020
- ISSN (Online) : 2278-0181
- Publisher Name : IJERT
- License:
This work is licensed under a Creative Commons Attribution 4.0 International License
Machine Learning Applications for Industry 4.0 Predictive Maintenance and High Conformity Quality Control
Next >
Aravind Potturua*
aEnterprise Business Architect, Smart Factory, Enterprise Performance, Deloitte LLP,
USA
Abstract:- Industry 4.0 is empowering manufacturing plants transform into Smart Factories by leveraging intelligent technologies. Artificial Intelligence and Machine Learning combined with IoT are the key enablers of this digital manufacturing transformation. This study outlines how Artificial Intelligence powered maintenance and quality control can help manufacturers to achieve operational efficiency.
keywords: Artificial Intelligence; Machine Learning; Industry 4.0; Predictive Maintenance; Quality Control; Computer Vision
I. INTRODUCTION
The term Artificial Intelligence (AI) is coined to any form of intelligence that is exhibited by non-humans. Nowadays, such form of intelligence usually captured in computer software can be obtained by utilizing Machine Learning (ML) algorithms. These algorithms are capable of processing large amounts of data, resulting in the detection of relevant patterns and insights which reside within the data. Given enough qualitative data, these algorithms can be trained to perform specific tasks that could previously only be carried out with the help of human intelligence.
Many industries have started to adopt intelligent algorithms to automate and enhance prediction making processes for a wide range of business applications. In the manufacturing industry for example such intelligent algorithms may provide additional value in a businesses maintenance and quality control strategy. This paper will provide a series of technical implementations regarding the implementation of machine learning software for predictive maintenance and quality control support within the manufacturing industry.
II. PREDICTIVE MAINTENANCE
To reduce mechanical component failure, most manufacturing companies rely on the concept of preventive maintenance [1]: maintenance programs including routine work, component change, reparation of detected components, and regular inspections after a pre-defined duration of operations. However, classic maintenance schedules like preventive maintenance have some inherent shortcomings:
Over-Maintenance: More than often, the inspected component is still in perfect condition, resulting in unnecessary maintenance procedures and component handling.
Reduced Manufacturing Capacity and Revenue Loss: Preventive maintenance requires manufacturing machines to be taken out of service, irrevocably resulting in reduced manufacturing capacity and revenue losses.
Incidental Damages: Regular maintenance requires invasive actions – such as disconnecting electric cables, loosening and tightening bolts, and removing mechanical components – which may cause incidental damaging of secondary components.
However, recent technological advances such as Machine Learning have provided manufacturing companies with a powerful tool, allowing them to implement innovative maintenance strategies such as predictive maintenance [1].
In predictive maintenance, advanced statistics and predictive models are used to estimate the condition and possibly predict the future failure of mechanical components. This poses advantages when compared to classic preventive maintenance schemes:
Cost Reduction: Mechanical components are only repaired or replaced when indicated by the algorithm. This reduces both the labor cost (maintenance staff) and the cost required for spare parts (inventory cost and actual component cost).
Reduction in Secondary Damages: By identifying potential component failures, manufacturing companies can reduce the financial losses incurred by secondary damages when component failure occurs. This because failed components have the tendency to damage other – usually nearby components, resulting in an aggregated cost in the case of component failure.
Reduced Outage Time: Predictive maintenance results in a reduced number of maintenance interventions, thereby reducing the outage time and increasing the manufacturing capacity. The expected annual benefits ($ per year), can be estimated by:
P(s) (f s
With the total annual benefits, P(s) the probability of successful of early component failure detection, f the benefit due to the decrease in outage time, and s the benefit due to forced outage time becoming scheduled outage time.
In what follows, I will discuss the concept of Survival analysis
which is a commonly used machine learning tool that allows the prediction of mechanical component degradation and component failure, and therefore the implementation of data- driven maintenance schemes.
Survival Analysis for component failure detection
Survival Analysis is the branch within statistical modeling and machine learning which unlike regular machine learning models that focus on regression and classification problems aims at predicting the expected duration until the occurrence of a certain event of interest.
Historically, survival analysis has been used extensively within the field of medicine to obtain insights into which physiological factors influence the lifespan of certain populations. Due to improved digital storage capacity and increased efforts in keeping detailed logs about executed maintenance and component wear survival analysis has become increasingly more popular for determining the time until mechanical component failure within high maintenance industries.
In this way survival analysis commonly referred to as reliability analysis or reliability theory when dealing with mechanical components provides valuable insights with respect to:
The components survival function: the probability of a mechanical component failure after time (or equivalently, the probability of component survival until time ), which can be denoted by the following function:
()component p ( > )
Mathematically, this function represents a curve starting at p =
1 (i.e., 100% chance of survival at time = 0) which approaches zero probability at = .
Variables of interest and Covariate relations: In the context of survival analysis, it is possible to detect the variables of interest i.e. the variables which have a significant influence on the survival function and therefore the time until failure of the mechanical component.
In addition, survival analysis allows the observation of interactions between different covariates, possibly resulting in valuable insights regarding perfect storm-scenarios in which the aggregation of a series of harmless variable conditions may lead to critical component failure.
In what follows, I present a step-by-step framework which allows the creation of a data-driven model to aid manufacturing companies in implementing a predictive maintenance strategy for mechanical systems [2][3]:
Step 1: Data collectionStep 2: Determine degradation typeStep 3: Machine Learning regression modelStep 4: Use obtained models for inferenceStep 5: Use Inference results for Predictive Maintenance Decision MakingStep 6: Iterate, Update Data, and Improve Inference Convolutional Layers Pooling Layers Fully Connected Layers Network Output Step 1: Data collection Step 2: Determine Network Architecture and Model Training Step 3: Model Implementation (test phase) Step 4: Model Implementation and Iteration
Next >