
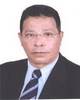
- Open Access
- Authors : Sobhy M. Ghoneam , Ahmed G. Embaby , Ebtesam A. Elhadhody, M. A. Asy
- Paper ID : IJERTV10IS120073
- Volume & Issue : Volume 10, Issue 12 (December 2021)
- Published (First Online): 20-12-2021
- ISSN (Online) : 2278-0181
- Publisher Name : IJERT
- License:
This work is licensed under a Creative Commons Attribution 4.0 International License
Magnetic Analysis of Eight Pole Active Magnetic Bearing using ANSYS Maxwell
Sobhy M. Ghoneam
Department of Production Engineering and Mechanical
Design, Faculty of Engineering, Shebin El-kom, Egypt
Ahmed G. Embaby
Department of Production Engineering and Mechanical
Design, Faculty of Engineering, Shebin El-kom, Egypt
M. A. Asy
Department of Production Engineering and Mechanical
Design, Faculty of Engineering, Shebin El-kom, Egypt
Ebtesam A. Elhadhody
Department of Production Engineering and Mechanical
Design, Faculty of Engineering, Shebin El-kom, Egypt
Abstract The active magnetic bearing (AMB) is an essential component of any industrial rotating machine. The magnetic analysis for the eight pole active magnetic bearing (AMB) is presented in this paper. The intended AMB has four pairs of electromagnets with four coils and a rotor that must be levitated. A 3D simulation of the model is analysed using ANSYS (version-16.0) base software. Finite element analysis is utilized in this study to determine various magnetic properties like magnetic flux density, magnetic flux density vector plot, magnetic flux, and vector plot of magnetic flux. The effect of different magnetic properties by changing current, air gap, and number of turns has been studied.
Keywords (Finite element analysis (FEA); ANSYS; Magnetic field; Magnetic flux; Magnetic flux density; Active magnetic bearing (AMB))
I. INTRODUCTION
The active magnetic bearing (AMB) is an essential component of any industrial rotating machine. A magnetic bearing is a system that utilizing magnetic force to lift a rotor without contacting the stator mechanically or physically. passive magnetic bearing and Active magnetic bearing are the two types of magnetic bearing systems. The magnetic force produced to lift an object in the case of passive magnetic bearing is unstable, and as a result, research towards active magnetic bearing is growing [1].
A rotor is floated in the distance (air gap) between the stator and the rotor without contacting the stator mechanically or physically in an AMB system by controlled current streaming through the stator winding. In many fields of engineering, an AMB system has several advantages over a conventional bearing system. There are many advantages to using AMB over conventional bearings. To support bearing loads, conventional bearings utilize fluid films or other physical contact forces, whereas active magnetic bearings use magnetic forces generated by feedback controllers to levitate the rotor within the magnetic field. AMBs have several advantages, including contact free operation, run without lubrication, no wear, high speed, decreased vibration, low bearing losses, lower maintenance costs, and a longer life span [1, 2, 3].
The importance of numerical simulations has grown dramatically in all scientific and engineering fields. AMB can be modelled and simulated using a variety of numerical
methods, including the finite element method, the finite difference method, the finite volume method, and the boundary element method, among others. The finite element method (FEM) is a very popular method for modelling and analysing the electromagnetic field in an AMB system [2, 3]. FEM analysis is conducted in 3 steps: preprocessing, processing, and postprocessing. Meshing, material imposition, defining boundary conditions, and providing excitation are all part of the preprocessing step. The processing step consists of solution equations and evaluation of variables. The post-processing step entails the visualisation of results in addition the determination of secondary variables as actually required.
A FEM simulation study of three and four coil AMB has been shown utilizing ANSYS software to perform the magnetic field analysis in the AMB. Provide a comparative analysis of three and four coil AMBs that have been worked on under various operating conditions. The force is evaluated by Maxwells stress tensor method [4]. Both the analytical procedure and transient FEM analysis are used to define and estimate the dynamic current stiffness and displacement stiffness for AMTB [5]. Using the finite element software COMSOL by usage a current signal, a 2D computer simulation of an axial active magnetic bearing system was conducted. The results of simulation verified the flux density distribution and electromagnetic force estimation of AMB system [6]. An eight-pole electromagnetic bearing has been designed and presented. Maximize the carrying capacity of a load utilizing numerical method, for the provided outer diameter, axial length, the maximize permissible current [7]. The behaviour of single coil and multi-coil actuators designed for active magnetic bearing (AMB) system is investigated. Magnetic flux, flux density, field strength, force profile, and inductance profile were analysed in 2D using Ansys Maxwell, and magnetic flux density, field strength, current density, and inductance profile were analysed in 3D. The quantities were compared in order to gain insight into the behaviour of single and multi-coil actuators [8]. The results of a single axis and double axis AMB simulation using ANSYS Maxwell 17.1 are presented. For two different structures, a Finite Element Method (FEM) based simulation has been shown, as well as their magnetic properties, such as flux pattern, force, flux density, and inductance, for various
air-gaps. The difference in current density caused by changing coil turns has also been investigated. The comparative results of single and double coil AMB are performed in 2-D and 3-D plots [9]. A simulation of two AMB structures, one with single electromagnets and the other with double opposed electromagnets. The theoretical model of single coil AMB and double coils AMB has been studied. A 2D and 3D simulation have been compared for single and double coils AMB system. Magnetic parameters like force, magnetic field, flux pattern and flux density are made and observed utilizing ANSYS Maxwell simulation software [10].
In this work, ANSYS Maxwell Software was used to create a 3D simulation of an eight pole active magnetic bearing. The simulation has been performed using the finite element method (FEM).
ACTIVE MAGNETIC BEARING
- AMB CONSTRUCTION AND PRINCIBALE WORK AMB is composed of various components such as rotor,
electromagnet, controller, position sensor, power amplifier etc. By balancing the rotor weight, biassed current is used to maintain the rotor in a desired position. If rotor is displaced from its desired position during the operation, then displacement of rotor determined by position sensor which feeds signals to controller. The controller transforms the position signal to output current. The power amplifier then amplifies the current and sends it to the electromagnet, which generates the magnetic force that returns the rotor to its operating position.. Fig. 1. describes the active magnetic bearing system’s block diagram. Fig. 2. Shows the construction of eight pole AMB which consists of rotor, stator, coil and air gap. The stator has an iron core, while the rotor is made of ferromagnetic material. To provide a proper magnetic field for the rotor, more coils of wire are wound around the iron core of the stator. This electromagnetic field creates a force that helps rotor to levitate and freely rotate in the air gap between rotor and stator without any physical contact between them. Fig. 3. Represented the configuration of AMB with direction of magnetic field and current in one electromagnet.
Fig. 1. Block diagram of Active Magnetic Bearing System
Fig. 2. Construction of eight pole AMB
fig. 3. The structure of U-shaped electromagnets with the magnetic flux loops
- MAGNETIC FORCE F AMB
When an electric current passes through the coils of AMB, a magnetic field has been generated which responsible for generating a magnetic force. The magnetic force for a single pole AMB can be calculated by the given equation:
F = (1)
By neglected the angle of pole. Where F, µ0, N, i, Ag, g is the magnetic force, the permeability of air, the number of turns, the coil current, the cross-sectional area of air-gap and the air-gap between rotor and the stator, respectively. In four coil AMB two pairs of electromagnets have been used. In fig. 2. Two pairs of electromagnets are illustrated. Each electromagnet can only produce an attractive force effecting on the ferromagnetic rotor. Thus, the rotor was attracted in opposite directions by a pair of electromagnets on the same bearing axis.. The force FX and Fy created by two pairs of electromagnets in both direction x and y according to these equations:
Fx = f3 – f1 = ( ) (2)
Fy = f4 f2 = ( ) (3)
The rotor’s stability in its operating position during the process of controlling is achieved by making the electrical current in each magnet in x and y direction in this way:
i1 = io ix ; i3 = io + ix in x direction (4)
i2 = io iy ; i4 = io + iy in y direction (5)
Where io is a bias current acting onto all actuators and ix, iy
are control current in both x and y direction, respectively.
g1 go x ; g3 go x in x direction (6) g2 go y ; g4 go y in y direction (7) Where go is the nominal air gap between rotor and stator where x and y are the displacement of the rotor from its original position in both x and y direction, respectively. By compensation equation (4), (6) in equation (2), and equation
(5), (7) in equation (3). The magnetic force in both x and y direction is given by the following equations:
fx = ( – ( )x (8) fy = ( – ( )y (9) Equation (8, 9) was achieved by assuming that the control current ix, iy and the displacement x,y are so small compared to the bias current io and nominal air gap go, respectively that the higher order terms for the control current and displacement were neglected. It has shown that, the magnetic force varied depending on the control current and the air gap thickness . The equation (8, 9) can be easily written as:
fx = ki ix – ks x (10)
fy = ki iy – ks y (11)
Where; fN = fAMB
Where; ki is called the current stiffness and ks is called the position stiffness and they can be calculated by the given equations:
ki = (12)
ks = – (13)
- MODELLING IN ANSYS SOFTWARE A ANSYS SOFTWARE
Using ANSYS Multiphasic the analysis of eight pole active magnetic bearing is carried out. Utilizing this software all stages such as defining geometry, applying physics, meshing, solving equations and visualizing results can be carried out [10]. This software serves as a foundation for a variety of application modules. It solves partial differential equations using the finite element method. Firstly, define the bearing geometry, type of material, the electric current and the boundary conditions in this step. This paper studied a three dimensional magneto static analysis of eight pole active magnetic bearing.
B CONSTRUCTION AND MATERIAL OF AMB
The active magnetic bearing construction design consists of rotor and stator with coils. The material for rotor and stator is steel 1008 and for coils is capper. The heterpolar design of AMB consists of eight pole at 45 degrees apart from each and other fig. 2. The parameters of AMB are given as: number of poles 8, air gap 0.5 mm, rotor outer diameter 50mm, rotor inner diameter 20mm, number of turns 260 and coil current 1A. These parameters are used to design AMB using finite element method with ANSYS software. Fig. 4. shows the mesh of eight pole active magnetic bearing. The AMB parameters are given in Table 1. .
Fig. 4. Mesh of eight pole AMB
Parameter Value stator inner diameter (mm) 56 stator outer diameter (mm) 139 rotor inner diameter (mm) 20 rotor outer diameter (mm) 55 air gap length (mm) 0.5 coil current 1A pole length (mm) 30 Pole width (mm) 10 AMB width(mm) 10 Number of turns 260 Table 1. Parameters of active magnetic bearing
- RESULTS AND DISCUTION
- MODELLING IN ANSYS SOFTWARE A ANSYS SOFTWARE
The 3D simulation representes magnetic flux density and the magnetic flux vector of eight pole active magnetic bearing. Commercial FEM Software ANSYS (version 16.0) has been carried out for this objective. In Fig. 5. The magnetic flux density of eight pole AMB with air gap 0.5mm, coil current 1A and number of turns 260 are shown. Fig. 6. Indicates vector plot of magnetic field for eight pole active magnetic bearing with air gap 0.5mm, coil current 1A and number of turns 260. Fig. 7. Illustrates vector plot of the flux density for the above system utilizing same parameters. It has been observed that as the air gap increases, The flux linkage between the stator and the rotor is reduced, and the leakage flux is elevated. Fig. (8 to 10) shows the effect of changing the air gap on flux density, magnetic flux and magnetic force. It is noted that the larger the air gap the smaller the flux density, magnetic flux and magnetic force. In all cases of increasing the air gap, It is assumed that the coil current is constant 1A of all various air gap positions. Fig(11 to 13) gives the effect of changing the number of turns on flux density, magnetic flux and magnetic force. It has been observed that as the number of turns increases the, magnetic flux, flux density and magnetic force are increased vice- versa. In all cases of increasing the number of turns, the coil current is assumed to be constant 1A and the air gap 0.5mm. Fig. 14. representes a 3D plot of force, current and air gap. It’s noticed that as the air g increases, the operating coil current increases and force increases too. At min value of
current (0A) the value of force almost zero, when air gap is constant, and when the current increases until it reaches its maximum value (6A), It’s noticed that the force increases with the increase of current. Looking at the air gap at its lowest value, which is zero, the value of force is approximately zero, when the current not changed. But when the value of air gap increases until it reaches the maximum value (1.2mm), the force increased in order to compensate for the loss in the magnetic force due to the increase of air g which is necessary to levitate the rotor, the force increases and vice-versa. Fig. 15. provides a 3D plot of flux density, current and air gap. It’s noticed that as the air gap increases the the flux density decreases and it increases with the increase of current. This is because as the current increases, the magnetic force increases, and thus the magnetic flux density increases when the air gap is constant. As the air gap increases, the magnetic force decreases, as we mentioned earlier, so the flux density also decreases when the current is constant. Fig. 16. Shows a 3D plot of flux density, current and number of turns. It’s seen that the flux density increases as the increase of both number of turns and air gap. That is because at the number of turns increases, the magnetic force increases and thus the manetic flux density increases when the current is constant. And when the current increases, when the number of turns is constant, the magnetic force increases and the flux density increases too.
Fig. 5. Magnetic flux density of AMB
Fig. 6. vector plot of magnetic field
Fig. 7. vector plot of magnetic flux density
Fig. 8. Flux vs air gap at n=260 and I=1A
Fig. 9. Magnetic flux vs air gap at I=1A and n=260
fig. 10. Force vs air gap at I=1A and n=260
Fig. 11. Flux density vs number of turns at I=1A and
g=0.5mm
Fig. 12. Flux density vs number of turns at I=1A and g=0.5mm
Fig. 13. Force vs number of turns at I=1A and g=0.5mm
Fig. 14. 3D plot of force vs current vs air gap
fig. 15. 3D plot of flux density vs current vs air gap
fig. 16. fiux density vs number of turns vs current
V. CONCLUSION
The finite element method is used in this work to create a 3D simulation of eight pole active magnetic bearing. ANSYS Software was used to investigate various magnetic properties like magnetic flux density, magnetic field, and its vector plot. The effect of winding current, air gap, and number of turns of coils on magnetic force, magnetic flux, and magnetic flux density has been presented. As a result, this paper presents a method for modelling and simulating eight pole active magnetic bearing utilizing the finite element method.
REFERENCES
- H. Bleuler, M. Cole, P. Keogh, R. Larsonneur, E. Maslen, Y. Okada, G. Schweitzer, A. Traxler et al., Magnetic Bearings: Theory, Design, and Application to Rotating Machinery. Springer Science & Business Media, 2009.
- M. Autila, E. Lantto, and A. Arkkio, Determination of forces and linearized parameters of radial active magnetic bearings by finite element technique, IEEE Transactions on Magnetics, vol. 34, no. 3, pp. 684 694, 1998.
- K. P. Lijesh and H. Hirani, Design and development of halbach electromagnet for active magnetic bearing, Progress In Electromagnetics Research, vol. 56, pp. 173181, 2015.
- P. K. Biswas and S. Banerjee, Ansys based fem analysis for three and four coil active magnetic bearing-a comparative study, International Journal of Applied Science and Engineering, vol. 11, no. 3, pp. 277 292, 2013.
- Y. Sun, Y.-S. Ho, and L. Yu, Dynamic stiffnesses of active magnetic thrust bearing including eddy-current effects, IEEE Transactions on Magnetics, vol. 45, no. 1, pp. 139149, 2009.
- J. Laldingliana, P. K. Biswas and S. Debnath, “Magnetic analysis of single-axis active magnetic bearing using ansys base environment”, 2017.
- Dr. K.P. Lijesh; optimization of eight pole radial active magnetic Bearing, ASME Journal of tribology; 2010.
- S.Debnath, P.K.Biswas, Comparative magnetic analysis of I-type actuator based active magnetic bearing system, Journal of Power Technologies 100 (3) (2020) 211222
- J.Laldingliana, P. K.Biswas, ANSYS Based Simulation of Single and Double Coil Axial Active Magnetic Bearing using Finite Element Method, International Journal of Engineering and Advanced Technology (IJEAT) ISSN: 2249 8958, Volume-9 Issue-3, February, 2020.
- L.Jonathan, D.Sukanta, B.P.Kumar, Fem software based 2-D and 3-D construction and simulation of single and double coils active magnetic bearing, International Journal of Innovative Technology and Exploring
Engineering (IJITEE)ISSN: 2278-3075,Volume-8 Issue-11, September 2019.
- Engineering (IJITEE)ISSN: 2278-3075,Volume-8 Issue-11, September 2019.
- S.Saha, M. Nabi, Analysis of active magnetic bearing using finite element method, Recent Developments in Control, Automation & Power Engineering (RDCAPE),IEEE, 2017 , pp. 7679.
- Liu, Y., Ming, S., Zhao, S., Han, J., & Ma, Y, Research on Automatic Balance Control of Active Magnetic Bearing-Rigid Rotor System. Shock and Vibration, 2019, 113, (2019).
on force and correction factor of an active magnetic thrust bearing. J
Braz. Soc. Mech. Sci. Eng. 40, 221 (2018).