
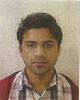
- Open Access
- Authors : Gourav Khullar , Rajwinder Singh Bansal
- Paper ID : IJERTV9IS110233
- Volume & Issue : Volume 09, Issue 11 (November 2020)
- Published (First Online): 02-12-2020
- ISSN (Online) : 2278-0181
- Publisher Name : IJERT
- License:
This work is licensed under a Creative Commons Attribution 4.0 International License
Mechanical And Microstructural Properties of Fly Ash based Geopolymer Concrete Incorporating with Bagasse Ash and Metakaolin
Gourav Khullar
Ramgarhia Institute Of Engineering & Technology, Phagwara, India
Rajwinder Singh Bansal
Ramgarhia Institute Of Engineering & Technology, Phagwara, India
Abstract In this experimental study, the bagasse ash and metakaolin is used to develop the geopolymer concrete. The fly ash based geopolymer concrete was prepared with bagasse ash and metakaolin which were used to replace fly ash at different percentages i.e. 10%, 20%, 30% and 40% to study the microstructure, mechanical and durability properties. Geopolymer Concrete was prepared with the use of alkaline solutions NaOH and Na2Sio3. Geopolymer concrete samples for bagasse ash and metakaolin based were cured at oven for 24 hours at 90C and then kept under room temperature for curing. Metakaolin contained geopolymer concrete has shown better mechanical and durability properties as compared with bagasse ash contained geopolymer concrete. Geopolymer concrete is raw material based concrete that leads to the usage of materials which are produced as a raw material from industries and when these raw materials were induced in the geopolymer preparation it leads to the reduction of carbon emissions and acts as a greener concrete towards environment. Microstructure studies concluded that the metakaolin contained geopolymer concrete has denser intermolecular bonding of materials as compared to the bagasse ash contained geopolymer due to which metakaolin shows better results in mechanical and durability properties when compared with bagasse ash.
Keywords Geopolymer Concrete, Fly Ash, Bagasse Ash, Alkaline Solutions, Metakaolin
I. INTRODUCTION
Concrete is the worlds most versatile, durable and reliable construction material. Next to water, concrete is the most used material, which requires large quantities of Portland cement and aggregates. It is reported that the consumption of cement in India is 421 million tonnes and likely to touch 550 million tonnes by 2020 and global cement consumption is 4.0 billion tonnes and likely to touch 4.2 billion tonnes by 2020 (Department of Industrial policy and promotion). On the other hand, the demand for construction aggregates in India amounted to 1.1 billion metric tons in 2006, making the country the third biggest aggregates market in the Asia/Pacific region and fourth largest market in the world (after China, the US, and Japan). Sales in India have risen an average of 7.7 percent annually over the past ten years, exceeding both regional and the Global demand for construction aggregates is expected to grow 4.7 percent annually through 2011 to 26.8 billion metric tons (Indian Concrete Institute).
Early pace of construction is increasing day by day which is leading towards the increase in carbon dioxide (CO2) emissions, which is basically released by the production of ordinary portland cement. Concrete use over the world is well
known and the increasing construction work has led to introduce such type of substitution or alternate material which will help to increase the pace of construction by early strength property and reduction the carbon emissions as well. The properties of geopolymer concrete for fresh and hardened concrete depends upon the type of materials that has been used for the preparation of geopolymer concrete. The durability of property of geopolymer concrete is better than the conventional concrete due the high composition of chemical compounds and due to this the thermal resistance of geopolymer concrete is better substitution for the ordinary conventional concrete.
It has been observed after studying the geopolymer concrete it showed the eco-friendly and greener properties towards the environment and better engineering properties [11, 12]. The use of eco-friendly material in concrete will help in many ways such as dumping of tonnes of waste will be utilized.
II. LITERATURE REVIEW
There is a wider area of concern that has to be filled by doing research on geopolymer concrete with bagasse ash and metakaolin replacement with fly ash and ground granulated blast furnace (GGBS). In this research the various percentages will be checked with fly ash and GGBS replacement with bagasse ash to check the geopolymer concrete properties for various tests and then fly ash and GGBS will be replaced by metakaolin for different percentages to check the various tests conducted on concrete to see its strength i.e compressive strength, flexural strength, split tensile strength, sulphate attack, abrasion test,.The work done with geopolymer concrete with fly ash replacement with bagasse and metakaolin has a broad area to work with and geopolymer concrete is future concrete so there is a gap in the research related to geopolymer concrete and by the use of such replacements we can check the geopolymer concrete properties by doing testing on it. Using such replacement with fly ash and GGBS will give an idea that up to which percentage the replacements can be used so that we can get the results in desired values.
III. MATERIAL USED
A. Fly Ash
Fly Ash is by product which is waste product which is obtained from the thermal power plants and it is a mineral admixture. Fly Ash was obtained from the Ropar Thermal
Power Plant of Class F. The specific gravity of fly ash is 2.35 g/cc.
B. Ground Granulated Blast Furnace Slag (GGBS)
GGBS is a ground granulated blast furnace slag particle which is obtained from the steel manufacturing plant. GGBS is a powder form can be replaced with fly ash. GGBS is kept constant with the 20% replacement with fly ash. GGBS specific gravity is 2.7 g/cc.
C. Bagasse Ash (BA)
It is a waste by-product of sugarcane industry and it is obtained after the burning of sugarcane. It is in ash form which was obtained from the Morinda Sugar Mill. It has specific gravity of 1.13 g/cc.
D. Metakaolin
Metakaolin is having high reactivity, silica based pozzolana. It is manufactured by the processing of specially selected pozzolanic ingredients under controlled conditions. It is form of a kaolite which is a clay mineral which has excellent cementitious properties. It is a clay mineral which is off white in colour and has a specific gravity 2.6 g/cc.
E. Fine Aggregates
The locally available river sand used as fine aggregates of size less than 4.75 mm.
F. Coarse aggregates
The aggregates having size grater then 4.75mm called as coarse aggregates. The locally available coarse aggregates having size 20 mm used. The shape of the coarse aggregates was rounded.
G. Alkaline Solutions
These solutions are used with the powder to mix it and prepare the geopolymer concrete. The solutions are used in ratios. The NaOH and Na2Sio3 are used in (1:2.5). The 12M of molarity is used for NaOH and the Na2Sio3 is used in the form of liquid of A53 grade which has 59.5 % of solid content in solution. Sodium hydroxide flakes were used in this study and NaOH used is of commercial grade with 97% purity.
H. Water
Normal tap water is used for fulfilling the demand of solid content present in the alkaline solutions. The use of water is less in geopolymer concrete.
I. Superplasticizer:
Superplasticizer Conplast SP 430 was used as a chemical addmexture for concrete.
Images of used materials shown in Figure 1.
Figure 1(a) Fly Ash
Figure 1(b) GGBS
Figure 1(c) Bagasse Ash (BA)
Figure 1(d) Metakaolin
Figure 1(e) Alkaline Solutions Figure 1. Materials Used
J. Mix Proportions
The details of th mix proportions and replacement levels are shown in Table 1.
Table 1: Details of the Mix Proportions and Replacement Levels
Mix |
Replacement Levels |
||
Fly Ash + GGBS (in %) |
Metakaolin (in %) |
Bagasse Ash (in %) |
|
Control |
80+20 |
0 |
0 |
Mix 1 |
72+18 |
10 |
0 |
Mix 2 |
64+16 |
20 |
0 |
Mix 3 |
56+14 |
30 |
0 |
Mix 4 |
48+12 |
40 |
0 |
Mix 5 |
72+18 |
0 |
10 |
Mix 6 |
64+16 |
0 |
20 |
Mix 7 |
56+14 |
0 |
30 |
Mix 8 |
48+12 |
0 |
40 |
IV. RESULTS AND DISCUSSIONS
In this section results has shown from figure 2 to figure 5 and also tabular results highlighted from table 2 to table 5.
A. Compressive Strength Test
Compressive strength testing is done to determine the strength of the concrete by casting cubes of size 150×150×150 mm to determine the strength of concrete for defined grade. It is a mechanical test for concrete. The cubes are tested according to IS 516-1959. In table 2 and figure 2, Compressive Strength at 28 Days is presented.
Table 2 Compressive Strength at 28 Days
S.NO |
Oven Dry Curing at 60 degree |
28 Days Testing (Mpa) |
||||
0% |
10% |
20% |
30% |
40% |
||
1. |
Metakaolin |
26 |
28.53 |
30.97 |
25.35 |
22.57 |
2. |
Bagasse Ash |
25.06 |
21.42 |
17.73 |
14.93 |
Figure 2 Compressive Strength at 28 Days
B. Flexural Strength Of Beam
Flexural strength is calculated to measure the flexural strength of concrete by casting beams of size 100×100×500
mm. Detail results of Strength of Beam at 28 Days shown in figure 3 and table 3.
Table 3 Flexural Strength of Beam at 28 Days
S.NO |
Materials |
28 Days Testing (Mpa) |
||||
0% |
10% |
20% |
30% |
40% |
||
1. |
Metakaolin |
3.8 |
3.98 |
4.35 |
3.52 |
2.97 |
2. |
Bagasse Ash |
3.77 |
2.87 |
2.56 |
2.36 |
Table 3 Flexural Strength of Beam at 28 Days
C. Split Tensile Strength Test:
Split Tensile Testing is also the mechanical testing and it is used to calculate the split tensile strength of concrete. The size is 150 mm diameter and 300 mm length of cylinder is used to calculate the strength. Results of Split Tensile Strength at 28 Days shown in figure 4 and table 4.
Table 4 Split Tensile Strength at 28 Days
S.NO |
Materials |
28 Days Testing (Mpa) |
||||
0% |
10% |
20% |
30% |
40% |
||
1. |
Metakaolin |
3.41 |
3.42 |
3.95 |
3.50 |
3.30 |
2. |
Bagasse Ash |
3.29 |
2.97 |
2.55 |
2.32 |
Figure 4 Split Tensile Strength at 28 Days
D. Sulphate Attack Test
Sulphate attack test is related to the durability property of concrete in which we immerse the concrete sample in the acid to check out the weight loss of the sample and how much reduction in strength has occurred. 5% of the weight of water acid is used for testing the sulphate attack and size of cube was 150×150v150 mm. The samples are cured for 28 days and then immersed in the acid for 28 days, 56 days and 96 days to check the ability of concrete in acid environment. Further Sulphate Attack test at 28 Days shown in figure 5 and table 5.
Table 5 Sulphate Attack test at 28 Days
S. No. |
Materials |
28 Days Testing (Mpa) after immersed in H2SO4 |
|||||
0% |
10% |
20% |
30% |
40% |
|||
1. |
Metakaolin |
Before |
26 |
28.53 |
30.97 |
25.35 |
22.57 |
After |
27.28 |
29.5 |
23.9 |
21.3 |
|||
2. |
Bagasse Ash |
Before |
24 |
25.06 |
21.42 |
17.73 |
14.93 |
After |
23.88 |
19.5 |
16.0 |
13.2 |
Figure 5. Sulphate Attack test at 28 Days
V. CONCLUSION
1. Geopolymer Concrete has shown good mechanical and durability properties for designed grade of geopolymer concrete with metakaolin contained geopolymer concrete as compared with bagasse ash based geopolymer concrete.
2. Metakaolin at 20% replacement and Bagasse Ash at 10% replacement have shown the maximum mechanical and durability result for geopolymer concrete.
3. Bagasse Ash at 10% replacement has shown the optimum percentage for best results for geopolymer concrete. If we add the more percentage for bagasse ash it shows a decline but higher percentage of bagasse ash can be used to produce the light weight concrete.
4. Geopolymer Concrete is prepared with the use of raw materials which is eco-friendly and it will act as a green material to the environment.
5. Oven dry samples and normal temperature samples results were compared and in case of metakaolin the normal curing samples achieved the required strength of grade M 25 but oven dry samples attained more compressive strength. Normal temperature curing for metakaolin contained geopolymer has attained 26.93Mpa strength and in case of oven dry samples strength attained was 30.75Mpa.
REFERENCES
[1] Torgal et.al, Alkali-activated binders: A review; Part 1. Historical background, terminology reaction mechanisms and hydration product Construction and Building Materials 22(7), pp. 1305- 1314, 2008a [2] S. Jalali et.al, Alkali-activated binders: A review. Part2. About materials and inders manufacture Construction and Building Materials 22 pp. 131 – 1322, 2008b [3] Tippayasam et.al, Geopolymer development by powders of metakaolin and wastes in hailand. Avd Science Technology 2010; 69:638. [4] Davidovits J. nvironmentally driven geopolymer cement applications. In: Geopolymer International conference Melbourne, Australia: Geopolymer Institute; 2002. [5] Du son et.al Geopolymer technology: the current state of the art Journal of Material Science 42, pp. 2917-2933, 2007. [6] Sofi Yasir et.al, Study of Properties of Fly Ash Based Geopolymer Concrete International Journal of Engineering Research Vol. 3, Issue 1, ISSN: 2321-7758, January 29, 2015. [7] Cembureau Cement in Cembureau Countries Statistics 2005- 2007 available athttp://www.cembureau.be/Documents/KeyFacts/STATISTICS/Ceme nt%20in%20C EMB%20countries.pdf
[8] Mehta, P. K. 2001 Reducing the Environmental Impact of Concrete, ACI Concrete International 23(10):pp. 61-66 [9] Portland Cement Association 2006 World Cement Consumption Growth Expected to Continue in Portland Cement Association Executive Report available at http://www.cement.org/exec/10-23- 06.htm. [10] Davidovits, J. 1991 Geopolymers: inorganic Geopolymeric new materials Journal of ThermalAnalysis 37, pp. 1633-1656. [11] Rangan, B.V. 2008 Low-Calcium Fly Ash-Based Geopolymer Concrete Chapter 2 Concrete Construction Engineering Handbook Second Edition, Editor-in-Chief: E.G. Nawy, CRC Press, New York, pp. 26.1-26.20; [12] Sumajouw et.al, 2006 Low-Calcium Fly Ash-Based Geopolymer Concrete: Reinforced Beams and Columns Research Report GC3 Faculty of Engineering, Curtin University of Technology available at http://espace.library.curtin.edu.au. [13] Ash Development Association of Australia, Total ash production and beneficial usage available at http://www.adaa.asn.au/statistics.htm [14] Wallah et.al, 2006 Low Calcium Fly Ash Based Geopolymer Concrete: Long erm Properties. Research Report GC2 Faculty of Engineering Curtin University of Technology a aila le at http://espace.library.curtin.edu.au [15] Sofi et.al, 2007 Bond performance of Reinforcing Bars in Inorganic Polymer Concrete (IPC) Journal of Materials Science 42(9) pp. 310 -3116. [16] Sarker et.al, 2007 Bond Strength of Geopolymer Concrete with Reinforcing Steel in: Zingoni A. (ed) Proceedings of Recent Development in Structural Engineering, Mechanics and Computation he etherlands pp. 131 -1320 [17] International Journal of Engineering Research & Technology (IJERT) Vol. 6 Issue 05, May 2017 [18] Bahurudeen et.al, Development of sugarcane bagasse ash based Portland pozzolana cement and evaluation of compatibility with super plasticizer, Construction and Building Materials Volume 68, pp. 465-475, 2014 [19] Guru Gobind Singh College of Engineering and Research Centre,Nasik, MS 24th, 25th, 26th March 2017, www.confrebceworld.in
[20] ISRN Polymer Science. 2013, p1-8. 8p. [21] Davidovits, J. 1984. Pyramids of Egypt Made of Man- Made Stone, Myth or Fact Symposium on Archaeometry 1984. Smithsonian Institution, Washington, DC. [22] A. Sivakumar and M. Santhanam, Evaluation of drying shrinkage and residual stresses of a high strength concrete using restrained ring test Indian Concrete Journal vol. 82, no. 6, pp. 4957, 2008.View at Google Scholar · View at Scopus [23] Jian-Tong et.al. (2002) Pu lication: Materials Journal. Volume: 99.Issue: 4. Appears on pages(s):398 https://www.concrete.org
[24] S E Wallah et.al, (2005) Introducing Fly Ash-Based. Geopolymer Concrete (Manufacture And Engineering Properties) 30th conference on our world in concrete & structure 24 August 2005. [25] Erhan Gu¨neyisi et.al (2008), Improving strength, drying shrinkage, and pore structure of concrete using metakaolin Article (PDF Available) in Materials and Structures 41(5):937-949 · June 2008 [26] Monita et.al, (2011) Strength and water penetrability of fly ash based geopolymer VOL. 6, NO. 7, JULY 2011 ISSN 1819-6608 ARPN Journal of Engineering and Applied Sciences ©2006-2011 Asian Research Publishing Network (ARPN). All rights reserved. [27] Benny Joseph et.al (2012), Influence of aggregate content on the behaviour of fly ash based geopolymer concrete Article in Scientia Iranica 19(5):1188 1194 · October 2012 [28] Aminul Islam Laskar et.al, (2012) Investigated the variation of workability of fly ash based Geopolymer concrete with the variation of lignin based plasticizer and poly-car o ylic ether ased super plasticizer Proceedings of International Conference on Advances in Architecture and Civil Engineering (AARCV 2012) 21st23rdJune 2012
[29] Abdul Aleem et.al, (2012) Optimum Mix for the Geopolymer Concrete Indian Journal of Science and Technology Volume 5,Issue 3, March 2012
[30] G. Dhinakaran et.al, (2012) Compressive strength and chloride resistance of metakaolin concrete Article (PDF Available) in KSCE Journal of Civil Engineering 16(7) · November 2012 [31] Jaydeep et.al, (2013) Study On Fly Ash Based Geo-Polymer Concrete Using Admixtures International Journal of Engineering Trends and Technology (IJETT) Volume 4 Issue 10 – Oct 2013 ISSN: 2231-5381 http://www.ijettjournal.org Page 4614 [32] Patel et al,(2013) Study on Durability of High Performance Concrete With Alccofine and Fly Ash International Journal of Advanced Engineering Research and Studies E-ISSN22498974 IJAERS/Vol.II/ Issue III/April-June,2013/154- 157
[33] Mahadeshwaran C. K et.al (2014) Effect of molarity in geopolymer concrete International Journal of Civil and Structural EngineeringVolume 4, No 2, 2013
[34] P. K. Jamdade et.al, (2014) Evaluate Strength of Geopolymer Concrete by Using Oven Curing IOSR Journal of Mechanical and Civil Engineering (IOSR- JMCE) e-ISSN: 2278-1684,p-ISSN: 2320-334X, Volume 11, Issue 6 Ver. V (Nov- Dec. 2014) [35] T. V. Srinivasmurthy et.al, (2015) Studies on Mix Design of Sustainable Geo- Polymer Concrete International Journal of Innovative Research in Engineering & Management (IJIREM)ISSN: 2350-0557, Volume-2, Issue-4, July 2015
[36] Shankar H. Sanni et.al, (2016) Study of Geopolymer Concrete under Different Curing Conditions International Journal of Recent Scientific Research Vol. 9, Issue, 3(H), pp. 25166-25170, March, 2018 [37] Jian-Tong Ding et.al, (2016) Effects of Metakaolin and Silica Fume on Properties of Concrete ACI Material Journal Title no. 99-M39 [38] B. B. Patil et.al, (2016) Strength and Durability Properties of High Performance Concrete incorporating igh Reacti ity Metakaolin International Journal of Modern Engineering Research (IJMER) www.ijmer.com Vol.2, Issue.3, May-June 2012 pp 1099-1104 ISSN: 2249-6645 [39] Arya Aravind et.al, (2017) Study of Mechanical Properties of Geopolymer Concrete Reinforced with Steel Fi re International Journal of Engineering Research & Technology (IJERT) ISSN: 2278-0181 Vol. 3 Issue 9, September- 2014 [40] Kamlesh et.al, (2018) Study of Strength Parameters and durability of Fly ash ased Geopolymer Concrete Indian Journal of ResearchVolume: 3 | Issue: 7 | July 2014 ISSN – 2250-1991
[41] Dilip Srini as Madankumar et.al (2019 ) Feasibility Analysis of use of Bagasse Ash for the Production of Geo Polymer Concrete International Journal of Engineering Research & Technology (IJER ) http://www.ijert.org ISS : 22 8- 0181 IJERTV6IS050086 Vol. 6 Issue 05, May 2017 [42] Rajendra. D et.al, Effect of Strength Properties on Concrete by Partial Replacement of Coarse Aggregate with Waste Cuddapah Stones International Journal of Engineering Research & Technology (IJERT) http://www.ijert.org ISSN: 2278-0181 IJERTV6IS050240 Vol. 6 Issue 05, May – 2017 [43] Royal Minerals, Kutch Gujarat www.royalmineral.co.in/ [44] IS 383 Specifications for Coarse and Fine Aggregates From Natural Sources For Concrete. [45] IS 456-2000 Plain and Reinforced Concrete Code of Practice is an Indian Standard code of practice for general structural use of plain and reinforced concrete. [46] Indian standard Recommended Guidelines for Concrete Mix Design IS 1026:1982, Bureau of India Standard, New Delhi. Indian standard concrete mix proportioning – Guidelines (First revision) IS 10262:2009, Bureau of India Standard, New Delhi, India. [47] Kushal Ghosh Effect of %Na2O and %Sio2 on Apperent Porosity And Sorptivity of Flyash Based Geopolymer IOSR Journal of Engineering (IOSRJEN) ISSN: 2250-3021 Volume 2, Issue 8 (August 2012), PP 96-101 www.iosrjen.org.