
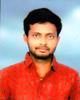
- Open Access
- Authors : Durgaprasad Kollipara , Katakamsetti Durga Bhanu , Rajamandri Surendra , Nalaganchu Chaitanya
- Paper ID : IJERTV11IS050149
- Volume & Issue : Volume 11, Issue 05 (May 2022)
- Published (First Online): 23-05-2022
- ISSN (Online) : 2278-0181
- Publisher Name : IJERT
- License:
This work is licensed under a Creative Commons Attribution 4.0 International License
Mechanical and Wear Properties of Heat Treated Al 7075
Durgaprasad Kollipara, Katakamsetti Durga Bhanu, Rajamandri Surendra , Nalaganchu Chaitanya V.K.R.,V.N.B & A.G.K College of Engineering
Abstract-In this paper an Al 7075 alloy is a commonly used commercial material that is manufactured using a wrought manufacturing process and has a high strength. The bulk behaviour of metals and alloys is influenced by the presence of distinct phases and their relative quantities. Hence, Al7075 alloy has been subjected to solution treatment at 450 with an aim to understand the effect of heat treatment on the mechanical characteristics. After heat treatment the Al2Mg3Zn3 phases could be distributed in the Al and a minor amount of Al2CuMg phases, Al2Cu phases and Al7Cu2Fe phases precipitated at the grain boundaries and the grain size of the base material was reduced from 89.93 µm to 59.29 µm. In comparison to the basic material, the hardness increases, and the average hardness is 163.14 HV. Ultimate tensile strength and wear properties were both significantly raised as a result of the tensile and wear test
-
INTRODUCTION
The earth is being depleted of its natural resources, and it is of absolute importance to retard this destroying trend, which is for engineers to do so. One of the ways of saving the perishing environment is finding ways to contribute towards less energy consumption. One among many of these contributing methods is making fossil fuel killers, e.g., cars, airplanes, etc. lighter which is possible through using lighter metals like aluminum in their structure. One limitation in using a pure light metal may be its lack of strength. But the goal is worth fighting all the obstacles, and this fight is at least as old as the existence of blacksmith who beat a piece of metal to render it stronger. Among likely candidates for light structure material, is aluminum, to which because of its unique properties, to mention one among many, not showing brittle response under a specific temperature (transition temperature) in contrast to steel1, which makes it an ideal metal for cryogenic conditions, industry and as result research, are showing greater interest. The good thing about this element is its high strength to weight ratio into the bargain2; the drawback is its relatively low strength. These two characteristics make aluminum suitable for low stress applications. But most of engineering purposes deal with moderate to high stresses in which pure aluminum may give in. To overcome this, it is an old fashion, as one of the methods of enhancing this metal, to add other elements like copper, manganese, silicon, magnesium, zinc, etc. to it as alloying elements. In addition to alloying elements in the base metal there exist some other interesting strengthening methods such as, microstructure modification (grain size reduction), precipitation hardening, dispersion strengthening, and work hardening.
One or combination of these may be applied to alloy depending on its properties and limitations. It seems, from among alloying elements, zinc and magnesium play greater role in giving the aluminum strength. 7xxx aluminum alloys which contain zinc and magnesium, as their main alloying elements in varying amounts (which define the rest of the digits after number 7 in the name of the alloy) have gained the top priority when considering nominees for suitable material for aero-transportation vehicles. For, in the airplane, safety is the main issue, in addition to strength of components, other factors like stress corrosion must be taken into account at the time of designing the components.
All strengthening mechanisms rely on one principle; Hindering movement of dislocations. All existing methods like Strain hardening, precipitation hardening, Hall- Petcheffect (grain boundary strengthening), dispersion strengthening, make the alloy stronger by decreasing the degree of mobility of the dislocations3-8. Talking about aluminum, depending on the major alloying element, the contribution of each of the mechanisms differ dramatically. For example, if an aluminum alloy has the copper as its major alloying element (2xxx series of wrought aluminum alloy) it can be precipitation hardened; on the other hand, if copper is superseded by magnesium (5xxx series of wrought aluminum alloy), precipitation strengthening will have negligible contribution towards the yield strength augmentation of alloy. 7xxx aluminum alloys, are called heat treatable alloys as they can be strengthened through precipitation strengthening. One of the notorious shortcomings of precipitation hardened 7xxx alloys is their lack of resistance against stress and exfoliation corrosion. Industry owners and researchers have turned to a special heat treatment called retrogression and re aging to make the stress corrosion to surrender by a great degree.
The optimum properties of aluminium are achieved by alloying additions and heat treatments. This promotes the formation of small hard precipitates which interfere with the motion of dislocations and improve its mechanical properties. One of the most commonly used aluminium alloy for structural applications is 7075 Al alloy due to its attractive comprehensive properties such as low density, high strength, ductility, toughness and resistance to fatigue9-12. It has been extensively utilized in aircraft structural parts and other highly stressed structural applications13-17.
But aluminium-zinc alloy as it is in 7075 Al alloy is susceptible to embrittlement because of micro segregation of MgZn2 precipitates which may lead to catastrophic
failure of components produced from it. The alloy is also susceptibility to stress corrosion cracking. This is due to inhomogeneity of the alloy and inherent residual stresses associated with its fabrication methods.
The formation of these micro segregations (hard precipitates) and inherent residual stresses that are associated with their fabrication methods have serious negative effect on their mechanical properties. Hence, this study is aimed at resolving the problems of micro segregations and inherent residual stresses that are associated with aluminium-zinc for improved service performance. The objectives of the work is to investigate the effects of heat treatment on the microstructure, hardness, tensile strength, and wear properties of aluminium-zinc alloy The earth is being depleted of its natural resources, and it is of absolute importance to retard this destroying trend, which is for engineers to do so. One of the ways of saving the perishing environment is finding ways to contribute towards less energy consumption. One among many of these contributing methods is making fossil fuel killers, e.g., cars, airplanes, etc. lighter which is possible through using lighter metals like aluminum in their structure. One limitation in using a pure light metal may be its lack of strength. But the goal is worth fighting all the obstacles, and this fight is at least as old as the existence of blacksmith who beat a piece of metal to render it stronger.
Among likely candidates for light structure material, is aluminum, to which because of its unique properties, to mention one among many, not showing brittle response under a specific temperature (transition temperature) in contrast to steel1, which makes it an ideal metal for cryogenic conditions, industry and as result research, are showing greater interest. The good thing about this element is its high strength to weight ratio into the bargain2; the drawback is its relatively low strength. These two characteristics make aluminum suitable for low stress applications. But most of engineeringpurposes deal with moderate to high stresses in which pure aluminum may give in. To overcome this, it is an old fashion, as one of the methods of enhancing this metal, to add other elements like copper, manganese, silicon, magnesium, zinc, etc. to it as alloying elements. In addition to alloying elements in the base metal there exist some other interesting strengthening methods such as, microstructure modification (grain size reduction), precipitation hardening, dispersion strengthening, and work hardening. One or combination of these may be applied to alloy depending on its properties and limitations. It seems, from among alloying elements, zinc and magnesium play greater role in giving the aluminum strength. 7xxx aluminum alloys which contain zinc and magnesium, as their main alloying elements in varying amounts (which define the rest of the digits after number 7 in the name of the alloy) have gained the top priority when considering nominees for suitable material for aero-transportation vehicles. For, in the airplane, safety is the main issue, in addition to strength of components, other factors like stress corrosion must be taken into account at the time of designing the components.
All strengthening mechanisms rely on one principle; Hindering movement of dislocations. All existing methods like Strain hardening, precipitation hardening, Hall-Petch effect (grain boundary strengthening), dispersion strengthening, make the alloy stronger by decreasing the degree of mobility of the dislocations3-8. Talking about aluminum, depending on the major alloying element, the contribution of each of the mechanisms differ dramatically. For example, if an aluminum alloy has the copper as its major alloying element (2xxx series of wrought aluminum alloy) it can be precipitation hardened; on the other hand, if copper is superseded by magnesium (5xxx series of wrought aluminum alloy), precipitation strengthening will have negligible contribution towards the yield strength augmentation of alloy. 7xxx aluminum alloys, are called heat treatable alloys as they can be strengthened through precipitation strengthening. One of the notorious shortcomings of precipitation hardened 7xxx alloys is their lack of resistance against stress and exfoliation corrosion. Industry owners and researchers have turned to a special heat treatment called retrogression and re aging to make the stress corrosion to surrender by a great degree.
The optimum properties of aluminium are achieved by alloying additions and heat treatments. This promotes the formation of small hard precipitates which interfere with the motion of dislocations and improve its mechanical properties. One of the most commonly used aluminium alloy for structural applications is 7075 Al alloy due to its attractive comprehensive properties such as low density, high strength, ductility, toughness and resistance to fatigue9-12. It has been extensively utilized in aircraft structural parts and other highly stressed structural applications13-17.
But aluminium-zinc alloy as it is in 7075 Al alloy is susceptible to embrittlement because of micro segregation of MgZn2 precipitates which may lead to catastrophic failure of components produced from it. The alloy is also susceptibility to stress corrosion cracking. This is due to inhomogeneity of the alloy and inherent residual stresses associated with its fabrication methods.
The formation of these micro segregations (hard precipitates) and inherent residual stresses that are associated with their fabrication methods have serious negative effect on their mechanical properties. Hence, this study is aimed at resolving the problems of micro segregations and inherent residual stresses that are associated with aluminium-zinc for improved service performance. The objectives of the work is to investigate the effects of heat treatment on the microstructure, hardness, tensile strength, and wear properties of aluminium-zinc alloy
1.1 OBJECTIVES
To study the micro structural evaluation during heat treatment
To study the effect of micro structure on the hardness, tensile properties and wear properties
-
HEAT TREATMENT
Heat treatment is as an operation involving the heating and cooling of a metal or an alloy in the solid-state to obtain certain desirable properties without change composition. The process of heat treatment is carried out to change the grain size, to modify the structure of the material, and to relieve the stresses set up the material after hot or cold working.
The heat treatment is done to improve the machinability. To improve magnetic and electrical properties.
To increase resistance to wear, heat and corrosion, and much more reason.
Heat treatment consists of heating the metal near or above its critical temperature, held for a particular time at that finally cooling the metal in some medium which may be air, water, brine, or molten salts. The heat treatment processincludes annealing, case hardening, tempering, normalizing and quenching, nitriding, cyaniding, etc
2.1 TYPES OF HEAT TREATMENT PROCESSES
Following are the different types of heat treatment processes: Annealing
Normalizing Hardening Tempering Nitriding Cyaniding
Induction Hardening Flame Hardening
III MATERIALS AND METHOD
Al 7075 alloy (5.66.1% zinc, 2.12.5% magnesium, 1.2 1.6% copper, and less than a half percent of silicon, iron, manganese, titanium, chromium, and other metals. Remaining % Al) billet was secure from Chetan steel, Hyderabad, India as shown in fig 3.1
Fig 3.1Al 7075 Raw Material
Form the cast billet, sample of size 100x100x10 mm3 were machined and subjected to heat treatment as shown in fig
3.2. Since the maximum solubility of Al in Zn is at 4300C by referring to Zn-Al phase diagram, the temperature for solution heat treatment was selected as 4500C. Heat treatment was executed in a box furnace (India) with ± 20C error as shown in fig 3.3
Fig: 3.2 Samples were machined by Using Power Hacksaw
Fig: 3.3 Muffle Furnace
The samples were propping in the furnace, and heat treatment was carried out. Heat treatment cycle that incorporates heating rate, soaking time, and cooling rate espouse for the heat treatment process is shown in Fig 3.4. Cooling was carried out atmospheric air cooling at room temperature. Base alloy and solution treated Al7075 were entitled as Al7075 and HT-Al 7075, respectively
Fig: 3.4 Heat Treatment Process Cycle
-
OPTICAL MICROSCOPE
Specimens of size 10 x 10 x 10 mm3 were cut from the heat-treated samples and base materials for microstructure studies and hardness measurement.
For perceive the microstructures (as shown in fig 4.5) of the samples before and after heat treatment, the abandoned metallographic polishing protocol was espoused, and etching was carried out by using Kellers agent. (Composition: water-95%, Nitric acid-2.5%, Hydrochloric acid-1.5%, Hydrofluoric acid 1%).
Fig: 3.5 Optical Microscope (Leica, Germany)
-
HARDNESS TEST
For hardness measurements (as shown in fig 3.6), Vickers indentation method (at 100 g load) was selected, and measurements were arbitrarily obtained at different locations on the polished surfaces of the samples.
Fig: 3.6 Vickers Hardness (omni tech India)
-
TENSILE TEST
Tensile specimens were prepared according to ASTM-E8 standards as shown in fig 3.7. Mechanical properties were determined using stress-strain curves in uniaxial tensile testing at a strain rate of 0.01/s.
Fig: 3.7 Dimensions of Tensile Test Specimen
-
WEAR TESTING MEASUREMENT
Wear is the removal of material from one or both of two solid surfaces in solid state contact. As the wear is a surface removal event that happens mostly on the outer surfaces, surface modification of current alloys is more appropriate and affordable than employing the wear resistant alloys
-
EXPERIMENTAL PROCEDURE OF WEAR TEST
Dry sliding wear tests for different number of specimen was conducted by using a pin-on-disc machine as shown in fig 3.8
Fig: 3.8 Wear Testing Machine
Wear track diameter of 70 mm held the pin in place on disc counter face (EN31 steel disc). Using a dead weight loading technique, a pin was pressed firmly into the disc. At a sliding velocity of 2 and 3 m/s, all specimens were subjected to the wear test under normal loads of 20 and 30 N.
Under the same conditions stated above, wear tests were conducted for a total sliding distance of about 3000 metres. They were 30 mm long and had a diameter of 12 mm each. Because it is important to have a fresh and level contact surface for testing the pins, they were prepared by being polished with 80-grit emery paper prior to the test. Acetone was used to clean and weigh the samples and wear track before and after each test. Microbalances were used to ensure accuracy to within 0.0001 grammes. The wear rate was determinedusing the height loss method and reported in terms of wear volume loss per sliding distance
The following parameters were used for this experiment:
-
Load
-
Speed
-
Distance
In the present experiment the parameters such as speed, time and load are kept constant throughout for all the experiments. These parameters are given in Table 3.1
Pin material
Al, Al/C, Al/C/3B4C, Al/C/6B4C, Al/C/9B4C
Disc material
EN 31 steel
Pin dimension
Cylinder with diameter 12 mm height 30 mm
Sliding speed (m/s)
2, 3
Normal load (N)
20, 30
Sliding distance (m)
3000
Table3.1 Parameter Taken Constant during Sliding Wear Test
-
-
PIN-ON-DISC TEST
-
Disc testing was performed to characterize tribological properties in this experiment. The following is the method for the tests
Initially, the pin surface was flattened so that it could support the load over its whole cross-section, known as the first stage. In order to achieve this, the pin sample was ground on 80-grit emery paper before testing
The second step of the experiment included a run-in-wear test. The initial turbulence related with friction and wear curves can be avoided at this time.
The third and last stage of testing, known as "constant/steady-state wear," is the most critical phase.
Currently, there is a fierce battle between various methods of transporting materials. (Transfer of material from pin onto the disc and formation of wear debris and their subsequent removal). Prior to the test, both the pin and the disc were cleaned with ethanol-soaked cotton (Surappa et al 2007)
Precautionary measures were made to ensure that the load was applied in the correct direction before to the start of every experiment. Figure 3.9 depicts the Pin-on-Disc configuration in a simplified manner.
Fig: 3.9Schematic Views of the Pin-On-Disk Apparatus
IV. RESULTS AND DISCUSSIONS
-
MICRO STRUCTURE
The microstructure of the samples was characterized by an optical microscope. Fig: 4.1 (a) & (b) shows the optical microstructure of base material Al 7075 and HT- Al 7075 respectively. It reveals a non-dendritic structure. The microstructure consists mainly of the matrix Al () phase and the grain boundaries eutectic (+) phase. The average grain size was measured as 89.93 µm for base materials Al 7075, 59.29 µm for HT- Al 7075.
(a)
Fig (b)
Fig 4.1: show the microstructure (a) base material Al7075 and (b) HT-Al 7075 samples
-
SEM AND EDAX ANALYSIS
The results of the SEM observation and EDAX analysis of HT-Al7075 alloy after heat treatment at 4500C for 4 hours are shown in fig 4.2. These analyses reveals that the lamellar Al2Mg, MgCu2 and MgZn2 phases almost completely disappears and only the insoluble Al2CuMg phases, Al2Cu phases and Al7Cu2Fe phase is left. The EDAX results reveals that the white arrow particles are 37.80% Al, 1.76% Mg, 2.47% Si, 1.60% Ca, 5.79% Fe and
41.79%Cu (weight fraction), which is close to the stoichiometry of Al2CuMg, Al2Cu and Al7Cu2Fe phase.
Fig (a)
Fig (b)
Fig 4.2: (a) SEM observation and (b) EDAX analysis of HT-Al7075 alloy
after heat treatment at 450 for 4 hours
-
HARDNESS AND TENSILE PROPERTIES
Fig 4.3: Hardness Value of the Samples
Fig: 4.3 shows the micro hardness measurements of the samples performed on the sample surface. From the measurements, average values were deliberate and observed as increased after heat treatment 163.14 ± 2.3 HV compared with base alloy 132.058 ± 5.2 HV. The hardness values for heat treatment alloy scarcely increased compared with Al7075. A wide range distribution of hardness values was observed in Al7075 compared with HT-Al7075. The comparison of tensile properties shows the deleterious effect of the grain refinement on the ductility of Al7075 after heat treatment, table 4.1. Tensile properties obtained from the stress stain curves demonstrate the potential of grain refinement on enhancing the yield strength and ultimate tensile strength of Al7075, Figure 5.4.
Table 4.1 Mechanical properties of samples obtained from tensile test after heat treatment
Fig: 4.4 Stress- Strain Curve of the Samples
-
WEAR PROPERTIES
-
SAMPLE CALCULATION FOR WEAR PROPERTIES
Track diameter (D) 70mm = 0.07m Speed(N)=500rpm
Time (T)= 10min
Correctional area of Specimen (A)= 50.26 mm2 Load= 30N
Height loss from graph = 140microns = 0.14mm
Volume loss = height loss x area = 0.14 x 50.26 = 7.0364 mm3
Sliding Distance = x DNT= x0.07x500x10 = 1099 m Wear Rate = Volume loss/ sliding distance = (7.0364/1099)
= 6.403×10-3 mm3/m
Specific wear rate = Wear rate/load = (6.403×10-3 / 30) =
2.134 10-4 mm3/Nm
Wear resistance = 1/ wear rate = 1/ 2.134 10-4 = 156.187 m/mm3
5.122×10
6.403×10
S. No
Samples
Height Loss (mm)
Sliding Distance (m)
Volume Loss (mm3)
Wear Rate (mm3/m)
Wear Resistance (m/mm3)
Specific Wear Rate
(10 mm3/Nm)
1
Al7075
0.047
1099
2.3622
-3
156.187
2.134
2
HT-Al7075
0.112
1099
5.6291
-3
195.23
1.707
TABLE 4.2 Summary of Wear Values of Tested Samples
material
Yield strength (Mpa)
UTS(Mpa)
Al 7075
193.315
386.354
S. No
Samples
Wear Rate (mm3/m)
Wear Resistance (m/mm3)
Specific Wear Rate (10-4 mm3/Nm)
1
Al7075
6.403×10-3
156.187
2.134
2
HT-Al7075
5.122×10-3
195.23
1.707
TABLE 4.3summary of wear properties of tested samples
V.CONCLUSION
Al 7075 alloy was subjected to solution treatment at 4500C for 4 hours to study the role of altering microscope on mechanical properties.
-
After heat treatment, the grain refinement was achieved from 89.93 µm to 59.29 µm. The intermetallic phase was decreased after the heat treatment.
-
Micro structural observation and EDAX analysis of HT-Al7075 alloy confirms the intermetallic phases after heat treatment.
-
Higher hardness was measured for HT-Al7075 lloy that could be attribute to grain size reduction.
-
-
Due to the supersaturated condition with higher yield strength, ultimate tensile strength and wear properties was measured for HT-Al 7075 compared with the Al7075. However, decreased ductility in heat treatment is a significant observation.
Fig 4.5 wear rate of samples
Wear test was conducted on pin on disc machine. Wear rate Vs sample graph was drawn successfully. From the fig 4.5 it was clearly observed that the wear rate decreased from base material Al7075 to after treatment sample HT- Al7075 from 6.403×10-3 mm3/m to 5.122×10-3 mm3/m due to the effect of the grain refinement after the heat treatment.
Fig:4.6 Specific Wear Rate of Samples
Specific wear rate Vs samples graph was drawn successfully from the fig 5.7 it was clearly observed that specific wear rate decreased from base material base material Al 7075 to after treatment HT-Al7075
VI.REFERENCES
[1] Randolph Kissell RLFJ. Aluminum Structures: A Guide to Their Specifications and Design. 2nd ed. John Wiley & Sons, Inc; 2002. 544 p. [2] Chen Q, Lin S, Yang C, et al. Grain fragmentation in ultrasonic assisted TIG weld of pure aluminum. UltrasonSonochem. 2017; 39:403413. [3] Hatch JE. Aluminum Properties and Physical Metallurgy. ASM International; 1984. [4] Kaufman JG. Introduction to Aluminum Alloys and Tempers.ASM International; 2000.
[5] Argon AS. Strengthening Mechanisms in Crystal Plasticity.Oxford University Press; 2008.
[6] Whang SH. Nanostructured metals and alloys. Woodhead Publishing; 2011. [7] Rouhi S, Mostafapour A, Ashjari M, et al. Effects of welding environment on microstructure and mechanical properties of friction stir welded AZ91C magnesium alloy joints. Science and Technology of Welding and Joining. 2016;21(1):2531. [8] Ashjari M, Mostafapour Asl A, Rouhi S, et al. Materials Science and Engineering: A. 2015;645:4046. [9] Heinz A and Haszler A. Recent development in aluminum alloys for aerospace applications. Materials Science and Engineering A. 2000; 280(1):102-7. http://dx.doi.org/10.1016/S0921-5093(99)00674-7
[10] Williams JC and Starke Junior EA. Progress in structural materials for aerospace systems. Acta Materialia. 2003; 51(19):5775-99. http://dx.doi.org/10.1016/j.actamat.2003.08.023 [11] Clark R, Coughran B, Traina I, Hernandez A, Scheck T, Etuk C et al. On the correlation of mechanical and physical properties of 7075-T6 Al alloy. Engineering Failure Analysis. 2005; 12:520-6. http://dx.doi.org/10.1016/j. engfailanal.2004.09.005 [12] Li JF and Peng ZW. Mechanical properties, corrosion behaviours and microstructures of 7075 aluminium alloy with various aging treatments. Transactions of Nonferrous Metal Society of China. 2008; 18(4):755-62. http://dx.doi.org/10.1016/S1003-6326(08)60130-2
[13] Woei-Shyan LS and Wu-Chung S. The strain rate and temperature dependence of the dynamic impact properties of 7075 aluminum alloy. Journal of Materials Process and Technology. 2000;100:116-22. http://dx.doi.org/10.1016/S0924-0136(99)00465-3
[14] Lin G, Zhang H, Zhang X, Han D, Zhang Y and Peng D. Influences of processing routine on mechanical properties and structures of 7075 aluminium alloy thick plate. Transactions of Nonferrous Metal Society of China. 2003; 13(4):809-13. [15] Shwe WHA, Kay TL and Waing KKO. The effect of ageing treatment of aluminum alloys for fuselage structure-light aircraft. World Academy of Science, Engineering and Technology. 2008; 46:696-9. [16] Zhao T and Jiang Y. Fatigue of 7075-T651 aluminum alloy. International Journal of Fatigue. 2008; 830:834-849. http://dx.doi.org/10.1016/j.ijfatigue.2007.07.005 [17] Mohammad T and Esmail E. Mechanical and anisotropic behaviours of 7075 aluminum alloy sheets. Materials and Design. 2010, 32(2):1594-9.http://dx.doi.org/10.1016/j.matdes.2010.09.001
[18] Ma K, Wen H, Hu T, et al. Mechanical behaviour and strengthening mechanisms in ultrafine grain precipitation strengthened aluminum alloy. Acta Materialia. 2014;62(1):141 155. [19] Xu X, Zhao Y, Wang X, et al. Materials Science and Engineering: A.2015;648:367370. [20] Chen J, Zhen L, Yang S, et al. Investigation of precipitation behaviour and related hardening in AA 7055 aluminum alloy. Materials Science and Engineering: A. 2009;500(12):3442. [21] Xu X, Zhao Y, Wang X, et al. Materials Science and Engineering: A. 2016;654:278281. [22] Nie XW, Zhang LJ, Du Y. Experiments and modelling of double- peak precipitation hardening and strengthening mechanisms in Al-Zn-Mg alloy. Transactions of Nonferrous Metals Society of China. 2014;24(7):21382144. [23] Yang W, Ding H, Mu Y, et al. Materials Science and Engineering: A. 2017;707:193198.