
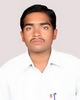
- Open Access
- Authors : Pravin Vyavahare , Bharat Admile , S G Kulkarni
- Paper ID : IJERTV10IS040283
- Volume & Issue : Volume 10, Issue 04 (April 2021)
- Published (First Online): 04-05-2021
- ISSN (Online) : 2278-0181
- Publisher Name : IJERT
- License:
This work is licensed under a Creative Commons Attribution 4.0 International License
Mechanical Characterization of Stir Cast Al 356-B4C Composite
Pravin Vyavahare1, Bharat Admile2, S G Kulkarni3
#Dept. of Mechanical Engg, SKNSCOE, Solapur Univercity
Abstract:- The development of light weight material for industrial utilities attracted Aluminum composites as this material have superior mechanical properties over unreinforced alloy. The present investigation focused on utilization of boron carbide into Al356 alloy fabricated by stir casting. The Boron Carbide particle weight fractions of 3, 6,9, 12 % wt. of particle sizes 53-
106 m were reinforced into matrix material. The scanning electron microscopy (SEM) was done to see distribution of the B4C particles in the matrix. The evaluation of mechanical properties viz; tensile strength, compressive strength, density and hardness were carried out. It was found that the tensile strength, compressive strength and hardness of the metal matrix composite (MMC) increases as weight fractions of the B4C particles increases. Also density of composite decreases subsequently. So boron carbide has potential to fabricate strengthened metal matrix composite for diverse Al alloy applications.
Keywords MMC, Stir casting, B4C, Al356, SEM, Hardness.
-
INTRODUCTION
Metal matrix composites (MMCs) are the combination of metal matrix & reinforcement or filler material which gives excellent mechanical properties and they are classified according to reinforcement type or its content. MMCs have ability to achieve any combination of stiffness, strength and density. The principal matrix materials for MMCs are Aluminium and its alloys. The major advantage of aluminium matrix composites over other material such as steel are, increased specific strength and stiffness, lower thermal coefficient of expansion, wear resistance, lower density and good corrosion resistance.
Metal matrix composites (MMCs) have received substantial attention due to their excellent strength, stiffness, lighter and wear resistance for tribolgological, aerospace and marine industries. Though MMCs possess superior properties, they have not been widely applied due to the complexity of fabrication. The conventional stir casting is convenient processing method for fabrication, as it is relatively inexpensive and offers wide selection of materials and processing conditions1. Stir casting offers better matrix particle bonding due to stirring action of particles into molten Aluminum. Among various reinforced used, Boron Carbide particulate reinforced aluminium composites possess a unique combination of high specific strength, high elastic modulus, good wear resistance and good thermal stability than the corresponding non-reinforced matrix alloy system. Hence, composites with boron carbide as reinforcement are possible to overcome the cost barrier and weight for wide spread applications in Bullet proof tees and armor tank.
Manufacturing of aluminium composite by stir casting is one of the most economical methods of processing MMC. In
this project silicon carbide and boron carbide particulate reinforced aluminum alloy matrix composites are produced by stir casting process by varying the particulate addition by weight fraction of Al (90%), Sic (5%, 6.5%, 8%) and B4C
(5%, 3.5%, 2%). Micro structural changes of the cast composites are studied by using metallurgical microscope and scanning electron microscope (SEM) [1]. The paper is the result of investigations made on microstructure and mechanical behavior of 3 and 6 weight percentage of nano sized B4C particulate reinforced to Al7075 alloy composites. Al7075 matrix composite having nano boron carbide was fabricated by liquid stir casting method [2]. Metal Matrix Composites (MMCs) have been widely investigated and used in automobile and aerospace industries due to their advantages of improved strength, stiffness and increased wear resistance over the monolithic alloys. Also considering limited reports on the study of weight % influence on wear characteristics of Al- 6061-Boron Carbide (B4Cp) composites. This study presents the effect of weight % of B4Cp in Al-6061 alloy matrix on wear loss during dry sliding wear in pin-on-disc tribometer at different wear parameters against oil hardened non-shrinking (OHNS) steel disk at room temperature. The composites are prepared by stir casting technique. Tribological investigations were examined according to the L9 orthogonal array of Taguchi. The influence of % of reinforcement along with load, speed and distance were examined for the wear loss of composites [3]. Boron carbide is one of the potential neutron- shielding materials and its use can be maximized for structural shielding application by dispersing it into metal matrixes such as aluminum. Dispersion of B4C and its interfacial stability is a major issue during its processing. This investigation is on the synthesis of B4C-reinforced 6061 aluminum matrix composite by liquidmetal stir-casting technique under optimized conditions after solving the issues related to the processing, and evaluation of the structural, mechanical, and interfacial characteristics. During processing of composites, pretreatment of B4C particles is necessary to improve its dispersion [4]. Aluminium matrix composites (AMCs) reinforced with Nano-sized MgO particles are widely used for high performance applications such as automotive, military, aerospace and electricity industries because of their improved physical and mechanical properties. In this research, Magnesium Oxide (MgO) Nano particles were synthesized by Solution Combustion Synthesis process. The Nano particles were characterized by Powder X-ray diffraction (PXRD). A356.1 Aluminum alloy was reinforced with 0.5, 1.0, 1.5 and
2.0 Wt.% of the Synthesized Magnesium Oxide Nano particle, via Stir casting Technique. [5]
-
EXPERIMENTATION
-
Specimen Preparation
B4C reinforced Aluminum alloy (Al356) composites, processed by stir casting route was used in this work. The three types of stir cast composites had a reinforcement particle size of 53-106 m each. The required quantities of Boron carbide (3, 6, 9 and 12 Wt. %) were taken in powder containers. Then the Boron carbide was heated to 4500 C and maintained at that temperature for about 20 min. then weighed quantity of Al 356 alloy was melted in a crucible at 8000 C which is more than 1000 C above liquidus temperature of the matrix alloy. The molten metal was stirred for 10 minutes to create a vortex and the weighed quantity of preheated Boron carbide particles were slowly added to the molten alloy. A small amount of Mg (1 wt. %) was added to ensure good wettability of Boron carbide particles with molten metal. After mixing the composite melt was poured into mould for the preparation of specimen.
Table 1 shows the chemical composition of the Al 356, Table 2 shows its mechanical properties and Table 3 shows the major chemical composition of the Boron carbide.
Fig. 1 shows stir casting set up and specimen.
Fig. 1 Stir casting set up and specimen
TABLE 1 CHEMICAL COMPOSITION OF THE Al 356
Composition
Si
Fe
Cu
Mn
Zn
Mg
Ti
Al
Wt.%
7.24
0.26
0.17
0.24
0.10
0.43
0.05
Bal
TABLE 2 MECHANICAL PROPERTIES OF AL356
Tensile strength (N/mm2)
Elongation
%
Hardness (BHN)
UT
(N/mm2)
151.27
2.2
93
151.27
Molecular Formula
B4C
Molar mass
55.255 g/mol
Density
2.52 g/cm3, solid.
Melting point
2,763 °C (5,005 °F; 3,036 K)
Boiling point
3,500 °C (6,330 °F; 3,770 K)
Acidity (pKa) 67 (20 °C)
67 (20 °C)
Appearance
Dark Gray or Black Powder, odourless
Solubility in water
Insoluble
Molecular Formula
B4C
Molar mass
55.255 g/mol
Density
2.52 g/cm3, solid.
Melting point
2,763 °C (5,005 °F; 3,036 K)
Boiling point
3,500 °C (6,330 °F; 3,770 K)
Acidity (pKa) 67 (20 °C)
67 (20 °C)
Appearance
Dark Gray or Black Powder, odourless
Solubility in water
Insoluble
TABLE 3 PROPERTIES OF BORON CARBIDE
-
Mechanical Testing of Composites
Microstructural analysis done by XRD & SEM with standard metallographic process to check uniform distribution of reinforcement of B4C into Aluminium. The tensile tests were conducted on MMC samples according to BS1490 at room temperature, using a universal testing machine. The specimens used were of diameter 13 mm and Gauge length 62 mm, machined from the cast composites with the gauge length of the specimen parallel to the longitudinal axis of the castings. The wear tests were conducted as per ASTM-G99 using pin- on-disc set up. The specimens used were of diameter 10 mm, and length 100 mm machined from cast composites. The Brinell hardness tests were conducted in accordance with the ASTM E10. Density measured as per BS EN1706:1998/BS 1490:1988 in laboratory
-
-
RESULT AND DISCUSSION
-
Microstructure Analysis
As the microstructure plays an important role in the overall performance of a composite and the physical properties depend on the microstructure, reinforcement particle size, shape and distribution in the matrix alloy. Prepared samples were examined using a Scanning Electron Microscope (SEM) to study the distribution pattern of Boron carbide in the matrix.
Fig. 2 Microscopic views of 3% Boron Carbide reinforced in Al356 at 100 X
Fig. 3 Microscopic views of 6% Boron Carbide reinforced in Al356 at 100X
Fig. 4 Microscopic views of 9% Boron Carbide reinforced in Al356 at 100 X
Fig. 5 Microscopic views of 12% Boron Carbide reinforced in Al356 at 100 X
The microstructure of MMCs clearly shows a uniform distribution of Boron Carbide in the matrix (Fig 2, 3, 4 and 5) with no void and discontinuities observed. There was good interfacial bonding between the Boron carbide particles and matrix material. However, in few composites the particle clustering occurred in some places, and also some places were identified without Boron Carbide inclusion. During fabrication, the particles were added into the molten alloys was observed to be floating on the surface.
-
Density
Density values of the Boron Carbide composites decreases linearly with addition of Boron Carbide particles. The decrease in density of composites can be endorsed to lower density of Boron Carbide particles (1.9 g/cc) than that of the unreinforced Al alloy (2.76 g/cc). The level of density increases with Boron Carbide wt% as shown in Fig. 6
Density in (kg /cm3)
Density in (kg /cm3)
150
150
100
95.84
64.17
100
95.84
64.17
50
20.79
36.64 36.19
50
20.79
36.64 36.19
0
0
1
2
3
4
5
1
2
3
4
5
Fig. 6 Variation of Density with wt fraaction of Boron Carbide
-
Ultimate Tensile Strength
The tensile testing of the composite was done, on Universal testing machine to evaluate tensile properties.
Fig. 7 Variation of UTS with wt fraaction of Boron Carbide
The tensile strength increased with an increase in the weight percentage of Boron Carbide. Therefore the Boron Carbide particles act as barriers to the dislocations when taking up the load applied .Good bonding of smaller size Boron Carbide particles with the matrix is the reason for this behaviour. The tensile strength improves from 154.27 to
186.65 Mpa, which is almost 20% improvement. The decrease in the tensile strength of the samples with Boron Carbide weight fraction beyond 5 % is due to the poor wettability of the reinforcement with the matrix and due to clustering of the reinforcement particles the composite.
-
Wear Strength
Samples are prepared with (L/D) ratio as 10.0, so length of specimen is 100 mm and diameter is 10 mm and 6mm. Further samples are polished to achieve flat surfaces with emery paper.
Table 4. Variation of Initial wt. and Final wt.
Sr.
No.
Sample Name
Initial Wt. (gm)
Final Wt. (gm)
Wt. difference (gm)
1.
As cast
18.432
18.420
0.012
2.
B4C-3%
18.485
18.470
0.015
3.
B4C-6%
17.327
17.320
0.007
4.
B4C-9%
17.684
17.670
0.014
5.
B4C-12%
17.088
17.080
0.008
Wear test determines load applied 20N and 250 RPM of time limit 10 minutes . The observe the initial weight of pin sample before use of test. For wear test for removing material and final weight observe shown in Fig 7.
Wear strength increases with increasing percentage of Boron Carbide particulates. However the Wear strength of the composites begins to drop when the Boron Carbide content increased. Beyond 9 wt%, the Boron Carbide particles interact with each other of compare to base metal matrix composite .
-
Hardness
Samples are tested as per as per STD BS EN1706:1998/BS 1490:1988. For Brinell hardness test surface being tested generally requires metallographic surface finish
and it was done with help of 100, 220, 400, 600 and 1000 grit size emery papers.
Fig. 9 Variation of BHN with wt fraction of Boron Carbide
The results of the hardness test (Fig 9) show increase in hardness with the weight fraction of Boron Carbide. It shows that hardness increases by almost 11% in 16% Boron Carbide composite as compared with Al alloy.
-
-
CONCLUSIONS
-
Addition of boron carbide increases mechanical properties of composites..
-
Hardness of composite increases with increase in boron carbide percentage.
-
Tensile properties of Al-B4C composite increases with increase in boron carbide.
-
The mechanical properties viz; tensile, hardness etc increase due to hard boron carbide particle.
-
Wear resistance of Al-B4C composite increases due to presence of hard boron carbide particle.
-
Due to stirring, grain refinement helps to increase mechanical properties.
-
From microstructure study, uniform dispersion of B4C particle enhances mechanical strength of composites.
REFERENCES
-
M .D. Antony Arul Prakash, M. Arockia Jaswin, Microstructural Analysis Of Aluminum Hybid Metal Matrix Composites Developed Using Stir Casting Process, 2015, International Journal of Advances in Engineering, 1(3), PP 333 339.
-
T H Manjunatha, Dr. Yadavalli Basavaraj, Madeva Nagaral, Dr. V Venkatraman, Jayashree I Harti, Investigations on Mechanical Behavior of Al7075 – Nano B4C Composites,2018, IOP Conf. Series: Materials Science and Engineering 376 012091 doi:10.1088/1757-899X/376/1/012091,PP 1-6.
-
B Manjunatha, H.B.Niranjan And K.G.Satyanarayana, Effect Of Amount Of Boron Carbide On Wear Loss Of Al-6061 Matrix Composite By Taguchi Technique And Response Surface Analysis,2018, IOP Conf. Series: Materials Science and Engineering 376 012071 doi:10.1088/1757-899X/376/1/012071,PP 1-12.
-
V.P. Mahesh, Praseeda S. Nair, T.P.D. Rajan, B.C. Pai And R.C. Hubli, Processing Of Surface-Treated Boron Carbide-Reinforced Aluminum Matrix Composites By Liquid Metal Stir-Casting Technique,2011, Journal of Composite Materials 45(23) DOI: 10.1177/0021998311401086, PP 23712378.
-
Mr.Praveen.G, Mr.Girisha.K.B, Mr.Yogeesha.H.C, Synthesis, Characterization and Mechanical Properties of A356.1 Aluminum Alloy Matrix Composite Reinforced With Mgo Nano Particles, June 2014, International Journal of Engineering Science Invention ISSN (Online): 2319 6734, ISSN (Print): 2319 6726 www.ijesi.org Volume 3 Issue 6 , PP.53-59.
-
Raghavendra MJ , Praveen Kumar K , Arun R, Arjun S, A Study on Microstructure and Characterization of Aluminum 7075 Metal Matrix Reinforced With Silicon Carbide Particles Using Stir Casting Method, Dec 2017, IJRET: International Journal of Research in Engineering and Technology ISSN: 2319-1163 | ISSN: 2321-7308 Volume: 06 Issue: 12 , PP 89-95.
-
Ashish K Srivastava, Amit Rai Dixit And Sandeep Tiwari, Investigation Of Micro Structural And Mechanical Properties Of Metal Matrix Composite A359/B4C Through Electromagnetic Stir Casting,2015,Indian Journal of Engineering and Material Sciences Vol.23,PP 171-180.
-
T.B Prasad, Sridhar, H.S., Development And Characterization Of A356 Alloy Reinforced With Bottom Ash Metal Matrix Particulate Composite For Automotive Application: A Review, October 2016, International Journal of Innovative Research & Development www.ijird.com , Vol 5 Issue 11,PP 165-168.
-
A. Devaraju and K. Pazhanivel, Evaluation of Microstructure, Mechanical and Wear Properties of Aluminum Reinforced With Boron Carbide Nano Composite, May 2016, Indian Journal of Science and Technology, Vol 9(20), DOI: 10.17485/ijst/2016/v9i20/84294 , PP 1-6.
-
S. Rama Rao, G. Padmanabhan, Fabrication and Mechanical Properties of Aluminum-Boron Carbide Composites,2012, International Journal of Materials and Biomaterials Applications, 2(3), PP 15-18.
-
N Subramanian, K Vijayaraghavan, V.V.Arunsankar, K. Sudha, Analysis And Investigation on A2024 Metal Matrix Composites With B4c And Graphite ,September 2013, International Journal of Innovative Research in Science, Engineering and Technology Vol. 2, Issue 9,ISSN: 2319-8753, PP 4636-4642.
-
Mr. N.Venkat Kishore, Dr. K.Venkata Rao, Mechanical Properties in MMC of Aluminium Alloy (A356/LM25) Matrix and Boron Carbide (B4C) Reinforcement, February 2016, International Journal of Engineering Research & Technology (IJERT) ISSN: 2278- 0181,Vol. 5 Issue 02,PP 683-689.
-
K.P.Reddy,K.Kumar,Linga Raj, Effect of Heat Treatment on Mechanical Properties of A356 Reinforced With Boron Carbide Composites, April 2016, International Journal of Engineering And Science, Vol.6, Issue 4, Issn (e): 2278-4721, ISSN : 2319-6483 , PP 112-123.
-
Manish Maurya, Nagendra Kumar Maurya, Fabrication of A359 Alloy Reinforced With B4C Particulates & Characterization of Mechanical Properties, December 2017, International Journal of Advance research and Science and Engineering, Volume No.6, Special Issue No.(02) ,ISSN:2319-8354,PP 532-538.
-
Akhilesh Jayakumar, Mahesh Rangaraj, Property Analysis of Aluminium (LM-25) Metal Matrix Composite, February 2014, International Journal of Emerging Technology and Advanced Engineering, Volume 4, Issue 2, ISSN: 2250-2459,PP 495-501.
-
S. Sathishkumar, Fabrication and Analysis of Aluminium with Graphite Reinforcement Based Metal Matrix Composites,2017, Journal of Mechanical Engineering Research and Developments, Vol. 40, No. 3, ISSN: 1024-1752, PP. 456-464.
-
Prashanth K Mulge, Sunil Mangshetty, A Study of optimize the casting process Parameters of Al 365/LM25 Alloy using Taguchi Technique, June 2015, International Journal of Engineering Research and Technology (IJERT),Vol 4 Issue 06, ISSN: 2278-0181, PP 382-389.
ACKNOWLWDGEMENT
I express my deep sense of regard and gratitude towards technical staffs & Co-aids at SKN Sinhgad COE, Pandharpur for composite fabrication for SEM & EDS of composite specimens.