
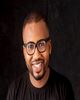
- Open Access
- Authors : Kolawole D. Olanipekun
- Paper ID : IJERTV10IS120094
- Volume & Issue : Volume 10, Issue 12 (December 2021)
- Published (First Online): 07-01-2022
- ISSN (Online) : 2278-0181
- Publisher Name : IJERT
- License:
This work is licensed under a Creative Commons Attribution 4.0 International License
Mechanical Property Characterisation of Groundnut Fibre Reinforced Polyethylene
Kolawole D.Olanipekun
Ex-Undergraduate Student, Department of Metallurgical & Materials Engineering University of Lagos, Akoka, Yaba, Lagos, Nigeria
Abstract Recently, thermoplastic and thermoset polymers are combined with natural fillers to produce the composites, which possess better strength and good resistance to fracture. Composites, the wonder material with light-weight; high strength-to-weight ratio, stiffness properties and controlled anisotropy have emerged as a major class of structural elements and are either used or being considered as substitutions for metals/traditional material like metals, wood etc. Accordingly, manufacturing of high-performance engineering materials from renewable resources has been pursued by researchers across the world owning to renewable raw materials are environmentally sound and do not cause health problem. This present work aims to elucidate the mechanical (tensile, hardness and impact) and morphological properties of untreated groundnut shell reinforced Low density Polyethylene composites to suit a wider application. The composite specimens were prepared with different weight percentages (100, 95, 92.5, 90, 85 & 80%) with uniformly distributed groundnut shell particles in polymer matrix with the aid of a locally fabricated automated compounding polymeric mixer. The mechanical properties of the developed composite were investigated. Scanning electron microscopy was used to examine the microstructure and degree of bonding of the composites. The results revealed that all mechanical properties except the Tensile strength and Ultimate tensile strength did not increase uniformly with additions in filler but exhibited maximum properties at specific percentages of filler additions. However, the use of the compounding mixer enhanced the bonding and uniform blending of the composites. The results revealed that using groundnut shell particles as reinforcement for polymer matrix could successfully develop beneficial composites.
KeywordsMetal Matrix Composites(MMC), Ceramic Matrix Composites(CMC), Polymer Matrix Composites(PMC), low Density Polyethylene Composites(LDPC),Polymeric Compounding Mixer(PCM), High Density Polyethylene (HDPE), Carbonized Bone Particles (CBp), Groundnut Shell-high Density Polyethylene(EGR), Coconut Shell-High Density Polyethylene(ECO), Palm kernel Shell- High Density Polyethylene(EPK), Scanning Electron Microscopy (SEM), X-ray Diffraction (XRD).
I. INTRODUCTION
In the last three decades polymer composites (PMCs) have been of interest to industry and researchers, partially in the areas of automotive, aerospace, electronic systems, medical products, civil construction, chemical industries, and consumer appliances (Capiati et al 1975). This interest is driven by properties and qualities such as high strength to weight ratio, good electrical insulation, non-corrosive, ability to transfer load, easy and inexpensive processing. etc ( Chawler, 1987; Shalin, 1995). Fiber reinforcement represents physical rather than a chemical means of changing a material to suit various engineering applications (Móczó et al, 2008). While, particle fillers are employed to improve high temperature performance, reduce friction, increase wear resistance and to reduce shrinkage (Saha et al, 2007). The particles also share the load with the matrix, but to a lesser extent than a fiber (Chawler, 1987). Particle reinforcements are therefore used to improve stiffness but not generally to strengthen (Farrel et al, 1996).. From the mechanical point of view it cannot be said that the incorporation of fillers in polymer matrix is always positive effects. For example, elastic modulus, hardness and wear resistance can lead to deterioration of tensile strength and ductility deteriorated. Some properties can be evaluated as a priority with sufficient accuracy (elastic modulus); however the processing technique that is used has a lot to do with the actual property values obtained. The strain to failure, for example, is very sensitive to defects that can easily be introduced into the material during processing. The aggregates are also an element of discontinuity in the material, which determines the deterioration of some important mechanical properties, such as impact resistance; the formation of aggregates must be prevented from forming during processing. In this field, experience has shown that the physical and mechanical characteristics of the composite depend, in addition to the properties of the individual components, the size, the shape and degree of dispersion of the particles, as well as the degree of accession between the latter, and the polymer matrix (Móczó et al, 2008).
With the growing demand of particles reinforcement polymer matrix composites, economic competition and ecological pressure, there is an increasing need to synthesis particles reinforcement polymer matrix composites from a cost effective source and by a cheap method. The incorporation of particle fillers in a polymer matrix can bring about dramatic changes in the properties of polymer matrix. To produce a PMC which has good properties by using particle reinforcement, a narrow particle size distribution, high surface area and homogenous dispersion should be achieved. Without a good proper dispersion of the nano or micro particles in the composite, filler aggregates would act as defective sites; these defective sites (agglomerates and segregation) limit the mechanical performance (Móczó et al, 2008). In order to acquire a good dispersed composite with separated particles, the manner of combining polymers and particles should be considered as the most important key to gain the desired material properties (saira et al 2007). For dispersing the particles in polymer, mechanical alloying has been established as a good processing tool which breaks up agglomerates and distribute filler particles homogeneously in the polymer (Escobar et al, 2005). This unique capability
of mechanical alloying using a polymeric compounding mixer is a reason for choosing mechanical alloying as a processing technique for this work.
A composite can be defined as a heterogeneous substances consisting of two or more materials of notably different physical properties which do not lose their characteristics or the identity of each component. The constituents of the composite – the REINFORCEMENT which is the strong load carrying material embedded in the weaker material known as the MATRIX retain their individual and chemical properties, yet together they produce a combination of qualities which individual constituents are incapable of producing. The reinforcement provides strength and rigidity, helping to support the structural load while the matrix maintains the position and orientation of the reinforcement.
The advantage of composites over their conventional counterparts is the ability to meet diverse design requirements with significant weight savings as well as strength-to-weight ratio.
2.0. SOME CONCEPTS & TESTS RELATED TO MECHANICALLY REINFORCED MATERIALS
-
Polymeric Compounding Mixer (PMC)
Is a mechanically automated chamber for blending polymeric formulations or polymers and additives in a molten state
.Homogeneous blend, dispersive and distributive mixing and heat are important factors. (John of Reading, 2014).
-
Electric Motor
Electric motors take almost as many different forms as mixers. Motors can be classified by size, power source, enclosure, and even application. An essential part of any electric motor is the name plate. Without the informatio found on a nameplate, most motors look like a cylindrical or rectangular housing with wires leading in and a rotating shaft coming out. Understanding the information on a motor nameplate will help identify an existing motor or specify a new motor. Although some information is unique to individual manufacturers, much of the information is essential for proper operation and application of a motor.
-
Impact Testing
A metal may be very hard (and therefore very strng and yet be unsuitable for applications in which it is subjected to sudden loads in service. Materials behave quite differently when they are loaded suddenly than when they are loaded more slowly as in tensile testing. Because of this fact, impact test is considered to be one of the basic mechanical tests (especially for ferrous metals). The term brittle fracture is used to describe rapid propagation of cracks without any excessive plastic deformation at a stress level below the yield stress of the material. Metals that show ductile behaviour usually can, under certain circumstances, behave in a brittle fashion. The stress needed to cause yield rises as the temperature falls. At very low temperatures, fracture occurs before yielding. Impact tests are used not also to measure the energy absorbing capacity of the material subjected to sudden loading; but also to determine the transition temperature from ductile to brittle behaviour.
-
Hardness Test
Hardness is the property of a material that enables it to resist plastic deformation, usually by penetration. However, the term hardness may also refer to resistance to bending, scratching, abrasion or cutting. Hardness is not an intrinsic material property dictated by precise definitions in terms of fundamental units of mass, length and time. A hardness property value is the result of a defined measurement procedure. There are three principal standard test methods for expressing the relationship between hardness and the size of the impression, these being Brinell, Vickers, and Rockwell. For practical and calibration reasons, each of these methods is divided into a range of scales, defined by a combination of applied load and indenter geometry.
-
Rockwell Hardness Test
The Rockwell hardness test method consists of indenting the test material with a diamond cone or hardened steel ball indenter. The indenter is forced into the test material under a preliminary minor load usually 10 kgf. When equilibrium has been reached, an indicating device, which follows the movements of the indenter and so responds to changes in depth of penetration of the indenter is set to a datum position. While the preliminary minor load is still applied an additional major load is applied with resulting increase in penetration. When equilibrium has again been reached, the additional major load is removed but the preliminary minor load is still maintained. Removal of the additional major load allows a partial recovery, so reducing the depth of penetration. The permanent increase in depth of penetration, resulting from the application and removal of the additional major load is used to calculate the Rockwell hardness number.
Advantages of the Rockwell hardness method include the direct Rockwell hardness number readout and rapid testing time. Disadvantages include many arbitrary non-related scales and possible effects from the specimen support anvil (try putting a cigarette paper under a test block and take note of the effect on the hardness reading! Vickers and Brinell methods don't suffer from this effect).
-
Rockwell Superficial Hardness Test
The Rockwell Superficial hardness test method consists of indenting the test material with a diamond cone (N scale) or hardened steel ball indenter. The indenter is forced into the test material under a preliminary minor load usually 3 kgf. When equilibrium has been reached, an indicating device that follows the movements of the indenter and so responds to changes in depth of penetration of the indenter is set to a datum position. While the preliminary minor load is still applied an additional major load, is applied with resulting increase in penetration. When equilibrium has again been reached, the additional major load is removed but the preliminary minor load is still maintained. Removal of the additional major load allows a partial recovery, so reducing the
depth of penetration. The permanent increase in depth of penetration, resulting from the application and removal of the additional major load is used to calculate the Rockwell Superficial hardness number.
-
The Brinell hardness Test
The Brinell hardness test method consists of indenting the test material with a 10 mm diameter hardened steel or carbide ball subjected to a load of 3000 kg. For softer materials the load can be reduced to 1500 kg or 500 kg to avoid excessive indentation. The full load is normally applied for 10 to 15 seconds in the case of iron and steel and for at least 30 seconds in the case of other metals. The diameter of the indentation left in the test material is measured with a low powered microscope. The Brinell harness number is calculated by dividing the load applied by the surface area of the indentation.
The diameter of the impression is the average of two readings at right angles and the use of a Brinell hardness number table can simplify the determination of the Brinell hardness. A well-structured Brinell hardness number reveals the test conditions, and looks like this, "75 HB 10/500/30" which means that a Brinell Hardness of 75 was obtained using a 10mm diameter hardened steel with a 500 kilogram load applied for a period of 30 seconds. On tests of extremely hard metals a tungsten carbide ball is substituted for the steel ball. Compared to the other hardness test methods, the Brinell ball makes the deepest and widest indentation, so the test averages the hardness over a wider amount of material, which will more accurately account for multiple grain structures and any irregularities in the uniformity of the material. This method is the best for achieving the bulk or macro- hardness of a material, particularly those materials with heterogeneous structures.
-
Vickers Hardness Test
The Vickers hardness test method consists of indenting the test material with a diamond indenter, in the form of a right pyramid with a square base and an angle of 136 degrees between opposite faces subjected to a load of 1 to 100 kgf. The full load is normally applied for 10 to 15 seconds. The two diagonals of the indentation left in the surface of the material after removal of the load are measured using a microscope and their average calculated. The area of the sloping surface of the indentation is calculated. The Vickers hardness is the quotient obtained by dividing the kgf load by the square mm area of indentation.
When the mean diagonal of the indentation has been determined the Vickers hardness may be calculated from the formula, but is more convenient to use conversion tables. The Vickers hardness should be reported like 800 HV/10, which means a Vickers hardness of 800, was obtained using a 10 kgf force.
Several different loading settings give practically identical hardness numbers on uniform material, which is much better than the arbitrary changing of scale with the other hardness testing methods. The advantages of the Vickers hardness test are that extremely accurate readings can be taken, and just one type of indenter is used for all types of metals and surface treatments. Although thoroughly adaptable and very precise for testing the softest and hardest of materials, under varying loads, the Vickers machine is a floor standing unit that is more expensive than the Brinell or Rockwell machines.
3.0 MATERIALS AND METHODOLOGY
-
Introduction
Below are summarised procedures of the design and fabrication of the Polymeric compounding mixer, materials acquisition, casting of the reinforced composites and characterisation of the sampls produced.
-
Equipment
The apparatus that were used in the course of this research work are:
Polymeric Compounding Mixer, Weighing balance, wooden moulds, hand trowel, Ceramic electric cooker, hand gloves, standard sieves, Universal testing machine, Izod testing machine, Brinell hardness testing machine, Scanning electron microscope
-
Materials
The materials that were used in the course of this study include: Low density Polyethylene (LDPE) and groundnut shell.
-
Design of Polymeric Compounding Mixer
Determination of volume of mixer: Summation of the different volumes of the Standard specimen size of the mechanical tests( bend, fatigue, flexural strength, tensile and impact tests) to be carried on
[ all the volumes of test specimen] = 3.359 × 104 (M)= V Additional 20% of total volume for tolerance = 20%V*V= V + 20%V
3 = (where = required volume and = total volume calculated)
4
Determination of work done by stirrer
Heat energy ( J ) from Heater band + Work done by stirrer ( J )= Mc ( J ) + Heat Loss ( J )
(I V T)b + Work done by stirrer =
+ (13)
1 + 3
1 3
(Where b = heater band, m= mixer, k1= conductivity of heater band,K3= conductivity of mixer, A= curved surface area of mixer, X1= thickness of heater band X3= thickness of mixer T1= temperature of heater band T3= temperature of mixing chamber )
Figure 1: Different Views of the Polymeric Compounding Mixer System
-
Procedures
-
Cleaning of groundnut shell.
Figure 2: Assembled View of the Polymeric Compounding
LDPE (%)
Groundnut shell (%)
100
0
95
5
90
10
85
15
80
20
LDPE (%)
Groundnut shell (%)
100
0
95
5
90
10
85
15
80
20
Table 1: Values of weight of LDPE and reinforcement
The groundnut shells were washed to remove any dirt and sun-dried for some days before grinding. The grinded particulates were sieved with a hand sieve size of 80 microns in the laboratory.
Weighing of the Groundnut shell-LDPE matrix composite
-
Weighing of the polyethylene pellets
The polyethylene pellets were weighed using an electronic weighing machine. A beaker is placed on the weighing machine and the pellets are added gradually into the beaker, the weight indication is observed as more LDPE pellets are continually added. Pouring of the pellets into the beaker is stopped when the desired weight for a particular formulation is achieved. The beaker is removed from the weighing machine and is placed aside.
The formulation used for the pellets is given below
The total volume of the mixing chamber is given to be 1700cm3 20% of this volume is calculated = 340cm3q
The weight of the charge must not exceed this volume Therefore the weight will be calculated thus: Volume x density Where density of LDPE = 0.925g/cm3
The ratio of matrix to filler was given thus:
Total mass of charge = 340cm3 x 0.925g/cm3 =314.5g
This mass was shared with respect to the ratio of LDPE to groundnut shell.
LDPE (%)
Groundnut shell (%)
LDPE
(g)
Groundnut shell (g)
100
0
293.55
15.89
95
5
290.90
23.00
90
10
283.05
31.45
85
15
267.33
47.18
80
20
251.60
62.90
LDPE (%)
Groundnut shell (%)
LDPE
(g)
Groundnut shell (g)
100
0
293.55
15.89
95
5
290.90
23.00
90
10
283.05
31.45
85
15
267.33
47.18
80
20
251.60
62.90
Table 2: Values of weight of LDPE and reinforcement (g)
-
Mixing of the reinforcement with matrix
The blending action is effected by the Polymeric Compounding Mixer, which was operated at a speed of 90 revolutions per minute and the heater band was left to heat for 2 hours to average temperature of 240 degree Celsius.
Casting of the mixture
The mixture was poured into a mould already coated with paper tape and allowed to cure. This procedure is repeated for all samples produced with changes in the particular percentage. After curing the samples are stripped from the mould.
GROUNDNUT
GROUNDNUT SHELL PARTICULATE AFTER GRINDING AND SIEVING
GROUNDNUT
GROUNDNUT SHELL PARTICULATE AFTER GRINDING AND SIEVING
CAST SAMPLES OF COMPOSITES
100% POLYEHTYLENE
CAST SAMPLES OF COMPOSITES
100% POLYEHTYLENE
95% POLYETHYLENE & 5% REINFORCEMENT BLENDED
90% POLYETHYLENE & 10% REINFORCEMENT BLENDED
95% POLYETHYLENE & 5% REINFORCEMENT BLENDED
90% POLYETHYLENE & 10% REINFORCEMENT BLENDED
Figure 3: Snapshots of Reinforcement (Groundnut shells), Polyethylene & Different mixtures of Produced Composites
4.0 RESULTS AND DISCUSSION ON MECHANICAL TEST
Table 3: Result of mechanical tests on 0% weight fraction (100% Polyethylene)
Composition |
Tensile strain at Maximum Tensile stress (mm/mm) |
Maximum Tensile stress (MPa) |
Energy at Maximum Tensile stress (J) |
Youngs modulus (MPa) |
Brinell Hardness (BHN) |
Impact strength (J) |
100% Polyethylene |
0.11500 |
7.92997 |
0.73292 |
79.68 |
23.46 |
7.48 |
Table 4: Result of mechanical tests on 5% weight fraction (95% Polyethylene)
Composition |
Tensile strain at Maximum Tensile stress (mm/mm) |
Maximum Tensile stress (MPa) |
Energy at Maximum Tensile stress (J) |
Youngs modulus (MPa) |
Brinell Hardness (BHN) |
Impact strength (J) |
5% GS and 95% Polyethylene |
0.20889 |
12.69350 |
2.58922 |
23.81 |
23.81 |
8.976 |
Table 5: Result of mechanical tests on 10% weight fraction (90% Polyethylene)
Composition |
Tensile strain at Maximum Tensile stress (mm/mm) |
Maximum Tensile stress (MPa) |
Energy at Maximum Tensile stress (J) |
Youngs modulus (MPa) |
Brinell Hardness (BHN) |
Impact strength (J) |
10%GS and 90% Polyethylene |
0.13778 |
33.14966 |
1.13512 |
596.46463 |
28.44 |
6.12 |
Tble 6: Result of mechanical tests on 15% weight fraction (85% Polyethylene)
Composition |
Tensile strain at Maximum Tensile stress (mm/mm) |
Maximum Tensile stress (MPa) |
Energy at Maximum Tensile stress (J) |
Youngs modulus (MPa) |
Brinell Hardness (BHN) |
Impact strength (J) |
15%GS and 85% Polyethylene |
0.14222 |
33.26685 |
1.24952 |
612.82010 |
27.26 |
8.024 |
Table 7: Result of mechanical tests on 20% weight fraction (80% Polyethylene)
Composition |
Tensile strain at Maximum Tensile stress (mm/mm) |
Maximum Tensile stress (MPa) |
Energy at Maximum Tensile stress (J) |
Youngs modulus (MPa) |
Brinell Hardness (BHN) |
Impact strength (Joules) |
20% GS and 80% Polyethylene |
0.10556 |
34.27161 |
0.81074 |
643.64214 |
14.14 |
6.392 |
Table 8: Flexural Test Result
Sample |
Length (L) |
Thickness (d) |
Width (b) |
Force applied(N) |
Flexural Strength(Mpa) |
80% PE 20% Groundnut |
114.45 |
8.54 |
47.04 |
310 |
15.51 |
85% PE 15% Groundnut |
115.85 |
7.18 |
46.92 |
320 |
22.99 |
95% PE 5% Groundnut |
118.10 |
5.98 |
46.55 |
250 |
26.60 |
100% PE |
116.27 |
8.26 |
44.94 |
290 |
16.50 |
4.0 Hardness Test
A gradual increase in the hardness value from 5% to 7.5% filler concentration followed by a steady decrease was observed. However facts still holds that increase in concentration of the fillers increases the hardness property of the polythene materials. The unpredictable pattern of the hardness may be probed to be caused by the poor interfacial bonding or surface adhesion of the fillers and LDPE.
% variation
Figure 4: Chart of Brinell hardness number against filler concentration
IMAPACT VALUES IN JOULES
10
IMPACT VALUES
IMPACT VALUES
8
6
4
2
0
-
Impact test
It is clearly observed that there is a fluctuating change in the ability to absorb sudden energy with the highest energy absorbed at 5% filler concentration, The poor interfacial bonding between the filler and the matrix polymer causes micro cracks to occur at the point of impact, which causes the cracks to easily propagate in the composite. These micro cracks are responsible for the decreased in impact strength resistance of the composites. The size and dispersion of filler particles in the matrix can affect the composite properties. Small,well-dispersed particles generally give better properties.(Adeosun et al 2012)
Figure 5: Chart of Impact strength against filler concentration
YIELD STRESS(Mpa)
40
30
20
10
-
Tensile Test
Yield strength: The tensile strength of groundnut shell reinforced LDPE composites improved significantly and this increase was proportional to concentration as seen in the graph below(). The improvements in tensile strengths of the composites are due to good interfacial bonding and the presence of agglomerate particles. (Adeosun et al, 2012)
0
control 5 7.5 10 15 20
Figure 6: Chart of Yield stress against filler concentration
7
6
UTS VALUES
UTS VALUES
5
4
3
2
1
0
CONTROL 5 7.5 10 15 20
-
Ultimate Tensile strength
The ultimate tensile strength of groundnut shell reinforced LDPE also in like manner as the yield strength with the highest strength occurring at 20% filler concentration. This increase can be attributed to interfacial bonding and presence of agglomerates.
Ultimate Tensile strength(MPa)
Figure 7: Chart of Ultimate tensile stress against filler concentration
40
BRINELL HARDNESS NU
IMPACT ENERGY
20 TENSILE STRENGTH
0
CONTROL 5 7.5 10 15 20
Figure 8: Chart of test values with filler concentration
e st v n s f se
.
a
.
al g ts m
e st v n s f se
.
a
.
al g ts m
-
SEM microstructure for the Groundnut shell reinforced low density polyethylene composites
Scanning Electron microscope test was carried out on th reinforced samples with the highest, intermediate and lowe ultimate tensile strength. An accelerating voltage of 15k was used and the a magnification of 500 which showed eve distribution of the fillers in the matrix for all the system investigated as shown. This property suggests formation o good interface between the filler phase and the matrix pha which is a well desired property in composite fabrication The micrograph showed a satisfactory adherence as consequence of the fibrous and irregular nature of the fillers The increase in the amount of filler increased the interfaci regions, thus exaggerating the weakening of the resultin composite to crack propagation. Addition of filler inhibi polymer mobility, thereby lowering the ability of the syste to absorb energy during fracture propagation.
Figure 9: 12 Micrograph of filler concentration 5%
Figure 10: Micrograph of filler concentration 5% Figure 11: Micrograph of filler concentration 7.5%
Figure 10: Micrograph of filler concentration 5% Figure 11: Micrograph of filler concentration 7.5%
5.0 CONCLUSION ON MECHANICAL PROPERTY CHARACTERISATION
The notion to reinforce LDPE materials with Agro-waste like groundnut shell using a polymeric compounding mixer can be very much supported as the use of agro-waste like groundnut shells will not only help to eradicate environmental pollution, create employment but increase biodegradability of LDPE.
However research carried out as shown that: Polymeric Compounding mixers allows for an increased uniform matrix- reinforcement compaction, blending and interfacial bonding
On the other hand, the idea of processing LDPE with different weight fraction of groundnut shells as undisputedly and vividly proved to increase the mechanical properties positively:
In figure the ability to resist indentation and abrasion was significant at 7.5% filler concentration
In figure it was resolved that a relatively low filler concentration should be observed in groundnut shell reinforced-LDPE composites in applications requiring high resistance to sudden force like in the use for handles for doors. And if concentration should be increased, effective dispersion of small particle size reinforcement should be put into consideration.
Applications requiring high tensile strength such as in fittings, gaskets, soles for shoes, rigid containers, bags and metal laminates etc. can best be designed with groundnut shell reinforced-LDPE composites with filler concentrations of 7.5% and above.
6.0 REFERENCES
-
S.O.Adeosun, M.A.Usman, W.A.Ayoola and I.O.Sekunowo, Evaluation of the Mechanical Properties of Polypropylene-Aluminum-Dross Composite, International Scholarly Research Network ISRN Polymer Science,vol 2012, ArticleID282515,2012.
-
Capiati, N.J. and R.S. Porter, The concept of one polymer composites modelled with high density polyethylene. Journal of Materials Science, 1975. 10 (10): P. 1671-1677
-
Barkoula, N.M., T. Peijs, T. Schimanski and J. Loos, Prcessing of single polymer composites using the concept of constrained fibers. Polymer Composites, 2005. 26 (1): P. 114-120.
-
Chawla, K.K., Composite materials: science and engineering. 1987, New York: SpringerVerlag.
-
Schwartz, M.M., Composite Materials, Volume I: Properties, Non-Destructive Testing, and Repair. 1997, New Jersey: Prentice Hall PTR.
-
Jang, B.Z., Advanced Polymer Composites: Principles and Applications. 1994, xx: ASM International.
-
Roulin-Moloney, A.C., Fractography and Failure Mechanisms of Polymers and Composites. 1989, London: Elsevier Applied Science
-
. Shalin, R.E., Polymer Matrix Composites. 1995, London: Chapman and Hall.
-
Móczó, J. and B. Pukánszky, Polymer Micro and Nanocomposites: Structure, Interactions, Properties. Journal of Industrial and Engineering Chemistry, 2008. 14 (5): P. 535 563.
-
Murphy, T.P., Reinforced and Filled Thermoplastics- Reinforced. Industrial & Engineering Chemistry, 1966. 58 (5): P. 41 49. 10.
-
Sanli, S., A. Durmus, and N. Ercan, Effect of Nucleating Agent on the Nonisothermal Crystallization Kinetics of Glass Fiber- and Mineral-Filled Polyamide-6 Composites. Journal of Applied Polymer Science, 2012. 125 (S1): P. E268 – E281.
-
Ye, L., T. Scheuring, and K. Friedrich, Matrix Morphology and Fibre Pull-Out Strength of T700/PPS and T700/PET Thermoplastic Composites, Journal of Materials Science, 1995. 30 (19): P. 4761 – 4769.
-
Pukánszky, B. and G. Vörös, Stress Distribution around Inclusions, Interaction, and Mechanical Properties of Particulate-Filled Composites. Polymer Composites, 1996. 17 (3): P. 384 392. 103
-
Etcheverry, M. and S.E. Barbosa, Glass Fiber Reinforced Polypropylene Mechanical Properties Enhancement by Adhesion Improvement. Journal of Thermoplastic Composite Materials, 2012. 5 (6): P. 1084 1113.
-
Byerlin, Al.Al and L.K. Pakhomova, Polymeric Matrices for High-Strength Reinforced Composites. Review. Polymer Science U.S.S.R, 1990. 32 (7): P. 1275 1311.
-
Saira, T., M.Ali Munawar and S. Khan, Natural Fiber-Reinforced Polymer Composites. Proc. Pakistan Acad. Sci., 2007. 44 (2): P. 129 144.