
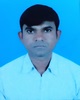
- Open Access
- Authors : Anil G. Dethe , V. N. Mujbaile
- Paper ID : IJERTV10IS030084
- Volume & Issue : Volume 10, Issue 03 (March 2021)
- Published (First Online): 18-03-2021
- ISSN (Online) : 2278-0181
- Publisher Name : IJERT
- License:
This work is licensed under a Creative Commons Attribution 4.0 International License
Modeling and Fe Analysis of Spot Weld in A Structure
Anil G.Dethe *
(Student, IV Semester M. Tech (MED), Mechanical Engineering Department,
Karmavir Dadasaheb Kannamwar College of Engineering, Nagpur, 440009 (Maharashtra) (Indian)
V. N. Mujbaile **
** (Assistant Professor, Mechanical Engineering Department,
Karmavir Dadasaheb Kannamwar College of Engineering, Nagpur, 440009 (Maharashtra) (Indian)
Abstract In this Project we are going to analyze the BIW (Body In White) using ANSYS software under the static loading. The BIW consist mainly two part i.e. top hat and flat plate which are joint together by using resistance spot weld. Spot welds made by resistance spot welding are used extensively in automotive engineering. However, owing to increasing demands in the use of advanced and lightweight materials, resistance spot welding has become a popular alternative for producing spot welds. Because of the complexity and uncertainties of resistance spot welds and thus formed structures, the finite-element (FE) modeling of the welds for Dyanamics analysis is a research issue. In this project first outlines some of the existing modeling of top hat and analyzed by using ANSYS software for different materials and positions of spot welds. SOLID 185 (Tetrahedral 4 node 185) elements is used FE modeling. In this work by using ANSYS V 14.5 software we going to generate mesh BIW part and model generated by using CATIA V5 software.
Keywords Resistance spot welding, CATIA V5,ANSYS V 14.5& FEA
II OBJECTIVES
The literature review on strength and ductility of sheet metal BIW part shows that behavior of while static loading under different position of spot weld is of interest to many and varied aspects & parameters for analysis.
The design of sheet metal BIW part while static loading has to choose the variety of parameters which include geometrical parameters, different types of sheet materials, size of sheet etc. Hence it is of interest to analyze some of the sheet metal BIW part for different materials and different position of spot weld varying some all of the parameters like plate thickness, various sheet material , sizes of sheet compare to the different spot weld position analysis on various loading condition, finding the suitable materials and the best position of spot in BIW part.
III SCOPE & METHODOLOGY
INTRODUCTION
Resistance welding is the most commonly used method for joining steel sheets. No filler metal is needed and the heat required for the weld pool is created by means of resistance when a high welding current is directed through the welded work pieces. An electro-conductive contact surface is created between the work pieces by pressing them together. Contact is made using the shape of either the welded surfaces of the work pieces or the shape of the electrodes. Water-cooled electrodes made of alloyed copper are used in resistance welding. Electrodes convey a pressing force to the joint and direct the welding current to the joint in the appropriate manner. After welding, the electrodes rapidly cool down the welded joint .Work stages in resistance welding are very fast. The surfaces to be welded do not usually need to be cleaned before welding, in addition to which the weld does not usually require grinding or post heating. The Resistance welding process can be easily automated. Resistance welding is a highly efficient production method that is particularly well-suited for automated production lines and mass production.
Therefore there is scope for changing the position of spot weld in BIW part and Analyze static structural analysis in BIW part and to find out the suitable materials and best position of the spot weld in BIW part.
The proposed work include following step.
-
Study of literature review on various work reported.
-
Selecting some of BIW part are available.
-
The geometrical model shall be prepared for the varied position of spot on BIW part
-
CAD Model is prepared using various tool catia version-5
i.e. extrude, revolve, mirror etc .
-
The analysis results obtained shall help to identify the region of stress concentration and best position of spot in BIW part.
MODELING OF BIW PART
FLATE PLATE
Plate length 564 mm Width- 110 mm
Thickness of the plate t= 1.5 mm
TOP HAT
Length- 110 mm
Height- 29 mm
length of TOP HAT = 564 mm
IV SHEET METAL PLATE (BIW PART) VIEW NOMENCLATURE
Figure 1: BIW part assembly view Nomenclature
Figure:2 Complete model of BIW Part
Figure :3. various views of assembly of BIW part.
S R. N O. |
MATERIALS NAME |
DENSITY ( ) Kg/m3 |
YOUNGS MODULUS (E) Pa |
POISSONS RATIO (1/m) |
1 |
STRUCTURAL STEEL |
7850 |
2*1011 |
0.3 |
2 |
ALUMINUM ALLOY |
2770 |
7.1*1010 |
0.33 |
3 |
MAGNESIUM ALLOY |
1800 |
4.5*1010 |
0.35 |
S R. N O. |
MATERIALS NAME |
DENSITY ( ) Kg/m3 |
YOUNGS MODULUS (E) Pa |
POISSONS RATIO (1/m) |
1 |
STRUCTURAL STEEL |
7850 |
2*1011 |
0.3 |
2 |
ALUMINUM ALLOY |
2770 |
7.1*1010 |
0.33 |
3 |
MAGNESIUM ALLOY |
1800 |
4.5*1010 |
0.35 |
V MATERIALS SELECTION
VI FINITE ELEMENT ANALYSIS FOR SPOT WELDS IN A STRUCTURE
Meshing of model
Fig4: Meshing of BIW Part
The element used is tetrahedran elements
Fig 5: Tetrahedron Element
SUPPORT OF SHEET METAL (BIW PART)
Figure 6: Constraints on a Flat Plate DIFFERENT POSITION OF SPOT WELD SPOT AT CORNER POSITION
Figure 7: Spot at corner
SPOT NEAR TO BEND POSITION
Figure 8: Spot at near bend position
SPOT AT MIDDLE POSITION
Figure 9: Spot at middle position
All the Boundary condition fixed support and force are applied in combine manner on sheet metal BIW part assembly as shown in figure 10
Figure10: Combination of all the Boundary condition.
The first doing the analysis setting and time setting find out the shear stress and equivalent stresses, for different materials and position of spot weld in BIW Part.
EQUIVALENT STRESSES FOR SHEET METAL BIW PART
-
RESULT WHEN SPOT AT CORNER
-
Material structural steel
Fig.29:- Equivalent stress Spot weld at corner (ST)
-
Material aluminum alloy
Fig.30:- Equivalent stress Spot weld at corner (AL)
-
Material magnesium alloy
Fig.31:- Equivalent stress Spot weld at corner (AL)
-
-
RESULT WHEN SPOT WELD AT NEAR TO BEND
-
Material structural steel
Fig.32:- Equivalent stress Spot weld at near to bend (ST)
-
Material aluminum alloy
Fig.33:- Equivalent stress Spot weld at near to bend (ST)
-
Material magnesium alloy
Fig.34:- Equivalent stress Spot weld at near to bend (MG)
-
-
RESULT WHEN SPOT AT MIDDLE POSITION
-
Material structural steel
Fig.35:- Equivalent stress Spot weld at mddle position (ST)
-
Material aluminum alloy
Fig.36:- Equivalent stress Spot weld at middle position (AL)
-
Material magnesium alloy
Fig.37:- Equivalent stress Spot weld at middle position (MG)
COMPARISON OF RESULT BY USING CHART.
MATERIALS
spot at middel equivalent stress
spot at corner equivalent stress
spot at near to bend equivalent stress
st
0.55457 MPa
2.3617 MPa
0.78503 MPa
al
0.55044 MPa
2.3162 MPa
0.77214 MPa
mg
0.54751 MPa
2.2819 MPa
0.76295 MPa
Table 3: Variation in Equivalent stress (Mpa)
Equivalent stress
Equivalent stress
Equivalent stress
2.5
2
1.5
1
0.5
st
al
mg
spot at middel
equivalent stress
0.55457
0.55044
0.54751
spot at corner
equivalent stress
2.3617
2.3162
2.2819
spot at near to bend equivalent stress
0.78503
0.77214
0.76295
st
al
mg
spot at middel
equivalent stress
0.55457
0.55044
0.54751
spot at corner
equivalent stress
2.3617
2.3162
2.2819
spot at near to bend equivalent stress
0.78503
0.77214
0.76295
0
Graph 3: Variation in Equivalent stress varying in position of spot weld.
SHEAR STRESS FOR SHEET METAL BIW PART
-
RESULT WHEN SPOT AT CORNER
-
Material structural steel
Fig.38:- Shear stress spot weld at corner (ST)
-
Material aluminum alloy
Fig.39:- Shear stress spot weld at corner (AL)
-
Material magnesium alloy
Fig.40:- Shear stress spot weld at corner (AL)
-
-
RESULT WHEN SPOT WELD AT NEAR TO BEND
-
Material structural steel
Fig.41:- shear stress Spot weld at near to bend (ST)
-
Material aluminum alloy
Fig.42:- shear stress Spot weld at near to bend (AL)
-
Material magnesium alloy
Fig.43:- shear stress Spot weld at near to bend (AL)
-
-
RESULT WHEN SPOT AT MIDDLE POSITION
-
Material structural steel
Fig.44:- shear stress Spot weld at middle position (ST)
-
Material aluminum alloy
Fig.45:- shear stress Spot weld at middle position (AL)
-
Material magnesium alloy
-
-
-
Fig.46:- shear stress Spot weld at middle position (AL)
COMPARISON OF RESULT BY USING CHART
MATERIALS |
spot at middel maximum shear stress MPa |
spot at corner maximum shear stress MPa |
spot at near to bend maximum shear stress MPa |
st |
0.29416 |
1.2099 |
0.4177 |
al |
0.29352 |
1.2016 |
0.41356 |
mg |
0.29299 |
1.1958 |
0.41219 |
Maximum shear stress
Maximum shear stress
Table 4: Variation in max. Shear stress for different materials and position of spot weld.
Maximum shear stress
1.4
1.2
1
0.8
0.6
0.4
0.2
0
st al mg
spot at middel
Maximum shear stress
1.4
1.2
1
0.8
0.6
0.4
0.2
0
st al mg
spot at middel
maximum shear
stress MPa
spot at corner maximum shear stress
MPa
spot at near to bend maximum shear stress MPa
0.29416
0.29352 0.29299
maximum shear
stress MPa
spot at corner maximum shear stress
MPa
spot at near to bend maximum shear stress MPa
0.29416
0.29352 0.29299
1.2099
1.2099
1.2016
1.2016
1.1958
1.1958
0.4177
0.4177
0.41356
0.41356
0.41219
0.41219
Graph 5.15.2 Variation in max.shear stress for different materials and position of spot weld.
-
CONCLUSION
CAD model of the BIW part of sheet metal plate assemblies is generated in CATIA V5 and this model is imported to ANSYS 14.5 for processing work. For different position of spot weld by static structural analysis.
Following are the conclusions from the above results obtained:
-
Equivalent stress is maximum for steel when Spot weld at middle as compared to other materials and position of spot weld.
-
Shear stress is approximately same for all materials and different position of spot weld.
-
-
FUTURE SCOPE
Following work may form the scope for future work
-
Fatigue analysis by varying the position of spot weld of BIW part of sheet metal plate.
-
Further work on different shape of BIW part of sheet metal plate, analyzed by using experimental data.
-
-
REFERENCES
-
G. So derberg, Kristina Warmefjord, Lars Lindkvist, Rolf Berlin, The influence of spot weld position variation on geometrical quality, CIRP Annals. Manufacturing Technology, vol. 61, 2012, pp. 1316.
-
AhmetH.Ertas, FazlO.Sonmez, Design optimization of spot- welded plates for maximum fatigue life, Finite Elements in Analysis and Design, vol. 47, 2011, pp.413423.
-
Min Hu a, Zhongqin Lin a, Xinmin Lai a, Jun Ni, Simulation and analysis of assembly processes considering, International Journal of Machine Tools & Manufacture, vol. 41, 2001, pp. 22332243.
-
Kristina War0mefjord, Rikard Soderberg and Lars Lindkvist, Variation Simulation of Spot Welding Sequence for Sheet Metal Assemblies, Nord Design 2010.
-
Stijn Donders, Marc Brughmans, Luc Hermans, Nick Tzannetakis, The Effect of Spot Weld Failure on Dynamic Vehicle Performance, 2001.
-
Dariusz Ceglarek, Jianjun Shi, Dimmensional Variation Reduction for Automotive Body Assembly, Manufacturing Review, vol. 8, june 1995, pp. 2.
-
Jaime A. Camelio and S. Jack Hu Dariusz Ceglarek, Impact of Fixture Design on Sheet Metal Assembly Variation, journal of Manufacturing Systems, Vol. 23/No. 3, 2004.
-
K. D. Hardikar, D.J.Nidgalkar, Dr. K.H. Inamdar, Techniques to ensure minimum distortion of an assembly of metal parts induced due to the process of welding used for an assembly, International Journal of Scientific & Engineering Research Volume 3, Issue 2, February-2012.Wilson FW, editor-in-chief. Fundamentals of tool design. Society of Manufacturing Engineers, Academic Press, New York, 1962.