
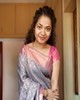
- Open Access
- Authors : Madhushree R, J. Sharana Basavaraja
- Paper ID : IJERTV13IS090068
- Volume & Issue : Volume 13, Issue 09 (September 2024)
- Published (First Online): 05-10-2024
- ISSN (Online) : 2278-0181
- Publisher Name : IJERT
- License:
This work is licensed under a Creative Commons Attribution 4.0 International License
Modelling and Analysis of Connector Spring for Novel Termination Technology
Madhushree R, J. Sharana Basavaraja
Department of Mechanical Engineering, B. M. S. College of Engineering, Bengaluru-560019, Department of Mechanical Engineering, B. M. S. College of Engineering, Bengaluru-560019,
Abstract- Electromechanical packaging development engineers must overcome difficult obstacles to create designs that satisfy system standards for high performance, high reliability, and low cost. This is undoubtedly the case with the development of electrical connections, which are a crucial component of the majority of electronic package designs. It is getting more and harder to create a connection that satisfies every criterion of a certain electronic packaging application. By doing away with the necessity for a tool for termination and including the value-added feature of strain relief in the design for the given dimension, a novel termination technology has been presented as part of innovation work. The suggested design for electronic connections may provide a variety of advantages in terms of functionality, dependability, toughness, and package size.
Creo software is used to create a model with a minimum of four parts that is appropriate for both stackable and continuous terminal block connectors, and Ansys software is used for simulation and analysis.
Keywords- Finite element analysis, Wire Termination, Connectors, Strain relief, Actuator.
-
INTRODUCTION
A connector is a coupling device that joins electrical termination to create an electrical circuit. Enables contact between wires, cables, printed circuit boards(pcb) and electrical components that transmit data, power and signal in the harshest environment. A connector is essentially a part that enables systems for the transfer of electrical energy or optical and electronic data to be used to their full potential. Connectors are created to accommodate a wide range of needs and applications in order to satisfy these expectations. To meet constantly increasing demand, smart, strong, secure, and quick transmission technologies are required. The distribution of energy and signals is carried out through connectors. Basically, there are three main kinds of connections:
-
Wire-to-wire: Connection between one conductor (cable, wire) and another.
-
Wire(cable)-to-board: Connection between a conductor and a circuit board.
-
Board-to-board: Connection between one circuit board and another.
In most applications, contact is made using a firm(pin or blade) and a flexible (spring clamp or jack) contact element. Circuit boards may come in direct or indirect contact. Housing components and contact carriers are used to conduct contacts. The pitch is a term used to indicate the separation between two contacts. Connector mis mating is avoided by polarity or keying of the mating face and pins. To avoid unintentional separation, spring latch systems, snap-in hooks, and bolted connections are employed. Because of their strong
conductivity, copper alloys are mostly employed as contact components. To ensure good corrosion protection and wear, they are coated. Due to their electrical insulating qualities, polymers are virtually often used to create contact carriers. Housing is made of plastic and metal alloys.
-
Conductor connection technology
-
Crimping technology: The most popular method of connecting wires is crimping. Its the person plastic deformation brings together the strands in the crimping zone of the contact element.
-
Insulation-displacement technology: In order to make electrical contact with the conductor inside, the wire is driven down into a fork-shaped contact that consists of a slot with cutting edges that displace insulation on each side of it.
-
Insulation-piercing technology: A round or blade-like contact spike is used to pierce the stranded wire and establish electrical contact.
-
Screw and spring-clamp terminals: The stripped wire is put into a hole or barrel of the contact terminal and secured there with a screw.
-
-
Termination technology
An electrical device linked to either end of an electrical wire is known as a wire termination.
-
THT solder termination: Connector soldering pins are placed within through-plated PCB holes. They will then be wave soldered to other components automatically and simultaneously.
-
Press-in technology: The fundamental of this solderless connection method is the insertion of a pin into a through- plated PCB hole.
-
Wire-wrap termination: A wire wrapped around an angular termination pin is known as a wire-wrap connection.
-
Crimp termination: A flexible conductor is confined in a gas- tight way within the crimp contact in crimp terminations by controlled deformation.
-
IDC insulation displacement connection: The IDC cutting termination engages the wires by resiliently penetrating the wire insulation in a single motion.
-
Solder lug termination: Each stripped and tinned wire is manually soldered to a solder lug one at a time.
-
Faston termination: Faston terminals are offered in both male and female variants and come in a range of sizes, shapes, and designs to match various applications.
-
Cage clamp termination: A spring is used in the cage clamp termination method to make contact with both flexible and solid conductors.
Market survey
Problem definition
Literature survey
Concept 1
Concept 2
Concept 3
Concept 4
Concept 5
Concept 6
Concept validation
CAD Modelling
Simulation and analysis
-
Screw termination: The wire may be held by a metal plate pressed on the wire by a screw, a wrap of wire directly under the head of a screw, or what is essentially a set screw in the side of a metal tube.
-
-
New Product Development Process
Fig 1: New product development process
-
Idea Generation: Finding fresh ideas for improving the performance of current goods or for creating new ones is the first stage in the creation of a new product.
-
Idea Screening: The product idea is evaluated at this stage of the development of a new product.
-
Concept Development & Testing: This stage of new product development embraces the change from concepts to finished goods.
-
Marketing Strategy: The product manager creates and refines a marketing strategy for the launch of a new product.
-
Business Analysis: To determine if these elements fulfil the objectives of the organization, an evaluation of the expenses, sales, and profit prediction with regard to the new product is carried out throughout the business analysis phases.
-
Product Development: A prototype or functional model of the product is created in order to list all of its tangible and imaginative characteristics.
-
Market Analyss: The product is subsequently tested on the market if it successfully completes the development and pretest phases and appears to still be a profitable proposition.
Fig 2: Flow chart of the process
B. Comparison study of the terminations
SL. NO
Mecha nism
Actuatio n
pros
cons
1
Wedge
Nut
Wide range of wire
Wire preparation elimination
Ease of manufacturing See through
connection
Requires more pitch
Increase in overall size Requires helical spring
Increase in cost
2
Push button
Push button
Ease of manufacturing Wire preparation elimination Toolless
Wide range of wire size Robust wire
termination
Spring stability No Feedback loop Termination force is more
3
Rotatin g
Retracta ble button
Zero insertion and excertion force
Ease of manufacturing Wide range of wire size Feedback loop Elimination of
wire preparation
Ease of assembly Requires specific material
4
Stacka ble Housin g
stacking
Easy of assembly Elimination of wire preparation grip pattern Covers Wide range of wire size
Can include see through assembly material for visual termination Strain relief
feature
Working feasibility Ease of manufacturing Requires
special material
-
-
-
-
METHODOLOGY
A. Flow chart
A Flow chart is prepared before the project is proceeded further to understand the sequence of activities and how they are carried out. This helps to identify in which stage the project is and documenting the activities.
Feedback loop from stacking Applicable for moderately high vibration requirements
5
Cam followe r
tool
Requires special material
Easy of manufacturing and assembly Covers Wide range of wire size Applicable for
moderately high vibration requirements Value added Strain relief feature
Cam follower feature advantageous for feedback loop
and locking
Working feasibility Requires special plastic material Spring design
6
Stacka ble Cam
Lever
Covers Wide range of wire size Elimination of
wire preparation Easy of manufacturing and assembly Compact design Value added feature of strain relief and feedback feature Applicable for moderately high vibration requirements
Working feasibility Requires special plastic material
Tool requirement
7
Push spring
Push button
Covers Wide range of wire size
Easy of manufacturing and assembly Compact design Strain relief feature Applicable for moderately high vibration requirements Working feasibility
Spring design
No feedback loop
-
Stackable feature:
The development of an improved connector of the type at concern, with which sufficient number of individual connectors of uniform construction are combined to handle the circuits of a unit having a significant number of outside circuit connections, each carrying a distinct type of current.
-
Strain relief:
A strain relief is used to bring flexible wire to a hard connector or connecting point. A correctly constructed strain relief will prevent mechanical force applied to the outside of a wire from being transmitted to the electrical terminations within the connection or device, potentially resulting in failure. A well- designed segmented strain relief will include walls and voids that allow the bend radius to extend further away from the connector or connecting point. To obtain the required bend radius, the sizes of the solid parts and the gaps between solid pieces are modified. In general, segmented strain reliefs are constructed so that the segment nearest to the fixed point closes first and the segment farthest away from the fixed point closes last. This gives the most bend relief while also protecting the electrical terminations within the connection.
-
CAD modelling: Creo software:
The creation of a complicated model necessitates the use of CAD software with advanced features that allow for the most precise modelling of the required 3D model. The spring and contact rail were created using sheet metal component modelling for a thickness of 5 mm, while the housing and lever were modelled as a drafts using CREO Parametric for dimensions of 15 x 10 x 5. The model consisted total of four parts, which are put together using the softwares assembly tool to display a drafting design model for the proposal created as shown in fig 4,5,6 and 7.
Table 1: Comparison study of termination
-
-
DEVELOPMENT OF NOVEL TERMINATION
The intent is to include tool-free actuation, creating a model suitable for both stacking and continuous terminal block connections, aggregating a wide range of wires, miniaturization, and dimensions of 15 x 10 x 5 mm.
Fig 3: Modelling of novel termination
-
Parts of cage clamp connector:
-
Connector Housing:
Connectors need to maintain their dimensional stability as a result of significant chemical and thermal impacts. For efficient connector assembly and mating activity, the centre line spacing, straightness, and flatness of the connectors has been maintained. The connection housing accomplishes this stability by retaining the position of the contacts, dynamically protecting the contacts from the working environment, and electrically and mechanically isolating the contact spring. Surface and volume resistivity as well as dielectric withstanding voltage are examples of electrical characteristics that have an impact on the housings insulating capabilities. The flexural strength/modulus and creep strength of the connection housing are among its mechanical properties.
Polyphenylene sulphide (PPS), polyethylene terephthalate (PET), poly-butylene terephthalate (PBT), polycyclohexylenedimethylene terephthalate (PCT), liquid crystalline polymer (LCP), FR-4, and polyimide are a few of the frequently utilized materials for fabricating connection housings.
Fig 4: Connector housing
resistance. The most popular alloy to employ when stress relaxation resistance is an issue is beryllium copper. The majority of applications are also acceptable for
phosphor bronzes.
Fig 5: Contact spring
iii. Spring clamp
The force of a spring is used by spring clamps to keep the wire clamped. They are a more recent alternative to screw clamps and are particularly helpful in situations where there is a need for tiny wire sizes and constrained workspace. A form of cable interconnect known as a push clamp offers a powerful locking mechanism that can only be released by pressing the connector body, avoiding unintentional disconnections, require no rotating force, is easily pluggable in. This self-latching device is well known around the world for its rapid and simple mating and unmating capabilities. It allows for functioning in a very small place and offers complete security against vibration, shock, or pulling on the wire. To enter a wire into a spring cage, one need to push the lever to open the termination. The push-in connection can work with ferruled and unferruled wires.
-
Contact Springs
-
The conduit for the transfer of a signal, power, and/or round between the circuits that a connector joins is provided by the contact spring. Additionally, it offers the normal force, which aids in the creation and maintenance of the separable interface. The normal force is the component of the force that is perpendicular to the surface of contact. Insertion and extraction force, contact force, contact retention, and contact wipe are the main mechanical criteria of the contact spring. The contact spring must meet certain electrical specifications, including contact resistance, current rating, inductance, capacitance, and bandwidth.
It is a design exercise to verify that spring stresses are not excessive to account for loss of normal force during plastic deformation. For frequently used copper alloys, the yield strength varies, and as a result, so does the stress relaxation
iv. Lever actuator
Fig 6: Spring clamp
IJERTV13IS090068
A lever-type actuator in which a grooved lever is pivotally placed on a connector housing aligned with the spring face between the first and second bents of the spring. The spring
(This work is licensed under a Creative Commons Attribution 4.0 International License.)
that creates space in the rectangular groove for the wire to be terminated is compressed upon pressing the lever by providing load. Lever actuators do eliminate from the requirement to use a tool for every termination, which ultimately saves a lot of time. When no load is applied, the spring is presumed to be in the resting position; however, when a force is applied perpendicular to the spring by a lever, the spring compresses, creating a gap for the wire, which will be terminated when the load is released.
to ensure simulation accuracy is creating a high-quality model.
Hexahedral finite element mesh generation method is used to create the entire hexahedral finite element model of the structure. It entails a number of steps, including reading the geometrical model, defining intersection planes and intersection contours, creating a quadrilateral mesh based on a contour grid, creating a section mesh, defining the hexahedral finite elements, and exporting the numerical model.
C. Material properties
Cr
Mn
Si
Ni
P
S
C
N
MIN
16
–
–
6
–
–
–
–
MAX
18
2
1
8
.045
.03
.15
.1
The nominal composition of Type 301 (S30100), an austenitic stainless steel, is 17% chromium and 7% nickel. This grade of steel is a great option for aesthetic structural applications due to its high strengths in the six possible states or tempers, resistance to atmospheric corrosion, and brilliant, appealing surface. A wide range of magnetic and mechanical characteristics may be generated for a number of applications by temper rolling and altering the chemical composition within the parameters established by the ASTM requirements.
-
Spring:
Fig 7: Lever actuator
-
-
FEA ANALYSIS
Modulus of elasticity
195
KN/mm^2
Poisson ratio
.29
Density
7.9
Kg/dm^3
Melting point
1400-1450
°C
Thermal conductivity
14.7
W/m°K
Electrical resistivity
70
µcm
Electrical conductivity
1.4
MS/m
Specific heat
460
J/(kg K)
Table 2: Chemical composition of SS301
The cage clamp spring is made of ss130 and has three bends. The first bend serves in attaching a spring to the housing, the second bend accepts an actuator load for terminating the wire, and the third curve helps in achieving the strain relief feature for the wire. One end of the spring has an inverted T-shaped component that is used to stitch the spring into the housing on one face and to join another face to the contact rail, which is used to transmit electricity down the route.
After the second bend, the springs rectangular portion, which is perpendicular to the T-shaped portion, will have a rectangular cut made to allow the wire to travel down the profile and accomplish termination. The third component of the spring that is bent at a 45-degree angle to the rectangular part and is utilized to achieve strain relief at the springs end towards the housing.
-
Meshing:
Meshing, also known as mesh generation, is the process of producing a two-dimensional or three-dimensional grid; it consists of dividing a domain by breaking complicated geometries into manageable pieces. The Ansys Mesh capabilities are frequently mentioned as the industry benchmark for modelling and workflow simulation for meshing complicated components. When it comes to the engineering simulation process, meshing is crucial. One of the most important aspects that should be taken into account
Table 3: Material properties for SS301
-
Boundary conditions
Parts that arent included in the model but are interacting with it are represented by supports. Supports help in domain truncation, which facilitates rapidly getting numerically correct results without modelling portions of the geometry which are not of major concern.
The spring component is provided a fixed support, signifying that it is attached to the housing, which is highlighted in blue. The push actuator is provided a dis- placement support that represents the movement of that spring component during the wire engagement and disengagement.
IJERTV13IS090068
(This work is licensed under a Creative Commons Attribution 4.0 International License.)
-
Coefficient of friction:
The amount of friction between two surfaces is measured by the coefficient of friction(µ) A low coefficient of friction value means that less effort is needed to cause sliding than would be needed if the coefficient of friction were to be high. The value of the coefficient of friction is given by: Frictional force(µ) = F/N where F is the frictional force and N is the normal force. The coefficient of friction is the ratio of a frictional force to a normal force and hence has no units.
-
-
RESULT
One of the most crucial phases of any structural design process is the stress analysis. In terms of the size and distribution of stresses or strains in the structure of interest that is subjected to a certain load and boundary condition, an appropriate analytical approach should deliver relatively accurate, dependable data. The engineer will be able to predict the structures strength using the information from the analysis. In order to be sure that a structure will serve its intended purpose in a certain loading environment, structural stress analysis is carried out. Its critical to predict every potential failure mode and design around it. Considering the Tensile strength of the material to be around 1500MPa, the stress generated is within the range to avoid any permanent deformation on the spring.
Fig 8: Stress analysis
The Force required to operate the spring is at 12.62 N . The increase in the force is due to the hit back of the spring and excessive push of the spring
Fig 9: Force analysis
-
CONCLUSION
In the present work a novel termination technology has been devised and proposd. The suggested design is compatible with both stackable and continuous terminal types.The suggested design incorporates value-added features such as the elimination of a tool and a strain relief feature. The force needed to move the spring is 12.62 N. The springs hitback and excessive spring push are what caused the force to grow. The stress generated is within the range to prevent any long- term deformation of the spring given that the materials tensile strength is approximately 1500 MPa.
ACKNOWLEDGEMENT
The authors would like to acknowledge B.M.S. College of Engineering, Bengaluru, India for providing necessary support and resources to conduct this study.
REFERENCES
-
Mohamed Aboulkassem and Christian Schrettlinger. Push-in clamp retainer, push-in clamp assembly and electric connector element, January 29 2019. US Patent 10,193,244.
-
Albert Albers, Paul Martin, and Benoit Lorentz. Modeling and design of contacts in electrical connectors. In DS 68-4: Proceedings of the 18th International Conference on Engineering Design (ICED 11), Impacting Society through Engineering Design, Vol. 4: Product and Systems Design, Lyngby/Copenhagen, Denmark, 15.-19.08. 2011, 2011.
-
Edgar W Breisch. Detachable electrical connector, March 2 1948. US Patent 2,436,914.
-
Harting. Harting users guide termination technologies. HARTING Electric GmbH Co. KG, HARTING Electronics GmbH Co. KG,(4th Edition 2017, revised 06/17), 2017.
-
Wolfgang Hohorst. Electrical terminal with actuating press-button, November 11 1997. US Patent 5,685,735.
-
Udo Hoppe. Electrical connection clamp or terminal clamp, March 1 2011. US Patent 7,896,686.
-
Yeh-Liang Hsu, Yuan-Chan Hsu, and Ming-Sho Hsu. Shape optimal design of contact springs of electronic connectors. J. Electron. Packag., 124(3):178183, 2002.
-
Wei Liu, Jian You, Zinan Liu, Yi Hou, Xun Zhu, and Jiang Yu. Analysis of crucial factors affecting contact force of pcb spring terminals based on simulation and rank correlation. IEEE Access, 10:8693586942, 2022.
-
Tom Macek and James M Pitarresi. Structural optimization of an electrical spring contact. In Proceedings of IEEE 43rd Electronic Components and Technology Conference (ECTC93), pages 1125 1134. IEEE, 1993.
-
Dorin Maier. Product and process innovation: a new perspective on the organizational development. International Journal of Advanced Engineering and Management Research, 3(6):132138, 2018.
-
Irene Sawchyn and Edward S Sproles. Optimizing force and geometry parameters in design of reduced insertion force connectors. IEEE transactions on com-ponents, hybrids, and manufacturing technology, 15(6):10251033, 1992.
-
Faisal Shalabi and Christian Bach. How to improve the new product development. Saudi Journal of Engineering and Technology Middle East Publishers,(127-134), 2016.
-
Irena Silinevica, Maris Igavens, and Liene Amantova-Salmane. Research of the new product development process. Latgale National Economy Research, 1(8):116124, 2016.
-
Mustafa TOSUN and Huseyin AKSOY. Electrical-thermal-mechanical analysis of cable connection with screw-connected terminal strips using finite element method. Sakarya University Journal of Computer and Information Sciences, 4(1):96110, 2021.
-
Brent L Weight, Christopher A Mattson, Spencer P Magleby, and Larry L How- ell. Configuration selection, modeling, and preliminary testing in support ofconstant force electrical connectors. 2007.
IJERTV13IS090068
(This work is licensed under a Creative Commons Attribution 4.0 International License.)
IJERTV13IS090068
(This work is licensed under a Creative Commons Attribution 4.0 International License.)