
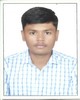
- Open Access
- Authors : Pandurang Takmoge , Umesh Fulari , Nrupalshingh Pawar , Abhay Gund
- Paper ID : IJERTV9IS070383
- Volume & Issue : Volume 09, Issue 07 (July 2020)
- Published (First Online): 25-07-2020
- ISSN (Online) : 2278-0181
- Publisher Name : IJERT
- License:
This work is licensed under a Creative Commons Attribution 4.0 International License
Modification of Single Ball Transmission Drive
Umesh Fulari1
1Department of Mechanical Engineering, Savitribai Phule Pune University, Maharashtra, India.
Nrupalshingh Pawar3,
Department of Mechanical Engineering, Savitribai Phule Pune University, Maharashtra, India.
Pandurang Takmoge2,
Department of Mechanical Engineering, Savitribai Phule Pune University, Maharashtra, India.
Abhay Gund4
Department of Mechanical Engineering, Savitribai Phule Pune University, Maharashtra, India.
Abstract: – Now the industries in all the field are moving towards the smart engineering specially in the era of manufacturing that also the conventional machining or traditional machining processes. These processes requires the high degree of accuracy and precision of the work which is only possible by means of smooth and slow machining done by continuously variable transmission (CVTs).Continuously variable transmission is difficult to achieve by means of conventional drives like Gear, Belt, Clutch, Coupling he we are designing the system which will give the continuously variable transmission by means of single ball arrangement or mechanism.
KeywordsDisc, Single Ball, Mild steel Frame, Bearing House, Pulley, Prime Mover, Belt, Shaft.
1. INTRODUCTION
Now a days industries are totally focusing on precise and accurate machining of components, parts and job which have too much complexity while machining. This Era is about industry revolution which come to 4.0 to 1.0, 2.0, 3.0 and all. So, in industry 4.0 is totally based on software and information technology tool for monitoring and controlling of manufacturing process in industry like turning, facing, drilling, milling, tapering, chamfering, boring, grinding etc. Till date today we are using the transmission drives for the machining process to control the speed, feed, accuracy and to define the precise components. Basically, the transmission in machining involve two motions.
-
Primary transmission motion:
Primary motion is basically mechanical rotary or reciprocating motion in case of machining process the primary motion approaches tool as well as the moment the moment of workpiece with respective directions. Due to primary motion actual cutting forces are produced and the material from the workpiece removed easily. Primary motion consumes nearly 70% of energy of whole machining operation. Primary motion transmission is given as below.
Electric m tor
Belt Drive
Pully
Electric m tor
Belt Drive
Pully
Tool/ Workpiece
Tool/ Workpiece
Gear
Gear
Fig.1.1 Conventional transmission for machining
This motion includes
-
Moment of tool with respect to workpiece.
-
Motion of workpiece with respect tool.
While primary motion differs in ball traction drive as
Source Electric Motor
Input Shaft
Ball
Output Shaft
Source Electric Motor
Input Shaft
Ball
Output Shaft
Fig.1.2 Modification transmission
-
-
Auxiliary transmission motion:
As per name suggest auxiliary uses alternative transmission which has no direct contact or relation for metal removal during machining it include non-cutting motions which are carried quickly and easily.
Auxiliary motion helps to
-
Reduce the labor cost.
-
Reduce production cycle time.
-
Increase productivity.
-
Loading and unloading job.
-
Motion synchronization according to shape and size.
-
Monitor and control the motion according to process or method, operation.
-
PRINCIPLE OF OPERATION
-
Single Ball Transmission Drive
Single ball transmission drive works on the principle of Continuously Variable Transmission (CVT).
In such transmission a device or mechanism is designed in such a way that speed reduction or acceleration of speed achieved continuously with respective of time, operation or process.
-
Construction and Working
2
f =Yield stress N/mm
yt
Fig.2.1 Single ball transmission drive.
Fig.2.1 shows an adjustable spherical ball inside the hub of a huge bearing which cause the axial movement of the ball, input shaft and output shaft are connected to the spherical ball through cast iron disc having some curvature in order to reduce the percentage of slip and power loss during operation. Input shaft is driven by prime mover i.e. primary motion or electric motor through belt and pully and whole assembly was installed within fixed frame. The ball is kept in oil casing for better lubrication.
-
Working: –
As the motor shaft that convert the electrical energy into mechanical rotary motion is given to input shaft (i) and hence the ball is connected to input shaft so that the ball also start to rotate which cause the rotation of output shaft due to relative motion between them. As the ball is kept in oil casing the average percentage of slip, power loss and level of noise produce is minimized
-
To reduce the speed and torque
As the lock nut mechanism attached to the ball assembly as the nut is rotate clockwise which will lower the ball hence the speed is reduce due to more radial distance through periphery of ball hence speed and speed and torque transmitted to output shaft.
(B) For Bearing D=Inner cage diameter D1=Outer cage diameter B=Width in mm
-
Design of Driver Motor Type: Single Phase AC Motor Power: 1/15HP (373 Watts) Voltage: 230V, 50Hz Current: 0.5A
Speed: 1440rpm (max) Operating Speed: 1440rpm Motor Torque:
P= (2NT) ÷ 60
T= (373 × 60) ÷ (2××1440)
T= 2.47 Nm
Power is transmitted from the motor shaft to the input shaft of drive by means of an open belt drive.
Motor pulley diameter= 20mm
IP-shaft pulley diameter= 170mm Reduction ratio= 4
IP-shaft speed= 1440/4 = 360rpm Torque at IP shaft= 4×2.4 = 9.6 Nm Material Selection of Shaft: Designation= EN24
Ultimate Tensile Strength= 800N/mm² Yield Strength= 680N/mm²
-
Design of Shaft
Referring to American Society of Mechanical Engineers(ASME) design of shaft is done. Since the load on the shaft is mainly due to the machinery which is not constant, it is very necessary to take proper tolerances and allowance in order to bear the load fluctuations.According to ASME code permissible values of shearstress (fs) may be calculated from the following relations:
fs max = 0.18 × fut (ultimate tensile strength)
= 0.18 * 800
= 144 N/mm² OR
-
-
To increase speed and torque
As the nut is rotated in an anticlockwise direction cause to move the ball in upward hence the disc are eccentric so the radial distance of rotation through periphery of ball
fs max = 0.3 × fyt
= 0.3* 680
= 204 N/mm²
(yield strength)
reduce hence the speed increased.
-
-
DESIGN AND EXPERIMENTAL SETUP Nomenclature
(A) For Shaft
P=Power of the input shaft in watts N=Speed of shaft in rpm
T=Torque transmitted by the shaft in Nm
2
Considering the minimum value:
fs max = 144N/mm²
Weight of pully = 3kg = 3×9.81 = 29.43N
This is the allowable value of shear stress (fs) that can beused in the shaft material for safe operation.
f max =Maximum Allowable working stress in N/m
s
2
f =Ultimate tensile stress in N/mm
ut
Fig. 3.1 SFD-BMD
3.2.1 Diameter of shaft Considering Combine Loadig
Diameter of Shaft By Equivalent Twisting Movement
1) Torque (T) = (T1-T2) × R
= (1800-900)×85
= 76.55 Nm
2) = = (3×9.81)×(9)
3.3 Angle of Response
T1 = µ T1 = 1800N
T2
eµ = 0.5 T2 = 900N
µ = 0.5
= 3.162
0.3
= 10.5
Experimental Setup
Fig.3.2 Experimental Setup
2 2
= 1.32 Nm
3) = 2 + 2 = (76.55)2 + (1.32)2 = 76.56 Nm
4) = 3
16
= 12.40 =16 mm
Diameter (d) = 12.40 mm
Diameter of Shaft By Equivalent Bending Movement
-
Equivalent Bending Moment Meq = 1 [ + 2 + 2]
2
= 1 [1320 + 13202 + 765502]
2
Meq = 76550 Nmm
-
Meq = 1 b×d3
2
d3 = 765550×32
×144
d = 15.63 = 16mm
Diameter (d) = 16mm
For safe operation select the diameter of shaft which is maximum.
To achieve the tolerance of pH7 on the pulley we need to bore the pulley hole & the minimum hole possible is 16mm, so adopting the shaft diameter 16mm.
-
-
SOFTWARE RESULT AND ANALYSIS
Strain Analysis
Strain is the reaction of a framework to an applied pressure. At the point when a material is stacked with a power, it creates a stress, which at that point makes a material distort. Building strain is characterized as the measure of disfigurement toward the applied power isolated by the underlying length of the material.
Fig. 4.1 Strain Analysis
Stress Analysis
Stress examination is an essential undertaking for mechanical, plane design specialists associated with the structure of structures all things considered, for example, burrow extensions and dams, airplane, mechanical bodies, and even plastic cutlery what's more, staples. Stress examination is likewise utilized in the upkeep of such
structures, and to examine the reasons for basic disappointment.
Fig.4.2 Stress Analysis
-
CONCLUSION
-
Firstly, most of the industries uses CVTS for their operation which is difficult by means of gear, belt, rope, chain drive because gear levels to heavy impact while varying speed. Belt and rope have huge amount of slip and wear hence we observed such problem and design the mechanism for continuously variable transmission (CVTS). This mechanism enables the machining operation at various
operation at various velocity and having stepless, shockless speed variation along compact size and most efficient to economy. From the test result from software and experimentally it can nearly achieve 75% of efficiency at high speed.
REFERENCES
-
D. S. Welkar, Prof. P. G. Damle, K. A. Patil, Review of Free Ball traction Drive for CVT, International Journal of Research in Advent Technology, Vol.3, No.12, December 2015 E-ISSN: 2321-9637
-
Peter J Milner, Akehurst S, Brace CJ, Vaughan ND, Performance Investigations of a Novel Rolling Traction CVT Consultant Engineers, Society of Automotive Engineers, Inc.
-
Kodgire, V. D. (2017) Material Science and Metallurgy for Engineers, Everest Publishing House.
-
Bhandari, V. B. (2007) Design of Machine Element, McGraw-
Hill Education.
-
Smithson, R., Miller, D., and Allen, D. Scalability for an Alternative Rolling Traction CVT, SAE Paper 2004-01- 0355, 2004.