
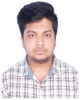
- Open Access
- Authors : Athreya Tallanje , Anush Matty Rajesh
- Paper ID : IJERTV10IS080221
- Volume & Issue : Volume 10, Issue 08 (August 2021)
- Published (First Online): 03-09-2021
- ISSN (Online) : 2278-0181
- Publisher Name : IJERT
- License:
This work is licensed under a Creative Commons Attribution 4.0 International License
Non-Linear Static Analysis on Roll Over Protective Structure (ROPS) of Asphalt Compactor
Athreya Tallanje Scholar in Mechanical Engineering Bangalore, Karnataka-560048 India |
Anush Matty Rajesh Scholar in Mechanical Engineering Bangalore, Karnataka-560061 India |
Abstract :- Roll Over Protective Structure (ROPS) is a passive safety component that protects an operator in case of machine roll. The ROPS has been made mandatory to be installed in the earth moving machines such as compactor, grader, excavator etc., as these machines operate at different inclinations and at different earth irregularities. In this study a ROPS has been proposed for an Asphalt Compactor that is in compliance with ISO 3471 standard. The proposed structure has been designed to meet the packaging constraints of the compactor and to undergo non- elastic deformation without touching the operator at any point when the loads are applied. A Non-linear static analysis has been carried out on the proposed structure using Finite Element Analysis (FEA) tool ANSYS to predict its energy absorption under non-elastic deformation when the loads of lateral, vertical and longitudinal are applied.
Keywords Roll Over Protective Structure; Deflection Limiting Volume; Energy absorption; Non elastic deformation; Non-linear analysis.
-
INTRODUCTION
Earth moving machines are also known as off-highway vehicles. They have a wide application in construction, mining, demolition, etc. The different earth moving vehicles include excavators, bull-dozers, backhoe loaders, compactors, trenchers, tower cranes, graders, pavers, dump trucks, etc. In this study, an Asphalt compactor has been considered. Asphalt compactor/ Roller compactors/ rollers are used in the construction of roads by compacting the soil, asphalt and concrete. The Roller compactors operate at various inclinations or uneven terrains like at the edge of a cliff. While operating in such conditions, the machine may lose balance and might roll over which results in injuries or death to the operator. The accidents due to the machine roll over is depicted in the Fig-1a. To prevent this, a Roll Over Protective Structure (ROPS) is installed. ROPS is a passive safety component installed in earth moving machinery to undergo a non-elastic deformation in order to absorb the energy completely in case of a machine roll over. THE ROPS must be tested to check its efficacy by simulating the rolling condition. Various standards are used as a benchmark to test the ROPS. Among them ISO 3471 is a widely used standard. ISO 3471 depicts the structure requirements, loading condition and acceptance criterion of the structure. Since testing is very expensive and time consuming, a finite element analysis (FEA) is preferred. In this study, a two post ROPS for an Asphalt Compactor of 9-tonne capacity has been proposed. The proposed ROPS is checked for its
compliance with the ISO 3471 standard by performing a non- linear static analysis.
Fig. 1. Rollover Accident of a Compactor [17]
-
OUTLINE OF ROLL OVER PROTECTIVE STRUCTURE (ROPS)
The ROPS proposed in this study is based on the ISO 3471 and ISO 3164 standards. ISO 3471 specifies the magnitude of loads that has to be applied on the ROPS in lateral, longitudinal and vertical direction. It also specifies the minimum lateral energy to be absorbed by the ROPS under non-elastic conditions. Acceptance criteria for the design is depicted in this standard. ISO 3164 specifies the dimensions of DLV (Deflecting Limiting Volume). A DLV is a space where the operator sits and operates the machine. As per the acceptance criteria in this standard, to ensure the safety of the operator, the deformed of ROPS should not enter the DLV at any instance [2].
Based on these standards, a ROPS is proposed for an Asphalt compactor. The specifications of the compactor are shown in Fig-2. The dimensions of ROPS are limited by the aspects of orthogonal DLV as per the standard and the packaging constraints in the machine. The proposed structure has a tower type vertical column. The cross section of the vertical column has been chosen by using an iterative approach to get the required stiffness. Simple square cross sectioned beams are used throughout the structure. The entire structure is made of ASTM A36 steel and has a thickness of 5 mm. The proposed structure has a total mass of 154.29 kg. The dimensions of the proposed ROPS and the DLV are shown in Fig-3 and Fig-4 respectively.
Fig. 2. Specifications of Chosen Asphalt Comactor[15]
The compactor shown in the Fig-2 is just for the depiction of the specifications and does not represent any model or any brand. Also, the ROPS in Fig-2 does not represent the ROPS that has been proposed in this study.
TABLE I. SPECIFICATIONS OF CHOSEN ASPHALT COMPACTOR
Parameters
Values
Overall Length (L)
5710 mm
Overall Width (W)
2300 mm
Height with ROPS/FOPS (H)
3010 mm
Wheel Base (L)
2900 mm
Operating Weight – with ROPS/FOPS
9000
Fig. 3. Dimensions of Proposed ROPS
Fig. 4. Dimensions of the Deflection Limiting Volume (DLV) [2]
ASTM A 36 is a low carbon steel with carbon content less than 0.3%. The properties of material are as specified in Table-2 and the Fig-5. shows the stress- strain curve of ASTM A36 [16].
TABLE II. MATERIAL PROPERTY DATA
Properties
Values
Yield Strength
250 MPa
Young's Modulus
200 GPa
Poisson's Ratio
0.3
Bulk Modulus
166.67 GPa
Shear Modulus
76.923 GPa
Tangent Modulus
1.45 GPa
Ultimate Strength
460 MPa
Fig. 5. Stress-Strain Curve of ASTM A36
The structure has been modelled using Catia V5, the model is depicted in the Fig-6.
Fig. 6. Catia V5 model of the proposed structure
The loads acting on the ROPS are calculated as per ISO 3471. These loads are dependent on the machine mass. Table-3 depicts the forces acting along lateral, longitudinal, vertical directions and the energy to be absorbed by the ROPS when lateral load is applied.
As per the ISO 3471, for a compactor of mass(m) 9010 kg, Lateral load force (N)=5*m
Vertical load force (N)=19.61*m Longitudinal load force (N)=4*m
Lateral Energy Absorption (J)=9 500* (m/10 000)1.25
TABLE III. LOADS AND ENERGY CALCULATIONS [1]
Parameter
Value
Mass of the machine (kg)
9010
Lateral load force (N)
45050
Vertical load force (N)
176686.1
Longitudinal load force (N)
36040
Lateral load energy (J)
8339.29
-
LOADING AND BOUNDARY CONDITIONS The proposed structure has been meshed with both
hexagonal and tetrahedron mesh of 10 mm size at appropriate locations. There are 105758 elements in the meshed model. The Fig-7 and Fig-8 shows the finite element model of the structure.
Base of the vertical columns of the sructure are fixed and the loads of lateral, vertical and longitudinal are applied on the ROPS sequentially as per standards as shown in the Fig-9, Fig-10 and Fig-11.
Fig. 7. Finite Element Model of the ROPS
Fig. 8. Finite Element Model of the ROPS
Fig. 9. Boundary Conditions for Lateral Loading
Fig. 10. Boundary Conditions for Vertical Loading
Fig. 11. Boundary Conditions for Longitudinal Loading
-
RESULTS AND DISCUSSIONS
A Non-linear static analysis is carried out using Finite Element Analysis to predict the energy absorption capacity of the ROPS when it undergoes a non-elastic deformation. Both material and geometric nonlinearities are considered and the loads are applied gradually until the force-energy requirements as specified in ISO 3471 are reached. The studies reveal that the most roll over takes place in the lateral direction, hence it is very important to check the energy absorption capacity of the ROPS for the lateral load. The energy absorption capacity of the structure is found by plotting load vs deformation curve as specified in ISO 3471.
Fig. 12. Load vs Deformation graph as specified in ISO 3471 [1]
The area under the curve shown in the Fig-12 is used to predict the energy absorption, therefore
U=(1*F1)/2+((2-1)*(F1+F2)/2)+………+((N-N-
1)*(FN-1+FN)/2)) ———————-(1)
where, U is the Energy absorption, is the deformation and F is the load [1]
-
Lateral Loading
The loads are applied gradually until a magnitude of 45050 N is attained. The direction of load is as depicted in Fig-9. The Fig-13 shows the non-elastic deformation of the structure that is predicted using the FEA tool ANSYS for these loads. The
maximum deformation of the structure for the applied loads is 316mm.
Fig. 13. Deformation due to non-linear Lateral Loading
Fig. 14. Load vs Deflection graph for lateral load
As shown in Fig. 14, the curve is linear up to a limit. In this region the lateral load is directly proportional to the structure's deformation. Following the limit, a substantial change in deformation is observed for a small change in load. This section of the graph shows the material non-linearity of the structure.
From equation 1, Energy absorption for the curve shown in Fig-14 is calculated and tabulated in Table-4.
TABLE IV. ENERGY ABSORPTION CALCULATION TABLE FOR
S. No.
Time (Sec)
Lateral Load (N)
Deflection (mm)
Energy Absorption(J)
1
1
0
0
0
2
1.2
1001.1
1.55
0.77
3
1.4
2002.2
3.11
3.11
4
1.7
3503.9
5.44
9.54
5
2
5005.6
7.78
19.48
6
2.2
6006.7
9.34
28.07
S. No.
Time (Sec)
Lateral Load (N)
Deflection (mm)
Energy Absorption(J)
1
1
0
0
0
2
1.2
1001.1
1.55
0.77
3
1.4
2002.2
3.11
3.11
4
1.7
3503.9
5.44
9.54
5
2
5005.6
7.78
19.48
6
2.2
6006.7
9.34
28.07
LATERAL LOADING
7
2.4
7007.8
10.90
48.34
8
2.7
8509.4
13.24
66.50
9
3
10011
15.58
88.20
10
3.2
11012
17.15
104.64
11
3.4
12013
18.71
122.66
12
3.7
13515
21.06
152.64
13
4
15017
23.41
186.18
14
4.2
16018
24.98
210.51
15
4.4
17019
26.55
251.88
16
4.7
18521
28.90
293.73
17
5
20022
31.26
339.17
18
5.2
21023
32.83
371.45
19
5.4
22024
34.41
405.40
20
5.7
23526
36.79
459.53
21
6
25028
39.18
517.63
22
6.2
26029
40.79
558.75
23
6.4
27030
42.45
617.68
24
6.7
28532
45.13
692.30
25
7
30033
48.15
780.53
26
7.2
31034
50.37
848.43
27
7.4
32036
52.81
925.38
28
7.7
33537
56.92
1060.23
29
8
35039
61.94
1232.36
30
8.2
36040
66.08
1379.17
31
8.4
37041
71.02
1496.05
32
8.7
38543
81.48
1891.54
33
9
40044
97.54
2522.60
34
9.2
41046
115.52
3099.45
35
9.4
42047
145.12
4329.22
36
9.7
43548
217.53
7428.19
37
10
45050
315.99
11479.35
td>
13515
7
2.4
7007.8
10.90
48.34
8
2.7
8509.4
13.24
66.50
9
3
10011
15.58
88.20
10
3.2
11012
17.15
104.64
11
3.4
12013
18.71
122.66
12
3.7
21.06
152.64
13
4
15017
23.41
186.18
14
4.2
16018
24.98
210.51
15
4.4
17019
26.55
251.88
16
4.7
18521
28.90
293.73
17
5
20022
31.26
339.17
18
5.2
21023
32.83
371.45
19
5.4
22024
34.41
405.40
20
5.7
23526
36.79
459.53
21
6
25028
39.18
517.63
22
6.2
26029
40.79
558.75
23
6.4
27030
42.45
617.68
24
6.7
28532
45.13
692.30
25
7
30033
48.15
780.53
26
7.2
31034
50.37
848.43
27
7.4
32036
52.81
925.38
28
7.7
33537
56.92
1060.23
29
8
35039
61.94
1232.36
30
8.2
36040
66.08
1379.17
31
8.4
37041
71.02
1496.05
32
8.7
38543
81.48
1891.54
33
9
40044
97.54
2522.60
34
9.2
41046
115.52
3099.45
35
9.4
42047
145.12
4329.22
36
9.7
43548
217.53
7428.19
37
10
45050
315.99
11479.35
Fig. 15. Energy Absorption vs time for lateral load
In this study, the loads are applied to the structure gradually with respect to time. From the Fig-15, it can be clearly observed that up to 8 seconds the energy absorption is very less. This is because the material in that region behaves linearly. After 8 seconds the energy absorption has increased drastically due to material non-linearity.
Fig. 16. Energy Absorption vs deformation
As per the ISO 3471, the minimum energy absorption for the lateral load of 45050 N should be 8339.30J. The energy absorbed by the proposed structure is 11479.35 J and the maximum deformation is 315.99 mm. In the proposed structure there is a clearance of about 520 mm in the lateral direction. Therefore, the deformation does not enter the Deflection Limiting Volume (DLV) at any instance. Energy absorption vs time and Energy absorption vs Lateral Load are plotted to understand the behaviour of the ROPS when lateral loads are applied.
The plot in the Fig-16 shows that up to 100mm deformation, the energy absorbed by the structure is quite low. Following that, the energy absorption in the structure steadily increases due to the material's non-linear behaviour.
-
Vertical Loading
The loads are applied gradually until a magnitude of 176686.1 N is attained. The direction of load is as depicted in the Fig-10. The Fig-17 shows the non-elastic deformation of the structure. The maximum deformation of the structure for the applied load is 352.56mm.
7
2.4
28652
13.06
237.76
8
2.7
33427
15.99
328.59
9
3
38202
18.97
435.38
10
3.2
42978
20.98
517.13
11
3.4
47753
23.02
609.45
12
3.7
52528
26.12
765.14
13
4
57304
29.29
938.89
14
4.2
62079
31.43
1066.81
15
4.4
66854
33.60
1263.10
16
4.7
71630
36.92
1492.85
17
5
76405
40.30
1743.32
18
5.2
81180
42.60
1924.23
19
5.4
85955
44.92
2118.61
20
5.7
90731
48.47
2431.79
21
6
95506
52.12
2771.766
22
6.2
100280
54.61
3015.32
23
6.4
105060
57.17
3267.01
24
6.7
109830
61.14
3693.56
25
7
114610
65.46
4177.90
26
7.2
119,380
68.80
4568.55
27
7.4
124160
72.75
5049.54
28
7.7
133710
81
6112.87
29
8
138480
87.99
7064.72
30
8.2
143260
94.11
7926.42
31
8.4
148030
99.48
8146.51
32
8.7
152810
110.33
9777.52
33
9
157,580.00
149.2
15809.95
34
9.2
176,686.10
352.56
65134.40
7
2.4
28652
13.06
237.76
8
2.7
33427
15.99
328.59
9
3
38202
18.97
435.38
10
3.2
42978
20.98
517.13
11
3.4
47753
23.02
609.45
12
3.7
52528
26.12
765.14
13
4
57304
29.29
938.89
14
4.2
62079
31.43
1066.81
15
4.4
66854
33.60
1263.10
16
4.7
71630
36.92
1492.85
17
5
76405
40.30
1743.32
18
5.2
81180
42.60
1924.23
19
5.4
85955
44.92
2118.61
20
5.7
90731
48.47
2431.79
21
6
95506
52.12
2771.766
22
6.2
100280
54.61
3015.32
23
6.4
105060
57.17
3267.01
24
6.7
109830
61.14
3693.56
25
7
114610
65.46
4177.90
26
7.2
119,380
68.80
4568.55
27
7.4
124160
72.75
5049.54
28
7.7
133710
81
6112.87
29
8
138480
87.99
7064.72
30
8.2
143260
94.11
7926.42
31
8.4
148030
99.48
8146.51
32
8.7
152810
110.33
9777.52
33
9
157,580.00
149.2
15809.95
34
9.2
176,686.10
352.56
65134.40
Fig. 17. Deformation due to Non-Linear static Vertical load
Fig. 18. Load vs Deflection graph for vertical load
The curve shown in Fig-18 is linear up to a limit. In this region the vertical load is directly proportional to the structure's deformation. Following the limit, a substantial change in deformation is observed for a small change in load. This section of the graph shows the material non-linearity of the structure.
From equation 1, Energy absorption for the curve shown in Fig-18 is calculated and tabulated in Table-5.
Sl. No.
Time (Sec)
Vertical Load (N)
Deflection (mm)
Energy Absorption(J)
1
1
0
0
0
2
1.2
4775.3
1.8
4.31
3
1.4
9550.6
3.63
17.40
4
1.7
14326
6.40
50.53
5
2
19101
9.22
97.64
6
2.2
23877
11.14
138.71
Sl. No.
Time (Sec)
Vertical Load (N)
Deflection (mm)
Energy Absorption(J)
1
1
0
0
0
2
1.2
4775.3
1.8
4.31
3
1.4
9550.6
3.63
17.40
4
1.7
14326
6.40
50.53
5
2
19101
9.22
97.64
6
2.2
23877
11.14
138.71
TABLE V. ENERGY ABSORPTION CALCULATION TABLE FOR VERTICAL LOADING
For the maximum vertical load of 176686.1 N, the energy absorbed by the structure is 65134.40 J and the maximum deformation is 352.56 mm. In the proposed structure there is a clearance of about 475 mm in the vertical direction. Therefore, the deformation does not enter the Deflection Limiting Volume (DLV) at any instance. Energy absorption vs time and Energy absorption vs Vertical Load are plotted to understand the behaviour of the ROPS when vertical loads are applied.
Fig. 19. Energy Absorption vs time for vertical load
Fig. 20. Energy Absorption vs deformation
The graphs in Fig-19 & Fig-20 depict that the energy absorbed by the structure is significantly low for smaller loads as the material behaves elastically. As the load increases over time, the deformation of the structure rises owing to non-elastic behaviour, which increases energy absorption.
-
Longitudinal Loading
The loads are applied gradually until a magnitude of 36040 N is attained. The direction of load is as depicted in the Fig-11. The Fig-21 shows the non-elastic deformation of the structure. The maximum deformation of the structure for the applied load is 185.33mm.
Fig. 21. Deformation due to Non-Linear static Longitudinal load
Fig. 22. Load vs Deflection graph for Longitudinal load
The curve shown in Fig-22 is linear up to a limit. In this region the longitudinal load is directly proportional to the structure's deformation. Following the limit, a substantial change in deformation is observed for a subtle change in load. This section of the graph shows the material non- linearity of the structure.
From equation 1, Energy absorption for the curve shown in Fig-22 is calculated and exhibited in Table-6.
TABLE VI. ENERGY ABSORPTION CALCULATION
S.
No.
Time (Sec)
Longitudinal Load (N)
Deflection (mm)
Energy Absorption(J)
1
1
0
0.00
0
2
1.2
800.89
1.59
0.63
3
1.4
1601.8
3.18
2.55
4
1.7
2803.1
5.57
7.81
5
2
4004.4
7.96
15.93
6
2.2
4805.3
9.55
22.95
7
2.4
5606.2
11.14
39.52
8
2.7
6807.6
13.53
54.35
9
3
8008.9
15.92
72.03
10
3.2
8809.8
17.51
85.42
11
3.4
9610.7
19.10
100.08
12
3.7
10812
21.49
124.45
13
4
12013
23.87
151.70
14
4.2
12814
25.47
171.46
15
4.4
13615
27.06
205.24
16
4.7
14816
29.44
239.17
17
5
16018
31.83
275.97
18
5.2
16819
33.42
302.08
19
5.4
17620
35.01
329.47
20
5.7
18821
37.40
372.95
21
6
20022
39.78
419.29
22
6.2
20823
41.37
451.78
23
6.4
21624
42.96
498.32
24
6.7
22825
45.35
551.35
25
7
24027
47.74
607.22
26
7.2
24828
49.33
646.06
27
7.4
25628
50.91
686.15
28
7.7
26830
53.30
748.70
29
8
28031
55.68
814.10
30
8.2
28832
57.27
859.30
31
8.4
29633
58.98
923.67
32
8.7
30834
62.66
1035.02
33
9
32036
68.39
1215.02
34
9.2
32836
74.94
1442.91
35
9.4
33637
86.34
1821.91
36
9.7
34839
118.05
2907.43
37
10
36040
185.33
5724.01
For the maximum longitudinal load of 36040 N, the energy absorbed by the structure is 5724 J and the maximum deformation is 185.33 mm. In the structure there is a clearance of about 250 mm in the longitudinal direction. Therefore, the predicted deformation does not enter the Deflection Limiting Volume (DLV) at any instance. Energy absorption vs time and Energy absorption vs Longitudinal Load are plotted to understand the behaviour of the ROPS when Longitudinal loads are applied.
Fig. 23. Energy Absorption vs time for Longitudinal load
Fig. 24. Energy Absorption vs deformation
The plots in the Fig-23 & Fig-24 show that the energy absorbed is significantly lower for smaller loads because the material behaves elastically. As the load increases over time, the deformation of the structure rises owing to non-elastic behaviour of the material, which increases energy absorption.
TABLE VII. COMPARISON TABLE
Directio n of Loading
Required Minimum Energy Absorption as per standard (J)
Energy Absorpti on by the proposed structure (J)
Deformat ion observed (mm)
Actual Clear ance (mm)
Lateral
8339.30
11479.37
315.99
520
Vertical
Not Specified in the standard
65134.40
352.56
475
Longitudin al
Not Specified in the standard
5724.01
185.33
250
From the above table it can be inferred that the deformations due to the lateral, vertical and longitudinal loads do not enter the Deflection Limiting volume and the energy absorption in the lateral case is more than the required minimum energy absorption as specified in ISO 3471. Therefore, it can be concluded that the proposed ROPS is safe.
-
-
CONCLUSION
A Roll Over Protective structure (ROPS) for an Asphalt compactor of 9-tonne has been proposed in this study. A Non-Linear static analysis has been carried out on the proposed structure and non-elastic deformations, energy absorptions are predicted for lateral, vertical and longitudinal loads using FEA tool ANSYS. As specified in the acceptance criterion of the standard, deformations are not entering the Deflection limiting point at any instance when the loads are applied. Also, the absorbed energy by the structure is more than the required minimum energy. Since the criterions specified in the standards are met, it can be concluded that the proposed ROPS is safe.
REFERENCES
-
International Organization for Standardization (2008) ISO 3471:2008: Earth-moving machinery Roll-over protective structures Laboratory tests and performance requirements. Geneva, ISO.
-
International Organization for Standardization (2008) ISO 3164:2013: Earth-moving machinery Laboratory evaluations of protective structures Specifications for deflection-limiting volume. Geneva, ISO.
-
Sakthivel M, Dhandapani N, Vetriselvan V, Arunachalam J. Design and Analysis of Tractor Roll Over Protective Structure for the Influence of Deformation, Stress Distribution and Strain Energy. Journal of Physics: Conference Series. 2021;1717:012029.
-
Yang Z, Yun C. Mechanical Analysis of ROPS Lateral Loading Test- bed for Mining Dump Truck. Journal of Physics: Conference Series. 2020;1575:012004.
-
Kumar V, Dr. Mallesh G, Radhakrishna K R. Non-Linear Analysis of a Two Post Roll-Over Protective Structure for Motor Grader. International Journal of Engineering and Advanced Technology. 2020;9(4):2339-2344.
-
Rajesh Kumar T, Haridass R, Dhandapani N V, Dinakar M. Non- Linear Static Analysis of Off-Road Vehicle Cabin ROPS Structure Using Finite Element Method. International Journal of Engineering & Technology. 2018;7(2.24):411.
-
Vishnu P, Manjunath A R, H S Kumaraswamy. Finite Element Analysis and Cost Effective Design for Roll Over Protection Structure (ROPS) of Soil Compactor. International Journal of Engineering Research in Mechanical and Civil Engineering (IJERMCE). 2017;2(4):7.
-
Li W, Tao J, Liu M. Nonlinear analysis and uncertainty optimisation of mining dump truck's ROPS based on TPS-HDMR. International Journal of Heavy Vehicle Systems. 2015;22(1):73.
-
Vamshi Chennuri, Harish Kothagadi, Riyazuddin Mohammad. Design And Stress Analysis Of Four-post Rollover Protective Structure Of Agricultural-wheeled Tractor. International Journal of Mechanical Engineering and Robotics Research. 2015;.
-
Syed Khaisar Sardar, Kiran Narkar, D R Panchagade. Non- Linear Analysis Of Roll Over Protection Structure. International Journal of Mechanical And Production Engineering. 2014;2(9).
-
Malik M, Kshirsagar S, Barve S. DOE for Non-Linear Structural Analysis of ROPS (Rollover Protective Structure). SAE Technical Paper Series. 2012;.
-
J. Mangado, J.I. Arana, C. Jarén, S. Arazuri, P. Arnal. Design Calculations on Roll-over Protective Structures for Agricultural Tractors. Biosystems Engineering. 2007;96(2):181-191.
-
Etherton J, Ronaghi M, Current R. Development of a pultruded FRP composite material ROPS for farm tractors. Composite Structures. 2007;78(2):162-169.
- Soil Compactor. (n.d.). Sakainet. Retrieved May 28, 2021, from https://www.sakainet.co.jp/en/products/soil_compactor/sv520series.ht ml
-
AZoM. (2014, May 23). ASTM A36 Mild/Low Carbon Steel. https://www.azom.com/article.aspx?ArticleID=6117#:%7E:text=AST
M%20A36%20is%20the%20most,bend%20more%20readily%20than
%20C1018.
-
Compactor Rollover Injures Operator. (2014, November 3). YouTube. https://www.youtube.com/watch?v=jZRUDwuRufY