
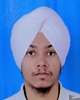
- Open Access
- Authors : Lovepreet Singh, Harmanjit Singh, Jaspal Singh, Jaspreet Singh
- Paper ID : IJERTV13IS060046
- Volume & Issue : Volume 13, Issue 06 (June 2024)
- Published (First Online): 12-06-2024
- ISSN (Online) : 2278-0181
- Publisher Name : IJERT
- License:
This work is licensed under a Creative Commons Attribution 4.0 International License
Numerical Study of Tube to Increase The Heat Transfer Performance by Geometric Modification Using CFD Method
Lovepreet Singh, Harmanjit Singh, Jaspal Singh, Jaspreet Singh,
Student, Department of Mechanical Engineering, Chandigarh University (CU), Mohali, Punjab(INDIA), Pin code- 140413
Abstract This project comprises a survey of the heat transfer performance of the tube with different geometrical modification following inserted dents over the surface and insert helical baffles in the tube. In this research water and Ethylene glycol used as a flowing fluid and find out the heat transfer rate in all tubes. Results are reveals that the rate of heat transfer increased in tubes which has dents over surface and helical baffles. The rate of heat transfer in tubes which has dents increased as 5% as compared to simple tube while it increased 10% in case of helical baffles. The heat transfer coefficient increased as increasing the inlet temperature and velocity of flowing fluid.
Keywords- Nanofluid, angular bend tube, Rate of Heat Transfer, Pressure drop, Heat transfer coefficient.
Nomenclature:
– Density
– Kinematic Viscosity
Cp – Specific Heat Capacity k – Thermal Conductivity
h – Heat Transfer Co-efficient V – Velocity
Dh – Hydraulic Diameter Di – Diameter of inner tube Do – Diameter of outer tube
Ah – Cross-sectional area of inner tube passing hot fluid Ac – Cross-sectional area of inner tube passing cold fluid
p – Pressure Drop
U – Overall Heat Transfer Co-efficient Q – Heat Transfer Rate
°C – Degree Celsius
T – Temperature gradient K Kelvin
INTRODUCTION
Heat exchange processes are very crucial and widely used in modern thermal engineering applications. On this account, various studies on heat exchangers have been performed to increase the thermal or heat transfer performance between the fluids during the past several decades [1]. Most of the studies have focused on the development of high-performance compact heat exchangers. The alternate goal of the researchers is to increase the system thermodynamic energy and develop a less expensive heat exchanger. Bergles et al. [2,3] and Webb er al. [4,5] have attempted to simplify this problem by suggesting Performance Evaluation Criteria (PEC). PEC defines the performance benefits of the exchanger which are having enhanced surface area. Bergles et al. [2,3] introduced a method to find out the comparative performance of existing surfaces. Webb et al. [4,5] by using PEC to select the preferred enhancement type to calculate the optimum geometrical parameters for the preferred enhancement type. Various types of heat exchangers are developed to exchange the thermal energy between the fluids for a specific application. There are methods to enhance the heat transfer of the heat exchanger like geometry modification or fluid modification. In case geometry modification, some changes are done in the geometry of the heat exchanger for example adding the baffles in shell and tube exchanger, by adding baffles the turbulence flow developed inside the heat exchanger and baffle make effect on the pressure drop of the heat exchanger. Parnita et al. [6] study the effect of the baffles inside the shell and tube heat exchanger. In their investigation single, double segmental and helical baffles are investigated and evaluate the pressure drop with each baffle of the heat exchanger. Increasing the number of baffles beyond certain number gives serious effect on the pressure drop. They investigate in case of single segmental baffles more pressure drop is noticed while it is reduced by adding helical baffles. Parnita et al. [6] also noticed that single segmental shows the dead zone where the heat transfer not take place effectively and this problem solved by double segmental baffles and these baffles are reduced the vibrational damages. But the use of helical baffles over other two lowers the pressure drop which in turn increases the overall system efficiency. So, it is proved that helical baffles are more advantageous than other two types of baffles.
By fluid modification there are modern fluids are introduced which have higher thermal conductivity, because of higher thermal conductivity the heat transfer performance also increases. These fluids are nanofluid. Choi et al [7] introduced the concept of nanofluid. Nanofluid in the modern fluid. In the base fluid nanoparticles are added, because of the addition of nanoparticles thermal conductivity of the fluid increases. So, the rate of the heat transfer or heat transfer performance increased. There are several experiment research done on the nanofluids and investigate the heat transfer performance and also illustrate the effect of the different nanoparticles on the thermal conductivity and in all experimental data, volume fraction of the nanoparticles is considered as a major parameter. Volume fraction also make serious effect on the thermal conductivity of the nanofluid. Farajollahi et al. [8] evaluate the result of the heat transfer of double pipe heat exchanger by using c-Al2O3/water and TiO2/water nanofluids on different volume concentration (0.3%, 0.5% ,0.75 %, 1%) and found out heat transfer increased by 19-56% and 18-58% AlO/water and TiO/water nanofluids as compared to distilled water, respectively.
INTRODUCTION TO TUBES:
The tube is the prominent part of the heat exchanger and the tube plays a vital role in the heat exchanger or other heat removal devices. It is specially designed to transfer the heat or cooling the fluid with low-medium viscosity. The tube is used to increase the heat transfer performance to place it inside the shell of the heat exchanger which provides a more heat transfer between the fluid flowing inside the tubes and fluid flowing inside the shell of the heat exchanger, this information is experimentally investigated by Labbadlia et al [9]. Main purpose of the tubes inside the shell is to enhance the heat transfer rate. There are so many methods to increase the heat transfer of heat exchanger for example geometry modification and fluid modification. Geometry modification is focused on modifying the geometry of the tube the rate of heat transfer will increase. The geometry modification of heat exchanger is one of the efficient ways to reduce the fouling factor, it is said by Anthony Chambon et al [10]. Nowadays the geometry modification of shell and tube in heat exchanger receive some attention because to enhance the heat transfer rate in heat exchanger in heat exchanger the fouling factor is one of common factor which reduce the heat transfer rate in heat exchanger So Yang et al. [11] and S. Eiamsa-ard et al [12] studied on fouling factor and enhance the heat transfer by adding the twisted tape in the tube to increase the turbulence flow in the tube so that the fouling will reduce and the heat transfer rate will increase and the further thermal characteristics of the round tube in which the twisted tape was fitted were studied by S. Eiamsa-ard, P. Promvonge [13]
On the other hand, tube material also affects heat transfer performance, mainly these tubes are made up of copper or steel alloys which May be welded but their many numerous alloys can also be used as per their desire like titanium, aluminum, and nickel. The material of the tube depends upon their requirements. M. A. Deleaver et al [14] studied the effects of micro structural metal foam properties, such as porosity, pore and fiber diameters, pore density, and relative density, on the heat exchanger performance.
They found that by using porous material the high specific area increased because of it the heat will extractmore through the
area. Because of the high thermal conductivity of aluminum, it will transfer more heat. Selecting a suitable material for a tube in cases that play an effective role in cost determination. In the study, tubes made of copper alloy, type 304 and 316 stainless steel, 6 percent molybdenum alloy, Super Ferritic and titanium. Nowadays every industry desire to enhance the efficiency of heat exchangers. An easy way to increase the heat transfer rate in any heat exchanger is by increasing the efficiency of the tube and shell in heat exchangers. This research was done by He, Z., Fang, et al [15].
Beside geometry modification, fluid also makes an impact on the rate of heat transfer. To increase the heat transfer of heat exchangers, researchers are investigating the influence of heat transfer by using different fluids. After investigation, Choi et al
[16] was introduced to nanofluids. Nanofluid is a liquid which contains nanometer size particles. These nanoparticles can be metals, oxides or allotropes of carbon with thermal conductivity. Metal nanoparticles should be chemically stable for example copper, gold and silver. Metal oxide for example aluminum, silica, titania, bismuth oxide, titania and zirconia are used as nanoparticles. Choi, experimentally studied that by adding and suspending the nanoparticles in base fluid the thermal conductivity increases so heat transfer will also increase. Yang et al. [17] studied the convective heat transfer performance, to increase it they used graphite nanoparticles in aq laminar flow through circular pipe. By adding the nanoparticles, the thermal conductivity increased and Yang et al. basically found that to increasing the volume fraction of nanoparticle and Reynolds number the heat transfer increased. There are some other factors are existed which are influence to the rate of heat transfer namely shape of tube, size of tube or, surface roughness of tube. Some important factors mentioned below which are responsible for increasing the heat transfer.DESIGN MODIFY WITH DIFFERENT TUBE GEOMETRY:
The rate of heat transfer in shell and tube heat exchanger is experimentally increased by N. jamshidis work. They use the Wilson plot method to calculate the heat transmitted coefficient. Mass flow rate of fluid, pitch diameter of fluid are most favorable parameters which are determined by the Taguchi method. Nusselt number, larger coil diameter and coil pitch are used to give a good result of rate of heat transfer [18]. The shell and tube heat exchanger used in food corporations, with the help of Newtonian and non-Newtonian fluids experiment of the helical tube is modified, the friction loss and convective heat is considered in this process. And the result given as an increase in the Reynolds number is that the heating process will be high as compared to the cooling process. This information is given by S. Rozzi et al [19]. R. Hasseini et al [20] experimentally work on shell and tube heat exchanger by using the three tubes i.e. smooth tube, corrugated tube and micro fins tube. And Nusselt, Euler Reynolds and Prandtl number are used to declare the result by varying the shell and tube heat exchanger performance over these three tubes. The micro fin tube gives the better result than others at the higher production rate of Reynolds number and Prandtl number. Vidhya et al [21] determine the effect of insulation on the shell and tube heat exchanger. With the different loads thermal analysis is conducted on it. This investigation declared the result that requirement in the increment on heat transfer rate at below the critical thickness,
insulation is most important. M. Esapour et al [22] investigates change of phase in multi tube heat exchanger and effect of the tubes on the process. RT35 fluids melting characteristics used as the material has ability to change phase and water inside in inner tubes. They declared the result that the increment in the number of inner tubes than the melting time will decrease by 29%, and the reduction ratio increases when the temperature range is low. And for all the studies in their experiment the rate of mass flow increased, reduction ratio and the melting point is similar to 11%. Mosaffa et al [23] solve the problem of phase change by the method of transforming temperature and they use the finned tube to study the enhancement in heat transfer in the latent heat thermal storage. Abduljalil et al [24] are numerically studying the solidification of phase change material with the two types of fins i.e., internal and external fins. They said that the effect of length of fin is more than the thickness and the achievement of Case G (8-cell phase change material unit geometry) has completely solidified and consumes a short time.
DESIGN MODIFY WITH DIFFERENT ARRANGEMENT OF BAFFLES:
Bin Gao et al investigate on the baffles in shell tube heat exchanger on different angles i.e., 8º, 12º, 20º, 30º, 40º. They show that a heat exchanger with helical baffle with angle 40º gives better performance with other five angles and lower Reynolds numbers limit. Wen Quan Tao also does the related investigation with different baffles angles i.e. 20º, 30º, 40º, 50º with the help of the helical baffle which is overlapped with muddle. Result shows the helix baffle with a 40º angle gives the batter performance [25,26]. In Lahun Zhang et al [27] investigation on heat transfer coefficient and pressure drop with one normal baffle and three different baffles with helical angles i.e., 7º, 13º, 25º. The results indicated in the shell side coefficient per unit pressure drop required more space for other baffles like (7º, 13º, 25º etc.) then the simple baffles. With increment of angle at same condition, the heat transfer coefficient will decrease. The number of shapes of baffles provide an increment in the rate of heat transfer and the shell produces good performance because of the baffles have different functions like after baffles interact with the hot surface of tube bundles the fluid is mixed each other, it reduces the vibration and support the deformation of tubes. This information is given by Mica et al [28]. The shell and tube heat exchanger with segmental baffles has a high rate of heat transfer, used mostly in the industries. When the fluid flowing zig zag flows the huge pressure loss in heat exchanger this is the kind of disadvantage of it. The data is taken from Bell et al and Wang et al [29,30]. Mustapha et al [31] experimental investigation on shell and tube heat exchanger, shell side hydrothermal performance by using orientation and different arrangement of baffles. They numerically analyzed the arrangement of baffles in characteristic thermal and dynamic shell side in a heat exchanger fitted with the help of segmental baffles. The Reynolds numbers range from 3000 t0 10,000 with baffle cut value is 38% to investigate the baffles, with baffle number 6, 8 and 19 and these baffles studied by different orientation angles and the geometry configuration of three different baffles i.e., 106.6, 80 and 64 mm. Younes Menni et al
[32] are experimentally studying the enhancement of the heat transfer performance in the channel by using Z-shaped baffles.In the channel the regime of turbulence of Reynolds number is 4400 to 20,400 and Z-baffle 45° angle by the in-phase and out- phase system. The Z-baffles, TEF (thermal performance enhancement factor) and the Nu (Nusselt number) values for the in- phase are dependent on the Reynolds number, pitch and height of baffles. Z- baffles in the in-phase increase the friction loss as compared to the smooth channel which has no baffles. As increasing in Re, pitch, and baffle height, the TEF in-phase Z-baffles will decrease. Raheem et al [33] examine the performance of thermal hydraulic and design parameters by using nanofluid and L-shaped baffles in the curved- corrugated channel. They evaluate the different parameters to arrangement of L-baffles at corner angle 30°, 45°, 60°, and 90° with the range of Reynolds number 8000-32,00 and ZnO particles range 0-4%. The L-shaped baffles use to generate the variation in the structure and due to breaks in the boundary layer, increased turbulence flow as well as vertex flow formation so the performance factor of thermal-hydraulic system enhanced.
METHODOLOGY
To select the dimensions of tube heat exchanger by analyzing the literature reviews of tube heat exchanger. To determine the materials of tubes for better performance of thermal conductivity. To select the Aluminium material to the tube in ANSYS interface. The design specifications of Double Pipe Heat Exchanger are shown in the following tables 1 and 2.
Table 1. Dimensions of tube
Parameter |
Tube |
Length |
1000 mm |
Major Diameter |
152 mm |
Thickness |
10 mm |
Table 2. Material and fluid selection of flat tube
Tube |
Material |
Fluid |
Flat tube |
Aluminum |
Water and Ethylene Glycol |
GEOMETRY AND DESIGN:
Thermal Conductivity of nanofluids was calculated using equation given below:
Velocity of has been calculated by using following equation:
Density of nanofluids was calculated as
The average heat transfer coefficient of nanofluid in flat tube was calculated as
IJERTV13IS060046
(This work is licensed under a Creative Commons Attribution 4.0 International License.)
Following figures are showing the geometry of tubes with different geometrical parameters. There are three type of tubes the first one is simple tube showing in figure, second one has dents over the surface and last one has helical baffles which showing in figure 1 and figure 2 respectively :
Fig. 1. 3d Modeling of Simple Tube
Fig 2. Helical Baffles Inserted Tube
MESHING:
Fig 3. Meshing of Simple Tube
Fig. 4, Meshing Of Tubes Which Has Dents Over Surface
Fig 5. Meshing Of Tube Which Has Helical Baffles
OPERATING PARAMETERS:
The operating parameters of Aluminum oxide (Al2O3) are given in table below:
Table 3. properties of Water
Properties of Water |
|||
Densit y |
Specific heat |
Viscosit y |
Thermal Conductivity |
998.2 |
4182 |
0.00100 3 |
0.600 |
Properties of Ethylene glycol |
|||
Density |
Specific heat |
Viscosity |
Thermal Conductivity |
1111.4 |
2415 |
0.0157 |
0.252 |
Table 4. Ethylene Glycol Property
BOUNDARY CONDITIONS:
Three sets of boundary conditions have been taken into consideration for the investigation of flat tube Heat Exchanger. The boundary conditions are shown in table 5.
Table 5. Boundary condition
SIMULATION PROCEDURE:
-
To select Ansys fluent tool.
-
Select geometry option and draw tube in design modular.
-
Next to select meshing part and by using sizing meshing tool, meshing done on tube.
-
Define inlet, outlet and wall parameter of the tube.
-
Start setup of the ANSYS fluent.
-
Now allow the energy equation to on and select model name.
-
By using boundary conditions, table based on different temperatures, volume concentration and no fluid applied boundary conditions.
-
Initialize the process using hybrid initialization.
-
Calculate the simulation result by using simulation option.
-
After completing the simulation, in report menu, select surface integral menu and compute outlet temperature of the tube.
-
Same in report menu, select flux menu to calculate mass flow rate.
-
Transfer the data in excel sheet and calculate results of heat transfer.
RESULT AND DISCUSSION
In this investigation, the counter flow configuration of tubes has been taken into consideration and different materials and fluids selected.
HEAT TRANSFER RATE:
Set No. |
Fluid |
Veloc ity |
Inlet Tempera ture () |
Mass flow Rate Kg/s |
1. |
Water |
2m/s- 3 m/s |
100-140 |
15.17596 |
2. |
Ethylene Glycol |
2m/s- 3m/s |
100-140 |
15.17596 |
The rate of heat transfer determines the heat transfer performance in the Simple tube, tube with dents and tube with helical baffles. It has been evaluated by using following equation:
Q= m * cp* (Tin Tout)
HEAT TRANSFER IN SIMPLE TUBE WITH FLOWING WATER INSIDE THE TUBE:
The rate of heat transfer is measured by using asnys fluent tool. Following tables shows the heat trasnfer on 100 deg. Celcius temprature. But the velocity of the flowing fluid is varied from 2-3 m/s. The specific heat at 100 deg. Temprature ius found out that is given in the tables.
Table 6. Rate of heat transfer of water in simple tube at 100 deg.
V Ti To M cp Q
Temperature
2 |
100 |
97.63205 |
15.66937 |
4.2157 |
156.4205 |
2.5 |
100 |
97.82517 |
19.58672 |
4.2157 |
179.5795 |
3 |
100 |
97.98056 |
23.50406 |
4.2157 |
200.0984 |
Table 7. Rate of heat transfer of water in simple tube at 120 deg.
Temperature
Table 8. Rate of heat transfer of water in simple tube at 140 deg.
Temperature
V |
Ti |
To |
M |
cp |
Q |
2 |
140 |
136.4481 |
15.66937 |
4.2826 |
238.3525 |
2.5 |
140 |
136.7378 |
19.58672 |
4.2826 |
273.6401 |
3 |
140 |
136.9708 |
23.50406 |
4.2826 |
304.9147 |
HEAT TRANSFER IN TUBE WHICH HAS DENTS OVER THE SURFACE:
Similary, the rate of heat transfer is found out on different temprature and velocity. But in this case the dents are placed over the surafce of the tube. Due to dents the roughness of the tube surface is increased , cause of it the rate of heat trasnfer is increased which are showing in following tables.
Table 9. Rate of Heat transfer of water in tube at 100 deg.
V |
Ti |
To |
m |
cp Q |
2 |
100 |
97.50105 |
15.66937 |
4.157 165.074 |
2.5 |
100 |
97.72517 |
19.58672 |
4.2157 187.8367 |
3 |
100 |
97.88056 |
23.50406 |
4.2157 210.007 |
Temperature
Table 10. Rate of Heat transfer of water in tube at 120 deg.
Temperature
Table 11. Rate of Heat transfer of water in tube at 140 deg. Temperature
V |
Ti |
To |
m |
cp |
Q |
2 |
140 |
136.2705 |
15.66937 |
4.2826 |
250.2702 |
2.5 |
140 |
136.5747 |
19.58672 |
4.2826 |
287.3222 |
3 |
140 |
136.8193 |
23.50406 |
4.2826 |
320.1604 |
HEAT TRANSFER IN TUBE WHICH HAS HELICAL BAFFLES:
Helical baffles are also affected to the heat transfer of the tube. It can be easily identified by analyzing the given data in following tables. By adding helical baffles, the rate of heat transfer increased by 10 % as compared to the simple tube.
Table 12. Rate of Heat transfer of water in tube (helical baffles) at 100 deg. Temperature
V |
Ti |
To |
m |
cp |
Q |
2 |
100 |
97.39526 |
15.66937 |
4.2157 |
172.0626 |
2.5 |
100 |
97.60769 |
19.58672 |
4.2157 |
197.5374 |
3 |
100 |
97.77862 |
23.50406 |
4.2157 |
220.1082 |
Table 13. Rate of Heat transfer of water in tube (helical baffles) at 120 deg. Temperature
V |
Ti |
To |
m |
cp |
Q |
2 |
120 |
116.5813 |
15.66937 |
4.2435 |
227.3185 |
2.5 |
120 |
116.8601 |
19.58665 |
4.2435 |
260.9731 |
3 |
120 |
117.0844 |
23.50406 |
4.2435 |
290.7971 |
Table 14. Rate of Heat transfer of water in tube (helical baffles) at 140 deg. Temperature
V |
Ti |
To |
m |
cp |
Q |
2 |
140 |
136.0929 |
15.66937 |
4.2826 |
262.1878 |
2.5 |
140 |
136.4116 |
19.58672 |
4.2826 |
301.0042 |
3 |
140 |
136.6679 |
23.50406 |
4.2826 |
335.4062 |
HEAT TRANSFER IN SIMPLE TUBE WITH FLOWING ETHYLENE GLYCOL INSIDE THE TUBE:
V |
Ti |
To |
m |
cp |
Q |
2 |
120 |
116.8921 |
15.66937 |
4.2435 |
206.653 |
2.5 |
120 |
117.1456 |
19.58665 |
4.2435 |
237.248 |
3 |
120 |
117.3495 |
23.50406 |
4.2435 |
264.36 |
The rate of heat trasnfer calculate of the Ethylene Glycol also to flowing this fluid in all different geometrical modified tubes. On different temprature, different velocity the rate of heat trasnfer calculated.
Table 15. Rate of Heat transfer of Ethylene Glycol in tube at 100 deg.
Temperature.
V |
Ti |
To |
m |
cp |
Q |
2 |
100 |
98.11756 |
17.44637 |
2.433 |
79.90396 |
2.5 |
100 |
98.20725 |
21.80793 |
2.433 |
95.12097 |
3 |
100 |
98.26703 |
26.16909 |
2.433 |
110.3372 |
Table 16. Rate of Heat transfer of Ethylene Glycol in tube at 120 deg.
Temperature.
V |
Ti |
To |
m |
cp |
Q |
2 |
120 |
117.897 |
17.44617 |
2.4608 |
90.28502 |
2.5 |
120 |
118.0091 |
21.80793 |
2.4608 |
106.8416 |
3 |
120 |
118.0838 |
26.16909 |
2.4608 |
123.3973 |
Table 17. Rate of Heat transfer of Ethylene Glycol in tube at 140 deg.
Temperature.
V |
Ti |
To |
m |
cp |
Q |
2 |
140 |
137.6765 |
17.44637 |
2.4999 |
101.3375 |
2.5 |
140 |
137.811 |
21.80793 |
2.4999 |
119.3391 |
3 |
140 |
137.9006 |
26.16909 |
2.4999 |
137.343 |
HEAT TRANSFER IN TUBE WHICH HAS DENTS OVER THE SURFACE:
Similary, in case of heat transfer of water, the rate of heat transfer also increased as compare to the simple tubes.
Table 18. Rate of Heat transfer of water in tube at 100 deg.
Temperature.
V |
Ti |
To |
m |
cp |
Q |
2 |
100 |
98.02344 |
17.44637 |
2.433 |
83.89916 |
2.5 |
100 |
98.11761 |
21.80793 |
2.433 |
99.87702 |
3 |
100 |
98.18038 |
26.16909 |
2.433 |
115.854 |
Table 19. Rate of Heat transfer of water in tube at 120 deg.
V |
Ti |
To |
m |
cp |
Q |
2 |
120 |
117.7919 |
17.44617 |
2.4608 |
94.79927 |
2.5 |
120 |
117.9096 |
21.80793 |
2.4608 |
112.1836 |
3 |
120 |
117.988 |
26.16909 |
2.4608 |
129.5672 |
Temperature.
Table 20. Rate of Heat transfer of water in tube at 140 deg.
Temperature.
V |
Ti |
To |
m |
cp |
Q |
2 |
140 |
137.5603 |
17.44637 |
2.4999 |
106.4044 |
2.5 |
140 |
137.7016 |
21.80793 |
2.4999 |
125.3061 |
3 |
140 |
137.7956 |
26.16909 |
2.4999 |
144.2101 |
HEAT TRANSFER IN TUBE WHICH HAS HELICAL BAFFLES:
In helical baffles the heat transfer performance of tube is increased as compared to the other geometry of the tubes.
Table 21. Rate of Heat transfer of Ethylene Glycol in tube (helical baffles) at 100 deg. Temperature.
V |
Ti |
To |
m |
cp |
Q |
2 |
100 |
97.82578 |
17.44637 |
2.433 |
92.28908 |
2.5 |
100 |
97.92937 |
21.80793 |
2.433 |
109.8647 |
3 |
100 |
97.99842 |
26.16909 |
2.433 |
127.4394 |
Table 22. Rate of Heat transfer of Ethylene Glycol in tube (helical baffles) at 120 deg. Temperature.
V |
Ti |
To |
m |
cp |
Q |
2 |
120 |
117.571 |
17.44617 |
2.4608 |
104.2792 |
2.5 |
120 |
117.7005 |
21.80793 |
2.4608 |
123.402 |
3 |
120 |
117.7868 |
26.16909 |
2.4608 |
142.5239 |
Table 23. Rate of Heat transfer of Ethylene Glycol in tube (helical baffles) at 120 deg. Temperature.
V |
Ti |
To |
m |
cp |
Q |
2 |
140 |
137.4442 |
17.44637 |
2.4999 |
111.4713 |
2.5 |
140 |
137.5921 |
21.80793 |
2.4999 |
131.273 |
3 |
140 |
137.6907 |
26.16909 |
2.4999 |
151.0773 |
GRAPH OF HEAT TRANSFER OF WATER IN ALL GEOMETRIES OF TUBE:
By analyzing the data of all tables of the heat transfer of the water and Ethylene Glycol to flowing inside the different modified tubes, the graphs are generated.
Heat Transfer In diffrent geometry of tubes at 100 deg. using water as fluid
250
200
150
100
50
0
2
2.5
3
simple tube heat transfer Dented tube heat Transfer
helical baffle tube heat transfer
Heat Transfer In diffrent geometry of tubes at 100 deg. using EG as fluid
140
120
100
80
60
40
20
0
2
2.5
3
simple tube heat transfer Dented tube heat Transfer
helical baffle tube heat transfer
Fig. 6 Graph of Heat transfer in all tubes at 100 deg. Temperature.
Heat Transfer In diffrent geometry of tubes at 120 deg. using water as fluid
350
300
250
200
150
100
50
0
2
2.5
3
simple tube heat transfer Dented tube heat Transfer
helical baffle tube heat transfer
Fig. 9 Graph of Heat transfer in all tubes at 100 deg. Temperature
Heat Transfer In diffrent geometry of tubes at 120 deg. using EG as fluid
160
140
120
100
80
60
40
20
0
2
2.5
3
simple tube heat transfer
Dented tube heat Transfer
helical baffle tube heat transfer
Fig. 7 Graph of Heat transfer in all tubes at 120 deg. Temperature.
Heat Transfer In diffrent geometry of tubes at 140 deg. using water as fluid
400
350
300
250
200
150
100
50
0
2
2.5
3
simple tube heat transfer Dented tube heat Transfer
helical baffle tube heat transfer
Fig. 10 Graph of Heat transfer in all tubes at 120 deg. Temperature
Fig. 8 Graph of Heat transfer in all tubes at 140 deg. Temperature
GRAPH OF HEAT TRANSFER OF EG IN ALL GEOMETRIES OF TUBE:
Similarly, water, the graphs of heat transfer of Ethylene Glycol are also draw, which are following given:
Heat Transfer In diffrent geometry of tubes at 140 deg. using EG as fluid
160
140
120
100
80
60
40
20
0
2
2.5
3
simple tube heat transfer
Dented tube heat Transfer
helical baffle tube heat transfer
Fig. 11 Graph of Heat transfer in all tubes at 140 deg. Temperature
CONCLUSION
The analysis reveals about the rate of heat performance of the tube with different geometrical modification. By numerical study of the tubes the results comprise that the rate of heat transfer increase in case of tubes which has dents over surface and also increased with helical baffles. The fluid is used namely water and Ethylene glycol inside the tube to transfer the heat. The material of the tubes is Aluminum. Fluid flow inside the tubes on different temperature like 100 , 120 and 140 mass flow rate of the fluid is varied according to the velocity of the fluid that is varied 2-3 m/s.
Following results are find out after analyses a numerical study of the tubes:
-
Rate of heat transfer increased with increasing the surface roughness of the tube.
-
Rate of heat transfer also enhanced by adding the helical baffles inside the tube.
-
As compared to heat transfer of water and Ethylene glycol, water has higher heat transfer.
-
Heat transfer also depends on the velocity of the flowing fluid.
REFERENCES
[1] S.U.S. Choi, Enhancing thermal conductivity of fluids with nanoparticle, ASME FED 231 (1995) 99. [2]. Bergles, B.-H. Chun, H.U. Kang, S.H. Kim, Effect of alumina nanoparticles in the fluid on heat transfer in double-pipe heat exchanger system, KoreanJ. Chem. Eng. 25 (2008) 966971.
[3]. Bergles, Y. Xuan, Q. Li, Investigation on convective heat transfer and flow features of nanofluide [4]. Webb, Y. Xuan, Q. Li, Investigation on convective heat transfer and flow features of nanofluids, ASME Journal of Heat Transfer 125 (2003) 151. [5]. Webb, Y. Yang, Z.G. Zhang, E.A. Grulke, W.B. Anderson, G. Wu, Heat transfer properties of nanoparticlein-fluid dispersions (nanofluids) in laminar flow, International Journal of Heat and Mass Transfer 48 (6) (2005) 1107. Applied Thermal Engineering xxx (2016) xxxxxx. [6]. Choi, Pranita Bichkar, Ojas Dandgaval, Pranita Dalvi, Rhushabh Godase, Tapobrata, Study of Shell and Tube Heat Exchanger with the Effect of Types of Baffles, Procedia Manufacturing, Volume 20, 2018, Pages 195- 200. [7]. Reddy MCS, Rao VV., Experimental studies on thermal conductivity of blends of ethylene glycolwater-based TiOInt Commun Heat Mass Transf. 2013;46:316. 2 nanofluids. [8]. Abazar Vahdat Azada, Nader Vahdat Azad, Application of nanofluids for the optimal design of shell and tube heat exchangers using genetic algorithm, Case Studies in Thermal Engineering, Volume 8, September 2016, Pages 198-206. [9]. Labbadlia, Laribi, B., Chetti, B., Hendrick, P, Numerical study of the influence of tube arrangement on the flow distribution in the header of shell and tube heat exchangers. Appl. Therm. Eng. 126, 315321 (2017). [10]. Shell-and-tube Heat Exchanger Geometry Modification: An Efficient way to Mitigate Fouling Anthony Chambon, Zoé Anxionnaz-Minvielle, Grégory Cwicklinski, Nathalie Guintrand, Aline Buffet & Bernard Vinet Nathalie Guintrand, Aline Buffet & Bernard Vinet (2018): Shell-and-tube Heat Exchanger. [11]. Yang, M., Wood, Z., Rickard, B., Crittenden, B., Gough, M., Droegemueller, P., Higley, T., Mitigation of crude oil fouling by turbulence enhancement in a batch stirred cell, Applied Therm. Eng. Vol. 54, no. 2,pp. 516-520, 2013.
[12]. S. Eiamsa-ard, P. Seemawute, K. Wongcharee, Influences of peripherally- cut twisted tape insert on heat transfer and thermal performance characteristics in laminar and turbulent tube flows, Experimental Thermal and Fluid Science 34 (2010). [13]. S. Eiamsa-ard, P. Promvonge, Thermal characteristics in round tube fitted with serrated twisted tape, Appl. Therm. Eng. 30 (13) (2010). [14]. M. A. Delavar and M. Azimi, Using Porous Material for Heat Transfer Enhancement in Heat Exchangers.Journal of Engineering Science and Technology Review 6 (1) (2013) 14-16. [15]. He, Z., Fang, X., Zhang, Z., Gao, X.: Numerical investigation on performance comparison of non-Newtonian fluid flow in vertical heat exchangers combined helical bafe with elliptic and circular tubes. Appl. Therm. Eng. 100, 8497 (2016). [16]. S.U.S. Choi, Enhancing thermal conductivity of fluids with nanoparticles, ASME FED 231 (1995) 99. [17]. Y. Yang, Z.G. Zhang, E.A. Grulke, W.B. Anderson, G. Wu, Heat transfer properties of nanoparticles in-fluid dispersions (nanofluids) in laminar flow, International Journal of Heat and Mass Transfer 48 (6) (2005) 1107. [18]. N.Jamshidi, M.Farhadi,D.D, Ganji, K. Sedighi, Experiment analysis of heat transfer enhancement in shell and helical tube heat exchange, AppliedThermal Engineering 51(2013) 644-652.
[19]. S.Rozzi, R. Massini, G Paciello, G.Pagliarini, S Rainieri, A. Trifiro, Heat treatment of fluid food in shell and tube heat exchanger: comparison between smooth and helically corrugated wall tubes, Journal of Food Engineering 79(2007) 249-254. [20]. R.Hosseini, A Hosseini-Ghaffar, M Soltani, Experimental determination of shell side heat transfer coefficient and pressure drop for an oil cooler shell and tube heat exchanger with three different tube bundles, Applied Thermal Engineering 27 (2007) 1001-1008.Elsevier. [21]. Vindhya, Raj, Piyush, A.K.Srivastava, Performance analysis of shell and tube type heat exchanger under the effect of varid operating condition, IOSR Journal of Mechanical and Civil Engineering Volume 11, Issue 3 Ver.VI (May-June. 2014) PP 08-17. [22]. M. Esapour, M.J. Hosseini b, A.A. Ranjbar, Y. Pahamli, R. Bahrampoury, Phase change in multi-tube heat exchangers, Renewable Energy 85 (2016) 1017-1025. [23]. A.H. Mosaffa, F. Talati, H. Basirat Tabrizi, M.A. Rosen,Analytical modeling of PCM solidification in a shell and tube finned thermal storage for air conditioning systems, Energy and Buildings 49 (2012) 356361. [24]. Abduljalil A. Al-Abidi, Sohif Mat, K. Sopian, M.Y. Sulaiman, Abdulrahman, Th Mohammad, Numerical study of PCM solidification in a triplex tube heat exchanger with internal and external fins, International Journal of Heat and Mass Transfer 61 (2013) 684695. [25]. Bin Gao, Qincheng Bi, Zesen Nie, Jiangbo Wu, Experimental study of effect of baffle helix angle on shell side performance of shell and tube heat exchanger with discontinue helical baffle. Experimental Thermal and Fluid Science 68(2015) 48-57 Elsevier. [26]. Wen Tao,Jian-Fei Zhang, Bin Li, Wen Jiang Huang, Yong Gang, Experimental performance comparison of heat exchanger with middle overlapped helical baffle, Chemical Engineering Science 64(2009) 1643- 1653. [27]. Luhong Zhang, Youmei Xia, Bin Jiang, Xiaoming Xiao, Xiaoling Yang, Pilot experimental study on shell and tube heat exchanger with small angle helical baffle, Chemical Engineering and Processing 69(2013) 112- 118.Elsevier. [28]. Vukic MV, Tomic MA, Zivkovic PM, Gradimir S. Effect of segmental baffles onthe shell-and-tube heat exchanger effectiveness. Hem Ind 2014;68(2):171e7. [29]. Bell KJ. Heat exchanger design for the process industries. ASME J Heat
Transf 2004; 126:877e85.
[30]. Raj RT, Ganne S. Shell side numerical analysis of a shell and tube heat exchanger considering the effect of baffle inclination angle on a fluid flow. Therm Sci Therm Sci 2012;16(4):1165e74. [31]. Mustapha Mellal, Redouane Benzeguir, Djamel Sahel, Houari Ameur, Hydro-thermal shell-side performance evaluation of a shell and tube heat exchanger under different baffle arrangement and orientation, International Journal of Thermal Sciences 121 (2017) 138-149. [32]. Younes Menni, Ahmed Azzi & Ali Chamkha, Enhancement of convective heat transfer in smooth air channels with wall-mounted obstacles in the flow path, Journal of Thermal Analysis and Calorimetry volume 135, pages 19511976 (2019). [33]. Raheem Kadhim, Ajeel, K.Sopian, Rozli Zulkifli, Thermal-hydraulic performance and design parameters in a curved-corrugated channel with L- shaped baffles and nanofluid, Journal of Energy Storage, Volume 34, February 2021, 101996.IJERTV13IS060046
(This work is licensed under a Creative Commons Attribution 4.0 International License.)