
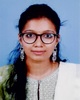
- Open Access
- Authors : Aswathi Raj , Narayanan N. I
- Paper ID : IJERTV11IS070138
- Volume & Issue : Volume 11, Issue 07 (July 2022)
- Published (First Online): 28-07-2022
- ISSN (Online) : 2278-0181
- Publisher Name : IJERT
- License:
This work is licensed under a Creative Commons Attribution 4.0 International License
Numerical Study On The Seismic Behavior of Wide Flange Column with Bolted Base Connection
Aswathi Raj
Dept. of Civil Engineering Govt. College of Engineering, Kannur
Kannur, India
Prof. Narayanan N. I
Dept. of Civil Engineering Govt. College of Engineering, Kannur
Kannur, India
AbstractThe primary force transmission components of the base connection are a pair of steel angles and a shear plate that connect the wide-flange column to the foundation. In the overall construction, the connections at the base of the columns are the most crucial. The foundation is responsible for conveying flexure, shear, and axial forces from the entire building. Mainly there are two types of base plate connections: welded base plate connections and bolted base plate connections. To overcome the limits of welded base plate connections the study focuses on bolted base connection for wide flange columns. Wide flange column fixed to bearing plate were subjected to cyclic lateral load along with axial compression and the inelastic behavior were investigated. This study is to analyses the reaction of bolted base connections on broad flange columns using ANSYS software. Study concentrates mainly on four sets of parameters. The behavior of wide flange column with the bolted base plate connection with varying angle plate thickness, effect of geometry of column segment, diameter of bolt diameter and introduction of stiffeners into wide flange column arrangement
Keywords Wide-flange column, column base connection, bolted base connection, cyclic loading
-
INTRODUCTION
In steel building frames, wide-flange elements are typically utilised as columns. Wide flange has H shaped cross section with wider flanges. A wide-flange section has a nearly square cross section and is ideal for constructing columns. To transfer column weights to the foundation generated by gravity, earthquakes, or wind, base connections are necessary at the bottom ends of wide-flange columns. There has been very little research into improving the structural performance and constructability of column base connections. The lower end of a wide-flange column is welded to a levelled and connected to the foundation steel plate in the base plate connection. The bolted base connection eliminates the negative impacts of field welding, provides a clear path for load transfer, and is simple to fabricate and erect. In the bolted base connection, the wide- flange column is connected to the foundation by a shear plate and two steel angles [1].
In the test arrangement [1], a bolted base connection connects a column segment to a steel footing. The upper end of the column segment is limited to show the point of inflection. The steel footing is firmly attached to the ground. To apply lateral force, a horizontal actuator is coupled to the reaction wall, while a vertical actuator is attached to the reaction frame to apply axial compression. A set of rollers was inserted between the vertical actuator and the response frame to allow sway under combined stress, and a hinge was installed between
the vertical actuator and the column portion. When connections were subjected to simultaneous column axial compression and strong axis bending, the inelastic behavior of the connections was examined. The axial compression of the column and the technique utilized to construct the angles used in the bolted base connection were among the test criteria that differed between the six experimental specimens. This study developed a simplified analytical model to analyze the backbone response of the bolted base connection's flexural strength in addition to the experimental work. Using the projected backbone response, a system with a bolted base connection can be evaluated for lateral load resistance and demand on the system's self- centering mechanisms to reduce residual deformations and offer a suitable post-event repair condition.
Under axial compression and weak-axis lateral force, the responses of a new type of bolted base connection supporting a wide-flange column are studied [2]. In this instance, three specimens were tested. Aside from the experimental investigation, this study developed a simple model for evaluating the backbone response of the weak-axis lateral strength of the bolted base connection using the plastic analysis approach and yield line theory. Cold folded and welded angles can be used in the bolted base connection under combined loads as surrogates for hot rolled angles, according to the testing. It may be possible to repair the secured base connection by replacing the broken angles with new ones if the bolted base connection can be re-centred.
Under axial load and lateral drift conditions, an experimental examination of the pre- and post-buckling behaviour of 12 steel wide-flange cantilever columns. The performance of these columns is influenced by a variety of loading and geometric criteria, including cross-sectional local web and flange slenderness ratios, applied axial load, and lateral and axial loading histories. This paper presents the main findings of an experimental programme that investigated the behaviour of wide-flange steel columns with high constant and changing axial load demands under monotonic and reversed cyclic lateral loading. Due to the stability of the created cross- sectional local buckling length under monotonic lateral drift, steel columns subjected to light axial load demands attain residual flexural strength, according to the test results [3].
The results of parametric finite-element (FE) simulations of over 50 wide-flange steel columns subjected to cyclic stresses are presented in this paper. Adjustments to the applied axial load ratio and the employed lateral loading history were used in FE simulations to analyse and refine a variety of seismic design criteria for steel moment-resisting-frame columns. A thorough
FE modelling approach is offered to mimic the hysteretic behaviour of wide-flange steel columns subjected to multi-axis cyclic loads. This is accomplished using the commercial software ABAQUS-FEA/CAE. To examine the seismic performance of steel MRF columns and to improve current seismic design provisions in North America, comprehensive parametric FE simulations are carried out. This is accomplished by the application of a high-fidelity finite element modelling approach that has been proven through existing testing on multiaxis cyclic stresses on steel columns [4]. This study investigates the hysteretic response of embedded column base (ECB) connections, which are commonly used to connect Steel Moment Frame columns to concrete footings. ECB connections are commonly utilised to connect steel columns to concrete footings in mid- and high-rise steel moment frames [5].
-
NUMERICAL MODELLING
-
Finite element model
Finite element model is developed and is validated against the experimental study conducted by Hetao et.al (2021). Modelling is done using ANSYS 2022 R2. Figure 4.2 the finite element model developed using ANSYS. Wide flange columns, pair of angle section and shear plate with bolt holes along with bolts are modelled separately and then suitable connections are provided between the components. Schematic diagram of the model developed is shown in Fig1. The dimensions of the material modelled for the numerical study is as shown in table 1
TABLE 1 GEOMETRY OF MODEL
Width of flange, b
200 mm
Web depth, d
200 mm
Thickness of flange, tf
12 mm
Thickness of eb, tw
8 mm
Short leg length
110 mm
Long leg length
180 mm
Thickness of angle plate
10 mm
Length of column segment
1500 mm
-
Geometrical Modelling
The model of column was developed as per Hetao et.al (2021) using ANSYS software. Solid and beam element was used to model the section. The Fig. 2 shows the finite element model of the specimen considered. Adaptive mesh sizing was used.
-
Material modellig
According to Chinese National Standards GB/T 228.1- 2010, genuine material properties of the column segment, angles and shear plate were measured using monotonic tensile test of the coupons selected and processed. TABLE 2 summarises the measured yield strength (Fy), measured ultimate strength (Fu) and permanent elongation of the material used in various components.
Components
thickness
Fy (MPa
Fu (MPa)
Column flange
12
404.9
596.5
Column web
8
440.3
603.4
Hot rolled angles
10
314.2
482.7
Cold folded
/welded angles
10
348.8
483.3
Shear plate
12
421.5
546.3
TABLE 2 MATERIAL PROPERTIES
Fig 1 Schematic diagram of model
-
Boundary conditions and loading
The top end of the column is restrained to represent point of inflection and bottom end fully fixed. First axial compression is provided at the top end of the column segment followed by concurrently applying the lateral displacement which causes the strong axis bending. Displacement controlled loading schemes are adopted here. Fig 2 indicates the loading and boundary conditions. When the column is exposed to axial compression alone, the angles and the shear plate are not severely stressed since the connecting components are suitably sized and detailed. Loading protocol is shown in Fig 3
Fig 2 Loading and boundary condition
Fig 5 Load vs Deformation curve of hot rolled specimen
-
Validation
Fig3 Loading protocol
The specimen was modelled in Design Modeller and then exported to Mechanical for boundary conditions and loading. Displacement controlled loading is provided. Friction type connection is used here with a coefficient of 0.2. the deformation contour of the wide flange column is shown in Fig
-
The reliability of finite element model was evaluated by comparing the failure modes and lateral force (N) versus deformation curve of the hot rolled specimen against the experimental curve from Hetao et.al (2021) as shown in Fig
-
The load carrying capacity of the hot rolled specimen is compared with experimental one and an error of 3.87% was observed. The behavior of cold rolled specimen was also analyzed and is shown in Fig 6. The comparison of load carrying capacity of the specimen is done with the experimental one and an error of 8.49% is observed.
Fig 4 Deformation contour
Fig 6 Load vs Deformation curve of cold rolled specimen
-
-
Parametric study
Parametric study was conducted on four areas such as thickness of angle plate, length of column segment, diameter of bolt and effect of stiffeners on the base plate. The comparison of the result is done in terms of load carrying capacity and energy dissipation capacity. Initially numerical model was validated against experimental model and then parametric study were carried out.
-
Effect of thickness of angle plate
The behaviour of wide flange column with bolted base connection is studied by varying the thickness of angle plate at the same time all other parameters is kept constant. The thickness of angle plate was varied from 5mm to 20mm and load vs displacement relation was studied and shown in Fig.6. The observed structural phenomenon is shown in the following sections.
The figure shows the comparison of backbone response curve of validated model, T-5, T-15 and T-20 models. There is an increase in loop area corresponding to the increase in displacement. The average peak load of T 5 is 70.319 kN and average peak load of T 20 is 118.94 Kn which indicate that load carrying capacity increased 69.14%. The test result suggests that as the thickness of angle plate is increased there is a higher percentage increase in capacity.
Fig 6 Backbone curve for different thickness of angle plate
Stiffness degradation is estimated as the slope of line joining positive and negative peak load for each hysteresis loop. Degradation of the stiffness was found to increase as the displacement increases and is depicted in Fig 7.
Fig 7 Stiffness degradation
Energy dissipation capacity of the specimens is found out by calculating the cumulative area of each loop of load versus displacement hysteresis curve. The comparison of energy dissipation of various specimens is done and is depicted in Fig 8. From the figure it is clear that as the thickness of angle plate is increased the energy dissipation continues to increase. The cumulative energy dissipation capacity of T 20 is 3.90 times the capacity of T 5. When the thickness of plate changes from 5mm to 10mm the energy dissipated is increased by 62.64% and thickness changes from 15mm to 20mm energy dissipated is only increased by 35.77%
Figure 8 Energy dissipation curve
-
Effect of length of column segment
The effect of length of column segment on the behaviour of wide flange column with bolted connection is studied. Column length is varied from 1500mm to 2100mm and the corresponding load versus displacement envelope curve is plotted.
Figure9 Backbone response curve for change in length of column segment
The comparison of backbone response curve of each specimen is carried out and shown in Fig 9. The average peak load of L 1500 was 50.06 kN and that of L 2100 is 24.01 kN which indicate that there is an decrease of load carrying capacity by 70.32%. it was found that the effect of length of column segment is inversely related to the load carrying capacity
Figure 10 stiffness degradation
Degradation of stiffness occurs as the displacement increases. The stiffness degradation of all the specimen were calculated and plotted in Fig
10. From the graph it is observed that as the length of the specimen was increased stiffness degradation was decreased which implies that the column base connection became less stiff when length of column segment was increased.
-
Effect of bolt diameter
For efficient bolted connection diameter and strength of the bolts are to be ensured. Hence here the diameter of bolt was varied and the behavior of wide flange column was studied by keeping all other parameters constant. The bolt diameter of specimens studied were varied from 20mm to 24mm. Three
specimens were used to study this parameter. The specimens chosen to study the load displacement relationship opted bolt diameters 20mm, 22mm and 24 mm. the bolt diameters are chosen such that they are available in the market as per requirements. It was observed that the load carrying capacity was increased as the diameter of bolts is increased. The results are shown in Fig 11 below
Fig 11 Backbone response curve for various bolt diameters
As the bolt diameter is increased from 20mm to 24mm the average load carrying capacity is increased by 7.16% and when the bolt diameter is increased from 22mm to 24mm the average load carrying capacity is found to increase by 8.31%
-
Effect of stiffeners
Stiffeners enable the introduction of different load paths and the support of highly directed loads, which may provide protection from damage and the emergence of cracks under compressive and tensile stresses. Base plate stiffeners are introduced into the arrangement of wide flange column with bolted connections as shown in Fig 12
Deformation behaviour of the column is studied. The load versus displacement relationships of the specimen is investigated as shown in figure 5.7. the behaviour of specimens with stiffeners is compared with the specimens without stiffeners. It is depicted in Fig 13.
Fig 12 base plate stiffeners in wide flange column
Fig 13 comparison of backbone response curve of specimen with and without stiffeners
The specimens considered here were T5-S10, T5, T10-S10 and T10. T5-S10 represents specimen with thickness of angle plate 5mm provided with stiffeners of 10 mm thickness. T10-S10 represents specimen with thickness of angle plate 10 mm provided with 10mm thick stiffeners. From the graph it is clear that as the rotation increases there is a corresponding increase in loop area.
The load carrying capacity increased by 11.38 % in case of specimen with 5mm thick angle plate and 10mm thick stiffeners, whereas the specimen with 10mm thick angle plate and 10mm thick stiffener offered an increase in ultimate load carrying capacity of 18.38 percent.
-
-
CONCLUDING REMARKS
-
The load carrying capacity was increased by 69.14 % as the thickness of angle plate was increased from 5 mm to 20 mm. this indicate that thickness of angle plate has a significant role on the load carrying capacity.
-
The cumulative energy dissipated is also affected by thickness of angle plate. Energy dissipated is increased by 62.64% when thickness increased from 5 mm to 10 mm and 35.77% when thickness varied from15 mm to 20 mm.
-
As length of the column segment was increased it was found that the load carrying capacity decreased. When length was increased from 1500mm to 1900 mm, load carrying capacity was increased by 23.07
%.
-
When diameter of bolts was increased from 20 mm to 24 mm the capacity was increased by 15.47%.
-
Introduction of stiffeners also has a critical role in the load carrying capacity. The comparison of specimen with stiffener and without stiffener was also carried out.
-
There are future analytical or experimental research opportunities on studies on techniques that can be used in improving the strength of angle plate where failure is occurred. Also the effect of no of bolts and bolt diameters can be studied in detail.
-
-
REFERENCES
112024. https://doi.org/10.1016/j.engstruct.2021.112024
[4] Elkady, Ahmed, and Dimitrios G. Lignos. "Improved seismic design and nonlinear modeling recommendations for wide-flange steel columns." Journal of Structural Engineering 144.9 (2018): 04018162. https://doi.org/10.1061/%28ASCE%29ST.1943-541X.0002166
[5] Qiu, Canxing, et al. "Seismic performance of concentrically braced frames with non-buckling braces: a comparative study." Engineering Structures 154 (2018): 93-102.https://doi.org/10.1016/j.engstruct.2017.10.075
[6] Zareie, Shahin, et al. "A novel shape memory alloy-based element for structural stability control in offshore structures under cyclic loading." Ships and Offshore Structures 15.8 (2020): 844-851. https://doi.org/10.1080/17445302.2019.1688920 [7] Bhowmik, T., K. H. Tan, and T. Balendra. "Lateral load- displacement response of low strength CFRP-confined capsule- shaped columns." Engineering Structures 150 (2017): 64-75. https://doi.org/10.1016/j.engstruct.2017.07.037 [8] Shirmohammadi, Fatemeh, and Asad Esmaeily. "Performance of reinforced concrete columns under bi-axial lateral force/displacement and axial load." Engineering structures 99 (2015): 63-77. https://doi.org/10.1016/j.engstruct.2015.04.042 [9] Cravero, Julien, Ahmed Elkady, and Dimitrios G. Lignos. "Experimental evaluation and numerical modeling of wide-flange steel columns subjected to constant and variable axial load coupled with lateral drift demands." Journal of Structural Engineering146.3 (2020): 04019222. https://doi.org/10.1061/(ASCE)ST.1943-
541X.0002499
[10] Elkady, Ahmed, and Dimitrios G. Lignos. "Improved seismic design and nonlinear modeling recommendations for wide-flange steel columns." Journal of Structural Engineering 144.9 (2018): 04018162. https://doi.org/10.1061/(ASCE)ST.1943-541X.0002166
[11] Inamasu, Hiroyuki, Amit M. Kanvinde, and Dimitrios G. Lignos. "Seismic stability of wide-flange steel columns interacting with embedded column base connections." Journal of Structural Engineering 145.12 (2019): 04019151. https://doi.org/10.1061/(ASCE)ST.1943-541X.0002410 [12] Newell, James D., and Chia-Ming Uang. "Cyclic behavior of steel wide-flange columns subjected to large drift." Journal of structural engineering 134.8 (2008): 1334-1342.https://doi.org/10.1061/(ASCE)0733-9445(2008)134:8(1334)
[13] Stoakes, Christopher D., and Larry A. Fahnestock. "Strong-axis stability of wide flange steel columns in the presence of weak-axis flexure." Journal of Structural Engineering 142.5 (2016): 04016004. https://doi.org/10.1061/(ASCE)ST.1943-541X.0001448
[14] Anand, Subhash C., Julian Snyder, and Chaman L. Dhar. "Buckling of Wide Flange Columns about Minor Axis." Journal of the Structural Division 99.1 (1973): 145-165.https://doi.org/10.1061/JSDEAG.0003418