
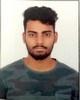
- Open Access
- Authors : Souri V S Sreeramagiri , T. Bhavani
- Paper ID : IJERTV10IS010142
- Volume & Issue : Volume 10, Issue 01 (January 2021)
- Published (First Online): 26-01-2021
- ISSN (Online) : 2278-0181
- Publisher Name : IJERT
- License:
This work is licensed under a Creative Commons Attribution 4.0 International License
NVH And Structural Adaptations in Automobiles: A Perspective
Souri V S Sreeramagiri
Final year,
-
Tech Mechanical Engineering, National Institute of Technology Karnataka,
-
Bhavani
IP Consultant, Lifeintelect Consultancy Pvt.Ltd,
Abstract:- This article gives an outlook on noise, vibration and harshness (harmonics) in automobiles, their influences on energy conservation, configuration of various components and the structural features that can minimize the adverse effects. Noise and vibration are unwanted phenomena in most systems and result in a loss of energy, and reduction in the fatigue life of the body. When it comes to automobiles, noise is highly unwanted as it also has a negative effect on the ambience and user experience. Vibration can also lead to friction and erosion on the surface of parts in contact. Thus, companies invest heavily in mitigating these NVH effects. The structural changes, assessment methods and the upcoming trends related to NVH research and its overall contribution to improving the efficiency and comfort of automobiles have been highlighted in this article following a thorough literature review.
Key words: Noise-vibration-harmonics; structural adaptations; MATLAB; FEA; structural acoustics; automobile.
-
INTRODUCTION
The study of the noise and vibration characteristics plays a crucial role in automotive engineering, optimization, and the structural arrangement of various components of automobiles while ensuring comfort and efficiency. The behavior of vibrations is heavily influenced by the structures through which they travel and their material characteristics. Vibration or motion of tangible structural components results in energy losses in the form of noise and friction. This energy loss leads to reduction in the overall efficiency of the system. Besides, the generated noise significantly affects the vehicle ambience and passenger comfort.
Acoustic induced vibration (AIV) is another source of disturbance mainly in systems involving vapor pressure flow. AIV is a structural vibration arising in a piping system when vapor flow is excited due to acoustic pressure. AIV is most commonly observed at junctions with sudden pressure drop like bypass or control valves. AIV control is very important since the demand for higher flow rates of automobiles is increasing day by day.
The various sources for vibrations and the mode of energy dissipation do always draw our attention in automotive research especially in ergonomics. The pressing need for improved fuel economy and sustainable development, force us to resolve the issues associated with NVH through structural modifications. These changes will give us a chance to control the acoustic properties of the system, which forms the essence of the present article. A brief introduction to NVH terminology, methods involved in the evaluation of NVH and its relation with various structural components, management of NVH through structural modifications, and the upcoming trends along with future role of structural adaptations with respect to NVH in automobiles are presented in this article.
-
Buzz, Squeak and Rattle (BSR)
The sound waves emanating from the vibrating structure alone results in buzz. Squeak is the noise originating from frictional movement between two parts. Squeak arises due to the elastic deformation of the contact surfaces storing energy, which is released as sound. Finally, rattle is the noise due to lose or very flexible elements under forced excitation. The BSR noise arises as a result of the relative motion of structural components exceeding a threshold value.
-
NVH -Evaluation
Typical instrumentation used to measure NVH includes microphones, accelerometers and force gauges, or load cells. NVH measuring facilities include semi-anechoic chambers, and rolling road dynamometers. In general, the signals are recorded direct to hard disk via an analog-to-digital converter. Harshness is a qualitative concept that is based on target characteristics rather than quantifiable variables. The dynamic systems are approximated to a point mass and spring model. Mathematical equations are derived for the given spring- mass ideal system and various parameters are calculated. The dynamic response and behavior ensure a considerably good match with the real system the model will be subjected to further evaluation and modification. Generation of the mathematical model for the system also takes in to account characteristics such as the stiffness coefficient and the damping factor. The two primary mathematical models implemented in such analysis are 1) Lumped parameter system, where the masses are represented at clusters at fixed points in space and 2) Distributed parameter model, where the mass is said to be distributed continuously throughout the system, represented by a function of space.
Many articles and reviews have come that threw light on various aspects of BSR, and NVH. A.R. Mohanty and Shahab Fatima
-
came out with an overview of automobile noise and vibration control. They reviewed the current state-of-the-art techniques in automobile noise and vibration control. They stressed on the fact that designers can take advantage of efficient numerical
modeling techniques and computer aided models to optimize the design to achieve low noise and vibration levels at the prototype level itself.
Mohammad Al zubi [2] has covered six groups of vibro-acoustic containment materials that are currently or potentially being used in the automotive area, in his Dissertation. These included fabrics, foam, honeycomb, monolithic &sandwich, periodic cellular material structures (PCMS) and general periodic groups. The author concluded that more rigid materials, such as cold rolled steel and block aluminum, stiff framed structures, in combination with highly absorbent cores or layers tend to limit vibration, and should be considered for this purpose in automotives, where weight is not a limitation. He also found that good potential exists for PCMS since they offer effective vibration control.
Shin, S-H and Cheong, C. [3] carried out experiments on characterization of instrument panel buzz, squeak and rattle in a vehicle. Wang binxing, and Zheng sifa et al [4] carried out acoustic modelling and analysis of vehicle interior noise, based on numerical calculations.
Stephen Hambric [5] has discussed in detail the approach to vibration analysis which threw light on developing mathematical model of the system by formulating the equations of motion, analyzing the natural frequencies and modes, analyzing the forced vibration response to prescribed disturbances, and investigating methods for controlling undesirable vibration levels. His models were based on distributed-parameter approach or Lumped-parameter approach and stressed on the fact to have just sufficient elements for natural vibration modes and frequencies in order to obtain a conclusive data.
Maressal. A, Pluymers. B et al [6] studied NVH optimization methodologies based on bead modification analysis in vehicle body design, which clearly indicated that NVH optimization can take place on the basis of virtual modeling and simulation which reduced cost and time-taken drastically. The main innovation introduced in this paper consisted of usage of structural optimization software in combination with an acoustic target function to optimize vehicle vibro-acoustics. The optimized components were evaluated in terms of radiated sound pressure level and manufacturability.
Though the articles threw light on the existing state of art, in vie of the changing environmental concerns, customers satisfaction, and safety concerns, there is a gap that has to be filled in by bringing out the essence of works concerned with effective management of NVH. Keeping in mind these aspects the present work is taken up which lays emphasis on the assessment methods of NVH, structural adaptations in relation to NVH in the field of automobiles and the emerging trends in automobiles with respect to NVH.
-
-
ESSENTIAL ELEMENTS OF THE ARTICLE
-
-
-
NVH and MATLAB
-
NVH and Finite Element Analysis (FEA)
-
Product Specific Structural Adaptations and NVH
-
Emerging Structural adaptations and NVH
-
NVH and MATLAB
MATLAB is a mathematical tool that helps us model complex dynamic systems to obtain simplified state equations that can be solved with the help of governing partial equations. This will give us an idea to reduce the cost of experimental verifications. MATLAB quickly assess the integrity of the components thereby increase the efficiency of the process. For example, Simulink is one such tool that allows graphical modeling and has an extensive library of various dynamic systems. MATLAB plays a significant role in developing suitable strategies with regard to NVH control.
Mélissa Férand , and Thomas Livebardon et al [7] carried out studies on a hybrid methodology, combining a detailed Large- Eddy- Simulation of a combustion chamber sector. They have arrived at an analytical propagation model of the extracted acoustic and entropy waves at the combustor exit through the turbine stages, and a far-field acoustic propagation, through variable exhaust temperatures. K. Khan, M. A. Akbar, and H. Koppelaar[8] studied coupled nonlinear partial differential equations for finding exact analytical solutions. A. Y. T. Leung, H. X. Yang, and Z. J. Guo,[9] came out with Periodic wave solutions of coupled integrable dispersion-less equations by residue harmonic balance. Y. Y. Lee, J. L. Huang, C. K. Hui, and C.
F. Ng [10] have obtained mathematical solution for sound absorption of a quadratic and cubic nonlinearly vibrating curved panel absorber. M. K. Lee, M. Hosseini Fouladi, and S. Narayana Namasivayam [11] have found out natural frequencies of thin rectangular plates using homotopy-perturbation method.
J. Le Besnerais[12] came out with a new multiphysics- model, and simulation environment for the fast calculation ,and analysis of acoustic noise and vibration levels due to Maxwell forces, in variable-speed rotating electrical machines. He analyzed numerical methods for predicting electromagnetic noise and compared them to analytical and semi- analytical techniques. He also presented the new coupling of electrical, electromagnetic and vibro-acoustic models. The model is validated using surface permanent magnet (SPMSM), interior permanent magnet (IPMSM) and squirrel cage induction machines (SCIM). The resonance and noise levels are estimated using MANATEE® simulation software
Similarly, studies were carried out and conclusions were drawn by using numerical simulations of electromagnetic and structural models [13], numerical solutions and rotor dynamic eccentricity effects, on synchronous machine vibrations for full run up [14]. F. Marion [15] and, K. Vansant,[16] studied magneto-vibroacoustics in relation to linking flux. Le Besnerais [17]
worked on Vibroacoustic Analysis of Radial and Tangential Air Gap Magnetic Forces in Permanent Magnet Synchronous Machines.
Sujit Kumar Jha and Ajay Sharma [18] studied the resonance effect of exhaust gases coming out of a muffler consisting of fibrous and porous materials to absorb noise and vibrations. The exhaust gas from the engine caused fatigue-failure in the exhaust pipe, due to continuous resonance. The modes on the muffler had to be separated away from the engines operating frequencies so as to minimize resonance. They conducted an impact test using a hard head hammer, and transfer functions were obtained using MATLAB. Results showed that an increase in the mass increased the damping and lowered the modes of the transfer function that influenced NVH.
-
Finite element Analysis (FEA) and NVH
Equations governing dynamic systems are often complex partial differential equations. In finite element analysis, a large system is broken down into smaller components through a process known as mesh or grid generation. The system of differential equations can then be safely approximated to simple algebraic equations. These equations are evaluated for every element and later summed up to compute the result for the overall system.FEA effectively simplifies the analysis of NVH systems and greatly reduces computational load and makes it feasible to account for minute aspects that can influence NVH. Jose Salvado, and Maria do Rosáriocalado et al [19] worked out on the problem of vibrations produced by switched reluctance actuators, focusing on the linear configuration of machines, aiming at its characterization, regarding the structural vibrations. They developed a 3D model of the actuator and used finite element method (FEM) to find its natural frequencies. Spectral analysis results of audio signals from experimental modal excitation were also established. The obtained data supported the characterization of the linear actuator based on the excited modes, vibration frequencies, and mode shapes. The study revealed that, identification of the most critical modes was of great significance for the actuators control strategies.
N. C. Lenin and R. Arumugam [20] studied acoustic noise, vibration, harmonics, and thermal variations of three-phase linear- switched- reluctance- machines (LSRM). Structural finite element analysis was used to compute the natural modes and frequencies. Harmonic analysis was done to identify the range of speeds producing high vibration and noise that should be skipped-over quickly during acceleration. Electromagnetic and thermal analysis of the LSRM was also carried out by FEA. They found that acoustic noise in the LSRM is caused primarily by the deformation of the stator-lamination-stack. Acoustic noise was severe during the periodic excitation of the LSRM phases, in natural vibration mode of the stack.
M. L. Chandravanshi, and A. K. Mukhopadhyay[21] performed FEM and EMA analysis of variations in vibration behavior of a vibratory feeder due to change in stiffness of helical springs. The reduced pitch in coils of helical springs changed the dynamic behavior of the vibratory feeder unit resulting in loss of performance. The continuous reversal stress acted as a catalyst resulting in permanent deformations in pitch of coils of the helical springs due to creep-phenomenon. A three-dimensional model based on solid-works was developed using FEM technique in ANSYS workbench. L.Y.Yao, and D.J.Yu, et al [22] carried out Numerical treatment of acoustic problems with the smoothed finite element method.
P. Forte, F. Frendo, and Rodrigues [23] conducted finite element parametric study of the influence of friction pad material and morphological characteristics on disc-brake vibration phenomena. They found that in general creep- groan and squeal that resulted in annoying vibrations, and noise of specific frequency ranges were like self-excited brake vibrations, caused by the stick-slip effect. It was found that the friction coefficient was dependent on the morphology of the mating surfaces, and on the operating conditions along with many other factors. Finite element complex- eigen-value parametric analyses were performed on a disc-brake assembly to evaluate dynamic instability of brakes with respect to multiple pads, number of pads, pad shape and size, and material parameters.
Chandrasekhar N. and Tang. C. et al. [24] carried out studies on the impact of current harmonics on the 6th and 12th electrical orders of the torque ripple, and relevant e-Machine-whine- noise, employing statistical correlation and regression analysis, based on te data-sets acquired from dynamometer testing, and finite element-based CAE calculations. The important e- Machine metrics included torque, ripple and radial electro-magnetic forces. These disturbances could radiate directly from the e-Machine-housing, and also could be transmitted through the structural attachments like stator bolts, stator ring, power-train mounts etc. They found that current harmonics impacted Torque ripple, which in turn translated into undesirable noise and vibration.
Ashok K Bagha, and Subodh V Modak [25] proposed a method for active noise control in the framework of active structural- acoustic control, incorporating system identification, for the development of the linear quadratic Gaussian controller. System identification was carried out using modal testing and finite element model, updating to obtain an accurate model of the plant for building up the Kalman filter. The objective of the proposed method was to actively reduce the noise inside the cavity due to disturbances acting on the cavity structure. The active control is achieved by controlling the structural vibrations, by taking into account the degree of coupling between the various structural and the acoustic modes. The effectiveness of the proposed method is evaluated experimentally on a 3D rectangular box cavity with a flexible plate.
-
Product specific structural adaptations and NVH
Quite often the requirement of the end-user, accessories, mode of transport, and nature of the fuel decide structural features of the finished product. The requirements can be need based, aesthetic or economy-driven and of late, environmental concerns have been dominating the automobile sector. In this regard many changes are being brought into the overall structural features and assembly of the motor vehicles. The added changes should be eco-friendly and at the same time should not disturb the
configuration of the vehicle in any way. Keeping this in mind in the last decade several studies and enough experimentation have been taken up to minimize energy losses, and subsequent pollution (both sound and air pollution) while ensuring safety of the vehicle, by suitably addressing the NVH problems. Even big companies like Toyota, Ford had to withdraw or recall their vehicles due to non-conformance to the latest emission standards. The following references throw light on the aspects wherein the NVH problems are resolved through product specific structural modifications.
ERIC TINGWALL [26] in his presentation talked about how Toyota V-6 and Porsche Flat-six produce differing sounds. Fire Joe Serrano, and Geoff Routledge et al [27] carried out experiments on methods of evaluating and mitigating NVH while operating the engine in Dynamic-Skip- Fire- mode. According to them cylinder deactivation technology is very essential in automotive industry in view of the demands of fuel economy and emission standards. GM's Active- Fuel-Management and Chrysler's Multi-Displacement- System, are cited as good examples of one fixed level of deactivation. The authors came out with Dynamic-Skip-Fire (DSF) as a better option in which the number of fired cylinders is continuously varied to match the torque demand which offered significant fuel savings over a wider operating range than the existing systems. They were also of the opinion that maintaining acceptable levels of NVH was challenging during the implementation of cylinder deactivation. This work covered the root causes and developed standards to quantify the NVH levels.
According to Anuj Rekhy, Robert Snyder and James M. Manimala [28] conventional acoustic absorbers like foams, fiberglass or liners that are normally employed in structures for industrial, infrastructural, automotive and aerospace applications to mitigate noise have limited effectiveness for low-frequencies (LF, <~500 Hz). This is mainly because such NVH arresters are needed in very large quantities to become effective in achieving the target.
Haosen Yang, Huirong Li, and HuiZheng [29] carried out optimization study of sandwich plates with corrugated cores for minimizing the transmitted sound power. A two-dimensional plate model is developed based on the spectral-element-method (SEM) for the calculation of the frequency-domain-vibration-response of the whole sandwich structure subject to airborne excitation, and the Rayleigh-integral-formula was used to calculate the transmitted sound power via its structure-born path. A genetic algorithm-based multi-parameter optimization method is employed to search for the optimal structural parameters with the objective to minimize the sound power transmitted.
A.BerryJ.Nicolas [30] felt that amongst the many mechanical parameters that influence structure-borne sound, the effects of stiffeners, added mass and complex support conditions along the structure boundaries had a greater impact on NVH suppression. He studied these effects incorporated into a model of sound radiation in air from a complex, baffled, rectangular panel under harmonic point force.
Studies on structural aspects such as non-linear vibroacoustic coupling-systems[31], laminated plates with non-linear elastic restraints[32], non-linear vibration of functionally graded CNT-reinforced composite beams resting on non-linear elastic foundations in thermal environment[33],bifurcation phenomena in non-linear curved beam subjected to base harmonic excitation[34], prediction of breakout noise from a rectangular duct with compliant walls[35], breakout noise characteristics of flexible rectangular duct[36], Primary and secondary resonance analyses of clamped-clamped micro-beams[37], elliptical integral solution for the large amplitude free vibration of a rectangular single mode plate backed by a multi-acoustic mode cavity[38], Free vibration analysis of a nonlinear panel coupled with extended cavity using the multi-level residue harmonic balance method[39], Nonlinear vibro-acoustic analysis of composite sandwich plates with skin-core debondings[40], Nonlinear fluid-structure interaction of an elastic panel in an acoustically excited two-dimensional inviscid compressible fluid[41], Nonlinear vibration of viscoelastic sandwich beams by the harmonic balance and finite element methods[42] clearly emphasized the resonance phenomena and their influence on vibrations, noise characteristics, effect of the natural frequency of the materials employed in structural elements, influence of shapes, elasticity of the structural elements on overall quality of noise characteristics and give us an idea on how to control NVH in a better way keeping in mind the product specifications.
Yiu-Yin Lee [43] came out with work on the vibration and sound radiation of a nonlinear duct. He developed an analytic formula for computing the nonlinear structural and acoustic responses, based on a classic method combined with Vietas substitution technique. The development of the analytic formula is based on the classical nonlinear thin plate theory and the three-dimensional wave equation. He found that the damping ratio and excitation level are the two key factors to determine the nonlinearities of the resonant peaks of nonlinear panels. He found that the acoustic peak values in the sound power figures were generally higher than those in the vibration figures. This implied that the high-frequency components in the sound responses are more significant than those in the vibration responses because the sound radiation efficiency was higher when the response frequency was higher. The anti-symmetric modal responses, which have been considered in only a few structural acoustic studies, are found to be as important as the symmetric modal responses. His findings pointed to the fact that the jump phenomenon can be found in the peaks of the structural modes coupled with the acoustic modes as in the case of resonant peaks of nonlinear structural vibrations.
Similarly, Y. Y. Lee [44], Y. Y. Lee, and J. L. Huangetal [45], came out with analytical solutions for nonlinear multimode beam vibratio using a modified harmonic balance approach coupled with Vietas substitution, quadratic, and cubic nonlinearly vibrating curved panel absorber, respectively.
Nitin Sharma, Trupti Ranjan Mahapatra, Subrata, and Kumar Panda [46] presented vibro-acoustic modeling and analysis of, un- baffled laminated composite flat panels, subjected to harmonic point load under various support conditions. The frequency values of the panel are obtained by using simulation model through the commercial finite element package (ANSYS) by batch
input technique. The modal values are exported to LMS-Virtual-Lab environment for the computation of acoustic responses of the vibrating laminated plate structure. An indirect boundary element approach has been adopted to extract the coupled vibro- acoustic responses. A comprehensive study was carroed out to highlight the effect of different structural parameters, support conditions, and the composite properties, on the acoustic radiation responses of the laminated -plate -structure.
Mathieu Sarrazin, and Steven Gillijns et al [47] conducted Interior Acoustic Simulation for In-Car Audio Design Sound. They studied different noise and vibration measurements on a multi-phase switched reluctance (SR) motor for automotive applications on a test rig. It was found that the radial magnetic force between stator and rotor was the main excitation source creating large deformations of the stator housing, resulting in serious vibrations and acoustic noise. The dominant vibration modes were verified by modal analysis and operational deflection shapes. The relationship between the current profiles, radial magnetic forces, and mechanical and acoustic vibrations is investigated.
Yongliang Wang,and Xunpeng Qin et al [48] studied noise control of mini car body-in-white based on acoustic panel participation method ,to predict the acoustic radiation of vehicle body for the control of interior noise. After obtaining the kinetic equations of coupled acoustic-structural finite element method, the numerical analytical methods of noise transfer function, and acoustic panel participation were obtained. Then the coupled acoustic-structural finite element model of body in white (BiW) and passenger compartment cavity of a mini-car was established and verified by modal test. The acoustic panel participation analysis of vehicle roof and floor are conducted, and the key acoustic panels are identified. In order to reduce the noise of critical frequency, damping material is pasted and welding of beam is done. This article stressed on the fact that the structural improvement according to APP method controlled the interior noise effectively using less damping material.
Vinay V Nesaragi et al [49] worked on the Analysis and strategies utilized for NVH of bonnet which safeguards and houses important car-parts. The analysis and improvement of a vehicle body structure based on NVH behavior is investigated by fem or numerical method. The surface modeling is accomplished for the vehicle body in CATIA and meshed in HYPERMESH software. Then, modal analysis and harmonic analysis were done in a frequency range between 0-100 Hz on HYPERMESH. A frequency map of the vehicle body is extracted and compared with a reference map to identify the defects. Modal analysis of bonnet revealed that they are in target and results are obtained for different modes. Harmonic analysis was done with and without stiffener for automotive car bonnet. With stiffener, displacements were less and safe-design was obtained.
Dejan V. Matijevi [50] in his Overview of Modern Contributions in Vehicle Noise and Vibration Refinement with Special Emphasis on Diagnostics presented certain considerations related to noise, vibration and harshness issues on modern motor vehicles. The influence on human body is processed and certain noise and vibration analyzers are presented.
M. Al-Zubi et al. [51] presented the data related to vibration and noise amelioration in and across several components and modules of an automobile, such as the panels, doors, engine covers, seats and others. This study examined the vibro-acoustic characteristics of some monolithic and composite materials and some generally periodic material structures. By experimental and numerical/empirical methods, they explored the possible ways of minimizing the transmission of noise and vibration. Some new constructions not hitherto probed for vibro-acoustic fitness were examined.
-
Emerging structural adaptations and NVH
In the aftermath of Montreal summit and passing of resolutions regarding carbon foot print, emission reduction, use of green- fuels and lately, the conversion of fossil-fuel run vehicles to electrically powered pollution less vehicles, and arrival of GPS- driven-driver-less vehicles, the transport mechanisms and especially the automobile industry and in general transport sector is undergoing a complete revamp. Mag-lev trains, electric cars, solar-powered buses are a few to mention in this regard. Whatever may be the mode of transport and whichever vehicle is employed, ultimately NVH control will decide the structural adjustments and modification in the appeal of automobiles especially the cars. The following references lay emphasis on this aspect.
Andrew J. Hull, and Daniel Perez [52] derived an analytical model of a circular beam with a T-shaped cross section for use in the high-frequency range. The T-shaped cross section is composed of an outer web and an inner flange. The web in-plane motion is modeled with two-dimensional elasticity equations of motion, and the left portion and right portion of the flange are modeled separately with Timoshenko shell equations. The differential equations are solved with unknown wave propagation coefficients multiplied by Bessel and exponential spatial domain functions. These are inserted into constraint and equilibrium equations at the intersection of the web and flange and into boundary conditions at the edges of the system. Two separate cases of structural axisymmetric motion and structural non-axisymmetric motion are considered to obtain a wholesome solution. The wave propagation coefficients that give a corresponding solution to the displacement field in the radial and tangential directions are arrived at.
Chenhui Zhao and Marehalli G. Prasad [53] came out with acoustic black holes which have been effectively used for structural design in controlling vibration and noise. An acoustic black hole represents a power-law tapered profile. Mélissa Férand, and Thomas Livebardon et al [54] worked on a hybrid methodology combining a detailed large eddy simulation of a combustion chamber sector. The analytical propagation model of the extracted acoustic and entropy waves at the combustor exiting through the turbine stages, and a far-field acoustic propagation through a variable exhaust temperature are explored
Sabin Sathyan, Ugur Aydin and Anouar Belahcen [55] presented a numerical method and computational results for acoustic noise of electromagnetic origin generated by an induction motor. The computation of noise incorporated three levels of numerical calculation steps, combining both the finite element method and boundary element methods. The role of magnetic forces in the production of acoustic noise is established in the paper by showing the magneto-mechanical and vibro-acoustic pathway of energy. The magnetic forces were computed through 2D electromagnetic finite element simulation, and the
deformation of the stator due to these forces was calculated using 3D structural finite element simulation. Boundary element- based computation was employed to calculate the sound pressure and sound power level in decibels. The use of the boundary element method instead of the finite element method in acoustic computation reduced the computational cost. Unlike finite element analysis, the boundary element approach did not require heavy meshing to model the air surrounding the motor, according to Simon et al [56].
Yiu-Yin Lee [57] investigated the nonlinear sructure-extended cavity interaction simulation using a new version of the multilevel residue harmonic balance method. The effects of excitation magnitude, cavity depth, damping and number of structural modes on sound and vibration responses are investigated for various panel cases. He found that the nonlinearity of a structural acoustic system highly depends on the cavity size. He propounded that, the additional volume in an extended cavity affects the nonlinearity, sound and vibration responses of a structural acoustic system and if an acoustic resonance couples with a structural resonance, nonlinearity is amplified and thus the insertion loss is adversely affected.
Yong Thung Cho [58] established that contrary to the size and simplicity of the motors in terms of structural design, sources of motor noise and vibration can be quite diverse and complicated. The particle velocity of the motor was reconstructed from near- field sound pressure measurements of motor noise. In addition to noncontact measurements conducted on a motor running at constant speed, the particle velocity of a stationary motor due to the impulse of an impact hammer was measured with an accelerometer. Motor noise was measured under motor run-up conditions with different rotational speeds. Combination of the three methods could accurately measure, the sources of motor noise over a wide range of frequencies.
Zhien Liu,and Shuai Yuan et al [59] worked on combining substructure and power flow theory. Based on a simple vehicle model, characteristics of vibration, noise, and power flow are studied. Compared conventional FEM, the new method is confirmed to be feasible. In case of a vehicle with the problem of low-frequency noise, finite element models of substructures for vehicle body and chassis are established. They also employed substructure power flow method to examine the transfer characteristics of multidimensional vibration energy for the whole vehicle system. They concluded that the adjustment stiffness of drive shaft support and bushes at rear- suspension lower- arm, could decrease the vehicle interior noise.
R. K. Dunne, D. A. Desai, and R. Sadiku [60] carried out investigations on the effect of poroelastic materials on the internal vehicle cabin noise levels due to the structural vibration induced from road-tire interaction in the 20-200 Hz frequency range. This was achieved by developing an effective and efficient finite element analysis (FEA) tool that is capable of predicting the change in sound pressure levels (SPLs) due to the use of natural fiber trims in the vehicle cabin. A scaled vehicle model using ABAQUS FEA software was developed, employing similarity scaling laws, in order to predict the influence of various types of poroelastic trims on internal vehicle noise. The results indicated that the implemented poroelastic materials reduced the SPL by as much as 2.935db. The results indicated that the FEA model is capable of accurately predicting the influence that the inserted poroelastic natural fiber trims on internal cabin noise levels.
Literature contained in the cited references [61, 62, 63, 64, 65] throws light on the emerging trends to deal with acoustics, vibration control, and challenges posed by NVH in the automotive sector. Influences of Electric Propulsion on Vehicle Vibro- acoustics [61] An analysis on the coupled vibro-acoustic response [62], Siemens PLM LMS Solutions for NVH Acoustics and Comfort [63], Small Changes in Vehicle Suspension Layouts Could Reduce Interior Road Noise [64] and Recent Advances in Active Noise Control Inside Automobile Cabins [65], are some of the recent efforts to understand and tackle specific problems in this industry with respect to NVH and structural adjustments.
Renato Brancati, Ernesto Rocca, Daniela Siano and Massimo Viscardi [66] performed experimental vibro-acoustic analysis of the gear rattle induced by multi-harmonic excitation. The analysis is performed with the aid of various measurement techniques conducted on a specific test rig to acquire the angular rotations of the gears by using encoders, accelerations obtained from a triaxial accelerometer, sound pressure level determined by employing both acoustic microphones, and the correct evaluation of the acoustic sources by utilizing a pv sound intensity probe. Performance indices were adopted to compare the dynamic behaviors of the system with respect to the speed of the pinion, the fluctuations in the speed of the pinion and the lubrication conditions. The results of the comparative analysis showed very good agreement between the vibro-acoustic measurements and the results from the encoder-based method. This paper dealt with the mechanism to interpret the physical behavior of the gear pair with respect to the impacts occurring between the teeth during the different phases of the phenomenon.
David Lennström [67] discussed the new challenges being experienced by engineers with the introduction of electrical motors into cars traditionally powered by internal combustion engines with regard to NVH in his thesis. The thesis explored the audible perception of the electric power train and developed and validated experimental methods for assessment of noise transmission. The main mechanical system properties that are responsible for the airborne radiation and transfer of electric power train induced noise were studied. The acoustic transfer functions' (ATF) spatial resolution with respect to estimated interior noise was investigated for theoretically derived and measured surface vibrations. He worked on EV-specific noise based on structure- borne sound. The method of in-situ estimation of blocked forces, and a theoretically independent source characterization, are evaluated for transfer path analysis (TPA) of a double isolated electric rear axle drive. This thesis is intended to support engineers to succeed with the acoustic refinement and thereby contributes to increasing competitiveness of hybrid/electric vehicles.
-
CONCLUSION
The literature cited gives a broader view of the research that has been carried out in the past decade and directs one towards the current NVH research in the field of transport, especially automobiles. The rising demand for sustainable technologies,
emission-free vehicles, increased safety concerns, and improved fuel-economy and efficiency, are the key factors which are going to influence all major research efforts in the automotive sector. NVH study and characterization play a crucial role in this regard. Multiple studies on vibration characteristics of systems have been able to successfully model and mitigate unwanted excitations through structural modifications, and reduce the energy loss arising from it. By characterizing the natural harmonics of a system, design modifications can be performed such that the possibility of resonance during operation is mitigated. This not only reduces the risk of large deformations but the cost of maintenance too. Such efforts greatly reduce the maintenance cost, increase longevity of systems and also ensure prolonged structural stability. In addition to this, the automotive sector being heavily reliant on consumer- experiences, will definitely look towards NVH modifications so as to provide increased passenger comfort and minimize ambient noise. Therefore, NVH is a field that is crucial to the progression of the automotive industry and thus, a comprehensive understanding of the field can facilitate improved efficiency and performance of products in the future There is no Conflict of Interest in the publication of this article.
-
REFERENCES
-
-
Mohanty, A.R., and Shahab Fatima, 2014, An overview of automobile noise and vibration control, Noise Notes 13(1), pp. 43-56. DOI: 10.1260/1475-4738.13.1.43.
-
Mohammad Al Zubi, 2012, Investigation and improvement of noise, vibration and harshness (NVH) properties of automotive panels, Wayne State University, Dissertations, https://digitalcommons.wayne.edu/cgi/viewcontent.cgi?article=1526&ontext=oa_dissertations
-
Shin, S.H, and Cheong, C., 2010, Experimental characterization of instrument panel buzz, squeak and rattle (BSR) in a vehicle, Applied Acoustics, 71, pp. 1162-1168.
-
Wang binxing, Zheng sifa, Zhoullin, Liu shengqiang, Lian xiaomin, and Li keqiang, 2010, Acoustic modelling and analysis of vehicle interior noise based on numerical calculation, Proceedings of the 2010 International Conference on Intelligent Computation Technology and Automation, (ICICTA 2010), pp. 404-407.
-
Stephen Hambric, 2006, Structural Acoustics TutorialPart 1: Vibrations in Structures, Acoustics Today 2(4). https://www.researchgate.net/publication/243716526_Structural_Acoustics_Tutorial-Part_1_Vibrations_in_Structures, DOI: 10.1121/1.2961142.
-
Maressa, A., Pluymers, B., Donders, S., and Desmet, W., 2010, NVH optimization methodologies based on bead modification analysis in vehicle body design. VEHICLE, NOISE AND VIBRATION (NVH), PROCEEDINGSOF ISMA2010 INCLUDING USD2010, pp.4319-4337 http://past.isma- isaac.be/downloads/isma2010/papers/isma2010_0522.pdf,
-
Mélissa Férand ,Thomas Livebardon , Stéphane Moreau and Marlène Sanjosé,2019, Numerical Prediction of Far-Field Combustion Noise from Aeronautical Engines, Acoustics , 1(1), pp. 174-198; https://doi.org/10.3390/acoustics1010012
-
Khan, K., Akbar, M. A., and Koppelaar, H., 2015, Study of coupled nonlinear partial differential equations for finding exact analytical solutions, Royal Society Open Science, 2(7), Article ID 140406,.View at: Publisher Site | Google Scholar
-
Leung, A. Y. T., Yang, H. X., and Guo, Z. J., 2017, Periodic wave solutions of coupled integrable dispersionless equations by residue harmonic balance, Communications in Nonlinear Science and Numerical Simulation, 17(11), pp. 45084514. View at: Publisher Site | Google Scholar
-
Lee, Y. Y., Huang, J. L, Hui, C. K., and Ng, C. F., 2012, Sound absorption of a quadratic and cubic nonlinearly vibrating curved panel absorber, Applied Mathematical Modelling, 36(11), pp. 55745588. Publisher Site | Google Scholar
-
Lee, M. K., Hosseini Fouladi, M., and Narayana Namasivayam,S., 2017 , Natural frequencies of thin rectangular plates using homotopy-perturbation method, Applied Mathematical Modelling, 50, pp. 524543.View at: Publisher Site | Google Scholar
-
Le Besnerais, J, Fast Prediction of Variable-Speed Acoustic Noise and Vibrations due to Magnetic Forces in Electrical Machines https://eomys.com/IMG/pdf/fast_prediction_of_acoustic_noise_and_vibrarions_due_to_magnetic_forces.pdf
-
Pellerey, P., Lanfranchi, V., and Friedrich, G., 2012, "Coupled Numerical Simulation between Electromagnetic and Structural Models: Influence of the Supply Harmonics for Synchronous Machine Vibrations," in Magnetics, IEEE Transactions, 48(2), pp.983-986.
-
Pellerey, P., Lanfranchi, V.,and Friedrich, G., 2012, "Numerical simulations of rotor dynamic eccentricity effects on synchronous machine vibrations for full run up," in Electrical Machines (ICEM), XXth International Conference on 2-5 Sept. 2012, pp.3008-3014.
-
Marion, F., 2013, Magneto-vibroacoustic analysis: a new dedicated context inside Flux ®11.2, Cedrat News, 2013.
-
Vansant, K., 2014, From Tesla to Pascal, a magneto-vibroacoustic analysis linking Flux® to LMS Virtual. Lab, Cedrat News, 2014.
-
Le Besnerais, 2015, "Vibroacoustic Analysis of Radial and Tangential Air-Gap Magnetic Forces in Permanent Magnet Synchronous Machines," in IEEE Transactions on Magnetics, 51(6), pp. 1-9.
-
Sujit Kumar Jha and Ajay Sharma, 2013, OPTIMAL AUTOMOBILE MUFFLER VIBRATION AND NOISE ANALYSIS, International Journal of Automotive and Mechanical Engineering (IJAME), 7, pp. 864-881. http://ijame.ump.edu.my/images/Volume_7/6_%20Jha%20and%20Sharma.pdf) ISSN: 2229-8649 (Print); ISSN: 2180-1606 (Online); January-June 2013 ©Universiti Malaysia Pahang DOI: http://dx.doi.org/10.15282/ijame.7.2012.6.0071 864.
-
Jose Salvado, Maria do Rosário Calado, António EspÃrito Santo, and Anna D. Guerman, 2017, Numerical Modal Analysis of Vibrations in a Three- Phase Linear Switched Reluctance Actuator, Modelling and Simulation in Engineering, pp.1-18. https://www.researchgate.net/publication/316230659_Numerical_Modal_Analysis_of_Vibrations_in_a_Three- Phase_Linear_Switched_Reluctance_Actuator DOI: 10.1155/2017/3258376.
-
Lenin , N. C., and Arumugam , R. , 2010, Acoustic noise, vibration, harmonics, thermal of three phase linear switched reluctance machines, Joint International Conference on Power Electronics, Drives and Energy Systems & Power India, Date of Conference: 20-23 Dec. 2010, Date Added to IEEE Xplore: 14 February 2011, ISBN Information: INSPEC Accession Number: 11823786, DOI: 10.1109/PEDES.2010.5712483,
-
.Chandravanshi, M.L and Mukhopadhyay A.K., 2017,Analysisofvariationsinvibrationbehaviorofvibratoryfeederduetochangeinstiffnessofhelicalspringsusing FEM and EMA methods, Journal of the Brazilian Society of Mechanical Sciences andEngineering , 39(4) DOI: 10.1007/s40430-017-0767-z, https://www.researchgate.net/publication/315921540
-
Yao, L. Y., Yu, D. J., Cui, X. Y and Zang, X. G., 2010, Numerical treatment of acoustic problems with the smoothed finite element method, Applied Acoustics, 71(8), pp. 743753. Publisher Site | Google Scholar
-
Forte, P., Frendo, F., and Rodrigues, R. N., 2016, Finite element parametric study of the influence of friction pad material and morphological characteristics on disc brake vibration phenomena, J. Phys.: Conf. Ser. 744 012239, doi:10.1088/1742-6596/744/1/012239.
-
Chandrasekhar, N., Tang, C., Limsuwan, N., and Hetrick, J. et al., 2017, "Current Harmonics, Torque Ripple and Whine Noise of Electric Machine in Electrified Vehicle Applications," SAE Technical Paper 2017-01-1226. https://doi.org/10.4271/2017-01-1226
-
Ashok K Bagha, and Subodh V Modak, 2017, Active structural-acoustic control of interior noise in a vibro-acoustic cavity incorporating system identification , J. of low-frequency, noise and vibration and active control, 36 (3), pp.261-276. https://journals.sagepub.com/doi/full/10.1177/0263092317719636.
-
ERIC TINGWALL, The Physics of Engine Notes, Or: Why a Toyota V-6 and Porsche Flat-Six Sound So Different, The science of engine sounds., JAN 1, 2015. http://tulatech.com/uploads/3/1/8/6/31863835/2014-01-1675.pdf,
-
Serrano, J., Routledge, G., Lo, N., and Shost, M. et al., 2014, Methods of Evaluating and Mitigating NVH when Operating an Engine in Dynamic Skip Fire," SAE Int. J. Engines,7(3), pp. 2014. doi:10.4271/2014-01-1675
-
Anuj Rekhy , Robert Snyder and James, M., 2019,On the Frequency Up-Conversion Mechanism in Metamaterials-Inspired Vibro-Impact Structures, Acoustics, 1(1), pp. 156-173. https://doi.org/10.3390/acoustics1010011 – 12 Feb 2019, (This article belongs to the Special Issue Innovative Design and Applications of Materials for Acoustically Performative Indoor and Outdoor Environments]
-
Haosen Yang, Huirong Li, Hui Zheng, 2017, A structural-acoustic optimization of two-dimensional sandwich plates with corrugated cores, Journal of vibration Control, Volume: 23 issue: 18, page(s): 3007-3022, https://doi.org/10.1177/1077546315625558.
-
Berry J. Nicolas, A., 1994, Structural acoustics and vibration behavior of complex panels, Applied Acoustics , 43(3), pp. 185-215.
.https://doi.org/10.1016/0003-682X(94)90047-7
-
Zhou, Q. Z., Wang, D. S., and Zhu, Y. Y., 2014, An approximate analytical method of the nonlinear vibroacoustic coupling system, Shock and Vibration, 2014, Article ID 315416, 10 pages. Publisher | Google Scholar
-
Yang, S., and Yang, Q., 2017, Geometrically nonlinear transient response of laminated plates with nonlinear elastic restraints, Shock ad Vibration, 2017, Article ID 2189420, 9 pages. Publisher Site | Google Scholar
-
Fan, J. Y. and Huang, J., 2018, Haar wavelet method for nonlinear vibration of functionally graded CNT-reinforced composite beams resting on nonlinear elastic foundations in thermal environment, Shock and Vibration, 2018, Article ID 9597541, 15 pages. Publisher Site | Google Scholar
-
Huang, J., Su, K. L. R., Lee, Y. Y. R, and Chen, S., 2018, Various bifurcation phenomena in a nonlinear curved beam subjected to base harmonic excitation, International Journal of Bifurcation and Chaos, 28(7), Article ID 1830023.Publisher Site | Google Scholar
-
Venkatesham, B, Tiwari, M., and Munjal, M. L., 2011, Prediction of breakout noise from a rectangular duct with compliant walls, International Journal of Acoustics and Vibration, 16(4), pp. 180190.Publisher Site | Google Scholar
-
Jade, N., and Venkatesham, B., 2018, Experimental study of breakout noise characteristics of flexible rectangular duct, Mechanical Systems and Signal Processing, 108, pp. 156172. Publisher Site | Google Scholar
-
Younesian, D., Sadri, M., and Esmailzadeh, E., 2014, Primary and secondary resonance analyses of clamped-clamped micro-beams, Nonlinear Dynamics, 76(4), pp. 18671884. Publisher Site | Google Scholar
-
Hui, C. K., Lee, Y. Y., and Reddy, J. N., 2011, Approximate elliptical integral solution for the large amplitude free vibration of a rectangular single mode plate backed by a multi-acoustic mode cavity, Thin-Walled Structures, 49( 9), pp. 11911194.Publisher Site | Google Scholar
-
Lee, Y. Y., 2016, Free vibration analysis of a nonlinear panel coupled with extended cavity using the multi-level residue harmonic balance method,
Thin-Walled Structures, 98, pp. 332336. Publisher Site | Google Scholar
-
Qu, Y., and Meng, G., 2017, Nonlinear vibro-acoustic analysis of composite sandwich plates with skin-core debondings, AIAA Journal, 55(5), pp. 17231733, Publisher Site | Google Scholar
-
Aginsky, Z, .and Gottlieb, O., 2013, Nonlinear fluid-structure interaction of an elastic panel in an acoustically excited two-dimensional inviscid compressible fluid, Physics of Fluids, 25(7), Article ID 076104.Publisher Site | Google Scholar
-
Jacques, N., Daya, E. M., and Potier-Ferry, M., 2010, Nonlinear vibration of viscoelastic sandwich beams by the harmonic balance and finite element methods, Journal of Sound and Vibration, 329(20), pp. 42514265. Publisher Site | Google Scholar
-
Yiu-Yin Lee, 2019, Analytic Formula for the Vibration and Sound Radiation of a Nonlinear Duct, 2019 |Article ID 9685142 | 12 pages |https://doi.org/10.1155/2019/9685142
-
Lee, Y. Y., 2016, Analytic solution for nonlinear multimode beam vibration using a modified harmonic balance approach and Vietas substitution, Shock and Vibration, 2016, Article ID 3462643, 6 pages. Publisher Site | Google Scholar
-
Lee, Y. Y., Huang, J. L., Hui, C. K. and Ng, C. F., 2012, Sound absorption of a quadratic and cubic nonlinearly vibrating curved panel absorber, Applied Mathematical Modelling, 36(11), pp. 55745588. Publisher Site | Google Scholar
-
Nitin Sharmaa , Trupti Ranjan Mahapatra, and Subrata Kumar Panda , 2017,Numerical Study of Vibro-Acoustic Responses of Un-Baffled Multi- Layered Composite Structure under Various End Conditions and Experimental Validation, Lat. Am. j. solids struct. , 14(8). , http://dx.doi.org/10.1590/1679-78253830,
-
Mathieu Sarrazin, Steven Gillijns, Jan Anthonis, Karl Janssens, Herman van der Auweraer , and Kevin Verhaeghe , NVH analysis of a 3 phase 12/8 SR motor drive for HEV applications, November 17-20, 2013, Interior Acoustic Simulation for In-Car Audio Design – Sound Published in: 2013 World Electric Vehicle Symposium and Exhibition (EVS27), 17-20 Nov. 2013, Electronic ISBN:978-1-4799-3832-2 ,INSPEC Accession Number: 14649097,
Publisher: IEEE, DOI: 10.1109/EVS.2013.6914767
-
Yongliang Wang, Xunpeng Qin, Li Lu, Huaming Liu, and Jinjing Huang, 2016, The noise control of minicar body in white based on acoustic panel participation method, Journal of Vibroengineering, 18(2), pp. 1332-1345. https://www.jvejournals.com/article/16222*******
-
Vinay V Nesaragi et al, 2014, Design and noise, vibration, harshness analysis of engine bonnet of the car, Int. Journal of Engineering Research and Applications, 4(7), pp.05-11.www.ijera.com ISSN: 2248-9622,https://core.ac.uk/download/pdf/25780553.pdf
-
Dejan V. Matijevi and Vladimir M. Popovi, 2017, Overview of Modern Contributions in Vehicle Noise and Vibration Refinement with Special Emphasis on Diagnostics, FME Transactions,45, pp.448-458.https://www.mas.bg.ac.rs/_media/istrazivanje/fme/vol45/3/18_dmatijevic_et_al.pdf,
-
Mohammad Al-Zubi, Emmanuel Ayorinde, Nabeel Alshabatat, Mehmet Dundar and YellapuMurty, 2014, SOUND AND VIBRATION CONSIDERATIONS OF SOME MATERIALS FOR AUTOMOTIVE ENGINEERING APPLICATIONS American Journal of Applied Sciences, 11 (10), pp. 1784-1797.
-
Andrew J. Hull , and Daniel Perez, 2019, A High-Frequency Model of a Circular Beam with a T-Shaped Cross Section, Acoustics, 1(1), pp. 295-
336. https://doi.org/10.3390/acoustics1010017
-
Chenhui Zhao and Marehalli G. Prasad, 2019, Acoustic Black Holes in Structural Design for Vibration and Noise Control, Acoustics , 1(1), pp. 220- 251. https://doi.org/10.3390/acoustics1010014 – 25 Feb 2019
-
Mélissa Férand , Thomas Livebardon , Stéphane Moreau and Marlène Sanjosé, 2019, Numerical Prediction of Far-Field Combustion Noise from Aeronautical Engines, Acoustics , 1(1), pp. 174- 198. https://doi.org/10.3390/acoustics1010012 – 19 Feb 2019,
-
Sabin Sathyan, UgurAydin and Anouar Belahcen, 2020, Article Acoustic Noise Computation of Electrical Motors Using the Boundary Element Method , Energies, 13(1), 245. https://doi.org/10.3390/en13010245
-
F. Simon, T. Haase, 2014, Activities of European Research Laboratories Regarding Helicopter Internal Noise, Aeroacoustics, AL07-04, DOI: 10.12762/2014., http://www.aerospacelab-journal.org/sites/www.aerospacelab-journal.org/files/AL07-04.pdf
-
Yiu-Yin Lee, 2018,Nonlinear structure-extended cavity interaction simulation using a new version of harmonic balance method, https://doi.org/10.1371/journal.pone.0199159https://journals.plos.org/plosone/article?id=10.1371/journal.pone.0199159, Published: July 3, 2018.
-
Yong Thung Cho, 2018, Characterizing Sources of Small DC Motor Noise and Vibration, Micromachines (Basel) PMID: 30393359,
PMCID: PMC6187501, DOI: 10.3390/mi9020084, 2018-02-01
-
Zhien Liu, Shuai Yuan, Shenghao Xiao, Songze Du, Yan Zhang, and Chihua Lu, 2017, Full Vehicle Vibration and Noise Analysis Based on Substructure Power Flow, 2017 , Article 8725346 , 17 pages . https://doi.org/10.1155/2017/8725346, https://www.hindawi.com/journals/sv/2017/8725346/
-
Dunne, R. K., Desai, D. A. and Sadiku R., 2018, Investigation and development of a numerical tool for the prediction and influence of natural fibre poroelastic trim behaviour on automotive cabin noise, Cogent Engineering , 5(1). https://www.tandfonline.com/doi/full/10.1080/23311916.2018.1548992,
-
Bekker, A., 2014, Influences of Electric Propulsion on Vehicle Vibro-acoustics, R & D Journal of the South African Institution of Mechanical Engineering, 30, pp. 47-54.
-
Sarigul AS, Arpaz O, Secgin A., 2018, An analysis on the coupled vibro-acoustic response characteristics of cavity-type structures, Phys Astron Int J., 2(5), pp. 476-482. DOI:10.15406/paij.2018.02.00127
-
Siemens PLM LMS Solutions for NVH Acoustics and Comfort …www.ddsplm.com wp-content uploads 2017/11
-
Timo von Wysocki , Jason Chahkar and Frank Gauterin, 2020, Small Changes in Vehicle Suspension Layouts Could Reduce Intrior Road Noise,
Vehicles, 2(1), pp.18-34. doi:10.3390/vehicles2010002 www.mdpi.com/journal/vehicles
-
Prasanga N. Samarasinghe, Wen Zhang, and Thushara D. Abhayapala, 2016, Recent Advances in Active Noise Control Inside Automobile Cabins,
Draft, pages 1-26. ,https://openresearch-repository.anu.edu.au/bitstream/1885/157006/2/P11_DP14.pdf
-
Renato Brancati, Ernesto Rocca, Daniela Siano and Massimo Viscardi, 2017, Experimental vibro-acoustic analysis of the gear rattle induced by multi- harmonic excitation, Proc IMechE Part D, J Automobile Engineering, IMechE 2017, pp. 112, Sagepub.co.uk/journalsPermissions.nav DOI: 10.1177/0954407017707670.
-
David Lennström, 2015, Assessment and control of tonal components in electric vehicles, Doctoral Thesis, Department of Civil, Environmental and Natural Resources Engineering, Luleå University of Technology, Printed by Luleå University of Technology, Graphic Production. 2015. https://trid.trb.org/view/1506310