
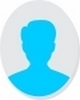
- Open Access
- Authors : Gaurav Bharadwaj, Satyanarayan Joshi, Ravindra Singh Chauhan, Virendra Kumar Sharma, Jitendra Kumar Deegwal
- Paper ID : IJERTV12IS090047
- Volume & Issue : Volume 12, Issue 09 (September 2023)
- Published (First Online): 29-09-2023
- ISSN (Online) : 2278-0181
- Publisher Name : IJERT
- License:
This work is licensed under a Creative Commons Attribution 4.0 International License
Optimal Singular Adaptive Observer Control Approach for a Wind Energy Conversion System Based on a Permanent Magnet Synchronous Generator Fed by a Matrix Converter
Gaurav Bharadwaj Research scholar,
Bhagwant University, Ajmer, Faculty, MEC Ajmer, India
Satyanarayan Joshi Research scholar,
Bhagwant University, Ajmer, India Faculty, MEC Ajmer, India
Ravindra Singh Chauhan Research scholar,
Bhagwant University, Ajmer Faculty, MEC Ajmer,
Virendra Kumar Sharma Electrical Engineering Bhagwant University, Ajmer Ajmer, India
Jitendra Kumar Deegwal Electronics and Communication Engineering,
Engineering College, Ajmer Ajmer, India
Abstract This paper suggests an adaptive control of the wind permanent magnet synchronous generator (PMSG) driven by a variable speed wind turbine. Processes in wind generator have been studied using a mathematical model. The results show suitability of using adaptive control using Optimal Singular Adaptive (OSA) observer. In this paper the control of a grid- connected wind energy conversion system (WECS) based on a sensor less vector-controlled cage induction machine fed by a matrix converter is presented. The machine is vector controlled using a model reference adaptive system (MRAS) observer to estimate the rotational speed and rotor position. The electrical torque of the induction generator is regulated to drive the WECS to the operating point where the wind turbine aerodynamic efficiency is maximised. Stability issues related to the operation of a WECS connected to the grid using a matrix converter are also discussed in this work. Experimental results, obtained with a 2.5 kW prototype are presented and fully discussed in this paper. A systematic controller design and implementation for a matrix-converter-based induction motor drive system is proposed. A nonlinear adaptive back stepping controller is proposed to improve the speed and position responses of the induction motor system. By using the proposed adaptive back stepping controller, the system can track a time- varying speed command and a time-varying position command well. Moreover, the system has a good load disturbance rejection capability. The realisation of the controller is very simple. All of the control loops, including the current loop, speed loop and position loop, are implemented by a digital signal processor. Several experimental results are given to validate the analysis. In this paper, the proposed predictive controller is modelled in MATLAB/SIMULINK and validated experimentally on a 6-kW wind turbine generator. Test results prove the effectiveness of the control strategy in terms of energy efficiency and dynamical adaptation to the wind turbine operational conditions. The experimental results also show that
the control method has good dynamic response to parameter variations and external disturbances. Therefore, the developed technique will help increase the uptake of permanent magnet synchronous generators and model predictive control methods in the wind power industry.
Keywords- wind energy conversion system; sliding mode control; direct power control; back stepping control; predictive currents control; permanent magnet synchronous generator
-
INTRODUCTION
Wind power generation has received a lot of attention in recent years as a means of generating electricity, and it has emerged as an important alternative source. In order to generate maximum power from a wind energy conversion system (WECS), it is necessary to accurately estimate aerodynamic torques and system uncertainties. It has become increasingly difficult to regulate wind energy conversion systems (WECS) and improve the quality of electrical power delivered to the grid under varying wind speeds. An investigation of grid-connected wind turbines uses permanent magnet synchronous generators (PMSGs) and bidirectional converters back-to-back [1]. PMSG speed is controlled by the machine-side converter (MSC), while DC bus voltage and power factor are controlled by the grid-side converter (GSC). Second-order sliding mode controls are used to regulate a nonlinear wind energy conversion system while reducing chattering, which causes mechanical wear with first-order sliding mode controls. A modified super-twisting method is used to create the sliding mode control. A MATLAB Simulink environment is used to build and simulate both the power and control components. Through the high activity of the control input, the study successfully decreased the chattering caused by the switching gain. Increasing demand
for electricity is causing a surge in supply.Matrix converters for AC/AC have several advantages. Matrix converters, for example, are one-stage converters. There is no DC-link energy storage component required. Additionally, it has a sinusoidal input current with a bidirectional power flow for the entire matrix converter drive system. In the past, matrix converters were developed in research laboratories only and could not be used widely in industry. There has been a change in the situation. A new technology developed by Eupec Co. integrates the entire matrix-converter power device in one package. A commercially available version of the integrated power modules has also been released.
Energy that is clean and renewable, however, receives the most attention. In the production of electric power, many renewable energy sources are used. Among these energy sources are photovoltaic, wind, biomass, fuel cells, and tidal [3]. There are many benefits associated with wind as an energy source, including its availability, omnipresence, and environmental friendliness. In addition to being highly reliable, it is also very cost-effective. With these features, wind power generation capability grew rapidly, with an average annual growth of 30% in the world's energy resources over the last decade [2]. Generators and wind turbines are the main components of wind energy generation. Power electronic converters could be used to feed it into the grid network or to use it standalone.
There are two types of wind turbines: fixed-speed and variable-speed. Fixed speed operation maintains a constant speed regardless of wind speed. Despite its simplicity and low cost, the system is more efficient. Energy capture is low, power quality is poor, and mechanical stress is high. With its high efficiency and good power quality, variable speed wind turbine generators capture a large amount of energy from the wind over a wide range of wind speeds. By overriding or generating reactive power, the topology can regulate the power factor.
In an AC/AC converter, sinusoidal output voltages are provided with varying amplitudes and frequencies, and sinusoidal input currents are drawn from the AC source. A rectifier, DC-link, or inverter is a commonly used component in conventional AC drive systems. An energy storage component for the DC-link is a large capacitor. Capacitors are large and expensive, so they can be critical components. There is a problem with the power factor and current harmonics of the AC input side. To absorb the energy during braking, the drive system also needs a braking resistance. Over the past few years, matrix converters have become increasingly popular in AC/AC converter applications.
Matrix converters are superior to traditional PWM (Pulse width modulation) drives due to their regeneration capacity and sinusoidal input current [3-4]. In this respect, matrix converters are similar to cycloconverters, since they lack a dc link and generate output waveforms made up of segments from the input waveforms. Therefore, the matrix converter possesses both the advantages of acycloconverter and a PWM drive:
-
Due to its regeneration capability, it is capable of operating in all four quadrants of the torque-speed plane.
-
The input current waveform is sinusoidal and the input power factor is unity. The input power factor may be controlled throughout the entire speed range.
-
As there is no DC link, no energy storage devices are required. The output voltage and input current waveforms can be controlled to be nearly sinusoidal.
-
As the harmonic distortion occurs at high frequencies, it may be used as a direct frequency changer, converting fixed ac or dc sources into variable sources
-
This paper proposes a novel matrix-converter-based IM control system. A digital signal processor implements all current, speed, and position loops. A satisfactory control performance can be achieved after applying adaptive backstepping speed- and position control algorithms. Furthermore, the system can track both time-varying speed and position commands[5]. This is the first time that an adaptive backstepping controller has been applied to a matrix converter-based IM system. Furthermore, the control law can be implemented very easily with a digital signal processor and can be applied to both speed and position control. However, in PMSG, its reactive power can be controlled and applied to other items of the power system[6].However, the generators are more costly and more prone to failure. Compared to the electrically excited generator, this generator is more efficient, more reliable, and has a higher power-to-weight ratio. A major drawback of PMSG is the high cost of PMs material and demagnetization at high temperatures. Despite this, the cost of PMs material has decreased in recent years due to their high performance and attractiveness in research [7], [8], [9][10].
1.1. Wind Energy Conversion System Modelling
There are two parts to this model: the generation side and the grid side (Fig. 1). In this study, power control of the generator side is the focus[11].
Fig. 1. PMSG-based wind energy conversion
1.2. Matrix Converter Drive System
This paper will consider the block diagram in Fig. 1a. System hardware includes a three-phase IM and load, a nine-switch matrix converter, and a digital signal processor [12]. A three-phase, Y connected, IM with a rated speed of 1500 rpm was chosen for the study. Velocity and position are sensed by a resolver [13]. Due
to the three-phase balanced drive system, two Hall effect current sensors are used to detect stator currents. Here's how it works. The position (speed) command is compared with the feedback position (speed). Next, the position (speed) controller generates the q-axis current command and transfers it into three-phase current commands. Next, the three-phase current commands are compared [14].
Fig. 2. Circuit diagram of whole drive Block diagram
-
Matrix Converter Switching Algorithm
Matrix converter switching patterns should satisfy the basic requirements. Matrix converter switches cannot short circuit input voltage sources[15]. The matrix converter switches cannot open the output load currents since the load is inductive. Matrix converters use two major switching methods: direct and indirect. Using only six switching patterns, the direct method provides output currents or voltages[16]. It is possible to obtain the required output voltage by controlling the duty cycle of the nine switches. To determine the switching states, this method requires a lot of computation. Direct switching is based on the switching strategy of conventional converters and inverters. A virtual equivalent circuit can explain the switching algorithm of indirect switching[17].
Fig.3 WECS Block Diagram
-
Wind turbine modelling
A wind turbine converts the kinetic energy of the wind into mechanical power. Kinetic energy and power, which is the input power to the wind turbine, can be expressed as [18]. (1) and (2) are the expressions for wind energy and power,
(1)
where m is the air mass expressed as = v
(2)
Since the mechanical power extracted from the wind is determined by the power coefficient of the turbine, which is usually provided by the manufacturer[19]. In this case, the output power is given as:
Where is the air density[20], R is the radius of the wind turbine, is the wind speed,(, ) is the power coefficient, is the tip speed ratio, and is the turbine blade
pitch. Therefore, the power coefficient and the tip speed ratio
are expressed as[21],
In this equation, a rotor spinning at a low speed can be controlled to maintain the optimum tip speed ratio by changing the rotational speed of the shaft at a low speed [22]. Consequently, the instantaneous change in wind speed necessitates MPPT operation. As the wind speed changes, a robust controller must be employed to regulate the speed of the rotor so as to maximize the power [23].
-
Matrix Converter
A matrix converter interfaces two multi-phase systems with different frequencies through an array of semiconductors. Fig. A three-phase-to-three-phase matrix converter with nine bi- directional switches. [24] provide a comprehensive explanation of the matrix converter's operation and modulation schemes. the MPPT applies the output voltage reference vector and input current reference vector to the matrix converter controller. In order to control the PMSG angular speed, the matrix converter produces a set of voltages [25].
Fig. 4 illustrates an example of how a matrix converter can be used
Where is the stator pulsation and is directly proportional to the shaft rotational speed, which depends on how the
generator interacts mechanically[31], And the overall equivalent model of PMSG based wind turbine is,
Matrix converters are controlled by switching functions. Direct modulation and indirect modulation are two general approaches to determining switching functions [26]. This paper uses the direct method. This method involves a modulator with input current and output voltage vectors as reference vectors and determining the switching functions to get the desired voltage and current output [27]. The output power captured by the WT as a function of the speed As a result, there is only one optimal point in Figure 2. It is possible to fine-tune the speed ratio or the tip speed of the wind turbine by taking into consideration some values in order to regulate the wind power [28].
Parameter
Value
No of phases
3
Rotor type
Round
Phase resistance
0.15 ohm
Inductance
5.3mH
Moment of Inertia (J)
0.016 (kgm2)
Number of pole pairs
4
Rated speed
rpm)
The PMSG parameters are given in Table 1[32], Table 1. System parameters of the PMSG
(9)
III.
Fig. 5. Wind turbine power characteristics
-
-
MODELING OF THE PMSG AND DC-DC CONVERTER
This PMSG model is based on the following simplifying assumptions: sinusoidal distribution of the stator winding, electric and magnetic symmetry, negligible iron losses, and unsaturated magnetic circuit. In the d-q reference frame, the voltage equation can be expressed as [29][30] if we ignore the homopolar voltage, Vo, which is symmetric.
This PMSG model is based on the following simplifying assumptions: sinusoidal distribution of the stator winding, electric and magnetic symmetry, negligible iron losses, and unsaturated magnetic circuit. In the d-q reference frame, the voltage equation can be expressed as [33][35] if we ignore The PMSG was simulated in MATLAB/Simulink to analyse the performance of the proposed sliding mode controller. able 1 lists the parameters of the system. Fig. A wind variation of 10 m/s and a minimum of 5 m/s is shown in Figure 4, which is the input to the PMSG wind energy system. The highly nonlinear nature of the control design and the wind speed range demonstrate its effectiveness. SMC controllers ensure speed tracking the homopolar voltage, Vo, which is symmetric
Fig. 6. PMSG control system configuration
Fig. 7. Variations in wind speed
Fig. 5 and Fig.7 demonstrate the variations in wind speed and rotor speed, respectively. The power coefficient, rotational shaft speed, and power profile are shown in Fig. 6, Fig. 7, and Fig. 8, respectively. The performance is comparable to those with an observed good performance is comparable to those with reference (Fig. 8). The output power and torque of a wind turbine are proportional to the rotor speed. The PI controller responds similarly to the adaptive backstepping controller after suitably adjusting the parameters. When a 2Nm load is added, the PI controller performs a more serious position disturbance than the adaptive backstepping controller. The PI controller's load disturbance response can be improved by increasing the parameter KI; however, the controller's related transient response overshoots as KI is increased. For the proposed matrixconverter IM drive system, the backstepping controller performs better than the PI controller.
Fig. 8. Power coefficients of the wind turbine
Using the sliding mode controller, a schematic diagram of the overall control configuration can be seen showing the performance of the generator. When the set point is (VDC = 1200V), the grid side control attempts to maintain the DC link voltage of the Back-to-Back converter during wind variations. The DC-link voltage is adjusted to settle around a continuous reference of 1200 V to illustrate its resistance to wind fluctuations. DC voltage will obviously change within permissible limits during simulation, i.e. grid currents over time, depicts 3-phase grid voltages over time. With increasing wind speed, the current increased, indicating the grid was receiving more active electricity.
-
CONCLUSION
Currently, research and development in the wind energy industry are focused on grid-connected wind turbines. Among the main concerns of today's wind turbine manufacturers are: A medium-voltage direct-driven permanent magnet synchronous generator with variable speed technology, as well as sophisticated control systems that improve wind energy conversion efficiency and meet grid code requirements. In this study, a fast response dynamic control using a modified super-twisting algorithm was constructed and simulated to validate the system. The wind turbine is connected to the load via a matrix converter that acts as the interface between the wind turbine and the load. As a means of controlling the matrix converter switches, direct space vector modulation is used. There are theoretical analysis and simulation results that are presented for the purpose of verifying the feasibility and performance of the proposed approach. This paper investigates a novel controller design for a matrix converter-based IM system. A digital signal processor executes all the control algorithms, such as the switching strategy, the coordinate transformation, the speed control, and the position control. A matrix converter-based IM system is designed using a systematic and analytical approach. Implementation validates the proposed design approach. Thus, matrix converter-drive systems gain a new direction. Higher-order sliding mode controls are used to regulate a nonlinear wind energy conversion system that causes mechanical wear when using first-order sliding mode controls. Due to the high activity of the control input, the study successfully reduced the chattering effect caused by the switching gain. Although the principle of higher order sliding mode controls is presented here, sliding mode controllers that
operate at orders greater than 2 can be used to further reduce chattering. Studying conditions such as load, grid connections, and faults can lead to the real implementation of higher-order sliding mode controllers.
-
REFERENCES
-
J. Electr. Eng. Comput. Sci., vol. 27, no. 1, pp. 274288, 2019, https://doi.org/10.3906/elk-1806-17.
[11] M. Aimene, A. Payman, and B. Dakyo, Comparative Study between Flatness-Based and FieldOriented Control Methods of a Grid- Connected Wind Energy Conversion System, Processes, vol. 10, no. 2, p. 378, 2022, https://doi.org/10.3390/pr10020378. [12] C.-T. Ma and Z.-H. Shi, A Distributed Control Scheme Using SiC- Based Low Voltage Ride-Through Compensator for Wind Turbine Generators, Micromachines, vol. 1, no. 39, 2021, https://doi.org/10.3390/mi13010039. [13] N. Hawkins, B. Bhagwat, and M. L. McIntyre, Nonlinear current- mode control of scig wind turbines, Energies, vol. 14, no. 1, 2021, https://doi.org/10.3390/en14010055. [14] N. El Ouanjli, A. Derouich, A. El Ghzizal, S. Motahhir, A. Chebabhi,Y. El Mourabit, and M. Taoussi, Modern improvement techniques of direct torque control for induction motor drives – a review, Prot. Control Mod. Power Syst., vol. 4, no. 11, 2019, https://doi.org/10.1186/s41601-019-0125-5.
[15] H. Hamla, L. Rahmani, and N. Belhaouchet, A modified direct torque control with minimum torque ripple and constant switching frequency for induction motor drives, Int. Trans. Electr. Energy Syst., vol. 29, no. 12, pp. 120, 2019, https://doi.org/10.100/2050-7038.12120. [16] P. D. Patel and S. N. Pandya, Comparative Analysis of Torque Ripple for Direct Torque Control based Induction Motor Drive with differentstrategies, Aust. J. Electr. Electron. Eng., Taylor Fr., 2022, https://doi.org/10.1080/1448837X.2021.2023249.
[17] G. S. Kaloi, J. Wang, and M. H. Baloch, Active and reactive power control of the doubly fed induction generator based on wind energy conversion system, Energy Reports, vol. 2, pp. 194200, 2016, https://doi.org/10.1016/j.egyr.2016.08.001. [18] S. M. Hosseini and M. Manthouri, Type 2 adaptive fuzzy control approach applied to variable speed DFIG based wind turbines with MPPT algorithm, Iranian Journal of Fuzzy Systems, vol. 19, no. 1, pp. 3145, 2022, https://dx.doi.org/10.22111/ijfs.2022.6549. [19] J. Tavoosi, A. Mohammadzadeh, B. Pahlevanzadeh, M. B. Kasmani, S.S. Band, R. Safdar, and A. H. Mosavi, A machine learning approach for active/reactive power control of grid-connected doubly-fed induction generators, Ain Shams Eng. J., vol. 13, no. 2, 2022, https://doi.org/10.1016/j.asej.2021.08.007.
[20] Y. Huang, Sliding Mode Observer Design for Permanent Magnetic Synchronous Generator Based Wind Energy Conversion Systems," Southern Illinois University at Edwardsville, 2017, https://www.proquest.com/docview/1899625348.