
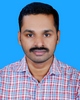
- Open Access
- Authors : Sajin E , Shanavas K P , Shijith K
- Paper ID : IJERTV10IS080167
- Volume & Issue : Volume 10, Issue 08 (August 2021)
- Published (First Online): 30-08-2021
- ISSN (Online) : 2278-0181
- Publisher Name : IJERT
- License:
This work is licensed under a Creative Commons Attribution 4.0 International License
Optimisation in CNC Turning by Teaching Learning based Algorithm
Sajin E 1 ,Shanavas K P 2, Shijith K 3
1,2,3 Assistant Professor, Dept. of Mechanical Engineering.
College of Engineering Vadakara Kozhikode, Kerala, India
Abstract Teaching learning based optimization is a recently developed optimization technique which seems to be a promising optimization technique with competitive performance among other evolutionary algorithms. In this study teaching learning based optimization is used for finding optimal process parameters for minimising surface roughness and maximizing material removal rate in CNC turning process. Experiments were done on mild steel work piece using coated carbide insert under dry condition. Response surface methodology was used for design of experiments and subsequent mathematical modelling of surface roughness and material removal rate. The process parameters that optimize surface roughness and material removal rate were found out using teaching learning based optimization. These results were compared with that obtained by another population based optimization technique genetic algorithm. Result shows that teaching learning based optimization provides better result in optimizing surface roughness and material removal rate than genetic algorithm. Also teaching learning based optimization converges faster to the optimum condition than genetic algorithm.
KeywordsCNC Turning, Teaching learning based optimization, Response surface methodology, Genetic algorithm, Surface roughness, Material removal rate.
-
INTRODUCTION
Machining is a process of gradual removal of excess material from the preformed blanks in the form of chips. Turning is one of the most widely employed machining processes for producing and finishing cylindrical and other work pieces. Turning is used to reduce the diameter of the work piece, usually to a specified dimension, and to produce a smooth finish on the metal. In turning material removal takes place by relative motion of the tool against the work piece. In turning the tool should be harder than the work piece for effective removal of the material. The work piece will be turned so that adjacent sections have different diameters. Basically it can be defined as the machining of external surface in which a single point cutting tool is feeding parallel to the axis of the rotating work piece which will remove the excess material from outer surface.
The three primary factors in any basic turning process are speed, feed, and depth of cut. Other factors such as kind of material and type of tool have a large influence, of course, but these three are the ones the operator can change by adjusting the controls, right at the machine. Speed always refers to the spindle and the work piece. When it is stated in revolutions per minute (rpm) it tells their rotating speed. But the important feature for a particular turning operation is the surface speed, or the speed at which the work piece material is moving past the cutting tool. It is simply the product of the rotating speed
times the circumference of the work piece before the cut is started. It is expressed in meter per minute (m/min), and it refers only to the work piece. Every different diameter on a work piece will have a different cutting speed, even though the rotating speed remains the same. Feed always refers to the cutting tool, and it is the rate at which the tool advances along its cutting path. On most power-fed lathes, the feed rate is directly related to the spindle speed and is expressed in mm (of tool advance) per revolution (of the spindle), or mm/rev. Depth of cut is the thickness of the layer being removed (in a single pass) from the work piece or the distance from the uncut surface of the work to the cut surface, expressed in mm. It is important to note, though, that the diameter of the work piece is reduced by two times the depth of cut because this layer is being removed from both sides of the work.
The material removal rate (MRR) in turning process is the volume of material that is removed per unit time or weight of material that is removed per unit time. It is expressed either in mm3/min or in g/min. The MRR value directly relates to the productivity of a machine. If the machine has high MRR then more amount of work can be carried out in given time and hence an increase in productivity. But just having a high MRR doesnt satisfy the conditions of a good product. The MRR should be adjusted in such a way that the other quality parameters such as surface roughness, tool wear rate etc. are not affected.
Surface roughness is an important measure of product quality since it greatly influences the performance of mechanical parts as well as production cost. Surface roughness has an impact on the mechanical properties like fatigue behaviour, corrosion resistance, creep life etc. It also affects other functional attributes of parts like friction, wear, light reflection, heat transmission, lubrication, electrical conductivity, etc. The resultant roughness produced by a machining process can be thought of as the combination of two independent quantities Ideal roughness and natural roughness. Ideal surface roughness is a function of feed and geometry of the tool. It represents the best possible finish which can be obtained for a given tool shape and feed. It can be achieved only if the built-up-edge, chatter and inaccuracies in the machine tool movements are eliminated completely. But in practice, it is not usually possible to achieve such conditions. One of the main factors contributing to natural roughness is the occurrence of a built-up edge and vibration of the machine tool. Thus, larger the built up edge, the rougher would be the surface produced, and factors tending to reduce chip-tool friction and to eliminate or reduce the built-up edge would give improved surface finish.
To ensure the quality of machining products, and to reduce the machining costs and increase the machining effectiveness, it is very important to select the machining parameters are selected in CNC machining. Traditional manufacturing industries have long depended on highly skilled work force, thus perhaps partially optimizing few parameters/ things without use of any scientific practice. The other aspect of relying on skilled workers is that it is very difficult to attain the optimum value each time. But use of NC/ CNC requires optimizing all the machining parameters in a specific way. In recent times, optimization algorithms are becoming increasingly popular in engineering design and decision making activities, primarily because of the availability and affordability of high speed computers.
The objective of this paper is to set up the optimum cutting parameters, optimizing Surface roughness and Material removal rate without violating the constraints. In this paper, the cutting parameters affecting these two objectives are assumed as spindle speed (rpm), feed (f) and depth of cut (d). The requirement is to establish the optimal value of these cutting parameters so that both objective functions are optimized together.
Response surface methodology (RSM) is a collection of mathematical and statistical technique that is useful for modelling and analysis of problems in which a response of interest is influenced by several variables and the objective is to optimise the response. In most RSM problems the form of relationship between response and the independent variables is unknown. Thus the first step is to find a suitable approximation for the true functional relationship between the response and the set of independent variables. If the response is well modelled by a linar function of the independent variable, then the approximating function is the first order model. If there is a curvature in the system, then a polynomial of higher degree must be used, such as the second order model.
Here the optimization is carried out using Teaching Learning Based Optimization (TLBO) technique. It is based on teaching-learning process in which every learner tries to learn something from other individuals to improve themselves. This algorithm simulates the traditional teaching-learning phenomenon of a class room.
-
LITRATURE REVIEW
Ashvin J Makadia et al [7] used response surface methodology to optimize machining parameters such as feed rate, tool nose radius, cutting speed and depth of cut in the CNC turning of AISI 410 steel. The effect of these parameters on surface roughness was studied to find out the most influencing parameter. Feed rate followed by tool nose radius were the most influencing parameters that effects surface roughness in the CNC turning of AISI 410 steel. By carrying out the optimization, optimum combination of parameters obtained were 255.75 m/min, 0.3mm, 0.1 mm/rev,
1.2 mm for cutting speed, depth of cut, feed rate and tool nose radius respectively.
Anil Gupta et al [8] carried out multi output optimization of surface roughness, cutting force, and tool life and power consumption using Taguchi method with logical fuzzy reasoning. Machining parameters considered for the CNC
turning of AISI P-20 tool steel were cutting speed, depth of cut, feed, nose radius and cutting environment. Optimum cutting speed, feed, depth of cut and nose radius obtained were 160m/min, 0.1 mm/rev, 0.2 mm and 0.8 mm respectively. Cryogenic environment was found to be reducing surface roughness, power consumption and cutting force and increasing tool life.
Chorng-Jyh Tzeng et al [9] optimized surface roughness for CNC turning process using Taguchi method and grey relational analysis method. Experimentation was carried out on SKD 11 by taking four influencing parameters namely cutting speed, feed, depth of cut and cutting fluid ratio. Depth of cut was found to be the most significant factor in the optimization of roughness average. Cutting speed was the most influencing factor in the case of roughness maximum.
Aman Aggarwal et al [10] carried out multi response optimization of CNC turning of AISI P-20 tool steel using response surface methodology and desirability function. Tool life, surface roughness, cutting force and power consumption were used as the responses for optimization by taking cutting speed, depth of cut, feed and nose radius as parameters. Experimentation was carried out by using liquid nitrogen as coolant.
M.Nalbant et al [11] investigated the effect of insert radius, feed rate, and depth of cut on surface roughness in turning of AISI 1030 steel using TiN coated tools. Taguchi method was used to obtain the optimal parameters in the turning process. Orthogonal array, signal to noise ratio and analysis of variance were used to obtain the performance characteristics. Insert radius followed by feed rate were the significant parameters in the optimization of surface roughness.
Hamdi Aouici et al [12] carried out the optimization of surface roughness and cutting force components in the hard turning of AISI H11 steel. The effects of cutting speed, feed rate, depth of cut and work piece hardness were experimentally investigated taking surface roughness and cutting force components as responses. Response surface methodology was used for mathematical modelling and optimization of responses. The study showed that feed rate and work piece hardness are the significant factors effecting surface roughness. The feed force and the cutting force are strongly influenced by the depth of cut whereas the cutting speed had very small influence.
Ilhan Asilturk et al [13] analyzed the effect of cutting speed, feed and depth of cut on surface roughness in the CNC turning of AISI 304 austenitic stainless steel using coated carbide insert under dry condition. Taguchi based response surface analysis were used for the optimization of surface roughness (both Ra and Rz). Mathematical modelling of the surface roughness as a function of cutting parameters was carried out using response surface methodology. Feed rate is the dominant factor affecting surface roughness, which is minimized when the feed rate and depth of cut are set to the lowest level, while the cutting speed is set to the highest level.
D. Philip Selvaraj et al [14] carried out optimization of two different grades of nitrogen alloyed duplex stainless steel by using Taguchi method. Machining were performed using TiC and TiCN coated carbide cutting tool inserts. Surface roughness, cutting force and tool wear were taken as the
response. Variation of these responses with respect to cutting speed and feed rate were studied at constant depth of cut by using signal to noise ratio and analysis of variance. Analysis showed that surface roughness and cutting force were significantly influenced by feed rate, whereas the tool wear was significantly influenced by cutting speed. Three levels and three factors design were used for experimentation.
Rajesh Kumar Bhushan [15] analyzed and carried out optimization of Al alloy-SiC composites for minimum tool wear and maximum material removal rate using tungsten carbide tool. Response surface methodology was used for optimization by taking cutting speed, depth of cut, feed rate and nose radius as cutting parameters. Optimum cutting parameters obtained for multi objective optimization were 210 m/min, 0.16mm/rev, 0.42 mm and 0.40 mm for cutting speed, feed, depth of cut and nose radius respectively.
Ashok Kumar Sahoo et al [16] carried out optimization of process parameters in turning of AISI 1040 steel. Taguchi method was used for optimization. Experimentation was carried out under dry condition using coated carbide insert. Surface roughness and material removal rate were optimized by taking cutting speed, depth of cut and feed as the parameters of optimization. Cutting speed and depth of cut were found to be the most and the least significant parameters respectively while considering the surface roughness.
K Sharavanakumar et al [17] used genetic algorithm for optimizing surface roughness and material removal rate in turning of Inconel 718. Mathematical modelling was done to show the influence of cutting speed, feed and depth of cut on surface roughness and material removal rate.
K Vijayakumar et al [18] applied ant colony algorithm for solving multi-pass turning optimization problems. The machining parameters were determined by minimizing the unit production cost, subject to various practical machining constraints. The optimum cutting speed and feed obtained were 103.05 m/min and 0.9 mm/rev for roughing cut and
162.02 m/min and 0.24 mm/rev for finishing cut respectively. It was found, by comparing the obtained unit cost of 1.6262$ with that obtained in genetic algorithm and simulated annealing, that ant colony algorithm performed better than other two.
-
urairaj and S.Gouri [19] carried out the optimization of CNC micro turning of Inconel 600 alloy with titanium carbide coated tool. Optimization of surface roughness and tool life were carried out using genetic algorithm. Cutting speed, feed and depth of cut were taken as the influencing parameters in the optimization of response. Surface finish was found to be better at lower values of cutting speed, feed and depth of cut.
Ramon Quiza Sardinas et al [20] carried out multi objective optimization of tool life and operation time by using Genetic Algorithm. Cutting speed, feed, depth of cut were taken as the influencing parameters in the optimization.
From the literature review it was found that lot of work has been done in the field of turning for modelling analysis and optimization. Various optimization techniques were found to be used for finding the optimal parameters. Teaching learning based optimization is a recently developed population based optimization technique which is not found to be used for optimizing responses such as surface roughness, material
removal rate etc. Also teaching learning based optimization seems to perform better than other optimization algorithms. Hence the objective of the present work is the application of this method in turning process. Surface roughness and material removal rate are considered here.
-
-
EXPERIMENTAL SET UP AND DATA COLLECTION
The machine which is used for performing the hard turning operation is shown in the Fig.1. The specification of the CNC machine used for experiment is described in Table I. Cutting tool used for the experimentation is coated tungsten carbide insert of specification DNMG150608. The specification of the tool holder is PDJNL 2020K10. Work piece used for experimentation is AISI 1040 mild steel bar of 60mm length and 25 mm diameter
TABLE I.CNC MACHINE SPECIFICATION
Type of Bed |
450slant |
Maximum distance between centers |
460 mm |
Spindle Speeds |
100-3000 RPM |
Spindle nose |
A2 -5 |
Longitudinal feed range |
1-5000 mm/min |
Cross feed range |
1-5000 mm/min |
Power of Spindle drive motor |
5.5 Kw |
Turning tool shank size |
20×20 mm |
Maximum spindle torque |
73 Nm |
Fig.1.CNC Machine used for experiment
In this study, spindle speed(s), feed (f) and depth of cut(d) have been considered as process variables. The working ranges of these parameters were selected for subsequent design of experiment using response surface methodology. The process variables with their units are listed in Table.II.
TABLE.II. PROCESS VARIABLES AND THEIR LIMIT
Levels |
Process parameters |
||
Spindle speed(rpm) |
Feed(mm/rev) |
Depth of cut(mm) |
|
1 |
800 |
0.05 |
0.6 |
2 |
1200 |
0.10 |
1.0 |
3 |
1600 |
0.15 |
1.4 |
For deriving clear and accurate conclusions from the experimental observations, designs of experiments are very useful. Response surface methodology based design was used for studying the influence of the three process parameters on the responses. Central composite design was preferred in this case. Here the experiments are carried out at three different levels using MINITAB 16 software.Total number of experiments done is 20 and the workpieces of which is shown in Fig.2.
.
Fig.2. Work pieces used for experiment
Material removal rate (MRR) measurement was done by measuring the weight before and after the machining is performed. MRR can be expressed either in mm3/min or in gm/min. Here gm/min is used for MRR calculation. Roughness measurement has been done using a portable stylus-type surface roughness tester is the SJ-210 model of Mitutoyo make shown in Fig.3.It is a shop-floor type surface roughness-measuring instrument, which traces the surfaces of various machine parts, calculates their surface roughness based on roughness standards and displays the results
TABLE.III. Data collected from Experiments
Expt.N o. |
s |
f |
d |
Ra |
Rq |
Rz |
MRR |
1 |
800 |
0.05 |
0.6 |
2.24 |
2.74 |
12.97 |
9.86 |
2 |
800 |
0.05 |
1.4 |
2.52 |
3.12 |
14.57 |
30.33 |
3 |
1200 |
0.10 |
1.4 |
1.28 |
1.63 |
8.161 |
85.96 |
4 |
1200 |
0.1 |
0.6 |
3.35 |
4.10 |
18.02 |
29.18 |
5 |
800 |
0.15 |
0.6 |
4.68 |
5.83 |
26.17 |
28.49 |
6 |
1200 |
0.1 |
1.0 |
1.66 |
2.11 |
10.51 |
51.92 |
7 |
1200 |
0.05 |
1.0 |
2.10 |
2.57 |
11.87 |
32.88 |
8 |
1600 |
0.05 |
1.4 |
1.83 |
2.38 |
11.95 |
54.97 |
9 |
1200 |
0.1 |
1.0 |
1.65 |
2.05 |
9.799 |
57.97 |
10 |
1600 |
0.05 |
0.6 |
3.47 |
4.23 |
18.38 |
27.36 |
11 |
1200 |
0.1 |
1.0 |
1.09 |
1.45 |
7.641 |
64.14 |
12 |
1200 |
0.15 |
1.0 |
1.63 |
2.08 |
10.64 |
70.90 |
13 |
1200 |
0.1 |
1.0 |
2.03 |
2.50 |
11.84 |
52.27 |
14 |
1200 |
0.1 |
1.0 |
1.19 |
1.47 |
7.474 |
63.95 |
15 |
1200 |
0.1 |
1.0 |
1.49 |
1.82 |
8.438 |
59.76 |
16 |
800 |
0.1 |
1.0 |
3.61 |
4.44 |
19.27 |
39.09 |
17 |
800 |
0.15 |
1.4 |
2.00 |
2.50 |
11.89 |
97.79 |
18 |
1600 |
0.15 |
0.6 |
2.66 |
3.26 |
14.66 |
67.92 |
19 |
1600 |
0.15 |
1.4 |
1.32 |
1.60 |
7.622 |
160 |
20 |
1600 |
0.1 |
1.0 |
1.68 |
2.09 |
9.808 |
76.82 |
IV MATHEMATICAL MODELLING
The relationship between the factors and the performance measures were modelled by quadratic regression. Regression coefficients were obtained using experimental data. Mathematical modelling refers to obtaining equation connecting response and influencing parameters. These equations are required for the optimization of the responses such as surface roughness and material removal rate. Response surface methodology based regression equations of the four responses as a function of the input parameters (spindle speed, feed and depth of cut) are as shown below.
The regression equation for surface roughness parameter Ra is
The regression equation for surface roughness parameter Rq is
Fig.3.Roughness measurement
Twenty specimens of same dimensions are prepared first. After that the weight of each specimen is measured using digital balance meter. Then specimen is turned at different speed, feed and depth of cut according to the design of experiment. Again the weight is measured for finding the material removal rate After that the roughness parameters are measured using surface roughness tester SJ210.Three roughness parameters Ra, Rq, Rz are measured for each specimen at three different locations and the average value is taken. Data collected are shown in TABLE III
The regression equation for surface roughness Rz is
The regression equation for material removal rate is
In the above equation s, f and d refers to spindle speed, feed
and depth of cut respectively. The obtained regression equation is further used for optimization using both TLBO These objective equations of Ra, Rq, Rz and MRR are optimized using lower and upper limits as shown below.
For spindle speed, 800 1600
For feed, 0.05 0.15
For depth of cut, 0.6 1.4
V OPTIMISATION USING TEACHING LEARNING BASED OPTIMISATION (TLBO)
Teaching-learning-based optimization is based on teaching- learning process in which every learner tries to learn something from other individuals to improve themselves. This algorithm simulates the traditional teaching-learning phenomenon of a class room [3]. Here, two different teachers, T1 and T2 are assumed teaching same subject to the same merit level students in two different classes. The distribution of marks obtained by the learners of two different classes taught by two different teachers are shown in the Fig.4.
Fig.4.Distribution of Marks Obtained By Learners [3]
Curves 1 and 2 represent the marks obtained by the learners taught by teacher T1 and T2 respectively. A normal distribution is assumed for the obtained marks. The normal distribution is defined as
where 2 is the variance, is the mean and x is any value for which the normal distribution function is required. It is seen from Fig.1.12 that curve-2 represents better results than curve-1 and so it can be said that teacher T2 is better than teacher T1 in terms of teaching. The main difference between both the results is their mean (M2 for Curve-2 and M1 for Curve-1), i.e. a good teacher produces a better mean for the results of the learners. Learners also learn from interaction between themselves, which also helps in their results.
Based on the above teaching process, Rao et al [3] developed a mathematical model and implemented for the optimization of an unconstrained non-linear continuous function, thereby developing a novel optimization technique called Teaching Learning-Based Optimization (TLBO).
Like other nature-inspired algorithms, TLBO is also a population based method that uses a population of solutions to proceed to the global solution. For TLBO, the population is considered as a group of learners or a class of learners. In
optimization algorithms, the population consists of different design variables. In TLBO, different design variables will be analogous to different subjects offered to learners and the learners result is analogous to the fitness, as in other population-based optimization techniques. The teacher is considered as the best solution obtained so far. The process of TLBO is divided into two parts. The first part consists of the Teacher Phase and the second part consists of the Learner Phase. The Teacher Phase means learning from the teacher and the Learner Phase means learning through the interaction between learners
A good teacher brings his or her learners up to his or her level in terms of knowledge. But in practice this is not possible and a teacher can only move the mean of a class up to some extent depending on the capability of the class. This follows a random process depending on many factors. Learners increase their knowledge by two different means: one through input from the teacher and the other through interaction between themselves. A learner learns something new if the other learner has more knowledge than him or her.
Teaching learning based optimization was done by using the experimental data and mathematical modelling which were considered earlier. Optimization performance of teaching learning based optimization was checked using MATLAB R2013a by using computer code. Parameters of optimization were population size=20 and number of generation=100.
VI RESULTS AND DISCUSSION
In the present study, TLBO algorithm is used for finding the optimal process parameters for minimizing surface roughness and maximizing material removal rate in CNC turning process. The results of the optimization are listed in Table IV.
TABLE.IV. RESULT OPTISATION BY TLBO
Response |
Optimum value |
Spindle speed (rpm) |
Feed (mm/rev) |
Depth of cut (mm) |
Ra |
0.61872 |
1457.2753 |
0.15 |
1.4 |
Rq |
0.78152 |
1464.5964 |
0.15 |
1.4 |
Rz |
4.62130 |
1488.0655 |
0.15 |
1.4 |
MRR |
156.1929 |
1600 |
0.15 |
1.4 |
Teaching learning based optimization algorithm can be used for other conventional and non-conventional machining processes to obtain the optimal process parameters. There is further scope for research on this recently developed optimization technique as less work has been reported on this optimization technique.
REFERENCES
-
Indrajit Mukherjee, Pradip Kumar Ray, A review of optimization techniques in metal cutting processes, Computers & Industrial Engineering 50 (2006) 1534.
-
Norfadzlan Yusup, Azlan Mohd Zain, Siti Zaiton Mohd Hashim, Evolutionary techniques in optimizing machining parameters: Review and recent applications (20072011), Expert Systems with Applications 39 (2012) 99099927.
-
Rao R.V, Savsani V.J, Vakharia D.P, TeachingLearning-Based Optimization: An optimization method for continuous non-linear large scale problems, Information Sciences 183 (2012) 115.
-
Rao R.V., Savsani V.J. and Vakharia D.P., Teachinglearning-based optimization: A novel method for constrained mechanical design optimization problems, Computer-Aided Design, 43 (2011): 303 315.
-
Erik Oberg, Franklin D. Jones, Holbrook L. Horton, Henry H. Ryffel., Machinerys Handbook , 26th edition, Industrial Press Inc. New York, 2000.
-
D.C. Montgomery, Design and Analysis of Experiments, fifth ed., John Wiley & sons Inc.
-
Ashvin J. Makadia, Nanavati J.I, Optimisation of machining parameters for turning operations based on response surface methodology, Measurement 46 (2013) 1521-1529.
-
Anil Gupta, Hari Singh, Aman Aggarwal, Taguchi-fuzzy multi output optimization (MOO) in high speed CNC turning of AISI P-20 tool steel, Expert Systems with Application 38 (2011) 6822-6828.
-
Chorng-Jyh Tzeng, Yu-Hsin Lin, Yung-Kuang Yang, Ming-Chang Jeng, Optimization of turning operations with multiple performance characteristics using the Taguchi method and Grey relational analysis, Journal of Materials Processing Technology 209(2009) 27532759.
-
Aman Aggarwal, Hari Singh, Pradeep Kumar, Manmohan Singh, Optimization of multiple quality characteristics for CNC turning under cryogenic cutting environment using desirability function, Journal of Materials Processing Technology 205(2008) 4250.
-
Nalbant. M, Gokkaya. H, Sur. G, Application of Taguchi method in the optimisation of cutting parameters for surface roughness in turning, Materials and Design 28(2007) 1379-1385.
-
Hamdi Aouici, Mohamed Athmane Yallese, Kamel Chaoui, Tarek Mabrouki, Jean-Francois Rigal, Analysis of surface roughness and cutting force components in hard turning with CBN tool: Prediction model and cutting conditions optimization, Measurement 45 (2012) 344-353.
-
Ilhan Asilturk, Suleyman Neseli, Multi response optimistion of CNC turning parameters via Taguchi method-based response surface analysis, Measurement 45 (2012) 785-794.
-
Philip Selvaraj. D, Chandramohan P, Mohanraj. M, Optimization of surface roughness, cutting force and tool wear of nitrogen alloyed duplex stainless steel in a dry turning process using Taguchi method, Measurement 49(2014) 205-215.
-
Rajesh Kumar Bhushan, Multiresponse Optimization of Al Alloy- SiC Composite Machining Parameters for Minimum Tool Wear and Maximum Metal Removal Rate, Journal of Manufacturing Science and Engineering, (2013), Vol. 135 / 021013-1
-
Ashok Kumar Sahoo, Achyuta Nanda Baral, Arun Kumar Rout, B.C.Routra, Multi-objective Optimization and Predictive Modelling of Surface Roughness and Material Removal Rate in Turning using Grey Relational and Regression Analysis, Procedia Engineering 38(2012) 1606-1627.
-
Saravanakumar. K, Pratheesh Kumar M.R, Shaik Dawood. A K, Optimization of CNC Turning Process Parameters on INCONEL 718 Using Genetic Algorithm, IRACST Engineering Science and Technology: An International Journal (ESTIJ), ISSN: 2250-3498, Vol.2, No. 4, (2012), 532-537.
-
Vijayakumar K, Prabhaharan G, Asokan P, Saravanan R, Optimization of multi-pass turning operations using ant colony system, International Journal of Machine Tools & Manufacture 43 (2003) 16331639.
-
Durairaj M, Gouri. S, Parametric Optimisation for Improved Tool Life and Surface Finish in Micro Turning using Genetic Algorithm, Procedia engineering 64(2013) 878-887.
-
Ramon Quiza Sardinas, Marcelino Rivas Santana, Eleno Alfonso Brindis, Genetic algorithm-based multi-objective optimization of cutting parameters in turning processes, Engineering Applications of Artificial Intelligence 19 (2006) 127133. K. Elissa, Title of paper if known, unpublished.