
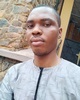
- Open Access
- Authors : I.U. Onyenanu , S. C. Nwigbo
- Paper ID : IJERTV10IS070295
- Volume & Issue : Volume 10, Issue 07 (July 2021)
- Published (First Online): 07-08-2021
- ISSN (Online) : 2278-0181
- Publisher Name : IJERT
- License:
This work is licensed under a Creative Commons Attribution 4.0 International License
Optimization of Aluminium Metal Matrix Composite (AMMC) for use in Automobile Brake Disc
1I.U. Onyenanu, 2S. C. Nwigbo
PhD
1,2Department of Mechanical Engineering, Nnamdi Azikiwe University, Awka Nigeria.
Abstract – This work presents the optimisation of aluminum metal matrix composite for vehicle disc brake. Research so far have shown aluminum metal matrix composite (AMMC) potentials in development of vehicle brake disc; however, the need to optimize the matrix and determine the best ratio is imperative which forms the bases of this work. A systematic approach was adopted for the work which cuts across developing an experiment using the design expert software 11.0 to producing the sample specimen using the stir casting technique while the optimum specimen sample was gotten using the D-Optimal mixture method of optimisation. Furthermore, the physical, chemical, and mechanical properties of the Aluminium Silicon Carbide composite (i.e., Al-SiC/ MMC). From the result of the optimisation, Silicon Carbide has great influence on the various mechanical properties conducted while graphite had effect on the wear rate. Again, magnesium tends to reduce porosity from the microstructural examination of the Aluminium metal matric composite (AMMC). The result of the research will give insight to industries who intends to utilize Aluminium metal matric composite (AMMC) for the development of the vehicle brake discs.
Keywords – Composite; Metal Matrix Composite (MMC), Disc Brake, Aluminium Metal Matrix Composite (AMMC), Brake.
I. INTRODUCTION
A brake is a mechanical device that inhibits motion by absorbing energy from a moving system. It is used for slowing or stopping a moving vehicle, wheel, axle, or to prevent its motion, most often accomplished by means of friction. In the method of performing this function, the brakes take in both kinetic strength of the moving member or the potential energy given up with the aid of items being reduced by way of hoists, elevators and so forth. The energy absorbed by using brakes is dissipated in the form of heat [22], [3]. This heat is dissipated in to the surrounding atmosphere to stop the vehicle, so the brake system should have the following requirements: The brakes must be strong enough to stop the vehicle with in a minimum Distance in an emergency. The driver must have proper control over the vehicle during braking and the vehicle must not skid. The brakes must have good ant fade characteristics i.e., their effectiveness should not decrease with constant prolonged application. The brakes should have good anti-wear properties [22], [3], [20]. However, without brake system, the vehicle will put a passenger in unsafe position. Therefore, it is a must for all vehicles to have proper brake.
Generally, the disc brake is a wheel brake which slows rotation of the wheel by the friction caused by pushing brake pads against a brake disc with a set of calipers. The brake disc is connected to the wheel and/or the axle. To stop the wheel, friction material in the form of brake pads, mounted on a device called a brake caliper, is forced mechanically, hydraulically, pneumatically or electromagnetically against both sides of the disc. Friction cause the disc and attached wheel to slow or stop. Brakes convert motion to heat, and if the brakes get too hot, they become less effective, a phenomenon known as brake fade. The brake disc (or rotor in American English) is usually made of cast iron. However, to reduce automobile weight and improve fuel efficiency, the auto industry has dramatically increased the use of aluminum in light vehicles in recent years. These materials having a lower density as compared to the conventionally used gray cast iron are expected to the results in weight reduction of up to 50-60 % in brake system. Moreover, these advanced materials have the potential to perform better under severe service conditions like higher speed, higher load etc. which are increasingly being encountered in modern automobiles.
In this work, an Aluminium matrix composite reinforced with silicon carbide will be developed for automobile brake disc. Then, optimization will be conducted on the samples using the D-Optimal Mixture Design to investigate the effect of the additives on the mechanical properties of the materials developed.
-
LITERATURE REVIEW
-
Aluminum Silicon Carbide (Al-SiC) Alloy Matrix for Disc Brake
Al-Si alloy is considered as a framework material on account of its gigantic properties like high wear resistance, low warm extension coefficient, great consumption resistance, and enhanced mechanical properties at an extensive variety of temperatures [14]. Aluminum silicon composites are the most vital and generally utilized throwing combinations to cast parts with complex shapes in light of simple castability and great bargain between mechanical properties and gentility. The use of aluminum compounds is likewise generally utilized as a part of car division which prompt financially supportable advancements [1].
The aluminum silicon alloy properties were impacted by the shape and conveyance of the eutectic silicon particles in
the matrix, furthermore by the iron inter metallic and copper stages that happen upon solidification remarked by [1]. The part of Fe, Mn, Cu, and Mg substance was touchier to varieties in microstructure and malleable properties of Al Si close – eutectic compound. The use of Al-SiC matrix in manufacture of vehicle brake disc is increasing due to its potential mechanical properties it exhibits.
-
Reviews on Disc Brake
B. Metal Matrix Composite (AMMC) Design Formulation
To develop an optimal mix for the sample, a mixture design which is a specialized form of the surface response method (RSM) was employed. For the purpose of this design, an Aluminium Metal Matrix Composite (AMMC) was refomulated to fine tune three product attribute which are measured as responses from a design experiment.
-
Response 1: The Hardness (BHN)
-
Response 2: Tensile Strength (MPa)
-
Response 3: Wear Rate (J/m3)
Three primary components vary as shown:
-
10% A (Silicon Carbide – SiC) 13%
-
2% B (Graphite) 2.5%
-
1% C (Magnesium – Mg) 2%
These components represent a total of sixteen (16) weight- percent of the total formulation, that is: A + B + C = 16%
Other materials (held constant) will make up the difference: 84 weight-percent of the Aluminum Metal Matrix Composite (AMMC). These includes; 2 weight-percent Aluminum Oxide (Al2O3) and the chief constituent 82 weight-percent Aluminum Alloy (Al 6061). For purposes of this experiment, they are ignored.
After the design of experiment formulation for the Aluminium Metal Matrix Composite (AMMC), the data generated was now utilized to for the development of the Table for the various samples. Table 2 shows the various sample description and the weight-percent that they constitute.
ID
Nature of Composite
Al 6061
(%wt.)
SiC 34
(%wt.)
Graphite 45
(%wt.)
Mg (%wt.)
Al2O3
(%wt.)
A
Hybrid
82
11.95
2.05
1.00
2
B
Hybrid
82
10.23
3.00
1.77
2
C
Hybrid
82
11.09
2.51
1.40
2
D
Hybrid
82
10.52
2.47
2.00
2
E
Hybrid
82
11.27
2.00
1.73
2
F
Hybrid
82
11.53
2.47
1.00
2
G
Hybrid
82
11.06
2.94
1.00
2
H
Hybrid
82
20
–
–
–
ID
Nature of Composite
Al 6061
(%wt.)
SiC 34
(%wt.)
Graphite 45
(%wt.)
Mg (%wt.)
Al2O3
(%wt.)
A
Hybrid
82
11.95
2.05
1.00
2
B
Hybrid
82
10.23
3.00
1.77
2
C
Hybrid
82
11.09
2.51
1.40
2
D
Hybrid
82
10.52
2.47
2.00
2
E
Hybrid
82
11.27
2.00
1.73
2
F
Hybrid
82
11.53
2.47
1.00
2
G
Hybrid
82
11.06
2.94
1.00
2
H
Hybrid
82
20
–
–
–
Table 2: Various sample description and their weight-percent
-
-
METHODOLOGY
A. Material
The material and equipment used during the course of this work are listed as follows: Aluminum Oxide (Al2O3), Silicon Carbide (SiC), Graphite, Magnesium (Mg) and Aluminum bars. Table 1 below shows the categories of the brake disc material. Then, the material descriptions used to obtain the characteristics which are closed to the requirement are explained below.
Table 1: Showing the categories of brake disc material.
S/N
Brake pad material
Material choice
1
Base Metal
Aluminium Alloy 6061
2
Reinforcement
Silicon Carbide
3
Wetting Agent
Magnesium
4
Friction modifiers
Graphite
5
Abrasive
Aluminum oxide
(Source: Joshi et. al, 2016)
-
Sample Preparation Procedures
For the purpose of this work, a total of eight (8) samples designated with the sample ID as shown in Table 2 are to be prepared. The procedures for preparing these compositions are as follows;
Aluminium alloy bars are cleaned to remove dust particles, weighed and then charged in the crucible for melting. Then, the reinforcement powder (Silicon carbide) and magnesium powder are weighed on the weighing machine (See Table 2 above for their different weight fractions), after which they would be pre heated for 45 minutes at a temperature 5000C. When the matrix would be in the semisolid stage condition at 6500C, pure magnesium powder is used as wetting agent. Again, the heater temperature is then increased to 8500C. At
this heater temperature, stirring is started and continued for five minutes. Stirring rpm is gradually increased from 0 to 300 RPM with the help of speed controller. The preheated reinforcements are added during five minutes of stirring. Reinforcements would be poured manually with the help of conical hopper. Afterwards, the stirrer rpm is then gradually lowered to the zero. Then molten composite slurry is poured in mould without giving time for reinforcement to settle down at crucible bottom. The mould is preheated at 2200C temperature for one hour before pouring the molten slurry in the mould. This is necessary to maintain slurry in molten condition throughout the pouring. Finally, the mould is then allowed to cool and after cooling runner, riser is removed from disc. Final finishing would be done using the lathe and milling machine to achieve dimensional accuracy. This procedure was repeated for all the samples with the ID (A-K).
For the sample H which is a binary matrix, after charging the aluminum bars in a crucible for melting, the reinforcement powder (Silicon carbide) would be weighed, after which they would be pre heated for 45 minutes at a temperature 5000C. The heater temperature is then increased to 8500C. At this heater temperature, stirring is started and continued for five minutes. Stirring rpm is gradually increased from 0 to 300 RPM with the help of speed controller. The preheated reinforcements are added during five minutes of stirring. Reinforcements would be poured manually with the help of conical hopper. Afterwards, the stirrer rpm is then gradually lowered to the zero. Then other processes would be observed as stated above.
-
Mechanical Tests of Sample
Various test will be conducted on the AMMC material samples developed. These tests will be done to verify the mechanical properties of the sample. For the purpose of this work, three (3) tests are scheduled to be conducted. They include; Hardness, Tensile/ Compression, Wear rate. It may be noted that each specimen was prepared and tested according to international standard (i.e., ASTM).
-
Optimization using the D-Optimal Mixture Design
D-Optimal mixture design was used to determine the optimum amount of material formulation toward the responses, which are hardness, tensile strength and wear rate of the Aluminium Metal Matrix Composite. The statistical parameters used in evaluating and selecting the best-fitted model are coefficient of determination (R2), adjusted coefficient of determination (adjusted R2), predicted coefficient of determination (predicted R2), coefficient of variation (C.V.), standard deviation, predicted residual sum of squares (PRESS), lack-of-fit, and regression data (P- value and F- value). The statistical analysis also constructs an equation from the best-fitted model. From the equation, the positivity of the coefficient presents the positive contribution toward the response, and vice versa. Also, a contour plot and three-dimensional response surface graph for each response were generated by Design-Expert Software Version 11.0 for a better explanation. The results generated from the optimization can be seen in result and discussion section.
-
-
RESULTS AND DISCUSSION
The result of this study was group into seven (3) different parts; results of the physical and chemical properties of the Aluminum alloy rod sample the optimization result of the experiment showing the predicted values and the actual values utilizing the coded equations, then the effect of the additives on the response. These results can be seen below;
-
Physical and Chemical properties of the Materials Used
To be certain of the particular composition and grade of Aluminum alloy that was utilized for this investigation, the Aluminum bars were subjected to physical, chemical and mechanical properties test. Table 3 presents the chemical composition of the Aluminum sample specimen. The samples were melted and produced at Kaiser Aluminum fabricated products, USA and the production. The certificate can be verified at http://Online.KaiserAluminium.com
Table 3: Chemical Composition (wt%)
Limits
Maximum
Si
0.80
Fe
0.70
Cu
0.40
Mn
0.15
Mg
1.20
Cr
0.35
Zn
0.25
Ti
0.15
Pb
NA
Bi
NA
Zr
NA
Ea
0.05
Tot
0.15
-
Optimization Analysis using Response Surface Methodology (RSM)
Preliminary study on Al-SiC/ MMC brake disc formulation was done by investigating the components that made up the disc material. Four excipients were chosen for Al-SiC/ MMC formulation based on their function. Three of them and Alumina were used as variables in D-optimal mixture design as they may have effect on the responses. The ranges of variables were also studied by using D-optimal mixture in design expert software. Table 4 shows the summary data table of the actual design after experiment.
Component 1
Component 2
Component 3
Response 1
Response 2
Respons
Run
A: Magnesium
B: Silicon Carbide
C: Graphite
Hardness
Tensile
Wear Ra
%
%
%
HV
N/mm2
mg/m
3
1.39085
9.60915
2
291
381
0.93
4
1.39085
9.60915
2
291
381
0.93
2
1
8.97885
3.02115
320
392
0.37
9
1
8.97885
3.02115
320
392
0.37
1
2
8.48946
2.51054
285
377
1.06
5
1.55336
7.74111
3.70554
278
361
1.13
7
1.55336
7.74111
3.70554
278
361
1.13
11
1.55336
7.74111
3.70554
278
361
1.13
10
1.13614
6.86386
5
240
347
1.43
8
2
6.80043
4.19957
213
293
1.85
6
2
6
5
201
269
2.25
Component 1
Component 2
Component 3
Response 1
Response 2
Respons
Run
A: Magnesium
B: Silicon Carbide
C: Graphite
Hardness
Tensile
Wear Ra
%
%
%
HV
N/mm2
mg/m
3
1.39085
9.60915
2
291
381
0.93
4
1.39085
9.60915
2
291
381
0.93
2
1
8.97885
3.02115
320
392
0.37
9
1
8.97885
3.02115
320
392
0.37
1
2
8.48946
2.51054
285
377
1.06
5
1.55336
7.74111
3.70554
278
361
1.13
7
1.55336
7.74111
3.70554
278
361
1.13
11
1.55336
7.74111
3.70554
278
361
1.13
10
1.13614
6.86386
5
240
347
1.43
8
2
6.80043
4.19957
213
293
1.85
6
2
6
5
201
269
2.25
Table 4: Summary of the Design table for the optimization
-
Predicted and Actual Results for the three (3) Responses
For Wear Rate;
Utilizing the design expert software, optimization was conducted on experimental design table. The coded equations were generated on each case and utilized to calculate the predicted values of the experiment. Fig. 1 shows the graphical representation of the predicted and actual values of the experiment. The graph confirms a high similarity for the predicted and actual values for the wear rate experiment.
Figure 1: Predicted and actual values for the wear rate
For Tensile Strength;
Figure 2 shows the graphical representation of the predicted and actual values of the Tensile strength experiment. Again, the graph confirms a high similarity for the predicted and actual values for the wear rate experiment.
Figure 2: Predicted and actual values for the Tensile Strength
For Hardness Value;
Fig. 3 shows the graphical representation of the predicted and actual values of the Hardness value from the experiment. Again, the graph confirms a high similarity for the predicted and actual values for the wear rate experiment.
Figure 3: Predicted and actual values for the Hardness
-
Effect of the Additives on the Response
From the result generated showing the contour diagram of relationship between three variables, i.e., percentage of magnesium (A), percentage of silicon carbide (B) and percentage of graphite (C), and with last component being aluminum oxide (%) to the wear rate of the Al-SiC/ MMC of the brake disc (Figure 4), it can be inferred that the value of the correlation coefficient (r) is about 0.769 for B while it is
0.385 at A and then 0.462 at C. This shows that Silicon Carbide contribute more in terms of wear resistance for the material developed. Figure 4 shows the 3D surface plot of relationship between three variables to the wear rate of the Al-SiC/ MMC of the brake disc.
Figure 4: 3D diagram of relationship between three variables to the wear rate of the Al-SiC/ MMC of the brake disc.
Again, from the result generated showing the contour diagram of relationship between three variables, i.e., percentage of magnesium (A), percentage of silicon carbide
(B) and percentage of graphite (C), and with last component being aluminum oxide (%) to the tensile strength of the Al- SiC/ MMC of the brake disc (Figure 5), it can be inferred that the value of the correlation coefficient (r) is about 0.77 for B while it is 0.39 at A and then 0.46 at C. This shows that Silicon Carbide contribute more in terms of wear resistance for the material developed. Figure 5 shows the 3D surface
plot of relationship between three variables to the tensile strength of the Al-SiC/ MMC of the brake disc.
Figure 5: 3D diagram of relationship between three variables to the Tensile strength of the Al-SiC/ MMC of the brake disc.
Finally, from the result generated showing the contour diagram of relationship between three variables, i.e., percentage of magnesium (A), percentage of silicon carbide
(B) and percentage of graphite (C), and with last component being aluminum oxide (%) to the Hardness of the Al-SiC/ MMC of the brake disc (Figure 6), it can be inferred that the value of the correlation coefficient (r) is about 0.77 for B while it is 0.39 at A and then 0.46 at C. This shows that Silicon Carbide contribute more in terms of wear resistance for the material developed. Figure 6 shows the 3D diagram of relationship between three variables to the tensile strength of the Al-SiC/ MMC of the brake disc.
Figure 6: 3D diagram of relationship between three variables to the Tensile strength of the Al-SiC/ MMC of the brake disc.
-
-
CONCLUSION
Through the execution of the proposed top-down development methodology, the optimisation of Aluminum Silicon Carbide Metal Matrix Composite for vehicle brake disc (Al-SiC/ MMC) is investigated. The proposed
methodology tackled the brake disc development through two major phases; they are physical, mechanical and chemical properties investigation of material, optimization of experimental samples using the D-Optimal method. With detailed and in-depth parametric investigation, the Al-SiC/ MMC was thoroughly investigated and analyzed. From the results generated, the following conclusions was made;
-
CES GRANTA analysis results showed that Al-SiC is a composite with promising feature for the brake disc industries in Nigeria and beyond.
-
The Energy dispersion spectroscopy (EDS) confirms the presence of the elements utilized for the development of Al-SiC/ MMC sample.
-
D-Optimal method of optimization reveals that the presence of silicon carbide (SiC) had greater effect on the overall mechanical properties of the material than other components added during the investigation.
-
While graphite had effect on the wear rate and the coefficient of the material. Again, magnesium tends to reduce porosity from the microstructural examination of the Aluminium metal matric composite (AMMC).
ACKNOWLEDGMENT
We wish to acknowledge NUTABOLTS Technologies LTD and Scientific Equipment Development Institute both in Enugu State, Nigeria for letting us use her equipment in other to achieve this work.
REFERENCES
-
A.V.S. Gowtham, T. Lakshmana Kishore and M. Komaleswara Rao (2017) Analysis of Spur Gear Using Boron Carbide Particulate Reinforced Lm6 Aluminium Metal Matrix Composite International Journal of Engineering Development and Research, IJEDR | Volume 5,
Issue 4 | ISSN: 2321-9939
-
Balasubramanyam N. and Prasanthi S. G. (2014), Design and Analysis of Disc Brake Rotor for a Two-Wheeler. International Journal of Mechanical and Industrial Technology (IJMIT) Vol. 1, Issue 1, pp: (7- 12), Month: October 2013-March 2014, Available at: www.researchpublish.com.
-
Chengal V.R., Gunasekhar M. R.., and Harinath G.G., (2013). Modeling and Analysis of FSAE Car Disc Brake Using FEM. International Journal of Emerging Technology and Advanced Engineering, Vol 3, Issue 9, page 383-389.
-
Manikandan M.S, Kumar K.V.N., Krishnamoorthi M., and Ganesh V., (2013). Control of Braking Force under Loaded and Empty Conditions on Two-Wheeler. International Journal of Mechanical, Aerospace, Industrial and Mechatronics Engineering Vol:7 No.9.
-
Saheb, N., Laoui, T., Daud, A. R., Harun, M., Radiman, S., & Yahaya,
R. (2001). Influence of Ti addition on wear properties of AlSi eutectic alloys. Wear, 249(8), 656-662.
-
Swapnil R.A. and Bhaskar D.P., (2014). Design and Analysis of Disc Brake. International Journal of Engineering Trends and Technology (IJETT). Vol 8, No 4.
-
Ukwu N.O., Onyenanu I.U. & Atanmo P.N. (2016). Design and Analysis of FSAE Brake System using locally sourced Material. JETIR. February 2016, Volume 3, Issue 2, 82-89.
-
Venkatesh C., Anjaneyulu B. and Rao K. K. (2016), Design and Analysis of Car Disc Brake by Using FEM International Journal for Research in Applied Science & Engineering Technology (IJRASET). Volume 4 Issue XII, IC Value: 13.98 ISSN: 2321-9653.