
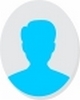
- Open Access
- Authors : P. Pravalika , C. Sai Priya , Dr. D. Govardhan
- Paper ID : IJERTV10IS060288
- Volume & Issue : Volume 10, Issue 06 (June 2021)
- Published (First Online): 28-06-2021
- ISSN (Online) : 2278-0181
- Publisher Name : IJERT
- License:
This work is licensed under a Creative Commons Attribution 4.0 International License
Optimization of Lay-Up Sequence of Composite Laminates Under Tensile and Compressive Loading
P. Pravalika1, C. Sai Priya2, Dr. D. Govardhan3
Research student1, Research student2, Head of the department3,
Department of Aeronautical Engineering, Institute of Aeronautical Engineering, Telangana, India.
Abstract: In this work, the optimization of the lay-up sequence of composite laminates under tensile and compressive loading is carried out by considering various combinations of angles of unidirectional carbon fiber reinforced composite plies. The objective of this work was to develop a model to study and understand the structural response of different layers in the laminate by considering different stacking sequences. The laminate of dimension 100mm*100mm is designed and meshed in Hypermesh 13.0 using quad elements and analyzed at a tensile load of 100N/mm and compressive load of 100N/m in MSC Patran and Nastran software. Two dimensional quad elements are used for meshing the model. Different combinations of stacking sequences are implemented from angles 0,45,60,90. Various symmetric staking configurations such as [0/45/-45/90], [0/45/-45/60] and [0/45/60/90] are considered for an eight-ply laminate and the laminates are modeled for analysis. The laminate thickness was maintained 1mm with each ply having a thickness of 0.125mm. The analysis results for stress and strain in both X and Y directions along with shear stress in XY-plane were plotted. The graphs obtained from the results were plotted using MS-Excel and are compared for the study.
Keywords: Hyper mesh 13.0, MSC Patran, Nastran, stacking sequence.
-
INTRODUCTION
Composite materials are generally the macroscopic combinations of two or more materials and the resultant is macroscopically homogeneous. If well designed, these composite materials exhibit the best qualities of their components which they are used to form and often some qualities that neither of the constituents possesses. The composite materials are well known for their high strength, stiffness per unit weight and lightweight. The four main types of composite materials are Fibrous, Laminated, Particulate and combination of all three.
A single sheet of the resin pre-impregnated tape with fibers aligned in a particular direction is called a ply or a lamina. All the fibers when aligned in one direction are known to be Unidirectional ply and when the fibers are aligned in perpendicular directions are called woven ply.
Fibrous composite materials generally are orthotropic in nature. The direction in which the fibers are laid out is the fiber direction (longitudinal direction) and the matrix direction (transverse direction) is perpendicular to fiber direction.
When more than a single ply is used to form a laminate, then it is known as a layered laminate. In other words, when all plies are of the same composite material and type, and are bonded together as a stack, then such a layered element is called a laminate. A laminate is defined in a system of axes known as Reference axes system. It is a set of mutually perpendicular directions parallel and perpendicular to a reference direction. The reference direction is generally taken coincident with the external loading directions.
The properties of a layered laminate depend on the individual ply properties and stacking sequence in which they are laid. In laminated panels, the plies can be oriented with a predetermined plan to achieve optimum efficiency of strength and stiffness. The lay-up might be from 0° to the axis to 45° or 90°. This design capability coupled with an analysis of operational loading gives unique utility in the design of high-performance material.
-
METHODOLOGY
Modeling and finite element analysis
A surface is created in Hypermesh software with geometry of dimension 100*100 (in mm) as a composite laminate plate. The model was meshed using PCOMP elements. The PCOMP card is used to define the laminate properties like material of the ply, thickness of the ply and ply orientation along with the stacking sequence of the plies.
Fig 2.1 Model
The plate was constrained at the center along the Y-axis and the centroid point of the plate was constrained for all the six DOF.
The composite material considered for the analysis was unidirectional Carbon Fiber Reinforced Polymer (CFRP). The mechanical properties and material strength values of the composite material are given in Table-2.1
Table-2.1 Material properties
The material card with the above properties was created and assigned to the model plate. Different stacking sequences were implemented for the plate model. The laminate ply sequences, individual ply thickness along with the orientations are specified in the hyper laminate under laminate definition.
The extensional stiffness matrix A, coupling stiffness matrix B and bending stiffness matrix D are obtained along with equivalent elastic constants.
The model is then imported to Patran software for further analysis. The load and boundary conditions are specified under Loads/BC. A distributed load of 100N/m and 100N/m was applied in the direction of fiber (X-direction) on either side of the plate for tensile and compressive loading.
The load application regions are then selected on both the edges on the right and left sides of the plate.
Fig 2.2 Loads
A linear static load case is created and linear static analysis is selected. Linear static subcase is selected and element stresses, element strains, displacements along with reaction forces are given as output requests. The bulk data file that is generated due to the analysis is given as an input file for the solver software (Nastran) and is run.
The .xdb file is attached under analysis to access results. Under the results window the linear static subcase is selected and required results such as Stress Tensor, stress invariants, displacements and reaction forces are selected and the results are viewed.
-
RESULT AND DISCUSSION
The results for the stress and strain components along the direction of fiber and direction of matrix (X and Y directions) and shear stress in the XY plane were obtained for every layer of the laminate using Nastran software as a solver. The maximum values of stress and strain of each ply
were considered for plotting the profiles.
The stress in X, Y directions along with shear stress in XY plane for the stacking sequences of [0/0/0/0]s , [45/45/45/45]s , [60/60/60/60]s and [90/90/90/90]s for an 8 ply symmetric composite laminate are obtained and the stress profiles are plotted as shown in the figures below.
Graph 3.1 Stress in X-Direction
The symmetric 8 ply laminate with ply angle orientations of 0° has shown maximum stress in X-direction (direction of fiber) and the laminate with 90° orientations has shown the least X-direction stress value when compared to other laminates as shown in the graph. 3.1.
On the other hand, the stress in Y-direction (direction of matrix) was found to be least in the laminate with 0° ply orientations and maximum in the laminate with 90° ply orientations when compared to other laminates as shown in the graph.3.2.
Graph 3.2 Stress in Y-Direction
Graph 3.3 Strain in X-Direction
The strain in X-direction was found to be high for laminate with ply orientations of 0° and low for 90° ply-oriented laminate when compared to other laminates as shown in the graph. 3.3. The strain value in Y-direction was found to be higher for laminate with 90° ply orientations and lower for 0° ply laminate when compared to other laminate as shown in the graph 3.4.
Graph 3.4 Strain in Y-Direction
Graph 3.5 Shear Stress in XY Plane
The shear stress was found to be equal for all the laminates with stacking sequences of [0/0/0/0] s, [45/45/45/45] s, [60/60/60/60] s and [90/90/90/90] s.
The stress distribution profiles in the X-direction for laminates with stacking sequences of [0/45/-45/90] s and [0/45/-45/60] s as shown in the graphs 3.8 and 3.11 are found to appear similar. The distribution of maximum stresses along Y-directions (direction of matrix) for an 8 ply CFRP laminate with stacking sequences of [0/45/-45/90] s and [0/45/-45/60] s is shown in graphs 3.7, 3.12. The stress response along the matrix direction (Y-direction) appears to be opposite to that of the stress responses in fiber direction (X-direction). The stresses in y-direction are seen to be carried largely by the layers that are present adjacent to the midplane of the midplane.
The values of strain in the 8 layers in the direction of fiber for laminate with [0/45/-45/90] s and [0/45/-45/60] s is plotted in the graphs as shown in the graphs. 3.8 and 3.13. The strain values in the Y-direction for the stacking sequences [0/45/- 45/90] s and [0/45/-45/60] s is shown in the graphs. 3.9 and
3.14 respectively.
The shear stress profiles in the XY plane for the stacking sequences [0/45/-45/90] s and [0/45/-45/60] s in an 8-ply laminate is shown in the graphs 3.10 and 3.15 respectively.
The shear stress profiles appear very similar in both the stacking sequences and the distribution of in-plane shear stresses as seen are uniformly distributed in the inner layers in both the sequences.
Graph 3.6 Stress in X-Direction
Graph 3.7 Stress in Y-Direction
Graph 3.8 Strain in X-Direction
Graph 3.9 Strain in Y-Direction
Graph 3.10 Shear Stress in XY Plane
Graph 3.11 Stress in X-Direction
Graph 3.12 Stress in Y-Direction
Graph 3.13 Strain in X-Direction
Graph 3.14 Strain in Y-Direction
Graph 4.15 Shear Stress in XY Plane
It can be viewed that the stress profile in X-direction for the 8-ply laminate with stacking sequence of [0/45/90/60] s (graph 4.16) represents that the stresses are majorly carried along the outermost layers aligned at 0° along fiber direction. The stresses further are seen to be uniformly distributed in the inner layers of the laminate as shown in the graph. 3.16.
The stress profile distribution in the Y-direction is seen to be opposite as that of the stress profile in X-direction for the stacking sequence [0/45/90/60] s. The stresses are largely distributed along the layers adjacent to the mid plane as shown in the graph 3.17
The shear stress profile for the stacking sequence [0/45/90/60] s is shown in the graph. 3.18. The distribution of in-plane shear stresses as seen in the figure are uniformly distributed in the inner layers. Stress is maximum in this stacking sequence as we can see from the figures. Stress in X-direction is maximum. We can also observe that shear stress is also maximum for this sequence. There is equal distribution of stress in remaining layers. Layers with 0- degree angle are showing greater results in this sequence for tensile loading and decent strains are observed in this sequence as shown in the graphs 3.19 & 3.20.
Graph 3.16 Stress in X-Direction
Graph 3.17 Stress in Y-Direction
Graph 3.18 Shear Stress in XY Plane
Graph 3.19 Strain in X-Direction
Graph 3.20 Strain in Y-Direction
The contour plots of total deformation, both translational and rotational for all the stacking sequences are obtained as shown in the figs. 3.1- 3.6. From the plots, it can be observed that for the stacking sequences [0/45/-45/90] s and [0/45/- 45/60] s, the translational deformation fringe patterns are quite similar. (Fig 3.1 & 3.3)
Fig 3.1 Displacement – Translational [0/45/-45/90]
Fig 3.2 Displacement – Rotational [0/45/-45/90]
Fig 3.3 Displacement Translational [0/45/-45/60]
Fig 3.4 Displacement Rotational [0/45/-45/60]
Fig 3.5 Displacement Translational [0/45/60/90]
Fig 3.6 Displacement – Rotational [0/45/60/90]
The composite laminate with stacking sequences such as [0/45/-45/90] s, [0/45/-45/60] s and [0/45/90/60] s was then subjected to compressive loading of 100N/m in the direction of fiber.
The stress distribution in the direction of the fiber for the stacking sequences [0/45/-45/90] s, [0/45/-45/60] is shown in the graphs 3.21 to 3.24. The stress profiles in the X-direction are quite similar with the layers adjacent to the midplane carrying lower stresses and the outer layers carrying larger compressive stresses. The stress distribution in the Y- direction is also quite similar, with the outer layers carrying lower stresses.
The stress profiles in the direction of the fiber (X-direction) are observed to be opposite to that of the stress profiles in the direction of the matrix (Y-direction).
The shear stress distribution for both stacking sequences [0/45/-45/60] s and [0/45/90/60] is obtained as shown in the graphs 3.25&3.26. The shear stresses acting on the XY plane are observed to be uniformly distributed in the inner layers of the laminate.
The strain in X-direction and Y-direction for both the sequences is obtained as shown in the graphs 3.27 to 3.30. The strain profile in the X-direction is observed to be opposite to that of the strain profile in Y-direction for both the sequences [0/45/-45/60] s and [0/45/90/60] s. However, the strain profiles in X and Y directions in both the sequences are quite similar.
Graph 3.21 Stress in X-Direction
Graph 3.22 Stress in X-Direction
Graph 3.23 Stress in Y-Direction
Graph 3.24 Stress in Y-Direction
Graph 3.25 Shear Stress in XY-Plane
Graph 3.26 Shear Stress in XY-Plane
Graph 3.27 Strain in X-Direction
Graph 3.28 Strain in Y-Direction
Graph 3.29 Strain in X-Direction
Graph 3.30 Strain in Y-Direction
The stress distribution for the composite laminate with stacking sequence of [0/45/90/60] s is shown in the graphs
-
& 3.32. The stress profile obtained in the X-direction
shows that the larger compressive stresses are carried by the outer layers of the laminate. The stress profile in Y-direction is observed to be opposite to that of the stress profile in X- direction, with the inner layers adjacent to midplane carrying large compressive stresses.
The shear stress distribution in the XY plane for the laminate is shown in the graph 3.33. The outermost layers of the laminate are subjected to larger values of shear stress when compared to the inner layers.
The strain distribution in the X and Y directions for the laminate with stacking sequence is shown in the graphs 3.34&3.35. The strain distribution in the direction of the fiber (X-direction) is observed to be opposite to that in the direction of the matrix (Y-direction).
Graph 3.31 Stress in X-Direction
Graph 3.32 Stress in Y-Direction
Graph 3.33 Shear Stress in XY-Plane
Graph 3.34 Strain in X-Direction
Graph 3.35 Strain in Y-Direction
The contour plots of total deformation, both translational and rotational for all the stacking sequences are obtained as shown in the figs. 3.7- 3.12.
Fig 3.7 Displacement Translational [0/45/60/90]
Fig 3.8 Displacement – Rotational [0/45/60/90]
Fig 3.9 Displacement – Translational [0/45/-45/90]
Fig 3.10 Displacement – Rotational [0/45/-45/90]
Fig 3.11 Displacement Translational [0/45/-45/60]
Fig 3.12 Displacement Rotational [0/45/-45/60]
-
-
CONCLUSION
The stacking sequences [0/45/-45/60]s and [0/45/-45/90]s showed similar stress distribution profiles throughout the layers in the laminates in the direction of fiber for tensile loading of 100N/m. The shear stress profiles in the XY plane for the both sequences were very similar and the shear stress distribution is uniform among the inner laers of the laminate.
The laminate with a stacking sequence of [0/60/45/90] also showed better stress distribution profiles for tensile load of 100N/m in the direction of fiber with the outermost layers carrying major stresses. The stresses were further distributed in a close to uniform manner in the inner layers of laminate. The composite laminate with stacking sequences such as [0/45/-45/90] s, [0/45/-45/60] s and [0/45/90/60] s was then subjected to compressive loading of 100N/m in the direction of fiber.
The stress distribution profiles for sequences [0/45/-45/90] s, [0/45/-45/60] s in the X-direction is quite similar with the layers adjacent to the midplane carrying lower stresses and the outer layers carrying larger compressive stresses. The stress distribution in the Y-direction is also quite similar,
with the outer layers carrying lower stresses.
The shear stress distribution in the XY plane for both stacking sequences [0/45/-45/60] s and [0/45/90/60] is observed to be uniformly distributed in the inner layers of the laminate.
The stress distribution profile for the composite laminate with stacking sequence of [0/45/90/60] s obtained in the X- direction shows that the larger compressive stresses are carried by the outer layers of the laminate.
The shear stress distribution in the XY plane for the laminate is obtained and it was observed that the outermost layers of the laminate are subjected to larger values of shear stress when compared to the inner layers.
-
FUTURE WORK
In the laminated composite panels, the plies can be oriented with a predetermined plan to achieve optimum efficiency and strength. This design capability when combined with an analysis of operational loading gives a unique utility in high performance material design. Such laminated composite panels can be manufactured and used according to the requirements of strength and performance.
BIBLIOGRAPHY
-
Becker, C. M. (2004). Interlaminar Stress Concentrations in Layered Structures: Part I – A Selective Literature Survey on the Free-Edge Effect since 1967. Journal of Composite Materials, 1037-1062.
-
CHERYL A. ROSE, C. T. (1993). AN APPROXIMATE SOLUTION FOR INTERLAMINAR STRESSES IN COMPOSITE LAMINATES. Composites Engineering, Vol 3, 271-285.
-
Datoo, M. H. (1991). Mechanics of Fibrous Composites. Springer Netherlands.
-
Dickson, J. T. (1978). Interlaminar Stresses in Symmetric Composite Laminates. Journal of Composite Materials, 390-402.
-
Evensen, A. P. (1970). Interlaminar Shear in Laminated Composites Under Generalized Plane Stress. Journal of Composite Materials, 204-220.
-
JN Reddy, D. R. (1994). Theories and computational models.
Applied Mechanics Reviews, 147-169.
-
JN Reddy, R. A. (2004). Shear Deformation Plate and Shell.
Mechanics of Advanced Materials and Structures, 535-582.
-
Jones, R. M. (2015). Mechanics of Composite Materials. CRC Press.
-
Kassapoglou c., P. (1986). An Efficient Method for the Calculation of Interlaminar Stresses in Composite Materials. Journal of Applied Mechanics, 744-750.
-
Mosfequr Rahman, S. A. (2014). EFFECT OF PLY STACKING SEQUENCE ON STRUCTURAL RESPONSE OF SYMMETRIC COMPOSITE LAMINATES. ASME.
-
N.J. Pagano, R. P. (1971). The Influence of Stacking Sequence on Laminate Strength. Journal of Composite Materials, 50-57.
-
PAGANO, N. J. (1977). STRESS FIELDS IN COMPOSITE LAMINATES. International Journal of Solids and Structures, 385-400.
-
Pagano, R. B. (1970). Interlaminar Stresses in Composite Laminates Under Uniform Axial Extension. Journal of Composite Materials, 234-245.
-
Pagano, S. R. (1983). ELASTIC RESPONSE OF COMPOSITE LAMINATES. Mechanics of Composite Materials, 227-242.
-
Shimpi, Y. M. (2002). A Review of Refined Shear Deformation Theories of Isotropic and Anisotropic Laminated Plates. Journal of Reinforced Platics and Composites, 775-813.
-
T. Kant, K. S. (2000). Estimation of transverse/interlaminar stresses in laminated. Composite Structures, 65-75.
-
Y.X. Zhang, C. Y. (2009). Recent developments in finite element analysis. Composite Structures (88), 147-157
-
Yin, W.-L. (1994). Free-Edge Effects in Anisotropic Laminates Under Extension, Bending and Twisting, Part I: A Stress-Function- Based Variational Approach. Journal of Applied Mechanics, 410- 415.