
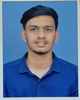
- Open Access
- Authors : Mr. Rajat P. Zinage, Ms. Sahana Bangarkinagi, Mr. Sachin Naik, Ms. Sowmya B. Kanoji, Prof. Praveen C. Kolur
- Paper ID : IJERTV12IS060106
- Volume & Issue : Volume 12, Issue 06 (June 2023)
- Published (First Online): 26-06-2023
- ISSN (Online) : 2278-0181
- Publisher Name : IJERT
- License:
This work is licensed under a Creative Commons Attribution 4.0 International License
Optimization of Machining Parameters of WEDM by using Taguchi Method to Improve Surface Roughness
Mr. Rajat P. Zinage
Basaveshwar Engineering College (Autonomous) Bagalkot Karnataka
Ms. Sahana Bangarkinagi
Basaveshwar Engineering College (Autonomous) Bagalkot Karnataka
Mr. Sachin Naik
Basaveshwar Engineering College (Autonomous) Bagalkot Karnataka
Ms. Sowmya B. Kanoji Prof. Praveen C. Kolur Basaveshwar Engineering College Basaveshwar Engineering College
(Autonomous)Bagalkot Karnataka (Autonomous)Bagalkot Karnataka
ABSTRACT
Wire electrical discharge machining generate sparks, discharges between a small wire electrode and a workpiece with de-ionized water as the dielectric medium. Which erodes the workpiece and to produce complex shapes by numerically controlled (NC) path. Optimization of process parameters for Wire electrical discharge machining (WEDM) using Taguchi method is to perform. The ultimate strategy of optimization is to attain the minimum Surface Roughness (SR) distinctly. The Design of Experiments is done in Taguchis L9 Orthogonal Array. Three input process parameters of WEDM namely Pulse on (T-ON), Pulse off (T- OFF), Wire feed at three levels were chosen as versatile to study the process performance in terms of Surface Roughness (SR).
1.INTRODUCTION
The extraction of reliable information from aerial WEDM or electric discharge machining is achieved when a discharge take place between two points of the anode and cathode, the intense heat is generated near the zone melts and evaporates the materials in the sparking zone. For improving the effectiveness of the process, the workpiece and the tool are submerged in a dielectric fluid (hydrocarbon or mineral oils)
It is found that if the materials of electrodes are same and when it is connected to positive terminal, it erodes fast. Due to this reason, workpiece is generally made the anode. Also some gap is kept in between tool and workpiece surfaces which are called as spark gap. In this process this spark occurs continuously at the spot where tool and workpiece surfaces are come closest, however the spot changes after each spark in the form of material removal after each continuous spark, the spark travels all over the surface. This causes uniform material removal over the surface.
2.LITERATURE SURVEY
[1] Vikram Singh, S.K. Pradhan Their work is to investigate the effects of various WEDM process parameters such as pulse on time, pulse off time, servo voltage and wire feed rate on the Material Removal Rate, Surface Roughness and Cutting Rate. Andto obtain the optimal settings of machining parameters at which the Material Removal Rate and Cutting Rate are maximum and the Surface Roughness is minimum in a range.
[2] Brajesh Kumar Lodhi, Sanjay Agarwal In their work they made an attempt to optimize the machining conditions for Surface Roughness based on (L9 Orthogonal Array) Taguchi methodology. Experiments were carried out under varying Pulse- On-time, Pulse-Off-time, Peak current, and Wire feed. An orthogonal array, the Signal-to-Noise (S/N) ratio, and the Analysis of Variance (ANOVA) were employed to the study the surface roughness in the WEDM of AISI D3 Steel. [3] Karthik R. et. al. Work involves optimization of machining parameters of Wire Electrical Discharge Machining used for machining of AZ31B magnesium (Mg) alloy with molybednum wire to attain the lowest Surface Roughness from the process. L9 orthogonal array with three input parameters such as Voltage (V), Pulse on time (µs) and pulse off time (µs) at three levels are used to conduct the experiments. Taguchi method is utilized to study the effect of these parameters on the Surface Roughness. [4] S. S. Mahapatra, Amar Patnaik Rough cutting operation in WEDM is treated as a challenging one because improvement of more than one machining performance measures. Metal Removal Rate, Surface Finish (SF) and Cutting Width (KERF) are sought to obtain a precision work. Using Taguchis parameter design, significant machining parameters affecting the performance measures are identified as Discharge current, Pulse duration, Pulse frequency, Wire speed, Wire tension, and Dielectric flow.3.Objectives
-
To study the effective machining parameters affecting Surface roughness of the WEDM process.
-
To improve the Surface finish by using Taguchi method.
4. Methodology
WEDM process consists large number of process parameters like discharge current, voltage, servo speed, wire tension, servo-control voltage, wire speed, pulse off time and dielectric fluid pressure etc. WEDM performance is measure in terms of surface roughness, material removal rate (MRR) and cutting width of the work piece.
This experiment is designed using Taguchi method which uses an OA (orthogonal array) to study the entire parametric space with a limited number of experiments. In this work three process parameter (factors) will be chosen such as Pulse on Time, Pulse off Time and Wire Speed. All of them will be in set at three different levels.
Selection of a particular OA (orthogonal array) is based on the number of levels of various factors. Here, 3 parameters each at 3 levels, 33 OA (orthogonal array) is selected. Each machining parameter is assigned to a column of OA (orthogonal array) and 9 machining parameter combinations will be designed. The response variables chosen for the present work is Surface roughness (Ra). The Smaller -is -better quality characteristic has been used for calculating the signal to noise (S/N) ratio of surface roughness.
Experiments is conducted using an ELCTRONICA EL-CUT CNC WEDM as per L9 OA (orthogonal array) combinations. The material of the workpiece is EN 31 steel. The workpieces are cut in dimension on 20×20 mm.
-
Selected Machining Parameters
-
Pulse on time (Ton)
-
Pulse off time (Toff)
-
Wire feed
-
Pulse on time (Ton) :- The time interval during which the spark (electron discharge) occurs between electrode (wire) and the work piece once the break down voltage of the dielectric is reached causing its ionization. Consequently the spark then causes erosion of the work piece material.
-
Pulse off time (Toff) :- The time duration between consecutive sparks during which there is no current supply to the electrodes and deionization of dielectric takes place. The dielectric also flushes the machining debris from the IEG (machining gap) during this time.
-
Wire feed :- This simply refers to the rate, again in m/min, that the wire filler metal is feed into the WEDM.
-
-
Levels of machining parameters
As per the research paper and Associated company the levels of machining parameters mentioned bellow are decided.
Sr.
no.
Parameters
Levels
L1
L2
L3
1.
Pulse on time (Ton)
112
115
118
2.
Pulse off time (Toff)
50
47
44
3.
Wire feed
3
5
7
Table 4.2.1 Levels of machining parameters
-
Design of experiment based on Taguchi method
Taguchi methods are statistical methods, sometimes called robust design methods, developed by Genichi Taguchi to improve the quality of mnufactured goods, and more recently also applied to engineering, biotechnology, marketing and advertising. Professional statisticians have welcomed the goals and improvements brought about by Taguchi methods, particularly by Taguchi's development of designs for studying variation.
Were,
A = Pulse on time
B = Pulse of time C = Wire feed
Fig 4.3.1 Taguchi L9 orthogonal array
To evaluate the effects of cutting parameters of Wire EDM process in terms of cutting performance characteristics such as Surface Roughness a Taguchi method used here to model the Wire EDM process. In the Taguchi method, process parameters which influence the products are separated into two main groups: control factors and noise factors. The control factors are used to select the best conditions for stability in design or manufacturing process, whereas the noise factors denote all factors that cause variation.
According to Taguchi based methodology, the characteristic that the smaller value indicates the better machining performance, such as Surface roughness is addressed as the-smaller-the-better type of problem. The S/N Ratio, i.e., , can be calculated as shown below
Smaller-the-better
-
Parameter combinations as per Taguchi L9 method
The parameter combinations are made by referring Fig 4.3.1 Taguchi L9 orthogonal array.
Combination |
Pulse on time ( TON ) µs |
Pulse off time ( Toff ) µs |
Wire feed m/min. |
1 |
112 |
50 |
3 |
2 |
112 |
47 |
5 |
3 |
112 |
44 |
7 |
4 |
115 |
50 |
5 |
5 |
115 |
47 |
7 |
6 |
115 |
44 |
3 |
7 |
118 |
50 |
7 |
8 |
118 |
47 |
3 |
9 |
118 |
44 |
5 |
2 |
112 |
47 |
5 |
2.6162 |
-8.3534 |
3 |
112 |
44 |
7 |
3.0302 |
-9.6294 |
4 |
115 |
50 |
5 |
3.3502 |
-10.5014 |
5 |
115 |
47 |
7 |
3.7769 |
-11.4269 |
6 |
115 |
44 |
3 |
4.0970 |
-12.2493 |
7 |
118 |
50 |
7 |
4.3078 |
-12.6851 |
8 |
118 |
47 |
3 |
4.1249 |
-12.3082 |
9 |
118 |
44 |
5 |
3.5280 |
-10.9505 |
Table 4.4.1 Parameter combinations as per Taguchi L9 method
5. Result
-
Observations
The experimental results are collected for surface roughness and 9 experiments were conducted using Taguchi (L9) experimental design methodology. Lower amount of surface roughness shows the high productivity of Wire EDM. Therefore, small the better are applied to calculate the S/N ratio of surface roughness respectively.
Table 5.1.1 Surface roughness values for each combination
With the help of these 9 combinations achieved 2.835 µm lowest surface roughness and 4.3078 µm highest surface roughness.
The results acquired are dissected using S/N Ratios, Response table, Response Graphs
Pulse on time
( TON )
Means of mean ( TON )
Pulse off time ( Toff
)
Means of mean ( Toff )
Wire feed
Means of mean (WF)
112
2.8271
50
3.497
3
3.6856
115
3.7413
47
3.50
5
3.1648
118
3.9869
44
3.551
7
3.7049
Surface roughness values
5
4.097 4.30784.1249
4 3.7769 3.528
3.3502
2.835 3.0302
3 2.6162
2
1
0
1 2 3 4 5 6 7 8 9
Surface roughness values
Fig 5.1.1 Graph of Surface roughness values
Table 5.1.2 Means of means
Combi- nations
Pulse on time ( TON )
µs
Pulse off time
( Toff )
µs
Wire feed
m/min.
Surface roughness (ra)
values
µm
S/N Ratio
db
1
112
50
3
2.835
-9.0510
-
Taguchi Analysis
Surface roughness versus pulse on time, pulse off time, wire feed is carried out on response graphs for means and S/N ratios as follows.
Means of means
Fig. 5.1.2 Effect of machine parameters on Surface roughness |
Means of S/N Ratio
6.CONCLUSION
-
All the three machining parameters are effective for surface roughness on the EN31 steel for the brass with zinc coted wire.
-
We have obtained surface roughness of three combinations out of nine which are below the range of 3.2-3.6µm incorporated by the company is accepted.
-
Among the three combinations we got minimum surface roughness from the combination of Pulse on time -112µs, Pulse off time -47µs, Wire feed -5m/min, Surface roughness -2.6162µm has been achieved.
7. REFERENCES
[1] Vikram Singh, S.K. Pradhan Optimization of WEDM parameters using Taguchi technique and Response SurfaceMethodology in machining of AISI D2 Steel. 12th Global congress on manufacturing and management, GCMM 2014
[2] Brajesh Kumar Lodhi, Sanjay Agarwal Optimization of machining parameters in WEDM of AISI D3 Steel using Taguchi Technique. 6th CIRP International Conference on High Performance Cutting, HPC 2014 [3] Karthik R, Viswanathan R, Balaji J, Sivashankar N, Arivazhagan R Optimization of WEDM Parameters for Machining of AZ31B Mg Alloy Using Taguchi Method. IOP Conference Series: Materials Science and Engineering.
Pulse on time (TON) |
Means of S/N Ratio (TON) |
Pulse off time ( Toff ) |
Means of S/n Ratio (Toff) |
Wire feed |
Means of S/N Ratio ( WF ) |
112 |
-9.0113 |
50 |
-10.7459 |
3 |
-11.2028 |
115 |
-11.3925 Fig |
47 5.1.1 Me |
-10.6962 ans of S/N R |
5 atio |
-9.9351 |
118 |
-11.9813 |
44 |
-10.9431 |
7 |
-11.2471 |
Table 5.1.3 Means of S/N Ratio
[4] S. S. Mahapatra, Amar Patnaik Optimization of wire electrical discharge machining (WEDM) process parameters using Taguchi method. Published in The International Journal of Advanced Manufacturing Technology. January 2007