
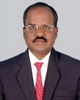
- Open Access
- Authors : Palanisamy. P , Perumal. S , Manojkumar. N. P
- Paper ID : IJERTV10IS010085
- Volume & Issue : Volume 10, Issue 01 (January 2021)
- Published (First Online): 21-01-2021
- ISSN (Online) : 2278-0181
- Publisher Name : IJERT
- License:
This work is licensed under a Creative Commons Attribution 4.0 International License
Optimization of Process Parameters on Reliability for Twist Drill life in Drilling
1Palanisam. P 2Perumal. S, 3Manojkumar. N. P
1Department of Mechanical Engineering, AVS College of Technology, Chennagoundapuram, Salem 636105,TN
2Assistant Professor, Muthayammal Engineering college, Rasipuram, Namakkal, TN-637418
3 krishnaveni carbon Pvt Ltd, Chinnavedampatty, Coimbatore, TN India,
Abstract:- Abstract: The process of material removal is one of the most extensively used mechanical processes in the industry. The process parameters such as speed, feed and point angle are experimentally investigated to maximize the tool life, which are the major machining conditions on reliability for Twist Drill life. For a company to succeed in todays highly competitive and technologically complex environment, it is essential that a company must know the reliability of its product, and able to control it, in order to produce products at an optimum reliability level. This yields the minimum life cycle cost for the user, as well as minimizing manufacturing cost of a product, without compromising the products reliability and quality. In this project, reliability analysis is made for cutting tool used for heavy and complex manufacturing. Since the downtime in transfer line due to tool failure is about 1/3 of the down time defined as the non-productive idling of the transfer line system. The ability to anticipate effectively the end of the useful tool life results in a better tool replacement strategy. This article studied effect of process parameters on reliability which have most influence on the tool life, which are predicted and optimized using rational Boolean Search.
Keywords Drilling, Reliability, process parameters, Design of Experiments
-
INTRODUCTION
-
MINIMIZING THE MANUFACTURERS COST
The figure below shows the product reliability on the x-axis and the producer's cost on the y-axis.
Figure 1 Total product cost vs. product reliability
If the producer increases the reliability of his product, he will increase the cost of the design and/or production of such a product. The figure above depicts such a scenario. The total product cost is the sum of the production and design costs as well as the other post-shipment costs. It can be seen that at an optimum reliability level, the total product cost is at a minimum. The optimum reliability level is the one that coincides with the minimum total cost over the entire lifetime of the product.
-
ADVANTAGES OF A RELIABILITY ENGINEERING PROGRAM
The following list presents useful information that can be obtained with the implementation of a sound reliability program.
-
Optimum burn in time or breaking time period.
-
Optimum preventive replace time for components in a repairable system.
-
Better information about the type of failures experienced by parts and systems that aid design, research, and development efforts to minimize these failures.
-
Establishment of which failures occur which time in the life of a product, and better preparation to cope with them.
-
Help providing guidelines for quality control practices.
-
Establishment of guidelines for evaluating suppliers from their product reliability point of view.
-
Increase customer satisfaction and an increase of sales as a result of customer satisfaction.
-
Increase of profits, or for the same profit, provision of even more reliable products and systems.
-
-
RELIABILITY ANALYSIS
Reliability is the probability of an item performing its intended function over a period of time under the operating conditions encountered. It should be observed that the above definition stresses four significant elements, namely,
-
Probability
-
Intended function
-
Time
-
Operating conditions
Apart from the above factor, reliability does change due to other factors like; quality, workman ship, manufacturing process, material process material storage, handling engineering change, deviation in production, inspection and test. Reliability is one of the most important quality characteristic of components, product and large complex system. The reliability of the cutting tool is determined.
-
-
OPTIMIZATION
Optimization is the act of obtaining the best result under given circumstances. In design, construction, and maintenance of any engineering system, engineers/managers have to take many technological and managerial decisions at several stages. The ultimate goal of such decisions is to either minimize the effort required or maximize the desired benefit. In this thesis work mathematical equations are developed by using minimum residual technique and the maximum tool life is estimated and optimized using Rational Boolean Search.
-
-
LITERATURE REVIEW
The mathematical theory of reliability has started receiving a great deal of attention from engineers and mathematicians. 1950s saw a large number of papers on components reliability, life-testing and failure distributions. The first significant paper to appear on mathematical models of multi component systems is by Moore and Shannon (1956). This paper shows that by proper incorporation of redundant technique a network of high reliability can be constructed using relatively less reliable component. Subsequently, several papers have been published on the reliability of redundant and majority voting systems. Moskowitz (1959), Mine (1959), Shooman (1968) and Mistra (1970) have described a use of a tie-set approach to the reliability evaluation of multi component system. The cut set approach is discussed by Barlow and Proschan (1965), Jenson and Belmore (1969) and Hansler (1971). Hurley (1963) uses the probability-map method for getting simplified reliability expression. Mistra and Rao (1970) have presented a procedure for reliability evaluation of redundant network using flow graphs which is consider a significant step forward in reliability evaluation. Benning (1970) presents the effect of an increasing hazard rate on reliability and mean life of redundant system. Banerjee and Rajamani (1972) have tried representing probability in two dimensions and have developed a parametric approach to analysis the reliability characteristic of general systems.
Viliam (1996) derived a recursive formula calculate the cutting tool reliability when the processing time distribution of the cutting tool can be represented by the accelerated failure time model. The formulas for cutting tool reliability when the processing time for each operation is random are also derived. The unknown parameters in the reliability function can be estimated from cutting tool life data obtained under either fixed conditions or variable conditions by using the maximum likelihood. Nick (2001) the overall idea is to investigate where reliability assessment model based on Gas can produce satisfactory solutions compared to the existing probabilistic reliability models. In general the application of Genetic Algorithm in reliability engineering is novel approach, which may contribute to a better understanding of the reliability characteristics of industrial systems and create a new method for reliability evaluation. Nakagawa (2003) defined a complexity of redundant systems as a logarithmic function of paths, using the concept of entropy. Further, reliability function of complexity is given, and the reliabilities of series and parallel systems with complexity are computed. As one typical redundan system, a majority voting system is analyzed and an optimal number of components are derived.
Claudio (2003) developed a Decision Tree (DT) approach to build empirical models for use in Monte Carlo reliability evaluation is presented. The main idea is to develop an estimation algorithm, by training a model on a restricted data set, and replacing the Evaluation Function (EF) by a simpler calculation, which provides reasonably accurate model outputs. The proposed approach is illustrated with two systems of different size, represented by their equivalent networks. The robustness of the DT approach as an approximated method to replace the EF is also analyzed. Excellent system reliability results are obtained by training a DT with a small amount of information.
-
PROBLEM DEFINITION
A case study of reliability of a twist drill is considered in the present work. This chapter given an idea of various types of twist drill, classifications of Twist drill, drill nomenclature, drill material and types of failure. Drilling is one of the most widely used methods of making holes. The cutting tool in this case is a drill with which a hole can be made from the solid or the diameter of a previous drilled hole can be increased (enlarging hole). The primary cutting motion in drilling is rotary; a straight line feed motion is used. In ordinary drill presses, both of these motions are imparted to the drill. The drill is clamped in the spindle which rotates it and feeds it download in to the work piece clamped stationary on the table.
Since 50 to 70 percent of all production time is used to make holes, it's apparent that any improvements made to the drilling processincluding the choice of the right drill, drill point geometry and sharpening methodswill make manufacturing more productive and improve quality. So it is not surprising that companies looking to earn higher return on their machine tool investments also are looking at the basic twist drill with renewed interest and depth of investigation. If accuracy and smoothness are not important in a drilled hole, at least the cost is. Too often a drill is selected merely for size and length. Much drilling can be done satisfactory with the standard point angle of 118. where quantities of holes must be produced, however, refinement in practice are desirable, factors that bear watching are: 1. machine sharpening that achieves good geometry of the drill point, such as cutting edges of the same length and at equal angles with the drill axis; 2. Point angle, lip clearance, and web thickness related to the material being drilled; 3. Proper support in a close fitting drill bushing of suitable length; and 4. Machine, chuck or driver and fixer in good condition. Sometime special drills are justified. Twist drills are usually available in sizes 0.8-12 mm plus. Special care is required when using the smallest sizes since these bits are thin and brittle. Always hold the drill square to the work and apply only light pressure when drilling. Sharpening – use a drill sharpener, a grindstone jig or an oilstone.
-
RELIABILITY ESTIMATION OF TWIST DRILL LIFE
All systems are made up of parts and components. The failure of a part or component may lead to the failure of the whole system in some cases and may not in others depending upon the functional relationship of components. In any case each component contributes to the system reliability (or unreliability) and it is worth while to express system reliability in terms of component reliability. This necessitates careful analysis of functions of all components and their failure models. Component failure models can be obtained two ways 1. From the basic failure rates and working stresses using stress models and 2. From part failure data obtained either from life-tests or failure reports of customers. It is almost impossible to establish failure rates of components for all working conditions. However, it is possible through extrapolation or interpolation to predict reliability under specific stress conditions from the available data.
-
PERFORMANCE TEST
-
Drill selection
Types of Twist drill: Parallel shank Twist Drills Jobber series Flute material: HSS, Drill Diameter: 10 mm
Flute Length: 89 3 mm, Overall Length: 132 2 mm
Web thickness : 1.76 41 mm, Web Taper: 1.58 22 mm
Lip Relief: 12 2 mm, Chisel Angle: 127 7 mm
Helix Angle: 29 3 mm, Run out: 9 8 mm
Lip out: 7 7 mm, Web out: 14 13 mm
Spacing Error: 13 12 mm
-
Specimen preparation
The work material supplied in 31mm length black bar, was a nominal 0.45% carbon, hot rolled steel and an analysis of representative samples sample showed the composition to be
c=0.41%, Mn= 0.86%, Si=0.30%, S=0.02%, P=0.03%.
The effect of small variations in the chemical composition of steel is known and such variations can occur not only between bars but also in bars.
-
Identifying the Important Process Control Variables
The independently controllable process parameters affecting the twist drill life were identified to enable the carrying out of the experimental work and developing the mathematical models, these being: Spindle speed (n), and feed (f) and Point angle (2k)
Input control variables:
Spindle speed (n), Feed (f), Point angle (2k) Output Response Number of holes to be drilled (Y).
-
Finding the Limits of Process Variables
In this research work, the chosen input parameters which effect the number of holes to be drilled are spindle speed (n), feed rate (f), and Point angle (2k). They are selected as factors to carry out the experimental works and the development of models. The chosen responses are number of holes to be drilled. The selected process parameters of the experiment for number of holes, with their limits, units and notations, are given in Table 1. The upper limit of the parameter is coded as +1.682 and the lower limit is coded -1.682. The coded values for intermediate values have been calculated from the following relationship:
X 1.682 2 X X max X min
——- (1)
i X X
max min
Where, Xi is the required coded value of a variable X, X is any value of the variable from X min to X max , Xmin is the lower limit of the variable and Xmax is the upper limit of the variable.
Table 4.1 Five Levels and three factors
S.No
Parameters
Units
Factor levels
-2
-1.682
0
+1.682
+2
1
Spindle speed
rev/min
360
500
710
1000
1420
2
Feed
mm/rev
0.16
0.22
0.31
0.45
0.63
3
Point angle
deg
114
116
118
120
122
-
Develop the Design Matrix
The use of experimental design to get the required information with minimum effort and time. Therefore, the experimental plan and program should be well prepared and designed to perform machining. Experimental design is a tool to aid the experimenter in coping with the complexities of the technical investigations. The design matrix selected for experiment is a three factor five level central composite rotatable design consisting of 20 sets of coded conditions. The design for the above said models comprises a full replication of 23 (=8) factorial design plus six centre points and six star points; these correspond to the first eight rows, the last six rows and rows nine to fourteen, respectively, in the design matrix.
Table 4.2 Design Matrix
S.No
Design Matrix
speed
Feed
Point angle
1
-1
-1
-1
2
+1
-1
-1
3
-1
+1
-1
4
+1
+1
-1
5
-1
-1
+1
6
+1
-1
+1
7
-1
+1
+1
8
+1
+1
+1
9
-1.682
0
0
10
+1.682
0
0
11
0
-1.682
0
12
0
+1.682
0
13
0
0
-1.682
14
0
0
+1.682
15
0
0
0
16
0
0
0
17
0
0
0
18
0
0
0
19
0
0
0
20
0
0
0
-
Method of Test
-
The drills shall be subjected to test by drilling a series of holes as continuously as possible in the test billet.
-
The drills shall be flooded with coolant throughout the test.
-
The drills shall be initially guided by hand feed and power shall be thrown into mesh immediately. When the outer corner of the drill reach the surface of the billet.
-
The spindle speed, feed and point angle shall be taken from the respective machine.
-
Termination criteria should be without seizing, Choking, Fusing and when the tool wear reach 0.1mm. The points of the drills and lips shall be fit for further service on completion of tests. However if the drills get blunk or breaks before the completion of specified test and if there is reason to doubt that such failure may be due to the existence of hard spot in the billet due to wrong method of test employed etc.
-
-
Experimental result
Drill life is usually expressed in terms of the number of holes drilled. The performance test is conducted in the leading cutting tool manufacturing industry Addison and company Ltd, Chennai. The tool wear is measured using Gonio meter.
Table 4.3 Input and output parameters
S.No
Spindle Speed rev/min
Feed mm/rev
point angle deg
Number of holes drilled
1
500
0.22
116
97
2
1000
0.22
116
86
3
500
0.45
116
62
4
1000
0.45
116
24
5
500
0.22
120
117
6
1000
0.22
120
112
7
500
0.45
120
85
8
1000
0.45
120
31
9
360
0.31
118
78
10
1420
0.31
118
36
11
710
0.16
118
132
12
710
0.63
118
52
13
710
0.31
114
35
14
710
0.31
122
73
15
710
0.31
118
74
16
710
0.31
118
73
17
710
0.31
119
74
18
710
0.31
118
75
19
710
0.31
119
73
20
710
0.31
120
74
-
-
Reliability Estimation
In life data analysis and reliability engineering, the output of the analysis is always an estimate. The true value of the probability of failure, the probability of success, the mean life, the parameter of distribution are any other applicable parameter is newer known, and will almost certainly remain unknown to us for all practical purpose. Once a product is no longer manufactured and all units that were ever produced have failed, and all of the data collected and analyzed, one could to have learned the true value of the reliability of the product, obviously, this is not a common occurrence. The objective of the reliability engineering and life data analysis is to accurately estimate the true values.
The Essential Computational steps of such a procedure are summarized below: Identifying the distribution
Fit the distribution Parameters Estimation Find the Reliability
-
Identifying the Distribution
A statistical distribution is fully described by its probability density function. We used the definition of pdf to show how all other function most commonly used in reliability engineering and life data analysis can be derived, namely the reliability function and failure rate function, etc. All of these can be determined directly from the probability density function definition, or f (t). Different distributions exist, such as the weibull, normal, exponential, lognormal, etc., and each of them has a predefined form of f (t). These distributions were formulated by statisticians, mathematicians and engineers to mathematically model or represent certain behavior. For example, the weibull distribution was formulated by Walloddi Weibull and thus it bears his name. Some distributions tend to better represent life data and are most commonly called life time distributions.
-
Statistical Properties of Weibull Distribution
-
The weibull distribution is a general purpose reliability distribution used to model material strength, time-to-failure of electronic and mechanical components, equipments, or systems. In most general case the three-parameter Weibull function is given by,
(2.1)
With three parameters , and .
Where, = scale parameter, = shape parameter (or slope), = location parameter
The Weibull Reliability Function
The equation for the three-parameter Weibull cumulative density function, cdf, is given by:
(2.2)
Recalling that the reliability function of a distribution is simply one minus the cdf, the reliability function for the three- parameter Weibull distribution is given by,
(2.3)
Ranking Method: Medium Ranks
-
Reliability Estimation
Reliability of the cutting tool based on the time. R (t) reflects the effect of the age of the twist drill. The table depicts that the reliability for the cutting tool for the corresponding number of holes drilled. Example the twist drill is completed 21 holes, the reliability of the tool is 0.9386.
Table 4.5 Reliability estimation
No of Holes to be drilled
Reliability
1
0.9915
11
0.9758
21
0.9386
31
0.8861
41
0.8144
51
0.7252
61
0.6228
71
0.5134
6. CONCLUSIONS
By means of MATLAB it was possible to derive a prediction equation relating three factors which affect the life of a 10mm diameter, two flutes Jobber series twist drill. Selection the parameters, namely speed, feed and point angle at the periphery was based on the assumption that these were the factors over which the drill user could exert positive control. Drill life is directly proportional to speed and feed and indirectly proportional to point angle.
The following conclusions have been arrived at from the results of the present investigation
-
The models developed can be employed easily on a drilling machine
-
The number of holes to be drilled have increased when the speed and feed is decreased.
-
The optimal values of speed, feed and point angle and Number of holes to be drilled are 360 rev/min, 0.63 mm/rev, 122 deg and 435 respectively.
-
Replacement decisions can be made at proper time. Maintenance and rework costs can be reduced.
-
REFERENCES
-
Chang Huajian and Shi Yongchang., A practical reliability analysis method for Engineers, Reliability Engineering and System Sail' O' 47 (1995) 93-95
-
Claudio M. Rocco S. A rule induction approach to improve Monte Carlo system reliability assessment, Reliability Engineering and System Safety 82 (2003) 8592
-
Cochran W.G. and Cox G.M. () Experimental Designs, 2nd edition, Newyork: John Wiley & sons.
-
Ghani J. A, Choudhury I. A, Hassan H.H, Application of Taguchi method in the optimization of end milling parameters, Journal of Materials Processing Technology 145 (2004) 8492
-
Huamin Liu and Viliam Makis., (1996), Cutting Tool Reliability Assessment in variable machining conditions, IEEE Transactions on Reliability, Vol 45, No. 4.
-
Johannes A. van den Bogaard, Jaya Shreeram, Aarnout C. Brombacher, A Method for Reliability Optimization through Degradation Analysis and Robust Design
-
Kim C. M. and Bai D. S. Analyses Of Accelerated Life Test Data Under Two Failure Modes, International Journal of Reliability, Quality and Safety Engineering Vol. 9, No. 2 (2002) 111-125
-
Kuljanic E, Sortino M, TWEM, a method based on cutting forcesmonitoring tool wear in face milling, International Journal of Machine Tools & Manufacture 45 (2005) 2934
-
Leszek Kielar and Prof. Jan Szadkowski., tool life equations determined from manufacturers data
-
Marimuthu K and Murugan N (2001), Robust Design of Experiments To predict Quality of Hardfaced valve seats, Recent advances in Material Processing, pp 152-163.
-
Nagasaka K and Hashimoto F (1988), Tool wear production and economics in machining stepped parts, Int J. Machine Tool Manufacturing, Vol. 28, pp 569-576.
-
Ruiz-Falco Rojas A Reliability Improvement Vs Quality? An Integrated Approach,
-
So Young Sohn and In Su Choi., (2001)., Fuzzy QFD for Supply Chain Management with reliability Consideration, Reliability System and safety 72 (2001), 327-334
-
Xiaoping Du and Wei Chen., Sequential Optimization and Reliability Assessment Method for Efficient Probabilistic Design, ASME Journal of Mechanical Design