
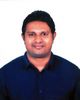
- Open Access
- Authors : Bhandari Avinash, R Shravanthi, G. Vamshi Krishna
- Paper ID : IJERTV12IS090092
- Volume & Issue : Volume 12, Issue 09 (September 2023)
- Published (First Online): 13-10-2023
- ISSN (Online) : 2278-0181
- Publisher Name : IJERT
- License:
This work is licensed under a Creative Commons Attribution 4.0 International License
Optimum Placement of Holes In Combusion Chamber to Burn the Unburnt Carbons
Bhandari Avinash¹
Design Engineer,
Department Of Process Planning Engineering, Veda Sri Chakra Technologies Pvt. Ltd, Hyderabad, India
R SHRAVANTHI ³
M-TECH STUDENT
Department of Aeronautical Engineering, Mallareddy College of Engineering &Technology, Hyderabad, India
G.Vamshi Krishna ² Design Engineer,
Department Of Process Planning Engineering, Veda Sri Chakra Technologies Pvt. Ltd, Hyderabad, India
ABSTRACT – The impact of aviation industries contributes total of 9 % of pollutions for current global warming.
Carbon components contributes of 12 % and sulphur oxides contained 6% of total pollution that impact on global emissions. The main reason for carbon emission is residual of unburnt carbons in combustion chamber during combustion. For this there should be a proper circulation of swirl flow during combustion which could help in burning the unburnt carbons mainly at corners of chamber.
There is device called Swirler device has been using for generating swirl flow which could help in burning the unburned carbons component. However, this device could add extra weight which could affect the performance of combustion.
The Objective of this thesis is the additions of holes with proper placement on the walls of combustion chamber to bypass air into the combustion chamber which interacts with the flow present inside the combustion chamber and produces swirl flow so that the un-burnt fuel present at corners of the combustion chamber comes in contact with these hot gases and complete burning process takes place efficiently.
Angles.
KEYWORDS: Primary Air Flow, Secondary Air Flow, Dilution Holes and Airflow, Swirler Flow, Lean Blowout Limits, Combustor, 1A. ir INMTaRssOFDlUowCTRIOatNe, Dilution Hole
-
Swirler
The swirler devices are the part of the combustor that the primary air (see Air flow paths below) flows through as it enters the combustion zone. Their role is to generate turbulence in the flow to rapidly mix the air with fuel. Early combustors tended to use bluff body domes (rather than swirlers), which used a simple plate to create wake turbulence to mix the fuel and air. Most modern designs, however, are swirl stabilized (use swirlers). The swirler establishes a local low pressure zone that forces some of the combustion products to recirculate creating the high
turbulence. However, the higher the turbulence, the higher the pressure loss will be for the combustor, so the dome and swirler must be carefully designed so as not to generate more turbulence than is needed to sufficiently mix the fuel and air.
-
Lean Blowout Limits
Lean Blowout is conditions in gas turbine engine combustion chamber during which the fuel supply to maintain or reduce engine RPM. In this process the burning may be so slow that the flame is carried out of the combustion chamber and extinguished. Aim of this project is to create swirl flow inside the combustion chamber so that lean blowout limits are increased.
Lean blowout (LBO) limits is critical to the operational performance of combustion systems in propulsion and power generation. The swirl flow plays an important role in flame stability and has been widely used in aviation engines. Therefore, the effects of swirl flow geometry and flow dynamics on LBO limits are significant. This project is conducted for studying the lean blowout limits of a single dome rectangular model combustor with swirl flow inlets. Different holes are placed at positions so that the dilution air is sent into the combustion chamber to produce maximum swirl flow which increase in air flow rate which dependently increases the lean blowout limits.
Fig 1: Shows the Combustion Process and Mixing Of the Bypass Flow
(https://en.wikipedia.org/wiki/Combustor)
-
Primary air
This is the main combustion air. It is highly compressed air from the high pressure compressor (often decelerated via the diffuser) that is fed through the main channels in the dome of the combustor and the first set of liner holes. This air is mixed with fuel, and then combusted.
-
Intermediate air
Intermediate air is the air injected into the combustion zone through the second set of liner holes (primary air goes through the first set). This air completes the reaction processes, cooling the air down and diluting the high concentrations of carbon monoxide (CO) and hydrogen (H2).
-
Dilution air
Dilution air is airflow injected through holes in the liner at the end of the combustion chamber to help cool the air to before it reaches the turbine stages. The air is carefully used to produce the uniform temperature profile desired in the combustor. However, as turbine blade technology improves, allowing them to withstand higher temperatures, dilution air is used less, allowing the use of more combustion air.
-
METHODOLOGY
The model is designed as per the dimensions in design modular. The model is imported in mesh and meshing is carried out to produce a finite mesh. Then the model is loaded in fluent solver and the models are given as per our requirements. Then the material to be send as flow over the body is selected. Then the specified values at each zone are given. Then solution is initialized from the required position and the iterations are carried out for results. Then contours and vectors required are captured and analysed with changes in flow.
2.1 Design Dimensions:
This paper is based on the consideration of design dimensions of combustion chamber of a (Rolls Royce engine RB112), they are as specified below:
Secondary air inlet
20 mm
Total width of combustion chamber
520 mm
Primary zone
160 mm
Secondary zone
140 mm
Width of dilution holes
5 mm
Air outlet
120 mm
Hole angles
30, 45, 60 degrees
Distance between holes
40mm, 50mm, 60 mm
Table 1: Dimension Parameters:
The following parameters are considered during analysis of our model
Air mass flow rate
4.28 Kg/s
Inlet air temperature
461.9 K
Inlet total pressure of air
4253 bar
Inlet static pressure of air
3889 bar
Mass flow rate of fuel
0.745 Kg/s
Inlet fuel temperature
430 K
Inlet total pressure of fuel
4053 bar
Velocity of fuel injection
15 m/s
Outlet temperature
1200 K
Pressure loss
6 %
Combustion efficiency
0.99
The modelling of the combustion chamber is done as a 2-D and symmetrical model in ANSYS sketching.
-
RESULTS AND DISCUSSIONS
-
Primary air inlet |
85 mm |
The results of pressure, temperature and velocity and vectors of velocity at holes placed at different distances such as 40mm, 50mm, 60mm and angles 30, 45, 60 degrees are shown in figures below.
Fig 2: Modelling of Combustion Chamber Table 2: Flow Properties Parameters
Fig 2: Mesh Structure
Fig 4: Static Pressure Contours at Length 40mm and At 30°
Fig 5: Static Temperature Contours at Length 40mm and At 30°
Fig 6: Velocity Magnitude Contours at Length 40mm and At 30°
Fig 7: Velocity Vector Contours at Length 40mm and At 30°
Fig 8 Static Pressure Contours at length 40 mm and at angle 45°
Fig 9: Static Temperature Contours at length 40mm and at
angle 45°
Fig 10: Velocity Magnitude Contours at length 40mm and at angle 45°
Fig 11: Velocity Vector Contours at length 40mm and at angle 45°
Fig 12: Velocity Vector Contours at length 50mm and at angle 30°
Fig 13: Static Temperature Contours at length 50mm and at
angle 30°
Fig 14: Static Pressure Contours at length 50 mm and at angle 30°
Fig 15: Velocity Magnitude Contours at length 50mm and at angle 30°
Fig 16: Static Pressure Contours at length 60mm and at angle 30°
Fig 17: Static Temperature Contours at length 60mm and at angle 30°
Fig 18: Velocity Magnitude Contours at length 60 mm and at angle 30°
Fig 19: Velocity Vector Contours at length 60mm and at angle 30°
Contours at length 60 and at angle 30°
Fig 20: Static Pressure Contours at length 60mm and at angle 45°
Fig 21: Static Temperature Contours at length 60mm and at angle 45°
Fig 22: Velocity Magnitude Contours at length 60 mm and at angle 45°
Fig 23: Velocity Vector Contours at length 60mm and at angle 45°
Fig 24: Static Pressure Contours at length 60 mm and at angle 60°
Fig 25: Static Temperature Contours at length 60mm and at angle 60°
Fig 26: Velocity Magnitude Contours at length 60mm and at angle 60°
Fig 27: Velocity Vector Contours at length 60 mm and at angle 60°
Length 50mm mass flow
rate vs angles
0.006
0.004
0.002
0
Based on the flow analysis, due to the swirl flow generated, the mass flow rate at the exit is changed. This change in mass flow rate is due to the optimum change in distance between the holes and angles at different position. This change is shown in graphs below i.e. graphs between mass flow rate versus length and graph between mass flow rate and angles.
0.006
0.004
0.002
0
Length 40mm mass flow
rate vs angles
0 20 40 60 80
0.006
0
20
40
60
80
Length 60mm mass flow
rate vs angles
0.004
0.002
0
0 20 40 60 80
-
CONCLUSION
Based on the results obtained that conclude the optimum distance and angle could replace the swirler devices with appropriate dilution holes placed at optimum angles to produce swirl flow which increases the mass flow rate at the exit of the combustion chamber. As per the analyses, the optimum position of the holes has been found at 30 degrees angle and the holes are placed 60mm apart. The velocity magnitude at this position of holes 1.22e+03m/s and mass which is not as produced by the swirler devices(75% – 80%) which is efficient enough i.e. 70% to increase the lean blowout limits of the combustion chamber.
So, this paper concludes that swirler devices can be replaced by the holes placed at optimum position and angle so that it produce swirl flow which compensate the weight of Swirler device that reduces the weight of the combustor and also the cost for the materials used for making swirler devices is reduced.
-
FUTURE SCOPE
This project can be further developed by performing analysis at more optimum angles and lengths so that more efficiency is obtained. Also holes can be used along with the swirler devices to obtain efficiency up to 85%.
-
REFERENCES
B. Selvababu
[4] A. B. Wassell, TheDesign and Development of High Performance Combustors, Lecture Series 93, Von KarmanInstitute of Fluid Dynamics, 1977. [5] A. H. Lefebvre and E. R. Norster, A Design of Tubular Combustion Chambers for optimum Mixing Performance,Technical Advances in Gas Turbine Design, pt. 3N, Proc. Inst. Mech. Eng., 1969.. [6] Study and performance analysis of gas turbine combustion chamber and improving combustion efficiency by using ceramic composite material coating by R Vijayan1 C Dhatchanamoorthy, M Mohanraj1 and M Pasumpon. [7] Heat transfer and flow characteristics inside a gas turbine combustor by Yap-Sheng Goh B.S., Louisiana State University, May 2003. [8] J. C. Han, S. Dutta, S. V. Ekkad, Gas Turbine Heat Transfer and Cooling Technology, Taylor & Francis, 2000. [9] A. H. Lefebvre, Gas Turbine Combustion, Taylor & Francis, 2nd Edition, 1998. [10] Koff, B.L., Aircraft Gas Turbine Emissions Challenge, J. of Engg.Turbine Power,116, 474-477, 1994.
[11] J.J. Mcguirk, and J.M.L.M. Palma, The Flow Inside a Model Gas Turbine Combustor: Calculations, J. of Eng. Gas Turbines Power, 115, 594-602, 1993. [12] H.L. Relation, J.L. Battaglioli, and W.F. Ng, Numerical Simulation of Nonreacting Flows for Industrial Gas Turbine Combustor Geometries, J. of Eng. Gas Turbines Power, 120, 460-467, 1998. [13] N.K. Rizk and H.C. Mongia, Three Dimensional Gas Turbine Combustor Emissions Modeling, J. of Eng. Gas Turbines Power, 115, 603-611, 1993. [14] D.G. Sloan, P.J. Smith, and L.D. Smooth, Modeling of Swirl in Turbulent Flow Systems, Prog. Energy Comb. Sci., 12, 103-250, 1986. [15] Design and improvement of combustion chamber for small gas turbine power plant by Jai Ganesh Chetiyar R, Hemanathan, Guru prasath M,B. Selvababu.
[16] A. B. Wassell, The Design and Development of High Performance Combustors, Lecture Series 93, Von Karman Institute of Fluid Dynamics, 1977. [17] A. H. Lefebvre and E. R. Norster, A Design of Tubular Combustion Chambers for optimum Mixing Performance, Technical Advances in Gas Turbine Design,pt. 3N, Proc. Inst. Mech. Eng., 1969.