
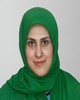
- Open Access
- Authors : Atieh Safari
- Paper ID : IJERTV9IS080238
- Volume & Issue : Volume 09, Issue 08 (August 2020)
- Published (First Online): 01-09-2020
- ISSN (Online) : 2278-0181
- Publisher Name : IJERT
- License:
This work is licensed under a Creative Commons Attribution 4.0 International License
Optimum Route Selection in Parallel Robot Manipulators by Analyzing Forward and Inverse Kinematics
Atieh Safari1
1Department of Electrical and Computer Engineering, Shahid Beheshti University, Tehran, Iran
Abstract:- None of the studies performed in the area of parallel robots has dealt with kinematic analysis of four-degree-of-freedom robotic manipulators featuring 4-RUU configuration (a rotational joint and two universal joints) and the mechanisms singularities and use of limit concept for the removal of them. Controlling robot based on forward and inverse kinematic solutions is a method widely applied in parallel manipulators (PM). Kinematic analysis of a PM includes finding of all the possible states of the final operator per certain inputs for active joints. Moreover, inverse kinematic, as well, is a mathematical expression determining the situation of a kinematic chain of PM in proportion to its active joint. Kinematic analysis of this set of robots necessitates an appropriate mathematical framework capable of providing complete explanation of the transmission and rotation. The present study seminally presents the relations pertinent to forward and inverse kinematics of parallel robotic manipulators with 4-RUU configuration following which Jacobian Matrix is applied to the estimation of singular points. Resultantly, an approach, named limit method, is utilized to remove the singularities of the robotic mechanism. The objective, in all of these methods, is controlling of the position of an object and the systems internal force so that no singularity could come about on the robots route. In the end, the obtained results will be elucidated for finding an optimum path of singularity removal on the robots direction of movement.
Keywords: Parallel robotic manipulator, singularities, Decartian space, limit method, Jacobian
-
INTRODUCTION
Parallel robotic manipulators have been actively studied during the past two decades. Controlling of these types of robots is a lot more difficult than single-arm robots. That is because parallel manipulators (PMs) are characterized by a more complex system rendering it occasionally unstable and the discussions are more related to motion control plus equilibrium equations of the shared load by the two arms. Despite such a complexity, parallel manipulators also possess advantages that have made them attractive to the researchers, including better operation on discontinuous surfaces such as when welding stairs and moving loads through obstacles. These robots rely only on one of their arms in a substantial part of their motion cycle. Therefore, it is necessary to create a proper movement pattern in consideration of stability scales for these robots. So, the use of novel methods is of a considerable importance in improving the controllability of parallel manipulators. Artificial intelligence and neural networks are amongst the proposed controlling method. The aforesaid methods found their way into industrial applications since 1960 on and they predominantly work based on experts knowledge using a decision-making style for the designing, monitoring of processes and controlling of industrial equipment. This instrument has been upgraded with the progress in computer technologies as well as following the emergence of personal computers as a result of which many artificial intelligence applications were actualized.
In 1980, its use become widespread in the industry, especially in Japan, with the invention of microprocessors based on artificial network algorithms. Supplementary calculations were highly taken into account in the foresaid country both in university and industry. As a result of these happenings, computational intelligence (CI) was born. Furthermore, during the recent decades, along with the extensive uses of computational intelligence in other sciences, novel controlling methods have been proposed and expanded under the title of smart control one instrument of which is the use of neural networks featuring various formulations. Up to the present point in time, the majority of the theoretical and practical works have been carried out on three- degree-of-freedom and/or six-degree-of-freedom PMs. But, it was only recently that the PMs with degrees of freedom below six (PMs with limited degrees of freedom) were taken into consideration. The mechanisms structure should have certain qualifications, including its being simple so that it can be made with the lowest cost; the system should be designed optimally in terms of energy consumption so that it can have lowest energy consumption rates, particularly in mobile (moving) applications. For some of the applications, there is a need for it to have the capability of carrying heavy loads. The final executor should be able to offer large velocities and accelerations and, finally, the designing concepts of it should be generalizable to a range of dimensions from micro to macro [1].
One of the characteristics of PMs is its possession of several kinematic closed-loops. In a PM, each branch shares the toleration of a quotient of the load making it capable of carrying heavier loads in a faster speed and acceleration while consuming lower energy. The most notable weakness of PMs pertains to workspace limitations resulting from manipulators collision and the existence of singularities. However, these robots might additionally obtain an uncontrollable one degree of freedom in singularity points following which move non-arbitrarily [2].
Discrete method is one of the most effective methods of obtaining workspace and reducing singularities. The method has been studied by Xiao et al and Brisan et al [56&57]. In this method, the workspace is obtained via selecting a domain of points in
Cartesian or polar coordinates followed by their evaluation as to figure out whether they violate the specified constraints or not. This method enables the consideration of all the mechanical constraints. On the other hand, the precision of the determined workspace depends on the number of the points and the calculation time increases with the increase in the number of singular points. Studies have been performed by some researchers regarding the singularity of the parallel mechanisms using screw theory with an introduction of two singular arrangement, fixed and estimated [3&4]. To find the workspace, some researchers have employed Grassmanns linear geometry [5&6]. Singularity analysis of parallel mechanisms has also been done by some researchers via defining Jacobian Matrix and the relations between the mobile platform and joint drivers with the introduction of three singularities, forward, inverse and combined singularities [7&8].
According to the heavy load of calculations in the accurate modeling methods, approximate methods can be applied for the modeling of continuous robots [9]. To model and muscles and hydrodynamics of the parallel robotic manipulators, a model, comprised of a large number of such elements as mass, spring and liner damper, has been utilized. In [10], robot is divided into several parts based on operator torques and each part is approximated with a fixed curvature. In cases that large forces are not imposed onto the body of the continuous robots, the approximation features a good precision. The method has been repeatedly used for the estimation of the kinematics of continuous robots in the absence of external loads [11].
-
SIMULATION PLAN
The present study specifically deals with the forward and inverse kinematics of 4-RUU parallel manipulators and investigates the relationship between the drivers and the mechanisms final status. Suchproperties as vast workspace, fast mountability and de-mountability, low inertia of the mobile parts, easy portability and low manufacturing costs have drawn attentions to PMs more than ever before. However, the major problem of these robots is in the workspace of the singular points appearing in the form of unwanted vibrations. In addition, the mechanism becomes uncontrollable in singularities and incapable of tolerating the external load and torque. After obtaining the singular points based on Jacobian Matrix analysis, limit concept will be applied to the removal of singularities so that the endlessness of the transformation function when moving from Decartian space to joint space can be prevented.
In the end, the singularities of the mechanism and Jacobian matrix are computed in a general mode following which limit concept is used to remove these points from PMs workspace. In inverse singular points, the robot tends towards infinity when being moved from Decartian space to joint space and this makes impossible the transformation from the former to the latter. Limit concept, in fact, offers a formulation based on which the inverse transfer function from Decartian space to joint space turns into a bounded value. In the end, mechanism parameters effective in the form of work space are identified and the best of them will be selected for the expansion of the work space.
-
KINEMATIC ANALYSIS OF 4-RUU PARALLEL MANIPULATOR
-
Geometrical Structure of Four-Degree-of-Freedom Parallel Manipulators
Kung and Joselin [67] introduced eleven four-degree-of-freedom mechanisms with three-degree transmission and one-degree rotation patterns out of which six are classified amongst 5R groups (composed of five rotational joint in each chain). The general form of PM, studied herein, is the same as that of 4-RUU. Letter R denotes hinge joint and U denotes universal joint in the current research paper.
Figure (1): a schematic view of 4-RUU robot [6&7]
As it can be seen in the above figure, the robot is consisted of a final operator attached to a fixed platform by means of four identical kinematic chains. Reference O, of fixed 0 coordinates system, and point P, of mobile 1 device, are situated on the fixed and mobile centers of the robot, respectively. Each branch of the robot is composed of five rotational joints. The first rotational joint is located on base A. In each of the second A and third C joints, there are two rotational joints, R, that are indeed considered as a joint U with a constrained one degree of freedom.
-
Kinematic Analysis
As shown in figure (2), the first hinge joint in base A is considered to have a rotational vector 1i(i=1, ,4). The first and second joints vectors are considered along z-axis and the third joints vector is assumed along mobile device z. Corresponding to figure (3-2) drawing, the third vector of the joint is considered with the name Si(i=1, ,4) that instantly changes with the angles of the second joint positioned in B.
T
T
Si 0, cos2i ,sin2i , 0
, i 1,, 4
(1)
The first hinge joint, located in point A, belongs to fixed coordinates system positioned in origin 0 in distance a. Also, the first universal joint is located in point B with a distance l from point A. The link AB always moves on a plane whereon vector vi is perpendicular. Therefore, the coordinates of points A and B in coordinate system 0 are:
ro 1,a, 0, 0T , ro 1,l cos a,l sin
, 0T
(2)
A1 B1 11 11
ro 1,0, a, 0T , ro 1,l cos ,l sin
a, 0T
A2 B2 12 12
ro 1,a, 0, 0T , ro 1,l cos a,l sin
, 0T
A3 B3 13 13
ro 1,0, a, 0T , ro 1,l cos ,l sin a, 0T
A4 B4 14 14
Figure (2): angular parameters of 4-RUU robot in a view of the overlaying plane [6&7]
The mobile platform has been connected to robot via four universal joints situated on points Ci. The length of the mobile platform from point P of reference 1 to point Ci is defined as b. If the Bi Ci links length is defined by a value equal too r, the point coordinates of Ci in mobile reference would be:
r
r
C1
C1
1 1,b, 0, 0T ,
r
r
C2
C2
1 1,0, b, 0T ,
1 1,b, 0, 0T
r
r
r
r
C3
C3
C4
C4
1 1,0, b, 0T
(3)
It can be concluded from the analysis that the four designing parameters, a, b, l and r and four joint variables, 11, 12, 13 and 14, control the movements of 4-RUU parallel manipulator.
-
Geometrical Constraints
To obtain the point coordinates of Ci, the transmission matrix takes the following form based on Eulerian Matrix
[6&8]:x2 x2 x2 x2
0T
M
0 1 2 3 31
(4)
MT MR
Where, MT and MR express the moving and rotational parts of transformation Matrix M that are as shown below:
2×0 y1 x1 y0 x2 y3 x3 y2
M 2x y x y x y x y
(5)
T 0 2 1 3 2 0 3 1
2×0 y3 x1 y2 x2 y1 x3 y0
x2 x2 x2 x2 2 x x x x 2 x x x x
0 1 2 3 1 2 0 3 1 3 0 2
0 1 2 3
0 1 2 3
M 2 x1x2 x0 x3 x2 x2 x2 x2 2 x2 x3 x0 x1
(6)
2 x x x x 2 x x x x x2 x2 x2 x2
1 3 0 2 2 3 0 1 0 1 2 3
In these matrices, the parameters of robots coordinates of route are x0, x1, x2, x3, y0, y1, y2 and y3. In fact, these parameters map the displacement vector in movement space through transformation matrix to the point in the reference coordinates. To simplify the algebraic variables, there is a need to make a variable change based on half of the angle, , about which joints rotate.
2
Considering a variable change equal to
= tan ( ), the following relations are obtained:
2
sin ij
2
2t
2t
ij
1 t2
, i 1, 2 , j 1,, 4 and
cos ij
1 t 2
ij
1 t 2
(7)
ij ij
The coordinates of pint Ci and the vectors perpendicular on plane ni defined in fixed coordinates system are:
ro Mr1 ,n0 Mn1
, i 1,, 4
(8)
Ci Ci i i
The coordinates of all points should be obtained based on geometrical parameters and spatial coordinates parameters. The link connecting Bi and Ci is on the same plane as vectors ni and vi and the constraints equations are acquired via scalar multiplication and external multiplication:
Ci
Ci
Bi
Bi
i i
i i
ro ro .v n0 0 , i 1,, 4
(9)
The constraints equations are calculated as beneath with the running of abovementioned mathematical operation:
1 11 11 11 0 1 11 0 2 11 0 0 11 3 1
1 11 11 11 0 1 11 0 2 11 0 0 11 3 1
11 11 11 3 2
11 11 11 3 2
g : at 2 bt 2 lt 2 a b l x x
-
2lt x x
2t 2 2 x y
-
2lt x x at 2 bt 2 lt 2 a b l x x
11 3 3
11 3 3
2t 2 2 x y 0
(10)
2 12 0 1 12 12 12 0 2 12 0 0 12 12 12 3 1
2 12 0 1 12 12 12 0 2 12 0 0 12 12 12 3 1
g : l lt 2 x x
-
at 2
-
bt 2
-
-
2lt 2
-
a b x x
2t 2
-
2 x y
-
at 2
-
bt 2
-
2lt 2
-
a b x x
12 3 2 12 3 3
12 3 2 12 3 3
lt 2
-
l x x
2t 2
2 x y 0
(11)
3 13 0 1 13 13 13 0 1 13 0 0 13 13 13 3 2
3 13 0 1 13 13 13 0 1 13 0 0 13 13 13 3 2
13 3 1 13 3 3
13 3 1 13 3 3
g : 2lt 2 x x
-
-
at 2 bt 2 lt 2 a b l x x
2t 2 2x y
-
at 2 bt 2 lt 2 a b l x x
2lt 2 x x
2t 2 2 x y 0
(12)
4 14 0 1 14 14 14 0 2 14 0 0 14 14 14 1 3
4 14 0 1 14 14 14 0 2 14 0 0 14 14 14 1 3
g : lt 2
-
l x x
-
-
at 2
-
bt 2
-
2lt 2
-
-
a bx x
2t 2
-
2x y
-
at 2
-
bt 2
-
2lt 2
-
-
a b x x
12 3 2 14 3 3
12 3 2 14 3 3
lt 2
-
l x x
2t 2
2 x y 0
(13)
To write the constraints along link r, distance equation is formulated as below:
Ci
Ci
Bi
Bi
ro ro 2 r2 , i 1,, 4
(14)
-
-
-
Solving the Inverse Kinematic Problem and Obtaining the Determinant
According to the transformation matrix and the eightfold constrained explained in the first part of the present study, the matrixs determinant and singularities can be specified. Resultant method was used to solve the inverse kinematics problem of the robots. The resultant method serves the elimination of one or several points from an equation system in such a way that the finally attained equation encompasses the effects of all the equations. In sum, the resultant method is defined in the form of the relation (3-21) of (m+n)×(m+n) matrixs determinants for removing variable x from two f and g polynomials that are of m and n degrees (relations 3-19 and 3-20), respectively [69&71]:
f a xm a a
0 ,m 1
(15)
0 m 0
g b xn b b 0 ,n 1
(16)
0 n 0
(17)
a0 b0
Resultant f , g, x det a b
1 1
a2 b2
a b
m m
In these relations, ai and bi are fixed coefficients and/or polynomials based on parameters other than x. The other entries of the above determinant are zero. Next, the algorithm used based on the resultant method will be explained parallel to the kinematic analysis of the 4-RUU parallel robot.
Using the joints coordinates, kinematic constraints governing the chains of each PM and resultant method, the inverse kinematic expression is obtained for each chain of the PM. The term should be devoid of the coordinates of the inactive joints the statuses of which are unclear.
Using the inverse kinematic term obtained for each chain and reusing the resultant method, a univariate mathematical expression is obtained that explains the inverse kinematic of the PM. This univariate term includes all the answers to parallel manipulators inverse kinematic problem. Then, following the attainment of this mathematical term, it will be solved along with backward solving of the equations so as to obtain the entire answers to the kinematic problem of the spatial PM (figure 3).
Figure (3): analyzing the kinematic problem of 4-RUU parallel manipulator in 3D Euclidean space
Figure (2) illustrates the i-th kinematic chain of 4-RUU parallel manipulator. According to the figure, relation (3-6) governs each chain of the robot:
x x 2 y y 2 z z 2 L2 0
(18)
Ei Ci Ei Ci Ei Ci 1
Exerting relations (3-1) and (3-2) and using the resultant method, the kinematic terms of the chain are obtained as below:
1 1 1 12
1 1 1 12
F x2 y2 z2 2ac x 2as y a2 L 0
(19)
F x2 y2 z2 2ac x 2x B x 2bc x 2bs x 2 y B y 2as y 2bc y 2bs y
2 2 2 2 2
2b 2 2bc as2 L a 2 2bs ac 2bs as x2 y2 2bs y 2bs x
2 2 2 B2 B2 B2 B2
2 y B a s2 2 b c y B 2xB ac2 2 b c xB 2b c a c2
(20)
2 2 2 2
F x2 y2 z2 2bs x 2x B x 2ac x 2bc x 2bs y 2y B y 2as y 2bc y
3 4 4 4 4
2 y B as4 2bc y B 2b s as 4 2b s x B 2b s ac4 2 x B
ac 4 2b 2
4 4 4 4
2bc a s 2bs y 2bc ac L x y 2bc x
a2
(21)
4 4 4 2 2 B4 B4
Then, the univariate inverse kinematic term is obtained based on t by changing the tangent of angles half and using the resultant methods output. Many random examples were attained via changing the values of design parameters, input values and coordinates of Bi points and the obtained answers were inserted in the inverse kinematic equations of the robot. It was eventually found out that a univariate t-based variable of degree eight is always expressive of the inverse kinematic of the 4- RUU parallel robot. The result indicates that the explained PM gives at least eight imaginary and real answers. The delineation of singularities and offering a method for solving the method will be explained in the forthcoming chapter.
3.3 Implementation of Limit Method for Removing Singularities from Robots Workspace
To remove the singular points from the workspace, theory number six of limit concept was applied according to Özdemir [70]. Based on the theory, if the number of equations required for the constraint exceeds that of the problems uncertainties (N>N*), the following limit can be defined:
i lim i t
t ts
, i 1,., m n
(22)
Where, i denotes eigenvalues of Jacobian matrix, t is the time parameter and ts indicates the sampled instant. In this case, the above-presented limit is restricted (singularities are removed from the workspace) provided that the following conditions hold:
-
Linear system A=R is found consistent and finite during ts.
i s
i s
-
If t
, i 1,, m n, v,, N
are equations of robots constraints, the following limit has to be finite:
s
s
lim t
N 1 t
, i 1,., m n
(23)
i s
i s
i t ts i
N 1 t
In this case, the inverse kinematic solution of the robot is devoid of the singularities if the following conditions are met:
t i t ,t ts
,i 1,., m n
(24)
i
i ,t ts
,i 1,., m n
The answer to the equation A=R can be expressed in the form of = 1 and/or = 1 () in which () denotes
the appended matrix A that is defined as demonstrated below:
ij
ij
adj A Cij
,i 1,. . . ,m ,
j 1,. . . ,m n
(25)
This way, it can be written that:
1 mnC R
, i 1,. . . ,m n
(26)
i j 1 ij j
And/or:
i t
i t t ,
i 1,. . . ,m n
(27)
s
s
u
u
s
s
s
s
It can be show that u t 0 per every v 1 for u 1,. . . ,v 1 . So, it can be concluded that all the values of i t
u t
, i 1,,m n
and u 0,, v 1have limited values and that they are ambiguity elimination problems taking a state of
zero
zero
if u t
0 , i 1,,m n and u 0,, v 1are met.
i
i
s
s
On the other hand, it can be shown that
h t
0 per every v 1 for i 1,,m n and h 0,,v 2 . Considering
i s
i s
i s
i s
these two relations, it can be concluded that v1 t 0 per every v 1 for i 1,,m n . These conditions conform to
those used for the verification of relation A R . In case that the relation is verified for the singular points situation, L'Hopital's rule can be used for v times to obtain equation (3-13) [7&1].
-
-
DETERMINATION OF AND ELIMINATION SINGULARITIES ON THE MOVEMENT ROUTE OF 4-RUU PARALLEL MANIPULATOR
-
Obtainment of the Workspace Including Singularities for 4-RUU Parallel Manipulator
Considering a PM as depited in figure (4) for the obtaining of workspace and in order to simplify and understand the longitudinal parameters of the used links, figure (5) portrays the longitudinal values for the simulation of the robots workspace only for two links thereof. It is evident that the variables pertinent to the other two links of the robot can be defined likewise. The first joint, situated in point Pa, is an active joint moving the manipulator. Thus, angle designates the singular values in inverse kinematic. A value from x, y and z coordinates should be assigned to each point of the link when performing encoding. The length f is the distance between the two points Pb to Pa mapped onto the plane y=0. Each point will be determined in the end of the link with a 3D vector specifying its position in space. Length of each link is fixed and within a distance e from the rotation center.
Figure (4): schematic view of 4-RUU PM for the obtaining of workspace
Figure (5): longitudinal parameters required for the drawing of 4-RUU PMs workspace
-
Considerations Related to Workspace Delineation
With the inverse kinematic analysis of the robot that determines the position of the active joints based on the final executors position, it is now possible to compute the joints distances. This allows the robot to specify the speed of the motors existent on the joints so that the final executor could be placed in an optimum position. There are various methods for obtaining the inverse kinematics of the robots and, as it was seen, Jacobian matrix was obtained for the robot in the chapter before the constraints specification. In fact, the inverse kinematic method can be used for the determination of the points the achievement of which is accessible to the mechanism designed for the robot. The shape and size of the workspace can be drawn in a process with the determination of the individual workspace points.
The first step in the calculation of inverse kinematic is mapping the final executors position on x-z plane. In this case, the length f is the distance between Pb to Pa mapped on plane y=0 and it can be calculated as explained underneath:
dy
dy
f d 2 P2 C
(28)
Now, it is possible to calculate the intersection locus of a circle with the center Pa and radius b and a circle with the center Pd and radius f, i.e. point Pb, given the two points of the workspace Pa and Pd, as two radii b and f from rotation center. The value of d, as the distance between Pa and Pd, will be:
d P P 2 P P 2
(29)
dx ax dz az
If d>b+f and d>0, the intersection point is credible hence computable. The aforementioned cases cause limitations to the d- value. Subsequently, values a and h and point coordinates b can be calculated as explained below:
b2 f 2 d 2
a 2 d
h b2 a2
(30)
(31)
P P
-
a Pdx Pax h Pdz Paz
(32)
bx ax d d
Pby 0
(33)
P P
-
a Pdz Paz h Pdx Pax
(34)
bz az d d
In the above equations, there are two possibilities (two points), Pbx, for the obtaining of the inter-circle intersection. The correct point will have a larger value and one of the answers will be removed from the state space because the two circles intersect one another in two points for the manipulators orientation. The angle between the two links will be carried out as below with the achievement of two points from each link:
tan1 Pbz Paz
Pbx Pax
(35)
It has to be noted in calculating the orientation of the other two links that it is enough to repeat the above-cited calculations for these links or the above analysis can also be rotated 120 degrees so that optimum answers can be obtained.
-
-
4-RUU Robots Workspace Delineation
The workspace of the robot without singularities elimination has been displayed in figure (4-3). The interesting feature of the delineated workspace is that the workspace limiting the joints rotation has taken the form of a slice of a spheres cross- section. In drawing the state space of the PM (figure 6), the link length of the final executor, c, has been assumed zero that means the trivialness of the final executors length in respect to the general space of robots movement.
(a)
(b)
Figure (6): delineation of 4-RUU PMs workspace for c=0; (a): view of the top and (b): view of the bottom
In figure (7), four various states have been considered for link c. The size of the vector pertaining to link c is in a range from zero to 40mm and the effect of these values on the workspace amount of robots movement will be analyzed. The positive direction of the vector is assumed to be upward in x-z plane. The larger the size of the vector the more extensive the workspace will be. It means that the robots placement in a horizontal plane featuring a positive direction provides for lesser encountering with singularities. When the vector related to link c is assigned a value equal to +40 (part (d) of figure (7)), it can be observed that the workspace becomes larger than normal state. In fact, this means the expansion of workspace following the change in the dimensions of PMs mechanism.
(a)
(b)
(c)
(d)
Figure (7): 4-RUU parallel manipulators workspace; (a): c=-20; (b): c=-40; (c): c=20 and (d): c=40
-
Inverse Kinematic Analysis
-
Jacobian Matrix Analysis and Delineation of a Workspace Free of Singular points
In mathematical terms, Jacobian matrix of PM relates the speed of the final executor to the speed of the mobile joints [67-69]. Zeroing of Jacobian matrixs determinant would be followed by the obtainment of the singularities in PM. Besides the calculations related to joint speed, obtained a little more computations in regard of robots dynamics gives the hardness matrix describing the link resistance of the final executor to the external forces. The obtained hardness matrix is of great importance in designing regards for its offering of the exact route and the amounts of larger load carriage.
The other importance of Jacobian matrix lies in its attainment of the singularities in workspace. Jacobian matrix needs links lengths for the analysis of inverse kinematics of the robot. In this section, an example is presented for the parametric analysis of one of the robots manipulators corresponding to figures (4) and (5). To inversely calculate the Jacobian Matrix, 1, 2 and 3 are used. In simple terms, kinematic equation of the robot takes the form = wherein is are the speed parameters in Cartesian space and are the speeds existent on joint space. In this case, Jacobian Matrix is defined as = 1.
Figure (8): schematic view of defining parameters in 4-RUU Robots Jacobian Matrix
Figure (9) exhibits amounts of state space through reduction of the singularities for link lengths of c =20mm and d=120mm as well as c=0mm and d=100mm. In order to have singularities better identified in state space, cross-sections have been considered of z-axis equal to 70mm, 100mm, 140mm and 170mm in the workspace. In the delineated diagram, the light blue and red points are adjacent to the singularities hence having a worse situation than the other points. Comparison of figures 9(a) and 9(b) makes it clear that, upon getting closer to zero, the length of the link c provides for a higher likelihood of singularity occurrence but for a lower number of points. It means that the link c covers the singularities hence it is useful for the expansion of the workspace. In order to perform a more precise comparison, figure (4-6) shows a cros-section of movement state space of robot along x-z plane.
Figure (9): delineation of workspace for 4-RUU PM with reduction of singularities in cross-sections of z-axis equal in size to 70mm, 100mm, 140mm and 170mm; (a): c=20mm and d=120mm and (b): c=0mm and d=100mm
Figure (10): delineation of workspace for 4-RUU PM with reduction of singularities in cross-sections of robots movement state space along x-z-plane; (a): c=20mm and d=120mm and (b): c=0mm and d=100mm
Using the proposed theory and the given constraints equations, the encoding of the limit method implementation was carried out parallel to the removal of robots workspace in certain points so as to obtain a robotic workspace devoid of singularities. After the exertion of the singular points on the robot, the 3D workspace is drawn as shown in figure (11). Since the effect of the singularities removal from workspace is not clearly visible in 3D space, vertical cross-sections equal in size to 70mm, 100mm, 140mm and 170mm have been prepared like previous section so that the effect of using limit method for the elimination of singularities could be clearly visible.
(a)
(b)
Figure (11): delineation of workspace of 4-RUU PM for a state of c=0; (a): view of the top and (b): view of the bottom
It becomes clear according to the figure that the obtained workspace has become free of singularities through the implementation of limit method. Furthermore, the dark blue points are workspace points less likely to reach the vicinity of singularities due to the implementation of limit method. However, with c-value approaching zero, the red points are risky points likely to reach the vicinity of singularities.
(a)
(b)
Figure (12): delineation of workspace of 4-RUU PM with the implementation of limit method for the removal of singularities in cross-sections of z-axis with sizes equal to 70mm, 100mm, 140mm and 170mm; (a): c=20mm and d=1200 and (b): c=0mm and d=100mm
-
-
-
-
CONCLUSION
It can be observed based on the results that the construction structure of parallel manipulators (PM) causes them to have a higher precision and precision in contrast to the serial manipulators. In specific terms, forward and inverse kinematics of the mechanism and the relationship between the drivers and the mechanisms final status were analyzed and it was seen that the results are consistent. The mechanism is uncontrollable in singularities hence incapable of tolerating the external load and torque. Due to the same reason, certain methods were obtained for singular points determination based on geometry of the ending part of the mechanisms workspace using singularities and Jacobian matrix and the mechanism parameters influencing the workspace were identified and the best of them was selected for the expansion of workspace. As it was observed in the test results, the model proposed in the present study possesses good accuracy for the controlling goals. The model that presents a continuous robot in the form of a collection of separate elements is not also faced with the singular computational states. The calculation volume of the model is also in an acceptable range and the time required for the implementation of the model for such applications as online control is also appropriate.
CONFLICTS OF INTEREST
The authors declare no conflict of interest.
REFERENCES
-
M. H. Saadatzi, Modeling And Control Of Redundant Parallel Robots Resistant Flexible Cables, Department Of Electrical And Computer Engineering Khajeh Nasir University
-
Zhao, J. S., Chen, M., Zhou, K., Dong, J. X., & Feng, Z. J. (2006). Workspace Of Parallel Manipulators With Symmetric Identical Kinematic Chains. Mechanism And Machine Theory, 41(6), 632-645.
-
Brisan, C., & Csiszar, A. (2011). Computation And Analysis Of The Workspace Of A Reconfigurable Parallel Robotic System. Mechanism And Machine Theory, 46(11), 1647-1668.
-
Hunt, K. H. (1978). Kinematic Geometry Of Mechanisms (Vol. 7). Oxford University Press, Usa.
-
Hao, K., & Ding, Y. (2006, June). Screw Theory And Singularity Analysis Of Parallel Robots. In 2006 International Conference On Mechatronics And Automation (Pp. 147-152). Ieee.
-
Merlet, J. P. (1989). Singular Configurations Of Parallel Manipulators And Grassmann Geometry. The International Journal Of Robotics Research, 8(5), 45-56.
-
Amine, S., Masouleh, M. T., Caro, S., Wenger, P., & Gosselin, C. (2012). Singularity Analysis Of 3t2r Parallel Mechanisms Using Grassmann Cayley Algebra And Grassmann Geometry. Mechanism And Machine Theory, 52, 326-340.
-
Gosselin, C., & Angeles, J. (1990). Singularity Analysis Of Closed-Loop Kinematic Chains. Ieee Transactions On Robotics And Automation, 6(3), 281-290.
-
Choi, H. B., Konno, A., & Uchiyama, M. (2010). Analytic Singularity Analysis Of A 4-Dof Parallel Robot Based On Jacobian Deficiencies. International Journal Of Control, Automation And Systems, 8(2), 378-384.
-
Zheng, T., Branson, D. T., Kang, R., Cianchetti, M., Guglielmino, E., Follador, M., … & Caldwell, D. G. (2012, May). Dynamic Continuum Arm Model For Use With Underwater Robotic Manipulators Inspired By Octopus Vulgaris. In 2012 Ieee International Conference On Robotics And Automation (Pp. 5289-5294). Ieee.
-
Jones, B. A., & Walker, I. D. (2006). Kinematics For Multisection Continuum Robots. Ieee Transactions On Robotics, 22(1), 43-55.