
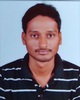
- Open Access
- Authors : Praveen Belligatti , Dr. D. K Kulkarni
- Paper ID : IJERTV11IS080017
- Volume & Issue : Volume 11, Issue 08 (August 2022)
- Published (First Online): 18-08-2022
- ISSN (Online) : 2278-0181
- Publisher Name : IJERT
- License:
This work is licensed under a Creative Commons Attribution 4.0 International License
Parametric Study and Optimization of Steel Dome Structure
Praveen Belligatti
Student
Dept. of Civil Engineering, SDMCET, Dharwad, India
Dr. D. K. Kulkarni
Professor,
Dept. of Civil Engineering, SDMCET, Dharwad, India
Abstract Domes are space constructions that offer an affordable way to cover a lot of valuable, column-free space. The utilization of domes can be seen in places like sports arenas, assembly halls, exposition centers, malls, industrial complexes, etc. This feature offers efficiency in the use of building materials and attractive appearance. The dome is used as a space truss in this article, with all joints being pinned to provide a torsion- and moment-free structure. As a result, only tensile and compressive forces are applied to all members. Even though only axial forces considered when designing a dome. So an effort to create software in Octave has been made. The program can be used to configure, analyze, design, and optimize the weight of a steel dome. The effects of the dead load and live load have been taken into account when designing the members, which are made of tubular steel sections.
To establish the relationship between weight variation and dome height, a parametric analysis was also conducted. For the domes with bracings in one or both directions, this analysis is expanded. It is also done a parametric analysis for the optimization of the dome using various methods, such as with discrete and continuous variables. Weight variation according to the number of plan segments has also been done.
Keywords:- Dome, Optimization, Octave, Bracings, etc..
- INTRODUCTION
Architects and engineers are constantly looking for new ways to solve the problem of space enclosure. Because of their diversity and flexibility, In their search for novel forms, architects and engineers might use space structures as a useful tool.. A three-dimensional collection of components known as a space structure is capable of withstanding loads that can be applied from any location. The proliferation of the space frame in recent decades has been primarily due to its great structural potential and visual beauty. Sports stadiums, exhibition pavilions, assembly halls, transit hubs, aviation hangars, workshops, and warehouses are just a few of the building types that utilize space frames. They have been utilized for mid- and short-span enclosures in addition to long-span roofs as roofs, floors, exterior walls, and canopies. A well-known illustration of space is a dome.
Domes have stimulated people’s interest because they enclose the most space with the least amount of surface area. This feature saves money by reducing the consumption of building materials. Despite the fact that stone was the only structural material used in ancient times, brickwork gradually replaced stone masonry. Timber was used for the same purpose in Middle Ages. However,
significant advancements in dome structures began with the development of the steel industry in the nineteenth century. This allowed the engineers to design large spanned and multi-story steel structures. Steel is now widely used to enclose large spans of length.
Because it depends on an engineer’s skill to iteratively consider several feasible shapes and sizes for each component of a certain construction using a computer, structural design has historically been a less-than-ideal procedure. This is just a fast variation of the same computations performed by engineers of the last century, but not a real improvement to the design process. During the last few years, a lot of work has been done to fully automate the design of structures. Nonetheless, most of the new methods developed share a common flaw: they are based on linear programming techniques, and thus treat structural optimization as if the search space is continuous, when it is actually discrete due to the limited number of structural shapes available on the market. These issues can be resolved using mathematical programming techniques for optimizing steel dome structures. Because total weight of structure is easily accessed by economy, an attempt is made here to reduce total weight of structure.
The utilization of a constrained issue search technique via mathematical programming is the main topic of this thesis. With minimal modification, the created code can be applied to a wide range of steel truss dome construction configurations.
- OBJECTIVES
- To develop software of computer programs in Octave programming language that will generate configuration and loading data, analyze the structural response, design and optimize the weight of domes. Only dead load and live load are considered in the present study. Design of members is done as per IS: 800- 2007 code.
- Weight Optimization is done through the process non linear constrained optimization method.
- Parametric study for weight variation of dome considering various parameters like height, number of sectors in plan and different variable approaches.
- METHODOLOGY
The Octave programming language was utilized to optimize the steel dome. The data is generated, the structure is analyzed and designed using a set of programs developed, and optimization is performed using the same programming language and the precise penalty approach.
In this chapter, the methodology adopted in data generation, analysis and optimization of dome structure has
Slope (in degrees) of segment considered,
been discussed. The codes developed to construct the programs, their logic and flow charts have been detailed.
slope = tan1 [(
+
) ( 180 )]
3.142
Flow Chart
PROCEDURE FOR DATA GENERATION FORMULAE USED IN DATA GENERATION
In following fig.6.2, the label B shows the base diameter and h is the height of the dome. Few used in data generation process are listed below.
Fig. 1.1 Data generation for steel dome
Radius of curvature of the dome
2
= +
where , is height of the segment considered from base .
= i ×
_sec _
where i is the i th segment along height
The coordinates of nodes can be calculated by using the formula
=
=
=
where j is jth sector along plan,
= 360
_sec
where n_sec_ht is number of segment along height
n_sec_plan is number of segments along plan FLOW CHART FOR DATA GENERATION
The flow control between various steps involved in data generation of dome is shown in fig 6.3. The connector D shown indicate the modification in the material properties of the member within optimization process. The optimization flowchart in Fig. 6.6 shows linking of D.
8 2
Distance from center of curvature to base ring of dome
= 2 (2)2
2
Radius at the i th segment level
Flowchart for data generation program
PROBLEM FORMULATION
The optimization problem is derived as follows to reduce weight.
Weight = density × volume
=density × area × length W = × V = × A × l
= 2 (
+2 2
)
2
Objective function:
To minimize the objective function:
W=
× ×
=1
where, n – number of members
-density
-cross-sectional area of i” th member
-length of i”th member
Subjected to constraints,
- For maximum tensile and compressive stress
| ()|
where,
i = 1, 2, 3.n = no. of members
p>(6.7)
j = 1, 2, 3.m = indicates loading conditions
= allowable stress in tension and compression
- For maximum buckling stress (slenderness ratio)
(x) (x)
where,
Pi (x) = bulking stress in member i
2
p=buckling load=
2
Fig. 6.5 Flowchart for Design
- For maximum deflection
(x)
where ,
= maximum allowable deflection
(span/360)….[IS:800-2007]
- For upper and lower limit of cross sectional area
- For maximum tensile and compressive stress
- RESULTS AND DISCUSSION
This thesis investigated the use of programs developed for the optimum structural design of 3-D dome structures. These strategies have been studied in terms of their application, efficiency, and success in solving dome structural challenges.
()
where,
()
A parametric study has been carried out by varying the
height, approaches for optimization (discrete and
()
()
= Lower bound area
= Upper bound area
UNCONSTRAINED PROBLEM
continuous variable), varying the number of sectors along
plan of the dome for selected base diameters. Results are in the form of tables and graphs and a discussion of the results is presented.
For penalty, the limited problem must be converted to an unconstrained one. The formulation of an unconstrained equation for the problem outlined in Chapter 4 is shown in the following equation.
PARAMETRIC STUDY
A detailed parametric evaluation of the various factors affecting the behavior of the dome structure is carried out. The program developed can analyze design and optimize the dome members without user interaction. In order to
1
f(x, (0))=
+[]{[
-|
()|] + [
- –
carry out the parametric study, base diameters, 20m, 30m,
(x)] + [ – (x)] + [ – ()
] + [()
– ]}2
40m, 50m, 60 m and 70m are considered. The study is
conducted for domes without bracings, domes with single
Here is the penalty term and(0)) is the initial penalty
parameter.
DESIGN OF DOME
Each dome member is designed as a tension or compression member using the limit state method
FLOWCHART FOR DESIGN OF DOME
The flow control between various steps involved in design of dome is shown in following chart
bracings and domes with double bracings.
VARIATION OF WEIGHT OF DOME WITH HEIGHT
The height is changed between 1/5th and 1/10th of the base diameter. There are 16 sectors in the plan and 8 segments along the height. The total optimum weight of structure for these various heights is for single braced domes.
Assum ed areas (in 2)
Area after 1st iteration (in 2)
Area after 2nd iteration (in 2)
Area after 3rd iteration (in 2)
Area after 4th iteration (in 2)
Area(in 2) obtained
by auto select list option
1 500 182 182 182 182 732 2 500 830 830 830 830 861 3 500 660 660 660 660 788 4 500 430 430 430 430 254 5 500 910 880 880 880 861 6 500 780 750 750 750 861 7 500 650 650 650 650 861 8 500 2080 2080 2080 2080 861 9 500 1080 1080 1080 1080 1730 10 500 850 850 850 850 1250 11 500 840 840 840 840 1110 2400
Cross section area
(Sq.mm.)
1800
1200
600
0
1 2 3 4 5 6 7 8 9 10 11
Group Number
Assumed areas
Area after 1st iteration
2400
Optimization of cross sectional area applying different
initial area (area in mm2)
Variation of total weight with different heights of the dome
Base dia (M) Ht (m) Ht Optimum wt of the structure (KN) 20 4.00 B/5 32.942 3.33 B/6 32.515 2.86 B/7 32.196 2.50 B/8 31.887 2.22 B/9 31.925 2.00 B/10 32.484 30 6.00 B/5 71.425 5.00 B/6 70.924 4.29 B/7 69.993 3.75 B/8 64.494 3.33 B/9 69.833 3.00 B/10 70.011 40 8.00 B/5 132.253 6.67 B/6 131.503 5.71 B/7 130.614 5.00 B/8 130.179 4.44 B/9 131.19 4.00 B/10 132.351 50 10.00 B/5 240.041 8.33 B/6 238.282 7.14 B/7 237.027 6.25 B/8 235.572 5.56 B/9 237.536 5.00 B/10 239.899 60 12.00 B/5 375.097 10.00 B/6 372.728 8.57 B/7 370.124 7.50 B/8 368.102 6.67 B/9 374.020 6.00 B/10 380.012 70 14.00 B/5 537.421 11.67 B/6 539.890 10.00 B/7 542.384 8.75 B/8 544.416 7.78 B/9 538.492 7.00 B/10 532.516 1800
1200
600
0
<>1 2 3 4 5 6 7 8 9 10 11
Group Number
Assumed areas
Area after 1st iteration
Optimization of cross sectional area applying uniform
initial area (area in mm2)
Group Number Assumed areas (in 2)
Area after 1st iteration (in 2)
Area after 2nd iteration (in 2)
Area after 3rd iteration (in 2)
Area after 4th iteration (in 2)
1 1000 182 182 182 182 2 1000 830 830 830 830 3 1000 660 660 660 660 4 1000 430 430 430 430 5 500 940 880 880 880 6 500 780 750 750 750 7 500 650 650 650 650 8 500 2080 2080 2080 2080 9 100 1080 1080 1080 1080 10 100 850 850 850 850 11 100 840 840 840 840 350.000
160
140
120
100
80
60
40
20
0
40m Dome with diffrent approaches
Without bracing Single bracing Double bracing
131.47
124.710
103.96
97.030
74.207
68.130
Discrete approach
1
Continuous approach
2
312.469
300.000
250.000
244.948
220.036
200.000
179.888
181.978
168.687
161.872157.611
166.023
Weight(KN)
Weight(kN)
VARIATION OF WEIGHT OF DOME WITH NUMBER OF SECTORS IN PLAN
The number of sectors in plan and number of segments along height also have an influence on total weight of the structure For the study, 10° to 45° differences in angle between sectors in plan are studied, with the number of sectors varying between 8, 10, 12, 16, 20, 24, 30, and 36. During this parametric analysis, the number of segments along height is held constant at 5. The structure’s weight varies as the number of sectors changes. First, it reduces the number of sectors by up to 24 for base diameters of 50m and 60m domes. This demonstrates that having 24 sectors reduces the weight of the dome structure. The variation of this number of sectors in plan and weight of structure is shown in Tables 7.9 to 7.10
Base diameter (Meter) No of sectors in Plan (deg.) No. of segments along height Weight (KN) 50 8 45 5.00 312.469 10 36 5.00 244.948 12 30 5.00 220.036 16 23 5.00 179.888 18 20 5.00 168.687 20 18 5.00 161.872 24 15 5.00 157.611 30 12 5.00 166.023 36 10 5.00 181.978 Weight of dome for different no. of sectors in plan for base diameter of 50m
8 10 12 16 18 20 24 30 36
No of sectors in Plan
150.000
100.000
50.000
0.000
Variation of weight of dome with number of sectors in plan for base diameter 50m
- –
- CONCLUSIONS
-
- As only gravity loading is considered, total weight of the structure increase as bracing members are added to the domes.
- The weight of the dome decrease as height of dome decreases from1/5th times the base diameter to height equal to 1/8th times the base diameter It demonstrates a maximum weight decrease of 3.2 percent for height variations ranging from 1/5th to 1/10th times the base diameters.
- The wt of dome reduces considerably if the number of sectors along plan is 24 for domes of base diameter of 50m and 60m considered for gravity loading.
- The difference in the weight by the 2 approaches (continuous variables and discrete variables) for dome without bracing is 8.19%, for domes with single bracing is 6.67% and for dome with double bracing is 5.14%.
- The results obtained for cross sectional area of members by designing (auto select option) in SAP 2006 was greater than that obtained by software developed in Octave. This shows the efficiency of the software developed
REFERENCES
[1] Tugrul TALASLIOGLU, ” Design optimisation of dome structures by enhanced genetic algorithm with multiple populations” , Scientific Research and Essays Vol. 7(45), pp. 3877 -3896, 19 November, 2012 [2] S. Çarba and M.P. Saka, “Optimum design of single layer network domes using harmony search method”, asian journal of civil engineering (building and housing) vol. 10, no. 1 (2009)Pages 97-112
[3] Wuxi, Jiang Su China, “Lectotype Optimization of Single-Layer Steel Reticulated Dome Based on Sectional Optimization”, 2010 Third International Conference on Information and Computing [4] H. S. Jadhav, Ajit S. Patil Parametric Study of Double Layer Steel Dome with Reference to Span to Height Ratio, International Journal of Science and Research (IJSR), India Online ISSN: 2319-7064 [5] O. Hasançebi, F. Erdal, M. P. Saka, ” Optimum design of geodesic steel domes under code provisions using metaheuristic techniques”, International Journal of Engineering and Applied Sciences (IJEAS) Vol.2, Issue 2(2010)88-103 [6] Galawezh Saber, Nildem Tayi, Ghaedan Hussein, “Analysis and Optimum Design of Curved Roof Structures”, 2nd International Balkans Conference on Challenges of Civil Engineering, BCCCE, 23-25 May 2013, Epoka University, Tirana, Albania. [7] J. Farkas, “Mathematical and technical optima in the design Of welded steel shell structures”, international journal of optimization in civil engineering Int. J. Optim. Civil eng., 2011; 1:141-153 [8] Matteo Dini, Giovani Estrada2, Maurizio Froli, Niccolò Baldassini, ” Form-finding and buckling optimization of gridshells using genetic algorithms”, Proceedings of the International Association for Shell and Spatial Structures (IASS) Symposium 2013