
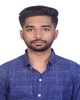
- Open Access
- Authors : Dirghanshu Pravin Devre , Hrushikesh Nitin Kharote , Abhiram Chandrashekhar Pande , Dr. Anand Relkar
- Paper ID : IJERTV11IS060134
- Volume & Issue : Volume 11, Issue 06 (June 2022)
- Published (First Online): 20-06-2022
- ISSN (Online) : 2278-0181
- Publisher Name : IJERT
- License:
This work is licensed under a Creative Commons Attribution 4.0 International License
Pochamatic Every Smart Home Deserve It
Dirghanshu Pravin Devre
Mechanical Department
School of Engineering & Techonology, Sandip University Nashik , Maharashtra
Prof Dr. Anand Relkar
Mechanical Department School of Engineering & Techonoloy,
Sandip University Nashik , Maharashtra
Hrushikesh Nitin Kharote
Mechanical Department
School of Engineering & Techonology, Sandip University Nashik , Maharashtra
Abhiram Chandrashekhar Pande
Mechanical Department
School of Engineering & Techonology, Sandip University Nashik , Maharashtra
Abstract:- Automatic floor cleaner is a compact robotics system which provides floor cleaning service in room and big offices reducing human labour. Basically, as a robot it eliminates human error and provide cleaning activity with much more efficiency. If we clean the floor manually then there is a possibility that the operator will leave some portion of the floor. Also due to manual labour involved this is time consuming and irritating to clean the floor. This is where the robot comes as an advantage. Also, the robot is small and compact in size. So, we can carry it and place it wherever we can on the house. The flexibility, time saving and efficiency make the robot a clean choice for cleaning the floor. The entire floor cleaning robot is divided into several parts, namely consisting of an Infrared Sensor, DC Motor, Step Up and Down Power controller. This tool works when the Arduino Uno microcontroller processes the ultrasonic sensor as a distance detector and a DC motor as a robot. It will be totally controlled by app and with the help of Bluetooth connectivity takes place. When an ultrasonic sensor detects a barrier in front of it, the robot will automatically look for a direction that is not a barrier to the floor cleaning robot. The aim of this work is to develop and modernized process for cleaning the floor with wet and dry. This machine is capable of performing cleaning of floor in dry as well as wet condition, and it also have storage box to store a dust.
-
Conclusion
Reviewing various literatures on floor cleaning machines it is concluded that there are certain limitations in floor cleaning machines which can be worked upon. For example, cleaning machines are made with an aim to clean only dry surface of the floor. This means that they are not use for wet surface of the floor. This is the major issue for cleaning the floor surface but in case of wet surface, floor cleaning machines contain moisture or little amount of water on the surface of floor. This machine can work in both dry and wet conditions. And at last this machine can dry the wet surface with the help of hot blower. The main catch in our project is the application which we have made in MIT inventor with the help of python in coding, it directly guides the surface cleaner and thus it performs the same. The ultimate need of this machine is satisfied and with the help of this machine can clean the floor easily. The application of this machine is high when compared to other existing floor cleaning machines. Overall, the concept is very much helpful and there is scope of a lot of development in mechanical parts
-
Gaph Finding
We found several gaps while going the research paper, which brought to a conclusion to fill the gaps as much as possible. The main loop hole which we found in major project was of lack of use of technology. So, we have tried to make an app which will control the robot aka surface cleaner. App and robot will be connected with the help of Bluetooth. It can be used manually as well as automatic, joystick is provided in the application.
For outer casing and inner parts where 3d printing is required there we have used PLA (polyatic acid) material for the same. The main advantage of using it is PLA is made from renewable raw materials. It has a reduced carbon footprint compared to fossil-based plastics. two reasons: crops absorb co2 when growing; It takes less energy and this produces less greenhouse gas to produce PLA than fossil-based plastic PLA is made in the USA (Nature Works Ingeo). PLA melts more easily because it has a lower melting point than many fossil- based plastics. Its easy to work with PLA and it requires less energy to transform. One of the two most used plastics in 3D printing (45% market share). It has a low melting point, inexpensive, easy-to print, no fumes. Its the best option in case of 3D printing. PLA is compostable. When PLA is incinerated, it emits fewer toxic fumes than oil-based plastics Food Contamination of food packaging is not a problem, unlike with plastic recycling. In case of biomedical use, PLA degrades into non-toxic acid
-
INTRODUCTION
Floor Cleaning has always been an integral part of the daily health and hygiene routine, be it a household or an industry. Floor cleaning is mainly of two types- Dry cleaning, which mainly involves removal of dust and particulate matter and wet cleaning, which involves cleaning of the surface with the use of water and other floor disinfectants to clean the floor of liquid waste. But recent statistics have shown an increasing number of slip and fall incidents due to the unclean floor and have an alarming impact on the safety of the people walking on floors at public places. 15% of the death takes place due to slip and fall. 1 in 6 workplace accidents is caused due to ineffective floor and surface cleaning. The reason behind the
same is ineffective cleaning because it is considered as menial and being a very laborious task to do. If we talk about dry cleaning processes, it has taken a greater advancement leap with the introduction of vacuum cleaners. This enables people to easily remove dust and particulate matter not just in industries but in households. But in case of the wet cleaning process or mopping, there hasnt been any major technological advancement and thus makes it much more unappealing to do. Thus, there is an emerging need of a paradigm shift in the field of mopping to more technologically sound machinery.
Here we are dealing with IOT based technology for cleaning purpose. We have tried to cover 3 tasks at the same time which are sweeping, vacuuming and moping
-
PROBLEM STATEMENT
During COVID-19 lockdown additional cleaning and hygiene maintain with no house help was extremely difficult and to also have to work from home & to save some quality time for personal growth was proving to be difficult.
To overcome this we problem, A robot suitable with industry
4.0 was necessary which can reduce human dependency and can perform daily task with same efficiency
-
Objective
Accepted & adopted Industry 4.0 to day-to-day life
To scan the obstacles earlier than the robot and to avoid collision when the robot is in motion.
To try to mop and sweep at the same time Ease in day-to-day operation
To save time
To reduce human efforts To reduce the cost
-
-
METHODOLOGY OF MANUFRACTURING
-
ELECTRICAL COMPONENTS
-
Set the requried standards of device.(Speed, cleanning radius, Weight, Operational Hours, Shape, Height, Turnning radius, Height above the surface.
Sr. No
Name
Description
Quantity
01
Bluetooth Module
SPP-C Bluetooth serial pass- through module wireless serial communication from machine Wireless SPPC Replace HC-05 HC-06
1 Pcs.
02
Infrared Sensor
/td>
IR Infrared Obstacle Avoidance Sensor Module for Arduino Smart Car Robot 3-wire Reflective Photoelectric
6 Pcs.
03
DC Motor
N20 DC12V 100RPM Gear
Motor 3mm Shaft Diameter
2 Pcs.
04
Battery Case
DIY Black Storage Box Holder Case For 3 x 18650 3.7V
2 Pcs.
05
IRF 520
0-24V Top Mosfet IRF520 MOS Driver Module
2 Pcs.
06
DC Female Jack Connector
3A 5.5×2.1mm DC Power Sock Jack Female Connector
1 Pcs.
07
BMS
3S 20A Li-ion Battery 18650 Charger 12.6V Cell 64x20x3.4mm.
PCB BMS Protection Boards Modules
1 Pcs.
08
Step Up Power converter
DC Stepper Motor Drive Controller Board Module L298N
1 Pcs.
09
Step up Boost Power Converter
XL6009 DC Step up boost Power Converter Module LM2577
1 Pcs.
10
PWM Blower Server
PWM blower server dedicated turbofan 9733 97x97x33mm 9.7cm 12V fan
1 Pcs.
11
Rechargeable Battery
Li-ion 2600 – 3000mAh 18650
rechargeable battery
6 Pcs
12
Battery Charger
12.6V charger for CCTV battery pack,3A lithium battery 12V
1 Pcs.
13
Switch
Switch 15 x 21 mm.
1 Pcs.
14
Battery Indicator
3S 3 Series Lithium Battery Capacity Indicator Module 12.6V
1 Pcs.
15
Speed Measuring Module
HC-020K Double Speed Measuring Module with Photoelectric Encoder
2 Pcs.
16
Arduino Nano
Pro Mini Atmega168 5V 16M For Arduino Nano Module
1 Pcs.
17
Step-Down Power Converter
DC Step Down Converter Module LM2596 DC 4.0~40 to 1.3-37V
2 Pcs.
18
End Switch
3D Printer RAMPS 1.4 End Stop Limit Switch Module
2 Pcs.
19
Cable
Cable 20-30-40cm 2.54mm 1pin Female to Male, Male to Male, Female to Female jumper wire for Arduino
20-30-40 Cms
20
USB Wire
Connector Wire for Arduino, for programming
1 Pcs.
21
Wheels
1:48 Remote Car Robot Gears Driver Motor
2 Pcs.
1st Step
-
Select the Electric Components based on above requriment
-
Measure and weight each and every component selected
2nd Step
-
Choose the desire shape of device (Cylindrical) and make the rough assembly of the device.
-
Adjust the shape and diameter of body depending by using trial and error methord
3rd Step
-
After completing the assembly. Use simmulations, and analysis to check the requied output.
4th Step
-
Convert all the body parts in STL format and print it with help of 3D printer
-
Assemble the parts once the printing is completed.
5th Step
-
-
METHOLOGY OF WORKING
Modeling (FDM) printers followed by 3D printing materials using other technologies.
Application Control
Bluetooth Module
-
Power
Ardunio IR Inputs
Motor Driver Unit
Motor
-
Selection criteria for PLA?
PLA plastic or polylactic acid is a vegetable-based plastic material, which commonly uses corn-starch as a raw material. The monomer is usually made from fermented plant starch. This material is a thermoplastic aliphatic polyester and it is the primary natural raw material used in 3D printing. PLA is a fully biodegradable thermoplastic polymer consisting of renewable raw materials. Among all 3D printing materials,
PLA is part of the most popular materials used for additive manufacturing for filament fabrication.
PLA is a bioplastic, used in 3D printing using the FDM (Fused Deposition Modeling) technology, and along with ABS (Acrylonitrile Butadiene Styrene), this material is one of the standard materials for this technology.
There is often a tendency to compare these plastic materials, as they are the two most common alternatives available for consumer printers. PLA plastic material is easy-to-use and offer some interesting mechanical properties.
-
-
3D PRINTING
3D printing, also known as additive manufacturing, is a method of creating a three-dimensional object layer-by-layer using a computer created design.
3D printing is an additive process whereby layers of material are built up to create a 3D part. This is the opposite of subtractive manufacturing processes, where a final design is cut from a larger block of material. As a result, 3D printing creates less material wastage
A. Classification of material
When youre deciding on what 3D printing materials you should choose for your job, you have to factor in the application, function, and design of your component or product.
3D printing materials come in a wide array of forms. Most consumer 3D printed products are made from thermoplastics. Designers and engineers prefer creating functional prototypes from 3D printing materials that have the same or similar material properties as whats used in creating the finished product.
Plastics are the most widely adopted 3D printed material – and it comes in filament, resin, granule, and powder forms. Most thermoplastic 3D printing materials can be used in home 3D printing technology and professional applications as well.
The basic classification for 3D printed materials is mention below with various properties and uses, starting with the different filament types available for Fused Deposition
PLA material is printed using 3D printers and mainly used to manufacture big parts up to 1x1x1m.
Even if this PLA material offers the opportunity to 3D print impressive big parts, but material design guidelines have to take into consideration before printing to avoid any problem during additive manufacturing process.
-
MECHANICAL & ELECTRICAL COMPOENTS ASSEMBLY
-
PROGRAMMING
-
MIT Inventor :
App Inventor lets you develop applications for Android phones using a web browser and either a connected phone or emulator. The App Inventor servers store your work and help you keep track of your projects.
-
Why C Language is used in programming of Arduino?
The Wiring and Arduino both use C/C++ as programming languages and Arduino uses a simplified version. Processing used Java as a programming language but served as the basis for Wiring, which was the basis for Arduino
-
Why java is used in programming of application?
AVA gives the best option for development of mobile applications that are based on Android, as Android consist of its own APIs and JAVA libraries.
So, for Android applications, you use android APIs as well as JAVA to write code for Android apps.
-
-
ADVANTAGES
-
Obstacle Avoiding
-
Automatically adjust to different motions
-
No Operator is required
-
Low Maintenance
-
Able to go under furniture & Around corners
-
Larger Dust Box
-
Longer Life-Span
-
No Wires or difficult wiring
-
Smart Home Connectivity
-
Easy to control with application
-
Time-Saving
-
Noise less operation o Integrated Dust Bin o Low Maintenance
-
Obstacle Avoiding
-
Easy to Programmable and to modify
-
WIFI & Bluetooth Connectivity.
-
-
FUTURE SCOPE
-
The device can be modified to use in Library, Classroom, Hospitals, Hotels.
-
With the proper modification is can also separate dry
& wet dust. Thus, it can be used in poultry farms to collect birds/animals waste (Excrement)
-
With Solar charging or solar roof down time can be reduce
-
Some additional feature to be taken into consideration,
-
Self-charging
-
Automatically Adjust to Different Surfaces
-
Schedule Cleaning
-
Enable to Set virtual Boundaries
-
Pet Friendly
-
Children & Toddlers friendly
-
Ability to Scan the room
-
Voice Assisting Features
-
Automated Cleaning and Scheduling features
-
-
CONCLUSION
-
This paper has presented and described the Aurdino-based Remote-Controlled Floor Cleaning Robot device. Additionally, it is also an effort to utilize the integrated sense of technology from different disciplines to scale technology used for the requirement of household purposes. We have
mentioned and clarified the requirements of the model and developed it to satisfy the requirements. This particular device has allowed us to attach both the process of vacuuming and moping into a single device. Experimental results target task clearly showed that the developed strategy was useful for developing the autonomous service robots. The developed propositions are useful for both extending robots ability and developing a new platform. Though a lot of changes can be inculcated in this like using solar, self-battery charging, etc which can also be classified in future scope. We can make it avoid rugged surfaces and walls. As always, possibilities are endless.
XIII. REFERENCES
[1] AUTOMATION AND CONTROLLING OF AUTOMATICFLOOR CLEANER, Rajaranjan Senapati
[2] Automatic Floor Cleaning Robot Using Arduino and Ultrasonic Sensor, Yuda Irawan, Muhardi Muhardi, Rian Ordila, Roni Diandra [3] Design and Development of an Automated Floor Cleaning Robot for Domestic Application, Raveena Ishalavath M, Sandhyashree N,Rakshitha R, Arpitha Shankar
[4] Design and Fabrication of Manually Operated Floor Cleaning Machine, Dr. Shailesh Dhomne, Rahul Gajbhiye, Ashutosh Singh, Pankaj Prajapati, Sachin Shende, Sumit Binzade [5] Multitasking floor cleaning machine, Madan Jagtap, Uttam Mourya,Suhas Deore, Akash Shrimandle, Faisal Usmani
[6] A Tiling-Theoretic Approach to Efficient Area Coverage in a Tetris- Inspired FloorCleaning Robot, PRABAKARAN VEERAJAGADHESWAR, MOHAN RAJESH ELARA, THEJUS PATHMAKUMAR, AND VENGADESH AYYALUSAMI [7] Remote Controlled Autonomous Floor Cleaning Robot, R.Senthil Kumar, Vaisakh KP, Sayanth A Kumar, Gaurav Dasgupta [8] Voice Controlled Smart Floor Cleaning Robot, R. N. Kulkarni,Shwetha Joshi, Sneha K, Shilpa R, M Shamili
[9] SOLAR OPERATED MULTIFUNCTIONAL FLOOR CLEANINGMACHINE, Vikrant Bhute, Piyush Ladse, Aniket Ingle, Nitesh Rane [10] A RESEARCH PAPER ON DESIGN AND DEVELOPMENT OF
FLOOR CLEANING MACHINE, Muhammad KashifShaikh Ghaffar, M. AadilArshad, Nandkishor S.Kale, Ansari M Bilal, Prof.
D. M. Ugle
[11] Arduino Based Cleaner Robot, Shubham Tiwari, Prof. Sangeeta Kotecha, Gaurav Rasal, Pramod Shukla, Ajinkya Mandavkar [12] Design and Analysis of Manually Operated Floor Cleaning Machine,M. Ranjit Kumar, N. Kapilan
[13] ARDUINO BASED DRY & WET AUTOMATIC FLOORCLEANER, Akanksha Vyas, Satyam Chourasia, Shubham Antapurkar, Raghvendra Prasad
[14] REVIEW PAPER ON FLOOR CLEANING MACHINE, Niravshah, Rohit Jadhav, Amogh Malekar, Hasim shah, Chetan thakur [15] Design and Fabrication of Arduino Operated Floor Cleaning
Machine, Pranav Doijad, Vikas Chavan, Sagar Todkari, Hrishikesh Surya, Kolambe C.E.