
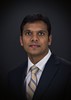
- Open Access
- Authors : Aravind Potturu
- Paper ID : IJERTV9IS110099
- Volume & Issue : Volume 09, Issue 11 (November 2020)
- Published (First Online): 21-11-2020
- ISSN (Online) : 2278-0181
- Publisher Name : IJERT
- License:
This work is licensed under a Creative Commons Attribution 4.0 International License
Prediction and Optimization of CNC Drilling Process of Biocompatible Materials
Aravind Potturua*
aResearcher, Smart Factory, Enterprise Performance, Deloitte LLP, USA
Abstract:- Titanium alloy has a prominent role in various fields and especially, in medical science and its field of applications because of its bio-compatibility. The biocompatible alloy when grafted in joints generally needs drilling operation for securing implants with natural bone. It is very essential to understand the parameters for the drilling process. The present work proposes a numerical approach to study the effect of various drilling parameters on the performance measures such as circularity, thrust and torque produced when CNC drilling is carried out on titanium alloy. The study provides an inexpensive time saving alternative to study the performance of machining before going for actual cutting operation. An optimal parametric setting has been proposed to guide the practitioners for improving accuracy of drilled holes during implanting of titanium alloy.
keywords: CNC drilling; Ti6Al4V; simulation and DEFORM-3D software
-
INTRODUCTION
Bone grafting is a surgical procedure aimed at replacing missing bone during repair of bone fractures. Repairing of bone fracture is extremely complex and poses a significant health risk to the patient or fail to heal properly. Due to adverse antigenic responses, xenografts are not considered suitable for bone grafting [1]. Till date, a large variety of material has been investigated for the orthopedic applications. However, bio-compatibility and bonding characteristics of the metallic materials with natural bone is still questionable [2,3]. Because of superior mechanical and physical properties such as high yield stress, highly corrosion resistance, high creep and high strength to weight ratio, toughness, wear resistance, and good biocompatibility [4-5] titanium alloy Ti6Al4V is widely used. Drilling is a method of machining by cutting used for making holes by means of twist drills. The principal metallic materials used in field of biomedical engineering are titanium, aluminum, stainless steel, cobalt-chromium alloys and titanium alloys [2]. Limited studies report on drilling of titanium alloys. Sakurai et al. [7-9] have studied on mechanical strength improvement and machining of Ti6Al4V. Grafting generally needs drilling of holes to join implant materials and natural bones. Simulation of drilling process for biocompatible alloy has been carried out to study the effects of various drill parameters on responses. Hong-bing et al. [10] developed a model to investigate the static and dynamic property of titanium alloy. Kilickap [11] suggests optimization of drilling parameters using design of experiment approach.
In this study, an FEM approach is proposed for analyzing influence of drilling parameters like spindle speed, feed rate and drill diameter on process responses such as circularity, thrust and torque using bio-compatible material (Ti6Al4V) as work piece. Drilling simulation has been developed by DEFORM-3D. The multiple responses are converted into an equivalent response using grey relation analysis. Finally, process parameters are optimized to provide best parameter setting for multiple responses. The study helps the practitioner to understand the process responses without resorting to expensive and time- consuming experimentation.
Nomenclature
Nomenclature
Nij Xij
ij
S/N
normalized value value of responses
absolute value of the difference of Xoj and Xij distinguishing grey co-efficient
grey relation grade signal to noise ratio average of S/N ratio
Nij Xij
ij
S/N
normalized value value of responses
absolute value of the difference of Xoj and Xij distinguishing grey co-efficient
grey relation grade signal to noise ratio average of S/N ratio
-
EXPERIMENTAL DESIGN AND SIMULATION APPROACH
A 3D model is developed using commercial finite element software DEFORM-3D. The model aims to simulate the drilling process, to predict the thrust and torque in the work piece material throughout the drilling process; and to predict the circularity at the entrance and at the exit sides. The FE model is based on Lagrangian formulation with explicit integration method. However, the tool is assumed fully elastic material, it is workpiece as a rigid body. The contact and the friction parameters between the tool and work piece are influenced by a number of factor such as rotational speed, feed rate and the drill diameter.
The shear friction co-efficient of 0.6 and elementary shape of tetrahedral is taken into account. In this study, the chip is not modeled due to computational cost therefore the friction between the chip and drill is ignored.
In order to reduce the computational cost, achieve best cutting quality and save of time Design of experiment approach is considered. The inputs spindle speed, feed rate and drill bit diameter are at three levels in which Taguchi L9 orthogonal (Table 2.) approach is used to develop a relationship between parametric inputs and output responses; was used for conducting experiments. The experimental responses circularity, thrust and torque are summarized in Table 3.
Table 1.Control Parameters Table 2. Taguchi L9 orthogonal experimental setup
Control parameters
Level 1
Level 2
Level 3
Spindle speed rpm
1500
1650
1800
Feed rate mm/rev
0.5
0.65
0.8
Drill bit diameter mm
4
5
6
Spindle speed rpm
Feed rate mm/rev
Drill bit diameter mm
1500
0.50
4
1500
0.65
5
1500
0.80
6
1750
0.50
5
1750
0.65
6
1750
0.80
4
2000
0.50
6
2000
0.65
4
2000
0.80
5
Control parameters
Level 1
Level 2
Level 3
Spindle speed rpm
1500
1650
1800
Feed rate mm/rev
0.5
0.65
0.8
Drill bit diameter mm
4
5
6
Spindle speed rpm
Feed rate mm/rev
Drill bit diameter mm
1500
0.50
4
1500
0.65
5
1500
0.80
6
1750
0.50
5
1750
0.65
6
1750
0.80
4
2000
0.50
6
2000
0.65
4
2000
0.80
5
-
CALCULATION OF THRUST FORCE AND TORQUE
The drilling operation includes various parameters such as cutting force, thrust force, cutting speed, feed rate and torque etc. are included in drilling operation. Empirical formulae of drilling basically used to predict the thrust force and torque. The results were approximated due it not included all the acting parameters in drilling operation. After investigating of different empirical formula, the formulas taken into account are Lee Saffer assumption equation [12] for thrust force and torque equation from [13], are shown in below
D W D W
T hrustforce, FZ S 2sin 2
Torque, M FC * D
(1)
(2)
( f 2 ) * w * S * cos( )
(D 2)
1 (2r D) tan
where,
Cutting force ,
FC
sin * 0.707
w sin
tan
,
,
sin
,
,
S = shear strength, D = drill bit diameter, W = web thickness, = point angle, f = feed, w = width of cutting lip, = friction angle, = effective rake angle at the middle of each cutting lip angle and = helix angle
-
MULTI PERFORMANCE OPTIMIZATION TECHNIQUE
The responses more than one and to convert the multi-response into a single response Taguchi based grey is proposed. In grey relation analysis, the unknown value is represented by black and known value by white, the grey relation shows the relationship between the white and black information. The grey relation theory gives the effective management of the uncertainty, multi- input and discrete data. Following steps are performed for the optimization of process responses [14].
-
Normalize the response parameters in the domain of < 0, 1 > by using following formula of
Larger the better
Nij
(X ij) max (X ij) (X ij) max (X ij) min
(Xij )maxXij
(3)
Lower the best
N ij
(X
ij )max
(X
ij )min
(4)
-
Calculate the grey relation co- efficient by using following formula
(xoj , Xij ) min max
ij max
(5)
where
ij xoj X ij ,
max maxmax xoj X ij
min minmin xoj X ij
ji k ,
ji k
= Distinguishing coefficient varies from 0 to 1. Here, we are taking as 0.5.
-
After determining the grey relational coefficient, we have to take average value of grey coefficients and this average value is called Grey Relational Grade
1
n
1
k 1
(xi (k ), x
j (k ))
(6)
-
For determining S/N ratio for larger the better the best, the following formula is used
1 n 1
S / N ratio 10log
n k 1 y 2
(7)
After determining S/N ratio, plot graphs by using Minitab software of version 16 then we can find the optimal settings for drilling process parameters.
-
-
-
RESULTS AND DISCUSSIONS
In present study drilling of titanium alloy have been performed in DEFORM-3D for simulation. The responses such as circularity at entry and exit, thrust force and torque (fig. 1.) are tabulated in Table 3. The Circularity can be defined as the ratio of minimum to maximum of hole diameter.
Fig. 1. (a) Thrust and (b) Torque
Table 3. Experimental responses Table Table 4.Calculated Thrust force and Torque
Sl. No.
Circularity at entry
Circularity at exit
Thrust force N
Torque N-mm
1
0.863
0.841
2890
2500
2
0.941
0.911
2940
5200
3
0.970
0.915
5730
9870
4
0.921
0.874
3950
11700
5
0.928
0.864
5000
17600
6
0.871
0.839
5540
9870
7
0.956
0.936
3840
14100
8
0.913
0.835
7540
14780
9
0.938
0.925
5670
7870
Drill bit diameter mm
Theoretical Thrust force N
Simulated Thrust force N
Theoretical Torque N- mm
Simulated Torque N- mm
4
2896.88
2890
2318.8
2500
5
3842.42
2940
4710
5200
6
4837.5
5000
8347.6
9780
Mean average relative
error
11.39%
10.44%
Sl. No.
Circularity at entry
Circularity at exit
Thrust force N
Torque N-mm
1
0.863
0.841
2890
2500
2
0.941
0.911
2940
5200
3
0.970
0.915
5730
9870
4
0.921
0.874
3950
11700
5
0.928
0.864
5000
17600
6
0.871
0.839
5540
9870
7
0.956
0.936
3840
14100
8
0.913
0.835
7540
14780
9
0.938
0.925
5670
7870
Drill bit diameter mm
Theoretical Thrust force N
Simulated Thrust force N
Theoretical Torque N- mm
Simulated Torque N- mm
4
2896.88
2890
2318.8
2500
5
3842.42
2940
4710
5200
6
4837.5
5000
8347.6
9780
Mean average relative
error
11.39%
10.44%
The results suggest us that the simulation we performed by DEFORM-3D software best suited for numerical analysis of drilling process [15]. The mean percentage error of thrust force and torque (Table 4) are 11.39% and 10.44% respectively due to the mesh size particle ratio, more the meshing is finer the results will be closer to the accuracy. The results suggest that the model is validating to take into consideration. The responses of machining are optimized by grey relation analysis for the optimal parameter setup. The following steps are going to be performed. Circularity is taken as larger the better and thrust force and torque taken as smaller the better.
-
Normalization of experimental responses are substituted by equations 2 & 3 enlisted in Table 4
-
Calculate the correspoding grey relational coefficients are substituted in equation 4.
-
Calculate the grey relational grade (GRG) is done by equation 6.
-
Converting the GRG value into signal-to-noise ratio (equation 7) enlisted in Table 5.
T
able 5.Experime
ntal responses an
d normalization
table
Sl.
No.
Normalized circularity at entry
Normalized Circularity at exit
Normalized Thrust force
Normalized Torque
Grey relation grade
S/N ratio
1
0
0.058
1
1
2
0.732
0.758
0.989
0.821
0.670
-3.48
3
1
0.795
0.389
0.512
0.760
-2.38
4
0.546
0.388
0.772
0.391
0.666
-3.53
5
0.607
0.288
0.546
0
0.528
-5.55
6
0.708
0.038
0.430
0.518
0.457
-6.79
7
0.876
1
0.796
0.232
0.417
-7.59
8
0.466
0
0
0.187
0.727
-2.78
9
0.702
0.896
0.402
0.644
0.383
-8.34
Statistatical tool software Minitab 16 is used to determine which parameters have significantly affects the performance characteristics. The results of ANOVA for the grey relation grades are listed in Table 5. It also indicates that the speed and drill bit diameter have higher impact on drilling. The signal-to-noise ratio in figure 1, suggest us the optimal parameter settings for the drilling operation. The results shown figure 2 below indicate us that optimal setup for drilling is obtained at 1500rpm, 0.65mm/rev and 5mm diameter. As the setup is not available in the experimental setup so the conformation test is need to be performed
Table 6. Anova table of the responses
Source
DOF
Sequential SS
Adjacent MS
F
Percentage contribution
Speed rpm
2
18.593
9.296
4.96
48.37 %
Feed rate mm/rev
2
5.514
2.757
1.47
14.35%
Drill bit diameter
2
10.588
5.294
2.82
27.32%
Residual error
2
3.75
1.875
–
–
Total
8
38.444
–
–
–
Fig. 1. S/N ratio graph
The optimum drilling parameters were analyses from S/N ratios of GRG; parameters are A1, B1 and C2. The experimental setup is not present. So, there will be need of confirmation test. Therefore, the predicted mean of parameters has been calculated [16] by the equation (9)
SS / N Y (A1 Y ) (B1 Y ) (C2 Y )
(8)
Where is the total average of s/n ratios (of MPI from Table 5) A1 , B1 and C 2 are the S/N of the average drilling parameters
at the optimal levels SS / N
denotes the predicted signal to noise ratio. Therefore the calculated values of the responses are Y =
0.581,
A1 = 0.699,
B1 = 0.641 and C 2
= 0.637 (from Table 5). Substituting the values in equation (8), the predicted mean
parameter is:
SS / N
= -1.7768.
The confidence interval (CI) for the predicted [17] mean of S/N is given by the equations (8 and 9)
1 1
CI
Fa (1; fe ).Ve N
eff
R
(9)
Neff
N
1 TDOF
(10)
where,
F (1; f e ) is the F- ratio required for 100 (1 ) percent confidence interval,
f e is error degree of freedom,
Ve error
variance is 1.875 (Table 6), R is number of replication, N number of experiment and TDOF
total degree of freedom (Table 6).
Substituting the values in equation (9), the calculated confidence interval is: CI = ±7.767. The 95% confidence interval of the predicted optimal parameters is obtained 5.99< SS / N < -9.5443
The confirmation experiment was performed (Table 7) on the parameters of 1500 rpm spindle rate, 0.5 mm/rev feed rate and 6mm drill bit diameter, thus confirmation signal to ratio of -6.7757 which lies between 5.99 < SS / N < -9.5443. Following table indicates the results and Grey relation grade and S/N ratio of confirmation test.
Table 7. Confirmation results
Sl.
No.
Speed rpm
Feed rate mm/rev
Drill bit diameter mm
Circularity at entry
Circularity at exit
Thrust force N
Torque N-mm
Grey relation grade
S/N ratio
10
1500
0.5
6
0.844
0.825
3744
14600
0.458
– 6.775
-
-
CONCLUSIONS
A numerical approach of modeling and simulation has been presented in this work to understand the parametric effects of drilling process parameters on responses. The model has been validated by comparing the analytical results with mean average relative error of 11.39% and 10.44% for thrust force and torque respectively, which confirms that proposed model can be implemented in the mankind development. The optimum parametric setting is obtained at drilling speed of 1500rpm, 0.65 mm/rev of feed and drill bit diameter of 5mm.
-
REFERENCES
-
C. M. Botelho, Silicon-substituted hydroxyapatite for biomedical applications, Thesis, Universty of Porto, 2009.
-
L. T. Bang, Synthesis and characterization of hydroxyapatite (HA) And silicon substituted hydroxyapatite (Si-HA) Produced by a precipitation method, Thesis, University Sains Malaysia, 2009.
-
B. H. Robert, Materials Science of Crystalline Bioceramics: A Review of Basic Properties and Applications, Chiang Mai University Journal, 1 (2002) 23- 46.
-
A. Choragudi, M. A. Kuttolamado and J. J. Jones, Investigation of the machining of titanium components in light weight vehicles [C], Proceedings of SAE 2010 World Congress & Exhibition. Detroit: SAE, 2010: 1-14.
-
D. Ulutan and T. Ozel, Machining induced surface integrity in titanium and nickel alloys: A review [J], Int J Mach. Tools and Manuf, 51 (2011) 250-280.
-
S. Sharifa and E. A.Rahim, Performance of coated- and uncoated-carbide tools when drilling titanium alloy Ti6Al4V, J Material Process Tech, 185 (2007) 72-76.
-
K. Sakurai, K. Adachi, K. Ogawa, and R. Niba, Drilling of Ti-6Al-4V alloy .J. Jpn. Inst. Light Met., 42 (1992) 389394.
-
K. Sakurai, K. Adachi, and K. Ogawa, Low frequency vibratory drilling of Ti-6Al-4V alloy, J Jpn Inst Light Met., 42 (1992) 633637.
-
K. Sakurai, K. Adachi, K. Ogawa and S. Hanasaki, Intermittently decelerate feed drilling of Ti-6%Al-4%V alloy. J. Jpn. Inst. Light Met., 46 (1996) 138 143.
-
W. U. Hong-bing, X. U. Chengguang, J. Zhi-xin, L. Gang, and Z. Xue-chan, Establishment of constitutive model of titanium alloy Ti6Al4V and validation of finite element, in Int Conf on Measur Tech and Mechtrn Autom.
-
E. Kilickap, Optimization of cutting parameters on delamination based on taguchi method during drilling of GFRP composite, Expert Systems with Applications, 37 (2010) 6116-6122.
-
A. Bhattacharya, Principles of metal cutting, Ncba, 2009.
-
A.Ghosh and A. K. Mallik, Manufacturing science, second ed., East west press, 2010.
-
Chatterjee, S., Abhishek, K., Yadav, R.K. and Mahapatra, S.S., 2014, May. Optimization of drilling process parameters by harmony search algorithm. In International Conference on Recent Advances and Innovations in Engineering (ICRAIE-2014) (pp. 1-5). IEEE.
-
Chatterjee, S., Mahapatra, S.S. and Abhishek, K., 2016. Simulation and optimization of machining parameters in drilling of titanium alloys. Simulation Modelling Practice and Theory, 62, pp.31-48.
-
P. K. Chaulia and R. Das, Process parameter optimization for fly ash brick by taguchi method, Materials Research, 11(2008) 159-164.
-
H. Singh and P. Kumar, Tool wear optimization in turning operation by taguchi method, Ind J Engn and materl scinc, 11 (2004) 19-24.