
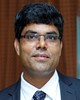
- Open Access
- Authors : Dattaji K. Shinde , Mudik Chandak , Pramod A. Naik , D N. Raut
- Paper ID : IJERTV9IS110122
- Volume & Issue : Volume 09, Issue 11 (November 2020)
- Published (First Online): 23-11-2020
- ISSN (Online) : 2278-0181
- Publisher Name : IJERT
- License:
This work is licensed under a Creative Commons Attribution 4.0 International License
Process Parameter Optimization for Laser 2D Barcode Engraving using Taguchi Design of Experiment Technique
Mudit Chandak1, Pramod A. Naik2 Dattaji K. Shinde 3 D N. Raut4
P.G. Student, Department of Production Engineering, Veermata Jijabai Technological Institute, Mumbai, India1 Research Scholar, Department of Production Engineering, Veermata Jijabai Technological Institute, Mumbai, India2 Associate Professor, Department of Production Engineering, Veermata Jijabai Technological Institute, Mumbai, India3
Professor, Department of Production Engineering, Veermata Jijabai Technological Institute, Mumbai, India4
AbstractThe focus area for this project is quality improvement by reducing defects, identifying the root cause by using advanced statistical tools such as Taguchi Design of Experiment methods. The product under study is automobile component viz. body. The body component has a major role in working of I.C. engine. It has an acute quality issue like type mix-up, operations missing, piled up work in process, increased throughput time, etc. due to product design and customer requirements. To solve these issues individual component level traceability needs to be implemented. 2-Dimensional barcode such as Data matrix code (DMC) is used to engrave on body component by using Laser engraving operations. To obtain optimum size and reliable scan-ability in various manufacturing environments, Taguchi Design of experiment methods is used. The body component traceability throughout the manufacturing process has the potential to change the way we approach the quality assurance and control issue. Thus, there is huge scope for data collection and analysis. This will assist to achieve the extremely ambitious goal of Zero Defect i.e. the title of World Class Manufacturer.
Keywords: Taguchi DoE, IC engine, Laser Engraving, Automotive component Traceability.
I. INTRODUCTION
The definition of traceability has been incorporated in 1987 into ISO 8402 and continues to feature in ISO 9001:2000 quality procedures. Traceability is then defined as the ability to trace the history, application or location of an entity by means of recorded identifications [9]. By introducing traceability in the production chain, the company should be able to verify the reliability of its products and respond to any complaints after the product is delivered for service.
Today we have technologies which enable the development of the Internet of Things (IoT); the realization of anti-counterfeiting traceability systems has become a reality. The purpose of this technique is to permit shoppers to reassure concerning the merchandise they purchase. The completed system will quickly and expeditiously investigate raw materials or process issues once their area unit product quality issues. It can contribute to quality control and recalls products when necessary, to improve the competitiveness of the company. [7]
Recalls and defective parts can be significantly identified towards the raw material, the process plan, the cutting tools used, operators, etc. The 5Ms Machine, Material, Method, Medium and Man are involved for the process is initially set
properly; it still defines itself, depending on the variation of the 5M and their interactions. So, in apply, traceability of producing processes suggests that recording product manufacturing info relating to raw materials, employees, machines, tools, storage, conditions then on, which may damage the corporate. [9]
The traceability project is conducted at XYZ Limited, India at ABC plant, for the automotive component. The ABC plant is manufacturing body for various automobile manufactures domestically as well as overseas. The management has the ambition to be a zero-defect company by the year 2021 i.e. to be a World Class Manufacturing Company (producing only 3.4 defective parts for every million opportunities).
As per the study conducted major defects reported and observed can be reduced by introducing traceability to individual body manufactured like operation missing, type mix-up, rework and scrap slippages. Traceability is also a key driver for Industry 4.0.
II. EXPERIMENTAL DETAILS
A. Product Details
The body is a child component of the internal combustion (I.C.) engine. The body can be visualized as a rod of diameter 30mm and 150 mm in length. The input material is a forging received from the vendor. Then successive turning, milling and gun drilling operations are carried. A phosphate surface coating process is performed to protect body from rust and extreme working conditions. The body is then thoroughly cleaned in high temperature and pressure condition for removing cutting oil, grease, metal burr, etc. Then it is subjected to visual inspection and ready for dispatch to customers.
B. Pilot Experiments
Various Traceability technologies are available like Data matrix code (DMC), Quick Response code (QR) and Radio frequency identification (RFID). [8] The Data matrix code has the highest level of data security and error correction code level among all available two-dimensional barcode algorithms. The RFID is the most promising technology for component level traceability due to its features like anti- counterfeiting, environment resistant, data carrying capacity and data editing. [9] But the cost to implement RFID is not feasible in the initial phase of component traceability project
at ABC plant. Thus, Laser DMC engraving technology is shortlisted for pilot trial experiment. The key challenge with laser DMC is that we need to ensure that code would be readable after phosphate coating process, as the impression will be filled. Most possible way is to increase laser penetration depth. This can be done by increasing the Laser power or multiple passes of Laser beam. Also, the DMC size influences the scanner readability and data carrying capacity.
C. Experimental Design
From the brainstorming session with the experienced professionals from concern domain, pilot experimentation and technology available resulted in two-factor details in the following. Suitable levels were decided based on proper literature survey and expert opinion.
Table 1: Factor-Level setting for an experiment
Factor |
UOM |
Level 1 |
Level 2 |
DMC Size |
mm2 |
8 x 8 |
10 x 10 |
Laser Passes |
number |
3p |
4p |
III. METHODOLOGY
A. Orthogonal Array
Taguchi Orthogonal array is selected after selecting factors and their levels. To select an appropriate orthogonal array, the total degrees of freedom need to be computed. The degrees of freedom are defined as the number of comparisons between process parameters that need to be made to determine which level is better and specifically how much better it is [4]. An orthogonal array can be selected from Minitab software as well as manually. So, if values of parameters and levels are entered in the software, orthogonal arrays i.e. L4 (2^3) is shown. I have defined factor-levels in
L4 (2^3) orthogonal array for the minimum number of experimental runs. Orthogonal array generated is as below.
Table 3: L4 (2^3) Orthogonal Array
Experiment No. |
Control factors |
|
DMC SIZE |
LASER PASSES |
|
1 |
1 |
1 |
2 |
1 |
2 |
3 |
2 |
1 |
4 |
2 |
2 |
B. Conduction of experiment
A loss function is defined to calculate the deviation between the experimental value and the desired value. Taguchi recommends the use of the loss function to measure the performance characteristic First of all deviating from the desired value. The value of the loss function is further transformed into a signal-to-noise ratio (S/N) [2][5]. There are 3 Signal-to-Noise ratios of common interest which are called as the objective function for optimization of Static problems.
Nominal the best, S/NT = -10 Log10 [ mean of sum of squares of measured data ]
Larger the better, S/NL = -10 Log10 [ mean of
sum of squares of {measured – ideal}]
Smaller the better, S/NS = 10 Log10 (square of mean/variance) [3]
Notice that, nominal the best objective function is used when response value is a specified target, below or beyond which will not get optimized value. For example, Aqua regia solution needs 1:3 of HNO3: HCL which is nominal value. Larger the better objective function is used when optimized response value is to maximize for the system. Smaller the better objective function is used when optimized response value is to minimize i.e. zero for the system. Here smaller the better objective function for Laser Engraving cycle time should be taken to find out optimal factor level setting. Then S/N ratios were calculated using smaller the better performance characteristics. The parts for the experiment are produced as per the dimension factor-level setting discussed above.
Table 4: Experimental results for FLOW RATE Variation and
S/Nratios
Expt. No. |
Control factors |
Engraving Cycle time |
Calculated S/N Ratios |
|
DMC SIZE |
LASER PASSES |
|||
1 |
8 x 8 |
3p |
17 |
-24.61 |
2 |
8 x 8 |
4p |
21 |
-26.45 |
3 |
10 x 10 |
3p |
24 |
-27.61 |
4 |
10 x 10 |
4p |
30 |
-29.55 |
C. Analysis
Main effect plots were generated from Minitab software to find out optimum combinations to reduce FLOW RATE variation. The effect of a factor level is defined as the deviation it causes from the overall mean. For generating main effect plots, response table values should be calculated by taking the average S/N ratio for same level experiments. Below is the response table for S/N ratios.
Table 5: Response Table of S/N ratios
Level |
DMC SIZE |
LASER PASSES |
1 |
-25.53 |
-26.11 |
2 |
-28.57 |
-27.99 |
Delta |
3.05 |
1.89 |
Rank |
1 |
2 |
These values show individual effects of factors and are commonly called as main effects. Rank in response table shows the amount of influence the factor have on the response variable. In the above response table, rank 1is for DMC SIZE; it shows that DMC SIZE has more influence on Laser DMC engraving cycle time followed by Laser Passes.
The analysis of variance is done to investigate which of the following process parameters has more influence on response value. ANOVA table can be generated from Minitab software or manual calculations. This is accomplished by separating the total variability of the S/N ratios, which is measured by the sum of squared deviations from the total mean of the S/N ratio, into contributions by each of the process parameters and the error [6]. First of all, the overall mean of S/N ratios can be calculated as.
.. (1)
Where, m= overall mean of all S/N ratios, i = S/N ratio for the ith experiment.
The total sum of squared deviation is distributed in two sources i.e. Sum of squared deviation for each process parameters SSP and sum of squared error SSe. Total sum of squared deviation & Sum of squares for each factor can be calculated by using effect of factors calculated in response table as:
. (2)
S.S. due to DMC SIZE (D) = [no. of expt. at level D1 * (mD1 – m) 2] + [no. of expt. at level D2 * (mD2 – m)
2](3)
S.S. due to Laser Passes (L) = [no. of expt. at level L1 * (mL1 – m) 2] + [no. of expt. at level L2 * (mL2 – m) 2] . (4)
Where,
MD1, mD2; mL1 & mL2 are the effect of factors DMC SIZE & Laser Passes for level 1 & 2 respectively.
The sum of squares for error is,
SSe = SST (SSD + SSL).. (5)
If t= no. of levels, n= no. of experiments, then the total degree of freedom is Dt = n-1 and degree of freedom for each testing parameter is Dt = t-1. Mean squares are calculated as MSP = SSP /Dt Then, the F-value for each design parameter is simply the ratio of the mean of squared deviations to the mean of the squared error (MSP /MSe). Percentage contribution of factors can be calculated by taking the percentage of the sum of squared deviation for each factor with the total sum of squares. F-test is performed to see which parameter has more influence on the response variable. After calculating F-value, it is checked for larger and smaller for each factor because usually factor having larger F-value has more influence on performance characteristics.
IV. EXPERIMENTAL RESULTS
Effects of factors were calculated by taking average S/N ratios for same level experiments which are shown in table 5. Effects of factors were calculated by taking average S/N ratios for same level experiments which are shown in table 5. Values in the response table show individual effects of factors and are commonly called as main effects.
A. Main effect plot
From the response table values, main effect plots are plotted by taking all factors on X-axis and response table values on Y-axis. By taking values from response tables, main effects are plotted on a single graph for S/N ratios. The goal in this experiment was to minimize the DMC engraving cycle time. Since negative (-ve) Log depicts a monotonic decreasing function; we should
maximize or minimize DMC engraving cycle time. Hence the optimum level for a factor is the level that gives the highest value of the mean of or lowest value of the mean of DMC engraving cycle time in the experimental region. Also, after taking data means into considerations, the optimum level is the level that gives the lowest value of DMC engraving cycle time in the experimental region. From figure 1 it is observed that the optimum settings of DMC SIZE & Laser Passes are 8×8 mm2 and 3 Laser passes if S/N ratios are taken into considerations. Hence results from main effect plot determines that the optimum DMC Laser engraving process parameters setting for reducing DMC engraving cycle time are DMC SIZE=8 x 8 mm2 and Laser Passes=3.
Main Effects Plot for SN ratios
Data Means
DMC SIZE PASSES
Main Effects Plot for SN ratios
Data Means
DMC SIZE PASSES
-25.5
-26.0
-26.5
-27.0
-27.5
-28.0
-28.5
-25.5
-26.0
-26.5
-27.0
-27.5
-28.0
-28.5
8×8
Signal-to-noise: Smaller is better
10×10
3p
4p
8×8
Signal-to-noise: Smaller is better
10×10
3p
4p
Mean of Means
Mean of Means
Mean of SN ratios
Mean of SN ratios
Figure 1: Main effect plot for S/N ratios
Main Effects Plot for Means
Data Means
DMC SIZE PASSES
Main Effects Plot for Means
Data Means
DMC SIZE PASSES
27
26
25
24
23
22
21
20
19
18
27
26
25
24
23
22
21
20
19
18
8×8
10×10
3p
4p
8×8
10×10
3p
4p
Figure 2: Main effect plot for response means
B. Anova Table
Table 6: ANOVA Table for S/N ratio
Source |
DO F |
Adj. SS |
Adj. MS |
F- valu e |
P- value |
% contributi on |
DMC SIZE |
1 |
9.282 |
9.282 |
3513 .81 |
0.011 |
72.26% |
LASER PASSES |
1 |
3.560 |
3.560 |
1347 .68 |
0.017 |
27.72% |
Error |
1 |
0.0026 |
0.0026 |
0.02% |
||
Total |
3 |
12.8447 |
Above ANOVA table is generated from Minitab software for S/N ratios and also checked for DMC engraving cycle time mean values, but it can be calculated manually also. Data analysis for the Taguchi method is done by ANOVA technique. Analysis indicates that percent of contribution by DMC SIZE is 72.26% and LASER PASSES is 27.72% in both the conditions. This shows that DMC SIZE makes more influence on DMC
engraving cycle time and Laser Passes has low influence. Also, more the F-value greater will be the influence on DMC engraving cycle time. So here DMC size has more F-value in both conditions. Lesser the P-value more will be the influence on DMC engraving cycle time. Here P- value is less for DMC SIZE in both conditions. Therefore, we can conclude that DMC SIZE is the most dominating factor & has more influence on DMC engraving cycle time.
C. Confirmation test
As we have optimum parameters setting to reduce DMC engraving cycle time, now compare the theoretical and practical value of optimum DMC engraving cycle time by conducting a confirmation experiment. The theoretical value of DMC engraving cycle time is calculated from the regression equation formulated from Minitab software and practical value is measured by conducting a confirmation experiment while considering optimum Laser DMC engraving process parameters. After getting optimum values of parameters, conducting the confirmation experiment in the same manner as conducted in above 4 experimental runs. Setting the process parameter values for DMC SIZE as 8×8 mm2 and Laser Passes at 3 and conducted the confirmation experiment. The practical value of DMC engraving cycle time after conducting an experiment is 17 seconds.
Regression equation formulated from Minitab software is: –
..(6)
For calculating theoretical value consider those values from the above equation which are variables of optimum parameters.
Therefore,
DMC engraving C.T. = 23-(4*1) – (2.5*1) (7) DMC engraving C.T. = 16.50 seconds
Deviation = Practical value theoretical value Deviation = 17-16.50 = 0.50 seconds.
Deviation between theoretical and practical value is the error caused due to human, process, machine, etc. So, the DMC engraving cycle time is optimized up to 17 seconds.
V. CONCLUSION
The body component has variety of product design and features available to suite the customer requirement. Due to this mass customization production planning on the shop floor becomes a challenge. As there is a chance of product mix-up of similar geometry and appearance, operations can go missing and gets detected at the visual inspection station at the process end. The quality complain resolution takes long time as data for the source of the defect is difficult in the absence of the updated log entries into the system. All this accounts for increased defect cost, which affects the bottom- line of the enterprises. The solution to this issue discussed here is component level traceability. This will help to store real time data of the body component like process flow sequence, production shift identification, Operator details
working on machine, Inspection reports and Throughput time of the body component and elimination of the operation missing incidents.
To introduce body component level traceability, we used laser engraving machine and Data matrix code (DMC) algorithm as 2-dimension barcode. Now to have complete traceability throughout the process the DMC code scan- ability should be ensured. But one of the Phosphates coating process is major concern area as the impression generated by laser gets filled by the coating. To increase the depth of penetration we need increase the number of laser passes, since laser power can be increased due to safety reasons. This served the Laser DMC scan purpose, but the laser engraving cycle time surged to alarming levels.
To find optimum Laser DMC size and Laser passes to ensure DMC scan-ability. We conducted pilot experiments to shortlist factor-level combination and conducted design of experiment using Taguchi orthogonal array L4(23). Which results are discussed as follows:
1. DMC size is the most dominant factor for Laser DMC engraving cycle time.
2. Optimum factor-level setting for engraving cycle time are DMC size is 8×8 mm2 and 3 Laser passes.
3. The optimum Laser engraving cycle time is 16.50 seconds was calculated and 17 seconds was observed.
The body component traceability throughout the manufacturing process has the potential to change the way we approach the quality assurance and control issue. Thus, there is huge scope for data collection and analysis. This will assist to achieve the extremely ambitious goal of Zero Defect i.e. the title of World Class Manufacturer (3.4 DPMO).
ACKNOWLEDTMENT
We thank to Bosch Ltd. Nasik for allowing the research activity for fuel pump nozzle assembly body component traceability throughout the manufacturing process using Laser DMC engraving technology was shortlisted for pilot trial experiment. Also, thanks to Production Engineering Department of VJTI Mumbai for financial support for this project work.
REFERENCES
[1] Chen, K S, Hsu, C H and Wu, CC, (2006), Int J Adv Manuf Technol, Process capability analysis for a multi-process product, 27: 1235. https://doi.org/10.1007/s00170-004-2312-3 [2] Hsieh, K L and Tong, LI, (2006), Int J Adv Manuf Technol, Incorporating process capability index and quality loss function into analyzing the process capability for qualitative data, 27: 1217. https://doi.org/10.1007/s00170-004-2314-1 [3] Yu, K T, Sheu, S H and Chen, K S, (2007), Int J Adv Manuf Technol, The evaluation of process capability for a machining center, 33: 505. https://doi.org/10.1007/s00170-006-0481-y [4] Mouralova, K, Benes, L, Bednar, (2019), J. et al. J Mech Sci Technol, Using a DOE for a comprehensive analysis of the surface quality and cutting speed in WED-machined hadfield steel, 33: 2371. https://doi.org/10.1007/s12206-019-0437-4 [5] Sagheer-Abbasi, Y, Ikramullah-Butt, S, Hussain, (2019), G. et al. Int J Adv Manuf Technol, Optimization of parameters for micro friction stir welding of aluminium 5052 using Taguchi technique, 102: 369. https://doi.org/10.1007/s00170-018-3138-8 [6] Dominik Jurkow, Johanna Stiernstedt, (2014), Ceramics International, Investigation of High Temperature Co-fired Ceramics sinteringconditions using Taguchi Design of the experiment, 40 10447-10455, https://doi.org/10.1016/j.ceramint.2014.03.015
[7] Ding J, Xu H, Li P, Zhu F ,(2019), Advances in Intelligent Systems and Computing, Research on Food Safety Traceability Technology Based on RFID Security Authentication and 2-Dimensional Code. In: Barolli L., Xhafa F., Javaid N., Enokido T. (eds) Innovative Mobile and Internet Services in Ubiquitous Computing. IMIS 2018., vol 773. Springer, Cham, https://doi.org/101007/978-3-319-93554-6_49 [8] Budak A, Ustundag A, Kilinc M S, Cevikcan E, (2018), Springer Series in Advanced Manufacturing. Springer, Digital Traceability Through Production Value Chain. In: Industry 4.0: Managing The Digital Transformation., Cham, https://doi.org/10.1007/978-3-319-57870-5_15 [9] Rouabhia-Essalhi, R and Amirat, A, (2017), Int J Adv Manuf Technol, An approach to implement internal traceability in machining workshops, 88: 719. https://doi.org/10.1007/s00170-016-8814-y