
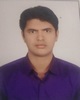
- Open Access
- Authors : Chandan Kumar , Prem Prateek , Sukriti Srivastava , Priti Kumari, Dr. Krishna Murari
- Paper ID : IJERTV9IS060638
- Volume & Issue : Volume 09, Issue 06 (June 2020)
- Published (First Online): 30-06-2020
- ISSN (Online) : 2278-0181
- Publisher Name : IJERT
- License:
This work is licensed under a Creative Commons Attribution 4.0 International License
Properties of Coconut Fiber Concrete at Elevated Temperature and Against Aggressive Environment
Prem Prateek1, Sukriti Srivastava1
1UG Student,
Dept of Civil Engineering, NSIT Bihta, Patna (India).
Priti Kumari2
2PG Scholar,
Dept of Nano Science & Nano Technology, AKU Patna (India).
Chandan Kumar*
*Assistant Professor,
Dept of Civil Engineering, NSIT Bihta, Patna(India).
Dr. Krishna Murari3
3Professor,
Dept of Civil Engineering, BIT Sindri, Dhanbad (India).
Abstract: -Concrete is a Composite material which is composed of Cement, fine and coarse aggregate with some admixture(if needed) binded together with a definite proportion of water. Wide scale use of concrete in construction have anadverse effect on the environment due to extreme reduction of natural resources ( stones, deposits, and aggregates) resulting in ecological imbalance. Another adverse effect of this is on the price of construction which is eventually going up.
Therefore,introduction of alternate waste material in place of natural aggregate in concrete production not only protects environment but also make concrete a suitable, economical and environment friendly.
In this paper, we are using coconut fiber as apotential replacement of fine aggregate by 2% of its weight in cement. As coconut fiber is vastly available near coastal areas, use of it in concrete should lead to increase in strength of concrete resulting increased sustainability from chemical effects in extremely hot weather condition and adverse chemical environment. The following study shows the effect of extremely hot exposure condition and adverse chemical environment such as acid attacks, sulphate attacks, and chloride attacks on the coconut fiber concrete of M30 grade by testing for 7 and 28 days to determine its compressive strength and loss of weight at raised temperature, and against adverse chemical environment respectively.
Keywords:- Coconut Fiber concrete, elevated temperature, aggressive environment, Compressive strength.
INTRODUCTION:-
According to the research, the high cost of conventional building materials plays a major role implanting housing delivery around the world. This leads a necessitated research to accommodate alternative material for future construction. Research for coconutfiber to use as aggregate material, leads to reduction of cost as well as weight of the concrete and enhancing its strength. As introducing coconutfiber as a suitable material, we are accounting for environmental impacts as well.It will be the first project to use coconut fiber in concrete to study its compressive strength and loss of weight: when exposed to an elevated temperature and adverse chemical environment
Coconutfiber are byproduct of agriculture which can be found in vast quantity near the coastal areas as they are traditional coconut cultivation areas.Sococonut fiber can be used near these areas,once they provide proper strength in compression when exposed to theirclimatic condition and resist the adverse effect of chemical such as sulphuric acid, sodium sulfate, sodium chloride.Coconut fiber haveTensile Strength of 21.5MPa which is the toughest among all natural fibers. They are capable of taking 4-6 times more strains than other fibers. Although it is a cheap and efficient, a major hindrance towards its wide scale use is high rate of water absorption, which can be reduced by providing oil coating. The advantages of Coconut fiber are : low cost, reasonable specific strength, low density, ease of availability, enhanced energy recovery, biodegradability, ability to be recycled in nature in a carbon neutral manner, resistance to fungi moth and rot, excellent insulation to sound , flame, moisture,dampness , toughness, durability and resilience.
Concrete is generally well resistant to chemical attack,provided anappropriate mix is used and concrete is properly compacted. There are some exceptions. Concrete containing Portland cement, being highly alkaline is not resistant to attack by strong acids or compounds which may convert to acids. Consequently, unless protected, concrete should not be used when this form of attack may occur[1].Chemical attack of concrete occur by way of decomposition of the products of hydration and formation of new compound which, if soluble may be leached out and if not soluble may be disruptive in situ. The attacking compounds must be in solution. The most vulnerable cement hydrate is Ca(OH)2, but C-S-H can also be attacked. Calcareous aggregates are also vulnerable[2]. Solid salt do not attack concrete but, when present in solution they can react with hydrated cement paste. Particularly common are sulfates of sodium, potassium, magnesium, and calcium which occur in soil or in groundwater. Because of solubility of calcium sulfate is low, groundwater with a high sulfate content contain the other sulfates as well as
calcium sulfate. The significance of this lies in the fact that those other sulfates as well as calcium sulfates react with the various products of hydration of cement and not only with Ca(OH)2[3].
-
MATERIALS AND METHODS:-
1).CEMENTCement is a binding material used in building construction and civil engineering construction.It is made by grinding calcined limestone and clay to a fine power, which can be mixed with water and poured to set as a solid mass and adheres to other materials to bind them together. In this project work we are going to use Pozzolana Portland Cement (PPC) of brandBirla Cement.
-
The physical properties of OPC as determined given in the table (1).
S.NO
Properties
Experimental Value
1.
Normal consistency % (IS:4031-Part-4-1988)
39%
2.
Initial setting time
41 min
3.
Final setting time
225 min
4.
Soundness of Cement (Le chatelier expansion)
2.75mm
5.
Fineness of Cement (IS:4031-Part-1-1996)
8.5
6.
Specific gravity
3.064
7.
Bulk Density
1450 kg/m3
8.
Compressive strength at 7 days
28 days
542.267KN
560.80KN
Fig1. Lab work of Consistency of cement
-
FINE AGGREGATE:-
-aggregates are inert materials mixed with binding material for construction purposes. It is the widely mined material in the world. For fine aggregate we will use locally available sand which pass through 4.75mm sieve. M sand available at NSIT,Bihta having the following characteristics has been used. Sand after Sieve analysis confirm to Zone-2 has been used as per specification IS:456-2000; IS:2386-Part-1-1963; IS:383-1970.
-
-
The physical properties of aggregate are given in table (2)
S.NO
Properties
Experimental Value
1.
Fineness Modulus
2.616
2.
Water absorption
0.80%
3.
Specific gravity
2.7
4.
Bulk Density
1695 kg/m3
Fig.2 Picture of coconut fiber.
Raw Fiber:-Procured from Coconut Mattress Manufacturing Unit.
Coconut iber:-Where the material is available as waste.
Processed Fiber:-Collected from Rope manufacturing unit.
Fig.3 Picture showing fine aggregate lab work.
-
COARSE AGGREGATE:-
Locally available black crushed stone in Bihta with nominal size passing through 20mm IS sieve have been used. The physical properties for coarse aggregate are found through laboratory test in accordance to IS:456-2000; IS:2386-Part-1-1963; IS:383- 1970.
-
-
The physical properties of aggregate are given in table (3)
S.NO
Properties
Experimental value
1.
Aggregate Crushing Value
10.45
2.
Aggregate Impact Value
7.92
3.
Specific Gravity
2.9
4.
Water Absorption
0.35%
5.
Bulk Density
1590 kg/m3
Fig.4 showing coarse aggregate lab work
-
WATER:- Water is used as a raw material during the manufacturing of various civil materials and in construction. It plays an important role in concrete preparation as binding the cement with other aggregate and play major role in the chemical process of releasing heat of hydration and hence imparting strength to it. The pH value of water used in concrete should always be greater than 6. In general, water fit for drinking is suitable for mixing concrete.
-
ADMIXTURE: -admixture are natural or manufactured chemicals which are used to give special properties to fresh and hardened concrete. It increases the workability without increasing water content or to decrease the water content at the same workability. In this project we have used CONMIX SP 1030 admixture from Radhekrishna Chemical Company.
Technical data of admixture is present in following table 4: –
S.NO
Properties
Data
1.
Appearance
Brown liquid
2.
Main Base
Sulphonated Naphthalene Formaldehyde
3.
Ph
7-8
4.
Chloride Content
Nil
5.
Specific gravity
1.2 at room temperature
6.
Shelf life
12 months in original packing
Fig.5 Picture of admixture used.
-
CONCRETE MIXES:-Mix design is defined as the process of selecting suitable ratio of ingredient to be mixed to form concrete of certain maximum strength and durability as economically as possible. The concrete mixes will be assigned with the use of type of fine aggregate and grade of the concrete. In this project we are usingconcrete of grade as M30. A mix design was conducted as per IS:10262-2009 to arrive at M30 mix concrete. The mix proportion of 1: 1.26 : 2.80 and water cement ratio of
0.442 is used. IS method of concrete mix was used to achieve a mix with strength of 30 MPa. Mix proportions were arrived and coconut fiber of 2% by weight of cement was added to the concrete mix.
-
MIXING, CASTING AND CURING OF COCONUT FIBER CONCRETE:- The coarse aggregate and fine aggregate were weighted,and the concrete mixture was prepared by hand mixing on a water tight platformand mixed thoroughly until a uniform color is obtained, later to it coconut fiber of 2% of weight of cement was added and mixed thoroughly. Then water is
added carefully, making sure no water is lost during mixing process. Water is added in stages for hydration of the cement which was carried out with preventive measure in place to avoid bleeding which may affect strength formation of concrete. Cleaned and oiled cube mould of dimension 150×150×150 mm was placed on a vibrating table, then concrete mix was placed in three layer, each layer first went through vibration to release air formed during mixing and vibration were stopped as soon as the cement slurry appeared on the top surface of the mould.
The specimen were allowed to remain in the steel mould for the first 24hrs at ambient condition of temperature 27± 2 C. After that specimen were demoulded with care to prevent edges from breaking apart and specimen were placed in the tank at the ambient temperature of 20C for 28 days for curing. The specimen shall not be allowed to become dry at any time until they have been tested. At the time before testing specimens are cured in air with a temperature of 20C and 50% relative humidity.
-
Table 5. Details of test specimens
-
Test Details
Shape and Dimension of Specimen
Compressive Strength
Cube: 150 × 150 × 150mm
Splitting Tensile Test
Cylinder: 150 × 300mm
Flexural Strength
Beam: 100 × 100 × 500mm
Durability Test
Cube: 150 × 150 × 150mm
Fig.7 Picture showing casting of concrete work.
-
-
TESTING METODOLOGY: –
Three cubes were tested for compressive strength each at 7 days and 28 days of curing using Universal Testing Machine.
-
Testing at Raised Temperature: –
Coconut fiber concrete was heated in an electric furnaceat a heating rate of 10c/min to target temperature of 200C, 400C,600C,800C,1000C respectively. At each target temperature, the specimen were maintained for 2hrs by Type K
thermocouple. After each exposure cycle, the specimens were allowed to cool at room temperature for 24hrs and then tested to assess the residual strength and weight loss.
-
Testing method for Adverse Chemical Environment: –
Six cubes of M30 coconut fiber concrete were immersed in 10% concentration of sulphuric acid, 10% sodium sulfate solution and 10% sodium chloride each for test period of 30 and 60 days. To avoid settling of solution, the solution was mixed every 7th day.
Once the test period is over, the specimens were taken out and left at room temperature for 3 days then kept in heat curing chamber for 2hrs to dry. Afterwards the specimens were tested for change in compressive strength and change in mass.
-
-
RESULTS: –
(1).COMPRESSIVE STRENGTH AT RAISED TEMPERATURE:-
Compressive strength of concrete is directly determined with the help of universal testing machine in concrete at NSIT, Bihta. As the temperature increases the compressive strength of the concrete decreases gradually upto temperature 400C, and the coconut fiber would have burnt at this point. After400C the rapid decrease in strengthwith increasing temperature is observed.
Table 3.1. showing results for compressive strength w.r.t raised temperature.
Raised Temperature (in degree centigrade)
Residual compressive strength (in MPa)
25
44.44
200
36.44
400
29.99
600
17.14
800
10.49
1000
5.15
50
compressive strength
compressive strength
40
30
20
10
0
25 200 400 600 800 1000
raised temperature
Graph 1. Change in compressive strength of specimen at raised temperature
-
COMPRESSIVE STRENGTH AGAINST ADVERSE CHEMICAL ENVIRONMENT: –
Three numbers of specimens in each acid, sulfate and chloride solution were tested for compressive strength after curing time and unit weight of specimens was noted before the test.
Table 3.2Compressive srength at adverse chemical environment.
Compressive strength no exposure (in MPa)
Compressive strength after 30 days exposure (in MPa)
Compressive strength after 60 days exposure (in MPa)
10% sulphuric acid
44.44
36.11
25.42
10% Sodium sulfate
44.44
39.99
37.29
10% Sodium chloride
44.44
40.41
38.46
50
40
30
20
10
0
10%
SULPHURIC ACID
10% sulphuric acid
50
40
30
20
10
0
10%
SULPHURIC ACID
10% sulphuric acid
No exposure
After 30 days exposure
No exposure
After 30 days exposure
After 60 days exposure
After 60 days exposure
compressive strength
compressive strength
Graph 2. Change in compressive strength of specimen against acid attack.
46
compressive strength
compressive strength
44
42
40
38
36
34
32
10% sodium sulfate
10% sodium sulfate
No exposure After 30 days exposure After 60 days exposure
Graph 3. Change in compressive strength of specimen against sulfate attack.
compressive strength
compressive strength
46
44
42
40
38
36
34
10% sodium chloride
10% sodium chloride
No exposure After 30 days exposure After 60 days exposure
Graph 4. Change in compressive strength of specimen against chloride attack.
-
LOSS OF WEIGHT DUE TO RAISED TEMPERATURE:-
As the temperature increases, there is an increase in the loss of weight probably due to the dehydration of the hydration products and the loss of water from the fine pores in the cement paste and aggregate particles.
% loss of weight of concrete
% loss of weight of concrete
Table 3.3Loss of weight at raised temperature
Raised Temperature (in degree centigrade)
% loss of weight of concrete.
Room temperature
0
200
5
400
8.6
600
9.33
800
10.75
1000
12.8
% loss of weight of concrete
% loss of weight of concrete
14
12
10
8
6
4
2
0
Room temp. 200
400
600
800
1000
14
12
10
8
6
4
2
0
Room temp. 200
400
600
800
1000
Raised temperature
Raised temperature
Graph 5.Percentage loss of weight due to raised temperature
-
LOSS OF WEIGHT DUE TO ADVERSE CHEMICAL ENVIRONMENT: –
OPC (M-30) cubes were immersed in 10% concentration of sulphuric acid, 10% sodium sulfate solution and 10% sodium chloride for test period of 30 days and 60 days. All the exposed specimen recorded weight loss and it was observed that the weight loss in case of acid attack was more as compared to sulfate and chloride attack.
Table 3.4Loss of weight due to aggressive environment.
Aggressive Environment
% loss of Weight (30 days exposure)
% loss of Weight (60 days exposure)
10% H2SO4
12.59
18.47
10% Na2SO4
8.15
14.29
10% NaCl
5.14
8.14
loss % in cocnrete due to aggressive environment
% loss of weight
% loss of weight
20
15
10
5
0
30 days exposure 60 days exposure
Aggressive environment
10% sulphuric acid 10% sodium sulfate 10% sodium chloride
Graph 6. Percentage loss of weight due to aggressive chemical environment.
-
-
CONCLUSION: –
The following experiment confirms that:
-
Loss of weight increased with increase in elevated temperature, weight loss was about 15% at 10000C.
-
M-30 coconut fiber concrete showed fall in its properties when exposed to temperatures above 200C.
-
It showed reduction in strengths in compression when exposed to high temperatures.
-
Loss of weight due to acid, sulfate and chloride attackis 11 %, 8.15 % and 5.14 % respectively after exposure of 30 days.
-
Loss of weight due to acid, sulfate and chloride attack is 17.47 %, 14.88 % and 8.99 % respectively after exposure of 60 days
-
Sulphuric acid attacks lead to more loss of weight and also deposition of a white layer of a gypsum crystal on the acid exposed surface of the specimen.
-
M-30 coconut fiber concrete showed reduction in strengths in compression when exposed to different aggressive chemical environment. This reduction was about 21.99%, 8.29% and 3.57% after 30 days exposure and 46.6%, 15.83 % and 13.20 % after 60 days exposure to acid, sulfate and chloride solution respectively.
REFERENCES BOOK: –
-
Neville A.M, Properties of concrete, 4th edition, Pearson Education, Inc. and Dorling Kindersley Publishing,Inc.1995. pp- 506- 517 & 563-569.
-
Shetty M.S. Concrete Technology, S.Chand& company Ltd; New Delhi, 2008 pp- 349- 419.
-
Gambhir M.L, Concrete Technology, 2nd edition, Tata Mc Graw-hill publishing company Ltd., New Delhi, pp- 100-103 & 333-339.
IS codes:
-
IS:456-2000; IS:2386-Part-1-1963; IS:383-1970.Specificationfine aggregates from natural sources for concrete.
-
IS:456-2000; IS:2386-Part-1-1963; IS:383-1970.— Specification coarse aggregates from natural sources for concrete.
-
IS: 10262-2009– Method of test for aggregate for concrete
-
IS:4031-Part-4-1988 ; IS:4031-Part-1-1996–Portland slag cementspecification.
-
IS 10262-2009 Concrete mix proportioning- Guidelines.
-
IS 516-1959 Method of tests for strength of concrete.
Journals:
-
Chandan Kumar et al Int. Journal of Engineering Research and Applications–ISSN : 2248-9622, Vol. 4, Issue 5( Version 2), May 2014, pp.151-157
-
Aly F.A., Connor D.O. and Abu-tair a., (2001) Explosive spalling of high strength concrete columns in fire Magazine of Concrete Research, Vol.- 53, No. 3, page. 197-204,
-
M. K. Abdelalim, G. E. Abdel-Aziz, M.A.K. El-Mohr and G.A. Salama (2009). Effect of aggregate type on the fire resistanc of normal and self- compacting concretes. Engineering Research Journal, page 47-62, London.
-
David N. Bilow and Mahmoud E. Kamara (2008) Fire and Concrete Structures. ASCE, USA
-
E. Annerel and L. Taerwe (2009) Approaches for the assessment of the residual strength of concrete exposed to fire. Concrete Repair, Rehabilitation and Retrofitting II Alexander et al (eds) Taylor & Francis Group, ISBN 978-0-415-46850-3, page 615-621, London.