
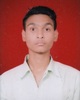
- Open Access
- Authors : Aniket Shobha Diliprao Hadole
- Paper ID : IJERTV10IS050188
- Volume & Issue : Volume 10, Issue 05 (May 2021)
- Published (First Online): 24-05-2021
- ISSN (Online) : 2278-0181
- Publisher Name : IJERT
- License:
This work is licensed under a Creative Commons Attribution 4.0 International License
Properties of Fly Ash based Geopolymer Concrete with GGBS & RHA
Aniket Shobha Diliprao Hadole
PG Student, Department of Civil engineering,
G.H.RAISONI University,Amravati, India Anjangaon Bari Road, Amravati – 444701
Abstract Now a days environmental pollution is the most important aspect on which we have to think about it. In the construction industries there is manufacture of materials like cement, bricks etc. these materials are widely used in each and every type of construction. From this source of materials some what by product are forms like fly ash generated from brick industries on other hand cement is consider as 1st binding material in our construction work and used of cement is more in construction that means cement production is done in huge amount in the industries.
This fly ash based geopolymer concrete replaced cement in our project. We improve the workability hardened property, compressive strength by adding some mineral & chemical solution. According to our project we adding GGBS act as a curing agent at ambient temperature in GPC, it makes concrete more workable and provide heat of concrete at ambient temperature on the other hand, RHA is adding with GPC. With some percentage variation like 5%, 10%, 15%, 20%. And studied the result of compressive strength and its workability. Result are describe in the result analysis and conclusion chapter in the project.
Keywords Geopolymer Concrete, Fly Ash, GGBS, Rice Husk Ash, Compressive Strength, etc.
INTRODUCTION
Small-scale usage of concrete has been documented to be thousands of years old. Concrete is a composite material composed of fine and coarse aggregate bonded together with a fluid cement (cement paste) that hardens over time. With infrastructure development growing and housing sector booming, demand for cement is also bound to increase. However, cement industry is extremely energy intensive. After thermal power plants and iron and steel sector, Indian cement industry is third largest coal user in country. Concrete made with Portland cement is the most widely used material on earth. The concrete industry is the largest user of natural resources in the world. Globally, over 14 billion tonneof concrete is placed per year and accounts for the annual 2.8 billion tonneof Portland cement produced. Significant increases in cement production have been observed and are anticipated to increase due to the massive increase in infrastructure and industrialization.
The global problems associated with us in todays world like environmental pollution, global warming (and hence climate change) are threats to sustainable future of this planet. Global warming is caused by emissions of greenhouse gases like methane, carbon-dioxide (CO2) to the atmosphere. Contribution of CO2 is appreciable accounting for about 65% of global warming. Concrete is most widely used
construction material after water, and conventionally it is produced using ordinary portland cement (OPC) as primary binder material. So with increasing demand and usage of concrete, production of OPC also demands an increase. Moreover in manufacturing of cement CO2 is released. It has been estimated that 1 ton of OPC production emits about 1 ton of CO2 and world cement production generates 2.8 billion ton man-made greenhouse gases annually. Efforts are being made to replace OPC partially or fully as binder material in concrete so as to reduce carbon emissions into atmosphere. An achievement in this regard is the development ofGeopolymer technology which utilizes wastes from various industries like fly ash, blast furnace slag, rice husk ash, silica fume etc. with alkaline medium to replace cement in concrete. This novel eco-friendly technology using geopolymer as eco-binder is considered to be promising in reducing CO2 emissions caused by cement industries.
Geopolymer is a new material in the world of concrete in which cement is totally replaced by pozzolanic material (Fly ash) that is rich in silica and alumina and activated by alkaline liquids to act as a binder in the concrete. The demand of concrete is increasing day by day to complete the need of development of infrastructure facilities. It is well known fact that the production of OPC not only consumes significant amount of natural resources and energy but also releases huge quantity of carbon dioxide to the atmosphere. It is necessary to find alternatives to make the concrete environment friendly with consideration of natural resources and atmospheric pollution.
Ground-granulated blast-furnace slag (GGBS or GGBFS) is obtained by quenching molten iron slag (a by- product of iron and steel-making) from a blast furnace in water or steam, to produce a glassy, granular product that is then dried and ground into a fine powder. As per report of working group on cement industries for the 12th plan around ten million tones blast furnace slag is currently generated in the country from iron and steel industries. GGBS is by product of iron industry. Ground Granulated Blast Furnace Slag is mineral admixture given in IS 456:2000, produce by grinding of blast furnace slag available in iron industries. GGBS is an amorphous powdery material having oxide composition (CaO,Fe2O3,Sio2,Al2O3 etc.) similar to portland cement but the actual content of these oxides would differ
.GGBS is widely accept for use in portland cement concrete to achieve improve workability, higher strength and
durability, superior resistances to chloride penetration, sulphate attack and alkali silica reaction.
EXPERIMENTAL INVESTIGATION
Materials and mix proportions: Fly Ash
Fly Ash also known as Pulverized Fuel Ash is one of the coal combustion products and is composed of the fine particles that are driven out of the boiler with the flue gases. Ash that falls in the bottom of the boiler is called bottom ash. Fly ash is generally captured by electrostatic precipitators or other particle filtration equipment before the flue gases reach the chimneys of coal fired power plants and together with the bottom ash removed from the bottom of boiler is known as coal ash. Fly ash contains substantial amount of silicon dioxide (SiO2), aluminum oxide (Al2O3), calcium oxide (CaO), Ferric Oxide (Fe2O3), Sodium Oxide (Na2O), Potassium Oxide (K2O), Titanium (TiO2), Magnesium Oxide (MgO), Sulphur Trioxide (SO3), Phosphorous Pentaoxide (P2O5). Fly Ash from India Bulls Pvt. Ltd. Amravati is used in concrete in dry powder form. The physical and chemical composition of fly ash is shown in table 1.
Table 1: Properties of Fly Ash
Sr.No. |
Parameters |
Results (%) |
1 |
Silica (SiO2) |
60.92 |
2 |
Alumina (Al2O3) |
27.95 |
3 |
Ferric Oxide (Fe2O3) |
4.60 |
4 |
Calcium Oxide (CaO) |
0.35 |
5 |
Sodium Oxide (Na2O) |
0.87 |
6 |
Potassium Oxide (K2O) |
0.27 |
7 |
Titanium (TiO2) |
1.53 |
8 |
Magnesium Oxide (MgO) |
37 |
9 |
Phosphorous Pentaoxide (P2O5) |
11 |
10 |
Sulphur Trioxide (SO3) |
0.31 |
Aggregates
The locally available natural river sand is used as fine aggregate. Various tests such as specific gravity, sieve analysis, water absorption, etc.have been performed. Crushed well graded aggregate black trap basalt of size 10 mm and 20 mm confirming the requirement of IS 383-1970 as coarse aggregate is used. The properties of aggregates is as shown in table.2
Table 2: Properties of Aggregates
Sr .No. |
Properties |
Result |
|
Fine Aggregates |
Course Aggregates |
||
1 |
Fineness Modulus |
3.03 |
2.70 |
2 |
Specific Gravity |
2.68 |
3.1 |
3 |
Silt/Dust Content |
3.1% |
Nil |
4 |
Water Absorption |
1% |
1% |
GGBS
Ground Granulated Blast furnace Slag is used as curing agent in geopolymer concrete. It is brougth from JSW cement limited, Raigad.
GGBS used in this project has physical and chemical composition has shown in this table 3
Table 3: Properties of GGBS
Sr.No |
Characteristics |
Test Result |
1 |
Fineness(%) |
3.83 |
2 |
Specific Gravity |
2.90 |
3 |
Residue left on 45µ(%) |
4.82 |
4 |
Initial Setting Time(Min) |
190 |
5 |
Insoluble Residue( %) |
0.3 |
6 |
Magnesia Content (%) |
7.79 |
7 |
Sulphide Sulphure (%) |
0.49 |
8 |
Sulphate Content (%) as SO3 |
0.45 |
9 |
Loss on ignition (%) |
0.42 |
10 |
Manganese Content (%) |
0.27 |
11 |
Chloride Content (%) |
0.001 |
12 |
Moisture Content (%) |
0.01 |
13 |
Glass Content (%) |
97.20 |
Rice Husk Ash (RHA)
The RHA is a very fine and porous material having a particle size in range of 5.75 micron. Physical properties of RHA as referred by some researchers are given below in Table 4
Table 4: Physical Properties RHA
Sr.No |
Properties |
Details |
1 |
Physical state |
Solid-non hazardous |
2 |
Appearance |
Very Fine Powder |
3 |
Particle Size |
25µ-mean |
4 |
Color |
Gray |
5 |
Odour |
Odourless |
6 |
Specific Gravity |
2.3 |
The mix proportions for alkali activated concrete were done as per Modified guidelines for geo polymer concrete mix design using Indian Standard[7]. GGBS content of 450kg/m3; alkaline solution to GGBS ratio of 0.4 and sodium hydroxide solution concentration of 14M was maintained for all mixtures based on various trial mixes. The mix proportions of geopolymer concrete are given in Table 4
Mixing
We started the mixing procedure by collecting all the materials at one place, initially we calculated all the required quantities for the mix. Then the calculated amount of aggregates were drawn in the mixing tray, after that the calculated amount of fine aggregates were also drawn in the tray. This mixture of aggregate and sand was mixed in the tray and mix it manualy to prepare the dry mix. After this calculated amount of fly ash was drawn in the mixing tray.
Then the calculated amount of alkaline activators those are Sodium Hydroxide and Sodium Silicate were mixed in the measuring cylinder so as to prepare an ideal solution of alkaline activators which was then poured in the tray. Then the required amount water, mixed with calculated amount of admixture was also poured in the tray. This whole assemblage was again mixed in the tray which gave us the Geopolymer concrete (that was used to prepare the specimens). As the no IS code is available for the mix design ofGeopolymer concrete, the mix design has been done by trial and error method on the basis of mix design of conventional concrete.
After making an GPC, on the basis ofof theme of our project, we compare GPC by adding different proportion of GGBS and RHA in the mix and cast a specimen, these cubes compare with 100% fly ash used in mix, along with that GPC
mixed we cast cubes compared it with GPC mixed with GGBS specimen and GPC mixed with RHA, cubes. The comparison only done for know the workability and compressive strength after 7 days and 28 days of casting.
Casting
When all the mixing process was complete the mould and slump cone test apparatus were oiled properly.so that the demoulding of cubes becomes easy and to get cubes in proper shape .the slump cone test was performed .the cube cast into moulds . The fresh concrete is casted into 100mm x100mm x100 mm cubes, to find the compressive strength. The specimens were prepared in accordance with IS 516-1953. The compaction is achieved by giving 25 manual stocks for each layer by using tamping rod. No other effort are taken to make the surface smooth
Curing
In this project the curing of GPC was done in two types i.e. at Ambient curing and Temperature curing.
Ambient curing: – After the 24 hours of casting of cube, the cubes were demoulded and placed at room temperature till the date of testing.
Temperature curing :- After the 24 hours of casting of cube, the cube were placed at oven temperature (80oc) for 24 hours and cubes were demoulded.
Quantities for 1 cu.m.(kg) with different % of GGBS & RHA
INGREDIENTS |
MIX (KG) |
||||
MIX |
M1 |
M2 |
M3 |
M4 |
M5 |
Fly ash |
394 |
374 |
355 |
335 |
315 |
GGBS /RHA |
0 |
20 |
39 |
59 |
79 |
Sodium silicate |
113 |
113 |
113 |
113 |
113 |
Sodium hydroxide |
45 |
45 |
45 |
45 |
45 |
Fine aggregate |
1201 |
1201 |
1201 |
1201 |
1201 |
coarse aggregate |
647 |
647 |
647 |
647 |
647 |
Water |
59 |
59 |
59 |
59 |
59 |
Admixture |
8 |
8 |
8 |
8 |
8 |
RESULTS AND DISCUSSIONS
A.WORKABILITY TEST
The slump test is the most well-known and widely used test method to characterize the workability of fresh concrete. This test is inexpensive test which measures consistency and is used on job sites to determine rapidly whether a concrete batch should be accepted or rejected. The test method is widely standardized throughout the world.
The slump cone test were carried out in laboratory on gpc as per IS 456-2000 the result of slump cone test are table no.1 slump after 25sec were measured. In the table no.1 the
terms used represents following meanings.
GPCT GPC for temperature curing GPCA GPC for ambient curingGPCG GPC with GGBS
GPCR GPC with RHA
Slump test of various mix proportions of RHA and GGBS in concrete are shown below
Table 1: Workability by Slump Cone Test of GPC
Sr.No |
Mixes |
Percentage (%) |
Slump (mm) |
1 |
GPCT |
0 |
32 |
2 |
GPCA |
0 |
32 |
3 |
GPCG |
5 |
28 |
4 |
GPCG |
10 |
25 |
5 |
GPCG |
15 |
22 |
6 |
GPCG |
20 |
19 |
7 |
GPCR |
5 |
22 |
8 |
GPCR |
10 |
19 |
9 |
GPCR |
15 |
16 |
10 |
GPCR |
20 |
12 |
-
Compressive Strength Test
The cubes are tested for their compressive strength on compression testing machine having capacity 3000KN. The load was applied uniformly until the failure of the specimen occurs. The specimen was placed horizontally between the loading surfaces of the compression testing machine and the load was applied without shock until the failure of the specimen occurred.
After the completion of curing period the cubes are broken to know the strength. The result of compressive test on GPC after 7days and 28 days and for different % of GGBS and RHA Ambient curing and oven curing are tabulated in table.
Table 2: Result of compressive strength test for variation in percent of GGBS at 7 Days & 28 Days
MIX
GGBS (%)
Type of curing
Compressive strength at 7 days
Compressive strength at 28 days
GPCA
0
Ambient
10.53
23.13
GPCT
0
Temperature
17.46
26.70
GPCG
5
Ambient
20.63
27.6
GPCG
10
Ambient
22
27.97
GPCG
15
Ambient
24.33
30.3
GPCG
20
Ambient
24.36
33.5
MIX
GGBS (%)
Type of curing
Compressive strength at 7 days
Compressive strength at 28 days
GPCA
0
Ambient
10.53
23.13
GPCT
0
Temperature
17.46
26.70
GPCR
5
Ambient
6.9
16.93
GPCR
10
Ambient
3.67
14.76
GPCR
15
Ambient
1.60
8.033
GPCR
20
Ambient
0.867
5.33
MIX
GGBS (%)
Type of curing
Compressive strength at 7 days
Compressive strength at 28 days
GPCA
0
Ambient
10.53
23.13
GPCT
0
Temperature
17.46
26.70
GPCR
5
Ambient
6.9
16.93
GPCR
10
Ambient
3.67
14.76
GPCR
15
Ambient
1.60
8.033
GPCR
20
Ambient
0.867
5.33
Result of compressive strength test for variation in percent of RHA at 7 Days & 28 Days
CONCLUSION
Based on the experimental investigations the following conclusions are drawn :-
-
Workability test result shows that workability of geopolymer concrete was good as compare to conventional concrete.
-
The workability of geopolymer concrete with GGBS get decreased with increased in percentage of GGBS in fly ash basedgeopolymer concrete.
-
Maximum strength of fly ash based geopolymer concrete with GGBS for ambient curing at 20% of replacement with GGBS is found 33.5Mpa.
-
GGBS is act as curing agent for GPC.
-
Maximum strength of fly ash based geopolymer concrete with RHA for ambient curing at 5% of replacement with RHA is found 16.93Mpa.
-
Above results show that increase in percentage of GGBS in geopolymer concrete increases its compressive strength upto 20% of GGBS but beyond 15% strength goes decreasing.
-
Now we also studied that there is increase in the percentage of RHA it decreases compressive strength.
-
Geopolymer concrete with 15% GGBS can be alternative material to cement concrete for cast-in- situ condition.
-
REFERENCES
-
Mayank Kumar, "Geopolymer Concrete: Leading the World Towards a Sustainable Future International Journal of Engineering Research& Technology (IJERT) ISSN: 2278-0181 Vol. 4 Issue 09, September- 2015
-
Ganpatinaidu (2012) Study on strength properties of GPC with addition of GGBS international research journal engineering and technology (IRJET) e-ISSN:2395-0056 volume:02 issue: 09,December 2012 www.IRJET.NET P-ISSN:2395-0072
-
Dr.BhushanShinde, KshitijaKadam,Effect of Alkaline Activator on Compressive Strength ofGeopolymer Concrete with Ambient Curing,
ICRTES: Volume 6, Special Issue 1, January 2017
-
Supraja et al. (2012) Geopolymer Concrete-A Review" International Journal of Engineering Sciences & Emerging Technologies, Feb 2012. ISSN: 2231 6604 Volume I, Issue 2.
-
D.B.Rajiwala,H.S.Patil(2011)"Geopolymer Concrete : A Concrete of Next Decade" Journal of Engineering Studies and Research (JERS)
Vol. II Issue 1
-
Nguyen Van Chanh, Bui Dang Trung. Dang Van Tuan, "Recent Research Geopolymer Concrete." The 3rd ACF International Conference-ACFNCA 2005
-
L.Krishnan, S.Karthikeyan, S.Nathiya, K. Suganya, "Geopolymer Concrete An Eco-Friendly Construction Material" International Journal of Research in Engineering and Technology
-
P. Chaiyapoom, S. Jiemsirilers, S. Wada, K. Hemra, P. Thavorniti "Preparation ofGeopolymer Using Fly Ash And Rice Husk Silica As Raw Materials", 18th international conference on composite materials, vol. 22, pp 1073-1078, 2009.
-
A IftiqarAhemad,S. Siddiraju, "Strength Properties On Fly Ash Eased Geo Polymer Concrete With Admixtures", International Journal of Civil Engineering and Technology (UCIET), Volume 7,lssue 3, May-
June 2016:3pp. 347-353
-
Ashish Kumar Singh, Mohd. Afaque Khan, Neeti Mishra,International Research Journal of Engineering and Technology (IRJET) e-ISSN: 2395-0056 Volume: 05 Issue: 04 | Apr-2018 www.irjet.net p-ISSN: 2395-0072