
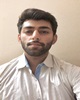
- Open Access
- Authors : Nakshtra Popli
- Paper ID : IJERTV10IS100066
- Volume & Issue : Volume 10, Issue 10 (October 2021)
- Published (First Online): 20-10-2021
- ISSN (Online) : 2278-0181
- Publisher Name : IJERT
- License:
This work is licensed under a Creative Commons Attribution 4.0 International License
Prosthetic ARM Controlling and Battery Improvement Techniques of A Prosthetic ARM
Nakshtra Popli
Electrical and Electronic Engineering Department
Gupta Institute of Technology and Management New Delhi, India
Abstract According to the statistics of the national limb loss Centre there are approximately 7 billion people in the United States who have lost their limbs. One of the major challenges is the battery and charging of the prosthetic arm. This paper presents an introduction to the prosthetic arm followed by the methods used to control the prosthetic arm. It also explains the battery management system of the prosthetic arm along with a different way of charging the arm using piezoelectric crystals.
KeywordsComponent; prosthetic arm; piezoelectric; my- electric control; stump
- INTRODUCTION
The human hand is able to perform a complex repertoire of sophisticated movements that enables us to interact with our environment and communicate with one another. EMG: Electromyography: diagnostics the muscle and the nerve cell that controls them. These nerve cells are motor neurones, they transmit electrical signals for muscles to contract and relax
- CLASSIFICATION OF A PROSTHETIC ARM AS PER AMPUTATION :
- Transradial prosthesis :
A transradial prosthesis is an artificial arm that attaches below the elbow. A passive device of the sort serves strictly cosmetic purposes.
- Transhumeral prosthesis:
A transhumeral prosthesis is an artificial arm that connects to the body above the elbow but below the shoulder. A transhumeral limb is more complicated than a transradial prosthesis due to a missing elbow
- Transradial prosthesis :
- MOTOR CONTROL:
Methods of controlling the complex movements of the prosthetic limb:
- MYOELECTRIC CONTROL
It relies on a complex algorithm to sense the massive amount of electrical activity in the stump emitted during contraction. These emissions are measurable at skin level at a microvolt level.
It has frequencies ranging from few Hz to 300Hz and 10 microvolts to 1 millivolt.
Procedure:
These myoelectric signals are detected by keeping 3 electrodes on the skin.
Two electrodes develop the voltage difference and the third one is the neutral area and its output is used to cancel the sound produced by the other two.
The voltage is amplified which produces significant current to control the electromechanical and electronic devices.
- TARGETED MOTOR REINNERVATION Central , peripheral motor and sensory pathways retain
significant residual connectivity and function for many years after the limb is removed.
This technique is TARGETED MOTOR REINNERVATION. This technique is used to increase the accuracy of MYOELECTRICALLY CONTROLLED PROSTHESIS
- ALTERNATE SYSTEM:
It involves the implantation of bipolar differential electromyographic electrodes within the muscle to create a system capable of reading EMG signals
- SONOMYOGRAPHY:
It is an alternate method of limb control.
It uses ultrasound to measure the change in size of the contracting muscles in the stump
- MYOELECTRIC CONTROL
- SENSATION:
Whilst information provided by detection of sound from microphones embedded in hand ensures that objects will not slip out.
Approach of adding sensors:
First approach : MULTIMODAL PLASTICITY
Here the loss of one sensory modality can be replaced by another.
Hearing can partially compensate for loss of touch
Second approach : Replication scenario by transferring stimuli(that provokes action) from the electronic sensors in the bionic limb to natural sensors on the limb stump
Commercially available smart prosthesis:
-
- I Limb:
- In this type of prosthesis, there are 36 grip options and a control option such as a mobile app
- Be Bionic:
- Each finger has different motions in this prosthesis. It provides an auto grip function to avoid slipping.
- Dynamic arm, ottobock:
- In this type of prosthesis, the elbow automatically takes advantage of the energy that is stored when the arm is extended and reuses it for flexion.
- NOISE IN EMG SIGNAL
The peak Peak magnitude of typical EMG signal is 0 to 10 MV and usually lies in the range of 20 to 400 HZ.
The noise of the electronic equipment adds disturbance to the EMG signal.
EMG is non-linear and non-stationary due to the number of active motor neurons in the muscle fibre. Proper contact of the skin and electrode is necessary for EMG recording. Muscle concentration generates a current which can be recorded in the form of analog signals with the help of electrodes. Electrodes are Agcl electrodes, in order to reduce noise caused by them.
A. SENSOR DESIGNING/ SENSOR EXTRACTION:
Pre-amplification:
For EMG signal, 2 electrode technique is not suitable because of the limitation of noise removal while in 3 electrode technique then noise is removed by the help of a differential amplifier.
The EMG amplifier is designed with variable gain 60dB-80dB because of the potential obtained from the muscle. The inherent noise is removed by a low pass filter which results in the output signal of 0 to 400 Hz.
The power source is 50 Hz frequency so to remove 50 Hz from the EMG signal, a notch filter is designed. In order to remove motion and external noise, a high pass filter with cut off 20 Hz is designed.
- BATTERY CONSUMPTION:
- The lithium (Li) battery in the EEG headset allows up to 12 hours of continuous usage when completely charged.
If fully discharged (after 12 hours of usage), it can take up to 4 hours to be recharged. However, the charging process takes between 30 minutes to 2 hours when not fully discharged.As a result, it is advised to recharge it before 12 hours of use.
usage on an ongoing basis The headset does not function when it is charging, for safety purposes.
- Electro-mechanical system
The electro-mechanical system is made up of eight servo motors with rated powers of 0.5 and 3.5 Watts that are located on various areas of the prosthetic arm (wrist, elbow, shoulder, and fingers). To give three degrees of freedom, three servo motors with a rated power of 3.5 Watts are mounted on the wrist, elbow, and shoulder regions. In addition, the five fingers are controlled by five servo motors with a rated power of 0.5 Watts each. As a result, the total power consumed by the servomotors is 13 Watts. To power all of the servo motors incorporated in the arm, a 5V battery with an output current of
-
- Ampere is required.
The wireless communication device runs with a 50 mA supply at 3.3 V and a power consumption of 0.165 Watts to operate. A network of smart sensors, including temperature, skin pressure, and ultrasonic proximity sensors, as well as accelerometers, potentiometers, strain gauges, and gyroscopes, is also employed.
The total current consumed by these sensors is 100 mA. The low-power single-board computer’s (Computing and Processing Unit) power consumption is 0.1 Watts, which corresponds to a current of 30 mA. To power all of the above- mentioned units, the system requires a power source with an output current of at least 2.8 A and an output voltage of at least 5V.
Two 10,000 mAh lithium-ion batteries with output currents of 2A each are chosen. They contain a charging circuit (by USB cable) and a 5V DC boost converter. As these batteries have an 80 percen efficiency loss on both ends, it is not suggested to run the arm while the battery is charging. The arm will be operational for 7 continuous hours with these two batteries, understanding that the typical hand movement per person throughout a day is similar to 1 to 3 hours of continuous movement depending on the daily activities performed. Finally, the entire system may be active for two whole days.
- Ampere is required.
- The lithium (Li) battery in the EEG headset allows up to 12 hours of continuous usage when completely charged.
- CHARGING OF PROSTHETIC ARM :
For charging of prosthetic arm the piezoelectric generator can be used to produce energy by walking.
Piezoelectric generators are made from a group of ferroelectric materials. Piezoelectric generators are commonly made of crystals PbTiO3, PbZrO3, PZT.
These crystals have the ability to produce electric charge when exposed to mechanical stress which is also called as direct effect. (Produces charge when exposed to continuous wearing stress) PVDS sheet is connected to buck converter of 5 V, the output of the buck is connected to 3.7V battery with capacity of 2300mAH
The maximum pressure of the feet while walking is on the heels and the toe.
Therefore with one piezoelectric generator: 1650 STEPS = 0.15V
For 1V = 1650steps/0.15 = 11000 steps
With 4 piezo: 11000/4 = 2750 steps Therefore,
1V would be produced in just 2750 steps.
REFERENCES
-
-
- S. Alderson, P. E Klopsteg, P. D. Wilson and Hafner, “The electric arm” in Human Limbsand their Substitutes, New York:McGrawHill, 1954.
Google Scholar
- B. Bigland and O.C.J. Lippold, “The relation between force velocity and integrated electrical activity in human muscles”, J. Physiol., vol. 123, pp. 214-224, 1954.
CrossRef Google Scholar
- K. Fukunaga, Introduction to Statistical Pattern Recognition, New York:Academic, 1972.
Google Scholar
- D. Graupe and J. Salahi, Multifunctional artificial limb control via EMG temporal analysisBackground and amputee tests, Chicago:Dep. Elec. Eng., Illinois Inst. Technol.
Google Scholar
- D. Graupe, J. Magnussen and A. Beex, “Microprocessor system for multifunctional control of upper-limb prostheses”, IEEE Trans. Automat. Contr., vol. AC-23, pp. 538-544, Aug. 1978.View Article Full Text: PDF (720KB) Google Scholar
- J. Lyman, A. Freedy and H. Zadaca, Studies and development of heuristic end-point control for artificial upper limbs, Oct. 1974.
Google Scholar
- M. A. Newman and G. N. Saridis, Development of a prosthetic arm, IN, West Lafayette:Purdue Univ., May 1978.
Google Scholar
- L. R. Rabiner and R. N. Schafer, Digital Processing of Speech Signals, NJ, Englewood Cliffs:Prentice-Hall, 1978.
Google Scholar
- P. Rimroth, M. A. Newman and G. N. Saridis, A study of electromygraphy for above-the-elbow amputation, IN, West Lafayette:Purdue Univ., 1978.
Google Scholar
- R. W. Wirta, D. R. Taylor and F. R. Finley, “Engineering principles in the control of external power by myoelectric signals”, Arch. Phys. Med., vol. 49, pp. 294-296, 1968.
Google Scholar
- R. W. Wirta, D. R. Taylor and F. R. Finley, “Pattern recognition arm prosthesis” in Bull. Prosthesis Res. BPR 10-30, DC, Washington:Veterans Administration, 1978.
- S. Alderson, P. E Klopsteg, P. D. Wilson and Hafner, “The electric arm” in Human Limbsand their Substitutes, New York:McGrawHill, 1954.
-
Google Scholar