
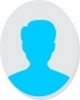
- Open Access
- Authors : Abhishek Kumar , Puneet Sharma , Amit Agarwal
- Paper ID : IJERTV10IS080073
- Volume & Issue : Volume 10, Issue 08 (August 2021)
- Published (First Online): 18-08-2021
- ISSN (Online) : 2278-0181
- Publisher Name : IJERT
- License:
This work is licensed under a Creative Commons Attribution 4.0 International License
RAMS of HVAC for Rolling Stock Application
Abhishek Kumar
RAMS & LCC Engineer
Sidwal Refrigeration Industries Pvt. Ltd.
Puneet Sharma
Manager Electrical Design, RAMS & LCC Sidwal Refrigeration Industries Pvt. Ltd.
Amit Agarwal
Vice President Servicing, RAMS & LCC Sidwal Refrigeration Industries Pvt. Ltd.
1 Abstract
Purpose -The purpose of this paper is to provide the detailed calculation of reliability, availability, maintainability, safety of HVAC for a desired mission time (time frame).
Methodology & approach – The complete calculation and detailed methodology is based on the systematic approach followed by the standards ROME LABORATORY RELIABILITY ENGINEERS TOOL KIT, EN-50126 & the practically used techniques in rolling stock industry.
Findings The paper provides information about the reliability critical items in a HVAC, how the series & parallel method of calculation is performed, how they are used in calculation of RAMS.
Research limitations This paper is there to provide the RAMS calculation at HVAC level only but this can also be performed at the train level. The author has taken only the methodology which was there in the standards & practically followed by him. There can be some other approach also for this calculation.
Practical Implications – This paper provide the overview of approach & methodology which can be used for the calculation of RAMS of HVAC (Heating Ventilation Air Conditioning) system and can directly use in the rolling stock application.
Key Words- Life Cycle cost, Reliability, Availability, Maintainability and Safety.
2 INTRODUCTION
-
RAMS (Reliability Availability Maintainability Safety)
-
Reliability
Reliability can be described as a discipline related to the design, development, test, and manufacture of an item, so that it successfully performs a certain task under specified conditions for a certain length of time or number of cycles with a specified probability.
-
Probability density function f (t) = e- *t
Where;
f (t)= probability density function = Failure rate
t = mission time MTBF = 1/
e.g. = 3.86 * 10 -6
MTBF = 1/ = 259067
Mission time (t) = Time for which the component has to perform its intended function. t = 69000 hours
The reliability at 69,000 hours is 0.77, as represented by the green shaded area to the right of the 69,000 hour point in the probability density function (pdf) plot shown above. The unreliability or probability of failure is 0.23, as represented by the pink shaded area to the left of the 69,000 hour point in the pdf plot.
-
Reliability Function R (t) = ()
= e- *t
Where;
R = Reliability = Failure rate t = mission time
e.g. = 3.86 * 10 -6
MTBF = 1/ = 259067
Mission time (t) = Time for which the component has to perform its intended function. For mission time t = 69000 hours
The reliability at 69,000 hours is 0.77. The unreliability or probability of failure is 0.23
-
Un-reliability F (t) = 1- R (t)
-
-
Availability
It is defined as the time for which of train is available for revenue service. Availability is defined as the percentage of time a system is considered ready to use when asked. It depends on the availability of all the subsystems of the train including HVAC.
A = MTBF MTBF+MTTR
A= /
/ +1/µ
A = µ
+µ
Where;
MTBF = Mean time between failure = 1/
MTTR = Mean time to repair
n ()
Where;
MTTR =
i=1
i=1
i=1
n ()
MTTRi is the repair time for each Line Replacement Unit (LRU) with a total quantity Qi and i is the failure rate for each LRU.
Where
i = the failure rate of the i th repairable unit MTTRi = the repair time of the i th repairable unit Q = the number of units in the system
-
Maintainability
The probability that a given maintenance action can be carried out within a stated time interval under stated conditions and using stated procedures and resources.
Repair rate = µ = 1
MTTR
Repair
Repair
t = allowable down time
Repair function =
µ * µ
Repair function =
µ * µ
t
t
Time
Time
µ µ = = MTTR
µ
Maintainability = M (t) = µ µ = 1 – µ
-
Safety
Safety is the state of being "safe", the state of being secure from harm or other non-desirable consequences. Safety can also refer to the control of documented hazards in order to attain a satisfactory level of risk. Capability not to harm persons, the environment, or any properties during a whole life cycle.
-
Deliverables of safety plan:-
Risk Analysis. Hazard log
Interface hazard analysis (IHA)
Operating & support hazard analysis (O&SHA) Preliminary Hazard Analysis (PHA)
FMECA Failure mode effect critical analysis FTA Fault tree analysis
-
Failures in HVAC that are considered in Safety Critical Failures
-
Fire start or smoke release from the HVAC.
-
HVAC explosion.
-
HVAC failures leading to electrocution.
-
Features leading to refrigerant leak outside the HVAC unit. Hazard Function h (t) = () =
()
Where;
R (t) = Reliability Function
f (t) = Probability density function = Failure rate
e.g. = 3.86 * 10 -6
MTBF = 1/ = 259067
Mission time (t) = Time for which the component has to perform its intended function. t = 69000 hours
The reliability at 69,000 hours is 0.77. The unreliability, or probability of failure, is 0.23.
-
-
-
Factors influencing RAMS in Rolling stock application:-
-
RAMS for lifecycle phases
Phase No.
Phase
General Task
RAM Task
Safety Task
1
Conceptual Design
Investigation done on the basis of scope of supply, application of the system & environment in which it has to perform its intended function.
Investigation on the following points to be done
System on which RAM is to be implemented.
Previous similar projects on which this RAM was applied also validating its performance by cross checking the failure rates & MTTR values.
Predict the failure rates as per respective standards or from the field data of similar projects undergoing in the similar environment & application.
Current targets of reliability & how these targets can be achieved i.e. series, parallel combination (redundancy) of the components that are having high failure rates.
Describe the possibility of the RAM controlling requirements for successive scheme life cycle RAM tasks.
Prepare Reliability Critical item list.
Investigation on the following points to be done
Over-all safety consequences of the system.
Previous similar projects on which this safety performance was applied also validating its performance by cross checking the hazard rate.
Current targets of safety & how these targets can be achieved i.e. by using EN45545 compliance used for non-metallic materials. Describe the possibility of the safety conrolling requirements for successive scheme life cycle safety tasks.
2
System explanation and operative context
Define the following System
Mission period & summary scope of operative requests
Inaugurate RAM policy RAM plan
Inaugurate Safety policy Safety plan
3
Risk investigation and calculation
Accomplish Risk Analysis Modernize RAM plan
Accomplish Risk Analysis. Hazard log
Interface hazard analysis (IHA) Operating & support hazard analysis (O&SHA)
Preliminary Hazard Analysis (PHA)
4
Description of system requests
Specify system necessities
Establish
RAM necessities description RAM plan
Validation plan for RAM necessities description
Establish
Safety necessities description Safety-related submission circumstances.
Update Hazard log
Update Interface hazard analysis (IHA)
Update Operating & support hazard analysis (O&SHA)
Update Preliminary Hazard Analysis
5
Design and allotment of system necessities
Define the system design. Identify the necessities for incorporation of pre-existing subsystems/mechanisms. Define acceptance standards and developments for subsystems/mechanisms.
Assign RAM necessities to subsystems/mechanisms.
Provide component level failure rates as per respective standard and calculate the system reliability by Reliability Block Diagram.
Modernize the RAM plan. Modernize validation plan for RAM requirements.
Accomplish hazard analysis. Assign safety requirements to subsystems/mechanisms. Update safety-related application situations. Update Hazard log
Update Interface hazard analysis (IHA)
Update Operating & support hazard analysis (O&SHA)
6
Design and execution
Design subsystems/mechanisms. Prepare O&M module. Define and create engineering process for manufacturing subsystems and mechanisms.
Define and create system amalgamation process. Prepare installation and contracting processes.
Strategy of RAM tasks of further phases.
Accomplish RAM investigation. Modernize the RAM plan. Modernize authentication plan for RAM necessities.
Update Reliability Block diagram. Update Fault tree analysis.
Predict the MTTR i.e. time to repair the particular component when the respective failure is arrived.
Check the accessibility of all the components to ensure the minimum MTTR so that maximum availability of the system can be ensured.
Strategy of Safety tasks of further phases.
Accomplish hazard analysis. Update safety-related submission circumstances.
Update safety-related application situations. Update Hazard log Update Interface hazard analysis (IHA)
Update Operating & support hazard analysis (O&SHA).
Prepare FMECA (Failure Mode Effect Critical Analysis).
7
Manufacturing
Implement and activate industrialized procedure
Inaugurate RAM declaration arrangements. Modernize the RAM plan. Modernize authentication plan for RAM requirements.
Check accessibility of all the components to ensure the minimum MTTR so that maximum availability of the system can be ensured.
If there is any change in component assembly as per manufacturing constraints update the MTTR and system availability report.
Strategy of Safety tasks of further phases.
Accomplish hazard analysis. Update safety-related submission circumstances.
Update safety-related application situations. Update Hazard log Update Interface hazard analysis (IHA)
Update Operating & support hazard analysis (O&SHA).
Update FMECA (Failure Mode Effect Critical Analysis).
8
Integration
Incorporate subsystems and mechanisms. Determine system functionality.
Test and examine scheme. Arrange system provision measures.
Inaugurate RAM declaration arrangements. Modernize the RAM plan. Modernize authentication plan for RAM requirements.
Check accessibility of all the components to ensure the minimum MTTR so that maximum availability of the system can be ensured.
If there is any change in component assembly as per manufacturing constraints update the MTTR and system availability report.
Strategy of Safety tasks of further phases.
Accomplish hazard analysis. Update safety-related submission circumstances.
Update safety-related application situations. Update Hazard log Update Interface hazard analysis (IHA)
Update Operating & support hazard analysis (O&SHA).
Update FMECA (Failure Mode Effect Critical Analysis).
9
System Authentication
Establish-
Authentication report. Procedure for the achievement and estimate of operational and maintenance data.
Inaugurate RAM declaration arrangements. Modernize the RAM plan.
Modernize authentication plan for RAM requirements.
Strategy of Safety tasks of further phases.
Accomplish hazard analysis. Update safety-related submission circumstances.
Update safety-related application situations. Update Hazard log Update Interface hazard analysis (IHA)
Update Operating & support hazard analysis (O&SHA).
Update FMECA (Failure Mode Effect Critical Analysis).
10
System approval
Record and recognition by signing off all the documents related to RAMS for Safety.
Verify the approval record.
Evaluate RAM authentication. Signoff all targets related to failure rates & reliability.
Inaugurate Self-regulating Safety Assessment Report. Declare validation of safety related documents.
11
Operation, maintenance and performance checking
Provide all statistics essential to express plans/actions for O&M. Implement O&M procedures.
Implement and retain FRACAS procedure for the acquisition and recording of RAM presentation data. Sustain FRACAS and intermittently
Implement and preserve procedure for the acquirement and recording of safety performance data.
Record modifications in the scheme configuration.
evaluate FRACAS records. Inaugurate records to trace the RAM tasks commenced. Reports of RAM performance investigation and calculation.
Check all the reliability parameters as per plan and implement all of them in the new project.
Accomplish hazard analysis. Validate safety-related submission circumstances.
Validate safety-related application situations. Validate Hazard log Validate Interface hazard analysis (IHA)
Validate Operating & support hazard analysis (O&SHA).
Validate FMECA (Failure Mode Effect Critical Analysis).
Inaugurate reports of safety performance analysis and assessment.
12
Decommissioning
Inaugurate decommissioning plan and linked report.
Recognize the RAM impact of decommissioning and dumping.
Recognize the Safety impact of decommissioning and dumping.
-
Failure categories and classification of failures according to failures
-
Relevant failures
A relevant failure of an item is an independent failure which results in a loss of function of that item caused by any of the following:
-
A fault in an equipment or sub-system while operating within its design and environmental specification limits;
-
Improper operation, maintenance, or testing of the item as a result of the Contractor supplied documentation.
-
Failures of transient nature including those with post investigation status as 'No fault found', shall be considered as relevant failure if in the opinion of the Engineer these are attributable to rolling stock. The decision of the Engineer shall be final.
-
Service failure
Any relevant failure or combination of relevant failures during revenue service operations, simulated revenue operations or during pre-departure equipment status checkouts to determine availability for revenue service, which results in one of the following:
-
Unavailability of the train to start revenue service after successful completion of pre-departure checkout.
-
Withdrawal of the train from revenue services.
-
A delay equivalent to or exceeding 3 minutes from the Schedule / Time table as noted at the destination station for the one- way trip.
S. no.
Top level failure events Train Level Effect
Effect on operation (passengers, other sub systems,)
1st line maintenance actions
Failure classification
Service Failure
Relevant Failure
1
Loss of ventilation in one car.
No sufficient air flow for emergency situations more than one cars
Withdrawal from operation
X
2
Loss of overheating protection 3rd level( Thermal fuse)
Passenger Safety
Withdrawal from operation
X
3
Fire inside the Evaporator section of HVAC
Passenger Safety
Withdrawal from operation
X
4
Total loss of cooling in one car or more cars
Passenger discomfort
Withdrawal from operation
X
5
Failure of Cab Booster
Driver discomfort
Withdrawal from operation
X
6
All Service Failure resulting in delay/detention for more than 60 (sixty) minutes or passenger deboard-ment in mid-section
Train withdrawal / Passenger Deboarding
Withdrawal from operation
X
7
Loss of ventilation in one HVAC
No sufficient air flow for emergency situations in one car
Withdrawal at the end of trip
X
8
Loss of overheating protection 1st level (bimetal thermostat)
Passenger Safety
Withdrawal from operation at the end of the trip
X
9
Loss of overheating protection 2nd level (SA sensor)
Passenger Safety
Withdrawal from operation at the end of the trip
X
10
Any leakage in piping connections between condenser / evaporator coils
No passenger discomfort
Withdrawal from operation at the end of the trip
X
11
Failure of any one HVAC in any car leading to increase in
Degrade in the temperature control in passenger area
Withdrawal from operation at the end of the trip
X
S. no.
Top level failure events Train Level Effect
Effect on operation (passengers, other sub systems,)
1st line maintenance actions
Failure classification
Service Failure
Relevant Failure
inside saloon/cab temperature
28 degree Celsius at the design ambient temperature.
12
Water dripping problem
No effect on the operation but passenger discomfort
Corrective actions
X
13
Noisy air conditioner due to compressor and condenser fans
Passenger discomfort
Withdrawal from operation at the end of the trip
X
-
-
-
Reliability prediction
Use recognized standards
-
Model failure of machineries
-
Examine system
-
Compute the system predicted failure of MTBF Evaluate prediction vs. target or required MTBF
-
Evaluate stress or temperature reduction design changes
-
Evaluate practically of design change specially when MTBF is self-inflicted
-
Methodologies
Rank
Method
Early defects
Random effects
Wear out
Description
1
Field Data
This statistics is provided by service team it is being calculated by RAMS team.
2
System reliability assessment
Combine the calculation method that combines prediction, procedure grading, operative profiles, and software and test data using Bayesian procedures.
3
Similar item Data
Based on investigational reliability field failure data on analogous products functioning in similar atmosphere. Uses generic data from association.
4
Translation
Interprets a reliability prediction based on an experimental value. Indirectly accounts for some factors affecting field reliability that is not unambiguously amounted for in the experimental model.
5
Empirical
Typically relies on experiential failure data to enumerate part-level experimental model variables. Applied is that valid failure rate is appropriate.
6
Physics- of- failure
Representations each failure mechanism for each module life separately. Component reliability is determined by merging the probability density function related with respective failure mechanism.
-
Common standards
-
MIL-HDBK 217
Generally associated with military system Provides for many environments Provides multiple quantity levels
-
Bell core (Telcordia) Telecommunication industries standard Models patterned after MIL-HDBK 217 Provides multiple quality level
-
HRD 5
Telecommunication industries standard Provides multiple quality level
-
NPRD-95
Non electric parts
Provides multiple quality level
-
NSWC-07 NAVAL SURFACE WARFARE CENTRE Hand book Reliability Prediction Procedures for Mechanical
-
-
Assumptions
-
The components are contnuous failure rates.
-
The mechanisms are in their suitable life period.
-
Infant mortalities are detached by element screening.
-
Wear out has not been reached.
-
The mechanisms are considerably standardized with those under which failure rates are dignified.
-
The prediction model uses a simple reliability series system of all mechanisms, in other words, a failure of any module is expected to lead a system failure.
-
-
Environments
-
Ground Benign GB = Non mobile temperature & humidity controlled environment.
-
Ground Benign GF = moderately controlled environment such as installation in permanent racks.
-
Space flight SF = Earth orbital. Approaches benign ground condition.
-
Missile, Flight SF = Condition related to powered flight of air breathing missiles, cruise missiles.
-
Missile, Launch ML =Serve condition related to missile launch, space vehicle re-entre and landing by parachute.
-
Cannon, Launch CL = Extreme severe conditions related to cannon launching of 155 mm and 5 inch.
-
-
-
LCC (Life Cycle Cost)
It is the overall cost which is bared by a stakeholder so that the system can perform its intended function for a particular mission time (time for which the system has to perform its intended function). It Comprise of Labor cost, material cost to perform Corrective, Preventive and overhauling maintenance for the complete life cycle of system.
-
Three pillars of LCC
Corrective Maintenance The maintenance activity performed when the failure is happened. Whenever any system or subsystem is produced it cannot be so robust that it will perform its intended function without any failure. Thus when the subsystem fails we replace it or repair it and record the failure rate for the input to RAMS.
Preventive maintenance- To minimize the failures we have to perform some kind of maintenance so that availability & reliability of our system is increased and the system can perform its intended function for more time.
Actions that can be performed as preventive task in HVAC-
-
Filter Cleaning (Fresh air)
-
Filter Cleaning (Mixed / Return air)
-
HVAC Inspection & Cleaning (Evaporator & Condenser Coil, Emergency inverter, transformer, FA RA SA & Humidity sensor)
-
HVAC Inspection & Cleaning (Supply fan & condenser fan motor, Compressor, Pressure Transducers, Heater bank, Contactors & circuit breakers, Controller, Fresh air & return air damper, Doors sealing gaskets, Thermal insulation, Sight glass)
Overhauling- Some of the sub-systems are having less life than the system. So we have to replace the subsystem at the particular interval. So that our system can perform its intended function without any failure. E.g. If the system is having 15 years of life & subsystem is having 7 years of life, we have to replace that subsystem twice during life of the system.
Note*- If we are not able to meet LCC targets of our customer we can decrease the frequency of overhauling and increase the failure rate.
2.11 Reliability Critical Item list of HVAC
Condenser Coil, Compressor, Liquid level indicator , Condenser Fan Assembly, HP Switch, LP Switch, Liquid line solenoid valve
, Solenoid Valve Coil, Hand shut-off valves, Filter Drier, Supply air Fan Assembly, Evaporator Coil, Expansion Valve, Heater Assembly, Fresh air damper, Emergency Inverter, Emergency Transformer, Temperature probe 1, Temperature probe 2, Temperature probe 3, Humidity sensor, Connector 1, Connector 2, Compressor contactor, Supply Fan Contactor, Condenser Fan Contactor, Heater contactor, Circuit breakers Compressor, Circuit breaker Supply Fan, Circuit Breaker Condenser fan, Circuit Breaker heater, Rotary switch , Controller, Relay, DC-DC Converter, Thermal overheat protector , Bimetal thermostat.
-
-
-
METHODOLOGY & CALCULATION
Description |
Formula |
Associated RBD |
Resultant Failure rate (Series connected) |
system = 1 + 2 + . + n Where system = Resultant failure rate of the system. 1 = failure rate of component 1 2 = failure rate of component 2 n = failure rate till n no. of components |
|
Resultant Failure rate (Parallel connected) |
Where |
|
Where |
||
Resultant Reliability (Series connected) |
R system = R 1 + R 2 + . + R n Where R system = Resultant reliability of the system. R 1 = reliability of component 1 R 2 = reliability of component 2 R n = reliability till n no. of components |
|
Resultant Reliability (Parallel connected) |
R system = 1-((1- R 1) (1- R 2) – .- (1- R n)) Where R system = Resultant reliability of the system. R 1 = reliability of component 1 R 2 = reliability of component 2 R n = reliability till n no. of components |
-
Reliability
-
Failure Rate prediction at subsystem level and calculation of failure rate at system level:
Table provided below defines the operational parameters of train during a mission time.
Train Mission Profile
Project: HVAC with 4 refrigeration circuits
Unit
No. of trains
1
nos.
No. of cars per train
6
nos.
Train working hours per day
21
hours
HVAC system working hours per day
21
hours
Annual distance
320000
Km
No. of days in year
365
days
Annual hours of operation
7665
hours
Average speed
46.14
Km/h
Mission time (in years)
2
years
Mission time (in hours)
15330
hours
There are two HVAC system installed in one saloon car of a train. So for 6 car train configuration, there are total 12 HVAC system installed on one train.
Scope of supply
Equipment
Qty per car
Qty per train
Saloon HVAC unit
2
12
The failure rate for the items (sub system) mentioned in below tables are taken from standard references. The calculation & conversion of failure rate are elaborated in more details below this table:
Failure Rate Data
S.No.
Item Description
MTBF (hours)
Failure rate (hour-1)
MDBF
(km)
FPMH
(10^-6 hours)
FPMK (10^-6
km)
1
HVAC
2
Condenser Coil
123791
8.08E-06
5711717
8.078
0.175
3
Compressor
62152
1.61E-05
2867693
16.090
0.349
4
Liquid level indicator
545791
1.83E-06
25182797
1.832
0.040
5
Condenser Fan Assembly
83584
1.20E-05
3856566
11.964
0.259
6
HP Switch
167752
5.96E-06
7740077
5.961
0.129
7
LP Switch
167752
5.96E-06
7740077
5.961
0.129
8
Liquid line solenoid valve
167752
5.96E-06
7740077
5.961
0.129
9
Solenoid Valve Coil
1438021
6.95E-07
66350289
0.695
0.015
10
Hand shut-off valves
167752
5.96E-06
7740077
5.961
0.129
11
Filter Drier
3448275
2.90E-07
159103409
0.290
0.006
12
Supply air Fan Assembly
83584
1.20E-05
3856566
11.964
0.259
13
Evaporator Coil
123791
8.08E-06
5711717
8.078
0.175
14
TX Valve
161168
6.20E-06
7436292
6.205
0.134
15
Heater Assembly
12165450
8.22E-08
561313869
0.082
0.002
16
Fresh air damper
99006
1.01E-05
4568137
10.100
0.219
17
Emergency Inverter
9999999
1.00E-07
461399954
0.100
0.002
18
Emergency Transformer
1669449
5.99E-07
77028381
0.599
0.013
19
Temperature probe 1
276816
3.61E-06
12772290
3.613
0.078
20
Temperature probe 2
276816
3.61E-06
12772290
3.613
0.078
21
Temperature probe 3
276816
3.61E-06
12772290
3.613
0.078
22
Humidity sensor
276816
3.61E-06
12772290
3.613
0.078
23
Connector 1
280614108
3.56E-09
12947534943
0.004
0.000
24
Connector 2
280614108
3.56E-09
12947534943
0.004
0.000
25
Compressor contactor
4697065
2.13E-07
216722579
0.213
0.005
26
Supply Fan Contactor
4697065
2.13E-07
216722579
0.213
0.005
27
condenser Fan Contactor
4697065
2.13E-07
216722579
0.213
0.005
28
Heater contactor
4697065
2.13E-07
216722579
0.213
0.005
29
Circuit breakers Compressor
1176470
8.50E-07
54282326
0.850
0.018
30
Circuit breaker Supply Fan
1176470
8.50E-07
54282326
0.850
0.018
31
Circuit Breaker condenser fan
1176470
8.50E-07
54282326
0.850
0.018
32
Circuit Breaker heater
1176470
8.50E-07
54282326
0.850
0.018
33
Rotary switch
12165450
8.22E-08
561313863
0.082
0.002
34
Controller
9999999
1.00E-07
461399954
0.100
0.002
35
Relay
9999999
1.00E-07
461399954
0.100
0.002
36
DC-DC Converter
498845016
2.00E-09
23016709038
0.002
0.000
37
Thermal Overheat fuse
15151823
6.60E-08
699105113
0.066
0.001
38
Bimetal thermostat
15151823
6.60E-08
699105113
0.066
0.001
Calculation of the above table
-
Condenser Coil
MTBF 123791 (from NPRD 95 Standard)
Failure Rate () = 1
= 1
123791
= 8.08E-06 hour-1
MDBF (Mean Distance between failure) = MTBF * Average speed of train = 123791 * 46.14
= 5711717 km
FPMH (Failure per million hour) = Failure Rate () * 106 = 8.08E-06 * 106
= 8.08
FPMK (Failure per million kilometer) = FPMH
= 8.08
46.14
= 0.175
Note* – Same calculation is followed for the complete table.
Intrinsic Reliability Calculation Cooling function
S.no.
Item Description
MTBF (hours)
Component Failure rate (/hour)
Quantity per HVAC
Total failure Rate (/hour) (HVAC Level)
1
Hand shut-off valves
167752
5.96E-06
8
4.77E-05
2
Solenoid coil
1438021
6.95E-07
4
2.78E-06
3
LP SWITCH
167752
5.96E-06
4
2.38E-05
4
Liquid level indicator
545791
1.83E-06
4
7.33E-06
5
Compressor Circuit breaker
1176470
8.50E-07
4
3.40E-06
6
Compressor Contactor
4697065
2.13E-07
4
8.52E-07
7
Expansion valve
161168
6.20E-06
4
2.48E-05
8
Filter Drier
3448275
2.90E-07
4
1.16E-06
9
HP Switch
167752
5.96E-06
4
2.38E-05
10
Liquid line solenoid Valve
167752
5.96E-06
4
2.38E-05
11
Compressor
62152
1.61E-05
4
6.44E-05
12
Evaporator coil
123791
8.08E-06
2
1.62E-05
13
Condenser coil
123791
8.08E-06
2
1.62E-05
14
Condenser fan circuit breaker
1176470
8.50E-07
2
1.70E-06
15
Condenser fan contactor
4697065
2.13E-07
2
4.26E-07
16
Condenser fan
83584
1.20E-05
2
2.39E-05
17
Supply fan circuit breaker
1176470
8.50E-07
2
1.70E-06
18
Supply Fan
83584
1.20E-05
2
2.39E-05
19
Supply fan contactor
4697065
2.13E-07
2
4.26E-07
Total failure rate HVAC level (/hour)
3.08E-04
Intrinsic failure rate FPMH HVAC level (/Million hour)
308.34
Intrinsic failure rate FPMK HVAC level (/Million km)
6.68
Intrinsic failure rate FPMK Train level (/Million km)
80.19
Total failure rate HVAC level (/hour) = Summation of all failure rates = 3.08E-04
Total MTTF HVAC level (hour) = 1
= 3246 hours
= 1
.
Intrinsic failure rate FPMH HVAC level (/Million hour) = Total failure rate HVAC level (/hour) * 106
= 308.34
Intrinsic failure rate FPMK HVAC level (/Million km) =Intrinsic failure rate FPMH HVAC level (/Million hour)
Average Speed
= 308.34
.
= 6.68
Intrinsic failure rate FPMK Train level (/Million km) = Intrinsic failure rate FPMK HVAC level * No. Of
HVAC in 1 Train
= 6.68 * 12
= 80.19
Relevant Failure – Reliability Calculation for Cooling function
S.no.
Item Description
Quantity per HVAC
MTBF (hours
)
Failure rate (/hour)
Duty cycle
Component MTBF with duty cycle
Total failure rate (HVAC level) with duty cycle
1
Connector 2
1
280614108
3.56E-09
1
280614108
3.56E-09
2
DC-DC convertor
2
498845016
2.00E-09
1
498845016
2.00E-09
3
Rotary switch
1
12165450
8.22E-08
1
12165450
8.22E-08
4
Controller
1
9999999
1.00E-07
1
9999999
1.00E-07
5
Connector 1
1
280614108
3.56E-09
1
280614108
3.56E-09
8.08E-06
Failure rate of electrical components
1.91E-07
6
Temperature probe 1
1
276816
3.61E-06
1
276816
3.61E-06
7
Temperature probe 2
1
276816
3.61E-06
1
276816
3.61E-06
Failure rate of sensors
2.00E-07
8
Hand shutoff valve
8
167752
5.96E-06
0.6
279587
3.57671E-06
9
Solenoid coil
4
1438021
6.95E-07
0.6
2396702
4.17E-07
10
LP
4
167752
5.96E-06
0.6
279587
3.58E-06
11
Liquid level indicator
4
545791
1.83E-06
0.6
909652
1.10E-06
12
Compressor circuit breaker
4
1176470
8.50E-07
0.6
1960783
5.10E-07
13
Compressor Contactor
4
4697065
2.13E-07
0.6
7828442
1.28E-07
14
Compressor
4
62152
1.61E-05
0.6
103587
9.65E-06
15
Liquid line solenoid valve
4
167752
5.96E-06
0.6
279587
3.58E-06
16
HP
4
167752
5.96E-06
0.6
279587
3.58E-06
17
Filter drier
4
3448275
2.90E-07
0.6
5747125
1.74E-07
18
Expansion valve
4
161168
6.20E-06
0.6
268613
3.72E-06
19
Evaporator coil
2
123791
0.6
206318
4.85E-06
20
Condenser coil
2
123791
8.08E-06
0.6
206318
4.85E-06
Failure rate of one cooling branch
3.97E-05
MTBF of one cooling branch
25185
Failure rate of two parallel cooling branch
2.42E-05
21
Condenser fan circuit breaker
2
1176470
8.50E-07
1
1176470
8.50E-07
22
Condenser fan contactor
2
4697065
2.13E-07
1
4697065
2.13E-07
23
Condenser fan
2
83584
1.20E-05
1
83584
1.20E-05
Failure rate of one condenser fan branch
1.30E-05
Failure rate of one complete cooling circuits
3.72E-05
MTBF of one complete cooling circuits
26885
Failure rate of all cooling circuits
2.12E-05
24
Supply fan circuit breaker
2
1176470
8.50E-07
1
1176470
8.50E-07
25
Supply fan contactor
2
4697065
2.13E-07
1
4697065
2.13E-07
26
Supply fan
2
83584
1.20E-05
1
83584
1.20E-05
Failure rate of one supply fan branch
1.30E-05
MTBF of one supply fan branch
76764
Failure rate of two supply fan branches
2.60E-06
Total failure rate HVAC level (/hour)
2.42.E-05
Total failure rate FPMH HVAC level (/Million hour)
24.20
Total failure rate FPMK HVAC level (/Million km)
0.52
Total failure rate FPMK Train level (/Million km)
6.29
Resultant Failure rate (Series connected) = system = 1 + 2 + . + n
Resultant Failure rate (Parallel connected) =
= 1
(())/)
Failure rate of electrical components (all are in Series)
= Connector 2 + DC-DC convertor + Rotary switch + Controller + Connector 1
= 3.56E-09 + 2.00E-09 + 8.22E-08 + 1.00E-07 + 3.56E-09
= 1.91E-07 Failures/ hour Failure rate of sensors (all are in Parallel) = 1
(())/)
Temperature Probe 1 = 3.61E-06 Temperature Probe 2 = 3.61E-06 MTBF = 276816 hours Mission Time = 15330 Hours
= 1
((276816))/15330)
= 2.00E-07 Failures / hour
Failure rate of one cooling branch
= Hand shutoff valve + Solenoid coil + LP + Liquid level indicator + Compressor circuit breaker + Compressor Contactor + Compressor + Liquid line solenoid valve + HP + Filter drier + Expansion valve + Evaporator coil + Condenser coil
= 3.97E-05 Failures/ hour
MTBF one cooling branch = 25185 hours
Failure rate of two parallel cooling branch = 1
(())/)
MTBF one cooling branch = 25185 hours Mission Time = 15330 hours
= 1
(())/)
= 1
((25185))/15330)
= 2.42E-05 Failures/ hour
Failure rate of one condenser fan branch =
Condenser fan circuit breaker + Condenser fan contactor + Condenser fan
= 8.50E-07 + 2.13E-07 + 1.20E-05
= 1.30E-05 Failures/ hour
Failure rate of one complete cooling circuits =
Failure rate of two parallel cooling branch + Failure rate of one condenser fan branch
= 2.42E-05 + 1.30E-05
= 3.72E-05 Failures/ hour
Failure rate of all 4 cooling circuits (Parallel)= 1
(())/)
MTBF One complete cooling circuit along with condenser fan = 26885 hours Mission Time = 15330 hours
1
((26885))/15330)
Failure rate of all 4 cooling circuits = 2.12E-05 Failures/hour
Failure rate of one supply fan branch (all in series)
= Supply fan circuit breaker + Supply fan contactor+ Supply fan
= 8.50E-07 + 2.13E-07 + 1.20E-05
= 1.30E-05 Failures/ Hour
Failure rate of two supply fan branches (Parallel) = 1
(())/)
MTBF one supply fan branch = 76764
1 ((76764))/15330)
Failure rate of two supply fan branches = 2.60E-06 Failures/ hour
Total failure rate HVAC level (Series) = Failure rate of electrical components + Failure rate of sensors + Failure rate of all cooling circuits + Failure rate of two supply fan branches
= 1.91E-07 + 2.00E-07+ 2.12E-05+ 2.60E-06
= 2.42.E-05 Failure/Hour
Total failure rate FPMH HVAC level (/Million hour) = Total failure rate HVAC level * 106
= 24.20
Total failure rate FPMK HVAC level (/Million km) = Total failure rate FPMH HVAC level
= 24.20
46.14
= 0.52
Total failure rate FPMK Train level (/Million km) = Total failure rate FPMK HVAC level * No. Of
HVAC per train
= 0.52* 12
= 6.29
td>
3.61E-06
Relevant Failure – Reliability Calculation for Heating function
S.no.
Item Description
Quantity per HVAC
MTBF (hours
)
Failure rate (hour-1)
Duty cycle
Component MTBF with duty cycle
Total failure rate on HVAC level with duty cycle
1
Connector 2
1
280614108
3.56E-09
1
280614108
3.56E-09
2
DC-DC convertor
2
498845016
2.00E-09
1
498845016
2.00E-09
3
Rotary switch
1
12165450
8.22E-08
1
12165450
8.22E-08
4
Controller
1
9999999
1.00E-07
1
9999999
1.00E-07
5
Connector 1
1
280614108
3.56E-09
1
280614108
3.56E-09
Failure rate of electrical components
1.91E-07
6
Temperature probe 1
1
276816
3.61E-06
1
276816
7
Temperature probe 2
1
276816
3.61E-06
1
276816
3.61E-06
Failure rate of sensors
2.00E-07
8
Heater circuit breaker
2
1176470
8.50E-07
1
1176470
8.50E-07
9
Heater contactor
2
4697065
2.13E-07
1
4697065
2.13E-07
10
Bimetal thermostat
4
15151823
6.60E-08
1
15151823
1.32E-07
11
Thermal overheat fuse
2
15151823
6.60E-08
1
15151823
6.60E-08
12
Heater
2
12165450
8.22E-08
1
12165450
8.22E-08
Failure rate of SF2 category components
1.34E-06
MTBF of one heating branch
744549
Failure rate of two heating branches
2.77E-08
13
Supply fan circuit breaker
2
1176470
8.50E-07
1
1176470
8.50E-07
14
Supply fan contactor
2
1176470
8.50E-07
1
1176470
8.50E-07
15
Supply fan
2
83584
1.20E-05
1
83584
1.20E-05
Failure rate of one supply fan branch
1.37E-05
MTBF of one supply fan branch
73185
Failure rate of two supply fan branches
2.86E-06
Total failure rate HVAC level (/hour)
3.28.E-06
Total failure rate FPMH HVAC level (/Million hour)
3.28
Total failure rate FPMK HVAC level (/Million km)
0.07
Total failure rate FPMK Train level (/Million km)
0.85
Relevant Failure – Reliability Calculation for Ventilation function
S.no.
Item Description
Quantity per HVAC
MTBF (hours
)
Failure rate (hour-1)
Duty cycle
Component MTBF with duty cycle
Total failure rate on HVAC level with duty cycle
1
Connector 2
1
280614108
3.56E-09
1
280614108
3.56E-09
2
DC-DC converter
2
498845016
2.00E-09
1
498845016
2.00E-09
3
Rotary switch
1
12165450
8.22E-08
1
12165450
8.22E-08
4
Controller
1
9999999
1.00E-07
1
9999999
1.00E-07
5
Connector 1
1
280614108
3.56E-09
1
280614108
3.56E-09
Failure rate of electrical components
1.91E-07
6
Temperature probe 1
1
276816
3.61E-06
1
276816
3.61E-06
7
Temperature probe 2
1
276816
3.61E-06
1
276816
3.61E-06
Failure rate of sensors
2.00E-07
8
Supply fan circuit breaker
2
280614108
3.56E-09
1
280614108
3.56E-09
9
Supply fan contactor
2
280614108
3.56E-09
1
280614108
3.56E-09
10
Supply fan
2
83584
1.20E-05
1
83584
1.20E-05
Failure rate of one supply fan branch
1.20E-05
MTBF of one supply fan branch
83534
Failure rate of two supply fan branches
2.20E-06
Total failure rate HVAC level (/hour)
2.59.E-06
Total failure rate FPMH HVAC level (/Million hour)
2.59
Total failure rate FPMK HVAC level (/Million km)
0.06
Total failure rate FPMK Train level (/Million km)
0.67
Service Failure – Reliability Calculation for Heating
S.no.
Item Description
Quantity per HVAC
MTBF
(hours )
Failure rate (hour-1)
Duty cycle
Component MTBF with duty cycle
Total failure rate (HVAC level) with duty cycle
1
Thermal Overheat fuse
2
15151823
6.60E-08
0.5
30303646
3.30E-08
MTBF Fuse
3.03E+07
Parallel FAILURE RATE Fuse
2.29E-14
2
Supply fan circuit breaker
2
1176470
8.50E-07
1
1176470
8.50E-07
3
Supply fan contactor
2
4697065
2.13E-07
1
4697065
2.13E-07
4
Supply fan
2
83584
1.20E-05
1
83584
1.20E-05
Failure Rate Series
1.30E-05
MTBF
7.68E+04
Parallel FAILURE RATE Of supply fan
2.60E-06
Failure rate of SF2 category components
2.60E-06
Total failure rate FPMH HVAC level (/Million hour)
2.60E+00
Total failure rate FPMK HVAC level (/Million km)
0.0564
Total failure rate FPMK Train level (/Million km)
0.677
Service Failure – Reliability Calculation for Emergency Ventilation function
S.no.
Item Description
Quantity per HVAC
MTBF (hours
)
Failure rate (hour-1)
Duty cycle
Component MTBF with duty cycle
Total failure rate on HVAC level with duty cycle
1
Connector 2
1
280614108
3.56361E-09
1
280614108
3.56E-09
2
DC-DC converter
2
498845016
2.00463E-09
1
498845016
2.00E-09
3
Rotary switch
1
12165450
8.22E-08
1
12165450
8.22E-08
4
Emergency Inverter
1
9999999
1.00E-07
1
9999999
1.00E-07
5
Emergency Transformer
1
1669449
5.99E-07
1
1669449
5.99E-07
Failure rate of electrical components
7.87E-07
6
Supply fan circuit breaker
2
1176470
8.5E-07
1
1176470
8.50E-07
7
Supply fan contactor
2
4697065
2.12899E-07
1
4697065
2.13E-07
8
Supply fan
2
83584
1.1964E-05
1
83584
1.20E-05
Failure rate of one supply fan branch
1.30E-05
MTBF of one supply fan branch
76764
Failure rate of two supply fan branches
2.60E-06
Total failure rate HVAC level (/hour)
3.39.E-06
Total failure rate FPMH HVAC level (/Million hour)
3.39
Total failure rate FPMK HVAC level (/Million km)
0.07
Total failure rate FPMK Train level (/Million km)
0.88
Reliability Calculation category wise
S.no.
Item Description
Total failure rate (Train level) FPMK
1
Relevant Failure Cooling function
6.294
2
Relevant Failure Heating function
0.853
3
Relevant Failure Ventilation
0.673
4
Service Failure Emergency Ventilation
0.881
5
Service Failure Heating
0.677
-
-
-
Reliability Block Diagram
Item Description
Per HVAC
MTBF
Life of item in years
Hour Per year
Mission Time
( Hours )
Reliability
Reliability %
HVAC
1
96.804%
Condenser Coil
2
123791
2
7300
14600
0.889
88.875
Compressor
4
62152
2
7300
14600
0.791
79.064
Liquid level indicator
4
545791
2
7300
14600
0.974
97.360
Condenser Fan Assembly
2
83584
2
7300
14600
0.840
83.973
HP Switch
4
167752
2
7300
14600
0.917
91.665
LP Switch
4
167752
2
7300
14600
0.917
91.665
Liquid line solenoid valve
4
167752
2
7300
14600
0.917
91.665
Solenoid Valve Coil
4
1438021
2
7300
14600
0.990
98.990
Hand shut-off valves
8
167752
2
7300
14600
0.917
91.665
Filter Drier
4
3448275
2
7300
14600
0.996
99.577
Supply air Fan Assembly
2
83584
2
7300
14600
0.840
83.973
Evaporator Coil
1
123791
2
7300
14600
0.889
88.875
TX Valve
4
161168
2
7300
14600
0.913
91.339
Heater Assembly
1
12165450
2
7300
14600
0.999
99.880
Fresh air damper
2
99006
2
7300
14600
0.863
86.289
Emergency Inverter
1
9999999
2
7300
14600
0.999
99.854
Emergency Transformer
1
1669449
2
7300
14600
0.991
99.129
Temperature probe 1
1
276816
2
7300
14600
0.949
94.862
Temperature probe 2
1
276816
2
7300
14600
0.949
94.862
Temperature probe 3
1
276816
2
7300
14600
0.949
94.862
Humidity sensor
1
276816
2
7300
14600
0.949
94.862
Connector 1
1
280614108
2
7300
14600
1.000
99.995
Connector 2
1
280614108
2
7300
14600
1.000
99.995
Compressor contactor
4
4697065
2
7300
14600
0.997
99.690
Supply Fan Contactor
2
4697065
2
7300
14600
0.997
99.690
Condenser Fan Contactor
2
4697065
2
7300
14600
0.997
99.690
Heater contactor
2
4697065
2
7300
14600
0.997
99.690
Circuit breakers Compressor
4
1176470
2
7300
14600
0.988
98.767
Circuit breaker Supply Fan
2
1176470
2
7300
14600
0.988
98.767
Circuit Breaker Condenser fan
2
1176470
2
7300
14600
0.988
98.767
Circuit Breaker heater
2
1176470
2
7300
14600
0.988
98.767
Rotary switch
1
12165450
2
7300
14600
0.999
99.880
Controller
1
200401
2
7300
14600
0.930
92.974
Relay
25
9999999
2
7300
14600
0.999
99.854
DC-DC Converter
2
498845016
2
7300
14600
1.000
99.997
Thermal Overheat protector
1
15151823
2
7300
14600
0.999
99.904
Bimetal thermostat
1
15151823
2
7300
14600
0.999
99.904
Reliability Block Diagram for RRTS HVAC unit
FAT
Hand shut LP Liquid level Compressor Compressor Compressor HP Hand shut
0.9486 off valve CB Contactor off valve 0.9166 0.9166 0.9736 0.9877 0.9969 0.7906 0.9166 0.9166
Connector 2 DC- DC Rotary Controller Connector 1 RAT Converter switch
0.9999 1.0000 0.9988 0.9297 0.9999 0.9486 0.384422308
0.998719 SAT
0.929688257 Filter Expansion Evaporator Condenser
0.9486 drier valve coil coil
0.99986439 0.9958 0.9134 0.8887 0.8887
Complete HVAC Reliability 0.96804
0.926840275
Hand shut LP Liquid level Compressor Compressor Compressor HP Hand shut off valve CB Contactor off valve
0.9166 0.9166 0.9736 0.9877 0.9969 0.7906 0.9166 0.9166 Condenser Cond. Fan Condenser Supply fan Supply fan Supply
fan CB Contactor fan CB Contactor fan
0.9877 0.9969 0.8397 0.9877 0.9969 0.8397
0.384422308 0.826799621
0.82679962
Filter Expansion Evaporator Condenser drier valve coil coil 0.9958 0.9134 0.8887 0.8887
0.621064105 0.51349557
Hand shut
LP
Liquid level
Compressor
Compressor
Compressor
HP
Hand shut
off valve
CB
Contactor
off valve
0.9166
0.9166
0.9736
0.9877
0.9969
0.7906
0.9166
0.9166
0.384422308
Filter
Expansion
Evaporator
Condenser
drier
valve
coil
coil
0.9958
0.9134
0.8887
0.8887
Hand shut
LP
Liquid level
Compressor
Compressor
Compressor
HP
Hand shut
off valve
CB
Contactor
off valve
0.9166
0.9166
0.9736
0.9877
0.9969
0.7906
0.9166
0.9166
Condenser
Cond. Fan
Condenser
Supply fan
Supply fan
Supply
fan CB
Contactor
fan
CB
Contactor
fan
0.9877
0.9969
0.8397
0.9877
0.9969
0.8397
0.384422308
0.82679962
0.826799621
Filter
Expansion
Evaporator
Condenser
drier
valve
coil
coil
0.970001629
0.9958
0.9134
0.8887
0.8887
0.51349557
0.621064105
Heater
Bimetal
Thermal Overheat protector
Heater
Contactor
Thermostat
0.9969
0.9990
0.9990
0.9988
Heater
0.993783796
CB
0.9877
0.999961359
Heater
Bimetal
Thermal Overheat protector
Heater
Contactor
Thermostat
0.987628516
0.9969
0.9990
0.9990
0.9988
0.993783796
0.99707184
Emergency Emergency
0.999257 Inverter Transformer
0.9985 0.9913
0.989846498
-
Availability
-
MTTR (Mean Time to repair) of complete HVAC
S.no.
Item Description
Qty per system, Qi
Individual Failure Rate, i [FPMH]
Average Time to Perform Corrective Maintenance Tasks, MTTRi
MTTR
i
(h)
Qi×i
Qi×i×MT TRi
Localiz ation
Isolat ion
Disasse mbly
Interch ange
Reassem ble
Alignm ent
Check out
1
Condenser Coil
2
8.078
0.16
0.16
0.25
0.25
0.93
0.25
6
8.00
16.16
1.29E+02
2
Compressor
4
16.090
0.16
0.16
0.25
0.25
0.93
0.25
6
8.00
64.36
5.15E+02
3
Sight glass
4
1.8322
0.0833
0.083
0.25
0.25
0.93
0.25
6
6.00
7.33
4.40E+01
4
Condenser Fan Assembly
2
11.964
0.0833
0.083
0.06
0.06
0.06
0.06
0.06
0.5
23.92
11.96
5
HP Switch
4
5.96118
0.0833
0.083
0.06
0.06
0.06
0.06
0.06
0.5
23.84
11.92
6
LP Switch
4
5.96118
0.0833
0.083
0.06
0.06
0.06
0.06
0.06
0.5
23.84
11.92
7
Liquid line solenoid valve
4
5.961
0.0833
0.083
0.25
0.25
0.93
0.25
6
6
23.84
143.07
8
Solenoid Valve Coil
4
0.695
0.0833
0.083
0.016
0.017
0.017
0.017
0.017
0.25
2.78
0.695
9
Hand shut-off valves
8
5.96118
0.0833
0.083
0.25
0.25
0.93
0.25
6
6
47.69
286.14
10
Filter Drier
4
0.29
0.0833
0.083
0.166
0.167
0.167
0.167
0.167
1
1.160
1.160
11
Supply air Fan Assembly
2
11.964
0.0833
0.083
0.066
0.067
0.067
0.067
0.067
0.5
23.93
11.96
12
Evaporator Coil
1
8.078
0.16
0.16
0.25
0.25
0.93
0.25
6
8
8.078
64.63
13
TX Valve
4
6.205
0.0833
0.083
0.25
0.25
0.93
0.25
6
6
24.82
148.912
14
Heater Assembly
1
0.082
0.0833
0.083
0.06
0.06
0.06
0.06
0.06
0.5
0.082
2
0.0411
15
Thermal overload fuse
1
0.066
0.0833
0.083
0.02
0.02
0.02
0.02
0.02
0.25
0.066
0.01649
16
Thermal fuse
1
0.066
0.0833
0.083
0.01
0.01
0.01
0.01
0.01
0.1
0.066
0.00659
17
Bimetal thermostat
3
0.066
0.0833
0.083
0.01
0.01
0.01
0.01
0.01
0.1
0.198
0.01979
18
Fresh air damper
2
10.1004
0.0833
0.083
0.37
0.37
0.37
0.37
0.37
2
20.20
40.402
19
Emergency Inverter
1
0.1
0.16
0.16
0.04
0.04
0.04
0.04
0.04
0.5
0.1
0.0500
20
Emergency Transformer
1
0.599
0.16
0.16
0.04
0.04
0.04
0.04
0.04
0.5
0.599
0.2995
21
Temperature probe 1
1
3.613
0.0833
0.083
0.02
0.02
0.02
0.02
0.02
0.25
3.613
0.903
22
Temperature probe 2
1
3.613
0.0833
0.083
0.17
0.17
0.17
0.17
0.17
1
3.612
3.613
23
Temperature probe 3
1
3.613
0.0833
0.083
0.0167
0.017
0.017
0.017
0.017
0.25
3.612
0.9031
24
Humidity sensor
1
3.613
0.0833
0.083
0.0167
0.017
0.017
0.017
0.017
0.25
3.612
0.90312
25
Connector 1
1
0.00356
0.0833
0.083
0.0667
0.067
0.067
0.067
0.067
0.5
0.003
0.00178
26
Connector 2
1
0.00356
0.0833
0.083
0.1667
0.167
0.167
0.167
0.167
1
0.003
0.0035
27
Compressor contactor
4
0.2129
0.0833
0.083
0.0167
0.017
0.017
0.017
0.017
0.25
0.851
0.2128
28
Supply Fan, Condenser Fan & Heater contactor
6
0.2129
0.0833
0.083
0.0167
0.017
0.017
0.017
0.017
0.25
1.277
0.31934
29
Circuit breakers (all type)
10
0.850
0.0833
0.083
0.0167
0.017
0.017
0.017
0.017
0.25
8.500
2.125001
30
Rotary switch
1
0.0822
0.0833
0.083
0.0167
0.017
0.017
0.017
0.017
0.25
0.082
0.02055
31
Controller
1
0.1
0.05
0.05
0.08
0.08
0.08
0.08
0.08
0.5
0.1
0.050000
32
Relay
25
0.1
0.0833
0.083
0.0667
0.067
0.067
0.067
0.067
0.5
2.500
1.250000
33
DC-DC Converter
2
0.002
0.0833
0.083
0.0167
0.017
0.017
0.017
0.017
0.25
0.004
0.001002
n i=1 n i=1
( ) = 1.43E+03
( ) = 3.41E+02
=
=
n () 1.43E+03
MTTR =
i=1
i=1
i=1
n () 3.41E+02
MTTR of Complete HVAC = 4.20E+00 hours
-
MTBF (Mean Time between Failures) of complete HVAC Reliability for 2 years of mission time = 96.80398%
Mission Time (hours) = 2 years = 2* 7665
=15330 hours
R (t) = ()
= e- *t
After applying above equation Failure rate () of complete HVAC = 2.121E-06
MTBF = 1/ Failure rate () =471475
-
Availability of Complete HVAC
A =
+
Availability of complete HVAC = 99.999109%
-
-
Maintainability
= 471475
471475+ .
= 0.99999109
Repair rate = µ = 1
MTTR
= 1
.
= 0.23809
t = allowable down time
= 2 hours
Maintainability = M (t) = µ µ = 1 – µ
= 0.3788
Maintainability of complete HVAC = 37.88 % -
Safety
Hazard Rate h (t) = ()
()
F (t) = 1- R (t)
= 1 0.96
= 0.04
R (t) = 0.96
h (t) = 0.04 = 0.04166
0.96
Hazard Rate of complete HVAC = 4.166%
-
RESULTS
Failure Rate of individual components so that main culprits of failure can be find out and either the components are to be changed or redundancy is provided.
Failure rate (per hour)
0.000018
0.000016
0.000014
0.000012
0.00001
0.000008
0.000006
0.000004
0.000002
Condensor Coil
Compressor Liquid level indicator Condensor Fan Assembly
HP Switch LP Switch
Liquid line solenoid valve Solenoid Valve Coil Hand shut-off valves
Filter Drier Supply air Fan Assembly
Evaporator Coil
TX Valve Heater Assembly Fresh air damper Emergency Inverter
Emergency Transformer Temperature probe 1
Temperature probe 2
Temperature probe 3
Hygrostate
Connector 1
Connector 2 Compressor contactor Supply Fan Contactor Condensor Fan Contactor
Heater contactor Circuit breakers Compressor Circuit breaker Supply Fan Circuit Breaker Condensor fan Circuit Breaker heater
Rotary switch Controller
Relay DC-DC Converter
Thermal Overheat protector Bimetal thermostate
Condensor Coil
Compressor Liquid level indicator Condensor Fan Assembly
HP Switch LP Switch
Liquid line solenoid valve Solenoid Valve Coil Hand shut-off valves
Filter Drier Supply air Fan Assembly
Evaporator Coil
TX Valve Heater Assembly Fresh air damper Emergency Inverter
Emergency Transformer Temperature probe 1
Temperature probe 2
Temperature probe 3
Hygrostate
Connector 1
Connector 2 Compressor contactor Supply Fan Contactor Condensor Fan Contactor
Heater contactor Circuit breakers Compressor Circuit breaker Supply Fan Circuit Breaker Condensor fan Circuit Breaker heater
Rotary switch Controller
Relay DC-DC Converter
Thermal Overheat protector Bimetal thermostate
0
Repair of individual components so that main culprits of loss in availability can be find out and either the components are to be changed or redundancy is provided.
Repair Time (hours)
Repair Time (hours)
DC-DC Converter
Relay Controller Rotary switch
Circuit breakers (all type) Supply Fan, Condensor Fan & Heater contactor
Compressor contactor Control Connector P2 Power Connector P1
Hygrostate Temprature probe 3
Temprature probe 2
Temprature probe 1 Emergency Transformer Emergency Inverter Fresh air damper Bimetal thermostat
Thermal fuse
ESTI
Heater Assembly
TX Valve Evaporator Coil
Supply air Fan Assembly
Filter Drier Hand shut-off valves Solenoid Valve Coil Liquid line solenoid valve
LP Switch HP Switch
Condensor Fan Assembly
Sight glass Compressor Condensor Coil
DC-DC Converter
Relay Controller Rotary switch
Circuit breakers (all type) Supply Fan, Condensor Fan & Heater contactor
Compressor contactor Control Connector P2 Power Connector P1
Hygrostate Temprature probe 3
Temprature probe 2
Temprature probe 1 Emergency Transformer Emergency Inverter Fresh air damper Bimetal thermostat
Thermal fuse
ESTI
Heater Assembly
TX Valve Evaporator Coil
Supply air Fan Assembly
Filter Drier Hand shut-off valves Solenoid Valve Coil Liquid line solenoid valve
LP Switch HP Switch
Condensor Fan Assembly
Sight glass Compressor Condensor Coil
0
1
2
3
4
5
6
7
8
9
0
1
2
3
4
5
6
7
8
9
Reliability of individual components so that main culprits of reliability can be find out and either the components are to be changed or redundancy is provided.
Reliability %
120.000
100.000
80.000
60.000
40.000
20.000
0.000
Condensor Coil
Compressor Liquid level indicator Condensor Fan Assembly
HP Switch LP Switch
Liquid line solenoid valve Solenoid Valve Coil Hand shut-off valves
Filter Drier
Supply air Fan Assembly
Evaporator Coil
TX Valve Heater Assembly Fresh air damper Emergency Inverter
Emergency Transformer Temperature probe 1
Temperature probe 2
Temperature probe 3
Hygrostate
Connector 1
Connector 2 Compressor contactor Supply Fan Contactor Condensor Fan Contactor
Heater contactor Circuit breakers Compressor Circuit breaker Supply Fan Circuit Breaker Condensor fan Circuit Breaker heater
Rotary switch
Controller
Relay DC-DC Converter
Thermal Overheat protector Bimetal thermostate
Condensor Coil
Compressor Liquid level indicator Condensor Fan Assembly
HP Switch LP Switch
Liquid line solenoid valve Solenoid Valve Coil Hand shut-off valves
Filter Drier
Supply air Fan Assembly
Evaporator Coil
TX Valve Heater Assembly Fresh air damper Emergency Inverter
Emergency Transformer Temperature probe 1
Temperature probe 2
Temperature probe 3
Hygrostate
Connector 1
Connector 2 Compressor contactor Supply Fan Contactor Condensor Fan Contactor
Heater contactor Circuit breakers Compressor Circuit breaker Supply Fan Circuit Breaker Condensor fan Circuit Breaker heater
Rotary switch
Controller
Relay DC-DC Converter
Thermal Overheat protector Bimetal thermostate
Reliability %
120.000
100.000
80.000
60.000
40.000
20.000
0.000
Data
Results
Reliability of complete HVAC with 4 Circuits (2 years of mission time)
96.804%
MTTR of complete HVAC with 4 Circuits (2 years of mission time)
4.20E+00 hours
Availability of complete HVAC with 4 Circuits (2 years of mission time)
99.99911%
Maintainability of complete HVAC with 4 Circuits (2 years of mission time)
37.88 %
Safety/ Hazard rate of complete HVAC with 4 Circuits (2 years of mission time)
4.166%
-
CONCLUSION
This research was accomplished in assistance with mentor in RAMS & service of HVAC with an approach of quality & reliability enhancement at the system level by taking in consideration of service failure & relevant failures.
The research work was carried out to find the reliability at system level by using the sub system level approach. To enhance the reliability of the system we provided redundancy at the subsystem level by analyzing the failure rate (taken from respective standards) of reliability critical sub system along with mission time.
On the basis of reliability & time to restore the system to perform its intended function, we calculated the availability of the system at train level.
Maintainability analysis of the system is carried out by taking in consideration of the repair rate and allowable down time at train level.
For safety analysis, we have taken the HVAC failure which leads to fire, HVAC explosion, toxic refrigerant leak, electrocution. We have calculated the Hazard rate by taking inputs from probability density function and reliability function.
The key objective of the research was to study how the redundancy provided at sub system level will enhance the system level reliability.
The key objective of this research was the calculation of the availability of HVAC at train level. The benchmark value of availability for HVAC in rolling stock is approx. greater than 95% during normal operation as by the calculation of 4 circuit, we get he value of 99.99 %. This shows the series parallel combination of sub system is perfect as per requirement of rolling stock.
-
ABBREVIATIONS
RAMS Reliability, availability, maintainability & safety HVAC Heating ventilation air conditioners
MTBF – Mean time between failure MDBF Mean distance between failure FPMH – Failure per million hour FPMK – Failure per million kilometers MTTR Mean time to repair
LCC Life cycle cost
-
REFERENCES
-
United States Air Force Rome Laboratory Reliability Engineer's Toolkit (1993).
-
MIL-HDBK-338, Electronic Reliability Design Handbook.
-
Klion, Jerome, A Redundancy Notebook, Rome Air Development Center, RADC-TR-77-287, December 1987.
-
Reliability Modeling and Prediction, MIL-STD-756B, November 1981.
-
McGregor, Malcolm A., Approximation Formulas for Reliability with Repair, IEEE Transactions on Reliability, Volume R-12, Number 4, December 1963.
-
Bazovsky, Igor, Reliability Theory and Practice.
-
O'Connor, Patrick, D. T., Practical Reliability Engineering.