
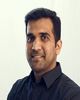
- Open Access
- Authors : Bharath Umesh Gadiyar , Manjunath Soppin , Praveen Ahuja
- Paper ID : IJERTV10IS020268
- Volume & Issue : Volume 10, Issue 02 (February 2021)
- Published (First Online): 08-03-2021
- ISSN (Online) : 2278-0181
- Publisher Name : IJERT
- License:
This work is licensed under a Creative Commons Attribution 4.0 International License
RBD and FE Analysis Approach for Stability Analysis of a Three Wheeled Equipment
Bharath Umesh Gadiyar1, Manjunath Soppin2, Praveen Ahuja3
Technical Lead1, Technical Manager2, Global Program Manager3, MCOE, HCL Technologies, Bangalore, India
AbstractStability is one of the key parameters which the designer has to keep in mind while designing a Three wheeled equipment. Stability depends on the center of gravity (COG) location of the equipment. When the COG of Three wheeled equipment shifts beyond the safe limit due to external load, the equipment gets destabilized and begins to tip over. The testing of the equipment for Stability can be simulated using Rigid Body Dynamics (RBD) or FE (Finite Element) analysis approach to study the tip over load. The Stability simulation is performed using RBD approach and results are compared with test values and later validated using FE analysis approach. Both RBD & FE analysis approach show good correlation with test results. However, it is observed that the RBD approach is better than the FE approach in terms of simulation speed and cost. This paper demonstrates the advantages of the RBD approach over FE analysis approach for the Stability simulation of a Three wheeled equipment.
Keywords Stability, Stability simulation, center of gravity (COG), Rigid Body Dynamics (RBD), FE analysis and Three wheeled equipment.
-
INTRODUCTION
There are various types of Three wheeled and Four wheeled equipment available in the market. Designing a Three wheeled equipment for stability is more challenging than a Four wheeled equipment as the center of gravity (COG) of the equipment shifts continuously. This paper describes the study on stability analysis of a Three wheeled equipment with the help of both physical test and simulation results. While designing any Three wheeled equipment, there is a reference tip over force against which the manufacturer tests their equipment. For the equipment mentioned in this paper, the minimum tip over force for the equipment to pass and get approval from the concerned authorities is set at 178N (40lbf).
consistent, versatile approach to find the stability of the equipment.
-
PROBLEM SOLUTION
To tackle the above described problem, various approaches are considered such as analytical calculation, physical test, simulation etc. This paper describes 2 approaches – actual physical test approach and virtual simulation-based approach. Physical test approach involves finding the force at which the equipment de-stabilizes using a force gauge. In this method, the force is gradually applied on the foot board until one of the rear wheel lifts off the ground. Simulation-based approach involves carrying out a virtual simulation using RBD analysis and/or FE analysis approach tool and the tip over force is noted down by monitoring the contact reaction force between the wheels and the floor.
-
Test Setup
The physical test procedure is carried out as per the standard prescribed by the concerned authorities for respective types of Three wheeled equipment. The physical test is performed as described below:
-
The equipment is placed in the manufacturers recommended use position with all wheels on a flat horizontal plane. With no external weight on the equipment, the foot board is placed in the lowest use position. The test is performed with the wheels positioned to most onerous position. (Fig 1) which is decided upon after averaging several test data.
-
-
-
-
PROBLEM DEFINITION
During design process, one of the crucial aspects to be considered is the stability of the Three wheeled equipment. As the magnitude and location of load application on the front most part (referred henceforth as foot board) varies, the COG of the equipment shifts continuously and beyond a safe point, begins to tip over. Few other factors that influences the COG are the swiveling front wheel, the friction between the foot board and the foot. These factors are not known during the design stage. Therefore, there is a need to find a more
Fig 1: Position of the front wheel (top view)
-
A force of 40 lbf (178 N) is applied vertically downward on the foot board using a probe. If the equipment does not tip over for the applied load of 40 lbf, then the equipment is considered to be safe and stable.
-
If the probe slides off at a particular spot on the foot board, it is considered a pass at that particular spot on the equipment.
-
Simulation based approach
It is observed that physical testing of the actual model is inconsistent as there are a lot of permutations and combinations for the force to be applied on the foot board. Hence it is recommended to shift to a more consistent and versatile method for stability i.e. to a virtual simulation method which in turn saves the cost of prototyping multiple designs and overall turnaround time.
Simulation is performed by using RBD analysis approach and validated using FE analysis approach. To simulate the physical test conditions, below shown steps are followed:
-
The material for all the parts is assigned as per the actual model to precisely capture the mass & COG of the equipment.
-
The front wheel is tilted to the most onerous position (Fig 1).
-
To provide front suspension effect, spring inside the front fork is modelled to replicate the physical model.
-
During force application on foot board, contact reaction force at all 3 wheels of the equipment which makes contact with ground is monitored.
-
Floor is considered as rigid and fixed.
-
-
RBD analysis approach:
The following procedure is followed for RBD analysis.
-
MSC-Adams used for the pre-processing, solving and post-processing.
-
Meshless approach, hence no modelling/meshing of parts.
-
Material is assigned and wheels are tilted as per the physical test (Fig 2, images are blurred intentionally).
-
Fixed joint connection is given between parts to realize the operating condition i.e. open condition of the equipment (Fig 3, images are blurred intentionally).
-
Revolute joint connection is defined between wheels and axles and between fork and foot board (Fig 4, images are blurred intentionally).
-
Force is applied on the foot board and the contact reaction force between the wheels of the equipment and the floor are cautiously monitored.
Fig 2: MSC Adams model of the equipment
Fig 3:Fixed Joint Connections Fig 4:Revolute Joints
-
-
FE analysis approach:
The following procedure is followed for FE analysis.
-
Hypermesh is used for pre-processing and LS-Dyna is used for solving and post-processing.
-
All the plastic parts are modelled as solid (tetrahedron) and all metal frames are modelled as shell mesh.
-
All the parts are assigned with MATL20 (Rigid material) i.e. the material does not undergo any deformation under load application.
-
Wheels are tilted as per the physical test (Fig 5, images are blurred intentionally).
-
*CONSTRAINED_RIGID_BODIES is used to define contacts between the parts (Fig 6, images are blurred intentionally).
-
Revolute joints are defined between wheel and axle and between fork and foot board (Fig 7, images are blurred intentionally).
-
Force is applied and the contact reaction force between the wheels of the equipment and the floor are cautiously montored.
-
Fig 5: LS Dyna model of the equipment
Fig 6:Constrained Rigid bodies Fig 7:Revolute Joints
-
Results
-
Results from RBD approach (MSC Adams)
The physical test and simulation using MSC-Adams were performed and the Force at which the equipment tips over were noted down.
It is observed in the physical test, that the force value at which the equipment de-stabilizes is 225N. This is the value that is seen on the force gauge at the moment when the rear wheel appears to lift off the ground. The MSC Adams results show that the force value at which the equipment de- stabilizes is 213N. The contact reaction force between the rear wheel and the floor is continuously monitored. The contact reaction force reduces as the input force increases. At the point where the contact reaction force becomes zero, it can be noted that the input force at this point is the force value to de-stabilize the equipment (Fig 8 and 10, images are blurred intentionally).
Fig 8: Destabilized state of the equipment (MSC Adams)
-
Results validation
The results obtained by simulation-based approach are never 100% accurate as there are certain limitations and assumptions. In order to ensure that the results obtained by simulation approach is close to the actual results, the same simulation is performed using LS-Dyna as an alternate tool.
From the results of LS-Dyna simulation, an input force value of 214N is observed at the moment when zero contact reaction force is observed between the wheel and the floor (Fig 9 & 11, images are blurred intentionally).
Fig 9: Destabilized state of the equipment (LS Dyna)
Fig 10: Input force and Contact force vs Time plot (For MSC Adams Model)
Fig 11: Input force and Contact force vs Time plot (For LS- Dyna Model)
-
Results summary
A brief summary of results is shown below in Table 1 and Chart 1.
Table 1: Summary of results
Chart 1: Physical test vs MSC Adams vs LS Dyna
-
-
CONCLUSION
The tip over force for physical test was found to be over the minimum value of 178N. Hence it can be concluded that the equipment is safe and passing the standards set by the concerned authorities. Simulation results show a correlation of +/- 20N with the physical test.
Efforts taken for RBD analysis approach (MSC-Adams) is significantly low compared to FE-analysis approach (LS- Dyna). This is because, RBD analysis is a meshless approach and significant amount of time is saved during meshing and solution activity. Brief summary is given in table 2 and chart 2.
Table 2: Overall simulation time taken for MSC Adams vs LS Dyna
The above table indicates that by using RBD analysis approach i.e. MSC Adams approach, around 65% of overall time is saved for each test simulation without compromising on the accuracy of results. Hence, MSC – Adams simulation approach is recommended for stability simulations to reduce the design lead time.
-
FUTURE SCOPE OF WORK
Due to the curved designed of the foot board, in physical test, it is observed that the force is applied vertically downward with the help of a force gauge with a cylindrical probe beginning from top edge of the foot board. The probe slides and stops at a location with a flatter surface on the foot board. In simulation approach, due to certain tool limitations, it is a challenge to simulate the movement of the probe.
Future scope of work is to explore the movement of the probe similar to the physical test setup i.e. the probe begins to slide from the top edge of the foot board, slides down and comes to a halt at the flatter base of the foot board before the force is applied.
Chart 2:MSC Adams vs LS Dyna
-
REFERENCES
-
Ls-dyna_971_manual, VOLUME I, May 2017, Version 971.
-
Adams Tutorial Kit for Mechanical Engineering Courses Second edition.
-
Standard no. 7.4.2 of Standard Consumer Safety Performance Specification given by the US CPSC.