
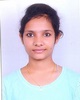
- Open Access
- [post-views]
- Authors : Janet Maria , B. P. Harish , Puneet Jain
- Paper ID : IJERTV9IS120065
- Volume & Issue : Volume 09, Issue 12 (December 2020)
- Published (First Online): 15-12-2020
- ISSN (Online) : 2278-0181
- Publisher Name : IJERT
- License:
This work is licensed under a Creative Commons Attribution 4.0 International License
Recuperation Efficiency and Stability Techniques for Battery Electric Vehicles
Janet Maria, B.P. Harish
Department of Electrical Engineering, University Visvesvaraya College of Engineering,
Bangalore University, Bengaluru.
Puneet Jain
ESP-AS12,
Robert Bosch Engineering and Business Solution, Bengaluru.
Abstract The conventional methodology of hydraulic braking in automobiles results in wastage of energy and exacerbated thermal profile due to the production of unwanted heat during braking. With the advent of electric vehicles, energy efficiency has assumed increased importance due to the constraints of battery capacity and the range of vehicle per charge. Hence, regenerative braking technique is widely used to achieve high energy efficiency. In regenerative mode, the motor acts as a generator and transforms the kinetic energy of the vehicle, upon braking, to electrical energy to restore the batteries or capacitors. To enhance the efficiency of regenerative braking in Battery Electric Vehicles (BEV) and achieve better stability of the vehicle, this work proposes 3 different techniques: Cooperative Regenerative Braking (CRB), Brake Force distribution (BFD) and Electronic Stability Program (ESP). This work details about improving the efficiency of Recuperation or Regenerative braking in BEV with the help of two electric-motors, mounted one on each axle, so that most of the kinetic energy generated while braking is gainfully utilized. It has been demonstrated that the braking efficiency is improved from 62.5% in existing methodologies to 84.66%. The successful implementation of these functional enhancements contribute to a new generation of electric vehicles on the road.
KeywordsRecuperation or Regenerative braking, Battery Electric Vehicle (BEV), E-motor, Cooperative Regenerative Braking (CRB), Brake Force distribution (BFD), Electronic Stability Program (ESP), Advanced Simulation and Control Engineering Tool (ASCET)
-
INTRODUCTION
In conventional vehicles, large part of the kinetic energy is converted, during friction braking, into heat and is emitted into the environment. The regenerative braking system uses an electric motor as a generator and converts much of the kinetic energy lost during braking and this energy is stored in the battery to be used during vehicle acceleration. But all the kinetic energy generated during deceleration cannot be converted using regenerative or recuperation braking [1]. The battery operated electric vehicles with rechargeable batteries have no gasoline engine. Battery electric vehicles store electricity on board with high-capacity battery packs, their battery power is used to run the electric motor and all on board electronics. The BEVs do not emit any harmful emissions and hence hazardous pollution caused by traditional gasoline- powered vehicles can be avoided [2]. A fully electrified regenerative braking system increases the driving range of the vehicle, reduces risk and benefits optimum use of a battery. The regenerative braking system has been improved by the advanced power electronic components such as ultra- capacitor, DC-DC converter (Buck-Boost) and flywheel [3, 4].
In the proposed work, two electric motors or e-motors are used on either axle and performed Brake Force Distribution (BFD) and Cooperative Regenerative Braking (CRB) to improve the regenerative braking efficiency. Further, Electronic stability Program (ESP) technique is deployed to improve the stability of the vehicle. All the three functionalities of Brake Force Distribution (BFD), Cooperative Regenerative Braking (CRB) and Electronic stability Program (ESP) are implemented as a software solution using Advanced Simulation and Control Engineering Tool (ASCET).
The rest of the paper is organized as follows: While Section II introduces brake force distribution, Section III presents cooperative regenerative braking. Section IV proposes electronic stability program. Section V presents results and discussion. Section VI concludes with directions to future work.
-
BRAKE FORCE DISTRIBUTION
When a driver applies the brake, the tyres carrying the least weight or load have more chance to skid and this can happen either by braking in the straight line or braking on cornering. To effectively brake an unevenly weighted car, braking power must be evenly distributed between the front and the rear wheels and is referred to as Brake Force Distribution. Brake force distribution plays a key role in a battery electric vehicle with two e-motors on each axle to improve the efficiency of regenerative braking. In the proposed work, while for brake circuit 1 regeneration process executes on the rear axle and hydraulic process executes on the front axle, for brake circuit 2 regeneration process executes on the front axle and hydraulic process executes on the rear axle.
To find Regeneration force at front and rear axle,
FFA= RegenFA * TotalRegen + FricFA ————-(1) where, FFA= Force at Front axle,
RegenFA= Regeneration force at Front axle, TotalRegen= Total regeneration,
FricFA= Friction at Front axle, The total force is given by,
FTotal= TotalRegen + FricFA + FricRA ————-(2) where, FricRA= Friction at Rear axle
FFA= BFDFA * FTotal ————-(3)
where, BFDFA is the part of total brake force which acts at the front axle for any brake force distribution function.
Substituting Eq. (1) and Eq. (2) in Eq. (3),
RegenFA * TotalRegen + FricFA= BFDFA (TotalRegen + FricFA + FricRA)
RegenFA= [BFDFA (TotalRegen + FricFA + FricRA) – FricFA] / TotalRegen
= [(BFDFA * TotalRegen) / TotalRegen] + [(BFDFA* FricFA) / TotalRegen] + [(BFDFA * FricRA) / TotalRegen ] – [FricFA / TotalRegen]
= BFDFA + (FricFA * BFDFA – FricFA + BFDFA *
FricRA) / TotalRegen ————- (4)
The sum of the BFD of the front axle and rear axle is unity i.e., the brake force should be distributed completely.
BFDFA + BFDRA= ————- (5)
Substituting Eq. (5) in Eq. (4),
RegenFA= BFDFA + [FricFA(1 – BFDRA) – FricFA +
BFDFAFricRA] / TotalRegen
= BFDFA + [BFDFAFricRA – BFDRAFricFA] / TotalRegen RegenRA= TotalRegen – RegenFA ————- (6)
To find brake force distribution at the front and the rear axle, radius (R) of the wheel and brake factor (Cp) has to be considered.
Force at front and rear axle w.r.t radius and brake factor
FFA= 2p * CpFA / RFA ————–(7)
FRA=2p * CpRA / RRA ————– (8)
FTotal= FFA* FRA
FTotal= 2p * [(CpFA / RFA) + (CpRA / RRA)] ————- (9)
Substituting Eq. (7) and Eq. (9) in Eq. (3)
2p * (CpFA / RFA) = BFDFA * 2p * [(CpFA / RFA) + (CpRA / RRA)]
BFDFA= (CpFA / RFA) / [ (CpFA / RFA) + (CpRA / RRA)]
BFDFA= (CpFA * RRA) / [( CpFA * RRA) + ( CpRA * RFA)]
———— (10)
Similarly BFD at rear axle
BFDRA= (CpRA * RFA) / [( CpRA * RFA) + ( CpFA * RRA)]
————- (11)
The mathematical analysis is carried out to achieve brake force distribution in order to vary the amount of force applied to each axle.
Fig.1: Functional diagram of braking system in Battery Electric Vehicle.
-
COOPERATIVE REGENERATIVE BRAKING Cooperative Regenerative Braking (CRB) is a process in
which both hydraulic and regenerative braking are carried out for highest regeneration for energy efficiency with constant brake pedal position and to improve the efficiency of the braking system. Fig.1 shows the functional diagram of braking system in a battery electric vehicle [5]. The cooperative regenerative braking comprise of the following funcions:
-
Brake torque blending
The brake demand raised by the driver is realized with both regenerative brake and/or hydraulic brake.
-
Pedal force blending
The driver should not feel at the brake pedal whether the brake system operation is performed as a hydraulic braking, a regenerative braking or a combined braking.
-
Brake fluid volume blending
In contrast to hydraulic braking, the shifted volume should not lead to a pressure build up in the brake calipers during regenerative braking.
The Cooperative Regenerative Braking operation have been programmed in ASCET for the following operating conditions:
-
Pure regenerative braking: The function at brake circuit 1 involves the brake request from the driver determined using a pedal travel sensor. Upon brake request, the CRB system is programmed to let the outlet valve of the rear axle to open and the inlet valve of the front axle to close. This results in a shift of brake fluid volume to low pressure accumulator and the desired regenerative brake torque is generated in response to driver brake request.
-
Combined regenerative and hydraulic braking: If there rises an additional brake request which cannot be achieved by regenerative braking alone, hydraulic braking is triggered, during which the inlet valve of the rear axle closes and the inlet valve of the front axle opens. The additional brake fluid volume gets shifted directly to front axle calipers and builds up hydraulic brake torque.
-
Blending from hydraulic to regenerative braking: In the presence of combined regenerative and hydraulic braking, maximum regenerative brake torque is increased by opening of inlet valve of rear axle by use of a computer controlled system mode referred to as dynamic position control. This action reduces pressure in the front axle by shifting brake fluid volume through the inlet valve of the rear axle to a low pressure accumulator. This increases the requested regenerative brake torque.
-
Leaving Jump-in area: The jump-in is the time taken by the brake rod to reach the booster body and jump-in area is the distance between the brake rod and booster body. Leaving the jump-in area leads to opening of the front axle inlet valve and closure of rear axle inlet valve and the pump shifts brake fluid volume to brake circuit or front axle brake caliper to reach the pressure corresponding to the actual pedal travel. Pressure control shifts rear axle volume to low pressure accumulator by use of inlet valve during further application pedal.
-
Returning to Jump-in area: Releasing the brake pedal necessitates shifting of volume of brake fluid to brake circuit or front axle brake caliper to reach the pressure value corresponding to actual pedal travel. Returning to the jump-in
area allows to decrease the pressure of brake fluid by use of the rear axle inlet valve and increase of regenerative brake.
-
Combined regenerative and hydraulic braking with low generator potential: If generator potential is not high enough to cover the rear axle portion of the driver brake request, additional hydraulic brake torque has to be built up at the rear axle. Combined regenerative and hydraulic braking is performed. The outlet valve of rear axle is closed and build- up of pressure at rear axle is achieved by controlled opening of inlet valve of rear axle by use of dynamic programming control mode. This shifts additional brake fluid volume directly to front and rear axle calipers. If this volume is not sufficient, the pump shifts additional volume out of the low pressure accumulator. If the rear axle is pressurized, regenerative torque is not going to increase anymore.
-
The process of CRB proposed in this work helps to provide highest regeneration with constant brake pedal position which is equal to pedal feel.
-
-
ELECTRONIC STABILITY PROGRAM Electronic Stability Program (ESP) is a technology used to
improve the stability of the vehicle by uncovering and diminishing dropping of road grip of the vehicle. ESP performs the function of Anti-lock Braking System and Traction control System i.e., during sudden braking when the vehicle leads to skidding, ESP operates by intercepting wheels from locking. When there is varying road surface, say slippery road, there might be chances of slipping of the vehicle at which the ESP operates by preventing the wheels of the vehicle from spinning thus controlling the traction of the wheels of the vehicle.
The ESP modulation provides the detailed functioning of the ESP, under various operating conditions, and is described below:
-
Normal braking: During normal braking, the driver presses the brake pedal which allows the hydraulic pressure from the master cylinder to pass through the inlet valve to the wheel hub as inlet valves and system pressure control valves by default are open, outlet valves and high pressure switch valves by default are close and thus forcing the wheels to stop.
-
Building of Pressure: Lets consider a scenario when the car has to take a right turn. Then by building a pressure on the front left wheel, the driver can easily turn the car without sliding. The inlet valve of front left wheel closes to build a pressure in the front wheel.
-
Decreasing of Pressure: Right before a wheel locks up, it will experience a rapid deceleration. The ESP controller understands that such a rapid deceleration is impossible, so it reduces the pressure to that brake until it sees an acceleration. When pressure has to be decreased, the respective wheel outlet valve is opened and the pressure is stored in the accumulator.
-
Full pressure decrease: When brake is released the pressure is decreased completely and sent back to the master cylinder through pump with the help of DC motor.
-
Active Braking: It uses a collection of vehicle sensors that monitors the presence of vehicles ahead and around the vehicle. It also has the ability to detect any situation where theres an impending collision with another vehicle. During active braking, Switchover valve also called
System pressure Control Valve closes and High pressure Switch Valve (HSV) opens. The pressure flows through it and pumps with the help of motor, and pulls pressure and pushes to the inlet valve of the respective wheel.
These ESP modulation schemes contribute to safe driving, under any circumstances, with enhanced stability. The ultimate effects are shorter braking distances and greater traction along with enhanced stability and higher levels of steering response.
-
-
RESULTS AND DISCUSSION
With the help of CRB and BFD techniques, the regeneration force has been increased from 4292 N to 5192 N which in turn improved the deceleration of the vehicle from 2.1 g to
2.54 g with a constant mass of the vehicle 2040 kg. Hence these techniques helped to upgrade braking efficiency from 62.5 % to 84.66 %.
Deceleration= Force (-ve)/ mass
=5192/2040
=2.54 g
BFD and ESP techniques. Efficiency graphs of different sources of regenerative braking with a deceleration of 2.54 g with respect to applied driver brake request and the distribution of regeneration and hydraulic force among each axle. The applied brake force is 5192 N which is determined by actual pedal displacement in mm. Of this total brake force, 4897 N force is achieved by the regeneration force and the rest is achieved by the hydraulic braking by the simulation of BFD and CRB.
Fig.2: Efficiency curves of different sources of regenerative braking (2.54 g)
Fig. 3: Current Strategy for front axle or rear axle: Maximum regeneration is zero
The results of various tests performed are shown in Fig.3 to Fig.7, under the following scenarios of system violations:
-
Current Strategy at front axle or rear axle: Fig 3 shows a set of simulation graphs when there is a failure either in the front axle or rear axle i.e., when regeneration brakng force is zero. In the event, complete driver request brake force is achieved by the hydraulic braking with the implementation of CRB.
-
Changed strategy at front axle: Fig. 4 shows the set of simulation graphs in the event of a failure in front axle i.e., maximum regeneration at the front axle is zero. The driver request is achieved by the regeneration brake force at the rear axle and the hydraulic force at the front axle with the implementation of CRB and BFD.
-
Changed strategy at rear axle: Fig. 5 shows the simulation graph in the event of a failure in the rear axle i.e., maximum regeneration at the rear axle is zero. The driver request is achieved by the regeneration brake force at the front axle and the hydraulic force at the rear axle with the implementation of CRB and BFD.
Fig. 4: Changed strategy at front axle: maximum regeneration at the front axle is zero.
Fig. 5: Changed strategy at rear axle: Maximum regeneration at rear axle is zero.
-
Stability violation at the front axle: Fig. 6 shows a set of simulation graphs in the event of a stability violation at the front axle i.e., the ABS stability index of the front left wheel and the front right wheel is zero. From the graph, it is seen that when there is stability violation in the front axle, it equally affects the stability at the rear axle too making the ABS stability index at the front left wheel and the rear right wheel zero. The stability violation is alerted to the driver.
-
Stability violation at the rear axle: Fig. 7 shows the set of simulation graphs in the event of a stability violation at rear axle i.e., the ABS stability index of the rear left wheel and the rear right wheel is zero. From the graph, it is observed that when there is stability violation in the rear axle it equally affects the stability at the front axle making the ABS stability index of the front left wheel and the front right wheel zero and the violation is alerted to the driver.
Fig. 6: Stability violation at the front axle
Fig. 7: Stability violation at the rear axle
The graphs Fig. 2 to Fig. 7 provide an insight on all issues related to the efficiency of regeneration braking and stability of the battery electric vehicle and the implications on other parameters in the event of various types of failures in the BEV system.
-
-
CONCLUSIONS AND FUTURE WORK
In the proposed work, Brake Force Distribution (BFD) and Cooperative Regenerative Braking (CRB) are implemented to
improve the regenerative braking efficiency of a battery electric vehicle. Further, the Electronic Stability Program (ESP) technique is deployed to improve the stability of the vehicle. All the three functionalities of Brake Force Distribution (BFD), Cooperative Regenerative Braking (CRB) and Electronic stability Program (ESP) are successfully implemented as a software solution using Advanced Simulation and Control Engineering Tool.
The results show that the proposed Brake Force Distribution technique computes the ratio at which the force has to be divided among the front and rear axle, with two e-motors, mounted one on each axle. It is demonstrated through simulations that the BFD improves the braking efficiency from 62.5% to 84.66 % and deceleration from 2.1g to 2.54 g. In Cooperative Regenerative Braking (CRB), both the hydraulic and the regenerative braking are performed to achieve the complete driver braking request. The Electronic stability Program (ESP) is demonstrated, through simulations, to perform the functions of Antilock Brake System and Traction Control System. The simulations results demonstrate the improvement in the stability of the system to meet the requirements of safety of the battery electric vehicle during motion. Hence, all the proposed solutions of BFD, ESP and CRB strategies are feasible and their effectiveness for Battery
Electric Vehicles is demonstrated to improve efficiency and stability of the vehicle. The successful implementation of these functional enhancements contribute to a new generation of electric vehicles on the road.
The brake force distribution can be further upgraded in order to improve the braking efficiency to nearly 100% by improving the deceleration contribution of regeneration braking to its theoretical maximum i.e., 3g.
REFERENCES
-
Electrek. Micah Toll, Regenerative braking: how it works and is it worth it in small EVs? Apr. 24th 2018.
Available at: https://electrek.co/2018/04/24/regenerative-braking-how- it-works/
-
Evgo. Types of electric vehicles: BEV, PHEV and HEV
Available at: https://www.evgo.com/why-evs/types-of-electric- vehicles/
-
Gaurav A. Chandak and A. A. Bhole, A review on regenerative braking in electric vehicle, Publisher: IEEE, Year: 2017.
-
Zhang Chuanwei, Bai Zhifeng, Cao Binggang and Li Jingcheng, Study on regenerative braking of electric vehicle, Publisher: IEEE, Year: 2004.
-
Brakes, Brake Control and Driver Assistance Systems Konrad Reif Ed. Function, Regulation and Components Bosch Professional Automotive Information by Konrad Reif Ed.