
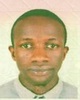
- Open Access
- Authors : Kamugisha Derrick Kansime
- Paper ID : IJERTV11IS120162
- Volume & Issue : Volume 11, Issue 12 (December 2022)
- Published (First Online): 21-02-2023
- ISSN (Online) : 2278-0181
- Publisher Name : IJERT
- License:
This work is licensed under a Creative Commons Attribution 4.0 International License
Reducing Waste in the production process through implementation of Lean Six Sigma Methodology: A Case of an Eyeglasses Manufacturing Company
Kamugisha Derrick Kansime,
School of Management, University of International Business and Economics, 100029, Beijing China
Abstract:- Lean six sigma is gaining prominence as a methodology for quality improvement in manufacturing industries since it helps to reduce quality defects and eliminate waste from the production process. This article presents a case study that demonstrates how Lean Six Sigma can be used to minimize waste during the production of eyeglasses. This article discusses in great detail the selection of the project and the use of the Lean Six Sigma methodology. It also shows how different tools and techniques from the Six Sigma methodology have been used to get big financial benefits, one of which is an increase in the company's profits.
Using Pareto analysis, overall equipment efficiency measurement, and cause-and-effect analysis, the production process was examined. The results showed that dust and other factors related to the work environment, such as contaminants linked to the liquid particles on the surface of the eyeglass frame products, which settle on the surface after drying and cause quality defects, are the main causes of electrophoresis quality defects.
Throughout the electrophoresis process, less time was required for drying in the oven, which is attributable to the implementation of 5S and lean six sigma tools. The failure rate dropped to 7.16%, a decrease of 3.34%, and the improvement rate was 31.82% as a result of the considerable decline in the number of electrophoresis quality faults. The electrophoresis failure rate exceeded the goal for improvements, which resulted in a significant reduction in rework waste and had a positive impact on order delivery schedules.
Keywords: Waste Elimination, Quality, Improvement, Lean Six Sigma methodology
1.0. INTRODUCTION
The global economy's competitive market environment has driven industrial enterprises to seek out workable solutions that will provide them a competitive advantage over their immediate competitors. As a result, many industries are looking for contemporary management approaches that will enable them to improve the quality of their products and/or services, streamline their manufacturing processes, drive down costs, increase financial performance, and, most significantly, enhance client satisfaction. This has been striven for using lean manufacturing techniques, six-sigma techniques, and their combination of strategies in management and manufacturing processes. Lean manufacturing techniques focus on eliminating waste, while Six Sigma methodologies focus on process control and variability reduction using statistical process control tools. [1]
The most well-known process improvement strategies for delivering bottom-line advantages are Lean and Six Sigma [2]. The term "Lean Six Sigma" was first used to describe a coupled strategy to enhance the performance of the business in the late 1990s and early 2000s [3]. A company's in-process variability will be reduced [4], lead time will be reduced, and company profit will be increased [5] if the lean six sigma framework is implemented properly.
Lean, also known as lean manufacturing, is a set of principles adopted by industrial organizations to enhance manufacturing and customer satisfaction while reducing waste [6]. The goal of excellence in Lean is to ensure that the ideal process occurs step by step as continuous improvements and preventative measures on the root causes of quality control issues and waste in industry [7]. Mechanical failures, setup and changeovers, idle and minor stoppages, lower speed operation, and rework costs are all examples of operational losses that can be reduced using lean techniques [8].
Waiting, defects, overproduction, and stockpiling are some of the waste problems that many companies face in their manufacturing lines [9]. Waste problems cost the company a lot of money, which includes lost revenue. As a result, increasing production line efficiency is the key to increasing profit [10].
To address problems with uncertain root causes and uncertain solutions, the Six Sigma methodology employs a structured DMAIC (Define-Measure-Analyze-Improve-Control) approach [11]. The DMAIC structure is similar to the traditional PlanDoCheck Act (PDCA) cycle, but Six Sigma specifies which quality management methods should be used at each step [12]. Implementing Six Sigma, which uses particular, ambitious targets, can increase the capacity for significant improvement, reduce process variability, and increase employees participation in improvement efforts and dedication to quality [13]. Six Sigma combines the performance of the business, criteria for measuring it, and project metrics into a quantifiable management system that managers may use to achieve strategic and operational goals [14]. When a company's operations are linked to its scorecard or key performance indicators, they bring in a lot of money [15].
Six Sigma provides a framework for process improvement as a statistical and non-statistical toolkit integrated within the DMAIC method [16]. It's a technique that's widely used in production and logistics management, but it has only lately been adopted by other discrete industrial companies [17]. As demand for products escalates, maintaining quality and dependable performance has become a priority for manufacturing businesses in order to obtain client satisfaction. To keep up with market competition, businesses must identify, monitor, evaluate, enhance, and regulate their present production systems. For continual productivity and quality improvements, several methodologies, approaches, and technologies are used [18].
Although downtime and inconsistencies are unavoidable during the production of any product, the primary purpose of process control or process capability analysis in any company is to explore the causes of downtime during the product's manufacturing process [19]. This enables manufacturing companies to track and measure the capability of their processes [20].
The combination of the two tools (Lean and Six Sigma), known as Lean Six Sigma (LSS), enables an organization to accomplish zero defects and quick delivery at minimal cost, as well as produce an optimal outcome that would not be possible if either technique were used alone [21]. When the Lean Six Sigma model was created, it demonstrated how Six Sigma can be used to improve process effectiveness first, and then lean to improve overall efficiency. It is preferable to use both at the same time to realize the concept of integration [22]. To fully implement lean and Six Sigma, organizations must use a comprehensive improvement process in which lean and Six Sigma work in tandem.
As a result of the pandemic crisis, manufacturing emphasis has shifted toward cost reduction through drastic measures such as factory closures, amalgamations, and perhaps even quality reduction [23], rather than refocusing on manufacturing re-engineering with a tilt toward Lean systems of production, waste elimination, and quality enforcement at all different phases [24]. Prior to the 1980s, production systems faced the additional challenge of low productivity due to a lack of work standardization. It was found that most of the old manufacturing processes did not add much value, which usually made the production cycle longer [25].
Several studies on the application of lean six sigma by various authors have been published, and they are not confined tothe textile manufacturing industry. In a study by Fu-Kwun Wang and Kao-Shan Chen [26], lean six sigma methodology was used in the service sector as a strategy to improve banking services. Furthermore, Soti et al. [27], Costa et al. [28], and Nabhani et al. [29] reported on the implementation of Lean Six Sigma (LSS) approaches in the food industry for improving productivity and performance.
Although there has been little research on the application of lean six sigma in the textile manufacturing industry, this study proposes that lean six sigma be used as an alternative approach to reducing waste in the textile industry. As a result, the lean six- sigma approach allows businesses to assess their current state and make improvement decisions based on situation analysis [30]. The study findings address the existing gaps in the literature by demonstrating the how, when, why, and how Lean Six Sigma may be applied to reduce waste in the manufacture of eyeglasses. In this article, the researcher step-by-step discuss how to utilize the DMAIC methodology to eliminate waste during the production of eyeglasses. The identity of the company, however, cannot be disclosed in the paper because of a non-disclosure agreement between the author and the company. With the main goal of minimizing quality defects in terms of manufacturing wastes and improving the efficiency of the production process, this study is designed to examine the contributions of lean six sigma to the production process.
2.0. METHODOLOGY
A case study methodology was used in this study. This method demonstrates how lean six sigma is used to evaluate an eyeglasses manufacturing company's current production process based on productivity and manufacturing wastes. With the DMAIC approach, these two methods were be used in the study. The case study technique was chosen because it allows researchers to investigate the production chain's multifaceted and crucial operations [31, 32]. Another benefit of this method is that it allows for direct observations, data collection in a situational setting, and comparison so that the generated data can be accepted [33]. The information that was gathered was based on how well the machines work (uptime, downtime, and cycle time) and how the materials move through each step of the manufacturing process.
-
Define Procedure
The operations involved in the production process were identified at the "define" step. To visualize the outcomes of the identification, the researcher will use the Value Stream Mapping (VSM) method. Machine (MC), manpower (MP), cycle time (CT), and available time are among the data required for the VSM approach (AT). The use of the VSM approach resulted into the determination of the entire manufacturing process time across the value stream. Value stream mapping is a lean manufacturing tool for analyzing and planning the flow of materials and information needed to deliver products to customers [34]. It can also help with significant waste reduction during the manufacturing process.
-
Measure Procedure
The "measure" stage is concerned with the "define" stage's follow-up. At this point, the process's performance is assessed. The process performance was used to assess overall performance in order to meet production targets. Initially, the lean function was used in this study to identify waste using the questionnaire [35].
The purposive sampling method was used for data collection. The next step was to use critical-to-quality specifications to identify the major waste. The critical-to-quality specifications was chosen using a Pareto diagram [36]. The Defect Per-Million Opportunities (DPMO) method [37] was then be used to calculate the sigma value.
-
Analyze Procedure
The lean six-sigma integration process was used to identify and analyze the causes of waste. Value Stream Analysis Tools (VALSAT) will be used in the study to calculate and determine the appropriate tools based on measurement [38]. The fault tree analysis approach was used to identify the sources of waste. At this step, the fault tree analysis will serve as a visual representation of the issues and circumstances that led to the waste. Quantitative and qualitative assessments was undertaken based on the fault tree analysis.
-
Improvement Procedure
In order to find solutions to the major problem of manufacturing waste linked to high setup time and changeover of manufacturing orders, the implementation of single-minute exchange of die (SMED) and 5S techniques were proposed and carried out.
In order to find a solution to the major problem of downtime as manufacturing waste linked to high setup times and changeovers of manufacturing orders, the implementation of 5S techniques was proposed and carried out [39].
-
Control Procedure
The "control" stage is the final stage of the DMAIC methodology. This study used the Standard Operational Procedures [40] of the chosen company to do control based on the available solutions.
-
Results
Large eyeglass factories primarily produce, develop, create, and market metal and plastic eyeglass components. The majority of the materials are exported, going to places like Southeast Asia, Japan, Australia, Europe, and the United States. To prevent the electroplating layer from breaking off or being damaged by the environment and human perspiration, the electrophoresis procedure must cover 30% of the metal glasses frame. In addition, it can lessen skin damage brought on by the discharge of nickel metal from the electroplating layer.
For quite a long time, electrophoresis process quality problems in factories have been numerous, and the product failure rate has occasionally reached 20% or higher. This has caused significant rework waste and impacted order delivery schedules. Regarding the factors that may be influencing the quality of the electrophoresis process, the researcher presumes that the environment of the manufacturing workshop plays an important role; other researchers attribute it to the different seasons and weather patterns; while still others believe there are technical difficulties within the electrophoresis procedure itself.
-
Define stage.
In order to identify the underlying cause of the quality issues spurred on by electrophoresis, the researcher primarily used the production flow chart (as illustrated in Figure 1) during the entire project. The quality defects of electrophoresis are primarily found to be associated with dust and other contaminants associated with the liquid particles on the surface of the eyeglass frame products, which precipitate on the surface after drying to generate quality defects.
Electroplating frame
Hang up
Ultrasound degreasing
Electric discharge
Electrolytic passivation
Electric glue
Pure water ultrasound
Activation
Inspecting
/verifying
-
Measure Stage
Dehydration
Hang down
Blow dry
Bake it
Figure 1. Flow chart of electrophoresis production
To identify significant quality defects and confirm the veracity of electrophoresis quality defect data. There are only two criteria for determining the quality of an electrophoresis: qualified and unqualified, making it a qualitative challenge. Only the finished product is inspected during the entire electrophoresis process; there is no in-process inspection. Therefore, the quality inspector's efficiency will have a direct impact on the data regarding the electrophoresis rate of failure. To evaluate the work capacity of quality inspectors, the researcher utilized Measurement System Analysis (MSA). After the researcher put the data into MINITAB to analyse it, Table 3 shows the results.
Table 1: MSA analysis results of electrophoresis quality inspectors
Quality inspectors
The quality inspectors own comparison
Comparison between quality inspectors and standardisation
All quality inspectors are compared to standards
Number of quality inspections
Matching number
Percentage
Number of quality inspections
Matching number
Percentage
Number of quality inspections
Matching number
Percent age
Employee A
50
38
76%
50
26
52%
50
18
36%
Employee B
50
43
86%
50
34
68%
50
24
48%
Employee C
50
37
74%
50
33
66%
50
21
42%
Employee D
50
37
74%
50
30
60%
50
20
40%
The information in Table 3 demonstrates that the four quality inspectors' operational standards clearly weren't met, which has a significant impact on the reliability of the quality inspection data. The researcher suggested that senior members of the quality control department be asked to organize an on-site training for the electrophoresis quality inspection operation. The goal was to help the four quality inspectors understand product qualification standards better, increase the system Kappa value of the quality inspection team, and reduce the chance of contamination.
The operational skills of the four quality inspectors got better after training, but to different degrees, and they can now do the work of quality inspection. The researcher modified the data collection form in order to more thoroughly and objectively assess the quality inspector's inspection data. Furthermore, the researcher used a Pareto chart to identify the primary quality faults in electrophoresis (see Figure 2 below). Figure 2 demonstrates that the three low-quality defects of line wool, particles, and watermarks account for 81.43% of all defects.
100.00%
90.00%
80.00%
70.00%
60.00%
50.00%
40.00%
30.00%
20.00%
10.00%
0.00%
Defective fraction Cummulative Percentage
Figure 2. Plato of electrophoretic quality defects
-
Analysis stage
After evaluating the primary electrophoresis quality faults, the researcher brainstormed with the workers on the front lines of the production line. The researcher then used fishbone diagrams (Cause and Effect Diagram and C&E Matrix) to identify potential causes of the issue, as shown in Figures 3, 4, and 5 below.
Measure
Machine
People
Wool clothes with soft nap
Outsider Dandruff
Visual ability
Clothing dust
Short hair
Inspection standards for electric adhesive
Baking filtration pot
Shoe dust
Foreign personnel dust
Quality inspector proficiency level
Filter pump cotton core
Line thread hair loss
Surface dust of electric glue washing cylinder
Air dust
Site environment 5S strength
Dyeing waiting time
Material
Method
Figure 3: Line-haired fishbone diagram
Measure
Machine
People
Visual ability
Surface cleanliness of the mounting tool
Clothing dust
Inspection standards for electro adhesive
Quality inspector proficiency level
Shoes dust
Outsider Dandruff
Dyeing maintenance
Baking dye filter
Equipment contact corrosion
Foreign personnel dust
Diatomaceous earth falls
Electro glue washing cylinder surface dust
Particulate matter
Air dust
Field environment 5S strength
Dyeing waiting time
Cleanliness of electric glue washing cylinder
Materials
Ring
Method
Figure 4: Fishbone diagram of particulate matter
Table 2: Causal matrix of electrophoresis quality defects
Process Name
Electro glue
Customer needs
Total
2
Output
Quality
bubble
scratch
Print
Colour
Wrinkled skin
3
Input
importance
10
6
5
4
1
2
Steps
Process
1
Receiver
2
Material substrate quality
1 10
3 13
5 25
9 36
1 1
1 2
92
3
Surface cloth
3 30
1 6
1 5
1 4
1 1
1 2
48
4
Surface imprinting
1 10
1 6
7 35
9 36
7 7
1 2
96
5
Cleanliness of the rack
9 90
1 6
1 5
1 4
1 1
1 2
108
6
Electro glue operation skills
1 10
3 13
5 25
1 4
1 1
3 6
64
7
Degreasing time / temperature
1 10
5 30
1 5
1 4
5 5
1 2
56
8
Electrolysis time cycle/ temperature
1 10
5 30
3 15
1 4
5 5
1 2
66
9
Activation time
1 10
3 13
1 5
1 4
3 3
1 2
42
10
Cleanliness of the rubber cylinder
9 90
3 13
1 5
1 4
1 1
1 2
120
11
Glue cylinder parameters
9 90
7 42
1 5
3 12
1 1
3 6
156
12
Electrolysis Time Temperature
1 10
1 6
1 5
1 4
1 1
5 10
36
13
Bake time temperature
1 10
5 30
1 5
1 4
3 3
1 2
54
14
Oven cleanliness
9 90
1 6
1 5
1 4
1 1
1 2
108
15
Oven performance
5 50
3 30
1 5
1 4
1 1
80
16
Air cleanliness
9 90
1 6
1 5
1 4
1 1
1 2
108
17
Proficiency of employees
1 10
1 6
7 35
1 4
1 1
1 2
58
18
Inspection standards
9 90
9 54
7 35
1 4
5 5
5 10
198
Total
710
318
225
140
39
58
1490
The researcher reached the conclusion that the unqualified electrophoresis outcomes are primarily caused by quality control problems generated by contaminants stuck to the surface of the eyeglass frame after evaluating the fishbone diagram and causal matrix diagram. In order to streamline data, the researcher referred to threading wool and particles together as impurities. The major impurity components are thread hair or granular dust, and the watermark is produced by the high temperature and short
heating time during drying following electrophoresis. Due to these two factors, the researcher chose to develop methods for lowering dust contaminants in the atmosphere and creating suitable drying conditions.
-
Improvement stage
The researcher implemented 5S and standard operating procedures in accordance with the findings from the analysis stage to carry out a number of improvement measures on the electrophoresis workshop, such as maintaining and improving electrophoresis equipment, optimizing the production process for electrophoresis, and filtering air supply and discharge in the electrophoresis workshop. The electrophoresis production line layout has been modified, and the U-shaped process layout has been set to reduce the amount of time needed to wait for drying in the oven after the electrophoresis process is complete, as shown in Figures 5 and
6 below. The system, on-site work environment, and microgravity environment have all undergone extensive necessary adjustments.
Figure 5. Electrophoresis workshop Figure 6. Electrophoresis workshop (Before improvement) (After improvement)
At this stage, the inspection information of the electrophoresis products the researcher observed on the job site was a surprise. The unqualified electrophoresis data occasionally increased to 20%. It was less than a month until the project's conclusion at this point in time. The frequency of watermarks and other significant problems had greatly decreased, and impurities continued to be the primary source of quality defects, according to an ongoing study on the quality issues associated with electrophoresis performed locally. After investigation and analysis, the researcher concluded that human clothing is the "main cause."
The researcher then hypothesized that there should be guidelines for the control of staff clothing at this precise moment for the clean room spraying operation. So, the researcher searched the pertinent data, and it turned out that staff members brought in 80% of the dust and pollutants in the clean room, proving that our assumption was accurate! The researcher also made the prompt decision that the staff in the electrophoresis workshop should change their attire and standardize the entrance and exit processes. After two weeks of several checks, the number of problems with the quality of electrophoresis has dropped by a lot, and the failure rate is now only 7.79%.
-
Control stage
During the review phase in April, when compared to the project baseline of 10.5%, the electrophoresis failure rate in April was 7.16%, a drop of 3.34%, and the improvement rate was 31.82%. The failure rate for electrophoresis has surpassed the goal for improvement. A number of standard documents, including electrophoresis workshop environmental maintenance specifications, electrophoresis equipment maintenance specifications, electrophoresis workshop air duct system maintenance specifications, electrophoresis workshop personnel access specifications, and others, have been developed in order to integrate and optimize the results. In addition, routine training plans for staff have been developed. These plans include MSA testing and training for new product inspection workers, induction training for electrophoresis operators, and others. The electrophoresis failure rate was consistently kept within the target value after three consecutive months of monitoring, as illustrated in Figure 7 below.
electrophoresis rate
Target
Tomb line
12.00%
10.00%
8.00%
6.00%
4.00%
2.00%
0.00%
Month(s)
01-Apr
02-Apr 03-Apr 04-Apr 05-Apr 06-Apr 07-Apr 08-Apr 09-Apr 10-Apr 11-Apr 12-Apr 13-Apr 14-Apr 15-Apr 16-Apr 17-Apr 18-Apr 19-Apr 20-Apr 21-Apr 22-Apr 23-Apr 24-Apr 25-Apr 26-Apr 27-Apr 28-Apr 29-Apr
30-Apr
Figure 7: Trend chart of unqualified rate of electrophoresis quality in April
4.0. CONCLUSION
Lean Six Sigma implementation cannot succeed without the steadfast backing of the company's top executives as well as their commitment to ongoing improvement. A project's success is influenced by three factors: concept (30%), performance (40%), and serendipity (30%). These elements are also necessary for the accomplishment of electrophoresis quality improvement efforts.
Despite not being a thorough study, the electrophoresis quality improvement project in this paper is a typical Lean Six Sigma improvement effort with significant historical importance for organizations. This study set a precedent for future research on Lean Six Sigma quality improvement efforts at the organization. Lean Six Sigma is an obvious notion that everyone on the electrophoresis production line, from the manager to the staff at all levels, has hands-on experience with, which shows the spirit of teamwork and complete participation in improvement.
Data availability statement
The author confirms that the data supporting this study's findings are available within this article.
Conflicting interests
The author declares that he doesnt have any conflicting interests in this article.
Ethics approval and consent to participate
Ethical approval from the university was sought before the study began. The researcher addressed ethical concerns and issues as per standard practice. Because research entails encounter with individuals or sensitive documents, it was vital to remember to behave accordingly during these interactions. During data collection, confidentiality and anonymity were protected by safely keeping the information received from participants away from anyone who was not involved in the research project.
REFERENCES
[1] Nafiz Afsan, Md. Abdul Aziz and A.R.M. Harunur Rashid. (2020) A Concise Literature Review on Comparison between Lean Manufacturing and Six Sigma with Their Separate and Combined Applications to a Few Specific Industrial Sectors. http://www.ieomsociety.org/imeom/210.pdf [2] Kumar, M., Antony, J., Singh, R.K., Tiwari, M.K. and Perry, D. (2006) Implementing the Lean Sigma Framework in an Indian SME: A Case Study.Production Planning and Control, 17, 407-423. https://doi.org/10.1080/09537280500483350
[3] Thomas, A.J., Francis, M., Fisher, R. and Byard, P. (2016) Implementing Lean Six Sigma to Overcome the Production Challenges in an Aerospace Company. Production Planning & Control, 27, 591-603. https://doi.org/10.1080/09537287.2016.1165300 [4] Breyfogle Iii, F.W. (2003) Implementing Six Sigma: Smarter Solutions Using Statistical Methods. John Wiley & Sons, New York. [5] Albliwi, S., Antony, J., Abdul Halim Lim, S. and van der Wiele,T. (2014) Critical Failure Factors of Lean Six Sigma: A Systematic Literature Review. International Journal of Quality & Reliability Management, 31, 1012-1030. https://doi.org/10.1108/IJQRM-09-2013-0147 [6] Ahmed. S, Manaf, N.F., & Islam, R. (2018). Measuring Lean Six Sigma and Quality Performance for Health care Organization. International Journal of Quality and Service Science, 10(3), 267-278. https://doi.org/10.1108/IJQSS-09- 2017-0076 [7] Emiliani, M.L. (1998), "Lean behaviors", Management Decision, Vol. 36 No. 9, pp. 615-631. https://doi.org/10.1108/00251749810239504 [8] Dadashnejad, A.-A. and Valmohammadi, C. (2018), "Investigating the effect of value stream mapping on operational losses: a case study", Journal of Engineering, Design and Technology, Vol. 16 No. 3, pp. 478-500. https://doi.org/10.1108/JEDT-11-2017-0123 [9] H. B. Ismail and Z. B. M. Yusof, "Understanding Defects During the Construction Process," Advanced Science Letters, vol. 24, pp. 4227-4231, 2018. [10] A. Karim and M. Islam, "Manufacturing practices and performance," International Journal of Quality & Reliability Management, vol. 28, pp. 43-61,2011. https://doi.org/10.1108/02656711111097544.
[11] Zu, X.; Fredendall, Douglas, T.J. The evolving theory of quality management: The role of Six Sigma. J.Oper. Manag. 2008, 26, 630- 650 https://doi.org/10.1016/j.jom.2008.02.001 [12] Linderman, K.; Schroeder, R.G.; Zaheer, S.; Choo, A.S. Six Sigma: A goal-theoretic perspective. J. Oper. Manag. 2002, 21, 193 203.https://doi.org/10.1016/S0272-6963(02)00087-6 [13] Linderman, K.; Schroeder, R.G.; Choo, A.S. Six Sigma (2005): The role of goals in improvement teams. J. Oper. Manag. 24, 779790 https://doi.org/10.1016/j.jom.2005.08.005 [14] Pande, P.; Neuman, R.P.; Cavanagh, R. The Six Sigma Way Team Fieldbook: An Implementation Guide for Process Improvement Teams, 1st ed.; McGraw-Hill Education: New York, NY, USA, 2002; ISBN 978-0-07-137314-2. [15] Heavey, C. and Murphy, E. (2012), "Integrating the Balanced Scorecard with Six Sigma", The TQM Journal, Vol. 24 No. 2, pp. 108-122 https://doi.org/10.1108/17542731211215062 [16] Chowdhury, S. The Power of Design for Six Sigma; Kaplan Business: Sydney, Australia, 2003. [17] Mwacharo, F.K. (2013). Challenges of Lean Management – Investigating the challenges and developing a recommendation for implementing Lean management techniques. Bachelor. HAMK University of Applied Sciences. [18] Gupta, V., Jain, R., Meena, M.L., & Dangayachi, G.S. (2018). Six-Sigma Application in Tire Manufacturing Company: A Case Study. Journal of Industrial Engineering International, 14, 511-520. https://doi.org/10.1007/s40092- 017-0234-6 [19] Pearn, W.L., & Chen, K.S. (1999). Making decisions in assessing process capability index C-pk. Quality and Reliability Engineering International, 15(4), 321-326. https://doi.org/10.1002/(SICI)1099-1638(199907/08)15:43.0.CO;2-5 [20] Wu, C.C, Kuo, H.L, & Chen, K.S. (2004). Implementing process capability indices for a complete product. The International Journal of Advanced Manufacturing Technology, 24(11), 891-898. https://doi.org/10.1007/s00170-003-1812-x [21] Salah S, Rahim A, Carretero JA (2010). The integration of six sigma and lean management. International Journal of Lean Six Sigma;1(3):249-274 [22] Crawford, R. (2004). Ammunition enterprise excellence ready for tomorrow? USA Armor School Research Library. David, L. (2010). Project Riskand Risk Management
[23] Saidul Huq, K.M. (2018). Impact of Lean Manufacturing on Process Industries. Master of Business Administration Dissertation. Bucking Institute of Technology, Sweden. [24] Anthony, P. (2018). Lean in a Lean Economy. Manufacturing Today [online]: http://www.manufacturing-today.com/sections/columns/2001-lean-in- a-lean-economy [25] Sayidmia, M.D. (2016). An approach to reduce Manufacturing waste and Improve the Process Cycle Efficiency of a footware Industry by using Lean Six-Sigma Model. Master of Science in Management of Technology Dissertation. Institute of Appropriate Technology. Bangladesh University of Engineering and Technology. [26] Fu-Kwun Wang, Kao-Shan Chen. (2010). Applying Lean Six Sigma and TRIZ methodology in banking services. Total Quality Management & Business Excellence, 301-315. J. Taylor et al., (n.d.). Proposed Progression of Lean Six Sigma. The Journal of Technology Studies, 1-8A. Soti, R. Shankar, and O. P. Kaushal (2012), "Six Sigma with innovation tool kit of TRIZ," International Journal of Business Innovation and Research, vol. 6, pp. 220- 237. https://doi.org/10.1504/IJBIR.2012.045638. [27] A. Soti, R. Shankar, and O. P. Kaushal, "Six Sigma with innovation tool kit of TRIZ," International Journal of Business Innovation and Research, vol.6, pp. 220- 237, 2012. https://doi.org/10.1504/IJBIR.2012.045638.
[28] L. B. M. Costa, M. Godinho Filho, L. D. Fredendall, and G. M. Devós Ganga (2021), "Lean six sigma in the food industry: Construct development and measurement validation," International Journal of Production Economics, vol. 231, p. 107843. https://doi.org/10.1016/j.ijpe.2020.107843. [29] F. Nabhani, S. Bala, G. Evans, and A. Shokri (2017), "Review of implementing lean six sigma to reduce environmental wastes of internal supply chains in food industry," in 15th international conference on manufacturing research, ICMR, pp. 327-332. [30] Erbiyik, H., & Saru, M. (2015). Six Sigma implementations in supply chain: an application for an automotive subsidiary industry in Bursa in Turkey.Procedia – Social and Behavioral Sciences, 195, 2556-2565. https://doi.org/10.1016/j.sbspro.2015.06.447
[31] Ingason, H.P., & Jónsdóttir, E.R. (2017). The house of competence of the quality manager. Cogent Business & Management, 4(1),1345050. https://doi.org/10.1080/23311975.2017.1345050 [32] Vinodh, S., Kumar, S.V., & Vimal, K.E.K. (2014). Implementing Lean Sigma in an Indian Rotary Switches Manufacturing Organization. Production Planning & Control, 25(4), 288-302. https://doi.org/10.1080/09537287.2012.684726 [33] Sunder M.V., Ganesh, L.S., & Marathe, R.R. (2019). Lean Six Sigma in Consumer Banking: An Empirical Inquiry. International Journal of Quality & Reliability Management. https://doi.org/10.1108/IJQRM-01-2019-0012 [34] Rother, M., & Shook, J. (2003). Learning to see: value-stream mapping to create value. [35] D. Black, "Partial justification of the Borda count," Public Choice, vol. 28, pp. 1-15, 1976. https://doi.org/10.1007/BF01718454 [36] A. R. Singh, V. Swarnakar, and A. K. Tiwari (2020), "Evaluating the effect of critical failure factors associated with sustainable Lean Six Sigma framework implementation in healthcare organization," International Journal of Quality & Reliability Management, vol. ahead-of-print. https://doi.org/10.1108/IJQRM07-2020-0243. [37] A. Coskun, W. P. Oosterhuis, M. Serteser, and I. Unsal, "Sigma metric or defects per million opportunities (DPMO): the performance of clinical laboratories should be evaluated by the Sigma metrics at decimal level with DPMOs," Clinical Chemistry and Laboratory Medicine (CCLM), vol. 54, pp. e217-e219, 2016. https://doi.org/10.1515/cclm-2015-1219. [38] P. Hines and N. Rich, "The seven value stream mapping tools," International Journal of Operations & Production Management, vol. 17, pp. 46-64, 1997. https://doi.org/10.1108/01443579710157989. [39] D. Cavallucci (2017), TRIZThe Theory of Inventive Problem Solving: Current Research and Trends in French Academic Institutions vol. 1: Springer. https://doi.org/10.1007/978-3-319-56593-4. [40] Purnomo, D. H., & Lukman, M. (2020). Reduce Waste using Integration of Lean Six Sigma and TRIZ Method: A Case Study in Wood Industry. Jurnal Teknik Industri, 21(2), 139-152. https://doi.org/10.22219/JTIUMM.Vol21.No2.19-152