
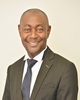
- Open Access
- Authors : Onjefu Leonard. A , Abubakar Idris , Amana Ocholi , Onjefu S. A, Kiangi Geoffrey
- Paper ID : IJERTV10IS110061
- Volume & Issue : Volume 10, Issue 11 (November 2021)
- Published (First Online): 18-11-2021
- ISSN (Online) : 2278-0181
- Publisher Name : IJERT
- License:
This work is licensed under a Creative Commons Attribution 4.0 International License
Reliability-Based Analysis For Failure Modes Of Mansard Roof Truss According To Euro Code 3
Onjefu Leonard. A1,3*, Abubakar Idris1, Amana Ocholi1, Onjefu S.A,2 Kiangi Geoffrey3 1Department of Civil Engineering, Ahmadu Bello University, Zaria, Kaduna State, Nigeria 2Department of Natural and Applied Sciences, Namibia University of Science and Technology 3Department of Construction and Civil Engineering, Triumphant College, Windhoek, Namibia
Abstract:-This paper shows the results of the safety assessment of Mansard steel roof truss using the First Order Reliability Methods. Four failure modes were considered in the studies: compression, bending, tension, as well as, combined compression and bending failure modes;
From the results obtained from the First Order Reliability Method, the safety index values range between 0.076 to 11.90 for the members, while the values for the joints range from 0.677 to 1.89. A careful study of the results shows that the safety index values decreased as the load ratio increased and the safety index values at a particular load ratio are generally higher for the members than the joints. These results point to the fact that failure will be initialized at joint before progression to other members.
Keywords: Euro code, Failure mode, FORM, Reliability, Safety index, Stochastic model, Truss
-
INTRODUCTION
Steel Trusses are normally designed to support imposed, wind and dead loads. Various types of steel trusses such as Mansard, Storage, Scissors, Fink, Howe, and others are opted for in designs. These trusses are selected based on design criteria before being constructed. These criteria include amongst others their usage, cost, Span – to – depth and so on [1].
Engineering design and analysis are based often on deterministic thinking, characterized in design calculations by the use of specified minimum material properties, specified load intensities and by prescribed procedures for computing stresses and displacements. This has led to uncertainties, and conversely the application of prescribed safety factors in the analysis and design [2].
Because of these uncertainties, "risk", the probability of structural failure from all possible causes, both from violation of predefined limit state and from other causes is unavoidable. Though, uncertainties and their importance on structural safety and performance can be analysed thoroughly only through the technique of probability [3]. Reliability-based design involves incorporating these uncertainties in current methods of design, thereby using probability methods to design at pre-defined safety levels [4]. [5] looked at the reliability of structure by means of different target safety levels and probability distribution functions. The results showed that high target safety index makes it difficult to determine the safety factors such that the same safety level can be reached for different structures.
In this work, a reliability-based analysis for failure modes of steel mansard roof trusses to Euro code 3 [6] was carried out. The proposed design procedure considers the design of the mansard roof truss using First Order Reliability Method (FORM) at target safety levels which the current Codes of Practice do not provide.
-
LIMIT STATE EQUATIONS
The top chord is subjected to compression and bending. The bottom chord, tie member and strut member are subjected to tension and compression.
-
Limit State Equation due to Compression
The failure mode due to compression is thus:
G (x) = permissible compression load applied compression load.
The design buckling resistance of a compression member should be taken as:
Nb,Rd=AFy (1)
Ym1
Where Nb, Rd is the permissible compression load, is the reduction factor, A, is the section area, Ym1 is partial factor and Fy is the yield strength.
For axial compression in members, the value of the appropriate non-dimensional slenderness should be
determined from the relevant buckling curve according to (Euro code 3).
= 1
+ 2 – 2 (2)
But,
= 0.5 [1 + ( – 0.2) + -2] [ EC 3, 1993]
Where is value to determine the reduction factor, is imperfection factor, is non-dimensional slenderness. Therefore,
= 1 (3) 0.5[1 + ( – 0.2) – -2] + [0.5(1 + ( – 0.2) + -2)2 – -2
[ EC 3, 1993]but, 1 = E/Fy = 93.9E (4)
E = 235/Fy
[ EC3, 1993]Where 1 is the slenderness value to determine the relative slenderness,
E is youngs modulus, Fy is the yield strength, is the Coefficient depending on yield strength From
= z/1A0.5 (5)
where A is the correction factor, z is the Slenderness ratio therefore, equation ( 5) after substitution becomes
= 1/ (6) 0.5[1+(z/1A0.50.2)+(z/1A0.5)2+(0.5(1+(z/1A0.50.2)+( z/1A0.5)-2)2 – z
zA0.5
From equation 1.
Nb,Rd = AFy (7)
0.5[1+(z/1A0.50.2)+(z/1A0.5)2+(0.5(1+(z/1A0.50.2)+( z/1A0.5)-2)2 – z
zA0.5
[ EC 3, 1993]Therefore,
G(x)=Nb,RdNsd (8)
Nsd=1.5xX(5)(1 + 0.9 x Alpha). (9)
Where Alpha is the ratio of dead to live load , X(5) is Imposed Loadings.
Therefore,
G(x) = AFy
0.5[1+(z/1A0.50.2)+(z/1A0.5)2+(0.5(1+(z/1A0.50.2)+( z/1A0.5)-2)2 – z
zA0.5 Ym1
– (1.5 x X(5)x(1 + 0.9 x Alpha)) (10)
[ EC 3, 1993]The design value of the compression force must satisfy:
Nsd 1.0 (11)
Nb, Rd
Where Nsd is the applied compression force, Nb, Rd is permissible compression force.
-
Limit State Equation for Bending
The failure mode due to bending is thus: G(x) permissible bending moment applied bending.
The design resistance for bending about one principal axis of a cross section is determine as follows:
Mc,Rd = WpFy (12)
Ym1
Where Mc, Rd is the permissible bending moment, Wp is the Section Modulus, Fy is the yield strength, Ym1 is the partial factor.
But,
Wp= Ix x (13)
Y
Where I xx is the moment of inertia, Y is the distance from the centroid axis to the top fibre.
But,
Y = d – Cx (14)
d is the depth of section, Cx is the centroid Therefore,
3 2
3 2
Ixx=tw(d-Tf)3/12+3(d-Tf)tw/2(Cx+Tf)2/12+BTf /2+BTf(Cx-Tf) (15)
3 2
3 2
Wp=tw(d-Tf)3/12+3(d-Tf)tw/2(Cx+Tf)2/12+BTf /2+BTf(Cx-Tf) /d-Cx (16)
3 2
3 2
Mc,Rd=(tw(d-Tf)3/12+3(d-Tf)tw/2(Cx+Tf)2+BTf /12+BTf(Cx-Tf/2) )Fy)/(d-Cx)Ym1 (17)
Where tw is the thickness of the web, Tf is the thickness of the flange, B is the width of the flange. The design moment for bending moment must satisfy
MEd 1.0 (18)
Mc, Rs
Where MEd is the design moment
MEd =1.5xX(5)xa(1+0.9Alpha)(L2a2)/2L (19)
Where,
3 2 2 2
3 2 2 2
a is the Support distance, L is the Span length, Alpha is the ratio of live to dead load The failure mode is thus,
G(x)=[tw(d-Tf)3/12+3(d-Tf)tw/2(Cx+Tf)2+BTf /12+BTf(Cx-Tf/2) )Fy]/(d-Cx)Ym1-[1.5xX(5)xa(1+0.9Alpha)(L a )/2L)] (20)
2. 3 Limit State Equation for Top chord
The limit state equation due to compression and bending is thus:
G(x)=Applied Compression + Applied bending < 1.0 (21) Permissible compression Permissible bending
Af(1.5xX(5)x (1+0.9Alpha) 0.5[1+(z/1A0.50.2)+(z/1A0.5)2+(0.5(1+(z/1A0.50.2)+( z/1A0.5)-2)2- z
zA0.5 Ym1
3
3
(1.5 x X(5) x a(1 + 0.9 Alpha) (L2 a2)/2L)/ tw(d-Tf)3/12+3(d-Tf)tw/2 – (Cx+Tf)2+BTf /12 + BTf(Cx-f/2)2)Fy/(d-Cx)Ym1 (22)
-
Limit State Equation for Bottom Chord
The limit state equation for bottom Chord is thus: G(x) = permissible tensile load Applied tensile load
The design resistance for tension is given as follows:
Nt,Rd=Afy (23)
Ym1
Where A is the area of the section, fy is the Design Strength, Ym1 is the Partial factor. The design value for tension force NEd must satisfy:
NEd 1.0 (24)
NE, Rd
Where NEd is the Applied tensile force.
NEd
=1.5xX(4)(1 + 0.9Alpha)
(25)
NE,Rd
=Afy Ym1
(26)
Therefore,
1.5 x X(4)x(1 + 0.9Alpha) 1.0 (27)
Afy/Ym1
G(X) = NERd – NEd
G(X) =AFy/m1 1.5 x X(4)(1+0.9ALPHA) (28)
-
Limit State Equation for Tie members
The limit state equation for tie member is thus: G(x) = permissible tensile load Applied tensile load The design resistance for tension is given as follows:
Nt,Rd=Afy/Ym1 (29)
Where A is the area of the section, fy is the Design Strength, Ym1 is the Partial factor The design value for the tension force NEd must satisfy
NEd 1.0 NE,Rd
Where NEd is the Applied tensile force, NERd is the Permissible tensile load.
NEd =1.5xX(4)(1+0.9Alpha) (30)
Nt,Rd = Afy/ Ym1
Therefore,
1.5 x X(4)x(1 + 0.9Alpha) 1.0 (31)
Afy/Ym1
G(X) = AFy/m1 (1.5 x X(4)(1+0.9ALPHA)) (32)
-
Limit State Equation for Strut members
The failure mode due to Strut members is thus
G (x) = permissible compression load applied compression load. The design buckling resistance of a Strut member should be taken as:
Nb,Rd=Afy (33)
Ym1
Where Nb, Rd is the permissible compression load, is the reduction factor, A is the section area, Fy is the yield strength, Ym1 is the partial factor.
For axial compression in members, the value of x the appropriate non-dimensional slenderness should be
determined
from the relevant buckling curve according to
= 1
+2-2 (34)
But,
=0.5[1+(- 0.2) + -2] (35)
where is the value to determine the reduction factor, is the imperfection factor, is the non-dimensional slenderness.
Therefore,
= 1 (36) 0.5[1 + ( – 0.2) – -2] + [0.5(1 + ( – 0.2) + -2)2 – -2
but, 1 = E/Fy = 93.9E (37)
E=235/Fy (38)
[ EC 3, 1993 ]Where 1 is the slenderness value to determine the relative slenderness, E is the youngs modulus, Fy is the yield strength, is the Coefficient depending on yield strength.
from, = z/1A0.5 (39)
Where A is the correction factor
= 1/ (40)
0.5[1+(z/1A0.50.2)+(z/1A0.5)2+(0.5(1+(z/1A0.50.2)+( z/1A0.5)-2)2- z
zA0.5
Nb,Rd = AFy (41)
0.5[1+(z/1A0.50.2)+(z/1A0.5)2+(0.5(1+(z/1A0.50.2)+( z/1A0.5)-2)2- z
zA0.5
therefore,
G(x)=Nb,RdNsd (42)
Nsd=1.5xX(5)(1+0.9xAlpha) (43)
Where Alpha is the ratio of dead to live load, X (5) is applied to load Therefore:
G(x) = AFy
0.5[1+(z/1A0.50.2)+(z/1A0.5)2+ (0.5(1+(z/1A0.50.2)+( z/1A0.5)-2)2- z
zA0.5 Ym1
(1.5xX(5)x(1+0.9xAlpha)) (44)
The design value of the compression force satisfies,
Nsd1.0 (45) Nb, Rd
Where Nsd is the applied compression force, Nb, Rd is the permissible compression force.
2.7. Limit state Equation for Connections
The limit state equation for the joints is thus:
G(X) = Pweld F (46)
Pweld = 0.9 x l x Ax fu/ 2 (47 )
mw
F = 1.5x X(5)a(1+0.9ALPHA)(L2-a2)/2L (48)
Where l length of the weld (mm), A is the Throat thickness (mm), fu is the Yield Strength (N/mm2), mw is the Partial Safety of factor.
Therefore, the limit state equation is given by:
G(X) = 0.9 x l x A x fu – 1.5 x X(5)a(1+0.9ALPHA)(L2-a2)/2L ( 49)
mw
Where, l Length of the weld (mm), A is the Throat thickness (mm), fu is the Yield Strength, ALPHA is the ratio of dead to live and; a is the Support distance; L is the Member length.
-
METHODOLOGY
-
First Order Reliability Procedure
The reliability function of a given surroundings is the probability that the system survives all the actions exerted upon it by the surroundings [7]. The reliability is defined as the systematic calculations and prediction of the probability of limit state violation [8]. Probabilistic design is concerned with the probability that a structure will realize the functions assigned to it. If R is the strength capacity and S the loading effect(s) of a structural system which are random variables, the key objective of the reliability index of any component is to confirm that R is at no time surpassed by S. in practice, R and S are typically functions of different basic variables [7]. To examine the effect of the variables on the performance of a structural system, there are five elementary steps required to arrive at a value for the reliability index .
The limit state equation is referred to as the performance or state function and expressed as:
g(xi) = g(x1,x2, xn) = R S (50)
where, xi for i=1, 2,n, represent the basic design variables. The limit state of the system can be expressed as:
g(xi) = 0 (51)
Graphically, the line g(xi) = 0 represents the failure surface while g(xi)> 0 represents the safe region and g(xi) < 0 corresponds to the failure region as depicted in Fig.1.
Adopting a reduced, normally distributed variable expression for each variate.
Xi = (xi – xi), i = 1,2,n (52)
xi
and in terms of these reduced variates, the limit state equation becomes:
g(sxiX`1+Xi,sx2X`2,+x2,,sxnX`n+xn)=0 (53)
where and S are the means and standard deviations of the design variables.
G (x) = 0
G (x) = 0
Y
G (x) < 0
G (x) < 0
1111111111111111
G (x)> 0
X
G (x)> 0
X
Fig.1: The most likely Failure Point [7]
Finding an expression of the distance from the failure surface to the origin of the reduced variate space: let the distance in question be D. the distance D, from a point Xi = (X1, X2, Xn) on the failure surface g(xi) = 0 to the origin xi space is also given as:
1 2 n
1 2 n
D = X2 + X2 ++ X2 ) (54)
in matrix form, D = (X X X )=
t
= (Xi X
t
= (Xi X
X
X
1 )½ (55)
X
X
1 2 n
2
X
X
n
The point on the failure surface (X*1, X*2, X *n), is minimized, having a distance to the origin may be determined by subjecting G(xi) = 0, by means of the Lagrange's multiplier and g(xi) is the limit state function. The minimum distance is obtained by introducing the gradient vector [7].
G1 = g , g, .. g (56)
X1 X2 Xn
In which,
g =g . X =xi g (57)
Xi Xi Xi Xi
Therefore, in vector form we have
X + G =0 (58)
(XtX)1/2
From which,
X = DG (59)
From equation (55)
D = [(DGt) ((DG)] 1/2 = D(GtG)1/2 (60)
=(GtG)1/2 (61)
Where Gt is the transpose of the gradient vector G. substituting equation (60) into equation (59) gives,
X = -GD (62)
(GtG)1/2
Multiplying both sides of the (62) by Gt, the transpose of the gradient vector matrix, we have
GtX = -GtGD (63)
( GtG)1/2 = -( GtG) 1/2 D
which implies
D=-GtX (64)
(GtG)1/2
The minimum distance from the origin describing the variable space to the line representing the failure surface equals and therefore equation (64) becomes
=-G*tX* (65)
(G*tG*)1/2
Where G* is the gradient vector at the most probable failure point (X1*, X2 *,Xn *). It is the value o which tells us of the safety of any given design under uncertainties in the decision variables.
In equation (65), where basic variables are assumed to be normally distributed and uncorrelated, Taylor's expansion of G(x) about the mean yield quite precise approximations of . Though, G(x) may contain non-normally distributed and frequently correlated variables, the accuracy of the estimates of be subject to heavily on the choice of the point of linearization. FORM procedures resolve this problem by introducing suitable transformations altering all variables into uncorrelated normal variables, subsequently linearizing the emergent non-linear function G(x) about a suitable point X*, selected through an optimization procedure, and hence a probability of failure is evaluated using standard normal integral.
-
Program Data Preparation
The mansard truss shown in Fig. 2 was designed following EC3. The means, standard deviations as well as the statistical distributions of the basic design variables were prepared as shown in Tables 1 to 5 by [7]
Fig. 2. Steel Mansard Truss
-
Parameters of Stochastic Model
The values of data used in the models are presented in Tables 1, 2,3,4 and 5.
Table 1: Parameters of Stochastic Model for Top Chord
S/N |
BASIC VARIABLES |
E(Xi) |
S(Xi) |
DISTRIBUTION |
COV |
1 |
Design strength Fy |
275N/mm2 |
13.75N/mm2 |
Normal |
0.05 |
2 |
Width of flange B |
190.5mm |
9.525mm |
Normal |
0.05 |
3 |
The thickness of flange Tf |
14.5mm |
0.725mm |
Normal |
0.05 |
4 |
The thickness of web t |
9.1mm |
0.455mm |
Normal |
0.05 |
5 |
Imposed load Qk |
1.5KN/m |
0.225KN/m |
Log-normal |
0.15 |
6 |
Depth of section d |
228.6mm |
11.43mm |
Normal |
0.05 |
7 |
Centriode Cx |
54.2mm |
2.71mm |
Normal |
0.05 |
8 |
Root radius r |
7.6mm |
2.28mm |
Log-normal |
0.3 |
Table 2: Parameters of Stochastic Model for Bottom Chord
S/N |
BASIC VARIABLES |
E(Xi) |
S(Xi) |
DISTRIBUTION |
COV |
1 |
Design strength Fy |
275N/mm2 |
13.75N/mm2 |
Normal |
0.05 |
2 |
Width of flange B |
190.5mm |
9.525mm |
Normal |
0.05 |
3 |
The thickness of flange Tf |
14.5mm |
0.725mm |
Normal |
0.05 |
4 |
The thickness of web tw |
9.1mm |
0.455mm |
Normal |
0.05 |
5 |
Live load Qk |
1.5KN/m |
0.45KN/m |
Log-normal |
0.15 |
6 |
Root radius r |
7.6mm |
0.456mm |
Log-normal |
0.3 |
7 |
Depth of section d |
228.6mm |
11.43mm |
Normal |
0.05 |
Table 3: Parameters of Stochastic Model for Tie Member
S/N |
BASIC VARIABLES |
E(Xi) |
S(Xi) |
DISTRIBUTION |
COV |
1 |
Design strength Fy |
275N/mm2 |
13.75N/mm2 |
Normal |
0.05 |
2 |
Member length l |
120mm |
6.0mm |
Normal |
0.05 |
3 |
Member thickness t |
8mm |
0.4mm |
Normal |
0.05 |
4 |
Live load Qk |
1.5KN/m |
0.225KN/m |
Log-normal |
0.15 |
Table 4: Parameters of Stochastic Model for Strut Members
S/N |
BASIC VARIABLES |
E(Xi) |
S(Xi) |
DISTRIBUTION |
COV |
1 |
Design strength Fy |
275N/mm2 |
13.75N/mm2 |
Normal |
0.05 |
2 |
Member length h |
120mm |
6mm |
Normal |
0.05 |
3 |
Member thickness t |
10mm |
0.5mm |
Normal |
0.05 |
4 |
Heel root radius r1 |
10mm |
0.5mm |
Log-Normal |
0.05 |
5 |
Toe radius r2 |
5mm |
1.5mm |
Log-normal |
0.3 |
6 |
Applied loading Qk |
1.5KN/m |
0.225KN/m |
Log-normal |
0.15 |
Table 5: Parameters of Stochastic Model for Connections
S/N |
BASIC VARIABLES |
E(Xi) |
S(Xi) |
DISTRIBUTION |
COV |
1 |
Design strength Fy |
275N/mm2 |
13.75N/mm2 |
Normal |
0.05 |
2 |
Length of weld L |
639mm |
31.95mm |
Normal |
0.05 |
3 |
The thickness of weld t |
56.6mm |
2.83mm |
Normal |
0.05 |
4 |
Imposed Load Qk |
1.5KN/m |
0.225KN/m |
Log-normal |
0.15 |
Table 6: Safety Index values, , and their corresponding probabilities of Failure, Pf, for Members Top Chord Members
0.130×10-8
Member |
Alpha 0.2 |
Alpha 0.4 |
Alpha 0.6 |
Alpha 0.8 |
Alpha 0.9 |
Alpha 1.0 |
||||||
Pf |
Pf |
Pf |
Pf |
Pf |
Pf |
|||||||
a-2 |
8.67 |
0.222×10-17 |
7.30 |
0.143×10-12 |
6.50 |
0.402×10-10 |
5.93 |
0.150×10-8 |
5.70 |
0.606×10-8 |
5.49 |
0.201×10-7 |
b-4 |
8.52 |
0.796×10-17 |
7.16 |
0.425×10-12 |
6.35 |
0.106×10-9 |
5.78 |
0.368×10-8 |
5.55 |
0.143×10-7 |
5.35 |
0.462×10-7 |
BOTTOM CHORD MEMBERS |
||||||||||||
m-1 |
10.0 |
0.713×10-23 |
5.96 |
3.56 |
0.185×10-3 |
1.85 |
0.320×10-1 |
1.15 |
0.125 |
0.524 |
0.300 |
|
m-3 |
9.63 |
0.293×10-21 |
5.58 |
0.124×10-7 |
3.18 |
0.744×10-3 |
1.47 |
0.711×10-1 |
0.766 |
0.222 |
0.138 |
0.445 |
TIE MEMBERS |
||||||||||||
1-2 |
10.70 |
0.497×10-26 |
6.84 |
0.395×10-11 |
4.53 |
0.294×10-5 |
2.88 |
0.199×10-2 |
2.19 |
0.142×10-1 |
1.52 |
0.554×10-1 |
3-4 |
10.07 |
0.350×10-23 |
6.17 |
0.345×10-9 |
3.85 |
0.585×10-4 |
2.19 |
0.140×10-1 |
1.52 |
0.644×10-1 |
0.908 |
0.181 |
STRUT MEMBERS |
||||||||||||
1-a |
9.42 |
0.237×10-20 |
5.49 |
0.197×10-7 |
3.11 |
0.945×10-3 |
1.41 |
0.793×10-1 |
0.764 |
0.222 |
0.076 |
0.470 |
2-3 |
10.70 |
0.497×10-26 |
6.89 |
0.282×10-11 |
4.55 |
0.274×10-5 |
2.87 |
0.204×10-2 |
2.25 |
0.142×10-1 |
1.56 |
0.597×10-1 |
4-5 |
11.90 |
0.639×10-32 |
8.35 |
0.342×10-16 |
6.06 |
0.701×10-9 |
4.41 |
0.529×10-5 |
3.73 |
0.956×10-4 |
3.11 |
0.945×10-3 |
Table 7: Safety Index values, , and their corresponding probabilities of Failure, Pf, for Joints
Joint |
Member |
Alpha=0.2 |
Alpha=0.4 |
Alpha=0.6 |
Alpha=0.8 |
Alpha=0.9 |
Alpha=1.0 |
||||||
Pf |
Pf |
Pf |
Pf |
Pf |
Pf |
||||||||
1 |
NM |
1.89 |
0.296×10-1 |
1.77 |
0.383×10-1 |
1.65 |
0.492×10-1 |
1.53 |
0.626×10-1 |
1.47 |
0.704×10-1 |
1.41 |
0.788×10-1 |
NP |
1.86 |
0.316×10-1 |
1.71 |
0.435×10-1 |
1.53 |
0.626×10-1 |
1.41 |
0.788×10-1 |
1.34 |
0.905×10-1 |
1.26 |
0.103 |
|
2 |
MN |
1.83 |
0.337×10-1 |
1.65 |
0.492×10-1 |
1.47 |
0.704×10-1 |
1.29 |
0.981×10-1 |
1.20 |
0.115 |
1.11 |
0.133 |
3 |
OP |
1.80 |
0.359×10-1 |
1.59 |
0.556×10-1 |
1.38 |
0.834×10-1 |
1.17 |
0.121 |
1.07 |
0.143 |
0.96 4 |
0.167 |
OR |
1.83 |
0.337×10-1 |
1.65 |
0.492×10-1 |
1.47 |
0.704×10-1 |
1.29 |
0.981×10-1 |
1.20 |
0.115 |
1.11 |
0.133 |
|
4 |
PO |
1.89 |
0.296×10-1 |
1.77 |
0.383×10-1 |
1.65 |
0.492×10-1 |
1.53 |
0.626×10-1 |
1.47 |
0.704×10-1 |
1.41 |
0.788×10-1 |
PN |
1.86 |
0.316×10-1 |
1.71 |
0.435×10-1 |
1.53 |
0.626×10-1 |
1.41 |
0.788×10-1 |
1.34 |
0.905×10-1 |
1.26 |
0.103 |
|
5 |
QR |
1.83 |
0.337×10-1 |
1.65 |
0.492×10-1 |
1.47 |
0.704×10-1 |
1.29 |
0.981×10-1 |
1.20 |
0.115 |
1.11 |
0.133 |
6 |
RQ |
1.86 |
0.316×10-1 |
1.71 |
0.435×10-1 |
1.53 |
0.626×10-1 |
1.41 |
0.788×10-1 |
1.34 |
0.905×10-1 |
1.26 |
0.103 |
RO |
1.89 |
0.296×10-1 |
1.77 |
0.383×10-1 |
1.65 |
0.492×10-1 |
1.53 |
0.626×10-1 |
1.47 |
0.704×10-1 |
1.41 |
0.788×10-1 |
4.2. Data from componential reliability analysis
Since the member forces are expressed in terms of the dead to live load ratio, the ratio was varied from 0.2 to 1.0 and necessary computation using FORM was carried out to determine the probability of failure ''Pf and the corresponding safety index, . This was done for the Top Chord members, Bottom Chord members, Web members, as well as the Joints. The results are tabulated in Tables 6 and 7. From Table 6 the beta values range 0.076 to 11.90 for the members, while the values for the joints in Table 7 range from 0.677 to 1.89. A careful study of the results shows that the values decreases as the load ratio increases and the values at a particular load ratio are generally higher for the members than the joints. These results point to the fact that failure will be initialized at joint before progression to other members.
A closer look at the results in Table 6 show that the safety levels ( values ) at all -levels, exhibit the following trend: The Strut members are the safest having the highest safety level, Tie members come next in succession; The Bottom Chord members are next with the Top chord following. Failure in the members will be in progression, starting with the members having the least safety level. It should be borne in mind that since it is statically determinate structures, failure of any member or joint denotes truss failure [8].
5.0 CONCLUSION AND RECOMMENDATIONS
The reliability-based design of Euro code 3 procedures for a Mansard roof truss system has been carried out with the aid of computer programs in the FORTRAN language. The FORM of analysis for the elements was carried using FORM5 [7].
From the results obtained for the First Order Reliability Method, the safety indices range between 0.076 to 11.90 for the members, while the values for the joints range from 0.677 to 1.89. Joint failure of a mansard roof truss designed by Euro code 3, will therefore be initiated before progressing to members under increased loading.
It is recommended that:
-
Mansard roof trusses should be designed at a lower value of rtio dead- to live loads.
-
the design of the joints in Mansard Steel roof trusses should be considered more seriously.
-
The reliability-based design needs to be carried out considering other wind speed in different Nations.
REFERENCES
-
V. J. Liew, " Analysis of Extendable IBS Steel Truss''. Departmental Seminar, Department of Civil Engineering, Universiti of Teknologi Malaysia, 2007.
-
T. Yiannis, and P. Manolis Robust and Efficient methods for Reliability-based structural optimization. Journal Institute of Structural Analysis and Seismic Research, National University Athens, 2000.
-
Faber, M.H Risk Assessment in Engineering, Principles, System Representation and Risk Criteria JCSS, ISBN 978-3-9093366-78-9: 2007.
-
G. Haig, and H. Milan, Reliability based calibration of Euro Codes considering a steel member. U.K. 2001.
-
R.M. Alpo, and T. Tomi, Reliability of Target Safety Level of Timber Structures, VTT Building and Transport, Espoo, Finland, 2002.
-
Eurocode 3: Design of steel structures- Part 1-1: General rules and rules for buildings. 2003.
-
I. Abubakar, and I.U Ahmed, Reliability Analysis of Steel Column Base Plate. Journal of Applied Science and Research vol.3, No.7, pp 189-194, 2007.
-
R.D. Melchers, Structural reliability analysis and prediction, Ellishorwood limited, Manchester, 1999.