
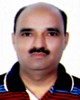
- Open Access
- Authors : Sanjeev Varshney , Neeraj Kumar
- Paper ID : IJERTV9IS110218
- Volume & Issue : Volume 09, Issue 11 (November 2020)
- Published (First Online): 07-12-2020
- ISSN (Online) : 2278-0181
- Publisher Name : IJERT
- License:
This work is licensed under a Creative Commons Attribution 4.0 International License
Reliability Based Design of Two Repairable Systems
Sanjeev Varshney1, Neeraj Kumar2
1. Asst. Prof. MED, Inderaprastha Engg. College, Ghaziabad (U.P), INDIA.
2 .Asst. Prof. MED, Indraprastha Engg. College, Ghaziabad (U.P), INDIA.
Abstract: In this paper we discuss the purpose of reliability engineering is to prevent the chance of failure. However, prevention of failure is almost physically and economically impossible. Any product designed and fabricated is bound to fail sooner or later. So, controlling the occurrence of failure is the aim of reliability design. If the product does not fail during the period it is supposed to operate, then it is called a reliable product and hence it has reliable design.
Systems are designed to realize the desired reliability by introducing redundancy at each element level. When put in operation the reliability changes as a function of time. However, in some cases, maintenance can be performed on the failed elements while remaining elements continue to function. This way the overall period for which the system remains functional, without coming to total failed state increases. Naturally reliability in such cases is dependent on the failure and repair rate of each element. For those systems, which are also having redundancy at each element level, but failed elements cannot be repaired, the overall functional time is less and corresponding reliability at different times is also less. In this paper the reliability of a two-parallel system with repairs has been evaluated.
INTRODUCTION:
Reliability is the probability that the product would perform its stipulated function satisfactorily for a specified period of time under envisaged environmental conditions with or without maintenance as the case may be what is stated in this definition if it is achieved, the product is called reliable.
TYPES OF FAILURES:
Before attempting to improve the reliability of products/system it is worthwhile to understand the types and causes of the failures. The products /system may have failures due to design or quality defects or may fail after giving service i.e. on attaining old age. Design failure may be caused if (1) the products have unworkable combination of parts , (2)the functional logic of the system does not correspond to the requirements, (3)environment in which the product is supposed to function is wrongly estimated and (4)the product is not qualified to function in the environment.
In the category of quality failures are those failures which occur due to the reasons of product not being made according to the drawing, using wrong fabrication technique, heat treatment, surface finish etc.; or the product might have been damaged in assembly, transportation, trial run etc. The old age failures those failures where the product has worked for certain period of time, but now it is not functioning. The reasons for this could be that old age has set in and the product is no longer capable of functioning or
some type of equilibrium, (i.e. thermal, chemical, hydraulic etc.) has reached which has made the product unworkable. The design failures could be avoided by making correct design and failures would get considerably reduced by enforcing proper quality control. The old age failure cannot be avoided; however, the age of the product can be increased or during the time the product is supposed to function, the occurrence of failures can be controlled.
REASONS OF FAILURE:
Products, parts, and components may fail from one or more causes.
1. Excessive stress: This may come from external causes, or from severity of environmental conditions or from internal reasons like internal power surge.
2. Mechanical stress: Continued vibrations may loosen the nuts, bolts, fittings etc.
3. Contaminations: Accumulations of dirt etc. may cause electric failure.
4. Evaporation: Filaments age because filament molecules evaporate.
5. Fatigue: Prolonged repetitive loading may cause fatigue fracture.
6. Friction: This commonly produces failure in belts, gears, and machinery in general.
7. Temperature variation: Repeated expansion and contraction would weaken the material.
8. Aging and wear out: This is not a primary cause, but it reflects prolonged exposure to other causes.
9. Sub-standard or defective parts: This due to poor quality control.
10. Operator or Maintenance induced error: This is also known as human error.
11. Corrosion: This is chemical change which weakens material.
12. Failure at the time of switching on: Some components have operating time and idle time. So, when these are switched on from idle state that time these have probability of failure like light bulbs.
CLASSIFICATION OF SEVERITY OF FAILURES:
(a)Catastrophic failures: In this category significant failures occur, that can result in injury, loss of life or major damage. (b)Critical failure: In this category complete system failure occurs, where the performance is not acceptable. (c)Marginal failure: System is degraded, with partial loss of performance.
(d) Negligible failure: Minor failure occurs, with no effect on acceptable system performance.
OCCURRENCE OF FAILURES:
(a)Frequent: If probability of failure is high i.e. P0.20, then the failures are quite frequent.
(b)Probable: If probability of failure is moderate i.e. 0.10P
<0.20, then the failures are quite probable.
(c)Occasional: If probability of failure is marginal i.e. 0.01 P< 0.10, then the failures are quite occasional.
(d) Remote: If probability of failure is very little i.e. 0.001 P< 0.010, then the failures are quite remote.
(e)Extremely unlikely: For very rare event, the probability of failures should be as low as given below i.e. P<0.001 Reliability evaluation criteria: The reliability of any product/system is measured in terms of the following criteria.
(A)Availability: This criterion is applicable for maintained systems. It is defined as the ratio of the cumulative working time to the total specified time. It has three sub divisions. (a)Instantaneous availability (Point availability): This is equal to the probability of system being available at any random time. In this case the systems may be required to function at any random time t, though the duty period in one go may be for very duration. Example: Computer processing the data of incoming and outgoing flights, door bells etc. (b)Average up time (Mission availability): In this case the system is expected to work for a comparatively longer time, when duty cycle comes. This is defined as the ratio of cumulative operating duty period to the total time in which the duty cycles come. However, the total time may be finite. Example: Telephone, Tracking radar system, Material testing facility etc.
Average up time A(T)= Working time/specified time T, where T is finite time.
(c) Steady state availability (Long duration availability): This is applicable to those systems which are expected to work continuously. This is again as the ratio of cumulative working period of the system to the total time in which the system is expected to be in working state. Mathematically total expected time is considered as infinite. In reality it would be large.
Steady state availability, A () = ( working time/ total time, T)
Examples: Thermal power plants, scanning radar system etc. (B)Probability of survival: The system designed according to this criterion should not reach a failed state during its mission time. This is applicable to both maintained and non- maintained systems. Example: if a space ehicle is expected to complete its mission, in time t, the system designed so that it does not reach failed state during this period. Another example: if the operation on a patient takes t1 time to complete, so during this period there should be continuous electric supply in the operation theatre. This means there should be no electricity failure.
(C) Mean time to system failure: This is used to evaluate the expected average working life of individual components, and systems, which may be maintained or non-maintained type. This has three sub-divisions as follows:
(a)MTBF (mean time b/w failures): This is the average life of a component. It is obtained by testing many identical items, like the life of an electric bulb, a bearing etc.
(b) MTTF (mean time to failure): It is the expected time to failure of a redundant non-maintained system. Example: a vehicle in outer space, inside having redundant viewing systems.
(c)MTTFF (Mean time to first failure): It is the expected time that the redundant system would take to reach the total failed state while on redundant failed items the maintenance is started immediately on their failure. Example: many thermal power units in a power station.
(d) Duration of a single down time: It is based on the time taken to restore a failed product/system to its working state. The duration of a single down time in such cases should always be less than a certain critical time. Example: the failed duration of ambulance transferring a critically ill patient should be less than a certain minimum period. Another example is of a scanning radar system. The longest duration of a single down time should be less than the time fastest missiles of the enemy take to reach the destination. For the reliable design of a product any one of the above criteria or more than one in any combination may be used depending on the type of service expected from the product.
MATHMATICAL ANALYSIS
Reliability of two element parallel system with two repair crew: As a result of repairs, the availability and reliability of the products increases. For the two-element parallel system with two repair crew, the availability and reliability matrices are as follows:
,
Both elements are assumed identical having failure rate and there are assumed two repair crew, each with repair rate µ. Assuming at time t=0, both elements are in working state, the governing equation for reliability can be written as follows:
The first two equations are
and
Taking the Laplacian of these equations and putting the initial conditions. We get
On solving for x0(s) and x1(s)
The term Where
so
Taking the inverse
The summation of and x0(t) and x1(t) is the reliability, so
This is reliability of two element parallel repairable system. Table: Reliability values at different t for (1) single element systemR1(t), (2) two element parallel systemR2(t), (3) two element stand by system R3(t) and (4) two element parallel system with repairs R4(t).
COMPARISON:
For comparison the reliability of (1) single element system R1(t), (2) two element parallel system R2(t), (3) two element stand by system R3(t) and (4) two element parallel system with repairs R4(t) have been calculated. The repair rates has been taken as 0.01 per hour and the value of µ is 1.0 per hour. The numerical values have been given in the table and the graph for the same as shown in the fig. The examination of table and fig reveal that reliability of two element parallel system with repairs is considerably more than all the three other systems.
t |
R1(t) |
R2(t) |
R3(t) |
R4(t) |
0 |
1 |
1 |
1 |
1 |
0.1 |
0.90483743 |
0.99094409 |
0.99532117 |
0.99323469 |
0.2 |
0.81873077 |
0.96714151 |
0.98247693 |
0.98029286 |
0.3 |
0.7408182 |
0.93282476 |
0.96306366 |
0.96581233 |
0.4 |
0.67032003 |
0.89131111 |
0.93844805 |
0.95107424 |
0.5 |
0.60653067 |
0.84518188 |
0.909796 |
0.93643063 |
0.6 |
0.54881161 |
0.79642904 |
0.87809858 |
0.92197639 |
0.7 |
0.49658531 |
0.74657363 |
0.84419503 |
0.90773529 |
0.8 |
0.44932896 |
0.69676137 |
0.80879213 |
0.89371139 |
0.9 |
0.40656966 |
0.64784044 |
0.77248235 |
0.87990338 |
1 |
0.36787945 |
0.60042363 |
0.7357589 |
0.86630851 |
2 |
0.1353353 |
0.25235495 |
0.40600589 |
0.74139231 |
3 |
0.04978707 |
0.09709539 |
0.19914848 |
0.63448817 |
4 |
0.01831564 |
0.03629582 |
0.09157821 |
0.54299897 |
5 |
0.00673795 |
0.0134305 |
0.035248 |
0.46470192 |
6 |
0.00247875 |
0.00495136 |
0.01735127 |
0.39769483 |
7 |
0.00091188 |
0.00182293 |
0.00729506 |
0.34034973 |
t |
R1(t) |
R2(t) |
R3(t) |
R4(t) |
0 |
1 |
1 |
1 |
1 |
0.1 |
0.90483743 |
0.99094409 |
0.99532117 |
0.99323469 |
0.2 |
0.81873077 |
0.96714151 |
0.98247693 |
0.98029286 |
0.3 |
0.7408182 |
0.93282476 |
0.96306366 |
0.96581233 |
0.4 |
0.67032003 |
0.89131111 |
0.93844805 |
0.95107424 |
0.5 |
0.60653067 |
0.84518188 |
0.909796 |
0.93643063 |
0.6 |
0.54881161 |
0.79642904 |
0.87809858 |
0.92197639 |
0.7 |
0.49658531 |
0.74657363 |
0.84419503 |
0.90773529 |
0.8 |
0.44932896 |
0.69676137 |
0.80879213 |
0.89371139 |
0.9 |
0.40656966 |
0.64784044 |
0.77248235 |
0.87990338 |
1 |
0.36787945 |
0.60042363 |
0.7357589 |
0.86630851 |
2 |
0.1353353 |
0.25235495 |
0.40600589 |
0.74139231 |
3 |
0.04978707 |
0.09709539 |
0.19914848 |
0.63448817 |
4 |
0.01831564 |
0.03629582 |
0.09157821 |
0.54299897 |
5 |
0.00673795 |
0.0134305 |
0.035248 |
0.46470192 |
6 |
0.00247875 |
0.00495136 |
0.01735127 |
0.39769483 /td> |
7 |
0.00091188 |
0.00182293 |
0.00729506 |
0.34034973 |
CONCLUSION:
The mathematical expression of reliability for two element parallel system with repairs has been developed. On comparison this is found to be more than single element system.
REFERENCES:
[1] Arora, J. S., 1989, Introduction to Optimum Design, McGraw-Hill, New York, NY. [2] Ayyub, B. M., and McCuen, R. H., 1997, Probability, Statistics, & Reliability for Engineers, CRC Press, New York, NY. [3] Choi, K. K., Yu, X., and Chang, K. H., 1996, A Mixed Design Approach for Probabilistic Structural Durability, Sixth AIAA/USAF/NASA/ISSMO Symposium on [4] Haftka, R. T., and Gurdal, Z., 1991, Elements of Structural Optimization, Klumer Academic Publications, Dordrecht, Netherlands. [5] Madsen, H. O., Krenk, S., and Lind, N. C., 1986, Methods of Structural Safety, Prentice-Hall, Englewood Cliffs, NJ. [6] Rubinstein, R. Y., 1981, Simulation and the Monte Carlo Method, John Wiley & Sons, New York, NY. [7] Tu, J., and Choi, K. K., 1997, A Performance Measure Approach in Reliability-Based Structural Optimization, Technical Report R97-02, Center for Computer-Aided Design, The University of Iowa, Iowa City, IA.