
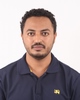
- Open Access
- Authors : Zeleke Natnael Bayu , Deng Sanpeng
- Paper ID : IJERTV10IS050295
- Volume & Issue : Volume 10, Issue 05 (May 2021)
- Published (First Online): 28-05-2021
- ISSN (Online) : 2278-0181
- Publisher Name : IJERT
- License:
This work is licensed under a Creative Commons Attribution 4.0 International License
Research and Development of A Training Platform for Assembly, Adjustment and Maintenance of Industrial Robot
Zeleke Natnael Bayu #1, Prof. Deng Sanpeng#2 Institute of Robotics and Intelligent Equipment. Tianjin University of Technology and Education Tianjin 300222, China
Abstract:- The establishment of a modern industrial robot is inseparable from the teaching and training equipment of industrial robots. At present, most of the training equipments on the markets are for the application and operation of industrial robots, there are only a few practical training equipments for installation, adjustment and maintenance of industrial robots, most of which do not meet the actual needs of students. The main objectives of this research is to carfully train students installation, adjustment and maintenance of industrial robot using BNRT-BRICS-RBT3 Robot Arm, it also focuses on the Design and development of a Graphical User Interface (GUI) to control the industrial robot, the approaches used in this analysis contains; utlizing a self developed computer software using VBNet. to control the robot arm. the robots forward Kinematics, and inverse kinematics, are established according to Denavit Hartenberg (D-H) method,also jacobian and The Cartesian coordinate system of the robot are realized implemented and tested.The research and development of this system can enrich and improve the educational equipment and teaching system of industrial robot, and it can be used as a special equipment for training high skilled talented personnel integration, installation, debugging and operation and maintenance of automatic production system.
Key Words: Industrial robot installation and maintenance, 6-DOF Robot, Educational and training equipment, industrial robot teaching system.
-
INTRODUCTION
In recent years, countries around the world are increasing the use of industrial robots, and they will need a large number of professionals to support them. Despite the establishment of research alliance between universities and the manufactruing industry, many of the research labs are scattered in many colleges, and the collaboration between teachers is not significant. the professional courses cannot effectively form a scientific research and education system, and the popularity of industrial robot education and teaching can be provided to more institutions. To guarantee effectiveness with robotic assembly, engineers need to adjust their parts, products and techniques to the distinct requirements of the industrial robot. These robots are also equipped with collaborative operation apparatus for transportation, detection, processing and storage.
In this thesis, the industrial robot training equipment was mainly studied in an effort to enrich and improve the teaching equipment and the education system in industrial robotics. The aim is to cultivate high-skilled personnel for integration, assembly, debugging, operation and maintenance of automatic production systems by implementing professional knowledge of mechanical design, theoretical mechanics, industrial robotics, virtual design and modeling.in this paper a study was conducted
for the industrial robot in the virtual environment with the aid of a computer software platform while analyzing its kinematics and dynamics. On the basis of these studies and according to task requirements, the following design was performed to the training equipment for assembly and maintenance of industrial robots.
Fig. 1 BNRT-BRICS-RBT3 Robot Arm
-
KINEMATICS ANALYSIS
The industrial robot platform used in this paper is a 6- DOF(Degree of Freedom) robotic arm manipulator BNRT- BRICS-RBT3 developed by Tianjin Bonus Robotics Technology Co. Ltd has been extensively used for reaserch and teching purosese. This type of robot has the advantages of simple structure, low cost, simple control, and a wide range of motion space. It is an ideal platform for designing control systems. It has a high degree of motion and flexibility, has a wide working space, and is an ideal manipulator for motion planning and programming system design. The forward kinematics of the robot is to analyze the position and state of the end effector relative to the reference coordinate system, so as to analyze and study the changes of the robot trajectory, given the geometric parameters and joint angles of the link.
The modeling of Kinematics of the industrial robot gives an advantage of the industrial automation process by making them fully-autonomous. Many systems can be used to calculate the direct kinematics. a common method used for creating coordinate system for the robot is D-H method, this technique the direct kinematics is determinate from
some parameters that need to be specified, depending upon each mechanism. Even so, it was selected to utilize the
C5
S
0 S5 0
0 C 0
C6
S
S6 0 0
C 0 0
homogeneous transformation matrix. This transformation
4A5= 5
5 5A6= 6 6
defines the position and orientation of the robot arm in space with respect to the base of the robot, however it does not tell us which setup of the arm is needed to accomplish this location [1]
0 1 0
0
0
0
0
0
n o a
0 0
1
1
0
0
p n
0 1
0 0
o a p
d6
1
1
Here in The Cartesian coordinate system of the robot
x1 x1 x1
x1 x 2 x 2 x 2 x 2
is established according to the D-H method, As shown in Figure 2:
T=T1*T2 ny1
nz1
oy1
oz1
ay1
az1
py1 * ny 2
pz1 nz 2
oy 2
oz 2
ay 2
az 2
py 2
pz 2
0
0
0
0
0
0
0
0
1
1
0 0 1
1 2 3 4 5
1 2 3 4 5
Where:- T1=0A1 A2 A3 and T2= A4 A5 A6
nx ox ax px
n
n
= y oy ay py
(1)
nz
0
0
oz az
0 0
pz
1
1
Fig. 2 Link coordinate Diagram of robot arm
Table 1 D-H Parameter of Robot arm
Joint (i)
n
d n (mm)
n
a n
(mm)
1
1 (0)
200
-90 °
0
2
2 (-90 °)
0
0
197
3
3 (0)
0
-90 °
90
4
4 (0)
83
90 °
0
5
5 (0)
0
-90 °
0
6
6 (0)
82
0
0
By equating the parameters in the above table we can find the transformation matrix A1 to A6 as shown below;
-
Forward Kinematics
The forward kinematics model of the six-degree-of-freedom (6-DOF) joint robot is established by using the homogeneous transformation matrix method, the homogeneous coordinate value of the robot end-effector relative to the respective reference coordinate system is obtained, and the corresponding relationship between the psition and angle of the robot end-effector and the joint variable value in the rectangular coordinate space is established.
-
Inverse Kinematic
The area where the inverse kinematics of a robot exists is called the working space of the robot. The purpose of solving the inverse kinematics solution of the robot is also to require the working space of the robot.Inverse Kinematics analysis identifies the joint angles for intended position and orientation in Cartesian space. Total Transformation matrix Equation will be utilized to determine inverse kinematics equations. Its method, nevertheless, is far more complicated than direct kinematics considering that there is no special
C1
0A S1
0 S1
0 C1
0
0
0
1 A
analytical solution. Each manipulator requires a specific approach taking into consideration the system structure and
= constraints. [2]
2
2
1 0 1 0 d
1
C2
0
0
-
S2
0 0
0 a2 C2
1
1
C3
0 S3
a3C3
-
-
INDUSTRIAL ROBOT SOFTWARE
INTERFACE
Industrial robots are composed of mechanical system,
S
S
C
C
2 2
0 a2
S2
S 0
2A3 3
C3 a3 S3
control system, drive system, and sensors. According to the actual need of the assembly project, this topic develops the
0 0 1 0
0
0
0 0 1
C4 0 S4 0
S
S
0 1 0 0
0
0
0
0
0 1
basic functional modules in the industrial robot assembly system: robot serial port communication and gripper motion control module, robot controller Ethernet communication module, and six-dimensional force sensor data acquisition
and display module. The controller only allows users to
3A4= 4
0 C4 0
program through the Language provided by the manufacturing industry, namely KRL (industrial Robot
0 1 0
0
0
0
0
0
d 4
1
1
Language), but does not provide the compiler and running environment of other high-level languages. KRL language only supports simple arithmetic operation, process control,
communication, robot motion and other functions, while shielding systems such as file operation and multi-threading. The PC side will record and display the communication status of the information sent and received, as shown in Figure 3:
Fig. 3 Software interface communication display
VBNET programming method is used on PC system based on non-open feature of industrial controller. The basic method is that information of six axis force sensor is firstly sent to internal PC system; besides, all gravity compensation, force control algorithm and transformation of coordinate system are completed in the PC system and then, operation results (kinematic position and orientation of the robot) are transmitted to the robot via communication wire, thus driving robotic motion. According to structure of hardware and software framework can be classified into four layers. As shown in the Figure 4:
Fig. 4 Software System Architecture
In the software system, the service requiring assembly task is provided with VBNET function, and these interfaces are directly called on application layer to solve problems appeared in the process of assembly. Furthermore, service layer also can be divided into two layers, of which one is in KUKA controller to ensure consistent interface on the pair; the other is on PC system to complete complex work (for example, signal acquisition for sensor, force control algorithm, visual recognition). Services to top layer are
guaranteed between KUKA controller and external PC system through inter-process communication and collaborative operation.
-
Ethernet Communication for robot controller
Communication is an important way to realize information exchange between KUKA controller on the robot and the external system. KUKA controller has reserved Ethernet ports for users and provided API network communication for users in KRL language. Besides, such controller supports common operations of network communication (for example, open channel, send data, read and receive buffer), and can send content in the format of XML stream. In addition, peripheral sensor system of the robot can realize information exchange with controller on the robot via such API of Ethernet communication.
The internal Ethernet communication functions in KUKA controller include API of Ethernet communication client and API of XML stream parser. When building Ethernet communication system, users shall realize server side in external part of the robot, and send data in the format of XML. API of XML stream parser can parse received XML stream, and data that has been parsed is stored in a buffer. Besides, KRL language also provides a buffer to read API [34]. See Figure 5 for communication process.
Fig. 5 Ethernet communication process Schematics
KUKA controller on the robot will check whether received data is sent in XML format, which has ensured correctness of such data. And then, data will be parsed. However, such controller on the robot can connect at most nine external systems and distinguish them through setting names of different channels. KUKA controller implements network connection with the external system through two methods. One method is that VxWorks directly makes network communication with the external system. The other method is to build a router via windows system as a virtual router for Ethernet communication between VxWorks and the external system. Besides, two systems in KUKA controller communicate through sharing memory. Windows system is not only a server of VxWorks system but also a client for external sensor system. See Figure 3.7 for the method of utilizing virtual router.
Fig. 6 Utilizing Virtual Router
The client, i.e. KUKA controller, shall be provided with settings as below when XML communication is made:
-
To configure information of external channel that can make communication with KUKA controller.
The external access information is set in C: \ KRC \ ROBOTER \ INIT \ XmlApiConfig.XML set the file as follows. <? xml version = "1.0"?>
<XmlApiConfig>
<XmlApiParam InitOnce="false"/>
<Channel SensorName="force" SensorType="udp">
<TCP_IP IP="192.168.1.100" Port="5001" Route="true"
MapPort="5001"/> </Channel>
</XmlApiConfig>
-
Define the format for receiving XML
In order for the robot controller to recognize the XML information sent from the outside , it is necessary to define the format of receiving XML stream in advance , and create a new force.xml in the C: \ KRC \ ROBOTER \ INIT \ folder . This article sets the content as follows.
<Elements>
<Element Tag="Out" Type="STRUCTTAG" Stacksize="10" />
<Element Tag="Out.XPos" Type="REAL" Stacksize="10"
/>
<Element Tag="Out.YPos" Type="REAL" Stacksize="10"
/>
<Element Tag="Out.ZPos" Type="REAL" Stacksize="10" />
</Elements>
3 Define the format in which the XML is sent
This predefined XML file format can be used when sending data to the outside. Similarly, it should be defined in the C:
\ KRC \ ROBOTER \ INIT \ folder, and the file name must end with +. For example, this article defines the format for sending XML file force + .xml, and the content is as folows.
<Robot>
<Pos X = "" Y = "" Z = "" A = "" B = "" C = "" />
</ Robot>
At this point, all the configuration contents are configured and the programming test can be performed. The program involved in this article is divided into two parts, one is the KUKA controller terminal, which adopts KRL language provided by KUKA for programming and communication, and the other end is an external PC, which uses VBNET language to write the server, and the two are connected through a network cable. The Program flow chart shown in FIG.7 where, the dotted line indicates that information transmitted, and the arrow indicates the direction of transmission.
Fig. 7 Flowchart of Ethernet communication program
-
-
SOFTWARE INTERFACE FEATURES
The training assembly software includes communication with PLC, designed to obtain the robot coordinates, real- time view of joint motion, joint teaching, robot assembly and maintenance teaching. External functions include manual communication connection, robot reset button, emergency stop button, Teach pendant control and exit button. The software interface is as shown in the Figure 5:
Fig. 5 Software interface
The current co-ordinates position of the robot is calculated by the forward or inverse kinematics, and the corresponding coordinates are calculated according to the D-H method, which is displayed in real time.in the Fig. below
Fig. 6 Robot arm co-ordinates
-
CONCLUSION
This paper presented the development of an Industrial robot installation and maintenance training with an educational software package and Solid Edge 3D model. The BNRT-BRICS-RBT3 robot arm was modeled in this research. A complete mathematical model of BNRT- BRICS-RBT3 robot is developed including complete Kinematics analyses of the robot arm. Forward and inverse kinematics equations were derived using Denavit- Hartenberg notation. Velocity Kinematic Jacobian, and Trajectory Planning solutions were generated and implemented by the developed software.
The complete software life cycle was implemented and validated. Then, by analyzing the kinematics theory of the robot and using the DH method in the kinematics analysis method, a mathematical model of the robot is established. Thus this scheme is a more general method in the research of robot kinematics. In this paper, each coordinate system is established on the basis of the axis of
each joint, and the parameter value of this method is obtained based on the position relation of each joint linkage, thus the mathematical model of the robot is obtained. Through this model, we can draw the relationship between the links of the robot in the form of a matrix, which is convenient for the subsequent parameter model establishment and analysis. A positive kinematic solution is obtained by this method. The inverse kinematics solution of the robot is solved using the inverse matrix of the transformation matrix. From this results, it can be known that there are multiple sets of solutions for the inverse kinematics of the robot. It is necessary to screen based on the size of the joint space of the robot and the actual working conditions. Since the robot is a three-dimensional, 6 DOF mechanical device, the Lagrangian method is also used to model the robot dynamics. The Lagrangian equation of robot dynamics was established based on the energy of the mechanical system, and the mathematical model of the dynamics of the system was solved. The transformation matrix of the end effector of the robot relative to the base, which is solved by the DH method, is used to find the position and angle of the end effector in the reference coordinate system.
Finally according to the industrial robot assembly and maintenance demonstration, the functions of the system are determined, which are: real time monitoring of the communication status, current coordinate calculation, joint motion, joint teaching, robot assembly and maintenance teaching, and set manual Connection, reset and exit buttons are also set.
ACKNOWLEDGMENT
This paper is supported by the National Key Technology R&D Program (2015BAK06B04); the key Technologies R&D Program of Tianjin (15ZXZNGX00260,17YFCZZC00270,17KPXMSF00190,
17KPXMMSF00180,18ZXJMTG00160) Tianjin University of technology and education Plan Project(18JCTPJC67100,18JCTPJC68300,18JCTPJC6750 0, 18JCTPJC64200)
REFERENCE
-
Pei Zhouqi , Ma Zhenfeng . Research and Practice of "Curriculum and Politics " Teaching Reform of Industrial Robot Technology [J]. Journal of Jiamusi Vocational College , 2020, 36 (01): 108-109.
-
Li Huahui . Development and practice of professional courses for industrial robots oriented by enterprise demand [J]. Hubei Agricultural Mechanization , 2019 (23): 141.
-
Yang Juan , Nong Yingbin . Research on the status of intelligent manufacturing training equipment [J]. China New Technology & Products , 2019 (23): 142-143.
-
Yao Pei , Zhang Zhiming . Construction of training grounds for industrial robotics specialty under school-enterprise cooperation
Taking Hunan Vocational College of Labor and Personnel as an example [J] .Southern Agricultural Machinery , 2019,50 (22): 88.
-
Xintai Yu , Zhang Ye , Zhang Haipeng , Sun Kangling . School system school-enterprise cooperation in the exploration and research Integration – Specialty industrial robotics [J]. Chinese school education , 2019 (36): 42-43.
-
HAO Jian Bao , woods it , Gong Jian Long , Yi Huan silver . Construction of industrial robots online virtual simulation technology platform [J]. Experimental Technology and Management , 2019,36 (11): 113-116.
-
Yan Hongmeng . Analysis on the training system of industrial robotics specialty in higher vocational colleges [J]. Equipment Management and Maintenance , 2019 (22): 49-50.
-
Chen Jitao , Song Haiyan , Sun Weili , Ge Weiwei . Based on the "Qingdao City Industrial robot training of public service platform" of industrial robots personnel training and skills training [J]. Asia- Pacific Education , 2019 (11): 43.
-
Wu Qian , Zhang Hongqiang , Liu Lei , Wang Yunling , Zhou Fenglan , Li Jiejing . Research on the Construction of Shared Productive Training Bases for Vocational Education Schools and EnterprisesTaking KEBA Industrial Robot Training Base as an Example [J] .Science and Technology Wind , 2019 (32): 240.
-
Ding Xuemei , Liu Jing . Industrial robot training base construction and exploration – Take Yizheng Technician College as an Example [J]. Management & Technology ( on Xunkan ), 2019 (11): 84-85.
-
Cai Peichun . Practice and thinking on the reform of the integrated curriculum of industrial robot application and maintenance [J]. Chinese and foreign entrepreneurs , 2019 (30): 171.