
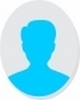
- Open Access
- Authors : Xuejiao Wang, Shipin Wu, Junlin Dai, Qiang Ma
- Paper ID : IJERTV13IS010036
- Volume & Issue : Volume 13, Issue 01 (January 2024)
- Published (First Online): 21-01-2024
- ISSN (Online) : 2278-0181
- Publisher Name : IJERT
- License:
This work is licensed under a Creative Commons Attribution 4.0 International License
Research on The Forming Qualit of Dual-phase Low Transformation Temperature Alloy Coatings Made By Laser Cladding Technology
Xuejiao Wang
School of Mechanical Engineering Tianjin University of Technology and Education
Tianjin, China
Shipin Wu
School of Mechanical Engineering Tianjin University of Technology and Education
Tianjin, China
Junlin Dai
School of Mechanical Engineering Tianjin University of Technology and Education
Tianjin, China
Qiang Ma
Tianjin Golden Bridge Welding Materials Internationl Trading Co.,Ltd
Tianjin, China
AbstractIn order to investigate the laser cladding process of dual phase low transformation temperature (LTT) alloy coatings, the influence of nine sets of laser cladding process parameters on the forming quality of dual phase LTT alloy coatings was studied using the single factor variable method. The results showed that as the laser power increased from 600W to 1000W, the coating surface gradually tended to be flat, and small holes changed from presence to absence. As the scanning speed increases from 8 mm/s to 15 mm/s, the number of small holes decreases until they disappear. When the powder feeding rate increases from 0.6 r/min to 1.0 r/min, the number of small pores increases and the size is larger. When the laser power is 1000W, the scanning speed is 8mm/s or 10mm/s, and the powder feeding rate is 0.8r/min, the laser cladding dual phase LTT alloy coating has good forming quality, no cracks, no pores and other defects.
Keywordslaser cladding; low transformation temperature; forming quality; process parameters
-
INTRODUCTION
Laser cladding technology is a new type of manufacturing and repair technology formed by combining rapid prototyping technology. It can quickly achieve near net forming of high- performance structural components by metallurgical melting and rapid solidification layer by layer stacking of metal powders using high-power lasers. Laser cladding technology is the foundation of laser cladding. In the process of laser cladding, process parameters are the key factors affecting the quality of the cladding layer. Unreasonable process parameters can cause defects such as cracks and pores to appear in the cladding layer. More researchers have investigated the effects of laser scanning speed and powder feeding rate on the geometric parameters (width, height) of the cladding layer[1][2]. Research has shown that as the scanning rate increases, the width and height of the cladding layer both decrease. Majumdar et al. manufactured 316L using laser forming technology and studied the influence of laser process parameters[3]. The results showed that as the laser scanning speed increased, the grain size decreased, but at the same time,
it may lead to the appearance of pores in the structure. Choosing the appropriate powder feeding speed can effectively reduce the formation of pores.
Low Transformation Temperature (LTT) materials control the martensitic transformation temperature (Ms) of deposited metals to a lower level (i.e. below 350 ) by precisely adjusting the alloying elements. Utilizing the volume expansion generated by martensitic transformation in the low-temperature range, residual compressive stress is generated to prevent cracking and deformation[4][5],improve stress corrosion resistance and fatigue life[6][8].The martensite residual austenite dual phase LTT material combines the high strength of the martensite matrix, effectively controlling deformation and preventing cold cracking during the laser cladding process of high-strength steel. In order to obtain a composite coating with high wear resistance, Chen Xizhang et al. prepared a new type of LTT flux cored welding wire by changing the ratio of alloy elements. The experimental results showed that the hardness of the plasma spray welding layer increased by 2.5 times and the wear resistance increased by 47.22 times[9].
At present, the application of dual phase LTT materials in laser cladding is relatively limited, and the research on the preparation process of dual phase LTT alloy coatings is not in- depth. Therefore, this article studied the influence of laser cladding process parameters on the forming quality of single- layer and multi-channel dual phase LTT alloy coatings through the single factor variable method, providing data support and theoretical basis for the manufacturing of multi-layer and multi-channel laser cladding dual phase LTT alloys, and ultimately obtaining laser cladding dual phase LTT alloys with good forming quality and defect free, providing theoretical basis and guidance for the preparation and practical application of dual phase LTT alloy coatings.
-
EXPERIMENTAL MATERIALS AND METHODS
-
Materials
The experimental substrate is Q345 steel, which has dimensions of 200mm in length, 60mm in width, and 10mm in thickness.After being ground by a grinding machine and sandpaper, is cleaned with anhydrous ethanol to ensure the surface cleanliness of the substrate. Laser cladding uses self- designed and prepared dual phase LTT alloy powder as the laser cladding alloy powder, with a particle size of 150 mesh ( 106 m) The chemical composition of the laser cladding dual phase LTT alloy coating is shown in Table 1.
-
Laser cladding testing method
Before the laser cladding test, the dual phase LTT alloy powder is mixed evenly using a ball mill, and then heated and dried in a vacuum drying oven to remove moisture from the alloy powder. The drying temperature is 110 and the drying time is 40 minutes. Laser cladding experiments were conducted using German IPG fiber laser and industrial robot arm instruments. The laser spot was 2mm, the defocus was 18mm, the overlap rate was 40%, the powder feeding gas flow rate was set at 7L/min, and the protective gas flow rate was set at 10L/min. Based on the characteristics of dual phase LTT alloy powder and laser cladding process, the process parameter range for laser cladding of dual phase LTT alloy is selected as laser power ranging from 600W to 1000W, powder feeding rate ranging from 0.6r/min to 1.0r/min, and scanning speed ranging from 8mm/s to 15mm/s. The specific process parameters are shown in Table 2.
The reverse judgment of process and forming based on the macroscopic morphology of the coating is an important basis for selecting process parameters[10]. By analyzing the melting width, melting height, dilution rate, and forming coefficient of coatings under different laser cladding process parameters, the selection range of process parameters is explored. A too high dilution rate can easily cause cracking of the fusion layer, and a too small substrate and coating may not bond firmly. A coating with a low dilution rate and a high forming coefficient will have better coating forming quality. The calculation formulas for dilution rate() and forming factor(n) are shown in (1) and
(2) respectively[11]:
= h / ( h + H ) 100% (1)
n = W / h (2)
In the formula, W represents the coating width, H represents the coating height, and H represents the melting depth of the substrate. The schematic diagram of the interface geometric dimensions of laser cladding coating is shown in Figure 1. And the cross-sectional geometric dimensions of laser cladding coatings under different process parameters were measured using Image J, and the forming coefficient and dilution rate were calculated.
Element
C
S
Mn
Si
P
Cr
Ni
Mo
Fe
Content (wt.%)
0.01
0.006
1.25
0.39
0.01
13.71
9.98
0.64
74.004
Table 1. Chemical composition of laser cladding dual phase LLTT alloy.
Table 2. Process parameters of laser cladding dual phase LTT alloy cladding layer.
Number
Laser power (W)
Scanning speed (mm/s)
Powder feed rate (r/min)
N1
800
10
0.6
N2
800
10
0.8
N3
800
10
1.0
N4
600
10
0.8
N5
800
10
0.8
N6
1000
10
0.8
N7
1000
8
0.8
N8
1000
12
0.8
N9
1000
15
0.8
Fig. 1. Interface geometric dimensions of laser Additive deposition layer.
-
-
RESULT AND ANALYSIS
-
The influence of laser power on coating quality
In the process of laser cladding, laser power is one of the key parameters that determine the characteristics of the melt pool and the final forming quality. When the laser power is set as a variable, which is 600W, 800W, and 1000W respectively, the scanning speed is fixed at 10mm/s, and the powder feeding rate is 0.8r/min. Observing the surface morphology of samples 4, 5, and 6 (Fig. 2), it can be seen that at lower laser power (600W), the powder that has not been completely melted will cause wrinkles and irregularities on the coating surface. With the increase of laser power, more heat is provided, which can more effectively melt the powder, increase the convection of the melt pool, and thus make the coating surface smoother[12][14]. Observing Fig. 3, when the laser power increases from 600W to 1000W, the number of small holes increases from many to few and then to none, indicating that when the laser power is too small, the heat source is small and not enough to completely melt the molten pool, which will lead to the appearance of small holes. Therefore, a laser power of around 1200W is closest to the optimal process parameters[15].
Fig. 2. Surface morphology of sedimentary layers at different laser power.
Fig. 3. Interface morphology of sedimentary layers with different laser power, corresponding to samples 4-6 in (a)~(c).
When the scanning speed is 10mm/s and the powder feeding rate is 0.8r/min, change the laser power and study the variation law of coating size. Fig. 4 shows the variation trends of melt width, melt height, dilution rate, and forming coefficient with laser power. It can be seen that when the laser scanning speed and powder feeding rate remain unchanged, within the selected laser power range, as the laser power increases, the coating melting width increases, and the increasing trend is obvious; Meanwhile, the melting height of the coating gradually increases, but the change is not significant. Analyzing the reasons, when fixing other manufacturing parameters during laser cladding, the setting of laser power has a significant impact on the energy received by the powder and substrate materials, as well as the microstructure and bonding quality of the final coating. However, the effect of laser power on the height of the coating is relatively limited, which may be because as the power increases, more powder is melted, and the
energy absorbed by the substrate also increases. These additional energies are mainly used to deepen the melting depth. From Fig. 4b, it can be seen that the dilution rate of the coating shows a trend of increasing power and gradually decreasing forming coefficient, where the dilution rate is calculated according to formula (1). As the laser power increases, a significant upward trend in dilution rate is observed. Analyzing the reason, the increase in laser power leads to an increase in the amount of heat released, which in turn causes the substrate material to receive more heat, resulting in an expansion of the volume of melted substrate material. Secondly, as the laser energy increases, some of the energy is converted into the driving force for the internal flow of the molten pool, which promotes the mixing effect between the substrate material and the cladding material at the interface, thereby causing an increase in dilution rate. Meanwhile, the decrease in forming coefficient indicates a decrease in deposition efficiency, which may affect the economy of the manufacturing process and the performance of the product.
-
The influence of scanning speed on coating quality
In the process of laser cladding, scanning speed is a key parameter that affects heat input, heating time, and powder utilization. The scanning speed, laser power, and powder feeding rate together determine the characteristics of the melt pool, which in turn affects the quality and morphology of the coating. When the laser scanning speed is set as a variable, which is 8mm/s, 12mm/s, and 15mm/s respectively, the fixed laser power is 1000W, and the powder feeding rate is 0.8r/min. Observing the surface morphology of samples 7, 8, and 9 (Fig. 5), it can be seen that the change in laser scanning speed also has a significant impact on the width of the coating. As the scanning speed increases, the interaction time between the laser and the dual phase LTT alloy powder decreases, resulting in a decrease in energy input at each point and a smaller size of the melt pool, resulting in a narrower coating[16]. This may affect the continuity and uniformity of the coating, especially at higher scanning speeds, which may lead to instability of the melt pool, affecting the deposition effect and the mechanical properties of the finished product. Observing Fig. 6, as the scanning speed increases from 8 mm/s to 15 mm/s.It is obvious that the number of small holes gradually decreases, and finally, as the laser scanning speed gradually increases, the small holes disappear, and the size of the small holes also gradually decreases. Therefore, the scanning speed should be appropriately increased, selecting around 10mm/s.
Fig. 4. The influence of laser power on the width and height of the deposited layer (a), The influence of laser power on the dilution rate and forming coefficient of the deposited layer (b).
Fig. 5. Surface morphology of sedimentary layers at different scanning speeds.
Fig. 6. Interface morphology of sedimentary layers with different scanning speeds, corresponding to samples 7-9 in (a)~(c).
When the laser power is 1000W and the powder feeding rate is 0.8r/min, the variation law of coating size was studied by changing the scanning speed. Fig. 7a shows the effect of scanning speed on the changes in melt width and melt height of the coating. The results indicate that within a specific range of laser scanning speed, the melting width and melting height slightly decrease with the increase of scanning speed. When the laser power and powder feeding rate remain constant, increasing the scanning speed will reduce the amount of powder deposited onto the substrate per unit time, that is, reduce the absolute amount of powder deposited, leading to a decrease in melting height. Meanwhile, the increase in scanning speed shortens the heat absorption time of the molten pool, lowers the temperature of the molten pool, and thus reduces the width of the molten pool. Fig. 7b reveals the relationship between the dilution rate and forming coefficient of the coating as the scanning speed increases. As the scanning speed increases, the dilution rate of the coating shows a decreasing trend. This is because the increase in scanning speed leads to a decrease in the energy absorbed by the coating and substrate, thereby reducing the melting amount of the substrate, reducing the dilution rate, and improving the forming coefficient.
Fig. 7. The effect of scanning speed on the width and height of the deposited layer (a), The effect of scanning speed on the dilution rate and forming coefficient of the deposited layer (b).
-
The influence of Powder feed rate on coating quality
In the process of laser cladding, the powder feeding rate is also a key parameter, which affects the utilization rate of powder and also affects the size of the cladding layer.Meanwhile, with the increase of powder feeding rate, the highest values of laser intensity and particle temperature significantly decrease.When the powder feeding rate is set as a variable, which is 0.6r/min, 0.8r/min, and 1.0r/min respectively, the fixed laser power is 800W, and the laser scanning speed is 800W. Observing the surface morphology of samples 1, 2, and 3 (Fig. 8), it can be seen that the coating surface is relatively flat, and the difference in coating width is not very obvious. The height of the coating cannot be accurately determined from the morphology diagram. Observing Fig. 9, when the powder feeding rate increases from
0.6 r/min to 1.0 r/min, there are many small pores with larger sizes. In order to avoid the occurrence of small holes again, the powder feeding rate should be appropriately reduced. Based on the above analysis, it is more appropriate to choose a powder feeding rate of around 0.6 r/min. Therefore, after optimizing the laser cladding process parameters, better quality laser cladding coatings can be prepared, while the appropriate powder feeding rate also avoids the occurrence of small holes and lack of fusion.
Fig. 8. Surface morphology of deposition layers with different powder feeding rates.
Fig. 9. Interface morphology of sedimentary layers with different powder feeding rates, corresponding to samples 1-3 in (a)~(c).
When the laser power is 800W and the laser scanning speed is 10mm/s, change the powder feeding rate to study the effect of powder feeding rate on the size change of laser cladding single-layer coating. Fig. 10a shows that during the laser cladding process, as the powder feeding rate increases, the melting height of the coating will increase while the melting width will decrease. This is because, while keeping other process parameters constant, an increase in powder feeding rate means an increase in the amount of powder fed into the melt, resulting in more powder being melted and thus increasing the melting height. At the same time, the increased powder feeding requires more heat to melt, which was originally used to heat the substrate. Therefore, the heat absorbed by the substrate decreases, the size of the melt pool decreases, and the melt width decreases. Furthermore, according to Fig. 10b, as the powder feeding rate increases, the dilution rate of the coating shows a decreasing trend. This may be due to the increase in the proportion of powder in the melt caused by feeding more powder, thereby reducing the proportion of substrate material in the melt, resulting in a natural decrease in dilution rate. The forming coefficient first decreases and then increases. At low powder feeding rates, the size of the melt pool is larger and the dilution rate is higher. However, as the powder feeding rate increases, the size of the melt pool decreases and the dilution rate decreases, resulting in a significant increase in the forming coefficient.
Fig. 10. The influence of powder feeding rate on the width and height of the deposited layer (a), The influence of scanning speed and powder feeding rate on the dilution rate and forming coefficient of the deposited layer (b).
-
-
RESULT AND ANALYSIS
IV. RESULT AND ANALYSIS
-
As the laser power increases from 600W to 1000W, the surface of the coating gradually becomes flat, and the number of small holes increases from presence to absence. As the scanning speed increases from 8 mm/s to 15 mm/s, the number of small holes decreases until they disappear. The melting width and height of the dual phase LTT coating gradually increase, the dilution rate gradually increases, and the forming coefficient gradually decreases.
-
When the scanning speed increases from 8 mm/s to 15 mm/s, the number of small holes decreases until there is no more. The melting width and melting height of the dual phase LTT coating gradually decrease, but the reduction is not significant. The dilution rate gradually decreases and the forming coefficient gradually increases.
-
When the powder feeding rate increases from 0.6r/min to 10r/min, the number and size of coating pores increase. The melting width and melting height of the coating increase, the dilution rate gradually decreases, and the forming coefficient first slightly decreases and then gradually increases.
-
When the laser power is 1000W, the scanning speed is 8mm/s or 10mm/s, and the powder feeding rate is 0.8r/min, the laser cladding dual phase LTT alloy coating has good forming quality, no cracks, no pores and other defects.
REFERENCES
[1] Huang Fengxiao, Jiang Zhonghao, and Zhang Jian. The influence of laser cladding process parameters on the macroscopic size of a single pass cladding layer, Thermal Processing Technology, vol. 39, no. 18, pp. 119-121, 2010. [2] Xu Shuwen. Structure and properties of low-temperature phase change metals by laser cladding, Wenzhou University, 2018. [3] Majumdar J D, Pinkerton A, Liu Z, Manna I, and Li L. Microstructure characterisation and process optimization of laser assisted rapid fabrication of 316L stainless steel, Applied Surface Science, vol. 247, no.1, pp. 320-327, 2005. [4] Wang Wenxian, Huo Lixing, Zhang Yufeng, and Wang Dongpo. Welding residual deformation of low phase transition point welded metal joints, Journal of Welding, vol. 24, no. 5, pp. 5-9, 2003. [5] Mikami Y, Morikage Y, Mochizuki M, and Toyoda M. Angular distortion of fillet welded T joint using low transformation temperature welding wire, Science and Technology of Welding and Joining, vol. 14, no. 2, pp. 97-105, 2009. [6] Wang Wenxian, Huo Lixing, Zhang Yufeng, and Wang Dongpo. Low phase transformation spot welding method for improving the fatigue strength of welded joints, National Welding Conference, 2001. [7] Wang Wenxian, Huo Lixing, Zhang Yufeng, Wang Dongpo, and Jing Hongyang. Low phase change spot welding strips improve the fatigue performance of longitudinal welded joints, Mechanical Strength, vol. 24, no. 2, pp. 273-6, 2002. [8] Ohta A. Fatigue strength improvement by using newly developed low transformation temperature welding material, Welding in the World, vol. 43, no. 6, pp. 38-42,1999. [9] Chen X Z, Hu K, and Lin S B. The Properties and Residual Stress of Argon arc Cladding Metal by Low Temperature Martensitic Transformation Powder, Journal of Surface Investigation: X- ray,Synchrotron and Neutron Techniques, vol. 11, no. 6, pp. 1329-1337, 2018. [10] Guan Zhenzhong.Laser Processing Process Manual, China Metrology Publishing House, 2007. [11] Wang Constitution. Preparation process and performance research of laser cladding high entropy composite coatings, Wuhan: Huazhong University of Science and Technology, 2022. [12] Wen P, Cai Z, Feng Z, and Wang G. Microstructure and mechanical properties of hot wire laser clad layers for repairing precipitation hardening martensitic stainless steel, Optics&Laser Technology, vol. 75, pp. 207-213, 2015. [13] Guodong Z, Hui Y, Qiyu W, Yazhi Z, Zhenggang L, Xudong H, and Yunsheng L. Microstructure and Properties of Laser Cladding Layer on Ferritic Stainless Steel, Journal of mechanical Engineering, vol. 52, no. 12, pp. 37-45, 2016. [14] Peng W, Zhipeng C, Zhenhua F, and Gang W. Mcrostructure and mechanical properties of hot wire laser clad layers for repairing precipitation hardening martensitic stainless steel, Optics&Laser Technology,vol. 75, pp. 207-213, 2015. [15] Wu Shipin. Study on the strengthening and toughening mechanism of low phase transition point (LTT) metal powder cored welding wire deposited metal, Tianjin University, 2019. [16] Qiao Hong, Li Qingtang, Fu Hanguang, and Lei Yongping. The effect of laser cladding process parameters on the microstructure and hardness of Fe-Cr-B alloy coatings, Journal of Materials Heat Treatment, vol. 35, no. 2, pp. 164-168, 2014.