
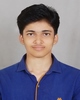
- Open Access
- Authors : Saket Sunil Godse , Sidhant Uttam Kasbe , Shivani Vijay Jadhav , S. S. Jagtap
- Paper ID : IJERTV10IS030156
- Volume & Issue : Volume 10, Issue 03 (March 2021)
- Published (First Online): 26-03-2021
- ISSN (Online) : 2278-0181
- Publisher Name : IJERT
- License:
This work is licensed under a Creative Commons Attribution 4.0 International License
Review on Flow Control Methods
Saket Sunil Godse
Department of Instrumentation Engineering AISSMSs Institute of Information Technology Pune, India
Sidhant Uttam Kasbe
Department of Instrumentation Engineering AISSMSs Institute of Information Technology
Pune, India
Shivani Vijay Jadhav
Department of Instrumentation Engineering AISSMSs Institute of Information Technology Pune, India
Prof. S. S. Jagtap
Department of Instrumentation Engineering AISSMSs Institute of Information Technology
Pune, India
Abstract In following paper the aim is to mention all the possible methods that can be used to control the flow and the applications of DCS in industrial sector. Amongst all the control systems, Distributed Control System is widely being used and is more popular in modern industrial processes. Distributed Control System is nothing but a computer controlled software application which is designed to work on the computer to complete the desired process by providing it with all necessary devices. Distributed Control System has plethora of advantages as compared to any other control system. Some of the advantages are, it helps to reduce the time required by the process to complete, as it can be automatically handled, it can reduce the labour cost, it also gives the ease to control and monitor real time condition. The flow control in pipeline is shown and also the process of bottle filling using distributed control system is mentioned. In most industries, flow management encompasses a big selection of application. Distributed Control System provides advanced management ways to regulate the method parameters.
Keywords DCS, DeltaV, Flow Control, PID, LabView, Flowmeters
-
INTRODUCTION
Process management instrumentality is meant to work the plants on a gentle state basis and square measure most significant to work out the performance of automatic system. Management of the method needs thorough management data, the behaviour of the method parts, method details, and inter-relation at intervals the sections of the method plant. Flow management encompasses a big selection of application in method industries. In 90% of method management applications have a tendency to manipulate the flow to get desired output. Flow is dynamic parameter and has totally different standardization strategies for standardization. The ratio and split range control take the place of cascade control. Ratio control is the technique in which it has two different values that are assigned a single set point respectively. The split range controls separate single set value into two independent set points. There are three tuning parameters for PID and it is also known as a three-term controller. The three parameters are proportional gain, integral gain and derivative gain. These three parameters effect in different way to the stability of system. So, the controller has to maintain the process variable close to desired set point. Flow is one of the dynamic parameters hence totally different
standardization methods for normalization Ziegler-Nichols method is utilized. The various types of feedback control include Proportional (P) Controller, Proportional-Integral (PI) Controller, and Proportional-Integral-Derivative (PID) Controller. The Tuning of PID Controller includes Ziegler- Nichols, Tyreus-Luyben Method, and Relay Auto-Tuning.
-
LITERATURE SURVEY
Rohit Nagvekar et al. [1] in their research paper elucidates about the tuning of stream control utilizing DeltaV DCS and matlab. The complete focus is on the three tuning strategies, for example, internal model control, PID tuner and the trial and error method. The paper gives definite data about the block diagram of the system which is used to control flow utilizing DeltaV. The flow from the pneumatic control valve is given to the turbine flow transmitter which changes over the input flow into 4-20ma signal. This 4-20ma signal is then given to the DCS that includes a PID controller functional block which deals with making the controlled variable closer to the set point value. It does as such by computing the values for proportional gain, reset and rate parameters by setting the method of the controller in the auto state. DCS ensure that the flow (controlled variable) arrives at nearer to the set point value. The output of DCS goes as an input to the current to pressure converter which considered liable for closing or opening of the control valve. Predominant flow exploitation alludes that DCS is the best combination. DCS provides very advanced approaches to control the method parameters. Thus we have a tendency to square measure attending to interface flow management loop with DCS. Study its behavior for a step input modification verify its transfer operate of our model victimization advanced DCS management functions. the comparative studies show that the simulations results vary from real time implementation results.
Sina Razvarz et al. [2] have mentioned that Flow control is vital evolving stream of Instrumentation. This paper mainly focuses on imitation and manipulating the flow handling of high viscous fluids. For this PID Control Algorithm is brought into play to control the flow operation in pipelines. It is the first try out to position a torsional actuator in order to manipulate the vibration on motor
hence restrict the flow operations in pipelines. Flow control loop set-up is primarily with a feedback control system. The suggested model contain comprises of induction motor, which causes a rotation in pump and consequently lead to flow of heavy oil in pipelines. There are only one or two case studies where analysis is done of solicitation of the PID Control for fluid -mechanics complication. Due to this shortfall of study, this paper has aimed to advance a PID control for flow-rate. By using Lyapunov stability analysis, the necessary circumstances for the minimal quantity of the proportional, integrator along with the derivation gains are obtained. The approach of utilizing torsional actuator on the motorpump arrangement is totally unique idea.
K. Pooventhan et al. [3] explains that the ratio and split range control take the place of cascade control. Ratio control is the technique in which it has two different values that are assigned a single set point respectively. The split range controls separate single set value into two independent set points. The multiple loops level processes lower the person's efforts and busts production. In split range control, the output of the controller is divided and dispatched to two or more control valves. In split range control applications, the controller regulates the actuation of first valve when the output ranges between 0 to 50% and the second valve when the output is in between 50 to 100%. The two parameters that are temperature and vacuum pressure are controlled to control the consistency level of flow.
Neha S. Narkhede et al. [4] have mentioned about the three tuning parameters for PID which are also known as a three-term controller. The three parameters are proportional gain, integral gain and derivative gain. This three parameters effect in different way to the stability of system. So, the controller has to maintain the process variable close to desired set point. The three tuning methods that are Ziegler Nichols, Cohen-Coon and Chein- Hrones-Reswick was depend on percent overshoot, settling time, rise time and integral absolute error. The ZN and CHR gave good results than CC method. MATLAB is a tool used to map out mathematical methods from real time data. Thus, transfer function model is obtained using system identificaion tool. In Lab View the real time execution of the tuning methods is done using the PID gains that are measured using formula.
Sujit Anandrao Jagnade et al. [5] in their paper focus on the Process Control. This is a fusion between the enumeration and engineering discipline that offer the mechanism, architecture, algorithm for manipulating a process. Determined by how the supervised outputs and controlled inputs present in a process involving chemical reactions. The chemical processes can be differentiated by the control layout as Single Input Single Output (SISO) Systems and Multiple Input Multiple Output (MIMO). The MIMO Systems slightly differ from SISO due to maximum number of variables as the name suggests nevertheless rather very important is linkage
between input and output variables. The various types of feedback control include Proportional (P) Controller, Proportional-Integral (PI) Controller, and Proportional- Integral-Derivative (PID) Controller. The Tuning of PID Controller includes Ziegler-Nichols, Tyreus- Luyben Method, and Relay Auto-Tuning. The Experimental setup and design signifies theoretical modelling for Single Tank System & Feedback Coupled Tanks Systems. The methods utilized for Tuning of PID Control are based on ultimate parameters like ultimate gain and ultimate period for a real time system operation. It is observed that out of controller design for the single tank system although three methods Relay Auto Tuning gives the most accurate response for designing of single tank system.
Khin Nway et al. [6] In the paper focuses around utilization of Distributed Control System (DCS) for bottle filling process. DCS was specially used because it provides more predictable scan rates than any other control system. DCS has more safety features and redundancy. The working/execution of bottle filling process is clarified. In the beginning, the bottle is continuously transferred to the air conveyer and then to rinser. As soon as the bottles arrive at the rinser, it starts to rinse through bottle nip clamping and turning around 180 degrees. After rinsing, the bottle turns over the origin and machines starts to fill the water into the bottle. Once the bottle is filled to desired level, the capping is performed using filling valves assembly respectively. After capping, the bottle is transferred to conveyer belt and the machine will start working as next anticipated procedure. To carry the bottles from bin to conveyer or vice versa, the bottle filling robot is employed. To control this bottle filling robot, two main transfer functions are used such as robot plant and controller stages. The robot plant can be represented by rotational dynamic of mechanical arm and controller stages are for compensation of robot plant in bottle filling robot system. The disturbance should also be brought in consideration to evaluate the performance of bottle filling robot system. The entire bottle filling process is carried out by using Distributed Control System and required elements.
Gabriel Constantin Sârbu et al. [7] In research paper focuses on the Vortex flow meter and coanda flowmeters. A study was conducted on the flowmeter including water which was constructed on the basis of coanda effect, which also included acceleration sensor causing static characteristics with standard flow meters. For the comparison of these two flowmeters, an installation was made providing hydraulic flow regime through the flowmeters. As the research needed constant flow during the measurement, this installation were made were in a way as to get constant flow and possibility of adjusting the amount of liquid flow in the desired range. The adjustment of liquid was made using electric valves which are driven by stepper motor.
Zulfadhli Mazlan et al. [8] In this paper have focused on enhancing the entire capability of conventional PID controller by designing and implementing the Adaptive Fuzzy PID Controller (AFPIDC) for applications of flow control. AFPIDC is developed and implemented because the controller used for various projects currently does not provide faster response and needs manual tuning. It can be linked with DCS-HMI and interfaced using MATLAB for mobile pilot plant. In this research, fuzzy logic is used to provide adaptive PID gain, which can be further added with initial PID gain. Also the performances of PID and AFPIDC are compared and analysed for further applications in the flow control. Adaptive Fuzzy PID Controller (AFPIDC) developed will be implemented to control the operation of the pilot plant and compare its performance with PID controller and Fuzzy Logic Controller. Following research includes the development of fuzzy inference system for Fuzzy Adaptive PID Controller using fuzzy logic toolbox in MATLAB. The implementation is used by two data acquisition card connected between laptop to control valve as output and from Orifice Flow Meter as input. The overshoot of 2.5% can be seen which are justifiable. Hence by auto tuning the initial PID gain by fuzzy reasoning, its observed that it provides better control performance as compared to PID controller with same initial gain. The objective of developing an Adaptive Fuzzy PID Controller and implementing it on the mobile pilot plant for flow control applications was successfully achieved.
Haruo Takatsu [9] The paper describes about the implementation of DCS in advance control technology. The plant pyramid is elucidated one by one. The pyramid consists of regulatory control, dynamic control, optimization, and planning. In the top- level I.e., planning production activities are planned and to satisfy varying needs. The functional requirements to execute advanced control in pyramid are discussed. The distinct items to be implemented are continuity, expandability, maintainability, and profitabil ity. In the next part of this paper implementation techniques to be applied in advanced control algorithms to industrial process are depicted. The divergent algorithm includes self- tuning control, fuzzy control, Model Predictive Control (MPC), Internal Model Control (IMC), and Multivariable MPC. MPC is approved and efficacious
control techniques in the industry especially in refinery and chemical processes. The MPC predicts the future way of behaving of the manipulated process output using the embedded processes. It makes it effortless to reinforce the process with long dead time, and reimburse the irregularities using the embedded feed forward function. For MPC reference trajectory and coincidence horizon tuning are important.
Jadhav Vilas K et al. [10] In this paper PID controller is used to control the flow rate of a closed loop flow control system. The elements of the flow control loop include Rotameter, Venturimeter, I/P converter, Control Valve, PID controller and Differential Pressure
Transmitter (DPT). In the flow control loop, parameter to be controlled is passed from tank to rotameter via pipe differential pressure of this flow is recognized through a device measuring flow rate. DPT converts the differential pressure into 4-20mA electrical signals. The o/p of DPT is supplied to PID controller through square root extractor. PID controller measure the difference between input signal with actual generated flow signal and a corrective o/p signal is manipulated by control valve. Control Valve is used as a final control element in the flow loop control. To enhance the action of DPT square root extractor is introduced to generate linear output. As per the nature of error the PID controller will response.
Jaideep Chakraborty et al.[11] The paper describes about the development of a Fuzzy Logic based control system for smooth controlling of the flow of feed water in a PFBR (Prototype Fast Breeder Reactor) to maintain the temperature of Steam generator sodium outlet temperature at a desired level during power setback. The flow of feed water into the steam generator is controlled by opening and closing of control valves. The Fuzzy Logic Controller (FLC) developed for this purpose will control the control valve based on the control value which is to be computed by a fuzzy logic controller using Fuzzy rules and inference based on the Steam generator sodium outlet temperature error and error rate. The secondary sodium outlet temperature of steam generator is required to be maintained at 352°C once full power is attained for which the feed water flow is controlled based on the secondary sodium outlet temperature. According to the process dynamics when secondary sodium outlet temperature exceeds 352°C feed water flow has to be increased resulting in more amount of heat being exchanged and thus bringing down the secondary sodium outlet temperature. Similarly if secondary sodium outlet temperature falls below 352°C then feed water flow has to be decreased resulting in less amount of heat being exchanged thus increasing the secondary sodium outlet temperature. A PI controller had already been used for achieving this control but it shows fluctuations in feed water flow during transients like one primary sodium pump trip when secondary sodium outlet temperature starts falling drastically due to reactor scram. To achieve smoothness in the feed water flow during such an incidence fuzzy logic controller has been proposed. The result has been compared with a PI controller and it has been observed that Fuzzy Logic Control performed better in attaining a smooth control of Feed water flow than PI control.
Yuezhong Liet al.[12] in paper describes that to equal the demands of ahigh-speedgas flowmeter calibration, ahigh-speedgas flow calibration system of dual buffer tanks and parallel structure is being constructed in accordance with the positive pressure standard meters calibration method. The systems experimental study mainly relates to the control accuracy of the flowrate and the calibration accuracy of the instrument in the experiment of flowcalibration. Apartfrom the flow measurement value,
the pipeline pressure and temperature value can beutilizedas the temperature and pressure re numeration for the flowrate in the standard state. In genuine systems application, the system requires 15 minutes to fill-up the first-order buffer tank, and high- speed calibration experiment requires to be completed in 30 minutes. The system can be used for regular needs of gas flow meter calibration. The system can be used for higher requirements of gas flow meter calibration if the system resolves the issueof stabilizationof gases by upgrading the architecture of the air compressor and the buffer tanks.
-
CONCLUSION
There are various advantages of DCS which allocate flexibility, simplicity by allowing central control, scalability, possible to control through dynamic graphic and monitoring and reporting of individual components and processes. Though there are some limitations of DCS like, failure of one controller effects more than one loop and requirement of skilled operator. The various extension or future scope of DCS is to make the DCS system more secure, so there will not be any cyber security attacks.
REFERENCES
-
Nagvekar, Abhiraj Bhalerao , Shubhangi Gajdhane,
Prof. Vijaykumar Bhanuse Tuning of flow control loop using DeltaV DCS and MATLAB International Journal of Engineering Research & Technology (IJERT) ISSN: 2278-0181 Vol. 9 Issue 05, pp.1225-1228, .
-
SinaRazvarz, Cristobal Vargas, Raheleh Jafari &
Alexander Gegov, Flow Control of Fluid in Pipelines Using PID
Controller IEEE Access February 2019, Vol. 7, 2019, pp.25673-
25680.
-
K. Pooventhan, K. Sowndarya, T. Mythilly & V. Dharthini, Enhancemen of Multi-loop Level Control with Optimized Ratio and Split Range Controller using DCS PCS7International Journal of Scientific & Engineering Research Volume 9, Issue 11, November-2018 ISSN 2229-5518, pp.1719-1723.
-
Neha S. Narkhede, Anil B. Kadu, Shilpa Y. Sondkar, LabVIEW Based System for PID Tuning and Implementation for a Flow Control Loop 2016 International Conference on Advanced Communication Control and Computing Technologies (ICACCCT) 26 January 2017, pp.436-442.
-
Anandrao Jagnade, Rohit Ashok Pandit & Arshad Ramesh Bagde Modeling, Simulation and Control of Flow Tank System International Journal of Science and Research (IJSR) ISSN (Online): 2319-7064 Volume 4 Issue 2, February 2015, pp.657- 669.
-
Khin Nway Oo, Zaw Min Naing & HlaMyo Tun,Implementation Of Distributed Control System in Process Control Management Using MATLAB International Journal of Scientific & Engineering Research Volume 3, Issue 6, June 2014, ISSN 2277- 8616, pp.149-154.
-
Gabriel Constantin Sarbu, Gheorghe Asachi, Modern Flowmeters International Conference and Exposition on Electrical and Power Engineering (EPE 2016), 20-22 October 2016, Iasi, Romania.
-
Zulfadhli Mazlan, R. Ibrahim, Development and Implementation of Adaptive Fuzzy PID Controller (AFPIDC) for Flow Control Application. Electrical and Electronics Engineering Department, Universiti Teknologi PETRONAS, Bandar Seri Iskandar, 31720, Tronoh, Perak, Malaysia.
-
Haruo Takatsu Advanced Control Technologies in DCS IA Solution Division Yokogawa Electric Corporation Tokyo, Japan.
-
Jadhav Vilas K, Anap Tushar, Gadakh Sachin & Dighe Sandip B. PID Based Flow Control Loop Department of Instrumentation & Control Engg. Pravara Rural Engineering College, Loni Ahmednagar Maharashtra.
-
Jaideep Chakraborty, T. Jayanthi, Pradeep Swaminathan Fuzzy Logic Based Feed Water Flow Control Model For Prototype Fast Breeder Reactor Indira Gandhi Centre for Atomic Research.
-
Yuezhong Li, Meigao Lv, Hualing Wu, Lingyuan Zeng The Build of High Speed Gas Flow Calibration System Based on Dual Buffer Tanks and Parallel Standard Meters Department of Mechanical and Electronic Engineering East China University of Technology Nanchang, China.