
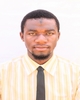
- Open Access
- Authors : Abdulyakin Usman, Lawal Salisu, Abubakar Lawan Iliyasu
- Paper ID : IJERTV12IS050319
- Volume & Issue : Volume 12, Issue 05 (May 2023)
- Published (First Online): 13-06-2023
- ISSN (Online) : 2278-0181
- Publisher Name : IJERT
- License:
This work is licensed under a Creative Commons Attribution 4.0 International License
Review on Technological Challenges of Vehicle Engine Emissions Control
1Abdulyakin Usman*, 2Lawal Salisu and 3Abubakar Lawan Iliyasu
1Department of Mechanical Engineering, Faculty of Engineering, Federal University Dutsin-Ma, Katsina, Nigeria 2Directorate of Physical Planning and Development, Umaru Musa Yar adua University, Katsina, Nigeria 3Department of Mechanical Engineering, Faculty of Engineering, Federal University Dutsin-Ma, Katsina, Nigeria
Abstract – Vehicle emission control efforts have a sixty-year history since their inception in the 1960s. Despite all these efforts, market and political pressure still exist on the auto manufactures to improve more on tailpipe emission control technologies. This paper provides up to date knowledge on latest, prominent, and currently available diesel and gasoline vehicle engine emission control technologies. Control technologies that were briefly introduced includes: diesel and gasoline particulate filters, Selective catalytic reduced catalyst, Diesel Oxidation catalyst, NOx absorbers, Exhausts gas recirculation, homogenous charge compression Ignition, Oxidation (two-way) catalyst, Oxidation- reduction (three-way) catalyst and four-way catalytic converter. The use of alternative, synthetic fuels derived from waste biomass and renewable electric energy has also been proposed to produce net zero CO2 emission (i.e. carbon neutral). Most prominent alternative fuel candidates were: ethanol, methanol, biodiesel, hydrogen and Hydro-treated vegetable oil (HVO). The development of electric vehicles, hybrid vehicles, plugin hybrids, and fuel cell vehicles is also a response to global pressures to lower emissions and improve fuel economy. The technological challenges encountered during the control includes: NOx PM tradeoff, high cost of technology, toxicity of some reducing element, increment in fuel consumption and poor durability. Newly developed control technologies that will overcome the short comings of the currently available emission control technologies are often expected to be developed in order to meet the air quality goals. Thus, the survey may served as a guide help to get up to date knowledge on currently available diesel and gasoline vehicle engine emission control technologies as well as their strength and weakness in development and utilization.
Keywords – Diesel; Gasoline; Exhaust emissions, Control technologies; Alternative fuel
-
INTRODUCTION
Transportation sector plays a vital role in world economic growth in moving people and goods around the globe, but it also has a significant environmental footprint and consumes more than half of global oil production (Carder et al., 2017). Global climate changes have been recognized as one of the most important environmental challenges to be face by humanity in the 21st century (Abouemara & Fikry, 2020). Global climate change, popularly known as global warming or the greenhouse effect, is caused by the addition of certain gases such as carbon dioxide (CO2), methane (CH4), nitrous oxide (N2O), and many chlorofluorocarbons (CFCs). These gases absorbed infrared radiation leading to excess thermal energy within the earth s biosphere. The prominent greenhouse gas is carbon dioxide (CO2) emissions from fossil fuel combustion.
As such, the strategy to control CO2 emission remain the main strategy to control global climate change (Pham et al., 2015). Automotive vehicles today are powered by either gasoline or diesel. Both of which are derived from petroleum, a non- renewable resource. These vehicles also emit several exhaust gases and pollutants most of these gases consist of harmful gases like carbon monoxide (CO), nitrogen oxide (NOx) and particulate matter (PM). Several technologies have been put in place to control vehicle exhaust emission. Yet, Motor vehicles engines, especially those fueled with diesel, contribute disproportionately to greenhouse gas emissions, as well as ambient air pollution responsible for millions of premature deaths worldwide each year (Anchan, 2018).
Looking to the future, a comprehensive plan to reduce the total emission from both existing and new diesel and gasoline engine are expected. The plan should have a target value. Such plane will definitely facilitate manufacture to develop far more durable and effective emission control system and to establish internal emission targets for new vehicles that are much stricter than legal standard. Emission control technologies in automobiles are employed to limit the discharge of noxious gases from internal-combustion engine via the engine exhaust, crankcase, fuel tank and carburetor. Gradually, many countries and territories have introduced emission control technologies intending to reduce vehicles emissions powered by internal combustion engines. Initially, researchers and experts concentrated on engine designs. Eventually, exhaust control methods and techniques were developed to reduce exhaust emissions from both spark-ignition and compression-ignition engines. Consequently, this paper reviewed the broad prominent technologies that were covered with the intent of controlling diesel and gasoline vehicle engine emission.
-
VEHICLE CONTROL TECHNOLOGIES
-
Control Technologies for Gasoline Fueled Vehicles
The control technologies discussed below represent current state of the art and possible future option of cleaning up diesel and gasoline engine exhaust. But meeting future emission goals is not as easy as simply choosing the best technology in each of the options. Technical, performance, size, and cost requirement, dictate that choice made in one option influence or limit the choice made in other options. Emission reduction technologies for gasoline-powered vehicles are focused on controlling HC, CO and NOX emissions. HC emissions come mostly from unburned gasoline, while CO emissions are the result of incomplete combustion (Hill et al., 2016). The way air
and fuel interact during the combustion process has a major impact on these two pollutants. In contrast, NOx is a byproduct of combustion, produced when nitrogen and oxygen in the air combine during the combustion process (Sanchez & German, 2012).
-
Electronic control systems: Electronic control technologies for stoichiometric engine using catalytic converter have been extensively developed. Nearly all engine emission control system used in the United States since 1981 incorporate computer control of the air-fuel ratio. Systems in resemblance have been used in Europe since late 1980s and Japan since 1978. These systems measure the air-fuel ratio in the exhaust and adjust the air-fuel mixture going into the engine to maintain stoichiometric (Faiz, 1998). Two types of catalytic converter are commonly used in automotive engines: Oxidation (two-way) catalyst, which controls hydrocarbon and carbon monoxide emissions; Oxidation-reduction (three-way) catalyst, which control hydrocarbons, carbon monoxide and nitrogen oxides. Hydrocarbon emissions have been reduced dramatically since their inception.
-
Two-way (Oxidation) Catalysts: This is the aftertreatment technology used for controlling tailpipe emissions of hydrocarbons, carbon monoxides and some components of particulate matter. The original types of autocatalysts are Oxidation catalysts and were used for gasoline cars from the mid-1970's until when three-way catalysts took the place. They look much similar with three-way catalysts in construction and composition, but are slightly less complex. Oxidation catalysts have little effect on nitrogen oxides (NOx), but convert hydrocarbons (HC) and carbon monoxide (CO)to carbon dioxide (CO2) and water (Demuynck et al., 2016). They are now rarely used on gasoline cars in developed counties because of the advantages of three-way catalysts, but are still used in some parts of the world where emissions regulation is less stringent.
-
Three-way catalyst (TWC): This is the aftertreatment technology used in stoichiometric gasoline vehicles for controlling tailpipe emissions of HC, CO, and NOX. Three-Way Catalysts remain the main autocatalyst technology used to control gasoline engines emissions. The catalyst operates in a closed-loop system including a lambda/oxygen sensor to regulate the gasoline engines air-to-fuel ratio. It can then simultaneously oxidize hydrocarbons and carbon monoxide to carbon dioxide and water while reducing NOx to nitrogen precisely at stoichiometry. When the catalyst has reached normal operating temperature this latest technology can simultaneously reduce HC, CO, and NOX by more than 99% (Sanchez & German, 2012).
-
Four-way Catalytic Converter: A four-way catalytic conversion system reduces emissions significantly. Despite the fact that it performs roughly the same function with three-way catalytic converter,
a four-way catalytic converter as depicted in figure 1 is of highly advantaged because it occupies less volume and eliminates particulates (Abouemara & Fikry, 2020).
Figure 1: Four-way Catalytic Converter
-
-
Gasoline particulate Filter (GPF): Stemming from the success of the diesel particulate filter (DPF) for diesel vehicles, this new technology the gasoline particulate Filter (GPF) offers a durable solution to control ultrafine particles emission from GDI cars in all driving conditions (Favre et al., 2016). This preferred solution as depicted in figure 2 is a relatively small close-coupled configuration will enable passive regeneration under most operating conditions due to the relatively high exhaust temperatures of GDI engines. Though, there are several approaches to decreasing gasoline particulate emissions, but none are robust with variable fuel and operating conditions, over the life of the vehicle (Timothy & Ameya, 2018).
Figure 2: Gasoline particulate Filter
-
Evaporative Emission and Control: Gasoline is relatively volatile fuel. Evaporation of significant gasoline occurs if gasoline is stored in a vented tank even at normal temperatures. Evaporative emission are controlled by venting the fuel tank (and, in carbureted vehicles, the carburetor bowl) to the atmosphere through a canister of activated charcoal. Hydrocarbon vapors are absorbed by the charcoal, so little vapor escape to the air (Bosteels & Searles, 2002).
-
-
Control Technologies for Diesel-Fueled Vehicles Hydrocarbons and carbon monoxides emissions are not
usually a concern with diesel engines, because engine-out hydrocarbons and carbon monoxides emissions are reduce by the lean operation which in simple oxidation catalysts enables high oxidation efficiency. PM and NOX emissions are more challenging to control and are the main focus of diesel emissions control research, as well as the main source of technology costs (Henze, 2021). Diesel vehicle exhaust contains less HC, CO and HC than gasoline vehicle, but the NOx and PM emissions are much higher than gasoline vehicle. These NOx and PM do great harm to human health.
-
Exhaust Gas Recirculation (EGR): EGR consist of recycling some Exhaust gas back to engine intake system for combustion under the detection of the exhaust Venturi flowmeter. Nitrogen and oxygen that are present in the atmospheric air enter into the combustion chamber, at the stage of high temperature; this courses the formation of NOx inside the combustion chamber. The EGR recirculates the amount of exhaust gases to the combustion chamber through air intake manifold. This gas mixes with oxygen in the air and help to reduce the high heat produces in the combustion chamber. Conversely the EGR help to reduce the combustion chamber temperature resulting in reducing the formation of NOx since are formed only at the high combustion chamber temperature. The recycled gases act as diluents, which reduced the pick gas temperature and hence lower the NOx emissions (Jankowski et al., 2002). It is the most significant technology for in- cylinder NOX reduction in diesel-powered engines. Its ability to reduce NOx is based on its diluting effect, which works in two ways: primarily by reducing the peak temperatures during combustion (NOx formation is proportional to combustion temperatures) and secondarily by reducing the concentration of O2 available for NOx formation (Sanchez & German, 2012). Exhaust gases mainly consists of CO2 and H2O, which are already combusted during previous cycle, they do not burn again when they are recirculate. The shortcoming attached to this technology is that its reduction in NOx is accompanied with an increase in fuel consumption, smoke, particulate and HC emissions (Anchan, 2018).
-
Homogenous Charge Compression Ignition: Homogenous Charge Compression Ignition fundamentally changes the combustion process by moving toward an ideal, extremely well mixed combustion event. Fuel is injected into a heated intake
air stream just outside of the cylinder (called port fuel injection), allowing for greater mixing and a near- homogenous charge of air and fuel. The enhanced mixing prevents formation of the fuel-rich zones where particulates form, and NOx emission are reduced (Timothy & Ameya, 2018).
-
Selective Catalytic reduction (SCR) Catalysts: This is another aftertreatment technology used in diesel vehicles for controlling emissions of NOX. It is called selective because the catalytic reduction of NOx with ammonia (NH3) as a reductant occurs preferentially to the oxidation of NH3 with oxygen as shown in the chemical reaction equations in figure 3 (Favre et al., 2016). SCR catalysts employ nitrogen- containing compounds (such as ammonia or urea) as reducing agents rather than hydrocarbons. Ammonia and urea compounds are very effective reducing agent than other nitrogen containing compound. Once the exhaust system is warm enough, SCR provide high level of NOx reduction, when appropriate amounts of ammonia are injected in to the exhaust stream. The pros of SCR systems are high conversion efficiencies, while in-use compliance and enforcement remain its main drawback (Henze, 2021).
.
4NH3+4NO+O24N2+6H2O
2NH3+NO+NO22N2+3H2O
8NH3+6NO27N2+12H2O
Figure 3: chemical reaction equations for Selective Catalytic reduction
-
NOx adsorbers or Lean NOx Traps (LNT): Stringent emission levels for NOx and PM are difficult to meet with EGR and in-cylinder emission reduction strategies. The options for aftertreatment NOx control are lean-NOx catalysts, lean NOx traps and SCR with ammonia (Favre et al., 2016). This latest technology adsorb and store NOx at lean conditions. The function of the NOx storage medium is achieved by materials that can form sufficiently stable nitrates within the lean operating engine points temperature range. Therefore, alkaline earth and to a certain extent also rare-earth compounds can be used to store NOx over a broad temperature range. This storage media are being regenerated in a NOx regeneration step when reaches their capacity. In such a step, the stored NOx is released by creating a rich atmosphere. The rich running portion is of very short duration and can be accomplished in a number of ways, but usually includes some combination of intake air throttling, Exhaust Gas Recirculation (EGR), late ignition timing, fuel injection in upstream LNT position, and post-combustion fuel injection (Demuynck et al., 2016).
-
Lean De-NOx Catalysts: This is also known as hydrocarbon-SCR. The systems in the catalytic coating used advanced structural properties so as to create a rich 'microclimate' where
hydrocarbons from the exhaust can reduce the nitrogen oxides to nitrogen, whie the overall exhaust remains lean. The hydrocarbon may be native (that occurring in the exhaust gas) or may be added to the exhaust gas via injection of additional fuel. This has the advantage that no additional reductant source (i.e. urea) needs to be carried out (Hill et al., 2016).
-
Diesel particulate filters (DPFs): This is an aftertreatment device for light duty vehicles. The technology traps particulate matter on the exhaust gas stream. It physically captures the soluble organic and soot fraction of PM on a substrate, often ceramic monolith or woven fibers. Gradually, the particles fill up and block the filter, causing backpressure (pressure increase in the exhaust system). Pressure increase in the exhaust system reduces fuel economy and affect engine performance, thus developing the need for cleansing process or regeneration (Pham et al., 2015). Diesel Particulate Filters (DPFs) have been applied to production vehicles since 2000 and have become standard equipment on all new diesel cars, buses and trucks. DPF as shown in the chemical reaction equations in figure 4 can effectively reduce PM with a reduction ratio of 80%-95%. It is made up of porous wall flow ceramic material and coated with noble metal coating (Kumar et al., 2016).
C+N02CO+NO (300-450) 2C+O22CO (>500)
2NO+O22NO2
4HC+3O22CO2+2H2O
2C0+O22CO2
Figure 4: chemical reaction equations for Diesel particulate
filters
-
Diesel oxidation catalysts (DOC): DOCs were reported to be the first commercial technology for PM abatement for light-duty Euro 3 levels vehicles implemented in Europe (Hill et al., 2016). The catalyst reduces PM emissions by targeting the soluble organic fraction of the particulates. It oxidizes hydrocarbon to carbon dioxide and water, thereby reducing the particulate mass emission. The technology remains a key technology for diesel engine PM emissions aftertreatment when high oxygen content of the exhaust rule out the use of three way catalyst. DOCs convert CO and HC but also decrease the mass of diesel particulate emission by oxidizing some of the hydrocarbons that are adsorbed on to the carbon particles (Abam, 2009). It also convert NO to NO2 as shown in the chemical reaction equations in figure 5, which is critical to oxidize soot collected on DPFs and improve SCR efficiency ( Timothy & Ameya, 2018).
2NO+O22NO2
4HC+3O22CO2+2H2O
2CO+O22CO2
Figure 5: chemical reaction equations for Diesel oxidation catalysts
The systems PM reduction rate is more than 10%-30%. It mainly composed of carrier, catalyst and sensor. All new diesel engines mounted on passenger cars, light-duty and heavy-duty trucks and buses are now equipped with DOCs (Singh et al., 2022).
-
ALTERNATIVE FUEL TECHNOLOGIES European Union has laid a plan for Competitive Low
Carbon Economy using technologies that emit less carbon, such that the greenhouse gases will be reduced to 40, 60, and 80% by 2030, 2040, and 2050 respectively (Kumar et al., 2016). To achieve this target, several initiatives have been taken by the member countries one of such is improvement in biofuels production, which is the most effective and efficient form of renewable energy. Biofuels are Fuels that are produced from biomass, as such vehicular pollutants that produce greenhouse gas emissions are reduced by the use of biofuels. The combustion of biofuels result to the emission of lower amount of carbon dioxide, carbon monoxide, sulfur dioxide, and particulate than with the combustion of fossil fuels (Taylor
& Demirbas, 2007). These biofuels can be classified as first generation, second generation, third generation, and fourth generation as depicted in figure 6. First-generation biofuels are derived mainly from food crops such as grains vegetable oil, and animal fats. Biodiesel and bio-ethanol are first-generation biofuels. Wheat straw, rice husks, and woody biomass produced from forestry residues or co-products and agricultural waste remain the source of second-generation biofuels. Hydrogen production by the conversion of biomass and algal biofuel production from Algae are third-generation biofuel. Algal hydrogen produced by algae cultivated in the presence of high solar efficiency is the fourth-generation biofuel (Bhan et al., 2020). They can be easily produced from the biomass, they are biodegradable and are environment friendly. Their combustion is almost similar to fossil fuels and they produce less toxic compounds and emissions. Furthermore, their net carbon emissions are significantly low, with no or little modifications to the engine. Some of the available biofuels that can easily replace fossil fuels are bioethanol, renewable methanol, biogas, biobutanol, biodiesel, biohydrogen and Hydro-treated vegetable oil (Greenbaum, 2014).
Biodiesel: Liquid fuels produced from renewable sources such as vegetable oils, animal fats, and waste cooking oil are called biodiesels. The carbon dioxide emitted after the combustion of biodiesel is absorbed while growing the oil crops, as such is referred to as carbon-neutral biofuel. It can be used as fuel in diesel engines either directly or by blending it with diesel fuel. Biodiesel contains no sulfur, with minimal amounts of carbon monoxide, particulate matter, and incompletely burned hydrocarbon. It is also 75% cleaner than petroleum diesel; it. It is mostly used as a conventional diesel supplement in order to reduce the levels of carbon monoxide, particulate matter, and hydrocarbons in the exhaust fumes of fossil diesel-based vehicles (Bhan et al., 2020).
Figure 6: Generations of biofuel
Methanol: Many tests have shown promising results using 85 100% by volume methanol as a transportation fuel in automobiles, trucks, and buses. During gasoline shortage, methanol had been used as the possible motor fuel substitute. Survey of applications of neat methanol and methanol gasoline blends has shown that the higher the methanol content in the gasoline methanol blends, the higher the brake fuel con-version efficiency of the SI engine and the lower the CO and HC emissions (Lee & Lavoie, 2013).
Ethanol: Another prominent source of fuel energy that can drive vehicles is ethanol. The conversion of ethanol into fuel is achieved by blending it with gasoline at the ratio of 85:15. The igniter is the small amount of gasoline. The burning of ethanol emits carbon dioxide and water into the environment, but when mixed with gasoline combusts sufficiently without harming the environment and reduces the emission of greenhouse gases into the environment (Timothy & Ameya, 2018). The use of ethanol as an alternative motor fuel has been steadily increasing worldwide for a number of reasons. Domestic production and use of ethanol for fuel can reduce air pollution, and reduce global climate change carbon dioxide buildup (Singh et al., 2022).
Hydro-treated vegetable oil (HVO): Biodiesel tends to dilute the engine lubrication oil, especially when particulate filters are frequently regenerated. This may be critical; as such the admixture of biodiesel to conventional diesel is limited so far. An alternative may be the use of hydrotreated vegetable oils. Hydro-treated vegetable oil (HVO) is a promising renewable drop-in fuel for diesel engines with very low CO2 impact. Furthermore, it shows a better emission behavior especially in relation to soot compared to standard diesel, which is caused by the absence of aromatic compounds and a better mixture formation. HVO is miscible with petroleum based diesel and can also be used as a straight substitute to petroleum based diesel (Stengel, 2015).
Hydrogen: Interest in hydrogen as a potential alternative automotive fuel has grown due to need of reducing greenhouse gas, CO2 emissions and to minimize dependence on fossil fuels. Hydrogen can be produced from a variety of renewable and non renewable sources. The combustion of hydrogen produces water and carbon containing pollutants such as hydrocarbons, carbon monoxides, carbon dioxide, and air toxics ae not emitted. However, trace amounts of these carbon containing pollutants may be emitted as a result of combustion of lubricating oil that might be leaking into engine cylinder. NOx is the only pollutant of concern from hydrogen engines. Hydrogen fuelled engines produces almost no CO2 and its global warming potential is insignificant (Anchan, 2018).
-
ZERO EMISSION VEHICLES TECHNOLOGY The advanced propulsion technologies of key interest are
electric vehicles, hybrid vehicles, plug-in hybrids, and fuel cell vehicles. In an electric vehicle, the electricity that is supplied from an electric utility provider runs the vehicle exclusively, while eliminating combustion on-board the vehicle. Batteries supply power to the motor. This batteries are charged via a central charging station (which can be installed in the owner s car garage) or via a portable charger that is plugged into an electrical outlet. In some regions electric vehicles are called zero emission vehicles (ZEVs), due to the fact that they don t consume fuel and therefore do not produce emissions. Although there are emissions attributable to the production of electricity to charge the vehicles, but it occurs at power plants, which are generally areas with relatively low population density (Pham et al., 2015). Fuel cells convert chemical energy to electricity, unlike batteries which are energy storage devices. Fuel cell vehicles use electricity produced from an electrochemical reaction that takes place when hydrogen and oxygen are combined in the fuel cell stack. A chemical conversion process is used instead of combustion, leading to higher levels of efficiency in a fuel cell vehicle. The production of electricity using fuel cells takes place without combustion or pollution and leaves only two byproducts, heat and water. Benefits include no emissions and fewer parts to be serviced and replaced. Electricity is also cheaper than gasoline. Electrically driven vehicles have very low noise levels and no local emissions (Kumar et al., 2016).
However, the long-term viability of electric vehicle may be affected by high electricity costs in recent years. The vehicle technology that can address some of the road blocks associated with electric vehicles is a hybrid electric vehicle (HEV) technology. This type of technology utilizes the benefits of both electrical system and internal combustion engine system. It combines a battery pack and electric motor with an internal combustion engine to increase efficiency (Lee & Lavoie, 2013). The hybrid electric vehicle (HEV) combustion and electric systems are combined in various configurations. In series configuration, the electric motor supplies power to move the wheels, while the combustion engine is connected to a generator that powers the motor and recharge the batteries. In parallel configuration, the combustion engine provides primary power, while the electric motor adds extra power for acceleration and climbing, or the electric motor is the primary power source, with extra power is provided by the combustion engine. In some types of parallel hybrid systems, the combustion engine and electric motor work in tandem, with
either system providing primary or secondary power depending on driving conditions. The additional hybrid system in some cases allows the vehicle to use a combustion engine when the batteries are depleted (Reitz, 2019).
-
CONCLUSION
-
In this report, a high-level review on vehicle engine exhausts control technologies for gasoline and diesel engines were summarized to cover lean NOx control, DPFs, and oxidation catalysts, including electronic control system and the rapidly developing technology of catalytic converters and gasoline particulate filters (GPF). The technological challenges of the control systems in development and utilization were presented. To control particulate matter emissions, the technologies including Diesel oxidation catalyst and exhaust gas recirculation system have been efficiency applied. Diesel
[5] Bosteels, D, and Searles, R.A. (2002). Exhaust Emmision Catalyst Technology,New Challenges and Opportunities in Europe. Association of Emissions Control by Catalyst, 46(1): 27-36. [6] Carder, D., Ryskamp, R., Besch, M., & Thiruvengadam, A. (2017). Emissions Control Challenges for Compression Ignition Engines. Procedia IUTAM, 103 111.https://doi.org/10.1016/j.piutam.2017.03.015
[7] Demuynck, J., Bosteels, D., & Building, D. (2018). Emissions control technologies to meet current and future european vehicle emissions legislation. Association of Emissions Control by Catalyst, pp: 27-36. [8] Faiz, A. (1998). Air pollution from Motor Vehicles, standards and technologies for controlling Emissions. World Bank Washington, D.C. 20433, U.S.A [9] Favre, C., Demuynck, C. and Bosteels, D. (2016). Emissions control Technologies to Meet current and Future European Vehicles Emission Legislation. Brussels. Belgium. Association for Emissionscontrol by Catalyst (AECC).
[10] Greenbaum, D. S. (2015). Sources of air pollution: gasoline and diesel engines. IARC Scientific Publication, pp: 49-62.oxidation catalyst is a well-accepted technology to limit
particulates emission because it can reduces PM by targeting the soluble organic fraction of the particulate mass emission by
25 to 50 percent. Its major challenge in utilization is the removal of NOx from the oxygen rich exhaust gas of combustion engines. Though, exhaust gas recirculation system has been identified to as the possible remedy technology to this tradeoff. Therefore, Exhaust gas recirculations remain the cost effective solution to fulfill NOx emission regulations, but it increases soot emission and fuel consumption in the conventional CI combustion. Lean NOx traps (LNT) technology are effective to reduce 60 to 70% NOx emission in real-world light duty systems, but the durability of LNTs under sulfur contamination has always been a major problem. Stricter incoming legislation could be achieved using SCR technology, due to its capacity to reduce NOx to about 95% during combustion process. Average reduction of Hydrocarbon to about 80-90 percent is possible with three-way catalysts and electronic engine control systems. But such devices have little impact on fuel economy as they slightly increase fuel consumption. The CO and HC in diesel engine emissions control via the DOC is very effective, however the oxidation catalyst suffer the trend of low temperature low activity and vice versa. Therefore, new technologies that will overcome the weakness of the present control technologies are expected to be developed in order to achieve better urban air quality.
REFERENCES
[1] Abam, F. I. (2009). Vehicular Emissions and Air Quality Standards in Nigeria. European Journal of Scientific Research, 34(4): 550 560. [2] Abouemara, K., & Fikry, S. (2020). Emission Control Technologies in Spark Ignition Engines. Journal of Student Research, 9(1): 1 35. [3] Anchan, A. (2018). Challenges & Emission Control Technologies for Heavy-Duty Commercial Vehicles to meet Bharat Stage VI Norms: A Review. International Research Journal of Engineering and Technology, 9931001. [4] Bhan, C., Verma, L., & Singh, J. (2020). Alternative Fuels for Sustainable Development. https://doi.org/10.1007/978-981-13-5889-0 [11] [12] Henze, K. (2021). Research on Emission Standards and Control Technology of Heavy Commercial Diesel Vehicles Research on Emission Standards and Control Technology of Heavy Commercial Diesel Vehicles. https://doi.org/10.1088/1755-1315/687/1/012030 [13] Hill, N., Windisch, E., Kirsch, F., Horton, G., Dun, C., Energy, R.,Hausberger, S., Matzer, C., Graz, T. U., Tepr, I. S., Donati, A. V,
Krause, J., Thiel, C., Jrc, E. C., Wells, P., Review, P., & Business, C. (2016). Improving understanding of technology and costs for CO2 reductions from cars and LCVs in the period to 2030 and development of cost curves. Climate Action, pp: 1-310.
14] Jankowski, A., Sandel, A., Seczyk, J. and Jankowska, B.S. (2002). Some Problems of improvement of fuel Efficiency and Emissions in internal Combustion Engines. Journal of KONES Internal Combustion Engines, 2 (2005): 333-356.
[15] Reitz, H., R., (2019). The future of the internal combustion engine. International Journal of Engine Research, pp: 1-8 https://doi.org/10.1177/1468087419877990 [16] Kumar, N., Sonthalia, A., & Pali, H. S. (2016). Biofuels Opportunities and Challenges. Journal of Metrology Society of India, pp: 1-23. https://doi.org/10.1007/978-981-13-9012-8 [17] Lee, R. A., & Lavoie, J. (2013). From first- to third-generation biofuels: Challenges of producing a commodity from a biomass of increasing complexity. Animal Frontiers, 3(2): 1-7. November 2015. https://doi.org/10.2527/af.2013-0010 [18] Pham, T., Lee, B., Lee, C., & Nguyen, M. (2015). Emission Control Technology. Current Air Quality Issues, pp: 221-249. https://doi.org/10.5772/59722 [19] Sanchez, F. P., & German, J. (2012). Estimated Cost of Emission Reduction Technologies for Light-Duty Vehicles. International Council on Clean Transportation. pp: 1-136. [20] Singh, S., Kulshrestha, M. J., Rani, N., Kumar, K., Sharma, C., & Aswal, D. K. (2022). An Overview of Vehicular Emission Standards. Journal of Metrology Society of India pp: 1-23. https://doi.org/10.1007/s12647-022-00555-4 [21] Stengel, B. (2015). Synthesis, Characterization, and Use of Hydro- Treated Oils and Fats for Engine Operation. A Report from the IEA Advanced Motor Fuels Implementing Agreement, pp: 1-51. [22] Taylor, P., & Demirbas, A. (2007). Energy Sources ,Economics,Planning , and Policy Fuel Alternatives to Gasoline. Fuel Alternatives to Gasoline, pp: 310-320. https://doi.org/10.1080/15567240600629492
[23] Timothy, J., and Ameya, J., (2018). Review of Vehicle Engine Efficiency and Emissions. International Journal of Engines, 11(6): 1307 1330. https://doi.org/10.4271/2018-01-0329.