
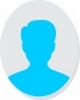
- Open Access
- Authors : Ali H. Alramadhan , Ibrahim O. Habiballah
- Paper ID : IJERTV9IS110242
- Volume & Issue : Volume 09, Issue 11 (November 2020)
- Published (First Online): 03-12-2020
- ISSN (Online) : 2278-0181
- Publisher Name : IJERT
- License:
This work is licensed under a Creative Commons Attribution 4.0 International License
Review the Upgrade of Distribution Transformers
Based on Distribution System Topologies, Load
Flow and Dissolved Gas Analysis
Ali H. Alramadhan
Systems Engineering Department
King Fahd University of Petroleum and Mineral
Dhahran, Saudi Arabia
Abstract—Distribution transformer is one of the critical and most expensive electrical components in the power system which is mainly to step-down and regulate the voltage to the loads side. In many industrial business (e.g. energy and petrochemical companies), sudden loss of a transformer can threaten the operation continuity where unplanned repair or replacement of
a transformer is time consuming that can’t be tolerated. In case
of total electrical power outage, the firm could be out of business. Therefore, several aspects are available to evaluate the conditions of oil-immersed transformer based on selected distribution topology, dissolved gas analysis (DGA), in addition to applying load flow and contingency analysis through computer software. This paper presents a review of the performance of electrical network when an oil-immersed transformer in service or out of service. It also reviews the use of transformer dissolved gas analysis to diagnose transformer faults in early stage.
Keywords— Distribution Transformer; Dissolved Gas Analysis (DGA); Load Flow; Distribution System Topologies.
I. INTRODUCTION
Solving power flow equations in distribution system requires the modelling of three major electrical components such as the voltage sources, representations for electrical cables and transformers, and the loads[1]. Three-phase transformers can be modelled by series and shunt admittance blocks to reflect the copper leakage and core losses respectively[2]. There are several considerations in transformer selection, such as type of winding connection, the phase difference between the primary and secondary, tap changer and power rating[3].
Therefore, one of the most used tools for evaluating the condition of transformers is dissolved gas analysis (DGA). It helps to identify and detect the deficiencies in the transformers after years of operation by analyzing the oil quality and the dissolved combustible gases inside the transformers. DGA test results can support estimating the right time to upgrade the transformers which eventually will enhance the reliability of power supply for a cost-effective approach. When one aged transformer in electrical network got damaged and became out of service, there will be impact on the overall power flow that reaches the loads. Depending on the optimization of the power distribution topology, the outage of one transformer can cause complete, partial or no outage to the load service.
Ibrahim O. Habiballah
Electrical Engineering Department
King Fahd University of Petroleum and Mineral
Dhahran, Saudi Arabia
In this paper, the first section will be about reviewing low voltage distribution system topologies to evaluate the impact of a transformer outage. The second section will be about reviewing different load flow methods and techniques which can be applied to study the performance of electrical network when a transformer in service or out of service. The last section will be about reviewing transformer dissolve gas analysis (DGA) which can be implemented to diagnose transformer faults in early stage.
II. REVIEW OF LOW VOLTAGE DISTRIBUTION SYSTEM TOPOLOGIES [4,5]
Selecting the best topology option for the power distribution system depends on the load requirements to satisfy the desired level of power supply reliability. As the reliability increases, the cost and complexity of power distribution will increase accordingly. The purpose of reviewing the distribution system topologies is to study the impact of losing a transformer at different distribution topologies.
A. Radial Systems
In the simple radial system, there is single power supply serving the all loads. It is the simplest power distribution system which consists of a single power source, a fused switch, a transformer, and a single bus to distribute power to the loads. In case of an electrical fault occurring between the supply circuit up to the bus, it will cause complete power outage. The reliability of system arrangement can be enhanced if there are two independent power sources available to enable either manual or automatic switching between power sources in case of power supply failure. Also, the simple radial system can be improved to be an expanded radial system by including an additional transformer as shown in “Fig. 1”. The loss of one transformer will not cause the loss of entire load. Hence, the reliability of the system will be increased as the number of transformers increases. In addition, the location of the secondary buses can be in different locations nearby the loads which can improve the voltage drop and electrical losses.
IJERTV9IS110242 www.ijert.org
Published by : International Journal of Engineering Research & Technology (IJERT)
http://www.ijert.org ISSN: 2278-0181
Vol. 9 Issue 11, November-2020
B. Primary Selective System
When two power sources are available, tie circuit breaker can be installed at the primary bus of the distribution system as shown in “Fig. 2”. If the tie circuit breaker is configured at the normally-close position, parallel connection between the two power supplies can be established. However, extra care should be taken to overcome any electrical faults. When an electrical fault occurred at one of the power sources, the fault shall be cleared to prevent the entire service loss.
Fig. 2 Primary-Selective System
C. Primary Loop System
To overcome the loss of the loads due to feeder cable failure, the loop system can be designed as shown in “Fig. 3”. Typically, the arrangement of an open loop system is achieved by installing four loop switches, keeping only one switch to be in normally open position. It possible maintain close loop system by replacing the switches with metal-clad circuit breakers to provide maximum selectivity.
Fig. 3 Primary Loop System
D. Secondary Selective System
To overcome loss of partial loads when one component fails such as a transformer, the arrangement of the secondary buses can be integrated by placing tie circuit breaker as shown in “Fig. 4”. If the configuration of the tie circuit breaker was normally-closed, the failure of one feeder or transformer will not cause any outage. The design of each transformer, along with its secondary circuit breaker shall be capable of handling the entire load in case of failure of one transformer.
Fig. 4 Secondary-Selective System
E. Ring Bus System
The buses configuration in the distribution system can be arranged in close loop as shown in “Fig. 5”. In this arrangement, the fault at one bus will cause only the isolation of that particular faulty bus and associated loads while the rest of the system will remain healthy.
Fig. 5 Primary Ring Bus System
F. Composite Systems
In industrial and commercial applications, it is rare to apply a single distribution system topology. Typically, combination of topologies can be arranged to satisfy the desirable reliability level. “Fig. 6” shows an extreme reliable system where failure of multiple components will not cause any interruption to the load.
Fig. 6 Composite System
IJERTV9IS110242 www.ijert.org
Published by : International Journal of Engineering Research & Technology (IJERT)
http://www.ijert.org ISSN: 2278-0181
Vol. 9 Issue 11, November-2020
III. REVIEW OF LOAD FLOW METHODS The load flow analysis during the outages of generators and branch circuits can be calculated either offline or online for planning and controlling studies, respectively[6]. The solution of nonlinear power flow equations can be classified as coordinate method such as Gauss-Seidel, or classified as a
gradient method such as the Newton-Raphson (NR) method[2].
Solving load flow nonlinear equations using the Gauss-Seidel method requires high numbers of iterations to converge to the desired accuracy where the number of iterations is proportional to the number of buses in the network[7,8]. Another drawback of the Gauss-Seidel method is that it suffers from divergence especially when the admittance matrix is ill-conditioned[8].
For highly complex systems, the Newton-Raphson method can solve the non-linear power flow equations with few numbers of iterations, despite the computation time of linearizing non-linear equations at initial estimated conditions and constructing Jacobian matrix [1]. NR is well known for its convergence properties; however, one of its drawbacks is that Jacobian matrix must be calculated in each iteration, which raises the concern of time and storage consumptions [3]. In [9], a modify version of Newton method for radial systems was introduced where Jacobian matrix was represented in UDUT form to avoid ill-condition in LU factorization.
One of the suitable load flow calculation methods that can be implemented for online and offline solutions regardless the size of the network is the Fast-Decoupled technique [3]. In [10], a power distribution system was broken down into several areas where, in each area, a power flow solution was performed in parallel and independently without impacting on the accuracy. This technique requires a slack bus to be assigned in each area, with inter-transmission lines between one area to another, where these lines are treated as loads injected to the buses. The main advantage of [10] is that as local computation is performed independently in each area based on fast-decouple method, besides minimizing the computation on the local CPUs which speeds up the overall computation. This technique required well synchronized communications between all areas[10].
In[11], a new proposed method based on network-topology was developed by constructing Bus-Injection to Branch-Current (BIBC) and Branch-Current to Bus-Voltage (BCBV) matrices to solve the load flow. This proposed technique required line data to be inserted graphically for radial distribution system[11].
IV. REVIEW ON TRANSFORMER DISSOLVE GAS ANALYSIS ASSESSMENT (DGA)
Diagnosing transformer faults in the early stage can be performed by implementing DGA which can avoid catastrophic electrical power failures[12]. In [12], five actual transformers failures were detected by DGA, then additional diagnostic tools (such as winding and dielectric resistances) were applied to investigate the faults further. Eventually, internal inspection of transformers was carried out to confirm the issues. In[13], a methodology was developed to predict the transformer conditions in long and short terms. For the short-term diagnosis, some typical tools were applied through four main steps; the first step was to check if the fault existed; the second step was to diagnose the conditions; the third step was to identify possible fault type; and the last step was to formulate the degree of confidence by combining the fault results from different DGA methods[13]. For long-term diagnosis, Remaining Useful Life (RUL) can be calculated based on the condition of the internal paper insulation [13]. The main three steps to perform DAG can be briefly described as follow:
A. Key Dissolve Gases (KDG) Condition
Based on IEEE C57.104 and IEC 60599, measuring the concentration of several gases can predict the faults in oil-immersed transformers[14]. These gases can be classified into three categories; five gases for hydrogen and hydrocarbon (H2, CH4, C2H2, C2H4, and C2H6), two gases for carbon oxides (CO, and CO2), and two gases as non-fault gases (O2, and N2) [15]. In general, there are three common technologies for measuring KDG; a spectroscopic system, which is based mainly on analyzing molecular mass; optical technology, which is based on light absorption; and solid-state technology, which is based on change of chemical or physical property of gas sensors[16]. In [14] a unique optical method is applied to measure KDG through an infrared spectroscopic method called Binary Zone Plate (BZP), which is cost-sufficient and consists of simple comparing with two well proven spectroscopic methods known as Fourier Transform Infrared Spectroscopy (FITIR) and Photoacoustic Spectroscopy (PAS).
B. Determine the Existence of the Fault
To evaluate the normality of transformer conditions based on individual and total KDG concentration, there are four classified conditions, starting from normal transformer “condition-1” up to severe transformer abnormality “condition-4” [17]. Table 1 in [17] used as start point if there was no DGA history record for transformers to evaluate transformers’ conditions. Then, the rate of gas generation shall be calculated to apply table 2 or table 3 in [17], where the increase of gas rate will indicate that the fault is still active and proper action shall be taken. When the gas concentration is high (such that transformer condition is classified as “condition-4”), it is recommended to take the transformer out of services and perform an internal inspection [17,18].
C. Estimate the type of the fault
Based the profile of detected KDG and significant gases proportions, there are four general fault types; Thermal-Oil, Thermal-Cellulose, Electrical-Partial Discharge, and Electrical-Arcing [17]. Well-defined five gas ratios (“R1”:CH4/H2, “R2”:C2H2/C2H4, “R3”:C2H2/CH4¸ “R4”:C2H6/C2H2, and “R5”:C2H4/C2H6) which can be used to identify a possible fault type based on IEEE C57.104, and IEC60599 [17-19]. Although, determining the exact type of fault is not accurate in all cases, it is recommended to apply and compare the results from different methods to come with reasonable decisions [12]. In [20], five DGA methods (Key Gas, IEC Ratio, Rogers Ratio, Dornenburg, Duval Triangle Methods) were applied to identify the type of fault from each method, where the result accuracy using this combined
IJERTV9IS110242 www.ijert.org
Published by : International Journal of Engineering Research & Technology (IJERT)
http://www.ijert.org ISSN: 2278-0181
Vol. 9 Issue 11, November-2020
analysis resulted into the highest accuracy comparing to result obtained from individual method.
V. CONCLUSIONS
The paper has reviewed different aspects to evaluate the condition of distribution transformers, and to determine the right time for the upgrade. The load flow in different power distribution topologies can be studied to evaluate the impact of transformer outage on the power delivered to the loads. The implementation of DGA using different methods can be a proactive assessment aims at enhancing the reliability of power network by closely monitoring the health of the transformers.
ACKNOWLEDGMENT
The authors acknowledge the support of King Fahd University of Petroleum and Minerals in conducting this research work.
REFERENCES
[1] Schneider, K. P. et al. (2018), “Analytic Considerations and Design Basis for the IEEE Distribution Test Feeders”. IEEE Transactions on Power Systems, vol. 33, no. 3, pp. 3181–3188.
[2] Bazrafshan, M., Gatsis, N. (2018), “Comprehensive Modeling of Three-Phase Distribution Systems via the Bus Admittance Matrix”. IEEE Transactions on Power Systems, vol. 33, no. 2, pp. 2015–2029.
[3] Chen, T. H., Chen, M. S., Hwang, K. J., Kotas, P., Chebli, E. A. (1991), “Distribution system power flow analysis-a rigid approach”. IEEE Transactions on Power Delivery, vol. 6, no. 3, pp. 1146–1152.
[4] I. of E. and E. Engineers and I. I. A. S. P. S. E. Committee (1994), “IEEE Recommended Practice for Electric Power Distribution for Industrial Plants”. IEEE.
[5] I. of E. and E. Engineers, I. I. A. S. P. S. E. Committee, I. S. Board, and
A. N. S. Institute (1991), “IEEE Recommended Practice for Electric Power Systems in Commercial Buildings”. IEEE.
[6] Stott, B., Alsac, O. (1974), “Fast Decoupled Load Flow”. IEEE Transactions on Power Apparatus and Systems, vol. PAS-93, no. 3, pp. 859–869.
[7] Abaali, H., Elhachmi, T., Rachid, S. (2018). “Comparison of newton Raphson and gauss seidel methods for power flow analysis”. World Acad. Sci. Eng. Technol. Int. J. Energy Power Eng 12, no. 9.
[8] Saadat, H. (2002). Power System Analysis. McGraw-Hill.
[9] Zhang, F., Cheng, C. S. (1997), “A modified Newton method for radial distribution system power flow analysis”. IEEE Transactions on Power Systems, vol. 12, no. 1, pp. 389–397.
[10] Yuan, C. et al. (2019), “Graph Computing based Distributed Fast Decoupled Power Flow Analysis”. IEEE Power Energy Society General Meeting (PESGM).
[11] Abul’Wafa, A. R. (2012), “A network-topology-based load flow for radial distribution networks with composite and exponential load”. Electric Power Systems Research 91 (2012): 37-43.
[12] Mahmoudi, N., Samimi, M. H., Mohseni, H. (2019), “Experiences with transformer diagnosis by DGA”: case studies. IET Generation, Transmission & Distribution, vol. 13, no. 23, pp. 5431–5439.
[13] Verdelho, M. I. et al. (2019), “Path: Predicting Transformer Health. 25th International Conference on Electricity Distribution”. CIRED.
[14] Glowacki, P., Shafai, C. (2017), “Binary Zone Plate Infrared Spectrometer for Dissolved Gas Analysis in High Voltage Equipment”. Proceedings, vol. 1, no. 4, p. 555.
[15] Rai, A. S., Maheshan, C. M. (2019), “Artificial Bee Colony Algorithm Based Interpretation Of Dissolved Gas Analysis”. 2019 4th International Conference on Electrical, Electronics, Communication, Computer Technologies and Optimization Techniques (ICEECCOT), Mysuru, India, 2019, pp. 106-110.
[16] Chatterjee, A., et al. (2013), “Usage of nanotechnology based gas sensor for health assessment and maintenance of transformers by DGA method”. International Journal of Electrical Power & Energy Systems, vol. 45, no. 1, pp. 137–141.
[17] Transformers Committee (2009), “IEEE Guide for the Interpretation of Gases Generated in Oil-Immersed Transformers”. IEEE Std C57.1042008 (Revision of IEEE Std C57.104-1991) , vol., no., pp.1-36, 2.
[18] Kweon, D., Kim, Y. (2018), “Interpretation of Turn-to-turn Insulation Fault by Dissolved Gas Analysis”. IEEE Transactions on Dielectrics and Electrical Insulation, vol. 25, no. 4, pp. 1560-1566.
[19] Hamrick, L. (2009), “Dissolved gas analysis for transformers”. Neta World, pp.01-04.
[20] Babukutty, S., Khule, S. (2019), “Combined Dissolved Gas Analysis: A Prescient Methodology for Recognizing Faults in Transformer by MATLAB GUI”. International Research Journal of Engineering and Technology (IRJET).
IJERTV9IS110242 www.ijert.org