
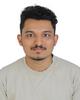
- Open Access
- Authors : Mr. Jouhar C, Mr.Riyas P, Mr. Mohammed Dilshad P, Mr. Mohammed Fahis M, Mr. Mohammed Shamnad Kv, Mr. Muhammed Busthan T
- Paper ID : IJERTV14IS030047
- Volume & Issue : Volume 14, Issue 03 (March 2025)
- Published (First Online): 18-03-2025
- ISSN (Online) : 2278-0181
- Publisher Name : IJERT
- License:
This work is licensed under a Creative Commons Attribution 4.0 International License
Robot for Rescuing Victims from Borewell
Mr. Jouhar C Mr.Riyas P
Assistant Professor Assistant Professor
Mr. Mohammed Dilshad P
Department of Electrical and
Department of Electrical and Department of Electrical and Electronics Engineering Electronics Engineering Electronics Engineering
Mr. Mohammed Fahis M Mr. Mohammed Shamnad Kv Mr. Muhammed Busthan T Department of Electrical and Department of Electrical and Department of Electrical and Electronics Engineering Electronics Engineering Electronics Engineering
MEA Engineering College, Vengoor, Perinthalmanna, India
Abstract Borewell accidents are a serious concern, often leading to tragic outcomes due to the difficulty in rescuing trapped individuals. This project proposes an innovative robotic system designed to assist in the safe retrieval of victims from borewells. The system is equipped with an Arduino Uno-based control mechanism, an ESP32 CAM module for live monitoring, various sensors for victim assessment, and robotic gripper arms for rescue operations. The entire system is controlled via a web page, enabling real-time intervention.
Keywords Borewell rescue, Arduino Uno, ESP32 CAM, heartbeat sensor, ultrasonic sensor, temperature sensor, robotic gripper arms, motor drives, servo motor, web-based control, real-time monitoring, automation.
I. INTRODUCTION
Since India is an agricultural nation, groundwater provides the majority of its farmers with water. Groundwater is being investigated by drilling bore wells. The only explanation for the current awful situation is that bore wells frequently remain uncovered after producing water, giving kids the chance to fall into them by accident. A terrible occurrence happened lately in India when a child became stuck after falling into a hole made by a four-exposure bore well. Because open borewells are frequently left exposed after water extraction, borewell accidents have grown to be a major concern, especially in developing nations. Rescue efforts are very difficult because children and small animals often fall into these narrow, deep tunnels. Traditional rescue techniques involve digging a parallel pit to reach the trapped victim, which is a labor-intensive, time-consuming, and high-risk process. These techniques frequently result in delays that reduce the chances of a successful rescue, sometimes leading to tragic outcomes. Saving a child takes more than one da. Even a small chance might reduce the chances of saving the child. Bore wells are often left exposed in various locations after being dug. Many children have died in these abandoned bore wells. Generally speaking, children's reckless and fun conduct is what causes this kind of catastrophe. Digging a parallel trench next to the bore well is the conventional method of saving the youngster. This approach of rescuing the trapped child is risky, time-consuming, and challenging. Robotic rescue systems have been put out as a cutting-edge
substitute for conventional rescue methods in order to overcome these issues. A borewell rescue robot is made to maneuver through the narrow opening of a borewell, use real- time monitoring to determine the victim's status. Numerous modern technologies are included into this robotic system, such as an Arduino Uno for system control, an ESP32 CAM module for live visualization, and numerous sensors, such as temperature, Heart Beat, and ultrasonic sensors, to track the victim's condition. The ESP 32-powered "Robotic Device For Borewell Rescue" is a technological solution made to increase the Reliability and safety of rescue operations when individuals fall into open borewells, an issue that is frequently encountered in rural regions. The problems of time consumption and the less chance of a successful rescue are addressed by the suggested remedy. This system utilizes the ESP32 microcontroller and Internet of Things (IoT) technology to monitor borewells, collect data, transmit it to a central platform, and provide real-time alerts, and automation for faster and more effective rescue operations with Arduino uno. It is energy-efficient and scalable for monitoring multiple borewells. In the proposed method mechanical system moves inside the borewell and moves its gripper arm with the user commands given and also equipped with sensors like ultrasonic sensor, gas sensor, and heart beat sensor. The borewell rescue robot offers remote operation via a web-based interface, allowing teams to monitor and control it safely from a distance. This reduces risks for rescuers and enables precise maneuvering inside the borewell. Real-time data acquisition ensures quick responses to environmental changes, aiding in critical decision-making. This technology marks a major advancement in emergency rescues, providing a faster, safer, and more efficient alternative to traditional methods. Future enhancements, such as AI integration and improved robotic gripping, can further revolutionize borewell rescues, increasing success rates and saving lives
-
SITUATION ANALYSIS
Borewell rescue operations are challenging because to limited oxygen supply, narrow borewell construction, low vision, and time-consuming manual techniques. Traditional techniques, including digging parallel trenches, are risky and time-consuming, sometimes resulting in delays and increasing the likelihood of equipment breakdowns and cave-
ins.Robotic rescue systems provide an efficient, automated solution that ensures timely and secure rescues thanks to their advanced sensors, remote control, and real-time video surveillance. Borewell rescue robots offer a safer, faster, and more reliable.
The rest of the paper is organized as follows ,chapter 2 discusses the litrature overview,chapter 3 discusses problem ststement snd objectives in the borewell rescue process,chapter 4 mentioned details of the proposed borewell rescue project,chapter 5 includes methodology and results,and chapter 6 describes the conclusion.
-
OVERVIEW OF KEY ASPECTS OF THE BOREWELL RESCUE ROBOT
The robotic arm is a crucial component of the borewell rescue robot, ensuring precision and control in retrieving trapped victims. It is equipped with servo motors for smooth movement and a gripper mechanism designed for safe handling. Integrated sensors provide real-time feedback on pressure, positioning, and victim condition, ensuring a secure and injury-free rescue. The arm's modular adaptability allows it to function in various borewell diameters and conditions, making it suitable for different rescue scenarios. Future AI- powered automation will further enhance efficiency, adaptability, and response time, making the rescue process safer and more effective
-
Servo Motor in Borewell Rescue Robot:
The servo motor ensures precise movement of the robotic arm and gripper using positional feedback. Its PWM control allows a firm yet gentle grip, while high torque and compact design enable smooth operation in confined spaces. The real- time feedback system prevents excessive force, ensuring safe victim extraction. Future AI integration will enhance its efficiency and adaptability
-
Mechanically Actuated Gripping Arms:
The gripper mechanism securely holds and safely retrieves the trapped victim using servo-controlled gripping arms for precise movement and controlled force. Pressure-sensitive sensors adjust the grip in real time, preventing excessive pressure and ensuring a firm yet gentle hold. The servo mechanism enables smooth and stable operation, avoiding jerks or instability dring rescue
-
Advanced Sensors Used:
The borewell rescue robot uses sensors for precision and safety. The heartbeat sensor tracks the victims pulse, while the ultrasonic sensor measures depth and detects obstacles. The temperature sensor monitors conditions to prevent risks, and the ESP32 CAM provides live video streaming for remote decisions. Pressure sensors in the gripper ensure a secure, injury-free hold, enhancing rescue efficiency and safety
-
Modular Adaptability in the Borewell Rescue Robot:
The borewell rescue robot features modular adaptability, allowing components like the robotic arm, gripper, and sensors to be adjusted, replaced, or upgraded based on borewell conditions. This design enables easy integration of advanced technologies such as AI-powered automation without a complete system overhaul. It improves navigation,
obstacle avoidance, and victim positioning, ensuring a faster, safer, and more effective rescue in various scenarios
-
AI-Powered Automation:
The borewell rescue robot uses AI-powered automation to improve efficiency, decision-making, and adaptability. It analyzes conditions, detects obstacles, and assesses the victims status using real-time sensor feedback. AI enables precise robotic movements, grip adjustments, and obstacle navigation, ensuring a safe and injury-free rescue. Future advancements will further enhance autonomous rescue operations, minimizing human intervention for faster and safer rescues
-
ROBOT FOR RESCUING VICTIMS FROM BOREWELL: AN LITERATURE OVERVIEW
The rise in borewell accidents, especially those involving children, has underscored the need for efficient rescue solutions. Traditional methods, such as digging parallel pits, are often slow and may be obstructed by geological challenges, decreasing the chance of success. Borewell rescue robots provide a faster and safer alternative, directly accessing the victim within the borewell using a compact and agile design that navigates confined spaces effectively [1]. To enhance rescue operations, borewell rescue robots incorporate essential components like cameras, sensors, manipulator arms, and oxygen supplies. Cameras, including infrared and night-vision options, allow real-time visualization, which helps rescuers locate and monitor the victims condition [2]. Ultrasonic and infrared sensors map the borewells interior, assisting in navigation and obstacle avoidance, while manipulator arms with secure holding mechanisms, such as 4-jaw chucks or circular clamps, allow for careful grasping and lifting of the child to minimize injury [3]. Control systems for these robots often rely on microcontrollers like Arduino or ESP32, enabling precise movement and positioning. Remote monitoring and control are facilitated by connectivity solutions such as Bluetooth and IoT applications, allowing safe operation from outside the borewell [4]. Additionally, the role of advanced imaging technologies and sensors in real-time monitoring during rescues was examined, stressing the necessity of effective victim location and condition evaluation through enhanced imaging capabilities [5]. A smart borewell rescue system powered by an ESP32 microcontroller manages motor drivers, cameras, and sensors. It features a robotic arm for retrieval, teleconferencing for communication, and temperature monitoring, all controlled in real-time via a mobile application. [6]. Despite these advancements, borewell rescue robots still face certain challenges. However, recent improvements in autonomous and semi-autonomous navigation, enabled by machine learning algorithms, allow robots to autonomously identify the safest route and adjust in real time. This capability has proven effective in field tests conducted in simulated borewell environments, which allow engineers to refine robot reliability and assess practical performance [7]. Further advancements in borewell rescue robots could include thermal imaging, which would improve victim detection accuracy, and long-range communication options like satellite links to extend operational reach in remote areas. Additionally, increased adaptability to handle
various borewell configurations and environmental conditions will further enhance these robots' versatility and effectiveness, ultimately providing a faster and safer alternative to traditional methods [8]. Applications for borewell rescue robots extend beyond child rescue operations and can be modified for use in hazardous environments, such as radioactive zones or underwater operations, where human risk is high [9]. Continuing to develop these rescue technologies promises not only to improve outcomes in emergency responses but also to expand their use in other fields requiring high precision and safety in confined or hazardous spaces [10].
-
PROBLEM STATEMENT AND OBJECTIVES
Borewell accidents, especially involving children, present a serious rescue challenge due to the narrow, deep, and inaccessible nature of borewells. Traditional rescue methods, such as digging parallel pits, are time-consuming, labor- intensive, and risky for both the victim and the rescue team. The lack of real-time monitoring, precise maneuvering, and controlled extraction mechanisms further complicates the process, often reducing the chances of a successful rescue. To address these challenges, this project aims to develop an advanced robotic borewell rescue system that integrates automation, real-time monitoring, and precision control to improve the efficiency and safety of rescue operations. The system is designed to assess the victims condition using an ESP32 CAM module and integrated sensors for heartbeat, temperature, and environmental monitoring. A servo- powered robotic gripper ensures safe and controlled extraction, adjusting its grip based on real-time pressure feedback. The robot operates through a web-based interface, allowing for remote control and real-time decision-making to minimize human risk. Additionally, the modular adaptability of the system enables it to function in borewells of varying depths and diameters, making it a versatile and scalable solution. The inclusion of AI-powered automation further enhances the system by enabling autonomous navigation, obstacle detection, and intelligent victim retrieval, significantly reducing rescue time. By integrating advanced robotics, sensor technology, and real-time monitoring, this project aims to revolutionize borewell rescue operations, ensuring a faster, safer, and more effective approach to victim retrieval
-
DETAILS OF THE ROBOT FOR RESCUING VICTIMS FROM BOREWELLS
-
-
This section outlines the borewell rescue system's block diagram, the hardware components utilized in constructing the robotic rescue mechanism, and the software details governing its operation
-
BLOCK DIAGRAM
The borewell rescue robot is designed with an automated control system that integrates multiple components to ensure efficient victim retrieval. The block diagram represents the key elements of the system and their interactions, ensuring smooth operation. At the core of the system is the Arduino
Uno microcontroller, which acts as the central processing unit that coordinates the functioning of various components. It receives input from multiple sensors, including the heartbeat sensor, ultrasonic sensor, and temperature sensor, which continuously monitor the victims health status and environmental conditions inside the borewell. The ultrasonic sensor helps measure the depth of the borewell and detects any obstacles, while the temperature sensor monitors the heat levels inside the borewell to assess any risk factors. For visual monitoring, the ESP32 CAM module provides real-time video streaming to a web-based interface, allowing remote operators to assess the situation and control the robot accordingly. The servo motor-driven robtic gripper arm is responsible for securely gripping and extracting the trapped victim. To ensure safety, pressure sensors in the gripper regulate the force applied, preventing injuries during retrieval. The robotic system is powered by motor drives and servo motors, which control the vertical movement of the robot inside the borewell. These motors allow precise adjustments to the robots position, ensuring that the gripper arm can accurately reach and secure the victim. The entire system is remotely operated through a web-based control panel, which enables rescue teams to monitor sensor data, adjust the robotic arm, and oversee the extraction process in real time Furthermore, AI-powered automation enhances the robots ability to navigate obstacles, adjust grip force, and optimize movement based on real-time data. The block diagram illustrates the flow of information from sensors to the control unit, followed by execution through actuators like servo motors and motor drives. This seamless integration of hardware and software ensures a safe, efficient, and reliable rescue operation, making the borewell rescue robot an advanced and effective solution for handling emergency scenarios. figure.1 mentioned the block diagram of the rescue operation with components
Fig 1. Block diagram of borewell rescue operation
-
CIRCUIT DIAGRAM
The circuit diagram of the borewell rescue robot represents the interconnection of key electronic components, ensuring a smooth and efficient rescue operation. The Arduino Uno microcontroller serves as the central processing unit, coordinating signals between input sensors and output actuators. It is connected to various sensors, including the heartbeat sensor, ultrasonic sensor, and temperature sensor, which continuously monitor the victims condition and environmental factors inside the borewell. These sensors
Provide real-time data to the microcontroller, enabling precise decision-making. The esp32 cam module, powered by a regulated power supply, provides live video streaming, allowing rescue operators to visually assess the borewells interior. The servo motors, controlled by pwm (pulse width modulation) signals from the Arduino, operate the robotic gripper arm, enabling it to reach, hold, and extract the trapped victim with controlled force. Additionally, motor drivers regulate the vertical movement of the robot, allowing it to descend and ascend safely within the borewell. A 12v battery powers the entire circuit, with voltage regulators ensuring stable power distribution to each component. The web-based control system receives sensor data and camera feed, allowing remote operation of the robotic arm and movement control. Ai-powered automation further enhances decision- making by adjusting the robots grip force, movement, and obstacle avoidance dynamically. The circuit diagram illustrates the structured flow of electrical signals between components, ensuring safe, efficient, and precise execution of rescue tasks. By integrating real-time monitoring, remote control, and automation, this system enhances the reliability and success of borewell rescue operations. Figure 2 displays the circuit design of the proposed work.
Fig 2. Circuit design of borewell rescue operation
The circuit diagram plays a vital role in the overall functionality and efficiency of our borewell rescue robot. It ensures proper integration of all electronic components, enabling smooth communication between sensors, motors, and controllers. By utilizing the Arduino Uno and esp32 cam module, we achieve precise control and real-time monitoring,
which are crucial for rescue operations. The incorporation of sensors such as heartbeat, ultrasonic, and temperature sensors enhances the systems ability to assess the victims condition and environmental factors. Additionally, the use of motor drivers and servo motors enables the robotic arms to perform gripping and lifting tasks effectively. A well-structured power supply circuit guarantees stable voltage distribution, preventing malfunctions during operation. Overall, the circuit diagram serves as a blueprint for constructing a reliable, efficient, and innovative rescue system, contributing to improved safety and success in borewell rescue missions.
V.METHODOLOGY &RESULT OF ROBOT RESCUE OPERATION
-
METHODOLOGY
The methodology for the borewell rescue robot involves a systematic approach to designing, developing, and implementing an automated robotic system for victim retrieval. the process includes hardware integration, software development, sensor deployment, and real-time monitoring to ensure an efficient, precise, and safe rescue operation.
-
System Design and Component Selection:
The first step involves designing the mechanical and electronic framework of the robot. Essential components such as the Arduino Uno microcontroller, ESP32 CAM module, servo motors, motor drivers, ultrasonic sensor, heartbeat sensor, and temperature sensor are selected based on functionality and efficiency to ensure real-time monitoring and precise control.
-
Circuit and Mechanical Assembly:
The electronic components are wired and connected to the Arduino Uno, ensuring stable communication between sensors, actuators, and the control system. The robotic gripper arm is integrated with servo motors and pressure sensors to ensure precise victim handling. The motors and motor drivers are installed to enable controlled vertical movement of the robot inside the borewell.
-
Sensor Integration and Data Acquisition:
Various sensors are implemented to continuously monitor the victims condition and environmental factors. The heartbeat sensor tracks the victims pulse, the ultrasonic sensor measures borewell depth and obstacles, and the temperature sensor records environmental conditions. The ESP32 CAM module provides real-time live streaming for remote access
-
Control System and Web-Based Interface:
A web-based control interface is developed to allow remote operation of the robot. The interface receives sensor data and live video feed, enabling operators to adjust the robotic arm, control the motors, and make real-time decisions. The robot is programmed using Arduino IDE to process sensor inputs and execute motor commands efficiently.
-
AI-Powered Automation and Decision-Making:
AI algorithms are incorporated to enhance automation, allowing the robot to navigate obstacles, adjust grip force, and optimize movement dynamically. This reduces human intervention and improves rescue efficiency.
-
Testing and Optimization:
The system undergoes multiple test runs in controlled environments to ensure sensor accuracy, motor efficiency, and stability during rescue operations. Adjustments are made to optimize the robotic arms movement, gripping mechanism, and real-time data transmission.
-
Deployement and Execution:
Once testing is successful, the robot is deployed in real-world scenarios, where it is inserted into the borewell, guided using the remote interface, and used to securely grip and retrieve the victim while continuously monitoring vital signs and environmental condition.This structured methodology ensures that the borewell rescue robot operates efficiently, accurately, and safely, making it a reliable solution for emergency rescue operations
-
-
RESULTS &DISCUSSION
This section explores borewell rescue operations using robotic arms, highlighting the effort and expertise required. We've gathered all necessary components and will program the arduino uno via arduino ide to control sensors and a camera module. This project demonstrates our commitment to innovation while improving safety and efficiency in rescue missions.
in this project we have hosen components such as arduino uno(model: at mea328p,operation voltage:5v) , esp32 cam module(2 mega pixel ,ov2640) ,motor driver(l298n), temperature sensor(dht11), gas sensor, ultra-sonic sensor, heart beat sensor, robotic gripper arm (to pick the child from borewells), and servo motor (tower pro servo motor, 180 degree rotation, operating voltage :4.8-7.2, operating speed : @ 4.8 v :0.20sec/60 degree, @6.6 v:0.16sec/60 degree, stall torque:@4.8 :10 and @6.6v:12 , gear type: semi metal ) and gear motor (10 rpm,12v,75 g) for our proto type model.
so in this specifications of the components the model is capable for rescuing the child from borewell who have weighted maximum 5kg.for further improvement and increase the holding capacity of rescue mission, want to improve and change the specification of components like gear motor and others.from the changes of the specification of the servo motor, and gear motor we can improve robotic gripper arm holding and weighing capacity in efficient manner.the rotation speed and rescue operation controlled by the arduino
uno, esp 32 cam module, servo motor and gear motor with robotic gripper arms.
in figure 3 shows the robotic gripper arm created by 3d printing capable for holding ,gripping with the commands from sensors and controlling web servors. The motor driver ic we have used in this proposed model. figure 4 outlines the web servor and controlling page ,wich controlled all operation of rescue process ,includes start ,stop,up,and down in controlled manner. arduino uno programmed by arduino ide software. and finally the figure 5 showcase the esp32 cam module for visualized representation of inside visual from borewell. that will be shown in the web servor page and helps the better operation and immediate action. also, we have used the different type of sensors for different application for the better and immediate action.in this proposed model we use the4( 3.7v lithium iron) cells.and it will be seriesly connected
,two parallell combination for provide better effective work. Especially the gear motor makes the powerfull role in this project.because carrying load capacity of robotic gripper arm will decide from the rating of the gear motor.rpm of the gear motor changes will be directly affect the load carryingcapacity of robotic gripper arm.if the rpm will be reduced ,the torque will be increaced,and that results the weight loading capacity increases.
finally we have to say that, we represent a prototype model of robot rescuing victims from borewells which capable to rescue a 5kg weight. from the appropriate change in the gearmotor and other components we have to rescue any victims with necessary weight. reducing the rpm of the gear motor increases torque, which enhances load carrying capacity of gripper arms and handle heavier load effectively.
Fig 3. Robotic arm
Fig 4. Web server control
Fig 5. ESP 32 Cam module
VI CONCLUSION
The development and utilization of robotic devices for borewell rescue operations represent a significant advancement in search and rescue technology. These devices offer a multitude of advantages, including enhanced safety, quicker response times, remote operation, and the ability to access confined and hazardous spaces while reducing the risks to human rescuers. The real-time data feedback, adaptability to challenging environments, and the potential for data collection and analysis further underscore their value. Human life is valuable, and we have a thorough and well- planned plan in place to save kids who fall into bore wells. In order to save the lives of children trapped in bore wells, we have built equipment that can handle a variety of situations that might occur during a rescue operation. Accidents involving bore wells have claimed numerous lives in the last ten years because rescue operations are difficult and time- consuming. But because to advanced technology, strong motors, and mechanical arms, this procedure can now be completed more quickly. Numerous lives could be saved by the suggested remedy.
In conclusion, the creation and application of a dual-arm mobile robot holds great promise for improving difficult rescue missions. This robot can function well in challenging situations since it is outfitted with temperature and ultrasonic sensors and is made to resemble human movement. Because it can identify any thermal irregularities or any fire threats, the temperature sensor is essential to maintaining safety. Additionally, by identifying impediments and guaranteeing a safe path during rescue, the ultrasonic sensor helps the robot maneuver through crowded and limited locations more precisely. This creative method has the potential to completely transform rescue operations while guaranteeing the security of the robot and any personnel participating. The borewell rescue robot is an effective solution to mitigate risks associated with conventional rescue operations. By integrating sensor technology, robotics, and web-based control, the system enhances safety and efficiency. This robotic approach offers several advantages, including faster response times, real-time monitoring, precise victim handling, reduced human risk, and adaptability to various borewell depths and conditions. However, there are also some limitations, such as high initial costs, dependency on internet connectivity for remote control, and potential challenges in navigating unpredictable borewell environments. Despite these challenges, further improvements, such as AI-based decision-making and improved robotic grip mechanisms, can enhance its performance in real-world scenarios, making borewell rescues more reliable and effective. The continued advancement of robotic technology in rescue operations will help save lives and provide a safer alternative to traditional rescue techniques. The borewell rescue robot will continue to evolve with AI integration, enabling autonomous victim identification and handling for improved decision-making. Enhanced robotic arms with soft gripping mechanisms will ensure safer and more delicate rescues. Improved camera resolution will provide better visibility inside deep borewells, enhancing real-time monitoring.
REFERENCES
-
Kale, P. A., Kamble, N. S., and Mane, T. S., "Robotic Device for Borewell Rescue Operation," IJCRT, Volume 12, Issue 5, 2024.
-
Arunkumar, K., Kumaran, T., Sravanthi, G., and Vijayanandh, R., "Design and Fabrication of Semi-Automatic Child Retraction Mechanism from Bore Well," AIP Conference Proceedings, 2022.
-
Zheng, Y., Wu, Z., and Ma, C., "Structural Optimization of Small- Diameter Deep Well Rescue Robot based on Hyperworks-Optistruct," Manufacturing Technology, 2022.
-
Sui, D., Wang, T., Zhao, S., et al., "An Enveloping Soft Gripper with High-Load Carrying Capacity," IEEE Robotics and Automation Letters, 2021.
-
Rajarathnam, D.R.P., Lakshmi Raj Thilak, R., Rithvik, K., Vignesh, G., & Mohamed Marsook Hameed, S.H., "Borewell Rescue Robot," International Journal of Modern Research in Engineering and Technology, 2018.
-
Kaur, P., Kaur, R., & Singh, G., "Pipeline Inspection and Borewell Rescue Robot," International Journal of Research in Engineering and Technology, 2014.
-
Karthik, S., Mohankumar, D.K., Chandramohan, K., & Udaiyakumar, K.C., "Investigation and Analysis on Child Rescue System from Open Bore Well," IOP Conference Series: Materials Science and Engineering, 2020.
-
Vyavahare, V. A., Popalghat, P. P., et al., "Borewell Rescue Robot Using Bluetooth," International Journal of Engineering Research, 2020.
-
Vishnu Vardhan, Y., Rao, P. S., Babu, N. M., and Babu, G. M., "Borewell Rescue Robot," Pramana Research Journal, Volume 9, Issue 4, 2019.
-
Kaimal, A.N., & Prasad, D., "Design and Development of Robot for Rescue Operations for Bore-Well Victims," International Journal of Mechanical and Production Engineering Research and Development, 2020