
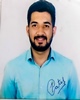
- Open Access
- Authors : Jignesh Vinod Patel
- Paper ID : IJERTV10IS090088
- Volume & Issue : Volume 10, Issue 09 (September 2021)
- Published (First Online): 21-09-2021
- ISSN (Online) : 2278-0181
- Publisher Name : IJERT
- License:
This work is licensed under a Creative Commons Attribution 4.0 International License
Robotic Manipulator (Robotic Arm)
Jignesh Vinod Patel
Instrumentation and Control Engineering Vishwakarma Institute of Technology Pune, India
Abstract This paper presents the design of a robotic manipulator which simulates movement to the grip and an object is also known as Robotic Arm. The Manipulator arm is made up of a finite number of individual rigid segments, each rigid segment is called as link. This arm is controlled by Arduino UNO, the robot can be implemented in the hazardous area for material handling and other productive work and can be also used in industries. To examine torque, we consider a prototype module for the robotic manipulator and simulate the task given to it. This paper concludes with some possible applications of 5 Degrees of freedom. The robotic manipulator mechanism is based on end effector to the robotic arm.
Keywords Robotic Manipultor, Arduino UNO, Degree of Freedom, End Effector, Servo motor, Forward Kinematics, Reverse Kinematics.
-
INTRODUCTION
Nowadays, Robotic Arms are used in various industries and operation in a hazardous environment. The robotic manipulator is very expensive due to its accuracy and precision. The robotic manipulator can reduce human work to a greater extent which in turn can lead to faster progress of industry. The robotic arm can be evaluated, such as backlash, payload, speed, repeatability, compliance, human safety, and cost. The forward and reverse kinematics are the day-to-day methods used in robotic industries. A robotic arm is a type of mechanical arm, usually programmable, with the arm may be the total mechanism or maybe the part of a more complex robot. Robotics Kinematic deals with study of motion without considering the forces acting on the robot structure. Forward Kinematics required position and orientation are determined from a given set of joint angles. Inverse Kinematics Joint angles of all joints in the arm are determined from position and orientation.
Human safety is difficult if the manipulator is to be used close to the paper. Arduino UNO is used as the brain of the robotic arm. The Arduino is programmed in such a way that the robot manipulator is controlled. We are getting smarter some of the earliest Robots of the mid-20th century were devices mostly controlled nearby humans or were simple tools able to perform the limited task.
-
LITRATURE REVIEW
-
A survey on Arduino Controlled Robotic Arm by Ankur Bhargava.
In this paper, a 5 Degree of Freedom (DOF) robotic arm has been developed. It is controlled by the Arduino Uno microcontroller which accepts input signals from a user a set of potentiometers. The Robotic Manipulator is made from four rotary joints and an end effector, where rotary motion is provided by a servomotor. Each link has been first designed using Solid works Sheet Metal Working
Toolbox and then fabricated using a 2mm thick Aluminum sheet. The servomotors and links thus produced assemble.
-
Review on development of industrial robotic Manipulator by Rahul Gautam
This selective operation robotic control method is needed to be overcome the problem such as placing or picking objects that at distant from the worker. The robotic Manipulator has been developed successfully as the movement of the robot can be controlled precisely. It is expensive to change the cable and therefore the design to reduce the friction on a table, is crucial to increase the time between maintenance.
-
Survey on Design and Development of competitive low-cost Robot Arm with Four Degrees of Freedom by Ashraf Elsassian
In this paper, the representation of the design, development, and implementation of the robot arm is done, which can perform simple tasks, such as light material. The robotic arm is designed and made from acrylic material where servo motors are used to perform links between arms. The servo motors consist of an encoder so that no need to use a controller. However, the rotation range of the servo motor is less than 180º, which greatly decreases the region reached by the arm and the possible positions. The design of the robot Manipulator was for four degrees of freedom. The end effector is not considered while designing because a readily available gripper is used as it is much easier and economical to use a commercial
-
-
WORKING PRINCIPLE
The robotic manipulator works on the principle of electrical input energy to perform some mechanical work effectively with the help of some automation and program-based. Linear joint links move in a linear fashion considering their joint when actuated. Rotary joint links move in rotary fashion concerning its joint when actuated. The robotic arm consists of a servo motor which is used for angular rotations. This servomotor used works on the principle of Fleming's right- hand rule and is controlled using an Arduino circuit board.
Degrees of freedom is defined as the ability of a joint to produce linear or rotary movement when actuated. The number of DOF for a robot is equal to the number of joint axes in the robotic arm.
-
Components
-
Servo Motor
The two major servo motors are used in the robotic arm, one for the base movements and two on the side of the base plate two transmit the motion through the various links to the arm. The servo motor is bolted to the base plate it keeps it fixed and avoids vibrations during the actual operations.
A rotary actuator is consisting of a suitable motor coupled to a sensor for position feedback. It requires a relatively sophisticated controller, often a dedicated module designed specifically for use with servo motors.
-
Connectors
The device that is used to join electrical terminations and create an electrical circuit is called an electrical connector. These are electro-mechanical devices consist of plugs called male-ended and jacks called female- ended. Connection may be temporary, as for portable equipment, require a tool for assemble and removal, or serve as a permanent electrical joint between two wires or devices. In our project, we used only the male-to-male connectors or the plugs for the connections.
-
Motor Driver L293D
The L293D is a popular 16-Pin Motor Driver IC. As the name suggested is mainly used as drive motors. A single L293D IC is capable of working two DC motors at the same time; also, the direction of these two motors can be controlled independently. If you have servo motors that have operating voltage less than 36V and operating current less than 600mA, which are controlled by digital circuits like 555 timers, digital gates, Op-Amp, Micron rollers like Arduino, PIC, ARM.
-
Arduino UNO
By sending servo signals a servo
control can be obtained, a series of repeating pulses variable width where either the width of the pulse (most common
-
-
Design
The types of Robotic Manipulator joints are
modern hobby servos) or duty cycle of pulse train and determines the position to be achieved by the MG995. The controller integrates the digital command signal into the analog parameter like the movement of the servo motor shaft.
With the help of the controller, we can upload the program regarding the movements of the servos. By using the controller, we can control the number of servos at a time and synchronize the operation of the servo for -operation of any servo in any sequence and -to synchronize actuation of four servos sequentially in a loop programmed.
rotary, Prismatic, Hooke, spherical. The Rotary the angle theta about the z-axis, the prismatic for linear dsplacement d axis of joint z the 2D Freedom described by yaw and pitch. The spherical is described by 3 rotation access wrist and shoulder.
A lower pair joint is the joint in which two contacting surfaces can slide over with one another in a rotary or linear manner. Revolute joint 1 DOF, Prismatic joint 1 DOF, Screw joint 1 DOF, Cylindrical joint 2 DOF, Planar joint 3 DOF, Spherical joint 3 DOF. The wrist motion consists of 3 that is Yaw Rotary motion executed about axis. Causes movement in right and left direction. The pitch rotary motion executed about on axis. And Causes movement up and down directions. Roll Rotary motion executed about axis.
-
Characterization
Most of the control is based on "servo libraries". By them, we can control servo motors as they provide an object-oriented interface and Support simultaneous steppers, with independent concurrent stepping on each Stepper motor. this library Firstly finds the servo that will take the longest time to move and adjust the other servo speeds so they all will arrive at the same time of the longest time. The next step is to configure the servo name (PINS) function, initialize and define the position by Servo. After that adding the desired positions into array form called "positions", which is used with Servo. Move to (positions) function to allocate the desired position(angle).
-
-
PROPOSED BLOCK DIAGRAM
-
RESULTS AND DISCUSSIONS
The base servo motor successfully rotates from 0 to 180 degrees and another that is motor placed in the elbow of the robot is successfully rotated from 0 to 360 degrees of angle.
-
LIMITATIONS
Any point on this robotic arm can only move along a circular path. Any task involving motion other than circular motion cannot be performed by such a robot. The scope of robots can be extended and limitations can be reduced by adding to the complexity of the robots.
-
FUTURE SCOPE
Robotic Arms have a wide scope of development. Shortly the arms will be able to perform every task as humans and in a much better way. Brain Computer Interface can be used to acquire signals from the human brain and control the arm. The system can work in the same way as a human arm.
-
CONCLUSION
This report presents the design and the development of a robotic arm, which can perform simple tasks, such as light material handling. The robotic arm is designed and built from aircraft-grade aluminum material where servo motors were used to perform arm movements. The design of the robotic arm is limited to the four degrees of freedom the design of a robotic arm has been complete. The prototype was
Built and confirmed functional. This system would make it easier for men to unrivaled the risk of handling suspicious objects which could be hazardous in its present environment and workplace. Complex duties would be achieved faster and more accurately with this design.
ACKNOWLEDGMENT
The authors would like to appreciate and personally thank Prof. P.M. kanjalkar for their significant contribution in developing the model of the robotic manipulator.
REFERENCES
-
Kurt E. C, Shang Y, A Geometric Approach for the Robotic arm kinematics with hardware design, Electrical Design and implementation, Journal of robotics, 2010, Volume 10.
-
Rahman A, Khan A. H, Dr. Ahmed T, Md Sajjad M, Design analysis and Implementation of Robotic arm The Animator, American Journal of Engineering Research, 2013, Volume 2, Issue 10.
-
Gautam R, Gedam A, Zade A, Mahawadiwar A, Review On Development of Industrial robotic arm, IRJET, March 2017, Volume 4, Issue 3.
-
Omijeh B. O, Uhunmwangho R, Ehikhamenle M, Design Analysis of a remote-controlled "Pick and Place" Robotic Vehicle, International Journal of Engineering Research And Development, 2014, Volume 10, Issue 5.
-
Katal G, Gupta S, Kakkar K, Design and Operation of Synchronized Robotic Arm, IJRET, Aug 2013, Volume 2, Issue 8.
-
Gunasekaran K, Design and analysis of articulated Inspection arm of a robot, International journals for trends