
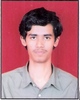
- Open Access
- [post-views]
- Authors : Abhijeet S. Kulkarni , Vishal Kamble , Sumedh Nakade , Akshaya Kamdi
- Paper ID : IJERTV10IS070120
- Volume & Issue : Volume 10, Issue 07 (July 2021)
- Published (First Online): 22-07-2021
- ISSN (Online) : 2278-0181
- Publisher Name : IJERT
- License:
This work is licensed under a Creative Commons Attribution 4.0 International License
Role of Building Information Modelling in Construction
Abhijeet S. Kulkarni Vishal Kamble Sumedh Nakade
Final Year B.E. Civil Engineering Savitribai Phule Pune University Pune, India.
Abstract:- Building Information Modelling BIM is becoming a better-known established collaboration process in the construction industry. Owners are increasingly requiring BIM services from construction managers, architects and engineering firms. Many construction firms are now investing in BIM technologies during bidding, preconstruction, construction and postconstruction. The goal of this project is to understand the uses and benefits of BIM for construction managers and examine BIM based scheduling. There are two objectives to this project. First is to identify the current uses of BIM in the Architectural / Structural / Engineering / Construction / Facility Management industry to better understand how the BIM-based build to design and design to build concepts can be used by construction managers under the Construction Management at Risk project delivery system. Second, a focus is placedon analyzing 3D BIM as well as BIM based scheduling.
First, the research identified the uses of Building Information Modelling for preconstruction, construction and post construction phases. Then, the project examined the uses and benefits of BIM in the construction of a research facility. Subsequently, a prototype 3D Building Information Model was created and studied. Furthermore, the BIM-based schedule wasintegrated to the 3D model. Finally, the project concluded with an analysis on the use, advantages and setbacks of BIM and its tools.
Prof. Akshaya Kamdi
-
E. Structural Engineering Universal College of Engineering and Research
Pune, India.
-
INTRODUCTION
The construction industry has experienced a gradual decrease in its labour productivity since 1960s. in a meantime, non-farm industries such as manufacturing industry have increased their labour productivity. The reduction of labour productivity in construction industry requires more labour hours per contract amount. This indicates construction industry is lacking the developmentfor labour saving ideas.
The main cause of lack of productivity in construction industry are related to its fragmented naturedue to tradition projects delivery, approach, traditional use of 2D Computer Aided Drafting (CAD) technology and size of construction firms. The traditional construction projects delivery approach, Design Bid Build, roles of participation during design and construction phases. Thearchitectural, structural engineers have long techniques to decrease the project costs and increase productivity and quality and reduce delivery time BIM simulates the construction projects in virtual environment. With BIM technology, an accurate virtual model of building is digitally constructed. When completed, BIM contains geometry and relevant data needed to support the design, procurement, fabrication and activities required to realize the building. After completion, it can be used for maintenance purpose.
A BIM characterizes the geometry, spatial relationship, geometric information, quantities and properties of building elements, cost estimation, material inventories, project schedule model describes the entire building life cycle. As a result, quantities and readily material can be extracted. Construction documents such as drawing, procurements details, submittal processes and other specifications can be easily interrelated.
It is important to note that BIM is not just software; it is also process and software BIM means not only using 3D intelligent models but also making changes in work flow and delivery process. BIM represents new paradigm, one that encourages integration of roles of all stakeholders on a project. It has the potential to promote greater efficiency and harmony among prayers who, in thepast, saw themselves as adversaries. BIM also supports the concept of integrated project delivery approach to integrate people, systems, and business structures and practices into a collaborative process to reduce waste and optimize efficiency through all phases of project life cycle.
In this project, uses of BIM includes visualization, 3D coordination, prefabrications, construction planning and monitoring, cost estimation and record model were discussed in details. BIM tools further analyzed by developing prototype 3D and 4D house model. The research concludes that although BIM tools do pose some shortcoming such as interoperability issues, use of BIM is verybeneficial to construction managers.
-
BACKGROUND
The section discussed the role and use of BIM from the Construction Management point of view. First Building Information Modelling is reviewed and defined. The uses of Building Information Model, and the Building Information Model software and integrators are also discussed mainly from a construction manager perspective.
Building Information Modelling (BIM) is process and practice of virtual design and construction throughout its lifecycle. It is a platform to share knowledge and communicate between project participants. In other words, Building Information Modelling is the process of developing the Building Information Model.
The BIM is primarily a 3D digital representation of a building and its intrinsic characteristics. It is made of intelligent building components which includes data attributes and parametric rules for each object. For instance, a door of certain material and dimension is parametrically related and hosted by a wall. BIM provides consistent and coordinated views and representations of digital model including reliable data for each view.
-
ORIGIN OF BIM
It is thought that Professor Charles M. Eastman, from Georgia Institute of Technology, coined the term. This theory is supported by the fact that the term Building Information Model is basically the same Building Product Model, a term that professor has used extensively in his book and papers published since the late 1970s. (Product model means data model or information model in engineering).
According to Laiserin and others, the first implementation of BIM was as a Virtual Building Concept by Graph iSOFTs ArchiCAD, first used in 1987.
BIM can be used to increase overall productivity in following ways:
-
BIM can help demonstrate the entire building life cycle including theprocesses of construction and facility operation.
-
Quantities and shared properties of materials can be
easily be extracted.
-
Scope of work can be isolated and defined.
-
Systems, assemblies and sequences can be better
expressed in relativescale with the entire facility or group of facilities.
-
-
OBJECTIVES
BIM is a new promising tool to Architecture, Structural and Construction industry., allowsconstructing building virtually before actual construction on field.
-
To study considerable benefits of BIM and developing a vision for future of BIM in India.
-
To offer improved quality assurance and data
exchange to process for more effective andefficient design.
-
To make effective use of data of the building project
during construction, operation andmaintenance.
-
To display and share design and feasibility studies for
construction.
-
The main objective of BIM is to enhance project
performance and produce better outcome.
-
-
PROBLEM STATEMENT
-
This project shows that how BIM is implementd in construction. In this project planning, analysisand designing of 2D and 3D plan on G+ 3 bungalows. Implementing the interior by the use of softwares. Scheduling of object and placing the material in the model should be operated carefully while making model. Analyzing the model means the loads acted on the structure finding how much load it can take. Dead load, live load, wind load is calculated or analyzed by the use of BIM to know how much load the structure can take. The MEP work means the mechanical, electrical, and plumbing work is designed and analyzed by BIM. Then thefinal stage means rendering and checking the model.
STATEMENT OF PROJECTs
Salient Feature
Utility of building |
Residential building |
Number of stories |
G+3 |
Shape of building |
Rectangular |
Number of staircases |
4 |
Number of lifts |
1 |
Type of structure |
RCC Framed Structure |
Type of wall |
Standard Brick wall |
Geometric details |
|
Floor to floor height |
3.65 m. (144 inch.) |
Height of plinth |
0.61 m. (24 inch.) |
Depth of foundation |
-3.65 m. (-144 inch.) |
Concrete grade |
M25 |
Grade of steel |
Fe415 |
-
PLANNING AND MAKING 2D MODEL OF THEPROJECT:
Civil engineering structures are created to serve some specific functions like human habitation, transportation, bridges, storage etc. in a safe and economical way. Computer aided design means CAD is used to make 2D model of the project. Auto Cad is the traditional way of planning and making of 2D structure plan. Auto cad is used create 2D plan in this project and it is also used tocreate 3D drawing also.
PLAN:
The CAD figure no.1 represents the plan of a G+3 bungalow. The plan clearly shows that it is abungalow. In the bungalow consist of three-room house which occupies entire floor of a block.
The plan shows the details of dimensions of each and every room and type of room and orientation of the different rooms like bed room, bathroom, kitchen, living room etc., all the bed rooms have similar arrangements.
The entire plan area is about 1500 sq. m. There is some space left around the building for parking. In the middle we have small construction which consists of one lift and those who want to fly through lift can use the facility. So, this represents the plan of our bungalow and detailed explanation of remaining parts like elevations and designing
in the next sections. Figure representsthe skeleton structure of the bungalow which is used to carry out the analysis of our bungalow.
All the loadings are acted on this skeletal structure to carry out the analysis of bungalow. This is not the actual structure but just represents the outline of the building in CAD.
-
DEVELOPING THE PLAN AND 3D MODEL WITHTHE HELP OF 2D PLAN:
The main difference between BIM and CAD are that CAD system is usually 2D document, which are created separately and have no intelligent connection between separately created documents. In CAD two lines represent wall. In BIM wall is created in the form of an interactive tool, which has its properties i.e., width, height, demolished or new, interior or exterior, and materials (boards and bricks) etc. The BIM platform assembles all information into one location and cross-links that dataamount associates. There is no link between the data created by CAD.
BIM allows use of a parametric 3D model to auto generate traditional model i.e., plans, sections, elevations, details and schedules. Model produce using BIM software is automatically co-ordinate throughout the project, which eliminates coordination mistakes, improve overall quality of the work.
I. IMPLEMENTING INTERIOR WITH THE HELP OF 2D PLAN:
Tools and features that make up architectures are specifically designed to BIM work flows. By utilizing BIM as oppose to CAD Revit architecture is able to leverage dynamic information in models allowing complex structures to be accurately design in short amount of time. This allows changes made in one part of model to automatically change to other parts of model, thus enhancingthe work flow for architecture users.
1) Procedure:
-
Considering one area for construction, we have
considered Lonavala, Pune (zone 4).
-
According to building bylaws, provision of plot area
and plinth area consideringF.S.I.
-
Provision of setback distances with respect to height
of structure
-
Preparing different plans for different floors, within
the plinth area.
-
Importing individual floors in a separate window and
by using Revit softwaremodeling is used.
-
After the completion of modeling of individual floors,
deleting the unnecessarylayers of imported data.
-
Open a new window and import all the individual
floors in separate levels and all the floors are joined as a single element.
J.ANALYZING THE STRUCTURAL MODEL:
All the loading are acted on the structure to carry out the analysis of the model. This is not theactual structure but just represents the outline of the structure in Revit Structures. A mesh is automatically created for the analysis of these building.
DEAD LOADS:
Dead consist of the permanent construction material loads compressing the roof, floor, wall and foundation systems, including cladding, finishes and fixed equipments. Dead load is the total load of all of the components of the building that generally do not change over time, such as the steel columns, concrete floors, bricks, roofing material etc. In Revit Structures assignment of dead load is automatically done by giving the property of member. In load case we have option called self- weight which automatically calculates weights using the properties of material i.e., density and after assignment of dead load the structure looks red in color.
LIVE LOADS:
Live loads are produced by the use and occupancy of structure. Loads include those from human occupants, furnishing, no fixed equipment, storage and construction and maintenance activities. The required loading condition, loads are presented in terms of uniform area loads, concentrated and uniform line loads. The uniform and concentrated live loads should not be applied simultaneously in structural evaluation. Concentrated loads should be applied to a small are or surface consistent with the application and should be located or directed to give the maximum load effect possible in endues conditions. For example, stair load should be applied to the center of stair tread between supports. In STAAD we assign live load in terms of UDL we have to create a loadcase for live load and select all the beams to carry such load.
WIND LOADS:
In the list of loads we can see wind load is present both in vertical and horizontal loads. This is because wind load causes uplift of roof by creating a negative pressure on the top of the roof. Wind produces non static loads on the structure at highly variable magnitudes. The variation in pressuresat different locations on a structure is complex to the point that pressure may become too analytically intensive for precise consideration in design. Therefore, wind load specifications attempt to amplify the design problem by considering basic static pressure zones on a structure of peak loads that are like to be experienced. For some pressure zones, the peak pressure depends on an arrow range of wind direction. The wind directionality effect must also be factored into determining risk consistent wind loads on structure.
Because the vary substantially over the surface of strucure. Wind load star considered at two different scales on scale, the load produced on the overall structure are on major structural systems that sustain wind loads from more than one surface of structure are considered the main wind force resisting systems (MWFRS). The structural systems such as trusses that experience loads from twosurfaces are regimes of the structure. The wind loads applied to MWFRS account for the large effects of time varying wind pressures on the surfaces of the structures. On a smaller scale, pressures are somewhat greater on localized surface area of building, particularly near abrupt changes in structure i.e., eaves, ridges, corners.
After designing the wind load can be assigned in two ways;
-
Collecting the standard values of load intensities for a particular height and assigning of the loads for respective height.
-
Calculation of wind load as per IS 875 part III. We designed our structure using secondmethod which involves the calculation of wind load using wind speed.
In Pune, we have a wind speed of 39 kmph for 10 m height and this value is used in calculation.
-
DESIGNING THE MODEL
Design of this model in the project is done by AutoCAD and Revit. 2D plan of the project Is done by using AutoCAD software and also the line plan of the model is done. 3D model is done by taking the reference of 2D plan that which we have drawn. First a new Revit file was created and saved. Then, the perimeters of walls were created. Once the perimeter walls completed, the interior walls are created. Then, the foundation walls, flooring, doors, windows, roof, stairs etc., were designed. Furthermore, the rooms were tagged. No mechanical, electrical and plumbing work is done. The difference between 3D and 2D modelling is reviewed.
FOUNDATION DESIGN:
Foundation provides support for structure, transferring their load to layers of soil that have sufficient bearing capacity and suitable settlement characteristics. There are very wide ranges of foundation types available, suitable for different applications, depending on consideration. Such asnature of load, ground conditions presence of water durability of soil, accessibility, sensitivity to noise and vibrations, proximity to other structure and load exerted on piles.
STRUCTURAL AND GEOTECHNICAL COORDINATION
A fully coordinated effort from geotechnical and structural engineers and geologist should ensurethat the result of pile foundation analysis is properly integrated in the overall foundation design. This coordination extends to plan and specification, preconstruction meetings and constructions.
DESIGN CONSIDERATIONS
Pile foundation analysis is based upon several simplifying assumptions which affect the accuracy of the results. The design engineer assures the analysis results comparing with load test results.
LOADING CONDITIONS
-
Usual this condition includes normal operating and frequent flood conditions. basicallowable stresses and safety factors should be used for loading conditions.
-
Unusual higher allowable stresses and low safety factor may be used for unusual loading conditions such as maintenance, floods, barge impact, construction or hurricanes. For these conditions allowable stresses may be 33%.
-
Extreme high allowable stresses and low safety factor are used for loading conditions suchas accidental or natural disaster that have a very remote probability and that involve emergency conditions after such disasters. For these conditions allowable stresses may be 75%.
-
Foundation properties soil strength and stiffness may depend on whether a load is vibratory, repetitive or static and whether it is of long or short duration.
BEAM DESIGN
A reinforced concrete beam should be able to resist tensile, compressive and shear stress induced in it by loads on the beam. To construct the further model, we have used three types of beams that are given below.
Doubly reinforced concrete beams: –
It is reinforced under compression tension regions. The necessity of steel of compression arises due to two reasons. When depth of beam is restricted. The strength availability singly reinforced beam is in adequate. At a support of continuous beam where bending moment changes sign such as situation may also arise in design of a beam rectangular in plan.
Fixed beam: –
It is supported at both ends and fixed to resist rotation. It is also called a built-in beam. Thefixed ends produce moments other than the reactions.
Cantilever beam: –
If a beam is fixed at one end and set to be free at the other end, it is termed as a cantilever beam. The beam distributes the load back to the support where it is forced against a moment and shear stress. Cantilever beams allow creation of a bay window, balconies.
ULTIMATE STRENGTH DESIGN OF FLEXURAL REINFORCEMENT
Design assumptions
-
Strength distributes linearly across the section.
-
Concrete resists only compressive stresses.
An ultimate strain of 0.003, the stress at extreme fiber of the beam reaches ultimate strength of concrete fc. the distribution of the compressive stresses is a complex curve. For calculation purpose, a stress block of 0.85fc spread over a depth, a, is used. Therefore, the total compressive stress in a rectangular beam is
FAILURE MODES AND REINFORCEMENT
-
Concrete is assumed to resist compression only; tension shall be resisted by reinforcements. Reinforcement shall be placed at the side of the beam that has tension. For simply supported beam, tension is at the bottom of the beam while for a cantileverend, tension is at the top of the beam.
-
Shear is at its maximum at the edge of supports. Diagonal shear cracks are normally developed close to the support. Stirrup for shear reinforcement is normally placed vertically to intercept the crack. They are normally closer spaced near the support and gradually spread out toward the center of the beam.
COLUMN DESIGN
A column is a very important component in a structure. It is like the legs on which a structure stand. It is designed to resist axial and lateral forces and transfer them safely to the footings in the ground.
You can manually calculate the superimposed loads on a column in a structure using a simple processoutlined in this linked article. Columns support floors in a structure. Slabs
and beams transfer the stresses to the columns. So, it is important to design strong columns.
Columns support floors in a structure. Slabs and beams transfer the stresses to the columns. So, it is important to design strong columns.
A column is defined as a compression member, the effective length of which exceeds three times the least lateral dimension. Compression members whose lengths do not exceed three times the least lateral dimension, may be made of plain concrete.
A column may be classified based on different criteria such as:
BASED ON SHAPE
-
Rectangle
BASED ON TYPE OF LOADING
-
Axially loaded column
-
A column subjected to axial load and unaxial bending
-
A column subjected to axial load and biaxial bending.
BASED ON PATTERN OF LATERAL REINFORCEMENT
-
Tied RCC columns
-
Spiral RCC columns
-
MINIMUM ECCENTRICITY
Emin > l/500 + D/30 >20
Where, l = unsupported length of column in mm D = lateral dimensions of column
TYPES OF REINFORCEMENTS FOR COLUMNS
-
Longitudinal Reinforcement
-
-
Minimum area of cross-section of longitudinal bars must be at least 0.8% of gross sectionarea of the column.
-
Maximum area of cross-section of longitudinal bars must not exceed 6% of the gross cross-section area of the column.
-
The bars should not be less than 12mm in diameter.
-
Minimum number of longitudinal bars must e four in rectangular column and 6 in circularcolumn.
-
Spacing of longitudinal bars measures along the periphery of a column should not exceed300mm.
-
Transverse reinforcement
-
-
It may be in the form of lateral ties or spirals.
-
The diameter of the lateral ties should not be less than 1/4th of the diameter of the largest longitudinal bar and in no case less than 6mm.
The pitch of lateral ties should not exceed
-
Least lateral dimension
-
16 x diameter of longitudinal bars (small)
300mm
-
Helical Reinforcement
The diameter of helical bars should not be less than 1/4th the diameter of largest longitudinal and notless than 6mm.
The pitch should not exceed (if helical reinforcement is allowed);
-
-
75mm
-
1/6th of the core diameter of the column
-
Pitch should not be less than,
-
-
25mm
-
3 x diameter of helical bar
Pitch should not exceed (if helical reinforcement is not allowed)
-
Least lateral dimension
-
-
16 x diameter of longitudinal bar (smaller)
300mm
SLAB DESIGN
INTRODUCTION
-
Effective span of slab:
Effective span of slab shall be lesser of the two
-
L = clear span + d (effective depth)
-
L = Center to center distance between the support
-
-
Depth of slab:
The depth of slab depends on bending moment and deflection criterion. the trail depth can beobtained using:
-
-
Effective depth d= Span /((L/d) Basic x modification factor)
-
For obtaining modification factor, the percentage of steel for slab can be assumed from 0.2to 0.5%.
-
The effective depth d of two-way slabs can also be aAssNuDmed using cl.24.1, IS 456 pTrHovEiIdReRdEshQoUrtIRspEaMn EisN<T3S.5m
and loading class is <3.5KN/m2.
-
The following thumb rules can be used:
-
-
One way slab d=(L/22) to (L/28).
-
Two ways simply supported slab d=(L/20) to (L/30)
-
Two-way restrained slab d=(L/30) to (L/32)
-
Load on slab:
The load on slab comprises of Dead load, floor finish and live load. The loads are calculated per unit area (load/m2). Dead load = D x 25 kN/m2 (Where D is thickness of slab in
m) Floor finish (Assumed as) = 1 to 2 kN/m2 Live load (Assumed as) = 3 to 5 kN/m2 (depending on the occupancy of the building)
DETAILING REQUIREMENTS OF REINFORCED CONCRETE SLAB AS PER IS456: 2000
-
Nominal Cover:
For Mild exposure 20 mm For Moderate exposure 30 mm However, if the diameter of bar doesnot exceed 12 mm, or cover may be reduced by 5 mm. Thus, for main reinforcement up to 12 mm diameter bar and for mild exposure, the nominal cover is 15 mm.
-
Minimum reinforcement:
The reinforcement in either direction in slab shall not be less than
-
-
0.15% of the total cross-sectional area for Fe-250 steel
-
0.12% of the total cross-sectional area for Fe-415 & Fe-500 steel.
-
Spacing of bars:
The maximum spacing of bars shall not exceed
-
-
Main Steel 3d or 300 mm whichever is smaller
-
Distribution steel 5d or 450 mm whichever is smaller Where, d is the effective depth of slab. Note: The minimum clear spacing of bars is not kept less than 75 mm (Preferably 100 mm) though code do not recommend any value.
-
Maximum diameter of bar:
The maximum diameter of bar in slab, shall not exceed D/8, where D is the total thickness of slab.
MATERIAL FOR THE STRUCTURE
The material for the structure were specified as concrete with their various constant as per IS code. Loadings were calculated partially, manually and rest were generated using Revit Structures load generator. The loading cases were categorized as: self-weight dead load from slab live load, windload, seismic load, load combinations.
DEAD LOAD FROM SLAB
Dead load from slab can also be generated by Revit Structures by specifying the floor thickness and theload on the floor per square feet. Calculation of the load per square feet was done considering the weight of beam, weight of column, RCC slab, terracing, external walls, internal walls, parapet over roof.
RCC STAIRCASE DESIGN
RCC Structures are nothing but reinforced concrete structures. RCC structure is composed of building components such as Footings, Columns, Beams, Slabs, and Staircase etc. These components are reinforced with steel that give stability to the structure. Staircase is one.
-
-
WORKING ON MEP
The optimal use of construction knowledge and experience in the fields of planning, design, and operation so that the overall project objectives can be met is defined as constructability. In simple terms, it is the prerequisite to begin on a construction project and MEP (Mechanical, Electrical, Plumbing) coordination is one of the most challenging tasks faced by the engineers and professionals as they can account for up 40 to 60% of the project.
Traditionally, MEP coordination was carried out manually by overlaying the plans sequentially and comparing them. This is a very tedious, time-consuming process and inefficient apart from being costly. With the advent of building information modeling (BIM), the efforts required in the coordination process were substantially eased with a saving in time and cost. Mechanical works like lifts, kitchen ducts, etc. are installed in MEP designs.
ADVANTAGE OF USING 3D BIM FOR MEP SERVICES
-
EFFICIENT CLASH DETECTION RESOLUTION A 3D model for Architecture, Structure, and MEP is created based on the designs developed by thedesigners. This aids in resolution of any conflicts before the onset of actual construction. These changes are easier and less expensive when compared to the changes that need to be carried on site. This, in turn, reduces wastage in terms of material and manpower, thereby resulting in cost savings.
-
COST SAVING
BIM follows the principle of Build Twice: the first in the form of a model complete with all the information and the second time on the site. This aids in resolution of any conflicts before the onset of actual construction. These changes are easier and less expensive when compared to the changes that need to be carried on site. This, in turn, reduces wastage in terms of material and manpower, thereby resulting in cost savings.
-
PREVENTION OF DELAYS
BIM coordination is carried out in the planning phase of the construction. Any errors in design arebrought to light at this stage. The elimination of errors in the planning stage provides a room for smooth execution on-site ruling out chances of delays arising due to faulty design.
-
REDUCING REWORK ON SITE
BIM database provides the information related to design and construction in the early design process. This data can be leveraged for the analysis and simulation of the model so that the resultantmodel is free of any conflicts. This reduced the probability of the necessity of rework required on the site.
Thus, BIM is a holistic approach to a building design. MEP coordination carried out through BIMresults in efficient and cost-effective buildings.
-
-
RENDERING OF MODEL
Rendering is the process of generating a photorealistic or non-photorealistic image from a 2D or 3Dmodel by means of a computer program. The resulting image is referred to as the render. Multiple models can be defined in a scene file containing objects in a strictly defined language or data structure. The scene file contains geometry, viewpoint, texture, lighting, and shading information describing the virtual scene. The data contained in the scene file is then passed to a rendering program to be processed and output to a digital image or raster graphics mage file. The term "rendering" is analogous to the concept of an artist's impression of a scene. The term "rendering" is also used to describe the process of calculating effects in an image editing program as well as video editing also.
Here are some most important types of rendering for design and architectural projects.
-
External 3D visualization
-
Interior rendering
-
-
CONCLUSION
-
Building information modeling is emerging as an innovative way to virtually design and manage projects. The survey explains the BIM potentials when used in the fields to better communicate and integrate construction information across different trades, allowing for efficient work process and better decisions. BIM as a tool to update the flow of information during, project is just as critical as first time. BIM develop their tools ability to be streamlined, but current process allows a BIM-enabled user to complete tasks with relatively good efficiently.
More specifically, the study concentrated on the deployment of the model to support planning, scheduling of the
operation in India. BIM save our time and money, not only during the design and construction of building, but through its entire lifecycle. BIM as its core, is not just software but a human activity that ultimately involves broad process changes.
REFERENCES
-
Ahuja et. Al. (2020) State of BIM adoption and outlook in India RICS School of Built Environment, Amity University.
-
G. M. Jagdeesh (2019) Investigation of BIM Adoption in India IJERT International Journal of Engineering Research and Technology Vol. 6, Issue 11, Nov 2019.
-
Nilay Singhal (2018) BIM Benefits in India
-
Sarkar et. Al (2015) Application of BIM to Real Estate Projects International Advanced Research Journal in Science, Engineering and Technology, Vol 2, Issue 9 Sept 2015.
-
Choughule and Konnur (2015) A Review of BIM for Construction Industry International Journal of Innovative Research in Advanced Engineering (IJIRAE), Issue 4, Vol. 2 (April 2015).
-
Z. Sampaio (2015) The Introduction of BIM Concept in Civil Engineering Cirriculum International Journal of Engineering Education Vol 31.
-
Sudha Venkatesh et. Al (2013) Status of BIM Adoption and the BIM Experience of Cost Consultants July 2014.
-
Khmlani, Kumar and Mukherjee (2012) Scope of BIM in India Journal of Engineering Science and Technology Review 2 (1) (2009) 165 169.
-
S. Azhar (2011) BIM: Trends, Benefits, Risks and Challenges for the AEC Industry Leadership and Management in Engineering.
-
Luthara (2010) Implementation of BIM in Architectural Firms in India Purdue University.
-
Geodert and Medati (2008) Integrating Construction Process Documentation into BIM Journal of Construction Engineering and Management.
-
IS 456: 2000 code book for design of beams, columns and slabs.
-
IS 875 Part I, Part II, Part III code book for live loads, dead loads and wind loads.
-
IS 1893: 2002 Part I code book for earthquake load design