
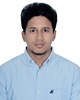
- Open Access
- Authors : Shaik Mohammad Tayyab , K.Chandra Sekhar
- Paper ID : IJERTV9IS100285
- Volume & Issue : Volume 09, Issue 10 (October 2020)
- Published (First Online): 03-11-2020
- ISSN (Online) : 2278-0181
- Publisher Name : IJERT
- License:
This work is licensed under a Creative Commons Attribution 4.0 International License
Role of Novel PDMS Panels in Monitoring Partial Discharges in GIS
Shaik Mohammad Tayyab Research Scholar – Dept. of E.E.E Acharya Nagarjuna University Guntur, India
Prof. K.Chandra Sekhar
H.O.D Dept. of E.E.E
R.V.R & J.C College of Engineering Guntur, India
Abstract This paper presents the functionality & role of PDMS panels for the monitoring of partial discharges in the GIS which is done in order to detect the faults on Gas Insulated Switchgears earlier so that the equipment is prevented from being damaged. The panel components & functioning of each component is clearly mentioned. The interconnection between the panels & the main equipments used were also discussed in detail. A specially designed PDMS panel serves the purpose of easy communication, monitoring & recording the partial discharges taking place in GIS on time to time basis through specialized software. The communication in between the PDMS panels & equipments is done through fiber optic cables for fast & accurate readings.
Keywords PD – Partial Discharge, UHF Sensors, & GIS – Gas Insulated Switchgears, EHV, HV, PDMS, Fiber Optics, LAN and SF6.
I. INTRODUCTION
GIS substations are in huge demand in the modern world scenario where there is lack of space availability for the big constructions. The typical transmission 400/132/33kV or 380/110/13.8kV Substations utilizes vast area if it is outdoor substation. The introduction of GIS substations has a tremendous variation in the occupancy of land when compared to outdoor substations. Now the protection of these transmission substations plays a vital role for the power system network. Partial discharges occurring in these substation heavy equipments like GIS, Power transformers etc. which contributes to the major part leading to the damages. So to secure & safeguard these heavy equipments against all blackouts & faults is the main criteria. UHF sensors are utilized for the detection of these PD pulses & monitoring is done by the specially designed PDMS (Partial Discharge Monitoring System) panels.
II. PARTIAL DISCHARGES IN GIS
Partial discharges in Gas Insulated Switchgears occur at high pressure of SF6 gas with very small gaps and have rapid breakdown times of sub-nanoseconds. PD pulses with fast rising waves have frequencies above 1 GHz which causes to excite switchgear chambers to various modes of resonance with Ultra High frequencies. The resonance persists for about microseconds at least as the chambers acts as low loss microwave cavities. The signals have very low voltage of around millivolts are amplified, displayed which makes the defect to detect easily. Gas Insulated switchgears in general for transmission substations follow the double bus single breaker scheme for 110kV or 132kV and one &
half breaker scheme for 380kV or400kV substations. Typical GIS photo for 380kV GIS is as below:
Fig (1): A typical 380kV GIS with one & half breaker scheme
III. PDMS PARTIAL DISCHARGE MONITORING SYSTEM The PDMS System plays a crucial role for continuous monitoring the occurrence of partial discharges in the Gas Insulated Switchgears & to communicate, updates the same in the HMI as well as the remote control center. It has main
three panels known as
OU Optical Unit
DC Distribution Cabinet
CC Control Cabinet
The general arrangement for PDMS system can be represented as below:
Fig (2): General Arrangement of PDMS panels.
Cable Number |
Description |
Purpose |
1 |
4×2.5sqmm armored |
Mains supply from CC to DC |
2 |
Data fiber multimode 4 core |
Data link from DC to OU |
Cable Number |
Description |
Purpose |
1 |
4×2.5sqmm armored |
Mains supply from CC to DC |
2 |
Data fiber multimode 4 core |
Data link from DC to OU |
TABLE I: General Cabling Arrangement
Cable Number |
Description |
Purpose |
||
3 |
UHF co-axial |
From OU to PD Sensor |
||
4 |
7×1.5sqmm armored |
Mains supply from DC to OU |
||
5 |
Data fiber multimode 24 core |
Data link from CC to DC |
IV. OPTICAL UNIT – OU
For the amplification & UHF signal detection, Optical unit has six individual front end signal modules. To protect from transients of high voltage, Diode protection is available. It has facility for channel self-test periodically to test the working condition of optical unit. By the process of filtering the narrow band noise is filtered out. The obtained signal after detecting and filtering is digitized and processed to get the data from each channel. This process checks the data stream for any partial discharge activity and records elements required for viewing through partial discharge monitoring software on PC system. The pulse is processed by detection and data acquisition system. The obtained result of Ultra high frequency channel is sent to PC system and fault recorder system. The control signals from PC system are transmitted through Ethernet cables to optical unit.
Fig (3): A Typical 7-Channel Optical Unit
V. DISTRIBUTION CABINET DC Distribution cabinet acts like communication between
the Control unit & optical unit. All Ethernet connections are routed by distribution cabinet & transfer them to Control cabinet by using a high speed fiber link. The distribution cabinet quantity depends on the size & complexity of partial discharge monitoring system.
Fig (4): A Typical DC Cabinet with main components
TABLE II: Parts of DC Cabinet
Part No |
Component Description |
1 |
Isolating Transformer |
2 |
Synch Driver Assembly |
3 |
Fiber Distribution box |
The main components of Distribution cabinet are:
a. Ethernet Switch: The Ethernet switches acts as interface between OCU data to RCC. Ethernet communications between the OCU & RDC can be fiber or copper depending on system configuration. All connections between RDC & RCC are through fiber.
Fig(5): A typical Ethernet Switch
b. Fiber termination box Housing for fiber cables terminations from RCC
c. Synchronization Driver Unit Synch driver unit receives timing & reset data from a synchronization interface unit fitted within RCC, this signal is generated from PCU system during normal operation & external sources during testing. The RDC synch driver unit converts incoming data to sync signal to drive OCU. The output is connected to OCU mains cable sync line within RDC.
Fig(6) : A Typical Synch driver unit
TABLE III: Representation of LEDs of synch driver unit.
LED |
ON |
OFF |
Rx |
Signal activity |
No activity |
PWR |
Device ON |
Device OFF |
d. Heater System – Heater system is installed to preent the buildup of humidity which can damage electronic systems within it. This system incorporates self-regulating heater that is controlled by hygrostat.
e. Circuit Breaker For Safety protection system, The different circuit breakers serves different purposes like to isolate the
i. Input power from control cabinet (Allows isolation of power to the circuits in distribution cabinet)
ii. OU Power, OU heater.
VI. CONTROL CABINET CC
The control cabinet is the main central data, control and power hub of partial discharge monitoring system. For the final processing & recording purpose, all the data from optical units are transmitted to monitoring server within control cabinet. The integration for the control and fault detection is done within monitoring system. Control cabinet has direct interface between the monitoring system, SAS or SCADA network and external LAN.
The main components of control cabinet are:
a. Power control unit – This interfaces the system server to the inputs like partial discharge alarm, Loss of AC alarm etc. The server watchdog is available for monitoring of the system server software. Pulses received from the server are detected and used to reset counters/timers in the PCU firmware. If no pulses are received in a time defined by the firmware, the PCU will signal a fault by setting an alarm and will reset DC supply to server.
Fig(7): Power control unit
b. Server The server controls the monitoring system displays and stores the system data. It links to PCU via serial cable for accurate phase timing from the VT inputs and alarm data. Data from OCU is phase resolved in software and displayed in correct phase & timing. This data is then collected during operation and stored as historical information from the system. It also contains dual LAN interface, LAN1 for the PCU local network to OCU and LAN2 for is used for remote access to headquarters PC system.
c. GPS System A Global Positioning System, interface module is installed in Control Cabinet which translates the signal of GPS system to a time code signal via serial link to server. The time signal is supplied from GPS module. Data is received by GPS module via an external antenna. The antenna cable to cabinet equipment is protected by surge voltage protector.
d. Ethernet Switch The Ethernet Switches acts as network interface between the distribution cabinet and server.
e. Fiber Termination Box – All the fiber cable terminations are done here.
f. UPS – This provides the filtered AC supply to monitoring system with battery backup & provides the ability for the safe shutdown of server during the loss of AC.
g. Hot Swap Unit This permits the removal of UPS without loss of power to the monitoring system.
The typical control cabinet is as below:
Fig(8): A typical CC Cabinet
TABLE IV: Parts of CC Cabinet.
Part No |
Component Description |
1 |
Keyboard |
2 |
Mouse |
3 |
Network Card |
4 |
Ethernet Switch |
5 |
Hot swap unit |
6 |
LCD Monitor |
7 |
PCU Assembly |
8 |
Fiber Termination box |
9 |
GPS Receiver |
VII. CONCLUSION
The monitoring of partial discharges is done perfectly with the help of above mentioned system using the optical units, control cabinets, distribution cabinets. This accuracy of monitoring the PD activities is essential for the early detection & prevention of the faults on Gas Insulated Switchgears by which the equipment is also saved from being damage which might result in huge loss. By using the advanced communication & control system like Substation Automation System, the monitoring is done easily from the far end remote control centers. Hence the GIS is protected from damages & blackouts and thus the stability of power system network is maintained.
VIII. ACKNOWLEDGEMENT
This paper is based on the research work which has been carried out during the commissioning & testing of Gas Insulated Switchgears in Saudi Arabia.
IX. REFERENCES
[1] International Electrotechnical Commission: INTERNATIONAL STANDARD IEC 60270, High-voltage test techniques Partial discharge measurement. [2] UHF Partial Discharge Monitoring for GIS", 10th International Symp. on High Voltage Engineering, Montreal, Vol. 4, p. 255-258, 1997 [3] The Excitation of UHF Signals by Partial Discharges in GIS", IEEE Transactions on Dielectrics and Electrical Insulation Vol.3, No. 2, April 1996. [4] IEC 62271-203 International Standard, Part 203- Gas insulated metal cladswitchgear for rated voltahges above 52kV. [5] Detection of Harmful Metallic particles in GIS using UHF sensors 2008 IEEE Transactions on Dielectrics and electric insulation. [6] Arshansky, I.S. The development of SF6- insulated test-sets for GIS die-lectric tests / I.S. Arshansky, S.Y. Matveev, [et al] // Proc. of 9th Intern. Symp. on High Voltage Engineering, Graz, Austria, 1995. Report 5276. [7] Halkiadis, I.S. A high-voltage low-cost wideband fiber optic transmission system with improved linearity [] / I.S. Halkiadis,N.G. Theofanous, D.A. Greaves // Electric Power Systems Research.
1996. No. 37. pp. 121 128.
[8] IEEE Substation Committee and Working Group K4 (CIS Diagnostic Methods), "Partial-Discharge Testing of Gas-Insulated Substations," IEEE Trans. on. PowerDelivery, vol. 7, no. 2, 1992, pp. 499-506. [9] K. Kurrer, K. Klunzinger, K. Feser, N. de Kock, D. Sologuren, "Sensitivity ofthe UHF-method for Defects in GIS with Regard to Online Partial Discharge detection," Proc. of the IEEEhf. Symp. on El. Ins., Montreal, 1996, Paper No. 2B-4. [10] J. S. Pearson, et al., "Partial Discharge Diagnostics for Gas-Insulated Substations," IEEE Trans. onDiel. andEl. Ins., vol. 2, no. 5, 1995, pp. 893-905.