
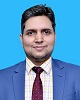
- Open Access
- Authors : Naveen Kumar , Suraj Vishwakarma
- Paper ID : IJERTV9IS030423
- Volume & Issue : Volume 09, Issue 03 (March 2020)
- Published (First Online): 03-04-2020
- ISSN (Online) : 2278-0181
- Publisher Name : IJERT
- License:
This work is licensed under a Creative Commons Attribution 4.0 International License
Roll Cage and Material Selection
Naveen Kumar1
1Assistant Professor, Department of Mechanical Engineering,
ABES Engineering College, Ghaziabad, Uttar Pradesh, India
Suraj Vishwakarma2
2Student,
Department of Mechanical Engineering, ABES Engineering College, Ghaziabad, Uttar Pradesh, India
-
Abstract:- A roll cage is a specially engineered and constructed frame built in (or sometimes around, in which case it is known as an exo cage) the passenger compartment of a vehicle to protect its occupants from being injured in an accident, particularly in the event of a roll over. The base frame of a vehicle is called a chassis. These two structures unite to form a closed or semi closed compartment (frame) in/on which other systems and subsystems are mounted.
Keeping in mind the basic requirements of a vehicle frame (aerodynamics and efficiency), we started designing the same which is compact in size, aesthetic in looks, ergonomic and capable of protecting its drivers in case of impact.
Keywords: CAE analysis, simulation
-
FRAME MATERIAL OPTIONS
Considering the basic utility of a vehicle frame and availability in the market, following materials can be considered for fabricating our vehicle frame.
i. Aluminium (6063)-T6 Cross-Section; 38.1 x 36.1 x 2 mm Composition:-
Cu- 0.1%
Fe- 0.35%
Mn- 0.1%
Mg- 0.45%-0.9%,
Cr- 0.1%
For the below table, consider the following abbreviations:
= Density of material
-
SYT = Yield strength
-
SUT = Ultimate Tensile strength
-
E = Modulus of elasticity
-
C = Cost
-
D = Estimated days for Delivery
MATERIAL
(g/cc)
SYT (MPa)
SUT (MPa)
E (GPa)
C
(Rs/feet)
D
AISI 6063-T6
2.7
214
241
68.3
70
7
-
-
CALCULATION OF BENDING STRENGTH AND BENDING
-
Aluminium (6063/T6)
Outer diameter (Do) = 38.1 mm Inner diameter (Di) = 34.1 mm
E = 68.9 GPA SY = 214 MPA R = 19.05 mm
Thickness (t) = 2 mm
-
MOMENT OF INERTIA: –
4
4
I = * (Do 4 – Di ) (1)
= *(38.1 4 – 34.1 4)
= 37063.16 mm4
-
BENDING STIFFNESS: –
Bending stiffness E*I
68.9 * 37063.16 * 10 3 N mm2
2.5536 * 10 9 N mm2
-
BENDING STRENGTH :-
Bending strength = (SY * I /C)
= (214 * 37063.16)/ (19.05) N mm
= 4.16 * 105 N mm
4. CAE ANALYSIS OF VEHICLE/FRAME
The frame is so designed to sustain significant loads and impacts (front, side, rollover and torsional). It should provide optimum damage protection to the drivers as well as to the vehicle itself in case of various impacts as mentioned below.
To be absolutely sure about the amount of safety a frame provides to the drivers, the CAD models of the frames employing the above four materials are simulated using software for-
-
Front impact
-
Side impact
-
Roll over
-
Torsion
ASSUMPTIONS CONSIDERED:
-
The frame material is considered to be isotropic and homogenous.
-
The tube joints are considered to be perfect.
-
FRONTAL IMPACT ANA0LYSIS Material-4 (Aluminum 6063 T6, 38.1*34.1*2)
-
-
-
Assumption & Considerations:
-
Front impact test was carried out assuming that the vehicle is having a mass of 240 kg (including the mass of both the drivers and dead weight) and travelling with a velocity of 40 kmph colliding head on with a stationary wall.
-
All the points at wheel mountings are fixed with zero degree of freedom constraints.
-
The load is applied at the front 4 nodes.
-
The mesh generated during this process is beam mesh with defined mesh control and fine density.
-
As per the rule specified by NHTSA (National Highway Safety Traffic Administration), the minimum impact time is of the order 250ms.
-
-
Calculation of Impact Forces:
Mass of vehicle including mass of drivers (m) =240kg
At the time of impact, velocity of the vehicle (vin) (2)
= 40kmph = 11.11 mps
Final velocity of the vehicle (vf) = 0 kmph Impact time (t) = .25 sec
We know,
Work done (W) = Change in Kinetic Energy W = ½ * m * (vin2 – vf2)
W=1/2 * 240 * (11.112 – 0)
W=14811.852 J Acceleration (a) = v/t a = 11.11/0.25 a = 44.44 m/s2
Applying second equation of motion s = ut ½at2
s = 11.11*.25 – 0.5*44.44*0.252 s = 1.3887 m
Fig.1.4(a Forces and Fixtures
-
Maximum Deformation = 5.39 mm
Fig.1.4(b) Maximum Deformation Analysis
Now,
Work done = Force(F) * Displacement(s) W = F * s
F = W/s
F = 14811.852/1.388 F = 10671.36 N
So, let front loading impact Force is 10700 N F = 10700 N
Number of nodes at front = 4
Load per nodes at front = 10900/4
= 2675 N
Load per nodes at front = 10900/4
= 2675 N
-
Maximum Stress Generated = 119 MPa
Fig.1.4(c) Maximum Stress Analysis
-
Factor of Safety
Maximum stress in rollcage = 119 Mpa Allowable stress = 215 Mpa
Fig.1.4(d) Factor of safety
4. ANALYSIS RESULTS :-
FOS = Maximum allowable steess Maximum stress generated
= 215
119
= 1.8
Optimizations:
During the preliminary analysis of the proposed design, it was found that the design was not strong enough in various portions to fulfill the requirements.
The reason behind it was stress concentration between the welded joints. So as to reduce the stress developed or to distribute it along the members, various supporting members were attached and the redundant members were removed.
Apart from that various other modifications were done in order to acquire good ergonomics, aesthetics, weight reduction etc.
Material-1 (Aluminum/6063 T6, 38.1*34.1*2) (3)
-
Assumptions & Considerations
-
Side impact test was carried out assuming that the vehicle is having a mass off 240 kg (including the mass of both the drivers and dead weight) and travelling with a velocity of 40 kmph colliding with another vehicle travelling with same speed.
-
All the points at wheel mountings are fixed with zero degree of freedom constraints.
-
The load is applied on 6 nodes at any one of the sides of the frame.
W=1/2 * 240 * (11.112 – 0)
-
The mesh generated during this process is beam mesh with defined mesh control and fine density.
-
As per the rule specified by NHTSA (National Highway Safety Traffic Administration), the minimum impact time is of the order 250ms.
b) Calculation of Impact Forces:
During side impact, it is assumed that the efficycle is at rest and another efficycle hits the first efficycle sideways. Impact time in this case is taken as 0.25 seconds.
Mass of the efficycle including mass of drivers (m) = 240 kg
Impact time (t) = 0.25 sec We know,
Work done (W) = Change in Kinetic Energy W = ½ m (vin2 – vf2)
At the time of impact, velocity of the vehicle (vin) = (4) 40kmph = 11.11 mps
W=14811.852 J
Acceleration (a) = v/t a = 11.11/0.25 a = 44.44 m/s2
Applying second equation of motion s = ut ½at2
s = 11.11*0.5 – 0.5*44.44*0.252 s = 1.388 m
Also,
Work done = Force (F) * Displacement (s) W = F * s
F = W/s
F =14811.852 /1.388 F = 10700 N
So, let front loading impact Force is 10700 N F = 10700N
Number of nodes at front = 6 Load per nodes at front = 10700/6
= 1750 N
(5)
Fig:- forces and fixtures
a) Analysis Results:
-
Maximum Deformation: 46.3 mm
Fig. 2.4(b) Maximum Deformation Analysis
-
Maximum Stress: 186.5 MPa
-
Factor of Safety:
Fig.2.4(c) Maximum stress Analysis
Maximum stress in roll cage = 186.5 MPa Allowable stress = 215 MPa
Factor of Safety = Maximum Allowable stress
Maximum stress generated
F.O.S = 1.15
a) Optimizations:
During the preliminary analysis of the proposed design, it was found that the design was not that strong in various portions or else we can say that the frame structure was not strong enough to fulfill the requirements.
The reason for this was the stress concentration between the welded joints, so as to reduce the stress developed or to distribute it along the members, various supporting members were attached and the redundant members were removed.
Apart from that various other modifications were done in order to acquire good ergonomics, aesthetics, weight reduction etc.
Material-1 (Aluminium/6063 T6, 38.1*34.1*2000)
-
Assumption & Considerations (6)
-
Rollover analysis was carried out assuming that the vehicle is having a mass of 240 kg (including the mass of both the drivers and dead weight) and the vehicle rolls upside down because of any external impact.
-
All the points at wheel mountings are fixed with zero degree of freedom constraints.
-
The vehicle is assumed to have been dropped from a height of 10 feet onto its top surface on the ground. This assumption is made to stimulate roll over condition.
-
The mesh generated during this process is beam mesh with defined mesh control and fine density.
-
It is assumed that the impact time of roll over is
0.25 seconds.
-
-
Calculation of Impact Forces:
Mass of the vehicle including mass of drivers (m) = 240 kg
Height from which vehicle is assumed to be dropped (h) = 10 feet = 3.048 m
Since the vehicle is dropped from a height, its potential energy changes into kinetic energy at the time of impact.
i.e. mgh = ½ mv2 v = (2*g*h)1/2
v = (2*9.81*3.048)1/2 v = 7.73 m/s (8)
Now,
Work done (W) = ½ mv2 W = ½ * 240 * 7.732
W = 7170.34 J
Displacement (s) = t * v
= 0.25 * 7.73
= 1.9325 m
We know,
= 1.9325 m
Fig:- Maximum Deformation analysis
Work done (W) = Force (F) * Displacement (s) W = F * s
F = W/s
F = 7170.348/1.9325 F = 3710.4
So, let the top loading force is 3712 N F = 3712 N
1. Maximum stress generated = 130 MPa (9)
Fig:- Maximum Stress Analysis
Number of nodes at top = 4
Load per nodes at front = 3712/4
= 928 N
Fig. 3.4(a) Forces and Fixtures
Allowable stress = 215 MPa
-
Analysis Results:-
-
Maximum Deformation: 24.89 mm
-
Factor of Safety = Maximum Allowable stress
Maximum stress generated F.O.S = 215/130 = 1.65
1) Factor of safety = 1.65
Fig.3.3(d) Factor of safety
a) Optimizations:
During the preliminary analysis of the proposed design, it was found that the design was not that strong in various portions or else we can say that the frame structure was not strong enough to fulfill the requirements.
The reason for this was the stress concentration between the welded joints, so as to reduce the stress developed or to distribute it along the members, various supporting members were attached and the redundant members were removed.
Apart from that various other modifications were done in order to acquire good ergonomics, aesthetics, weight reduction etc.
3.4. TORSIONAL ANALYSIS
F.O.S = 460/145.1 = 3.2
Material-1 (Aluminium/6063 T6, 38.1*34.1*2) (11)
-
Assumption & Considerations:
-
Torsional analysis was carried out assuming that the vehicle is having a mass of 240 kg (including the mass of both the drivers and dead weight). The front wheels experience bump on one side and droop on another.
-
The point at the rear swing arm hub is fixed with zero degree of freedom constraints.
-
One fourth of the load applied in front impact is applied at the two side nodes in equal magnitude and opposite direction.
-
The mesh generated during this process is beam mesh with defined mesh control and fine density.
-
-
Calculation of Impact Forces:
For Torsion, the twisting effect is assumed to be one fourth of the force in front impact. Force = (front impact force)/4
= 10700/4
= 2675 N
Number of nodes at side = 2
Load per node at side = 2675/2
= 1337.5 N
Fig. 4. 4(a) Forces and Fixtures
Analysis result:-
-
Maximumm Defirmation : 17.85
Load per node = 2675
= 1375.5 N
(11)
Fig.4.4(b): Maximum Deformation Analysis
-
Maximum Stress: 137 MPa
Fig.4.4(c) Maximum Stress Analysis
-
Factor of Safety:
Fig.4.4(d) Factor of safety
Maximum stress in roll cage = 137 MPa
Allowable stress = 215 MPa
-
Aluminium 6063, Tubular Cross section
Materials Selected for Frame:
Factor of Safety = Maximum Allowable stress 38.1*34.1*2.
Maximum stress generated F.O.S = 215/13 = 1.557 ~ 1.6
As clear from the table, Aluminium 6063 scored a total of 52 out of 60. It stood remarkably well on industrial as well as on road aspects of a vehicle.
Table 6.1 (Material Comparison)
W
9
9
9
8
W.O.F
9
7
8
9
D
5
8
6.5
9
C
7
8
7.5
8.5
S
9
9
8.5
8
Total
48
49
47.5
52.5
COCLUSION
After performing calculations and simulations on the rollcage we found that aluminium 6063-T6 is taken selected for manufacturing of rollcage of dimension 38.1*34.1*2.
REFRENCE
-
K. Mahadevan, K. Balaveera Reddy; Design Data Handbook, Fourth Edition(2019)
-
V. B. Bhandari; Design of Machine Elements, Third Edition.
-
Siddharth Aphale, Pradnesh Lachake; Design and Analysis of Roll Cage for an Electric Hybrid Tricycle, International Journal of Engineering Trends and Technology (IJETT) Volume-44 Number-2 -February 2017
-
Vikas Verma, Dr. S S Chauhan, Asst. Prof. Ranjeet Kumar; Design & Development of Combined Human and Electric Powered Vehicle, International Journal of Advance Engineering and Research Development Volume 3, Issue 4, April -2016
-
Sumit Panchal and Hemant Singh Rajput; Design, Analysis and Fabrication of Human Powered Hybrid Vehicle, European Journal of Advances in Engineering and Technology, 2016, 3(5): 40-45.
-
K.A. RAAGUL SRINIVASAN, S.A.PUVIYARASU; Optimized Design and Analysis a chassis of a Hybrid cycle, International Journal of Advance Engineering and Research Development Volume 3, Issue 10, October -2016.
-
Aditya Kumar Mohanty, Ankit Jambhulkar, Prof. Bhupesh Sarode; Design and Development of Roll Cage, International Research Journal of Engineeringand Technology (IRJET) Volume: 05 Issue: 03 | Mar-2018, e-ISSN: 2395-0056.
-
Shubham Kolhe, Vrushabh U. Joijode; ROLL CAGE DESIGN AND ANALYSIS FOR FORMULA STUDENT RACE CAR, INTERNATIONAL JOURNAL OF ENGINEERING SCIENCES & RESEARCH TECHNOLOGY.
-
Mahendra H M, B S Praveen Kumar, Puttaswamaiah.S, G.S Prakash; DESIGN AND CRASH ANALYSIS OF A ROLLCAGE FOR FORMULA SAE RACE CAR, IJRET: International Journal of Research in Engineering and Technology eISSN: 2319-1163 | pISSN: 2321-7308.
-
Tushar N. Patangray, Prof. Harshal D. Patil; Static Analysis of the Roll Cage of All-Terrain Vehicle, International Research Journal of Engineering and Technology (IRJET),Volume: 05 Issue: 08 | Aug 2018, e-ISSN: 2395-0056
-
Mr. Mohd Abu Bakar Ansari Prof. Vaibhav Bankar; Design and Analysis of Structure of Roll Cage for SUPRA SAE, International Journal for Scientific Research & Development| Vol. 6, Issue 03, 2018 | ISSN (online): 2321-0613
-