
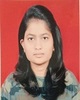
- Open Access
- Authors : Kalyani Anil Pawade , Dr. Vrushali V. Khatavkar
- Paper ID : IJERTV9IS100269
- Volume & Issue : Volume 09, Issue 10 (October 2020)
- Published (First Online): 03-11-2020
- ISSN (Online) : 2278-0181
- Publisher Name : IJERT
- License:
This work is licensed under a Creative Commons Attribution 4.0 International License
Sampled Data Control Processing for AC Pulse of Nonlinear System Load in Close Loop using Matlab Simulink
Miss. Kalyani Anil Pawade
Dept. of Electrical Engineering
PES. Modern College of Engineering,
Shivaji Nagar, pune-05
Dr. Vrushali V. Khatavkar
Dept. of Electrical Engineering
PES. Modern College of Engineering,
Shivaji Nagar, pune-05
Abstract:- Inverter may be a sort of adjustable-speed drive not able to manage AC motor speed and force.[7] With advances in solid-state power electronic devices and microprocessors, varied electrical converter management techniques using pulse width modulation (PWM) are getting progressively common in AC motor drive application. [16] These PWM-based drives area unit not able to manage each of the frequency and magnitude of voltage applied to motors.[9] This research analysis the speed system of Induction motor fed by Vage supply electrical converter by Sampled pulse information within the feedback path utilizing constant volt per hertz quantitative relation with 2 PWM techniques specifically, curving PWM and house vector PWM.[13] The performance of SPWM and SVPWM primarily based electrical converter has been analyzed in MATLAB. Here we are taking induction motor as a non linear load. [1]
Keywords:- Sampled and hold control processing, non linear load.
I. INTRODUCTION:
In this research paper we are taking induction motor as a non linear load because induction motor is mostly used in industry hence smooth speed controlling is required for efficient working and for greater efficiency. Near about 80-90% motor used are induction motors.[10] As far as the machine efficiency, robustness, reliability, durability, power factor, ripples, stable output voltage and torque are concerned, Single- phase induction motor stands at the a top of the order.[3] Induction motors are widely used in many residential, industrial, commercial, and utility applications.[19] But they require much more complex methods of control, more expensive and higher rated power converters than DC and permanent magnet machines.[11] Various techniques are in practice for speed control of induction motor. [20] In this research paper we discuss various speed controlling techniques of induction motor, compare all of them and try to implement the best suitable and most efficient method for speed controlling of induction motor so that we get smooth speed control without affecting the performance of the system and get reliable and desired output.[5]
II.BLOCK DIAGRAM OF OVERALL SYSTEM:
block.png
Fig.1 Sampled data Control processing for AC pulse of Nonlinear Systems load in Close
As we can discuss the three recent techniques of speed controlling of induction motor. On the basis of third technique that is sampled data control processing in close loop this whole system works. As we can seen in the block diagram (fig.1) actually it describes the basic working of our project. First block is pulse tuner. As we want to transfer a signal to controller block the output of pulse tuner is applied, the controller work only on DC signal but the input signal given to pulse tuner is AC signal, then in the pulse tuner input AC signal is converted into sampled distributed signal that means in DC signal by using ADC, and we get sampled data at the output of pulse tuner then this data is given to controller block.
In controller process a data signal as per programming already build by the user in the controller according to that PWM signal is generated but we cannot use the PWM signal to drive the induction motor because PWM signal is sampled discrete signal and the induction motor only work on single phase AC supply.
Hence, we connect auptocoupler and BJT. And now auptocoupler and BJT can use this digital data with respect to PWM and made a bridge for AC pulse. And now this AC pulse is given to the non linear, here we are using single phase induction motor as a non linear load. but, whatever the error factor generated, that error is given through feedback so that we get desired set refference value at the output. in this way the whole system works.
III. PROGRESS REPORT OF PROJECT:
a) Install matlab:
Before starting of my project firstly I am learnt how to install matlab in PC. Install matlab in PC of version [R2013a]. And started to use it.
b) Learn basic programming:
Firstly I started to do basic programming to understand working of a matlab. And do a basic program like:
Arithmetic operations: addition; subtraction; multiplication; division etc
Logical operations: AND; OR; NOT etc
c) Learn complex programming:
After understanding of basic programs then I started learning complex programming
Like: Matrix operations; Vector operations etc
d) Learning simulink:
Simulation is important part to study of matlab for full understanding of project express, innovate and make changes in project diagram. First of all started to know what is library, which are the components, how to drag components and what is simulink model screen etc.
e) Start to generate block diagram:
After fully understanding of matlab options then started to generate block diagram by searching components in matlab library, drag the required component from the list to the simulink model screen and connect all the components to form a desired block diagram. Then run it and get the result.
f) Analysis of non-linear load:
First of all select a particular highly demandable non linear load the try to control its speed and understand the behavior of the non linear load desired methods is to be applied to control its speed.
g) How to generate PWM control circuit of controlling the speed of non linear load:
After understanding the behavior of non linear load system try to control its speed by using PWM control circuit. And see its behavior from the waveform.
f) Try to find out the errors and then try to minimize it:
Try to minimize the errors by making changes in circuit.
IV. MATLAB SIMULATION MODEL:
Following figure shows another matlab model in which we make some changes for better understanding of us and to get a better output.
Starting parameters are as we discuss in model, those are given below:
. AC voltage supply: Here we are using Ac single phase voltage supply; of peak amplitude voltage of [ 110*sqrt(2) ] and frequency of 60 Hz.
. Rectifier: Here we are using rectifier with forward voltage of 0.8 V and internal resistance of 100 ohm. Rectifier is converting the AC current into DC
current. The rectifier consists of semiconductor diodes to do this function.
. L-C filter: Inductor having values of (1e-3) Henry of value and capacitor is of (39e-4) farad of value. L-C filter is use generally for LC circuits are used either for generating signals at a particular frequency, or picking out a signal at a particular frequency from a more complex signal, this function is called a bandpass filter.
. PWM IGBT Inverter: Here we are using PWM IGBT Inverter consisting of snubber resistance of 5000 ohms, and by using power electronics devices like IGBT/Diodes. It is used to it will used to converts DC current/voltage into AC current/voltage.
. Single phase induction motor: Induction motor is also is called as asynchronous motor. Here we are using single phase induction motor of voltage 110Vrms, 60Hz frequency and nominal power of [0.25*746] VA. Here we are using induction motor as a non linear load.
. Ramp: Here we are using ramp block with slop-2 and start time of 1. Ramp block is generally used for output a ramp signal at a specified time.
. Saturation: Here we are using saturation block which is used to limit input signal to upper and lower saturation values. Here we are taking upper limit is 1 and lower limit is 0.
. Voltage measuring block and multimeter: Both of the blocks are used to measure the voltage value from the auxiliary winding.
. Mux: use of mux is to multiplex scalar or vector signal. Here two inputs are given to the mux one from voltage measuring and another from multimeter and we get one output which is given to scope as an input, so that we can seen the auxiliary winding voltage.
Gain: Here we are using gain block with value of gain is [30/pi]. Gain multiplies the input by a constant value (gain). The ‘Output as bus’ to output a single bus signal By using all the parameters we understand the working of an induction motor. But we know that nature of non linear load that means speed of induction motor is variable hence to control the speed we try to add controller with it. Hence add some other blocks also as discuss below so that we control its speed.
Signal inputs: Here we are four types of input signal-
1) Step: following signal shows step waveform.
updated_matlab-ckt-1.png
Fig.2 Matlab Model Of project
input and the gain in the gain can each be a scalar, vector or matrix.
Bus selector: This block accepts a bus as input which can be created from a Bus Creator, Bus Selector or a block that defines its output using a bus object. The left list box shows the signals in the input bus. Use the Select button to select the output signals. The right list box shows the selections. Use the Up, Down, or Remove button to reorder the selections. Check
images (7).png
Fig 3. Waveform of step signal
2) Ramp: following signal shows ramp waveform. 1200px-Ramp_function.svg.png
Fig 4. Waveform of ramp signal
3) Repeated sequence: following signal shows repeated sequence waveform.
images (10).png
Fig 4. Waveform of repeated sequence signal
4) Sine wave: following signal shows sine waveform.
images (11).png
Fig 5. Waveform of sine wave signal
. Switches: We are uses three switches here for supplying desired voltage to the controller block.
. PID controller: This block implements continuous- and discrete-time PID control algorithms and includes advanced features such as anti-windup, external reset, and signal tracking. You can tune the PID gains automatically using the ‘Tune…’ button (requires Simulink Control Design). In controller process a data signal as per programming already build
by the user in the controller according to that PWM signal is generated but we cannot use the PWM signal to drive the induction motor because PWM signal is sampled discrete signal and the induction motor only work on single phase AC supply.
. PWM Generator: Output a pulse to the electronic switch of a one-quadrant DC to DC Converter. The duty cycle (input D) determines the percentage of the pulse period that the output (P) is on. Here we set switching frequency of 100Hz.
V. SIMULATION RESULTS OF MATLAB MODEL:
From all the waveforms shown above indicated the output when different input is given such as:
. Step signal
. Ramp signal
. Repeating sequence signal
. Sine wave signal
There are very small variations at the output this is conclude from all the waveforms. If we give sine waveform as an input then we get various variations and mal operation if we do not given proper sine wave then various big operating application industries are majorly suffer from this. Hence to overcome this difficulty we see waveforms and its behavior shown bellow.
. Following figure shows the output waveforms of simulation model-III when sine signal is given as an input.
A) Sine wave signal:
sine_scope-7.png
Fig.6 output waveform from scope-7 shows input applied to the system i.e sine wave
If step input is given then we get following output :
sine_scope-6.png
Fig.7 output waveform from scope-6 shows Sampled data control output given to Tm terminal of IM.
sine_scope-1.png
Fig.8 output waveform from scope-1 shows main and auxiliary winding current in (ampere)
sine_scope-4.png
Fig.9 output waveform from scope-4 shows rotor speed in (rpm)
sine_scope-3.png
Fig.10 output waveform from scope-3 shows load and electromagnetic toque in (N-m)
sine_scope-2.png
Fig.11 output waveform from scope-2 shows auxiliary winding voltage
VI. ADVANTAGES:
. Low power consumption.
. Low cost system as compared to VFD.
. Error correction system.
VII. APPLICATIONS:
. Textile miles.
textile industry.jpg
. Industrial use for smoothing motor during start.
CONCLUSION:
The contribution of this research paper is to see results practically and by using the overall procedure we get smooth inductive load output. And try to simulate different circuit so that we get desired output. Also we understand that for a better accuracy close loop system will provide reduce harmonics. From this we get an idea how to make our project better. For smoother controlling the speed of a non linear load i.e. Induction Motor.
REFERENCES:
[1] Ying-Ying Liu and Yun-kai Chu, “Control Method for Sampled-Data Systems with Multiple Channels Based on Dead band-Triggered Scheme”8, Hindawi Security and Communication Networks Volume 2018, Article ID 8165383.