
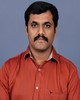
- Open Access
- Authors : S. Karthikkumar , P. Suseendhar , V. Kavithamani , R. Chandrasekaran
- Paper ID : IJERTV11IS090072
- Volume & Issue : Volume 11, Issue 09 (September 2022)
- Published (First Online): 28-09-2022
- ISSN (Online) : 2278-0181
- Publisher Name : IJERT
- License:
This work is licensed under a Creative Commons Attribution 4.0 International License
Schema of Wind Turbine System and Analysis of Appropriate Converter Topologies
S. Karthikkumar
Electrical and Electronics Engineering Jai Shriram Engineering College Tirupur 638660
Tamil Nadu, India
V. Kavithamani
Electrical and Electronics Engineering Jai Shriram Engineering College Tirupur 638660
Tamil Nadu, India
P. Suseendhar
Electrical and Electronics Engineering Karpagam Academy of Higher Education, Coimbatore 641021
Tamil Nadu, India
R. Chandrasekaran Electrical and Electronics Engineering Coimbatore Institute of Technology,
Coimbatore 641014 Tamil Nadu, India
Abstract A wind turbine is a device used for converting the kinetic energy of the wind into electrical energy. Their applications may ranges from charging an auxiliary power sources to supplying domestic power supplies and then to larger electric grids based on their rating and size. Because of the commercial advantages like ease of design, cheap in cost, efficiency in power generation horizontal axis wind turbine systems are widely used to transmit the shaft power through gearless (direct drive variable speed wind turbine system) mechanism which provides mechanical power to electric generator. Synchronous generator has the capability of direct connection to the wind turbine (without gear transmission) where the generator unit is completely decoupled from the load or grid side by the power electronic converter interface. Permanent magnet rotor of synchronous machine requires no external excitation and choice of modified SEPIC converter results better power transmission with reduced losses (or reduced switching stresses). Hence theoretical and practical concepts on the schema of wind turbine system with modeling on each section of conversion are performed. As a part of discussion a case study on wind turbine generators in Tamil Nadu is submitted
Keywords Wind energy; variable speed and constant speed system; power converter; synchronous generator; case study; modeling and simulation
-
INTRODUCTION
Movement of wind on a large scale is called as wind. It is about 2% of energy coming from sun, which is 50 to 100 times greater than the energy converted into biomass by all plants on earth [1]-[3]. It is caused by the uneven distribution of earths atmospheric pressure and rotation (Coriolis Effect) due to which the air circulates anticlockwise around the areas of low pressure in northern hemisphere and clockwise in southern hemisphere. These mechanisms are responsible for the creation of wind at a global level and those at the level of individual wind farm are in practice which is impacted by more local effects. Since the wind is accumulated with enormous amount of energy it is needy to generate electrical power on a possible large scale similar to that of non-
renewable resources. The total amount of extractable power in a wind is considerably larger than what we are utilizing from other resources. The speed and direction of the wind is considered to be the powerful economists of a wind farm. It is a source to generate electricity and load to destroy the turbine inertia. The estimation of power generation requires some statistical analysis since the speed and direction of wind vary with altitudes due to surface friction and temperature gradients [4]-[5].
Wind Resources Assessment (WRA) has become the essential protocol in determining whether the wind power is viable source of option (Herbert et al 2007). So many things have been experienced in these past years down to lower scale terrain effects and potentially damaging turbulence [6]. The unit has been involved in the realization of national wide WRA programme sponsored by the government of India in association with state nodal agencies. The ministry, agencies of central and state government continuously assessing new policies, programmes to identify the wind prone zones of different ranges. These programmes laid to the measurement of wind at 789 locations across the country for the period of 1 to 5 years. From the cumulative measurement of wind, 237 stations have been found to have Wind Power Density (WPD) in excess of 200 W/m2 at 50 meters above ground level. 108 consultancy projects are involved in micrositing, verification of data collection procedure and preparation of due diligence report. (CWET – Annual report 2013-2014). As on March 2014, 157 Wind Monitoring Stations (WMS) are operating in 17 states and 1 union territory (including 82 stations currently commissioned). In Tamil Nadu 16 WMS are installed during 2013-2014 and 18 are in operation as on March 2014. The total number of stations based on WPD is shown in Table 1.
S. No
WPD – W/m2
Number of stations
1
200-250
107
2
251-300
61
Table 1 Total number of Stations based on WPD
3
301-350
27
4
351-400
17
5
>401
25
Total
237
Courtesy: CWET-Annual report 2013-2014
The WMS are of 50m, 80m, 100 and 120m height and sensors are placed at 10m, 30m, 50m (50m height mast), 20m, 50m, 78m, 80m (80m height mast) 10m, 48m, 50m, 78m, 80m, 98m, 100m (100m height mast) 10m, 30m, 60m, 90m, 120m (120m height mast) levels. (All the heights are above ground level). C-WET has released partial fund of Rs. 191 Lakhs to the state nodal agencies to install WMS during the financial years from 2006 to 2014. As the wind velocity varies with altitude, measurement of wind speed at a required height can be calculated using an empirical relation and it is an exponential variation in wind velocity with height can be defined relative to wind measure at a reference height. Wind speed is not steady and in order to calculate the mean power delivered by a turbine, the probability density of distribution of wind speed for a site should be known. The plot of wind velocity Vw (m/s) Vs the total time period during a year (described in Weibull distribution) is called as wind speed distribution curve [7]-[9].
-
THEORY OF WIND TURBINE SYSTEM
Fig. 1 Power transfer in wind energy converter
The major components of modern horizontal axis WTG are the tower, rotor, drive train, yaw, electrical & electronic system and supporting subsystems. Nose cover (nacelle) accommodates the gear transmission and braking systems. Yaw mechanism is for steering the turbine head in response to changes in wind direction. Generators, switching and protection systems, transmission lines and also transformers will also be a part of a wind farm [10]. The control structure of a WECS is shown in Figure 1.
-
Description of system and subsystem
Wind turbine rotor converts the kinetic energy of wind into rotary mechanical energy. It consists of a hub, rotor blades and blade extenders to increase the swept area through the diameter. The hub is made of cast steel and mounted on the turbine rotor shaft. The rotor blades are made of reinforced plastic moulded on a steel shaft with turnable blade tip air brakes having fatigue strength, specific weight, and elasticity to accommodate severe wind phenomena. The typical assembled configuration of a WECS is illustrated in Figure 2.
Fig. 2 Major components of WECS
The tower is used to support the nacelle assembly above the ground level. They are made from tubula steels and enable turbine rotor to capture more energy to absorb and discharge the static and dynamic stress exerted on the nacelle assembly into the ground. The height of the tower is determined by radius of the rotor. The nacelle assembly along with rotor is placed over the tower through yaw mechanism. A wind gauge is placed on the nacelle top for measuring the wind speed and transmits the wind data to the closed loop controller. A wind vane is used here to sense the maximum wind direction and drives the yaw system to orient the turbine properly with respect to the wind. The yaw drive system consists of a mounting plate of cast steel, a ball bearing slew ring with inside cogging. The wind turbine system is coupled with generator through geared or gearless concept. The integrated gearbox is designed to transmit all the static and dynamic forces directly into the tower construction. Normally it has 3 stages with 4 parallel shafts or 2 stages with 3 parallel shafts depending on the generator poles. The low speed shaft is hollow and manufactured in one piece with a flange for direct mounting of the rotor. The gears increase the rotational speed from 30 to 40 rpm to about 900 to 1000 rpm. This mechanical energy is converted into electrical energy using generator and the power thus generated may be supplied to the grid or isolated load. A microprocessor based control unit is operated here for monitoring control and safety operations such as monitoring of brake system, yaw control, cut-in and cut-off of generator to the grid and for diagnosing various statistical informations regarding the performance of turbine and track record of faults are collected and recorded. The controller cabinet has a separate housing for soft switching equipments, contactors for generators, overload relays, circuit breakers and capacitor banks [11]. A fibre-optic system protects the sensor unit used for monitoring of parameters such as generator speed, temperature, oil and pressure level, vibration etc. The components are extensively protected against lightning strikes and transient conditions and are potentially balanced through effective earthing [12]-[13].
-
Classifications
The horizontal axis wind turbines are classified as up-wind and down-wind configuration based on the turbine facing the predominant direction of wind as shown in Figure 3. The upwind orientation requires active yaw control to keep rotor facing the wind direction to deliver smooth power. The
downwind configuration suffers from wind shadowing effects and hence the output power is reduced [14].
Fig. 3 Up-wind and Down-wind topology
Modern wind turbines are also classified based on the number of blades. Single bladed rotors are obsolete nowadays as they require additional counterweight and a robust hub to compensate for rotor eccentricity. The two bladed rotors are more difficult to control and have complex hub designs. More than 95% of turbines are 3 bladed rotors due to its ease of control and dynamic balancing. The turbine may be either stall or pitch regulated. The turbine blades are pitched out of the wind to turn the rotor in winds that are too high and too low to produce electricity. Pitch angle varies for various wind velocities in order to keep the output power constant at rated value for pitch regulated machine whereas in stall regulated machine pitch angle is fixed [15]-[16]. The controller compares the actual power with the reference value to produce error signal which in turns operates the pitch actuator to alter the pitch angle until the rated power is achieved. The pitch angle is fixed to have a minimum aerodynamic efficiency for the wind velocity below the rated value. In stall regulated machine the output power is reduced at higher wind velocities. Yaw control is rarely used in pitch controlled machines because of the stress involved and undesirable noise. Most of the turbines are employed with passive yaw control in which the pitch angle is fixed during its installation. At normal operating conditions, the variation of rotor speed is normally less than 5% and as the wind velocity increases, the angle of attack increases running the rotor at constant speed. The lift force on the rotor blades beyond a specific value of angle of attack decreases causing the drop in rotor efficiency proportionally power drops at higher wind velocities [17].
-
-
CHOICE OF GENERATOR FOR VARIABLE SPEED SYSTEM
Various generators are discussed in the literature suited for fixed and variable speed operation of WTS. The variable speed operation of the turbine system meticulously harvest the possible power at all times along with PPT controllers. The direct drive wind turbine system gave a 30% progress in market by 2014 comparing a year back. So the transformations have to be incorporated accordingly in a suitable electrical machine to feed the energy hungers. The
asynchronous and synchronous generators are the conventionally proven electrical machines in WECS and hence certain known and unknown theories have to be discussed to choose the right machine to fix the protocol. There is no induction generator in reality unless the induction motor runs in super-synchronous speed. Hence in the DFIG, the configuration is made such that there will be a bidirectional power flow at negative and positive slip operating regions which is termed as sub-synchronous and super-synchronous modes of operation. The power can be injected to the rotor circuit from the bus bar if the generator speed is less than synchronous speed and the power is delivered to the bus bar if the speed is above synchronous. By utilizing the mechanical energy and the potential supplied from the stator, generative action of the machine starts. Low price, robust structure, mechanical simplicity, resistance against disturbances and less vibration are the features of induction machine. The electromechanical strength of the machine is also good and its reliability holds better for low power applications [18]). Huge reactive power is drawn for the active power generation in the absence of phase controlled condensers. Power factor is determined by the value of slip rather than load, which is considered as a drawback. The SCIG and DFIG based WECS have poor efficiency and moreover they cannot track peak power as the wind velocity changes [19]. Also the direct drive mechanism can operate without any reactive power consumption. The induction machine cannot run efficiently during most of the times and draws huge reactive power [20]. Induction generators employed for direct driven system is a non linear system and requires non linear control strategy to bring the system to optimal operating point [21]. PMSG has the advantages of compact and simplicity in construction, high reliability, no need of field excitation, brush assembly and bidirectional power flow controllers. Also the machine has good power to weight ratio, higher efficiency than electrically excited generators. Recent developments in power electronic technology support PMSG for direct driven applications Electrical excited generators with larger number of poles have larger diameter for efficient operation. Whereas PMSG allows multiple operations with smaller pole pitch and yields cost effective design. The multipole radial flux permanent magnet rotor can be incorporated within a confined space of the nacelle suited for small, gearless, low speed wind turbine applications [22]. Therefore the factors are favored to make direct driven PMSG more suited for wind turbine concepts in the current trend.
-
Radial flux PMSG
Radial flux permanent magnet generators utilized for direct driven wind turbines can operate with good performance over wide range of wind speeds. Radial flux machines are most conventional where the distribution of flux is radial and the current flows in axial direction. Air-gap and length of the machines are independent and hence the diameter can be made small for larger axial length. The permanent magnets with less weight, higher flux densities are mounted on the surfce of the outer periphery of rotor. The topology is easy to fabricate employing higher number of poles. The advantages includes simple and cheaper in price [23]. The structure of radial flux rotor is shown in Figure 4.
Fig. 4 Structure of radial flux permanent magnet rotor
-
Axial flux PMSG
Fig. 5 Structure of axial flux permanent magnet rotor
The flux is distributed in the axial direction parallel to the rotating shaft. The machine has lower cogging torque, shorter axial length, less noise and higher torque-volume ratio (). It is difficult to fabricate stator core and maintain air-gap flux in slotted machines. The disadvantage includes low torque-mass ratio, large outer diameter and structural instability. Slotless single stator double rotor is a typical configuration of axial flux PMSG which is often referred as torus machine. It does not require any stator back iron since the main flux travels axially. The theoretical overview suggests that performance of radial flux PMSGs are more suited for DDVSWTS. The structure of axial flux rotor is shown in Figure 5.
-
-
PERFORMANCE COMPARISON OF DFIG & PMSG A 6 kW AC machine (DFIG and PMSG) was preferred
for the performance study. The system was modeled using MATLAB/SIMULINK toolbox.
-
Modeling and simulation of DFIG
The simulated waveforms reflecting the machine parameters of 3 phase, 50 Hz induction machine whose rating is 6 kW, coupled to a turbine rotor through the gear box. The value of stator resistance is 0.023 pu and stator inductance is 0.18 pu. The parameter of rotor referred to stator is Rr=0.016 pu and Lr = 0.16 pu. The magnetizing inductance Lm = 2.9 pu The system is made to operate for the wind speed from 6 m/s to 12 m/s. Due to excitation problem, the machine is made to run below synchronous speed at start and reaches super synchronous speed. The simulated results of output power are shown in Figures 6 to 9.
Fig. 6 Power generated by DFIG at 6 m/sec
Fig. 7 Power generated by DFIG at 8 m/sec
Fig. 8 Power generated by DFIG at 10 m/sec
Fig. 9 Power generated by DFIG at 12 m/sec
The steady state value of the system may be affected by the step change of wind at every fraction of seconds.
-
Modeling and simulation of PMSG
The simulated waveforms reflecting the machine parameters of 3 phase, 50 Hz induction machine whose rating is 6 kW, coupled to a turbine rotor through the gear box. The value of stator resistance is 0.023 pu and stator inductance is 0.18 pu. The parameter of rotor referred to stator is Rr=0.016 pu and Lr = 0.16 pu. The magnetizing inductance Lm = 2.9 pu The system is made to operate for the wind speed from 6 m/s to 12 m/s. Due to excitation problem, the machine is made to run below synchronous speed at start and reaches super synchronous speed. The simulation is made for 3 phase, 50 Hz PMSG whose rating is 6 kW, coupled directly to the turbine rotor. The stator resistance is 0.006 PU. The direct and quadrature axis stator reactance is Xd=1.305, Xq=0.474 respectively. The power generated at wind speed ranging from (6-12) m/s are shown in Figures 10 to 13.
Fig. 10 Power generated by PMSG at 6 m/sec
Fig. 11 Power generated by PMSG at 8 m/sec
Fig. 12 Power generated by PMSG at 10 m/sec
Fig. 13 Power generated by PMSG at 12 m/sec
The control strategy is more over similar to the DFIG, except it does not requires any external excitation since the rotor is permanent magnet. The d-axis and q-axis component regulates the generator power factor and speed by adjusting torque appropriately.
Table 2 Comparison of Real Power Generated in DFIG and PMSG
Wind Speed in m/s
Generated power in kW
DFIG
PMSG
6
2.750
3.302
8
3.032
3.681
10
3.457
3.808
12
3.740
4.092
The converters in PMSG are of full capacity whereas in DFIG they were at slip capacity. The generator speed is adjusted in both the cases according to the reference speed to capture maximum power at different wind velocity. The values of generated power observed from the simulations are summarized in the Table 2. Both the generators contribute to the maximum whereas PMSG is able to deliver more power than DFIG which can be attributed to its higher efficiency.
-
-
CASE STUDY REPORT
The following is a report of the field study conducted for the analysis of generators used in wind energy conversion system in various windmills in Coimbatore district, Tamil Nadu, India on the year 2015. The case study was preliminarily based on the performance evaluation of PMSG and DFIG. Various parameters like ratings, initial cost, running cost, maintenance, suitable climatic conditions have been considered in this case study. Due to global energy crisis, the unending utilization of fossil fuels has exploited the natural resources. Wind energy and wind farms have turned into a potential market in energy business. Selection of suitable wind turbine and generators produces maximum electrical
output. As per the report of 2015, there has been a reduction of 500 million tons of CO2. Wind power, as an alternative to burning fossil fuels, is plentiful, renewable, widely distributed, clean, produces no greenhouse gas emissions during operation, and uses little land. A feasibility study is made on both synchronous and asynchronous generators used in wind farm to analyze and compare the operation of these generators.
-
Windmill layout optimization
The first parameter considered is the ideal location and running conditions for the installation and operation of windmills. The plants must be installed where the wind flow is uninterrupted and where there is minimum disturbances in the terrain. Considering a flat terrain the wind speed increases logarithmically with height, but in case of complex terrain where the wind profile cannot be properly analyzed, a separation of wind flow occurs resulting in turbulence. One of the most important parameters is the turbulence intensity. Turbulence intensity quantifies how much the wind varies typically within 10 minutes. Because the fatigue loads of a number of major components in a wind turbine are mainly caused by turbulence, the knowledge of how turbulent a site is of crucial importance. A location with minimum terrain obstacle has to be chosen to minimize these effects. The distance between the windmills is also an important factor. A minimum distance of 150-600 m has to be maintained between two windmills. The spacing is calculated so as to compromise factors such as minimized capital cost, and the need for adequate separations for wind flow.
-
Economic Aspects
The economic factors can be divided as initial cost, running cost and maintenance cost. Though the initial cost is usually higher for synchronous generator than asynchronous generator, the PMSG is more advantageous than asynchronous generator in terms of running cost and maintenance cost. This high initial cost is due to the installation of permanent magnets in PMSG. In high rated machines, the synchronous generator with electrical exciter is more expensive than asynchronous generator. In case of induction generators there is high cost in the maintenance of the rotor structure. But in case of PMSG, the rotor is made up of permanent magnet and there is no need for rotor maintenance. The running cost is also lesser for PMSG than DFIG. The PMSG can be used for independent operation and can be operated at any speed. Whereas for the operation of the DFIG, a separate delta connected capacitor bank is required to supply the magnetizing current for exciting the generator which are more expensive. In induction generator, maintenance of gearbox is cstlier.
-
DFIG and PMSG
A 1500 kW induction machine (Plant 1) incorporated for the wind turbine is operated at negative slip region, when the rotor speed exceeds rated speed. A gearbox is used here to adjust the speed ratio between turbine shaft and generator which has to be inspected once in every week for maintenance and lubrication. Conventional control methodologies have been used in controlling the operation of the machine. A grid connection module with 3 pole circuit breaker is used in this system. A delta connected capacitor
bank with rating 3*137 µF (dry N2) with tolerance -5 to 10% is used to provide reactive power and to supply the magnetizing current. The output voltage frequency is regulated by the power system to which the generator is connected. Usually the output frequency will be 2-5% lower than the theoretical value. The power factor of the output depends upon the slip and not on the load on which it operate. A 1500 kW PMSG (Plant 2) based WECS is installed here which does not requires gearbox mechanism. The reactive power and adjustment ability is 100% across entire speed range. PMSG uses sophisticated control strategies to monitor and control the operation of the windmill. Every plant has installed a computer aided control system that monitors, analyze and record the operation of the plant. These data can be saved for up to a year within each plant. Every plant can be controlled by a central control unit. Beneath every plant an auxiliary transformer is installed under the ground with proper ventilation. The output frequency can be more easily regulated to remain at a constant value. The use of permanent magnet eliminates the use of DC field excitation.
-
-
CHOICE OF POWER CONVERTERS
Power electronic technology plays a vital role in gearless direct drive mechanism of VSWTS in order to synchronize the power output with the utility grid or private load. The fluctuated AC from the wind turbine generator is fed to three stages of power conversion. Rectifier converts variable AC to variable DC. Active switch of the boost converter is triggered to get the stabilized DC voltage from the fluctuated input. Then the DC voltage is inverted to desired AC voltage and frequency using PWM inverter. In this research, various DC- DC converters are analyzed based on the theory and real time simulation to make a choice for the proposed WECS as they play a key role in PPT and DC link voltage control.
-
Boost converter
Boost converter accepts the DC input from the rectifier and delivers DC output to the inverter. The output voltage is always greater than the input voltage as the name implies. The duty cycle of the active switch ranges between 0 and 1. By regulating the ON time of the active switch, the fluctuated input is stabilized to the constant DC output, which is normally 680 V for the proposed system. The internal configuration of the converter topology is highly suitable for wound rotor and PMSG based WECS. The design of inductor and capacitor are calculated based on the minimum overshoot level and required voltage range. Normally boost converters cannot reflect impedances that are greater than load impedances and it cannot track for MPPT in the non- operating region [24]. It is cost effective and very simple to implement whereas the performance was affected by input current harmonics and potential drop due to higher harmonic disturbances.
-
SEPIC Converter
Single ended primary inductor converter (SEPIC) is a kind of buck-boost converter capable of stepping up or stepping down the input voltage. It has non-inverting characteristics and belonging to the class of converters having two inductors. The voltage across the switch is equal to the sum of input and output voltage and hence the topology is not used for universal high power factor rectifier [25]-[26]. The static gain
of the SEPIC converter is lower than the conventional boost converter. The configuration will operate in discontinuous mode when the inductor current falls down to zero and in conduction mode when it rises. It has a larger voltage stress on the semiconductor switches, diodes results in larger conduction losses in switching elements and circuit components. The output current is pulsating and requires high value of series capacitance with current handling capabilities which is considered as drawback of the converter.
-
Modified SEPIC Converter
It is accomplished by the inclusion of additional diode DM and capacitor CM. The static gain of the classical SEPIC converter was improved by charging CM with the output of the classical boost converter. Hence the voltage applied to the inductor L2 is higher when the switch is in conduction. When the active switch is in OFF state, the energy stored in the inductor L1 is given to the load through D0 and CS and also to capacitor CM and diode DM. Therefore the voltage across the capacitor CM is equal to the voltage across the switch and the stress across the switch is reduced comparing the classical boost and SEPIC converters. Diode D0 and DM are blocked and both the inductors stores energy when the switch is in conduction mode. The input voltage is applied to the inductor L1 and voltage (VCS – VCM) is applied to the inductor L2. Hence the voltage across CM is greater than the voltage across CS. The sum of the voltage across the capacitors CM and CS is equal to the net output voltage. The average L1 inductor current is equal to the input current and average L2 inductor current is equal to the output current. Though the system has complex circuitry operation, it has the higher output gain for the given duty cycle. The operating modes of MOD-SEPIC converter have 2 stages. Initially when the switch S is in OFF state, the energy stored in the inductor L1 is transferred to the output through the capacitor CS and diode D0 and to the capacitor CM through diode DM. Therefore the voltage VCM is proportional to the switch voltage. When the switch S is turned ON, the diodes DM and D0 are blocked and the inductors L1 and L2 will gets charged and stores energy. The comparison of voltage gain is depicted in Table 2.
Table 2 Duty cycle Vs Gain
S.
No
Duty Cycle
Gain
Boost Converter
SEPIC
Converter
Modified SEPIC
1
0.1
1.11
0.11
1.22
2
0.2
1.25
0.25
1.5
3
0.3
1.42
0.42
1.85
4
0.4
1.66
0.66
2.33
5
0.5
2
1
3
6
0.6
2.5
1.5
4
7
0.7
3.33
2.33
5.66
8
0.8
5
4
9
9
0.9
10
9
19
-
-
CONCLUSIONS
Owing to their various advantages, majority of WECS are equipped with horizontal axis upwind configured wind turbine generators. The salient features of wind turbine
system and its characteristic performance have been discussed in detail. Various types of generator driven system, electrical generators used in WECS are analyzed based on maximum power extraction, controlling features and it is observed that PMSG is the better choice for direct drive wind turbine system. To add advantage, a case study has been undergone on the choice of generator, at various windmills located at Coimbatore district, Tamil Nadu, India. Finally to provide desired voltage profile from the fluctuating source, the choice of DC-DC converter have been explored based on the converter efficiency, static gain and switching stress. From the analysis, MOD-SEPIC converter is preferred, which is supported by the simulation results. The consecutive chapters will analyze the PPT algorithm, enhancing the quality of output power for the proposed system.
REFERENCES
[1] Subramani, P., Kadali, K.S. and Karthikkumar, S., 2020. Performance evaluation and circuit competence of multiple photovoltaic configurations under fractional shading state. IJAR, 6(12), pp.132-140. [2] Korlepara, N.P., Chandra, G.P., Seshagiri, B., Raju, V.N., Veeraiah, N. and Pragaspathy, S., 2021, October. ¬ Novel Freshness Indication Packaging Technology for Frozen Shrimps. In 2021 International Conference on Advancements in Electrical, Electronics, Communication, Computing and Automation (ICAECA) (pp. 1-5). IEEE. [3] NarasimhaRaju, V.S.N., Premalatha, M., Pragaspathy, S., Korlepara,N.P. and Kumar, M.M., 2021, October. Implementation of Instantaneous Symmetrical Component Theory based Hysteresis Controller for DSTATCOM. In 2021 International Conference on Advancements in Electrical, Electronics, Communication, Computing and Automation (ICAECA) (pp. 1-8). IEEE.
[4] Pragaspathy, S., Rao, R.R., Karthikeyan, V., Bhukya, R., Nalli, P.K. and Korlepara, K.P., 2022, February. Analysis and Appropriate Choice of Power Converters for Electric Vehicle Charging Infrastructure. In 2022 Second International Conference on Artificial Intelligence and Smart Energy (ICAIS) (pp. 1554-1558). IEEE. [5] Korlepara, N.P., Elanchezhian, E.B. and Subramani, P., 2022. Analysis of Dual Stator Winding Induction Generator-Based Wind Energy Conversion System Using Artificial Neural Network Maximum Power Point Tracking. International Journal of Renewable Energy Research (IJRER), 12(1), pp.372-382. [6] Phani Kumar, C., Elanchezhian, E.B. and Pragaspathy, S., 2022. An Adaptive Regulatory Approach to Improve the Power Quality in Solar PV-Integrated Low-Voltage Utility Grid. Journal of Circuits, Systems and Computers, p.2250301. [7] Rao, R.R. and Pragaspathy, S., 2022, March. Enhancement of electric power quality using UPQC with adaptive neural network model predictive control. In 2022 International Conference on Electronics and Renewable Systems (ICEARS) (pp. 233-238). IEEE. [8] Sibu, C.M., Preethi, S., Bharath Kumar, M.R., Pradeesh, K.S. and Pragaspathy, S., 2015. Design of Artificial Intelligence Based Speed Control, Automation & Braking System For Cars Using Open Source Brain-Computer Interface Technology. In International Conference on Innovative Trends in Electronics Communication and Applications (pp. 179-188). [9] Pragaspathy, S. and Anand, B., 2015. A meticulous MPPT algorithm in smoothening of wind powered output and reactive power variations for a direct driven PMSG using a single active switch controller. Advances in Natural and Applied Sciences, 9(13), pp.7-15. [10] Pragaspathy, S., Anand, B. and Maniiarasan, P., 2016. A comprehensive study on control strategy for a standalone variablespeed wind turbine system. Asian journal of research in social sciences and humanities, 6(12), pp.754-767.
[11] Pragaspathy, S. and Anand, B., 2017. Standalone battery storage unit for PMSG based variable speed wind turbine system. International Journal of Applied Research, 3(1), pp.655-662. [12] Kannan, R., Karthikkumar, S., Suseendhar, P., Pragaspathy, S., Chakravarthi, B.C.V. and Swamy, B., 2021, August. Hybrid Renewable Energy Fed Battery Electric Vehicle Charging Station. In 2021 Second International Conference on Electronics and Sustainable Communication Systems (ICESC) (pp. 151-156). IEEE. [13] Saravanan, S., Kalaiyarasi, M., Karunanithi, K., Karthi, S., Pragaspathy, S. and Kadali, K.S., 2022. Iot Based Healthcare System for Patient Monitoring. In IoT and Analytics for Sensor Networks (pp. 445-453). Springer, Singapore. [14] Nalli, P.K., Kadali, K.S., Bhukya, R., Palleswari, Y.T.R., Siva, A. and Pragaspathy, S., 2021, November. Design of Exponentially Weighted Median Filter Cascaded With Adaptive Median Filter. In Journal of Physics: Conference Series (Vol. 2089, No. 1, p. 012020). IOP Publishing. [15] Ganesh, M.S.R., Kadali, K.S., Bhukya, R., Palleswari, Y.T.R., Siva, A. and Pragaspathy, S., 2021, November. Design of Decision Based Recursive Weighted Median Filter With Exponential Weights. In Journal of Physics: Conference Series (Vol. 2089, No. 1, p. 012016). IOP Publishing. [16] Pragaspathy, S., Anand, B. and Maniiarasan, P., 2016. A performance investigation and mitigation of harmonics for the wind powered generators. Asian journal of research in social sciences and humanities, 6(12), pp.784-803. [17] Pragaspathy, S. and Anand, B., 2016. A Review on DC-DC converters for PMSG based standalone variable speed wind turbine system. International journal of engineering research and technology, 5(9), pp.41-45. [18] Menaga, S., Paruvathavardhini, J., Pragaspathy, S., Dhanapal, R. and Immanuel, D.J., 2021. An efficient biometric based authenticated geographic opportunistic routing for IoT applications using secure wireless sensor network. Materials Today: Proceedings. [19] Pragaspathy, S., Kumar, C.P., Raju, V.N., Kadali, K.S. and Saravanan, S., 2021. A high gain multi-port bidirectional converter with reduced voltage stress. Materials Today: Proceedings. [20] Karthikeyan, V., Rajasekar, S., Pragaspathy, S. and Blaabjerg, F., 2018, December. A High efficient DAB converter under heavy load conditions using inner phase shift control. In 2018 IEEE International Conference on Power Electronics, Drives and Energy Systems (PEDES) (pp. 1-6). IEEE. [21] Kumar, C.P., Pragaspathy, S., Karthikeyan, V. and Prakash, K.D., 2021, March. Power quality improvement for a hybrid renewable farm using UPQC. In 2021 International Conference on Artificial Intelligence and Smart Systems (ICAIS) (pp. 1483-1488). IEEE. [22] Pragaspathy, S. and Baskaran, A., 2017. Mitigation of Uncertainties in Wind-Powered Renewable Systems for Environmental Assets. Polish Journal of Environmental Studies, 26(1). [23] Pragaspathy, S. and Anand, B., 2019. An experimental validation on adaptive controllers in tracking and smoothening of wind power for a variable-speed system. ASTM International. [24] Karthikeyan, V., Rajasekar, S., Pragaspathy, S. and Blaabjerg, F., 2018, December. Core loss estimation of magnetic links in DAB converter operated in high-frequency non-sinusoidal flux waveforms. In 2018 IEEE International Conference on Power Electronics, Drives and Energy Systems (PEDES) (pp. 1-5). IEEE. [25] Chakravarthi, B.C.V., Naveen, P., Pragaspathy, S. and Raju, V.N., 2021, March. Performance of Induction Motor with hybrid Multi level inverter for Electric vehicles. In 2021 International Conference on Artificial Intelligence and Smart Systems (ICAIS) (pp. 1474-1478). IEEE. [26] Saravanan, S., Karunanithi, K. and Pragaspathy, S., 2020. A novel topology for bidirectional converter with high buck boost gain. Journal of Circuits, Systems and Computers, 29(14), p.2050222.