
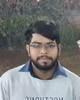
- Open Access
- Authors : Shantanu Sharma , Lovnish Kumar , Prashant Kumar
- Paper ID : IJERTV10IS050274
- Volume & Issue : Volume 10, Issue 05 (May 2021)
- Published (First Online): 31-05-2021
- ISSN (Online) : 2278-0181
- Publisher Name : IJERT
- License:
This work is licensed under a Creative Commons Attribution 4.0 International License
Scope of 3d Printing in Automobile Industry-Constraints, Viable Solutions and Relevant Applications
Shantanu Sharma, Lovnish Kumar, Prashant Kumar
Delhi Technological University
(Shahbad Daulatpur Village, Rohini, Delhi, 110042)
Abstract:- 3D printing technology has bought the manufacturing industry unprecedented advancement in term of Prototyping. It has proven its impeccable strength to deliver prototype faster and more accurate than conventional processes. However, when it comes its applications in the field of manufacturing (even after these perks of 3D printing) Automotive industry has not completely accepted this technology in its humble abode. Causes and concern may vary from high cost to limited material options. In this study, we have tried to explore various application of 3D printing in automotive industry in particular to jigs and fixture replacements, their merit over conventional jigs and fixtures
INTRODUCTION:
3D printing or additive manufacturing is a process of making three dimensional solid objects from a digital file. The creation of a 3D printed object is achieved using additive processes. In an additive process an object is created by laying down successive layers of material until the object is created. Each of these layers can be seen as a thinly sliced cross-section of the object.
3D printing is the opposite of subtractive manufacturing which is cutting out / hollowing out a piece of metal or plastic with for instance a milling machine.3D printing enables us to produce complex shapes using less material than traditional manufacturing methods.
It all starts with a 3D model. It can either be created from the ground up or can be downloaded from a 3D library. There are many different software tools available. From industrial grade to open source.
GrabCAD is free and works in any operating system. GrabCAD offers beginner lessons and has a built-in feature to export our model as a printable file e.g .STL or .OBJ.
The next step is to prepare it for 3D printer. This is called slicing.
Slicing: From printable file to 3D Printer
Slicing basically means slicing up a 3D model into hundreds or thousands of layers and is done with slicing software.
When our file is sliced, its ready for 3D printer. Feeding the file to printer can be done via USB, SD or Wi-Fi. The sliced file is now ready to be 3D printed layer by layer.
3D Printing Industry
Adoption of 3D printing has reached critical mass as those who have yet to integrate additive manufacturing somewhere in their supply chain are now part of an ever-shrinking minority. Where 3D printing was only suitable for prototyping and one-off manufacturing in the early stages, it is now rapidly transforming into a production technology.
Most of the current demand for 3D printing is industrial in nature. Acumen Research and Consulting forecasts the global 3D printing market to reach $41 billion by 2026.
As it evolves, 3D printing technology is destined to transform almost every major industry and change the way we live, work, and play in the future.
Examples of 3D Printing
3D printing encompasses many forms of technologies and materials as 3D printing is being used in almost all industries you could think of. Its important to see it as a cluster of diverse industries with a myriad of different applications.
A few examples:
-
consumer products (eyewear, footwear, design, furniture)
-
industrial products (manufacturing tools, prototypes, functional end-use parts)
-
dental products
-
prosthetics
-
architectural scale models & maquettes
-
reconstructing fossils
-
replicating ancient artefacts
-
reconstructing evidence in forensic pathology
-
movie props
3D PRINTING CONSTRAINTS W.R.T AUTOMOTIVE INDUSTRIES
-
Challenges faced during processing
Material selection
Based on the targeted application and capabilities of the printer and printer head. For Engineering parts, the material must be easy to handle and readily available. In the context of renewable materials, the material should also be based on natural or renewable resources.The 3D printing technology might use metal, polymer, hydrogels, resin, glass, ceramic, or polymer as materials to build 3D printed products. The material is placed layer-by-layer by the 3D printing machine's head. Therefore, the selection of suitable material can be considered a challenge in the utilization of 3D printing technology
The mechanical strength of products is another challenge in 3D printing technology. In terms of mechanical strength, the challenge of producing 3D printed products is to determine the suitable strength of 3D printed products. Most engineers worry if the biomedical product is not strong enough and has low mechanical strength. The engineer needs to check the 3D printed product to determine whether it has adequate tensile strength and stiffness to avoid end products that are of low quality and have low mechanical strength.
The limited choice of materials is the main challenge when utilizing 3D printing technology
Material Cost
PLA & ABS (Generic Formulations)
Generic PLA and ABS are the least expensive materials to print. The average 3D printer material cost for generic PLA and ABS approx $25 per kilogram from quality suppliers.
PLA & ABS (Specialty & Infused Formulations)
Prices in this category vary as there are a wide variety of unique versions of PLA and ABS that are specially formulated to unique specifications or add materials like ceramics, metals, wood or other materials to create unique visual effects. Materials in the specially formulated PLA and ABS category on average cost approximately $40 to $75 per kilogram.
ASA
ASA, a cousin to ABS, is great for using in outdoor applications and is quite inexpensive. You can expect to pay approximately $30 and $45 per kilogram for ASA 3D printing filament.
PETG
PETG emerged in 2017 as a very popular 3D printing filament due to its low cost and how it exhibits many industrial benefits. You should expect to pay between $30 and $40 per kilogram for generic versions of PETG and $45 to $70 for specialty formulations.
NYLON
Nylons are proprietary formulations of plastic, so you wont find generic versions. Due to the speciality nature, Nylon can be somewhat expensive and you should expect to pay between $80 and $110 USD per kilogram.
CARBON FIBER BLENDS
Many filament manufacturers are introducing blends of various plastics, inflused with Carbon Fiber. The addition of carbon fiber, improves certain characteristics of the base material, including reducing weight and increasing strength. These carbon fiber infused materials can run anywhere between $45 and $90 per kilogram.
POLYCARBONATE
Generic polycarbonate (PC) has incredible strength and temperature resistance, but is very difficult to print, even with an enclosed 3D printer like the F400. If youre game to try printing PC, you can expect to pay about $100 per kilogram. There are also blends of other materials with polycarbonate that are easier to print and actually cost less (PC-ABS for example). These formulations cost approximately $75 to $95 USD per kilogram.
Overall Cost Estimation
(credit: https://formlabs.com)
-
Challenges faced with respect to management
Skill Competency/Training
The demands and expectations of 3D printing technology are high. Therefore, engineering and technical skillsare required for the successful deployment of a wide range of 3D printing technology, from product design, material, technology, and, lastly, data management. At the same time, successful engineers must be creative, resourceful, and ready to figure things out in an industry that continues to develop and evolve. Therefore, the re-education of staff can be considered a challenge in the utilization of 3D printing technology
Cybersecurity
Cybersecurity is also a challenge in the management of 3D printing technology. Malicious cyber-attacks can affect the physical performance of 3D printing machines, the equipment, STL file and the component in the manufacturing system, which can cause a change in the shape, structural stiffness, natural frequency, and weight of the products
Hence, cybersecurity issue is another challenge to 3D printing technology used for manufacturing The sabotage can be executed remotely via internet access, which is ubiquitous in the 3D printing technology environment. The entire 3D printing technology data chain from design to manufacturing needs to be secured to maintain the integrity of both the digital data and the physical printed product when using 3D printing technology.
IMPACT OF 3D PRINTING IN THE AUTOMOTIVE INDUSTRY – VIABLE SOLUTIONS
For the past few decades, 3D printing in the automotive industry was primarily used by carmakers to create automotive prototypes to check their form and fit. The first technology for building parts was selective laser sintering or binder jetting. This allowed automakers to create aesthetically pleasant parts, but they were weak and could not be used long. According to engineering.com, today there are more robust technologies for automotive 3D printing, such as fused filament fabrication (FFF), which can be used not only for the production of prototypes but also for end-use parts.
3D printing for automotive parts can be a game-changer in the industry. The Global Automotive Outlook 2017 projects that the global automotive industry is set to reach 114 million in worldwide sales annually by 2024. This market has very high barriers of entry as it is dominated by just a few OEMs.The parts and accessories market looks different. There are a lot of large scale and smaller players and the competition there is very high. It is projected that this market will reach around US$ 17 Bn by the end of 2025.
And,according to Machine Design, consumption of 3D printing materials by the automotive industry will reach around $530 million by 2021
Printing solutions for the automotive industry provide benefits that can be easily evaluated in terms of performance characteristics. 3D printing can replace expensive and long lead-time CNC production. 3D printed plastic parts are cheaper and their production time in-house is shorter. And this means reductions in production costs, especially when dealing with the manufacturing of complex bodies.
In-house 3D prototyping can also help to control Intellectual Property (IP) infringements or information leaks as everything is produced on-site. 3D prototyping can also significantly reduce turnaround times across all stages of manufacturing allowing more agility. Unlike traditional approaches to vehicle design where a variety of materials are used, 3D printing in automotive design allows lower consumption of materials and wastage which is beneficial for all stages of manufacturing.
3D printer assisted design in the automotive industry allows designers to try multiple options of the same detail and iterations during the stages of new model development. It brings more flexibility, which results in efficient designs and flexibility in making changes in design throughout the process of model evaluation. This, in turn, helps auto manufacturers stay up to date with market needs and be ahead of the field
3D PRINTING APPLICATIONS
-
Reshaping the Prototyping Process
With 3D printing, automotive designers can quickly fabricate a prototype of a physical part or assembly, from a simple interior element to a dashboard or even a scale model of an entire car. Rapid prototyping enables companies to turn ideas into convincing proofs of concept. These concepts can then be advanced to high-fidelity prototypes that closely match the end result, and ultimately guide products through a series of validation stages toward mass production. In the automotive industry, this rapid validation is absolutely vital. Pausing an automotive manufacturing line for even an hour can be hugely costly,
Prototyping used to be time-consuming and therefore potentially expensive as a product goes through more iterations. With 3D printing, highly convincing and representative prototypes can be created within a day, at a much lower cost. Desktop 3D printers allow engineering and design teams to bring the technology in-house in order to increase iteration cycles and shorten the distance between idea and final product, strengthening their overall product development workflows.
-
Creating Custom, Complex, and High-Performance Parts
3D printing is ideal for producing custom parts at greatly reduced expense, empowering manufacturers with vast new capabilities in what they are able to produce and offer to their customers.For smaller companies who place custom at their core 3D printing car parts has provided ways of pushing the quality and creativity of their work, providing vital room to experiment with and perfect custom designs, without worry for the potential expense and time-intensive manufacturing processes that otherwise come with customization.
Larger companies are combining 3D printing technology with traditional means as well. Volkswagen recreated its iconic 1962 Microbus, replacing its gas engine with a 120 horsepower, 173 lb-ft torque electric drive. The Type 20 concept also sports a variety of improvements enabled by 3D printed parts, including generatively-designed cast aluminum wheels. Even the hubcaps are 3D printed: although they look like stamped steel, they were actually produced on SLA 3D printer and then electroplated to take on the look and feel of metal parts.
-
Producing Tooling and Manufacturing Aids
Engineers use manufacturing aids to make manufacturing and assembly processes simpler and more reliable, reducing cycle times and improving worker safety. Automotive factories and part suppliers use thousands of custom jigs and fixtures, each tailored and highly optimized for end-use. The result is a proliferation of custom tools, adding significant cost and complexity to the manufacturing process.Outsourcing the production of these custom parts to machining service providers who produce the parts from a solid billet of plastic or metal can delay production by weeks, while the long lead times also make it hard to adapt to changes on the factory floor.
Additive manufacturing can cut the lead time to a few hours and also dramatically reduce costs when compared to outsourcing parts to an external vendor. As complexity doesnt incur additional costs, the parts can also be better optimized for their end-use. New, resilient 3D printing materials have also allowed manufacturers to replace metal components in many cases with 3D printed plastic parts or to prototype and test the tools before committing.
-
Solving the Spare Parts Problem
-
-
Spare parts have historically represented a challenge for the automotive industry. Demand by nature is sporadic and unpredictable, making the value of producing spare components a debatable financial decision in some instances.
However, the value of products is more precarious and repairs more difficult in the absence of readily available spare parts. Producing spares in anticipation of later demand also requires great expenditure on storage
With the use of CAD, designs for all parts can be kept as a digital copy, making the need to keep inventory obsolete. With the proliferation of benchtop 3D printers, a spare part could potentialy be produced in-store upon customer request. The accessibility of the technology will encourage suppliers to open up new spaces to provide an easy supply of 3D printed components and spare parts.
Even parts that no longer exist can potentially be remade to requirement, on reverse engineered based on digital scans of existing parts. Older designs may find themselves with a new lease of life. People have classic cars that are 50+ years old. We might be able to support in a more automated way, through 3D printing
3D PRINTING ADVANTAGES BASED ON QCDMS PARAMETERS
AREA |
FACTOR |
ADVANTAGE |
LEARNING |
BENEFIT |
S |
SAFETY WHILE USAGE & FATIGUE |
Light weight Fixtures |
Impact of weight reduction on shop floor safety |
Equipment (Jigs) Usage And Human Safety Improved Fatigue Reduced |
Q |
ACCURACY |
Variation during Machining Operations minimised In 3D Printed Jigs |
Impact of manufacturing processes on accuracy of jigs |
Accurate Measurements as parts made as Per 3D Models |
C |
OVERALL COST |
40 ~ 50% Cost Reduced With 3d Printed Jigs |
Costing of different materials Direction for cost saving in future |
Cost Saving |
MANPOWER COST |
Low Weight Hence Manpower Reduced |
Manpower Cost Saved |
||
D |
LEAD TIME |
Reduced Manufacturing Time Hence Shorter Lead Time Better Manageable, Digital Inventory |
Lead time difference with change of technology |
Project Timeline Reduced |
TACT TIME |
Timely completion of work due to easy handling |
Impact of ergonomics on cycle time |
Line delay due to inspection reduced |
|
M |
OPERATOR MORALE |
Easy Handling & Easy Movement Worker Comfort & Improved Ergonomics |
Awareness about Focus items of shop floor management |
High Motivation of Operators |
CONCLUTION
Even though the implementation of a new approach to manufacturing might have been challenging at the beginning, companies experienced a positive impact on their production process and, consequently, in their end-products. In fact, The benefits were perceived in so many aspects of operations that companies intensified their investments in the 3D printing technology and transformed it into a vital part of manufacturing process. Concluding that it is one of the main indicators that industrial 3D printing is here to stay and is the future of manufacturing.
-
https://www.stratasys.co.in/3d-printers
REFERANCES
-
CII Workshop on 3D PRINTING for Manufacturing Agility
-
https://www.stratasys.com/explore/case-study/honda-access
-
https://www.fusion3design.com/how-much-does-3d-printing-filament-cost
-
10 Exciting Examples of 3D Printing in the Automotive Industry in 2021